Ever felt like mastering injection molding’s post-processing could be your secret weapon?
Manage injection molding post-processing by prioritizing proper cooling, trimming, surface finishing, and thorough inspection to enhance product quality, minimize defects, and boost efficiency.
You know, diving into each of these techniques can be like peeling back layers of complexity, each with its own quirks. I remember a time when a slight tweak in the cooling process saved us from a batch of warped parts—it was a game-changer! Let’s explore some detailed strategies that can revolutionize your manufacturing process.
Proper cooling reduces defects in injection molding.True
Proper cooling ensures uniform solidification, minimizing warping and defects.
Surface finishing is optional in post-processing.False
Surface finishing is crucial for aesthetics and functional quality of parts.
- 1. How Does Proper Cooling Impact Injection Molding Quality?
- 2. What Techniques Can Be Used for Effective Trimming and Deburring?
- 3. Why is surface finishing crucial in injection molded parts?
- 4. How Can Inspection Processes Reduce Defects in Injection Molding?
- 5. What Are Common Challenges in Post-Processing and How to Overcome Them?
- 6. How can I optimize production efficiency during post-processing?
- 7. Conclusion
How Does Proper Cooling Impact Injection Molding Quality?
Ever wondered why some plastic parts just don’t fit right or look off? It might be the cooling!
Proper cooling in injection molding enhances part quality, dimensional accuracy, and reduces defects. It accelerates production and boosts manufacturing efficiency.
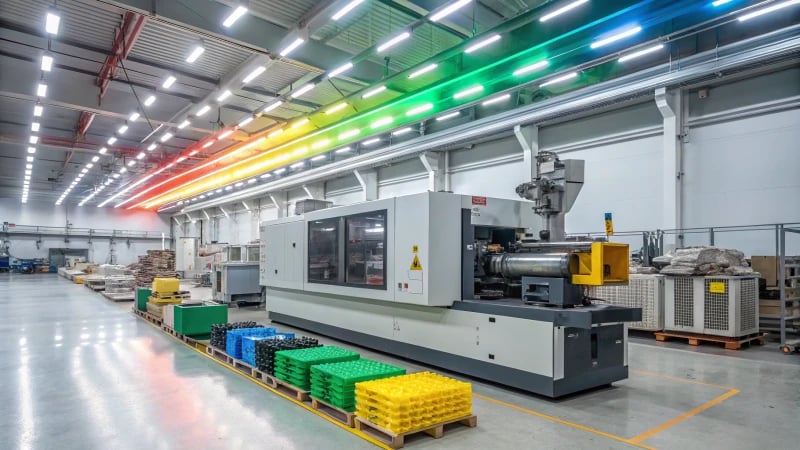
The Role of Cooling in Injection Molding
Have you ever watched a pot of soup cool down and noticed how the surface changes as it hardens? That’s a bit like what happens in injection molding1. Once that hot, molten plastic gets injected into a mold, it’s got to chill out and solidify just right to keep its shape. I remember the first time I saw this process; it felt almost magical seeing how the transformation depended so heavily on this cooling phase, which can take up to 80% of the cycle time.
Effects on Dimensional Accuracy
Imagine you’ve crafted this perfect piece in CAD, and you’re all set to see it in real life. But if cooling isn’t spot-on, those dimensions might be way off. It’s like baking a cake and finding it’s shrunk or expanded in odd places! Uneven cooling can mess with the fit and function of parts, especially when you’re making something precise like a gadget for consumer electronics.
Factor | Impact on Dimensional Accuracy |
---|---|
Cooling Rate | Faster cooling may cause shrinkage |
Cooling Uniformity | Ensures consistent part size |
Reducing Defects
I’ve seen parts come out looking warped or sporting unsightly sink marks, all because of improper cooling. It’s like leaving a tray of cookies in the oven too long—some bits are overcooked while others are just right. Consistent cooling helps prevent issues like differential shrinkage, which leads to warping.
- Warping: Happens when different areas cool at different rates.
- Sink Marks: Often from insufficient packing or not enough cooling.
Enhancing Production Efficiency
Streamlining the cooling process doesn’t just perk up part quality—it supercharges production efficiency. Imagine whipping up a batch of cookies faster without losing that delicious taste. By trimming cycle times, manufacturers can churn out more without skimping on quality. This involves balancing mold material, coolant flow rate, and cycle time like a pro.
Best Practices for Cooling Optimization
- Design Considerations: Aim for uniform wall thickness to keep cooling even.
- Cooling Channels: Use conformal cooling channels that hug the part’s geometry for smarter heat dissipation.
- Material Selection: Pick mold materials with top-notch thermal conductivity.
Bringing these practices into play? It’s like upgrading from a stovetop to a convection oven! For example, using conformal cooling techniques2 can slash cycle times and improve part consistency.
Advanced Cooling Technologies
Have you heard about variotherm or pulsed cooling? These are like the future of cooling tech! They offer razor-sharp temperature control for those tricky shapes and materials.
- Variotherm: Swaps between heating and cooling to boost surface finish.
- Pulsed Cooling: Tweaks coolant flow for the ultimate heat removal.
Diving into these technologies can be a game-changer in manufacturing settings3, helping meet tough quality benchmarks while keeping costs in check. It’s all about staying ahead in the competitive world of manufacturing.
Proper cooling reduces warping in injection molding.True
Consistent cooling prevents differential shrinkage, minimizing warping.
Cooling accounts for 50% of injection molding cycle time.False
Cooling can account for up to 80% of the cycle time.
What Techniques Can Be Used for Effective Trimming and Deburring?
Ever wondered how a simple tweak in trimming and deburring can turn an average product into a masterpiece? Let’s explore some hands-on techniques that could redefine your approach.
Effective trimming and deburring techniques include manual scraping, tumbling, thermal deburring, and precision grinding. These methods remove excess material and burrs, ensuring smooth finishes and enhanced product quality.
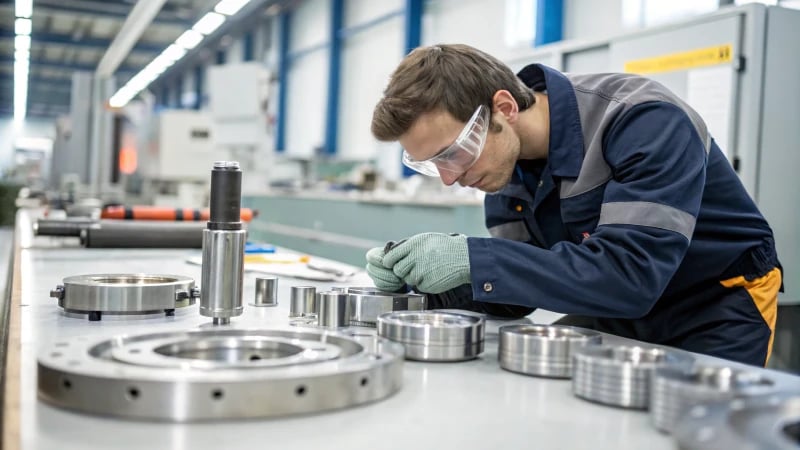
Manual Techniques
I remember the first time I picked up a file and some sandpaper, feeling like an artisan sculpting a masterpiece. Manual trimming and deburring are not just about using tools like files, sandpaper, and scrapers; it’s about the control and finesse4 you get, especially on delicate parts. It’s like the difference between a hand-painted portrait and a printed poster. The advantages include flexibility and low cost, making it my go-to for intricate work.
Mechanical Deburring
When it comes to handling larger batches, mechanical techniques have saved me countless hours. I’ve used tumbling with abrasive media in rotating barrels for uniform results across multiple parts. Think of it like a gentle rock polisher for your components. On the other hand, brushing machines, with their rotary brushes, remind me of a barber giving a clean finish — it’s all about precision setup.
Technique | Benefits | Limitations |
---|---|---|
Tumbling | Efficient for batch processes | May not reach deep recesses |
Brushing | Smooth finish | Requires precise setup |
Thermal Energy Deburring (TED)
One of the coolest methods I’ve encountered is TED, where parts are exposed to a burst of heat that vaporizes small burrs. It’s a bit like watching magic in action — fast and thorough, even reaching those hard-to-get places. However, this innovative method5 does demand respect due to the high temperatures involved.
Precision Grinding
Precision grinding has always felt like an art form to me, using grinding wheels or abrasive belts to meticulously remove excess material. It’s perfect for achieving those tight tolerances we designers love in metal parts. When accuracy is non-negotiable, this method is unbeatable.
Considerations for Safety and Quality
In my experience, safety is paramount when dealing with trimming and deburring. Proper personal protective equipment (PPE) and following safety protocols have been my best friends in avoiding mishaps. Plus, keeping equipment in top shape ensures consistent quality. And don’t forget to understand the material properties you’re working with — it’s key to selecting the right technique.
Each method has its unique charm, tailored to different materials and desired finishes. I’ve found that experimenting with various techniques can lead to discovering the perfect solution for any manufacturing challenge. If you’re as curious as I was when I first started, exploring advanced deburring methods6 might just open up new avenues for achieving impeccable results.
Manual deburring is cost-effective and flexible.True
Manual methods use inexpensive tools like files and sandpaper, offering flexibility.
TED is unsuitable for reaching inaccessible areas.False
TED can reach inaccessible areas by vaporizing burrs with heat bursts.
Why is surface finishing crucial in injection molded parts?
Ever noticed how the smoothness of a product can make all the difference? That’s where surface finishing steps in, transforming ordinary into extraordinary. It’s like the final touch that brings your masterpiece to life.
Surface finishing in injection molded parts is essential for improving visual appeal, durability, and functional performance, ensuring high quality and desired product characteristics.
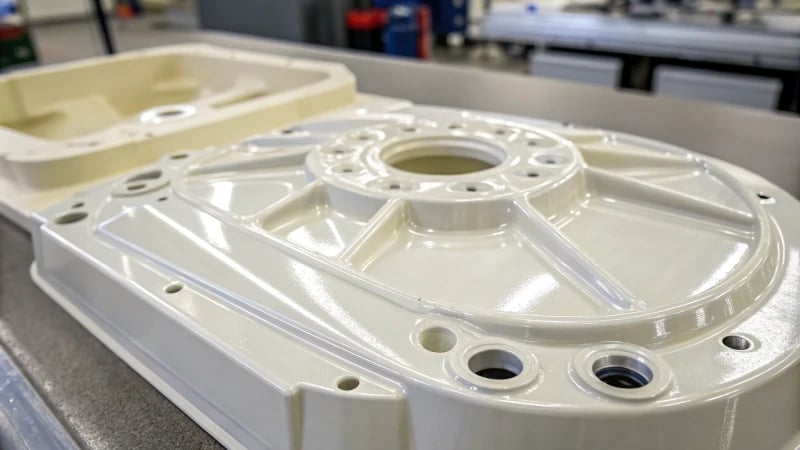
Aesthetic Appeal
I remember the first time I held a sleek gadget in my hand. It was love at first sight! The surface was glossy and vibrant, making it look like it belonged in a high-end store. Surface finishing plays a pivotal role in achieving that kind of allure, especially in consumer electronics7. A carefully chosen finish can enhance everything from color vibrancy to texture, ensuring your product stands out from the crowd.
Durability and Protection
Picture this: you’ve just designed a fantastic product, but over time, the sun fades its colors, and moisture wears it down. Heartbreaking, right? This is where surface finishing saves the day. By adding a protective layer, it shields your creation from environmental villains like UV light and moisture. Take UV-resistant coatings8, for instance—they’re like sunscreen for your products, preserving their beauty and functionality for years to come.
Functional Performance
Imagine gripping a tool with a rough handle—it just feels right, doesn’t it? That’s the magic of a well-thought-out surface finish. Whether it’s enhancing grip, reducing friction in moving parts, or ensuring a perfect fit during assembly, the finish can make or break a product’s performance. It’s not just about looks; it’s about how the product works seamlessly in its environment.
Industry Standards and Considerations
Navigating industry standards can feel like solving a complex puzzle—each piece must fit perfectly. In my experience, understanding these standards is crucial to ensure safety and performance. For example, the ISO 90019 guidelines often dictate consistent quality in surface finishes. Knowing these rules helps me make informed choices that meet both aesthetic and functional needs while adhering to industry norms.
Aspect | Impact of Surface Finishing |
---|---|
Aesthetic Appeal | Enhances color vibrancy and texture |
Durability | Adds protection against UV light & moisture |
Functionality | Influences grip and reduces friction |
Standards | Ensures compliance with industry norms |
By keeping these factors in mind, I ensure that my designs not only meet client expectations but also stand the test of time. The result? High-quality molded components10 that impress and endure.
Surface finishing enhances color vibrancy.True
Surface finishing improves the visual appeal by enhancing color vibrancy.
A rough finish decreases grip on parts.False
A rough finish is often used to improve grip, not decrease it.
How Can Inspection Processes Reduce Defects in Injection Molding?
Defects in injection molding can feel like a never-ending battle, but with a little strategy and the right inspection processes, we can catch issues before they snowball into major headaches.
Inspection processes in injection molding reduce defects by identifying errors early, allowing timely corrections. They ensure consistent quality, minimize rework costs, and enhance product reliability.
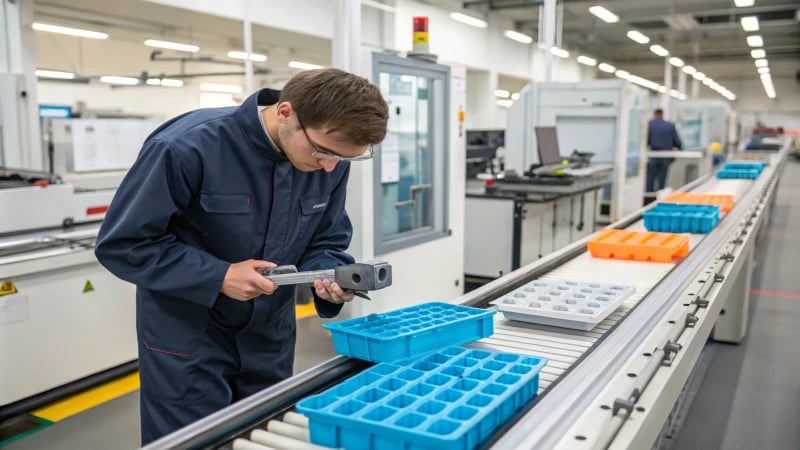
Understanding the Role of Inspection in Injection Molding
Having spent countless hours in the hustle and bustle of a mold shop, I’ve learned that maintaining high quality in injection molding is like keeping your favorite car running smoothly—it requires regular check-ups and a keen eye for detail. Inspections are our front-line defense, catching defects before they turn into costly mistakes. By evaluating everything from molds to materials and the final product11, we’re able to nip problems in the bud, reducing waste and ensuring our products consistently meet high standards.
Key Inspection Techniques
Over the years, I’ve come to rely on several key techniques that have become staples in my inspection toolkit:
- Visual Inspection: Imagine catching a glimpse of a tiny warp or discoloration just in time. This hands-on method lets us spot visible defects instantly.
- Dimensional Inspection: Precision tools become our best friends here, ensuring every measurement aligns perfectly with specifications.
- Non-destructive Testing (NDT): Think of it as a health check-up for parts. Techniques like ultrasonic testing let us peek inside without causing harm.
Technique | Purpose |
---|---|
Visual Inspection | Identify visible defects |
Dimensional Testing | Verify critical measurements |
NDT | Assess internal integrity |
Implementing a Robust Inspection Process
Crafting a solid inspection process feels like assembling a puzzle—every piece matters. Regular checks at various stages of production are crucial. Here’s how I tackle it:
- Pre-production Inspections: I make sure molds and machines are in tip-top shape, avoiding hiccups before they start.
- In-process Inspections: Keeping an eye on things as they roll ensures consistency and heads off potential issues.
- Final Product Inspections: Before anything leaves the shop, thorough checks ensure we deliver only the best.
Leveraging Technology for Enhanced Inspections
Incorporating modern technology into inspections is like having an extra set of eyes with superpowers. Automated inspection systems12 use cameras and sensors to spot defects that might slip past us, offering precision and speed that boost our confidence in each product’s quality.
Implementing these strategies not only minimizes defects but also enhances overall productivity and customer satisfaction by ensuring reliable product delivery. It’s all about combining old-school vigilance with new-school tech to create products that stand the test of time.
Visual inspection can detect internal defects in molds.False
Visual inspection only identifies surface defects, not internal issues.
NDT techniques assess internal part integrity without damage.True
Non-destructive testing evaluates internal structures without harming the part.
What Are Common Challenges in Post-Processing and How to Overcome Them?
Ever felt overwhelmed by the maze of post-processing in additive manufacturing? Trust me, you’re not alone.
Common post-processing challenges include material inconsistencies, surface finishes, and time management. Overcome these by using advanced simulation software, careful material handling, and automation systems.
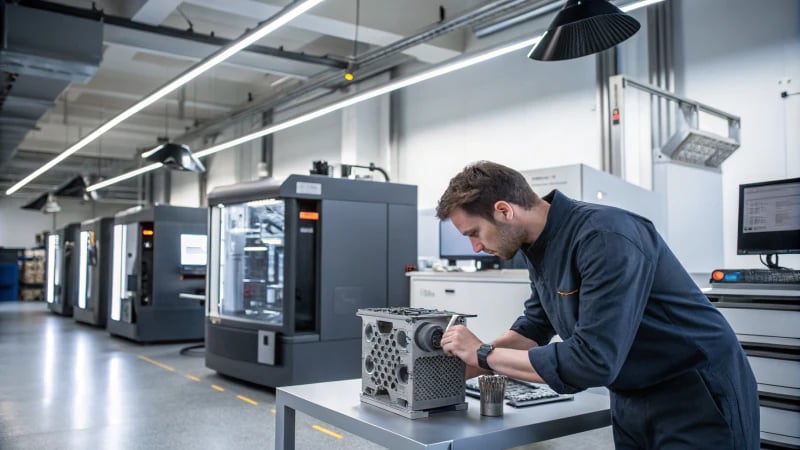
Understanding Material Inconsistencies
Oh boy, let me tell you about the time I thought I had it all figured out with a new plastic material—only to watch it warp and crack like nobody’s business during post-processing. Different materials react in unpredictable ways. To save yourself a few headaches, consider using simulation software13 to predict these behaviors and tweak your processes accordingly.
Achieving Desired Surface Finishes
Getting that perfect finish is like chasing a unicorn. The layer lines and material quirks can turn what should be a smooth surface into a bumpy ride. I once tried to eyeball it with manual sanding—it was a disaster. Techniques like chemical smoothing or bead blasting really saved the day. Plus, automated tools can give you that consistency manual work often lacks.
Managing Post-Process Times
If you’re anything like me, you might underestimate how long post-processing takes. It’s a classic rookie mistake. Streamlining this phase through automation14 can slash labor costs and boost efficiency. Implementing automated cleaning systems or robotic arms feels like having extra hands on deck.
Tools and Techniques Comparison
Technique | Advantages | Limitations |
---|---|---|
Chemical Smoothing | Quick, effective | Requires chemical safety |
Bead Blasting | Good for rough surfaces | May damage delicate parts |
Automated Systems | Consistent, time-saving | High initial cost |
Knowing the ins and outs of each technique helps me choose the best tool for the job at hand.
Quality Control and Assurance
Quality control is like my safety net. Ensuring consistent quality through rigorous quality control15 checks with advanced imaging and scanning technology has saved my bacon more than once. Integrating AI-based inspection systems further boosts precision, catching defects before they become costly issues.
Cost Management in Post-Processing
Balancing costs while maintaining quality feels like walking a tightrope. Analyzing cost efficiency16 with software solutions reveals where I can trim expenses without sacrificing quality. Regular audits have helped pinpoint unnecessary expenditures, paving the way for more cost-effective production.
By tackling these challenges head-on with the right strategies and tools, I’ve optimized post-processing in additive manufacturing for smoother and more successful outcomes.
Material inconsistencies can cause post-processing defects.True
Different materials react differently to post-processing, causing defects.
Automated systems increase post-processing times.False
Automation reduces labor costs and speeds up the workflow.
How can I optimize production efficiency during post-processing?
Ever feel like you’re juggling too many balls in the post-processing stage? Let’s dive into some smart strategies to streamline your workflow and make life a little easier.
Optimize production efficiency in post-processing by automating processes, streamlining workflows, and investing in technology. Evaluate and refine current processes, eliminate bottlenecks, and apply lean manufacturing principles for improved productivity and quality.
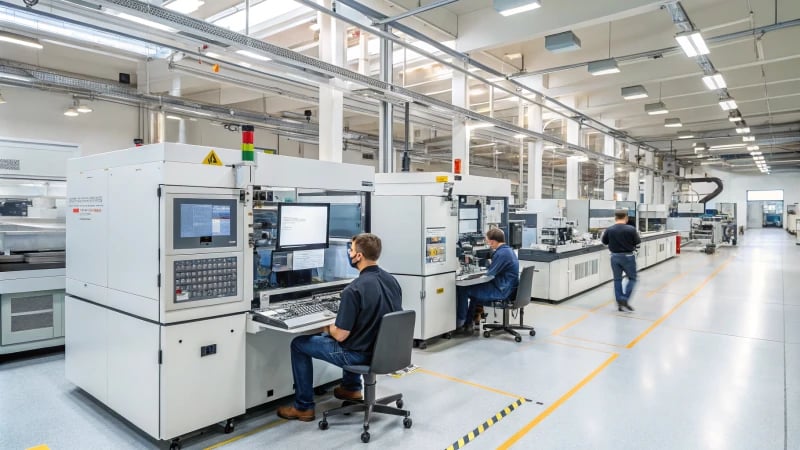
Leveraging Technology for Efficiency
In my journey, I’ve realized the power of advanced technology in boosting efficiency. Implementing automation tools17 has significantly cut down on manual labor and errors in my workflow. I once invested in a real-time monitoring system that offered analytics so insightful, it felt like having an extra pair of eyes on the production line. This allowed me to tweak processes on the fly, making my operations smoother than ever.
Technology | Benefit |
---|---|
Automation Tools | Reduces manual work |
Real-Time Analytics | Offers performance insights |
Streamlining Workflow Processes
I’ve found that assessing and restructuring workflows is like cleaning out a closet—essential yet revealing. Mapping each step uncovers redundancies you might overlook. Techniques like Value Stream Mapping18 can highlight wasteful areas. By adopting a "just-in-time" approach, I’ve ensured that resources are used efficiently, minimizing delays.
Implementing Lean Manufacturing Principles
When I first learned about lean principles, they seemed like common sense wrapped in a fancy package. But applying them changed everything. By focusing on eliminating waste and improving flow, I’ve seen substantial gains in efficiency during post-processing. The 5S methodology—Sort, Set in order, Shine, Standardize, Sustain—has become a mantra for maintaining an organized workspace. It’s amazing how much time you save when you’re not hunting for misplaced tools.
Efficient Resource Management
Resource management has been another area where I’ve seen tangible improvements. Ensuring that my team is well-trained and that equipment is regularly maintained has prevented unexpected downtime. Using resource management software19, I’ve been able to track usage and predict future needs effectively.
By incorporating these strategies, I’ve optimized production efficiency during post-processing, paving the way for smoother operations and better output quality. Each method requires a tailored approach based on the specific needs and conditions of your production line. And believe me, when everything clicks into place, it feels like hitting all green lights on your morning commute.
Automation tools can reduce manual labor by 50%.False
The exact percentage reduction depends on the industry and tools used.
Lean principles eliminate waste in post-processing.True
Lean principles focus on minimizing waste to improve efficiency.
Conclusion
Mastering post-processing in injection molding involves optimizing cooling, trimming, surface finishing, and inspection to enhance product quality and efficiency while minimizing defects.
-
Explore this link to understand each step of the injection molding process, enhancing your grasp on how cooling fits into the entire cycle. ↩
-
Learn about conformal cooling techniques to improve heat dissipation and efficiency in your molding processes. ↩
-
Discover cutting-edge cooling technologies that could revolutionize your production methods and improve quality. ↩
-
Explore manual tools that provide artisans with precise control during trimming and deburring processes. ↩
-
Learn about the innovative thermal energy deburring technique and how it efficiently removes small burrs. ↩
-
Discover advanced methods tailored to meet specific manufacturing needs, enhancing product quality. ↩
-
Discover how surface finishing enhances product aesthetics and market appeal in the competitive consumer electronics industry. ↩
-
Learn how UV-resistant coatings protect plastic parts from discoloration and degradation over time. ↩
-
Explore ISO 9001 guidelines to ensure consistent quality in surface finishing processes. ↩
-
Explore various surface finish options available for injection molded components. ↩
-
Discover the significance of product inspection in ensuring defect-free manufacturing processes. ↩
-
Learn how automated systems improve accuracy and efficiency in defect detection. ↩
-
Explore methods to predict and manage material behavior during post-processing to ensure quality. ↩
-
Understand how automation can streamline workflows and reduce labor costs. ↩
-
Discover how advanced imaging and AI can enhance defect detection. ↩
-
Learn ways to minimize costs without compromising on quality. ↩
-
Discover the latest automation tools that can streamline your manufacturing processes and reduce manual labor. ↩
-
Learn how Value Stream Mapping can help identify inefficiencies in your workflow and improve overall productivity. ↩
-
Explore software options for managing resources effectively, ensuring optimal usage and reduced waste. ↩