Injection molding is more than just a process; it’s a journey toward precision and excellence. Let’s explore how to make this journey smoother.
To achieve high repeatability in injection molding, focus on high-quality equipment, precise material management, optimized process parameters, and skilled personnel. These elements ensure consistent product quality and operational efficiency.
While the initial answer provides a foundational approach, understanding each element in depth offers valuable insights into refining your injection molding processes. Explore these areas further to enhance your production capabilities and reduce defects.
High-quality equipment ensures repeatability in injection molding.True
Stable equipment performance reduces variability, ensuring consistent output.
How Does Equipment Quality Impact Injection Molding Repeatability?
Equipment quality is crucial in injection molding, influencing repeatability and ensuring product consistency over time.
High-quality equipment in injection molding ensures stable performance, accurate parameter control, and consistent product output. Regular maintenance of both machines and molds is critical to maintaining precision and repeatability in production.
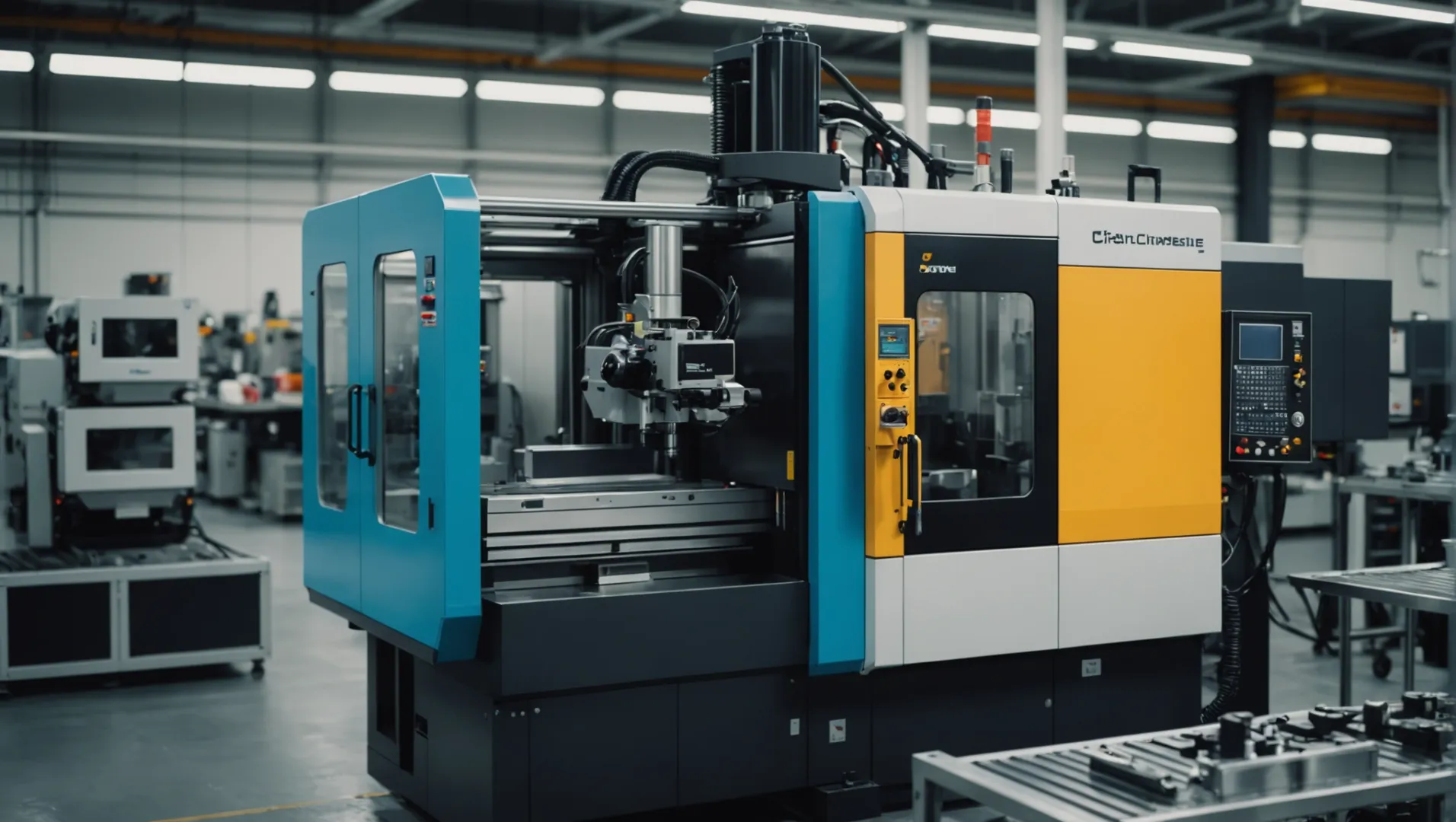
Importance of High-Quality Injection Molding Machines
Selecting a high-performance injection molding machine is foundational for achieving repeatability. These machines must offer stable operation, allowing precise control over various parameters such as injection pressure, speed, and clamping force. This stability ensures that every cycle produces consistent results, reducing variability in finished products. A well-maintained machine can operate optimally, preventing unexpected downtimes that can compromise repeatability.
Learn about high-performance injection molding machines1
Regular Maintenance and Servicing
Routine maintenance of injection molding equipment is non-negotiable. It involves periodic checks of critical components like the hydraulic and electrical systems. Addressing wear and tear promptly by replacing worn parts can prevent malfunctions that lead to deviations in product quality. Regular inspections help sustain the machine’s efficiency, ensuring it operates within its designed parameters consistently.
Explore maintenance strategies for injection molding machines2
Mold Quality and Maintenance
The mold’s quality directly impacts the precision and repeatability of injection molding. High-precision molds should meet dimensional tolerances and maintain a superior surface finish to minimize product defects. It’s equally important to implement a robust maintenance routine for molds, including cleaning, lubrication, and rust prevention, to extend their service life and preserve product consistency.
Discover the importance of mold maintenance3
Summary Table: Key Equipment Quality Factors
Aspect | Impact on Repeatability |
---|---|
Machine Stability | Ensures parameter control, reducing variability |
Maintenance Frequency | Prevents malfunctions, maintains operational efficiency |
Mold Precision | Directly affects dimensional accuracy of products |
Mold Care | Extends mold lifespan, sustains product quality |
High-quality machines enhance repeatability in injection molding.True
Stable operation of high-quality machines ensures consistent product output.
Mold maintenance is unnecessary for injection molding precision.False
Regular mold maintenance is crucial for maintaining product consistency.
What Role Do Materials Play in Ensuring Consistent Product Quality?
Materials are the backbone of product quality in manufacturing, impacting consistency and performance.
Materials are crucial in ensuring consistent product quality by affecting the mechanical properties, appearance, and performance of the final product. Quality control, proper storage, and handling practices are vital in maintaining material integrity.
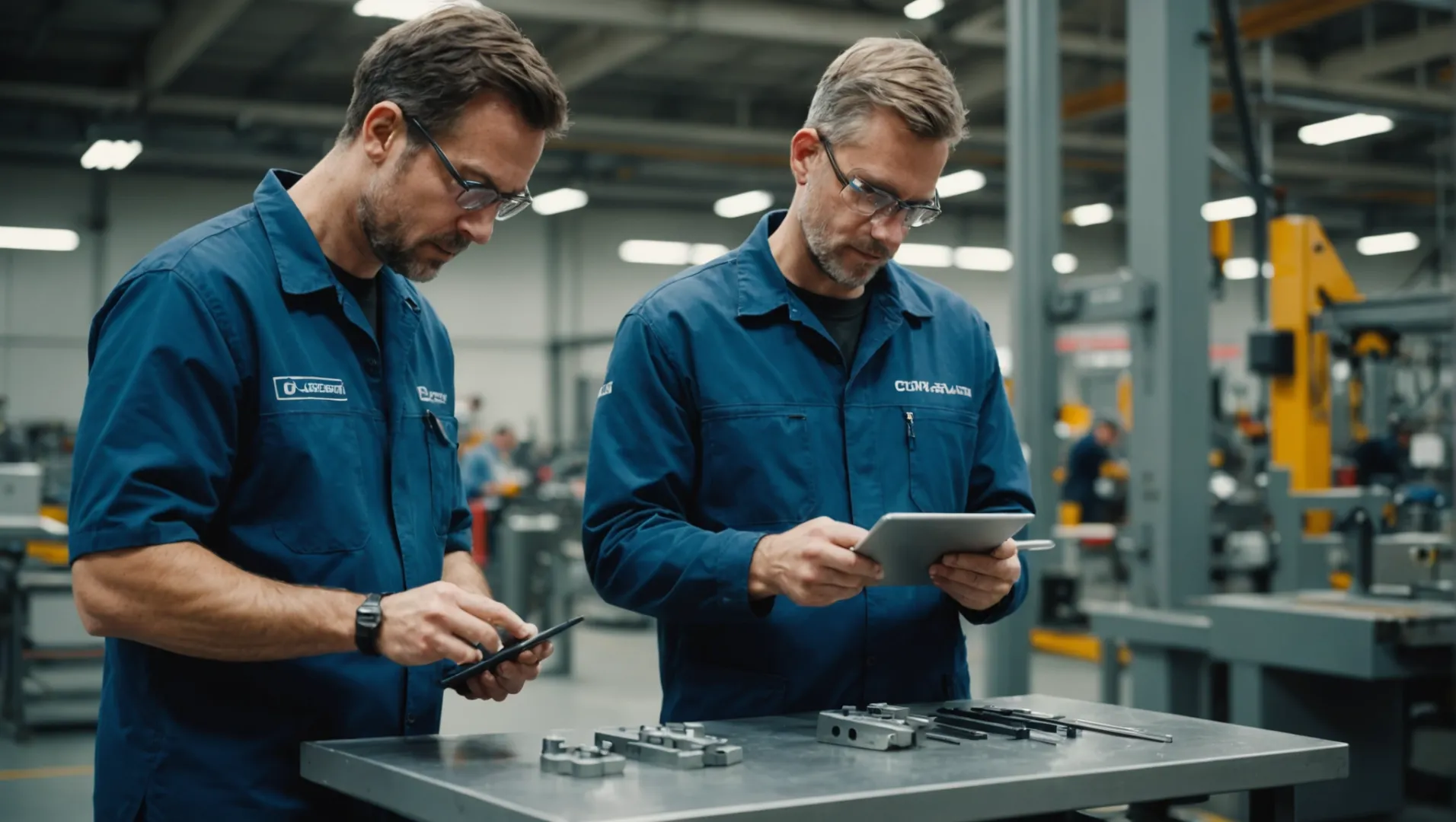
Importance of Material Quality Control
Material quality directly influences the final product’s attributes. Selecting suppliers with a proven track record of stable quality ensures that raw materials meet stringent specifications. Conducting thorough inspections, including particle size and moisture content, helps in maintaining uniformity across batches. Quality control measures prevent defects like warping or cracking, which can occur due to subpar materials.
Impact of Moisture on Material Integrity
Moisture absorption is a common issue, especially with hygroscopic materials like nylon and polycarbonate. This can lead to poor molding performance and inconsistent quality. Implementing drying protocols tailored to specific materials mitigates moisture-related issues. Controlling drying temperature and time is critical; excessive drying might degrade material properties, while insufficient drying can leave moisture that compromises product quality.
Material Type | Drying Temperature (°C) | Recommended Drying Time (hrs) |
---|---|---|
Nylon | 80 – 90 | 4 – 6 |
Polycarbonate | 110 – 120 | 3 – 5 |
Ensuring Consistency Through Material Management
Efficient material management involves systematic tracking and storage. Establishing a comprehensive database4 for raw materials assists in monitoring batch consistency and identifying potential issues early. Proper labeling and inventory management further enhance traceability and reduce waste.
Role of Innovative Materials in Enhancing Quality
Exploring advanced materials such as biopolymers and composites opens new avenues for improving product quality. These materials offer unique properties that can enhance strength, durability, and environmental compatibility. Partnering with innovative suppliers can provide access to cutting-edge materials that elevate product standards.
By focusing on material quality and handling, manufacturers can significantly enhance the consistency and reliability of their products. This foundational step not only ensures compliance with industry standards but also fosters customer trust and satisfaction.
Materials impact product appearance and performance.True
Materials affect mechanical properties, appearance, and final product performance.
Excessive drying improves material quality.False
Excessive drying can degrade material properties, harming product quality.
How Can Optimizing Process Parameters Enhance Repeatability?
Optimizing process parameters in injection molding is key to achieving high repeatability, ensuring each product is consistent and meets quality standards.
By carefully controlling injection temperature, pressure, speed, and cooling time, manufacturers can enhance repeatability in injection molding. This optimization reduces variability, leading to consistent product quality and reduced defect rates.
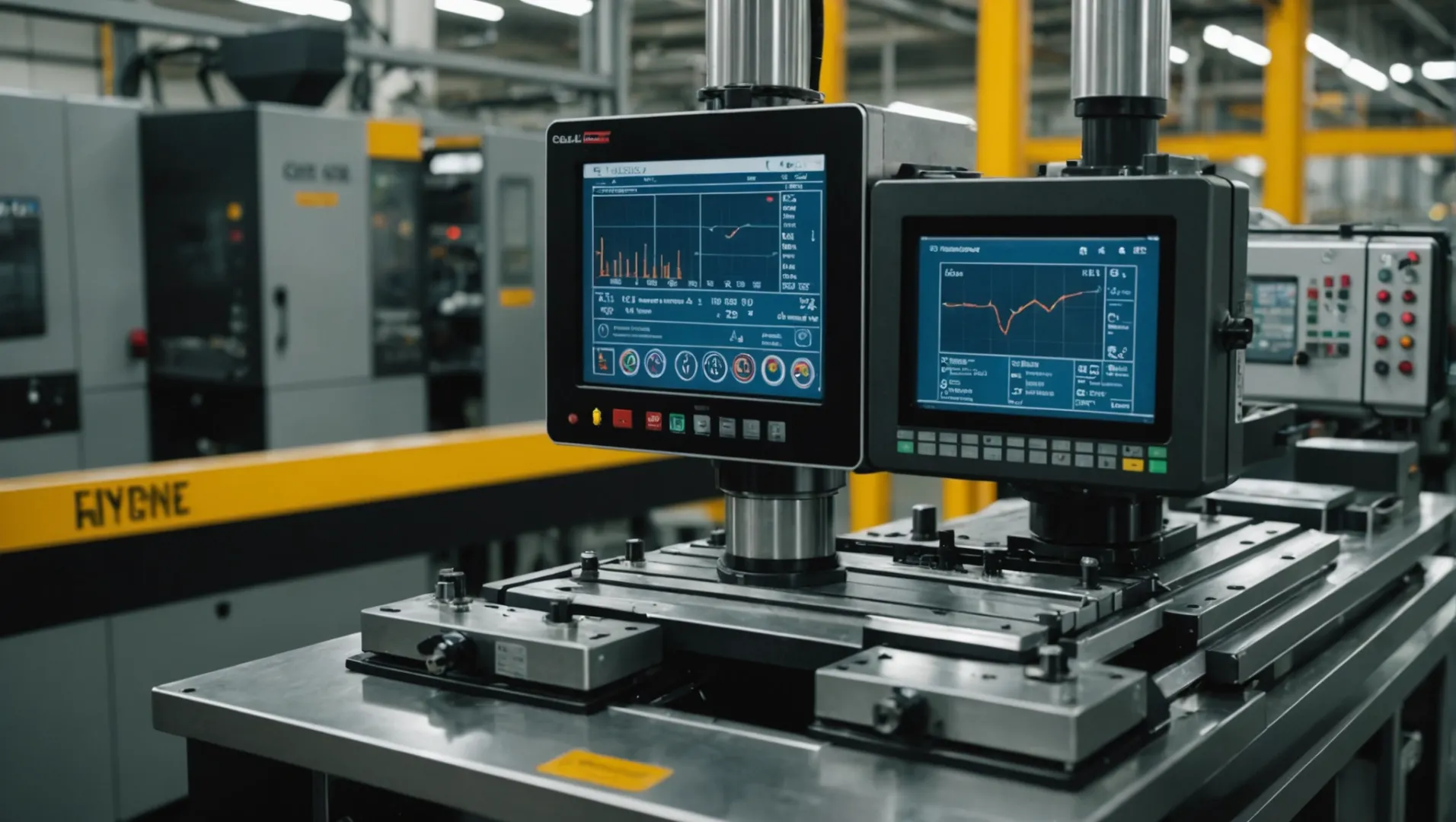
Importance of Process Parameter Optimization
The first step to enhancing repeatability in injection molding is understanding the significance of process parameters5. Each parameter plays a crucial role in determining the final quality of the product. Variations in temperature, pressure, or cooling time can lead to inconsistencies, resulting in defects such as warping or incomplete fills.
Key Parameters to Optimize
-
Injection Temperature: This affects the viscosity of the molten material. Too high, and it can degrade the material; too low, and it can cause incomplete filling. The goal is to find a temperature that ensures optimal flow without compromising the material’s integrity.
-
Injection Pressure: This determines how forcefully the material is injected into the mold. Insufficient pressure may lead to short shots or voids, while excessive pressure can cause flash or damage to the mold.
-
Injection Speed: This impacts how quickly the mold cavity is filled. A balanced speed prevents both material degradation and premature cooling.
-
Cooling Time: Proper cooling ensures that parts are adequately solidified before ejection, preventing warping and ensuring dimensional accuracy.
Parameter | Effect on Quality | Optimization Strategy |
---|---|---|
Injection Temperature | Influences material flow and integrity | Maintain within manufacturer’s recommended range |
Injection Pressure | Affects fill consistency and mold integrity | Adjust based on material type and part complexity |
Injection Speed | Impacts fill time and material properties | Balance speed with temperature and pressure |
Cooling Time | Ensures proper solidification and dimensional accuracy | Optimize based on part size and material properties |
Implementing an Automated Control System
An automated control system6 can monitor these parameters in real time, making adjustments as necessary to maintain optimal settings throughout production. This reduces human error and enhances repeatability by ensuring parameters remain within specified limits.
Building a Process Parameter Database
Establishing a comprehensive database for process parameters is essential. It allows for quick reference and adjustment, reducing downtime and ensuring consistent application of optimized settings across different production runs. This database should be updated regularly based on experimental data and observations7.
By focusing on these optimization strategies, manufacturers can significantly enhance the repeatability of their injection molding processes, leading to higher quality products and improved operational efficiency.
Injection temperature affects material flow in molding.True
Temperature impacts viscosity, crucial for filling molds correctly.
Automated systems decrease repeatability in injection molding.False
Automation enhances repeatability by maintaining optimal parameters.
Why Is Operator Training Crucial for Achieving High Repeatability?
Skilled operators are the backbone of injection molding efficiency, directly influencing product consistency and repeatability.
Operator training is essential in injection molding because it equips personnel with the skills needed to correctly operate machinery, adjust parameters, and implement quality control measures. Well-trained operators ensure adherence to standards, reducing variability and defects in production.
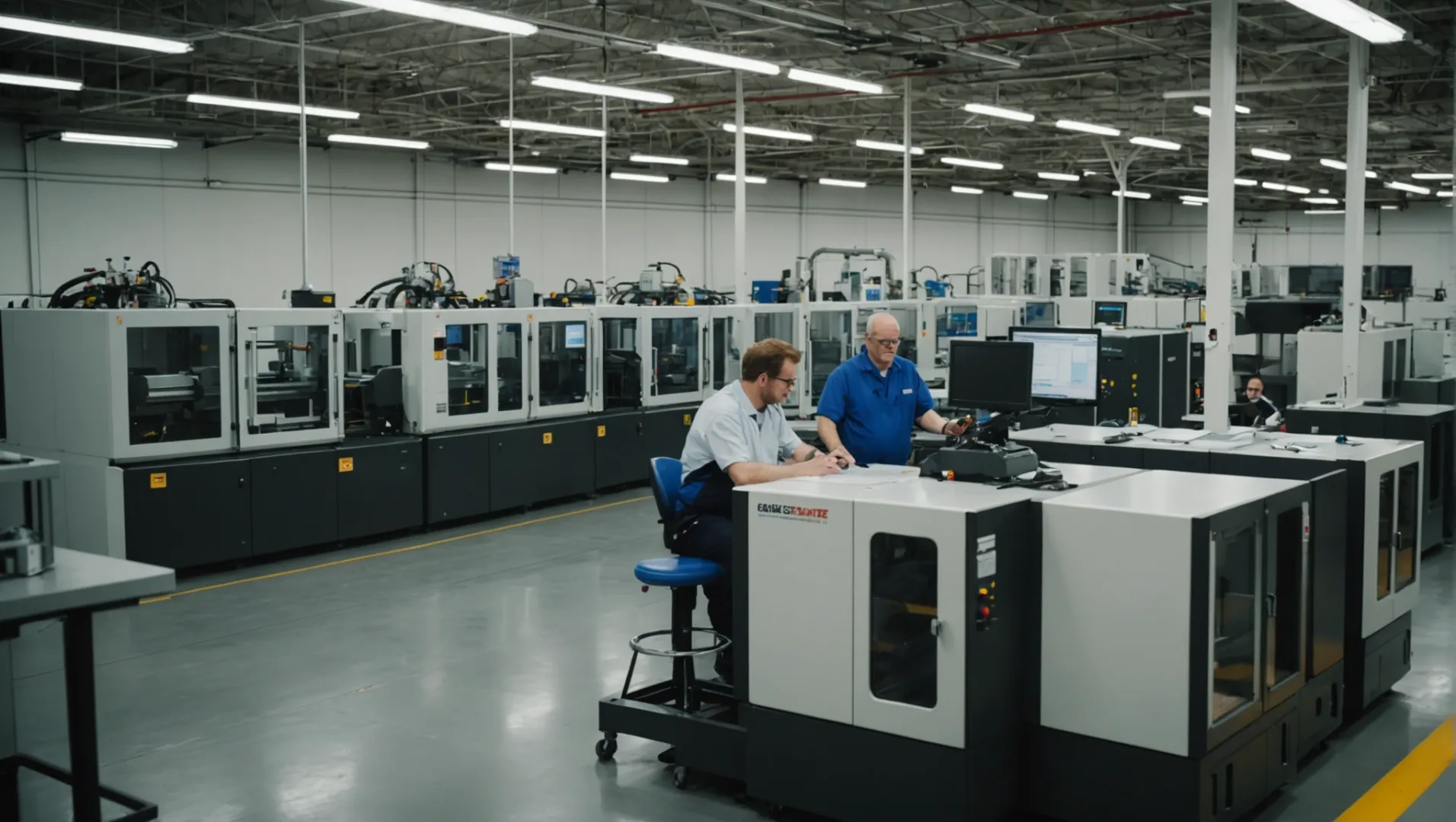
The Foundation of Skilled Operation
Operator training in injection molding is pivotal not only for the mastery of equipment but also for understanding the nuances of mold installation and adjustment. Operators familiar with the latest technology and techniques can prevent machine downtime8 and enhance productivity. This knowledge extends beyond basic operation to include troubleshooting, which mitigates production errors and reduces wastage.
Precision in Parameter Adjustment
Training allows operators to skillfully adjust injection molding parameters like temperature, pressure, and speed. These parameters, when finely tuned by knowledgeable personnel, ensure that the production process is consistent across different batches. For example, understanding the importance of maintaining the correct injection pressure helps prevent defects such as short shots or flashing, thereby improving product quality9.
Parameter | Impact on Repeatability |
---|---|
Injection Pressure | Affects part integrity and surface finish |
Cooling Time | Influences dimensional stability |
Holding Pressure | Ensures uniformity in mold filling |
Enhancing Quality Control Practices
A well-trained operator plays a crucial role in upholding quality control standards. By conducting regular inspections and understanding how to implement a robust quality management system, operators can detect deviations early. This proactive approach enables them to address issues swiftly, thus maintaining high repeatability in the production process.
Creating a Culture of Continuous Improvement
Encouraging operators to engage in ongoing education fosters a culture of continuous improvement. Establishing assessment systems where operators are regularly evaluated can further enhance their skills and motivation. This not only improves their performance but also leads to innovative solutions for complex challenges within the production environment. Encouraging continuous learning10 ensures operators remain adaptable to advancements in injection molding technology.
Operator training reduces injection molding defects.True
Training helps operators understand equipment and parameters, reducing defects.
Untrained operators ensure high repeatability in production.False
Without training, operators lack the skills to maintain consistency.
Conclusion
Mastering injection molding repeatability requires strategic focus on equipment, materials, processes, and personnel. Reflect on these strategies and adapt them to your specific needs.
-
Discover how advanced machines enhance injection molding efficiency.: 1. Good molding and coloring properties. 2. Strong bonding ability. 3. The two-color plastic mold processed by precision injection molding has good wear … ↩
-
Learn techniques to prolong machine lifespan and efficiency.: Improve dim overhead lighting. Plant lighting in an injection molding building that facilitates visibility can improve machine inspection. ↩
-
Understand how mold care impacts product precision.: Regular, careful injection mold maintenance can prevent part failures and lower the overall cost of your injection molding program. ↩
-
Explore how databases ensure material consistency and quality control.: Databases provide a more robust, scalable, secure, and efficient environment for managing supply chain data compared to spreadsheets. ↩
-
Discover how parameter optimization directly influences product consistency.: Injection molding tool and process engineers must take these 8 steps to ensure consistent and repeatable manufacturability of flawless molded parts. ↩
-
Learn how automation improves parameter control for better repeatability.: Better utilization of the machines. · Faster production: Robotic systems can move through processes without interruption. · Reduced labor costs · More sustainable … ↩
-
Understand the importance of a parameter database for efficient production.: Use a machine/mold setup sheet to document plastic parameters and use them on any acceptable machine into which the mold is placed. ↩
-
Discover strategies to minimize downtime through effective operator training.: 1. Track Downtime · 2. Monitor Production · 3. Create a Preventative Maintenance Schedule · 4. Provide Operator Decision Support · 5. Perform DMAIC Analysis. ↩
-
Learn how precise parameter adjustments enhance product quality.: Product quality analytics helps improve production through faster quality checks, predictive & prescriptive quality analytics, … ↩
-
Explore the benefits of fostering a continuous learning environment.: One of the central benefits of continuous learning is that it allows employees to develop new skills and refine and enhance the ones they currently possess. ↩