Imagine spending hours on a mold design only to have it fail during production. I’ve been there, and trust me, it’s no fun.
To design an effective injection mold ejection mechanism, analyze the product’s shape and material, calculate the ejection force, choose the right method, find optimal positions, and ensure integration with other mold systems.
Now, let’s dive deeper into what really makes an ejection mechanism work like a charm. Each detail matters—from understanding the quirks of the plastic materials to selecting the perfect ejection method. I’ve learned that breaking down these steps can transform a design from good to exceptional. Here are some insights and practical examples that might just make your next project smoother and more efficient.
Ejection force calculation is crucial for mold design.True
Accurate ejection force ensures product quality and prevents damage.
Shape analysis is irrelevant in ejection mechanism design.False
Shape analysis helps determine the best ejection method for efficiency.
- 1. How Do Plastic Product Characteristics Influence Ejection Design?
- 2. What Are the Different Methods of Ejection in Injection Molding?
- 3. How do I determine the best ejection position in a mold?
- 4. What Factors Influence the Calculation of Ejection Force?
- 5. How can I ensure proper coordination between the ejection mechanism and other mold parts?
- 6. What Mistakes Should I Avoid in Ejector Mechanism Design?
- 7. Conclusion
How Do Plastic Product Characteristics Influence Ejection Design?
When I first delved into the world of mold design, understanding how plastic characteristics affected ejection was a game changer. Let’s explore this essential aspect together.
Plastic product characteristics, such as shape, size, and material, influence ejection design by determining ejection methods and positions, ensuring the quality and structural integrity of molded products.
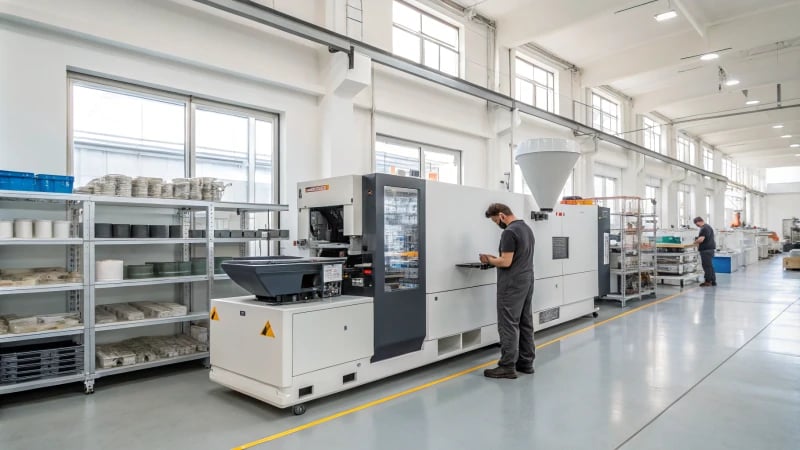
Understanding Product Shape and Size
The geometric shape and size of a plastic product are primary factors influencing ejection design. Simple shapes like flat plates may allow flexible ejection methods1, whereas complex structures with ribs or undercuts require a combination of methods. For example, a product with deep holes needs careful ejection design to avoid damaging the hole walls.
Product Type | Ejection Method |
---|---|
Simple flat plate | Push rod |
With deep holes | Combination |
Material Properties Impact
Different plastics have unique properties like elastic modulus and shrinkage rates. Polypropylene (PP) has a high shrinkage rate, requiring consideration of potential clamping force during ejection. Materials prone to deformation need careful selection of ejection positions to prevent damage.
- Polypropylene (PP): High shrinkage rate
- Polycarbonate (PC): Prone to stress cracking
Selecting Ejection Methods
Choosing an appropriate ejection method is crucial. Common methods include push rod, push tube, and push plate ejection, each suited for specific product types.
Push Rod Ejection
- Working Principle: Acts directly on the product surface.
- Applications: Suitable for regular shapes without undercuts.
Push Tube Ejection
- Working Principle: Moves along the product’s outer or inner surfaces.
- Applications: Ideal for cylindrical products.
Push Plate Ejection
- Working Principle: Contacts the entire bottom surface for ejection.
- Applications: Used for large, flat products without surface marks.
Determining Ejection Position
The ejection position should be uniformly distributed to ensure even stress distribution. It should avoid weak areas like thin walls or reinforcing ribs. Consideration of shrinkage deformation2 helps in selecting suitable positions.
Consideration | Action |
---|---|
Uniform distribution | Even stress |
Avoid weak areas | Prevent damage |
Calculating Ejection Force
Ejection force depends on factors like clamping force and friction between plastic and mold material. It can be theoretically calculated or estimated from empirical data. General force range is 0.5-3.0 kN/cm², adjustable for special materials or complex shapes.
Calculating ejection force accurately ensures smooth product release without deforming or damaging it during production. Guide device designs3 and reset mechanisms are essential for reliable mold operation.
Complex shapes require multiple ejection methods.True
Complex shapes often have features like ribs, needing varied ejection techniques.
Polypropylene has a low shrinkage rate.False
Polypropylene is known for its high shrinkage rate, affecting ejection design.
What Are the Different Methods of Ejection in Injection Molding?
Have you ever wondered how those intricate plastic parts pop out of their molds so perfectly?
Injection molding utilizes ejection methods such as push rod, push tube, push plate, and molded part ejection, customized to product specifications for smooth, damage-free removal.
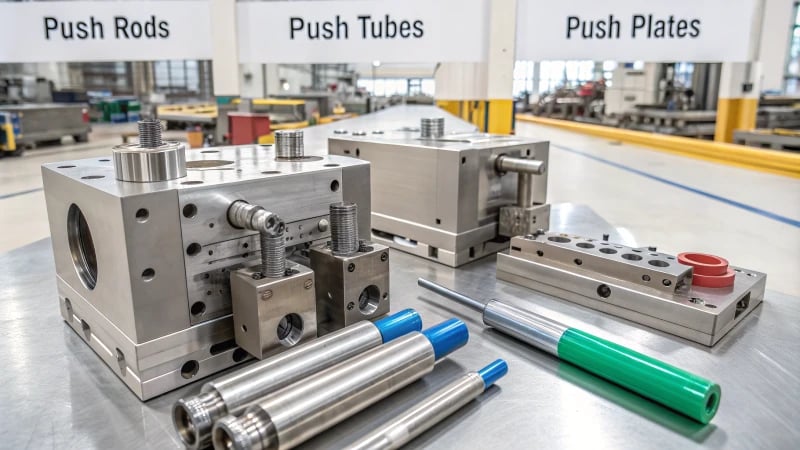
Push Rod Ejection
Imagine you’re crafting something simple yet essential, like a bottle cap. Push rod ejection is like giving it a gentle nudge to slip out of its mold. It’s straightforward and budget-friendly, perfect for regular-shaped items. But like giving a pat on the back, sometimes it leaves a mark.
Advantages:
- Cost-effective
- Suitable for regular shapes
Disadvantages:
- May leave marks on products
Push Tube Ejection
Think about holding a plastic pen barrel and realizing it’s crafted with precision. The push tube method is a master at this, hugging the contours just right to ensure it maintains its shape and look.
Advantages | Disadvantages |
---|---|
Ensures accuracy | More complex design |
Protects appearance | Limited application |
Examples include plastic pen barrels4.
Push Plate Ejection
For larger, delicate items like those big plastic pallets, push plate ejection is a lifesaver. It’s like using a gentle hand to make sure everything stays in shape without a single scratch.
Advantages:
- Uniform stress distribution
- No surface marks
Perfect for applications such as large plastic pallets5.
Ejection Using Molded Parts
Sometimes the mold itself lends a helping hand. It’s like your favorite pair of shoes that perfectly fit and guide your feet. This method works wonders with complex designs, using the mold’s movements to ease the product out.
Advantages:
- Utilizes existing mold movements
- Ideal for complex designs
Effective in molds with side core pulling mechanisms6.
Considerations in Ejection Method Selection
Choosing how to eject a product from its mold isn’t just technical; it’s almost an art. It’s about understanding the nuances of your product’s shape, size, and what it’s made of. Some materials shrink significantly, affecting the choice of ejection technique to avoid deformation during ejection7. Sometimes, blending methods is the key to getting that flawless finish. Each choice impacts quality and efficiency—so it’s always a balance between science and intuition.
Push rod ejection is cost-effective for regular shapes.True
Push rod ejection is simple, cost-effective, and suitable for regular shapes.
Push plate ejection may leave marks on the product surface.False
Push plate ejection prevents surface marks due to uniform stress distribution.
How do I determine the best ejection position in a mold?
Ever wondered how to perfect the ejection process in mold design? It’s an art, balancing precision with practicality, and it can make or break the quality of your final product.
To determine the best ejection position in a mold, analyze the product’s shape, size, and material properties for uniform stress distribution, avoid weak spots, and ensure compatibility with shrinkage and the ejection method.
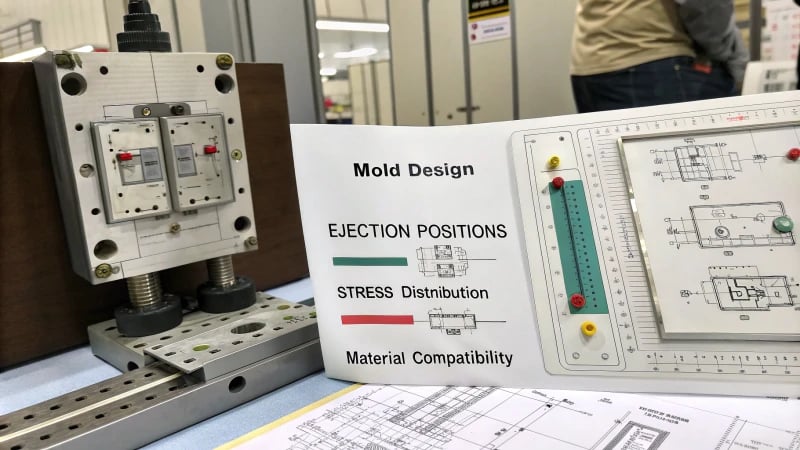
Analyzing Product Characteristics
I remember my first major project, where understanding the geometric shape8 and size of a product was crucial. It was like solving a puzzle where each piece had to fit perfectly. Products with simple shapes gave me the freedom to experiment with ejection methods, whereas complex designs demanded a more strategic approach. For instance, handling a large part with deep holes taught me how critical it is to prevent damage during ejection.
Equally important were the material properties. Working with polypropylene (PP), known for its high shrinkage rate, required me to factor in potential clamping force changes. Selecting the right ejection position was essential to maintain the product’s integrity and avoid deformation.
Choosing the Appropriate Ejection Method
- Push Rod Ejection: This was my go-to for many projects. Simple and effective, it suited most regular-shaped products without special undercuts.
- Push Tube Ejection: I found this ideal for cylindrical items, like pen barrels, where maintaining appearance quality was non-negotiable.
- Push Plate Ejection: Perfect for thin-walled, flat products, it ensured no marks on surfaces—a trick I learned while designing plastic pallets.
Here’s a comparison table for quick reference:
Method | Suitable For | Example Application |
---|---|---|
Push Rod | Regular shapes | Bottle cap molds |
Push Tube | Cylindrical with central holes | Pen barrel molds |
Push Plate | Large, flat surfaces | Plastic pallet molds |
Strategic Ejection Positioning
The principle of uniform distribution became my mantra to minimize stress during ejection. Whether working on circular products or those with unique contours, arranging points evenly was key to balance. Avoiding weak parts like thin walls or reinforcing ribs helped prevent damage during the ejection phase.
For materials prone to shrinkage, determining ejection positions that accommodate post-shrinkage was vital for smooth demolding. Understanding shrinkage deformation9 dynamics was something I couldn’t overlook.
Calculating Ejection Force
Calculating the ejection force felt like a delicate balancing act. While theoretical methods provided a framework—considering factors like clamping force and friction coefficients—empirical data often guided me to fine-tune these calculations. Adjustments were particularly necessary for unique materials or complex shapes.
Integrating Ejector Mechanisms with Mold Components
Designing guide devices for stability and ensuring seamless resets were challenges I embraced. Synchronizing ejector mechanisms with cooling and core pulling systems was like choreographing a dance, where each step had to be perfectly timed to avoid interference and enhance overall mold performance. Understanding ejector mechanism10 dynamics was crucial, especially during actions like side core pulling.
Push rod ejection is suitable for cylindrical products.False
Push tube ejection, not push rod, is ideal for cylindrical products.
Uniform distribution minimizes stress during ejection.True
Evenly distributed ejection points reduce stress and prevent damage.
What Factors Influence the Calculation of Ejection Force?
Ever wondered how to ensure a smooth release of products from a mold without any damage? Understanding the ejection force is key to achieving that.
Ejection force is influenced by material properties, mold design, and product geometry. Optimizing these factors improves production efficiency and minimizes defects.
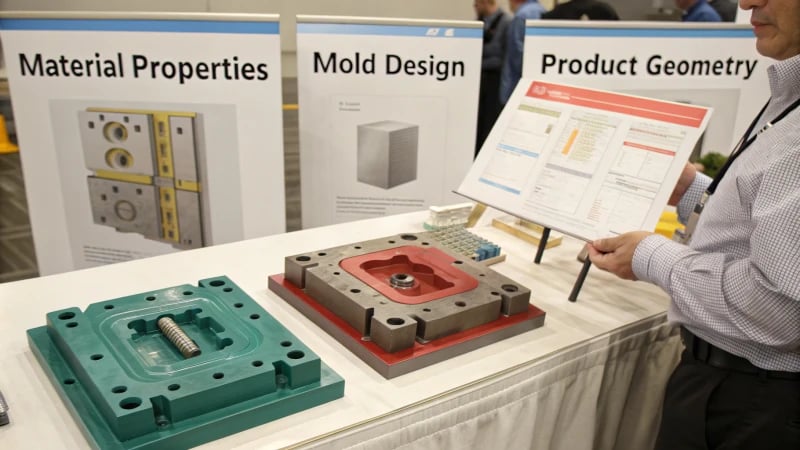
Material Properties
The plastic’s traits are like the foundation of a house when it comes to ejection force. I remember the first time I worked with polypropylene (PP), which has a high shrinkage rate. It was a learning curve, adjusting for the clamping forces11 created by its shrinkage. The rigidity of the material, or its elastic modulus, was another revelation—who knew that would play such a pivotal role?
Product Geometry
Geometry might have been a high school nightmare, but in mold design, it’s crucial. Simple shapes are a breeze, but throw in some ribs or undercuts, and it’s a whole new ball game. I once worked on a project with deep holes—it was like navigating a minefield to avoid damaging those delicate walls.
Geometry Type | Ejection Method | Considerations |
---|---|---|
Simple | Push rod | Flexible options |
Complex | Multiple methods | Risk of damage |
Deep hole | Specialized method | Wall integrity |
Mold Design
Designing the ejector mechanism was like piecing together a puzzle. I had to pick the right ejection method12—be it push rod, push tube, or push plate—depending on what the product needed. Ensuring even stress distribution was another task; uneven stress can be the silent assassin of your product’s integrity.
Operational Conditions
Temperature and cooling time13 aren’t just fancy terms—they can make or break your ejection force calculations. I recall having to sync up with other mold mechanisms like core pulling, ensuring everything worked like a well-oiled machine.
Calculation Methods
Whether you’re using theoretical formulas or empirical data, each method has its charm. Theoretical calculations consider projected area and material shrinkage rates, while empirical methods rely on historical data14. It’s fascinating how adjusting these figures can optimize mold efficiency and product quality without causing unnecessary wear on machinery.
Materials with high shrinkage need more ejection force.True
High shrinkage materials exert clamping forces, increasing ejection needs.
Simple shapes require more force than complex geometries.False
Simple shapes typically need less force; complex ones need more.
How can I ensure proper coordination between the ejection mechanism and other mold parts?
Have you ever thought about the intricate dance of mold parts working together to create perfect plastic products?
Ensure proper coordination by analyzing product characteristics, selecting suitable ejection methods, calculating ejection force, and designing compatible components. Balance cooling systems and core pulling mechanisms with ejection operations for seamless mold functionality.
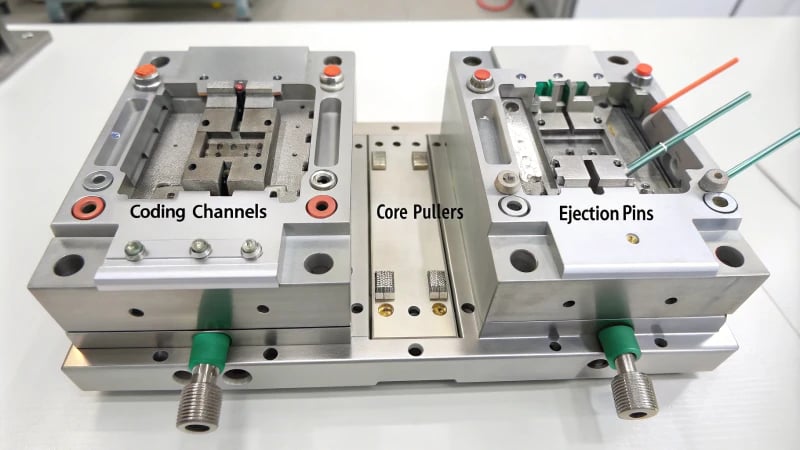
Analyzing Product Characteristics
I remember my first project where understanding the product’s shape and material was a game-changer. I was dealing with a complex item full of ribs and undercuts. Back then, I realized that for such intricate designs, multiple ejection methods were essential. For instance, polypropylene’s shrinkage taught me to be meticulous about selecting the right ejection methods15 to prevent damage during demolding.
Choosing Suitable Ejection Methods
Different products call for different ejection techniques, something I learned on the job:
- Push Rod Ejection: Perfect for regular shapes.
- Push Tube Ejection: Best for cylindrical products.
- Push Plate Ejection: Used for thin-walled items without visible marks.
Ejection Method | Application |
---|---|
Push Rod | Regular shapes |
Push Tube | Cylindrical products |
Push Plate | Thin-walled products |
Calculating Ejection Force
Getting the ejection force right was another lesson from my early days. Theoretical calculations combined with empirical values based on product area and material shrinkage helped me fine-tune this skill. For special plastics with high shrinkage, adjustments are necessary, ensuring effective demolding.
Structural Design of Ejector Mechanism
Designing the ejector mechanism requires precision. Guide pins and sleeves offer stability and accuracy, something I’ve relied on heavily. Whether it’s using reset rods or springs, efficient resetting post-ejection is vital for seamless operations.
Coordinating with Cooling Systems
Avoiding interference between the ejector mechanism and cooling components is crucial. I always ensure both systems respect each other’s space to maintain cooling efficiency while still allowing room for the ejector’s operation.
Synchronizing Core Pulling Mechanisms
In molds with side core pulling, ensuring the ejector works post-core pulling is key to avoiding clashes. Especially with inclined sliders doubling as core pullers and ejectors, thoughtful design is essential.
Understanding these elements has been invaluable in my journey to achieving flawless coordination in molds. Every project taught me something new, enhancing product quality and production efficiency. With each mold, my goal is to harmonize all these components seamlessly.
Push rod ejection is best for thin-walled products.False
Push plate ejection is suitable for thin-walled products, not push rod.
Ejection force typically ranges from 0.5-3.0kN per cm².True
The typical ejection force range mentioned is 0.5-3.0kN per cm².
What Mistakes Should I Avoid in Ejector Mechanism Design?
Imagine spending hours perfecting a design only to have it crumble due to overlooked details. Avoid these common pitfalls in ejector mechanism design for smoother manufacturing.
Avoid mistakes in ejector mechanism design by considering product characteristics, choosing the correct ejection method, accurately placing ejection points, calculating force correctly, and ensuring sound structural design for enhanced quality and efficiency.
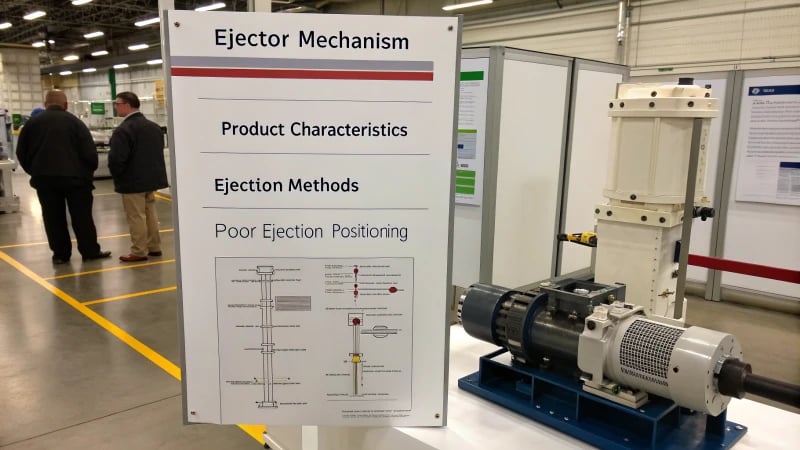
Analyzing Product Characteristics
Reflecting on my early days in design, I recall underestimating how crucial product characteristics are. The shape and size16 can dictate everything—like how a complex shape might need multiple ejection methods. I learned the hard way with a polypropylene product; its high shrinkage rate caught me off guard, clamping it tight during ejection. Now, I always consider material properties17 like shrinkage to avoid these hiccups.
Choosing the Right Ejection Method
There was this one time I thought a push rod would work for an intricate design—it left marks and deformed parts, a rookie mistake. Now, I know that for things like pen barrels, a push tube18 works wonders. It’s about matching the method to the product—like a puzzle piece.
Ejection Method | Suitable For | Example |
---|---|---|
Push Rod | Regular shapes | Bottle caps |
Push Tube | Cylindrical shapes | Pen barrels |
Push Plate | Thin-walled surfaces | Plastic pallets |
Determining the Ejection Position
I used to think placement was just about convenience, but once I placed ejectors near thin parts and ended up with broken pieces, I changed my approach. Now, I distribute them evenly and consider shrinkage deformation19 to ensure uniform stress.
Calculating the Ejection Force
Calculating force was my nemesis. Too little, and parts stuck; too much, and they broke. Using a blend of theoretical and empirical methods has saved me from many headaches. Clamping force and friction coefficients are now my go-tos.
Structural Design Errors
Early on, my designs had guide pins that misaligned after repeated use—talk about frustrating! Ensuring robust guide devices like pins and sleeves helps maintain stability and precision, preventing resetting issues20.
"A well-coordinated ejector mechanism minimizes defects and enhances productivity," says an industry expert.
Coordination with Other Mold Parts
I remember overlooking the interaction between the ejector mechanism and cooling systems—bad idea. It caused interference, affecting efficiency. Now, I ensure seamless integration with other mold components to maintain integrity and performance.
These insights have not only refined my designs but also significantly boosted efficiency and product quality. Addressing these common pitfalls has been a game-changer in my projects.
High shrinkage materials need careful ejection planning.True
Materials like polypropylene require careful planning to avoid clamping forces.
Push rods are ideal for intricate product designs.False
Push rods can leave marks on intricate designs; other methods are better.
Conclusion
Effective ejection mechanism design in injection molding requires analyzing product characteristics, selecting appropriate methods, calculating forces, and ensuring coordination with other mold components for optimal performance.
-
Explore diverse ejection techniques suitable for various plastic shapes and sizes to optimize your design process. ↩
-
Learn how shrinkage affects mold design and how to mitigate its effects on product quality. ↩
-
Discover strategies for designing effective guide devices to enhance mold stability and precision. ↩
-
Understand how push tube ejection maintains product accuracy. ↩
-
Explore the benefits of push plate ejection for large products. ↩
-
Discover how molded parts aid complex design ejections. ↩
-
Learn about handling PP’s shrinkage during ejection. ↩
-
Exploring this link helps in understanding how product shape influences ejection method selection. ↩
-
This link explains how shrinkage affects mold design choices and ensures effective ejection. ↩
-
Understanding guide devices enhances stability and precision in ejector mechanism designs. ↩
-
Explores how clamping forces due to material shrinkage impact the necessary ejection force. ↩
-
Details different ejection mechanisms and their applications in mold design. ↩
-
Examines how cooling duration influences material properties and ejection requirements. ↩
-
Discusses the use of historical data to determine ejection force adjustments. ↩
-
Learn about various ejection methods to choose the most suitable one for different plastic product designs. ↩
-
Understanding shape and size helps prevent damage during ejection, ensuring a defect-free product. ↩
-
Different materials behave differently during ejection; understanding these properties ensures proper design. ↩
-
Choosing the right method prevents product deformation and improves efficiency. ↩
-
Considering shrinkage ensures smooth demolding without defects. ↩
-
Proper resetting is crucial for continuous operation without errors. ↩