At the beginning of my path in product design, I soon discovered an important lesson. Picking the right plastic for molding is not just technical. It’s a crucial choice that probably decides the success or failure of a project. Let’s explore this important topic together!
Selecting the best plastic for molding involves understanding the unique qualities of options like polyethylene, polypropylene, polystyrene, PVC, and polycarbonate. This ensures you choose the right material for your project’s specific needs.
This guide provides insights into the details of each plastic type. These materials improve not only designs but also simplify manufacturing steps. Discover with me the thrill of transforming a basic idea into a market-ready product using various plastics. Different plastics such as polyethylene and polycarbonate play a crucial role. Explore these materials to see how they fit into your next big idea.
Polyethylene is the best plastic for all molding applications.False
This claim is false as polyethylene has specific advantages but may not suit every application.
Understanding plastic types enhances design and manufacturing success.True
This claim is true; knowing material properties aids in making informed choices for projects.
- 1. What Are the Key Properties to Consider in Plastic Molding?
- 2. How Do Different Plastics Compare in Terms of Cost and Performance?
- 3. What Are the Environmental Impacts of Using Various Plastics?
- 4. How Can Additives Enhance the Performance of Molding Plastics?
- 5. What Are Common Applications for Each Type of Plastic?
- 6. How Do I Choose the Right Plastic for My Specific Project?
- 7. Conclusion
What Are the Key Properties to Consider in Plastic Molding?
Selecting suitable materials for plastic molding might seem confusing. However, knowing the main characteristics is crucial for products to work well. What should you remember when starting this journey?
Key properties in plastic molding include mechanical strength, thermal resistance, chemical durability, processing characteristics, and dimensional stability, ensuring long-lasting and effective product performance.
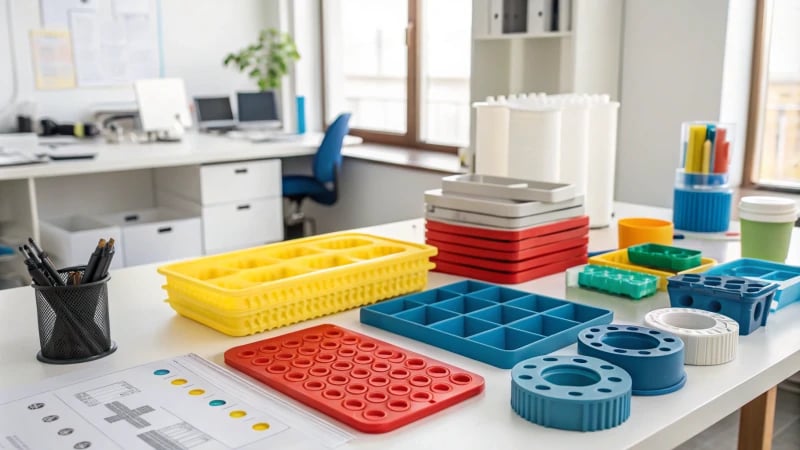
When selecting materials for plastic molding, particularly in injection molding, it’s crucial to understand key properties that influence the performance of the final product. Let’s delve into some essential properties:
1. Mechanical Properties
Mechanical properties such as tensile strength, impact resistance, and flexibility are vital in determining how a molded part will perform under various conditions. For instance, Polycarbonate (PC) is renowned for its high impact resistance and toughness, making it suitable for applications requiring durability. In contrast, Polystyrene (PS) offers good rigidity but is more brittle.
Property | Polycarbonate (PC) | Polystyrene (PS) |
---|---|---|
Impact Resistance | High | Low |
Tensile Strength | Moderate | Moderate |
By evaluating these properties, designers can optimize their material selection to ensure longevity and functionality in their products.
2. Thermal Properties
Thermal resistance is another critical aspect to consider. Materials like Polypropylene (PP) exhibit good heat resistance, allowing them to withstand higher temperatures without deforming. This is particularly useful in automotive applications where parts may be exposed to heat.
Conversely, Polyvinyl Chloride (PVC) has a narrower thermal stability range and requires careful temperature control during processing to prevent decomposition.
3. Chemical Resistance
Chemical durability plays a significant role in the longevity of molded products. For example, Polyethylene (PE) shows excellent chemical resistance, making it ideal for containers and pipes that hold corrosive substances.
Material | Chemical Resistance | Typical Applications |
---|---|---|
PE | Excellent | Films, pipes |
PP | Good | Automotive parts |
PVC | Moderate | Pipes, window profiles |
Understanding the chemical compatibility of materials ensures that the final products can withstand the environments they will be exposed to.
4. Processing Characteristics
The ease of processing is also essential when selecting materials for molding. For instance, Polyethylene (PE) has good fluidity, allowing it to fill molds easily during the injection process.
This trait is crucial for creating complex shapes with high dimensional accuracy. Here’s a comparison of some materials:
Material | Fluidity | Molding Process | Requirements |
---|---|---|---|
PE | High | Injection, Extrusion | Low equipment demands |
PS | Moderate | Injection | General equipment use |
PVC | Variable | Injection, Extrusion | Thermal stability needed |
Each material has specific requirements and characteristics that influence processing efficiency and product quality.
5. Dimensional Stability
Lastly, dimensional stability is a key factor that affects the quality of molded products over time. Materials like HDPE (High-Density Polyethylene) demonstrate excellent dimensional stability due to their low shrinkage rates during cooling. This property is essential in applications where precision is critical, such as in consumer electronics housings.
In contrast, materials with higher shrinkage rates may result in warping or deformation after cooling, impacting product integrity and fit.
By considering these properties—mechanical performance, thermal resistance, chemical durability, processing characteristics, and dimensional stability—designers can make informed decisions that lead to successful plastic molding outcomes. For further insights into material selection and design considerations, explore our comprehensive guides on plastic molding properties1. I hope these tips help you too!
Polycarbonate has high impact resistance compared to Polystyrene.True
Polycarbonate (PC) is known for its superior impact resistance, making it more durable than Polystyrene (PS), which has lower impact resistance.
Thermal properties are irrelevant in plastic molding material selection.False
Thermal properties significantly influence material performance, making them crucial for applications exposed to heat, contradicting the claim that they are irrelevant.
How Do Different Plastics Compare in Terms of Cost and Performance?
Exploring the world of plastics often feels confusing and difficult. Understanding how different plastics compare in terms of price and performance is very important for design projects. Let’s dive in together!
Polyethylene is affordable and flexible, while polycarbonate is more expensive but highly durable. Choose the type of plastic based on your specific needs and budget.
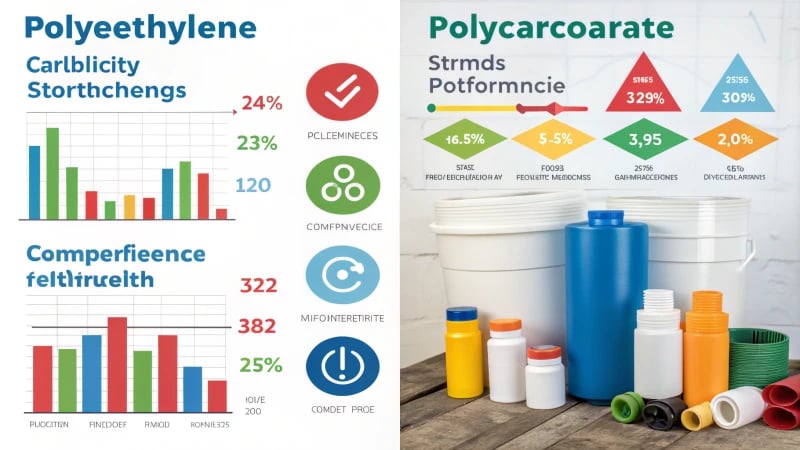
Main Content:
Over the years, I have struggled to choose the right materials for design. It feels overwhelming to go through all the options. I remember the first time I had to select a plastic for a project. There were many factors to think about! After careful thought and some mistakes, I understood that knowing about cost and performance mattered a lot for choosing correctly.
Let’s explore this together, shall we? Here’s a look at how different plastics compare, along with their unique qualities and strengths.
Cost Comparison of Common Plastics
When evaluating plastics, the cost is often a primary factor influencing material selection. Here’s how some of the most common plastics stack up:
Plastic Type | Cost (per kg) | Applications |
---|---|---|
Polyethylene (PE) | $1.00 – $1.50 | Bags, films, containers |
Polypropylene (PP) | $1.20 – $1.80 | Automotive parts, packaging |
Polystyrene (PS) | $1.50 – $2.00 | Packaging, toys, insulation |
Polyvinyl Chloride (PVC) | $1.30 – $2.50 | Pipes, flooring, electrical applications |
Polycarbonate (PC) | $2.00 – $3.50 | Optical lenses, electronic housings |
As we can see from the table, Polyethylene tends to be the least expensive option while Polycarbonate is on the higher end due to its advanced properties. The cost factors in raw material prices, processing techniques, and market demand.
Performance Characteristics
Cost is important but not the only thing to consider! Performance traits of plastics affect how well your project goes. Each type offers something unique:
Polyethylene (PE)
- Flexibility & Chemical Resistance: PE bends and stretches easily and resists chemicals well; it’s really great for flexible products.
- Crystallinity Variance: PE changes with density; LDPE is soft and suits films while HDPE is stronger and perfect for pipes.
Polypropylene (PP)
- High Strength & Heat Resistance: PP is strong and handles heat well; I often use it for durable but light projects.
- Lightweight: Its lightweight nature keeps designs efficient; this is crucial in car parts where every ounce matters.
Polystyrene (PS)
- Optical Clarity: Need clear materials? PS is amazing for displays with its clear and shiny surface.
- Electrical Insulation: It insulates well making it suitable for electrical casings.
Polyvinyl Chloride (PVC)
- Dual Nature: PVC can be hard or soft; I love using it for both sturdy pipes and flexible cables.
- Chemical Corrosion Resistance: In its hard form PVC resists chemicals effectively making it trustworthy in many situations.
Polycarbonate (PC)
- Impact Resistance: When safety is a worry PC stands out for its toughness; it’s perfect for protective gear.
- Dimensional Stability: PC holds its shape well under stress which is vital for precise parts; I trust its dependability.
Molding Advantages
Molding capabilities also play a significant role in choosing the right plastic. Here’s a brief comparison of their molding advantages:
Plastic Type | Molding Process Efficiency | Molding Temperature | Dimensional Stability |
---|---|---|---|
Polyethylene (PE) | High | Low | Good |
Polypropylene (PP) | Very High | Moderate | Excellent |
Polystyrene (PS) | Excellent | Wide range | Good |
Polyvinyl Chloride (PVC) | Moderate | Requires control | Moderate |
Polycarbonate (PC) | Good | High | Excellent |
i noticed that Polystyrene and Polypropylene mold efficiently while keeping shape stability; I value this greatly when crafting complex designs.
Conclusion of Insights
in looking at plastics I learned that knowing cost and performance differences heavily affects design choices; each type gives distinct benefits suited to specific uses. Curious about their environmental effects? Check out sustainability in plastics2.
Polyethylene is the least expensive plastic option available.True
Polyethylene (PE) costs between $1.00 - $1.50 per kg, making it the most affordable plastic.
Polycarbonate offers low impact resistance compared to other plastics.False
Contrary to this claim, polycarbonate is known for its excellent impact resistance, making it suitable for safety applications.
What Are the Environmental Impacts of Using Various Plastics?
I see more and more plastic around me. I feel both worried and urgent. The environmental effects are not just numbers. They affect all of us deeply. Wildlife suffers because of plastic. Ecosystems experience harm. Even our health is at risk.
The environmental impacts of plastics include long-lasting ecosystem presence, threats to wildlife through ingestion or entanglement, and health risks from harmful chemical releases. Understanding these effects aids in making informed, eco-friendly choices.
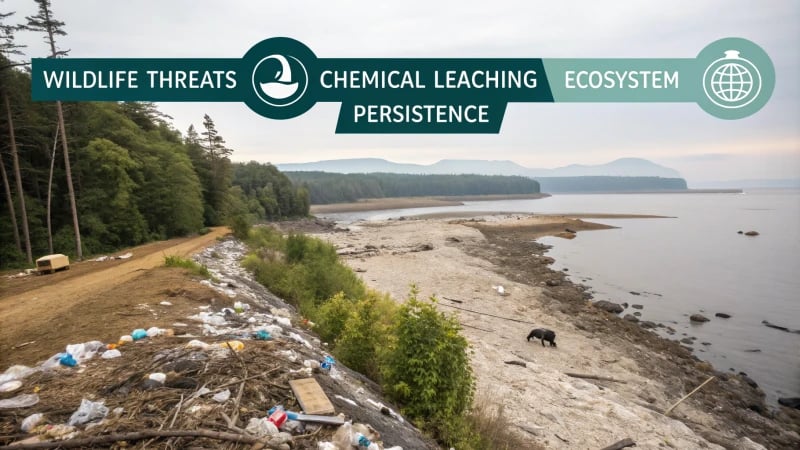
The Persistence of Plastics in the Environment
Here is a story. I once walked along a beach I used to visit when I was a child. The sand remained beautiful, but I noticed the litter – so much plastic washed ashore. It’s really haunting to think that many of these plastics will stay there for centuries.
Plastics are known for their strength. While this makes them very useful, it also means they last much longer than we like. For example, polyethylene (PE), which I used in different designs, stays in landfills for 100 to 500 years. Consider how much plastic has collected since I was young!
In our oceans, these plastics become tiny pieces called microplastics. Fish and marine animals eat them easily. I often think whether the seafood I eat has parts of this pollution. It’s a really sobering thought.
For more insights on this topic, check out microplastics impact3.
Effects on Wildlife
The impact on wildlife is truly heartbreaking. I watched a documentary about sea turtles. These beautiful animals often confuse plastic bags for jellyfish, which leads to poor health or even death. Birds also suffer; some feed their chicks plastic instead of nutritious food. This is not just about numbers; it’s about lives lost because of our actions.
Table: Common Wildlife Affected by Plastic Pollution
Species | Type of Impact | Example of Plastic Ingestion |
---|---|---|
Sea Turtles | Malnutrition/Death | Plastic bags |
Birds | Starvation/Choking | Bottle caps and straws |
Marine Mammals | Entanglement | Fishing nets |
Fish | Digestive Issues | Microplastics |
For further details on animal impacts, visit plastic effects on wildlife4.
Human Health Risks
It’s easy to miss how plastic pollution affects us. Chemicals leak from plastics into our food and water, posing serious health threats. I read studies that show polyvinyl chloride (PVC) releases harmful substances linked to health issues. This makes me think again about the plastic containers I use every day.
Microplastics have even appeared in our drinking water and human stools! It raises deep worries about what we eat without knowing. I want a healthy future for myself and my loved ones.
For more information on human health risks, see health risks from plastics5.
Solutions and Alternatives
Knowing the impacts of plastic isn’t just about regretting. It opens ways for solutions! Many companies now look into bioplastics or other materials to lessen the use of petroleum-based plastics.
I have seen how useful recycling programs are in cutting waste that reaches landfills and oceans. Each time I recycle a plastic item properly, I feel that I contribute a small but meaningful effort.
Another thrilling area is biodegradable plastics. These materials promise to keep the benefits of conventional plastics while reducing environmental harm significantly. I hope to see more innovations in this field. This is a step towards a brighter and more sustainable future.
For innovative solutions and more information, check out biodegradable alternatives6.
Plastic waste can take up to 500 years to decompose.True
Many plastics, like polyethylene, persist in landfills for centuries, contributing to environmental pollution.
Microplastics have been found in human drinking water.True
Research indicates that microplastics contaminate drinking water, posing potential health risks to humans.
How Can Additives Enhance the Performance of Molding Plastics?
Do you ever think about how simple plastics turn into high-quality materials? The world of additives is fascinating. Additives change regular plastics into something much better. They really improve the quality of molded plastics.
Additives enhance molding plastics by boosting strength, flexibility, and heat stability, allowing product customization and optimizing performance. They also improve manufacturing processes.
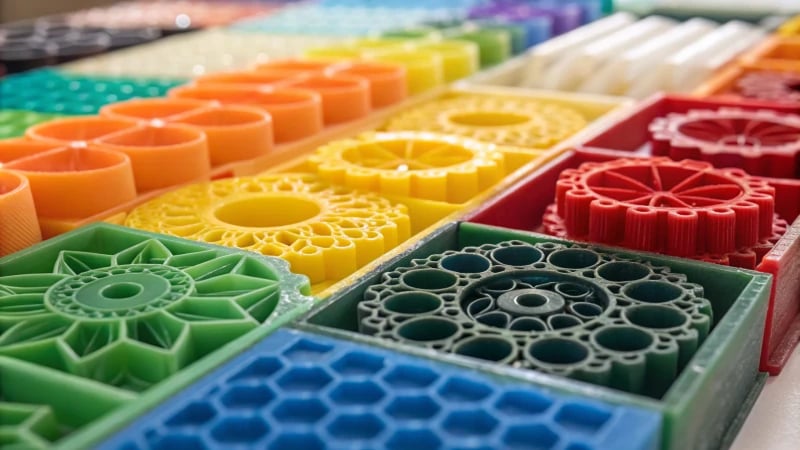
Understanding Additives in Molding Plastics
Additives are like secret ingredients in a recipe. They improve molding plastics in amazing ways, enriching strength, flexibility, and heat stability to meet specific needs. As a designer, I see how additives change projects, leading to better product performance and more efficient production.
Here are some main types of additives:
- Fillers: Increase strength and lower costs. They are common in many mixes.
- Plasticizers: Want more flexibility? These help make processing smoother.
- Stabilizers: Protect materials from damage during processing – essential!
- Colorants: Make products look attractive and match brand identity.
For example, adding glass fibers as fillers in Polypropylene (PP) significantly improves its strength, allowing for the molding of more robust automotive parts and home appliance housings. This versatility can be explored further in material enhancement techniques7.
Performance Characteristics of Common Plastics
Every plastic type has special qualities that can be enhanced through additives. Below is a comparison of some common plastics:
Plastic Type | Key Performance Characteristics | Molding Advantages |
---|---|---|
Polyethylene (PE) | Good flexibility, chemical resistance, variable crystallinity | Excellent flow, low melting point, dimensional stability |
Polypropylene (PP) | High strength, lightweight, good fatigue resistance | Fast cooling, customizable with additives |
Polystyrene (PS) | High rigidity, brittle, good optical clarity | Quick filling of molds, low melt viscosity |
Polyvinyl Chloride (PVC) | Strong chemical resistance; flexible or rigid based on plasticizers | Versatile molding processes; strong plasticity |
Polycarbonate (PC) | High impact resistance; excellent toughness | High precision molding; stable performance |
Understanding these characteristics can guide designers like me in selecting the right additives for specific applications. For deeper insights on molding techniques, check out advanced molding strategies8.
The Role of Additives in Process Optimization
Additives don’t just boost product performance; they also enhance the entire injection molding process. Here are some examples:
- Processing aids: Speed up production by improving flow and reducing mold friction.
- Antiblock agents: Keep film layers from sticking together. This saves many problems!
- Heat stabilizers: Necessary for materials like PVC to keep them stable during heat.
Using these additives allows manufacturers to enhance production efficiency and product quality. Explore optimization methods9 to learn more about improving your processes.
Conclusion: The Future of Additives in Molding Plastics
Our industry is growing alongside the rising need for high-performance plastics. Additives will become even more important as new ideas expand what we can do with ordinary materials. They will fit into more applications than ever before. It is time to keep pushing boundaries forward while considering ongoing developments at emerging trends in plastic additives10.
Additives can improve the strength of molding plastics.True
Incorporating additives like fillers enhances the mechanical strength of plastics, making them suitable for demanding applications such as automotive parts.
Plasticizers make plastics more rigid and brittle.False
Plasticizers are used to increase flexibility in plastics, not rigidity, allowing for better processability and usability in various applications.
What Are Common Applications for Each Type of Plastic?
Did you ever think about why certain plastics are used for specific things? Let’s explore the intriguing world of plastics. We will discover the interesting reasons behind their use.
Different plastics serve distinct purposes: polyethylene is used for bags and containers due to its flexibility, while polypropylene is employed in car parts for its strength. Understanding these applications aids in selecting appropriate materials.
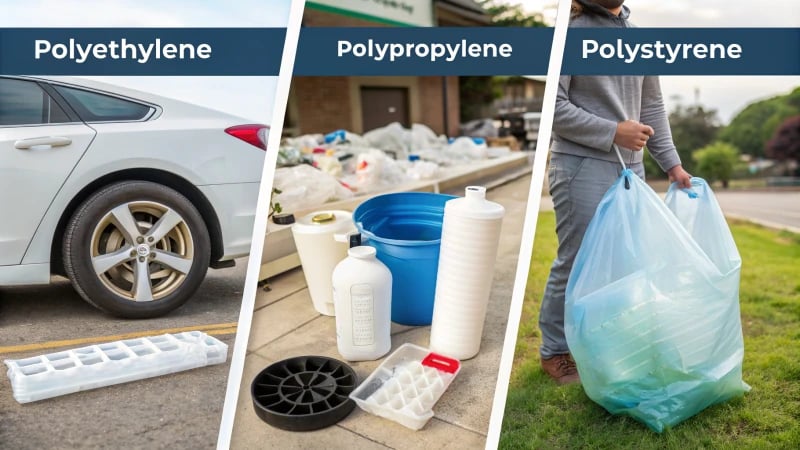
Common Uses of Polyethylene (PE)
Polyethylene feels like a dependable friend. Its adaptability makes it one of the most commonly used plastics in daily life.
Low-Density Polyethylene (LDPE)
- Uses: I remember packing lunches in soft, flexible plastic bags. LDPE is commonly used for plastic bags, cling films and different packaging materials. It is flexible and resistant to chemicals.
- Characteristics: Softness and transparency allow LDPE to fit various shapes. It’s perfect for packaging.
High-Density Polyethylene (HDPE)
- Uses: When thinking about strength, HDPE stands out. This robust plastic is found in pipes, detergent bottles and crates. These products are essential for everyday tasks.
- Characteristics: HDPE’s high strength and resistance to impact and moisture make it suitable for outdoor use, like construction materials that last long.
Common Uses of Polypropylene (PP)
Polypropylene resembles a strong yet light partner.
Uses
- Packaging: I often choose food containers made from PP. Widely used in food packaging, it keeps meals fresh.
- Automotive Parts: It’s intriguing to see how PP is used for car interiors and bumpers. This material is very durable. It resists wear and tear well.
Common Uses of Polystyrene (PS)
Polystyrene brings memories of colorful birthday parties.
Uses
- Disposable Products: From disposable cutlery to picnic cups, PS plays a key role in gatherings. Its low cost and easy production make it popular.
- Insulation: PS is valuable in thermal insulation for buildings. It keeps homes cozy and energy-efficient. This benefit is truly significant.
Common Uses of Polyvinyl Chloride (PVC)
PVC resembles a chameleon. It adapts to different needs based on its form.
Hard PVC
- Uses: I value hard PVC for its strength. It is used in pipes, window frames and medical devices. These items are crucial yet often unnoticed in daily life.
Soft PVC
- Uses: Soft PVC stands out in electrical cable insulation, flooring and synthetic leather. Its flexibility and reliability greatly contribute to our safety.
Common Uses of Polycarbonate (PC)
Polycarbonate is a high-performance plastic with great resilience.
Uses
- Safety Glasses: I recall wearing safety goggles during work; PC is used for their production due to its high impact resistance. Safety gear is very important.
- Electronic Housings: Transparency and toughness make PC ideal for electronic housings. It protects gadgets while providing a sleek look.
Type of Plastic | Common Applications | Performance Characteristics |
---|---|---|
Polyethylene (PE) | Plastic bags, cling films, packaging | Flexible, chemical resistant |
Polypropylene (PP) | Food containers, automotive parts | Strong, lightweight |
Polystyrene (PS) | Disposable cutlery, insulation | Rigid, good optical clarity |
Polyvinyl Chloride (PVC) | Pipes, window frames, medical devices | Versatile, strong |
Polycarbonate (PC) | Safety glasses, electronic housings | High impact resistance, durable |
Exploring these materials might inspire you to consider their everyday use and the stories they tell. For more information on how these materials are changing in the industry, explore the latest trends in plastic material science11. These trends dive into new uses of plastics.
Polyethylene is commonly used for plastic bags and packaging.True
Polyethylene's flexibility and chemical resistance make it ideal for various packaging applications, including plastic bags and cling films.
Polystyrene is primarily used in automotive parts manufacturing.False
Polystyrene is not typically used in automotive parts; it's more common in disposable products and insulation applications.
How Do I Choose the Right Plastic for My Specific Project?
Picking the correct plastic for my projects often feels similar to a chef choosing just the right ingredients. One must grasp the details and choose wisely. Smart choices really improve the end result.
To choose the right plastic, assess flexibility, strength, and molding benefits, while considering project conditions and aesthetics. Follow applicable regulations for optimal results.
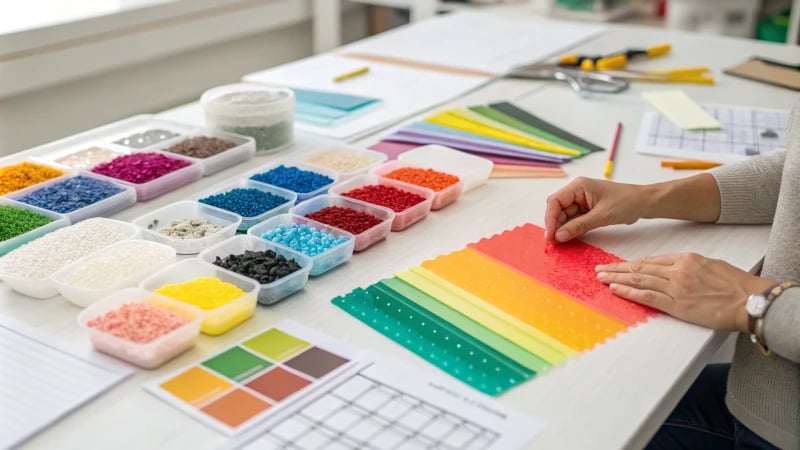
Choosing the right plastic for your specific project is crucial for ensuring optimal performance, durability, and cost-effectiveness. Here are several key factors to consider:
Performance Characteristics
Different types of plastics have unique properties that affect their suitability for various applications. For instance:
Plastic Type | Flexibility | Chemical Resistance | Strength | Heat Resistance |
---|---|---|---|---|
Polyethylene (PE) | Good (LDPE), Stiff (HDPE) | Excellent | Moderate | Low |
Polypropylene (PP) | Moderate | Good | High | Moderate |
Polystyrene (PS) | Brittle | Moderate | Moderate | Low |
Polyvinyl Chloride (PVC) | Flexible (soft), Rigid (hard) | Excellent | High | Low |
Polycarbonate (PC) | Very High | Good | Very High | High |
Molding Advantages
The molding process can greatly influence your choice of plastic. Each material has its own molding characteristics:
- Polyethylene (PE): Its good fluidity allows it to fill molds easily, making it ideal for complex shapes. The low melting point helps streamline the molding process.
- Polypropylene (PP): Known for its quick cooling time during injection molding, PP enhances production efficiency while allowing for customization with various additives to meet specific needs.
- Polystyrene (PS): Offers excellent fluidity, enabling detailed designs and shapes without significant mold wear.
- Polyvinyl Chloride (PVC): Versatile in molding processes; however, it requires careful temperature control to avoid decomposition during processing.
- Polycarbonate (PC): While it demands a higher processing temperature, it excels in replicating fine details and producing high-performance components.
Application Requirements
Understanding the end-use of your project can guide you towards the right material. Consider:
- Environmental Conditions: Will the plastic be exposed to harsh chemicals or high temperatures?
- Load-bearing Needs: Does the application require durability under repeated stress or weight?
- Aesthetic Qualities: Are transparency and gloss important for the final product?
For example, if you’re designing components for consumer electronics, exploring Polycarbonate12 could be beneficial due to its high strength and transparency.
Compliance and Regulations
Certain projects may require adherence to specific regulations regarding material safety and environmental impact. Ensure that the selected plastic complies with any applicable standards relevant to your industry.
- Food Safety: If your application involves food packaging, materials like Polypropylene might be more suitable due to their excellent resistance to chemicals and heat.
- Electrical Safety: For electrical applications, materials like Polystyrene with good insulating properties can be advantageous.
By carefully evaluating these factors, you can select the appropriate plastic that not only meets the functional requirements of your project but also optimizes production processes and regulatory compliance. Remember, each project is unique, so take the time to analyze your specific needs before making a decision.
Polycarbonate offers high strength and transparency for electronics.True
Polycarbonate is ideal for consumer electronics due to its exceptional strength and clarity, making it suitable for durable and aesthetically pleasing components.
PVC has excellent chemical resistance but low heat resistance.True
While PVC excels in resisting chemicals, it has a low tolerance for heat, which limits its applications in high-temperature environments.
Conclusion
This comprehensive guide discusses selecting the best plastic for molding by examining different types, their properties, applications, and key considerations for successful product design.
-
Discover a wealth of information on selecting the right materials for effective plastic molding processes. ↩
-
Explore deeper insights into the cost implications of various plastics and their performance metrics to make informed decisions. ↩
-
Discover how different plastics affect ecosystems and human health, providing valuable insights for informed decision-making. ↩
-
Explore the significant impact of plastic on wildlife and learn how it disrupts natural habitats. ↩
-
Learn about the health risks associated with plastic consumption and exposure in daily life. ↩
-
Find out about innovative materials that can replace traditional plastics for a more sustainable future. ↩
-
This link provides valuable insights into how different additives can improve specific plastic properties and processing techniques. ↩
-
Learn about the latest trends in additive technology that can revolutionize plastic manufacturing. ↩
-
Explore advanced techniques that optimize plastic injection molding processes for better efficiency. ↩
-
Stay updated on emerging trends in plastic additive innovations that may benefit your projects. ↩
-
Explore the versatile applications of polypropylene to enhance your knowledge for material selection. ↩
-
Discover expert insights on selecting the best plastic for your project to ensure functionality and compliance. ↩