In the intricate dance of injection molding, timing isn’t just important; it’s everything.
The best mold opening time in injection molding is determined by product characteristics, material type, process parameters, and mold design. Understanding these factors helps optimize cooling times and improve efficiency.
While knowing the primary factors is crucial, delving deeper into each element can unlock significant improvements in your manufacturing process. Let’s explore these factors in more detail to enhance your understanding and application.
Larger products require longer mold opening times.True
Larger products need extended cooling to prevent deformation during demolding.
How Does Product Size and Shape Affect Mold Opening Time?
Product size and shape are pivotal in determining the ideal mold opening time in injection molding.
Larger or complex-shaped products typically require longer mold opening times to prevent deformation, while thin-walled items cool faster and need shorter times.
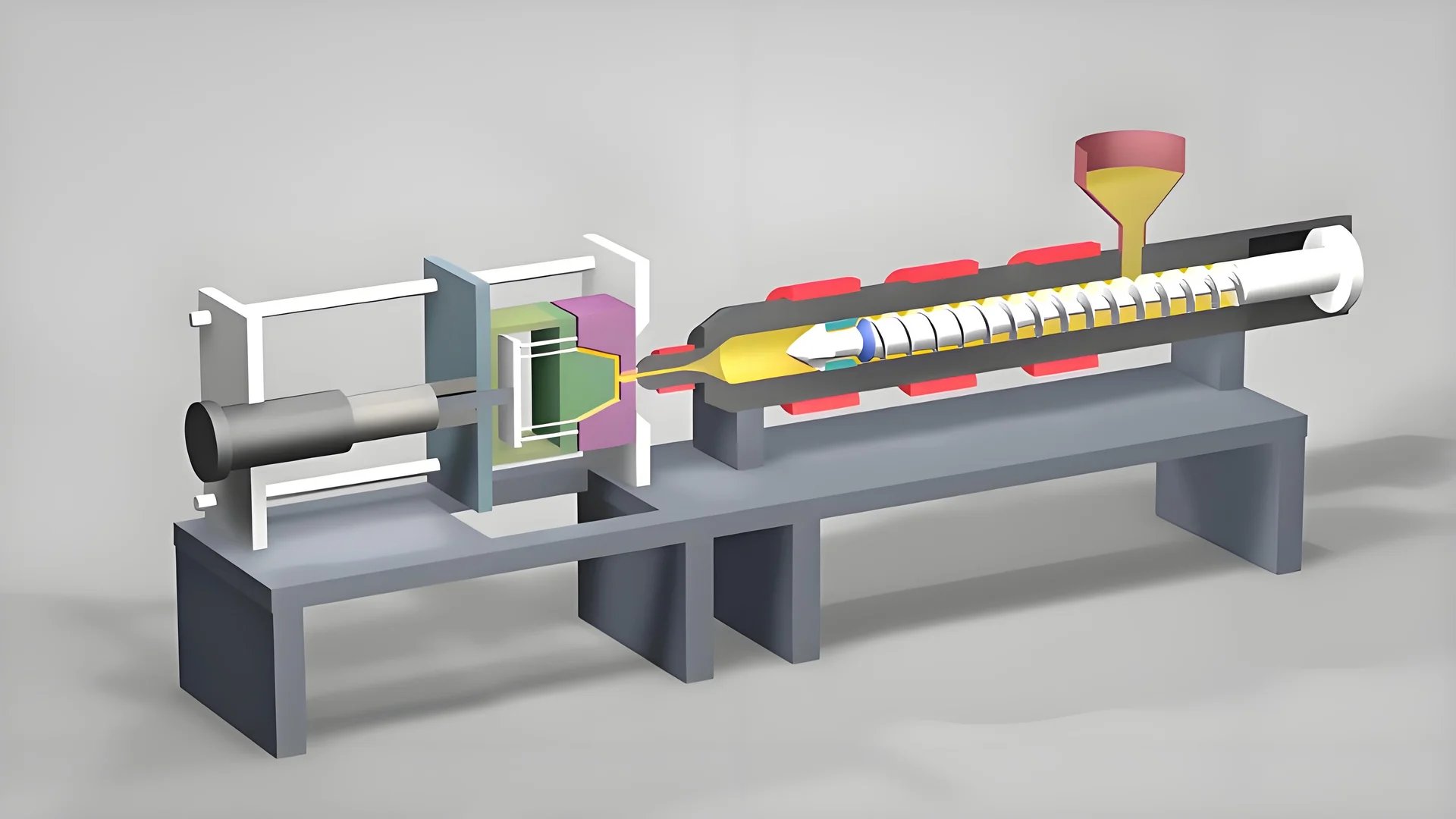
The Impact of Product Size on Mold Opening Time
The size of a product greatly influences its cooling rate and, subsequently, the mold opening time. Larger products, such as automotive parts, necessitate extended cooling periods to solidify properly. Without sufficient cooling, these products risk deforming or breaking during demolding. On the other hand, smaller items cool more rapidly, allowing for shorter mold opening durations. This difference is crucial in optimizing production cycles to maintain efficiency.
Product Type | Cooling Time Required | Mold Opening Time |
---|---|---|
Large automotive part | Long | Longer |
Small electronic part | Short | Shorter |
Influence of Product Shape on Mold Opening Time
The complexity of a product’s shape can significantly impact the mold opening time. Complex designs, such as those with intricate geometries or undercuts, generally require longer cooling periods. This ensures that all sections of the product have adequately solidified before the mold opens, preventing warping or damage.
Thin-walled products present a different challenge. Due to their fast cooling nature, they often require shorter mold opening times. However, if opened too soon, these products risk distortion. Striking a balance is key to maintaining high production quality without sacrificing speed.
Examples and Applications
-
Large Appliances: Components for large appliances often demand longer mold opening times due to their size. A refrigerator door panel must be cooled thoroughly to maintain its shape and strength during use.
-
Consumer Electronics: In contrast, thin-walled parts like smartphone casings cool quickly and should be demolded swiftly to prevent cycle time loss.
Understanding the nuances of product characteristics1 like size and shape allows manufacturers to tailor their mold opening strategies effectively. By doing so, they ensure both the integrity of their products and the efficiency of their production lines.
Larger products need longer mold opening times.True
Larger items cool slower, requiring more time to solidify properly.
Thin-walled items always need longer mold opening times.False
Thin-walled items cool faster, often needing shorter mold opening times.
Why Is Material Type Important for Determining Mold Opening Time?
Choosing the right material is crucial for setting the mold opening time in injection molding processes.
Material type impacts mold opening time due to its cooling characteristics. Crystalline plastics require longer cooling, whereas non-crystalline materials cool faster. Understanding these differences is essential for optimizing production.
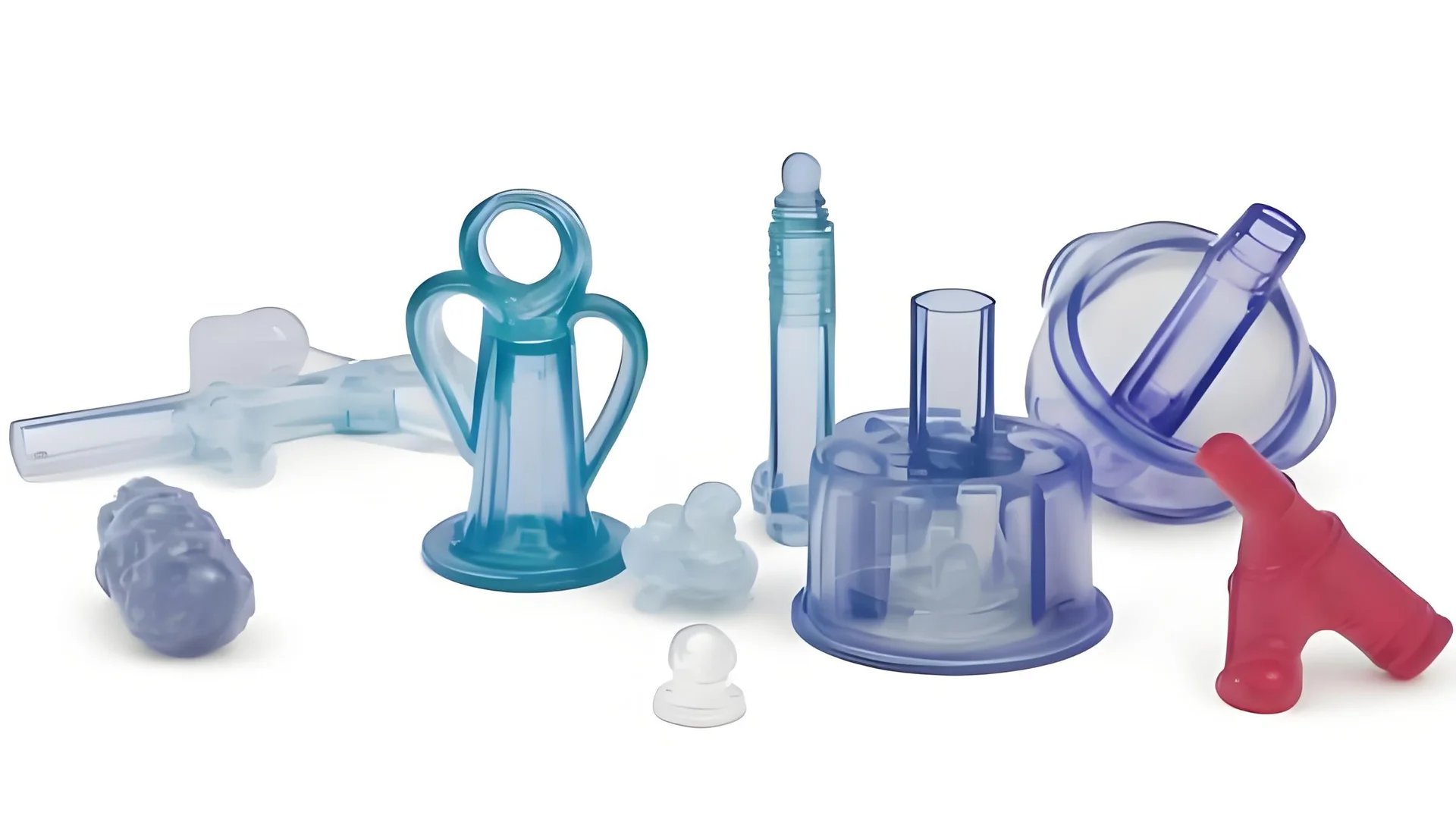
Understanding Material Characteristics
In injection molding, material type plays a pivotal role in determining mold opening time due to varying cooling rates and thermal properties. Each material’s molecular structure impacts how it behaves under heat and pressure, making material selection critical.
Crystalline vs. Non-crystalline Plastics
-
Crystalline Plastics: These materials, like polyethylene and polypropylene, have ordered molecular structures. They require longer cooling times to solidify properly, thus extending mold opening time. This is crucial to avoid defects such as warping or incomplete formation.
-
Non-crystalline Plastics: In contrast, materials like polystyrene and polycarbonate are amorphous and cool quicker due to their disordered molecular structure. This allows for shorter mold opening times, enhancing efficiency.
Material Type | Cooling Time | Mold Opening Time |
---|---|---|
Crystalline | Longer | Extended |
Non-crystalline | Shorter | Reduced |
Temperature-Sensitive Materials
Certain materials are sensitive to temperature fluctuations. Thermosensitive plastics can decompose or discolor at high temperatures, requiring precise control of the mold opening time to maintain quality and appearance. Adjusting the injection molding temperature2 can help optimize these conditions.
Influence of Material Properties on Mold Design
The choice of material affects not only the mold opening time but also necessitates adjustments in mold design. For instance, materials that need longer cooling times might benefit from enhanced cooling systems within the mold.
Enhancing Mold Cooling Systems
- Efficient Cooling Systems: Integrating advanced cooling channels can significantly speed up the cooling process for materials with extended cooling requirements.
- Optimizing Mold Structure: Considering mold complexity can aid in uniform cooling, which is particularly beneficial for crystalline plastics needing prolonged cooling.
Real-World Applications
In practice, a large automotive part made from polypropylene would require a longer mold opening time compared to a small electronic component made from polycarbonate. Such distinctions underscore the importance of aligning material properties with production goals to achieve optimal results.
Understanding these factors not only aids in determining the appropriate mold opening time but also improves overall production efficiency and product quality. Exploring further into material-specific cooling strategies3 can offer deeper insights into enhancing manufacturing processes.
Crystalline plastics require longer cooling times.True
Crystalline structures need more time to solidify, extending cooling.
Non-crystalline plastics cool slower than crystalline ones.False
Non-crystalline materials cool faster due to disordered molecular structure.
What Role Do Process Parameters Play in Mold Timing?
In the intricate dance of injection molding, process parameters hold the key to perfecting mold timing and achieving flawless results.
Process parameters like temperature, pressure, and speed critically influence mold timing by affecting cooling rates and product quality. Adjusting these parameters helps balance efficiency and performance.
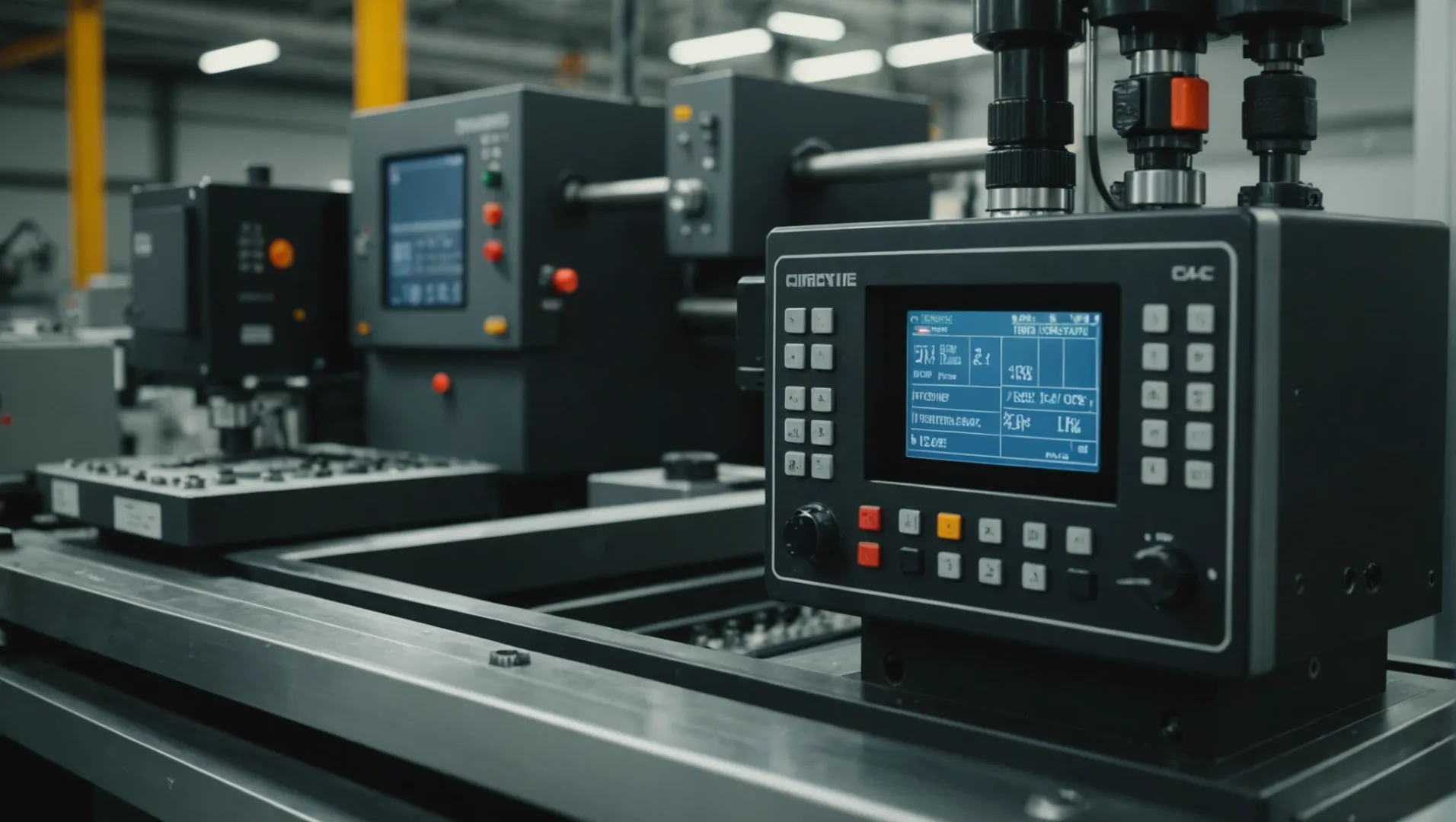
Understanding Injection Molding Temperature
Injection molding temperature is a pivotal parameter in determining mold timing. Higher temperatures enhance plastic flow within the mold, facilitating more intricate designs but extending cooling times. Conversely, lower temperatures can hasten cooling but might compromise product quality.
Balancing the temperature requires careful consideration of the material’s thermal properties and desired product specifications. For instance, crystalline plastics typically need higher temperatures for adequate flow but extended cooling times. In contrast, non-crystalline plastics might allow for lower temperature settings, reducing mold opening time without sacrificing quality.
The Impact of Injection Molding Pressure and Speed
Pressure and speed during injection molding are crucial for ensuring the material fills the mold cavity adequately. High pressure and speed can lead to increased internal stresses within the product, necessitating longer mold opening times to allow stress release and prevent warping or cracking.
A table summarizing the effects of varying pressure and speed settings:
Parameter | Effect on Product | Recommended Adjustment |
---|---|---|
High Pressure & Speed | Increased stress; potential warping | Extend mold opening time |
Low Pressure & Speed | Reduced fill quality; surface defects | Adjust other parameters |
In practice, optimizing these parameters often involves trial runs, adjusting based on observed product quality and production efficiency. This iterative approach ensures both performance and efficiency are balanced.
The Role of Cooling Systems
The efficiency of a mold’s cooling system is another essential factor influenced by process parameters. A robust cooling system can significantly reduce mold opening times by speeding up the product’s cooling rate.
In cases where cooling systems are less efficient, adjustments to process parameters like temperature and pressure may be necessary to compensate for longer cooling durations. Enhancing cooling systems can involve redesigning the system for better heat dissipation or employing advanced cooling technologies.
By examining these parameters in greater detail4, manufacturers can fine-tune their processes, achieving optimal mold opening times that balance speed and quality.
Higher molding temperatures extend cooling times.True
Higher temperatures enhance flow but require longer cooling to solidify.
Low pressure always improves fill quality in molds.False
Low pressure can lead to incomplete fills and surface defects.
How Can Mold Design Influence the Optimal Opening Time?
In injection molding, mold design is pivotal in determining when to open the mold for optimal results.
Mold design affects the optimal opening time by influencing cooling efficiency and structural complexity. Efficient cooling systems and simpler structures can reduce cooling time, while complex designs may require longer periods. Adjusting these elements helps achieve the best results in injection molding.
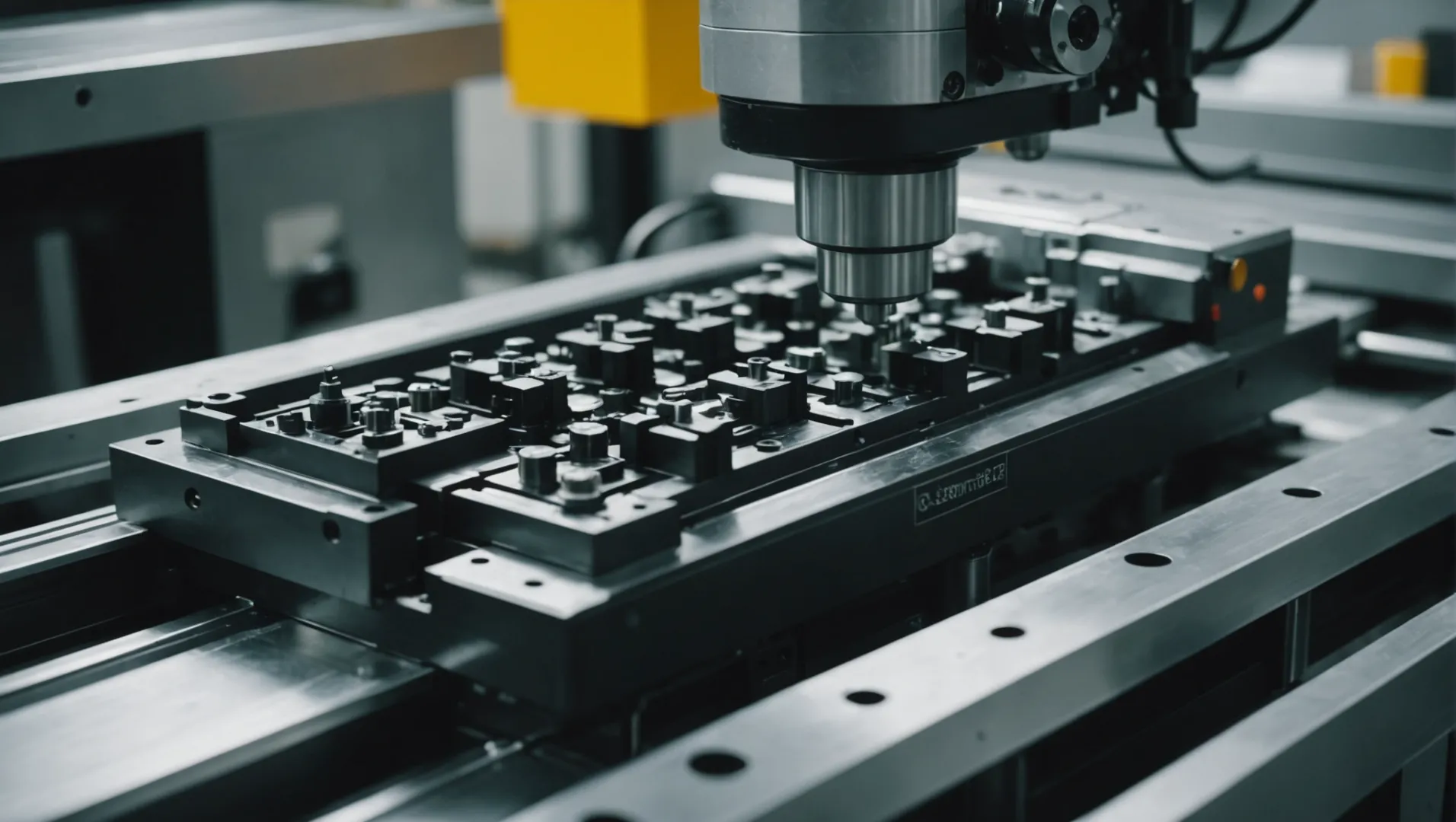
The Role of Mold Cooling Systems
A well-designed mold cooling system is essential in reducing the mold opening time. By efficiently dissipating heat, it allows the plastic to cool and solidify faster, which is crucial for maintaining product integrity and reducing cycle times.
-
Efficiency and Performance: High-performance cooling systems with strategically placed channels can significantly shorten cooling periods. For instance, conformal cooling, which follows the contour of the part, can improve thermal management compared to traditional straight-line cooling methods.
-
Optimization Strategies: If the existing cooling system is insufficient, consider optimizing or upgrading5 it to enhance performance. Adding more channels or using advanced materials for better thermal conductivity can be beneficial.
Impact of Mold Structure and Complexity
The complexity of the mold structure directly impacts cooling uniformity and efficiency, thereby influencing the optimal mold opening time.
-
Structural Elements: Molds with intricate features such as sliders and core pulls may require additional time to cool adequately. This ensures these parts separate smoothly without causing damage or defects.
-
Simplifying Designs: Whenever possible, simplifying the mold design can help reduce cooling times. Eliminating unnecessary features or using fewer moving parts can lead to more uniform cooling and faster cycle times.
Addressing Complex Mold Scenarios
Certain molds present unique challenges that necessitate tailored solutions for determining optimal opening times.
-
Case Studies: For example, molds used for manufacturing large automotive parts often face challenges due to their size and complexity. Implementing a detailed cooling analysis and conducting mold trials can aid in identifying potential issues early on.
-
Trial and Error: In practice, performing a mold trial with different opening times can help refine settings. Monitoring the cooling process and adjusting based on real-time data can lead to discovering the most efficient setup.
By considering these aspects of mold design, manufacturers can optimize the opening time to enhance product quality and production efficiency in injection molding.
Efficient cooling reduces mold opening time.True
Efficient cooling systems dissipate heat faster, reducing cooling time.
Complex mold designs shorten cycle times.False
Complex designs require longer cooling, increasing cycle times.
Conclusion
Finding the right mold opening time is all about balancing multiple factors. By refining your approach through trials and careful monitoring, you can elevate both efficiency and quality.
-
Explore how product traits influence mold timing strategies.: The quality and design of the mold directly impact the final product’s characteristics and production efficiency. 5. Production. The … ↩
-
Learn techniques to manage temperatures for thermosensitive materials effectively.: A temperature control system consists of three components: the mould, the temperature control unit and a heat transfer medium. Certain conditions have to be … ↩
-
Explore various methods to optimize cooling systems in molds.: There are two standard methods for injection molding machine cooling systems: air cooling system and water cooling system. ↩
-
Discover expert tips on refining process parameters for improved molding outcomes.: Steps to INJECTION MOLDING Process Optimization · 1. Tool functionality examination · 2. Short shot testing · 3. Gate seal studies · 4. Sample parts evaluation/data … ↩
-
Learn how to improve cooling efficiency for better mold performance.: It is best to specify the design and not rely on tool shop expertise in cooling. Many tool shops know very little of optimizing mold cooling, … ↩