I remember the first time I understood how much mold material influences a product’s look. It’s like picking the right paint for a masterpiece. Everything really depends on it.
The best mold material for product appearance depends on factors like surface finish quality, durability, thermal conductivity, and compatibility with the production material.
Imagine designing a shiny, clear container. Use a mold material like S136 steel. This steel shines brilliantly and fights rust over time. It definitely gives products a beautiful and lasting look.
Crafting items with a patterned surface? P20 steel becomes a favorite choice. Designers really enjoy how it allows for detailed patterns. It doesn’t wear down tools quickly. Products always turn out precise.
Precision parts need H13 steel. It stays stable under heat. Designs keep their exact size, even if production gets intense.
Special color effects require NAK80 steel. This steel shines both in looks and function. It has polished surfaces and releases molds easily. Materials like these turn design dreams into real products. These products look great and work well.
S136 steel is ideal for high gloss finishes.True
S136 steel is known for its excellent polishing capabilities, ideal for high gloss.
NAK80 steel cannot achieve textured surfaces.False
NAK80 can be textured due to its good machinability and polishability.
- 1. How does material selection affect high gloss and transparency?
- 2. How Does Steel Type Affect Texture and Pattern Creation?
- 3. Why Is Precision Important for Dimensional Accuracy?
- 4. How Do Material Properties Influence Multi-Color Effects?
- 5. How Can You Ensure Long-Term Mold Performance?
- 6. Conclusion
How does material selection affect high gloss and transparency?
Have you ever thought about how the right choice of material turns a boring product into something amazing? Materials really change things.
Material choice is very important in deciding the gloss and transparency of products. It changes how light touches the surface. S136 steel, for example, usually gives a high-gloss finish. This happens because it polishes really well. P20 steel, in contrast, suits textured designs better.
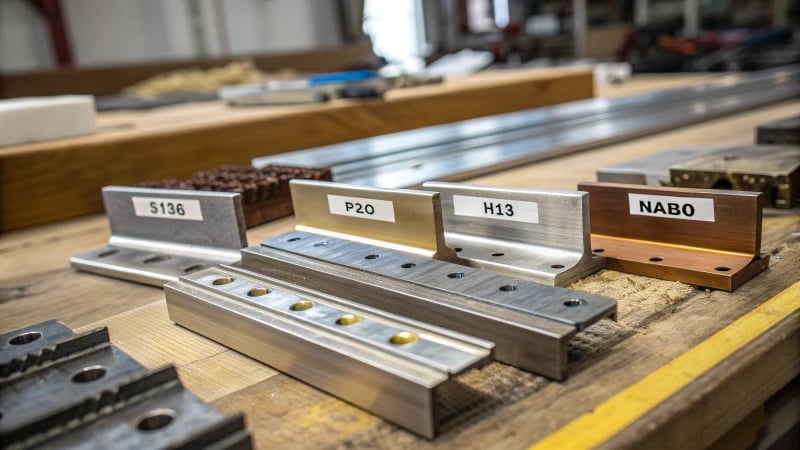
Understanding High Gloss and Transparency
I remember when I first entered the world of product design. It felt like opening a book full of endless ideas. Creating something that worked well and looked beautiful was exciting. I realized choosing materials was more than a technical choice; it was about bringing an idea to life and turning a concept into something real and stunning.
1. The Role of S136 Steel
S136 steel stands out in my collection. It’s like finding a perfect brush for an artist. Its purity and shine are ideal for a sleek, glossy look, crucial for products needing clarity and smoothness, like optical lenses or transparent containers that we love.
Property | S136 Steel |
---|---|
Polishability | Excellent |
Corrosion Resistance | High |
Hardness (HRC) | 48-52 |
The durability keeps the product shining, resisting rust or corrosion that would dull its glow. S136 is my choice whenever sparkle and endurance are needed—like timeless wardrobe pieces that never lose their charm.
2. Textures and Patterns with P20 Steel
For experimenting with textures or patterns, P20 steel becomes my reliable tool. It’s like using a palette knife to sculpt detailed designs. Whether crafting a textured automotive interior or adding flair to a cellphone case, P20 gives the needed versatility for creating depth and detail.
Exploring P20 steel2 has been a journey where I discovered how simple forms can capture complexity.
High Precision Dimensional Needs
H13 steel is my dependable companion in precision tasks. It’s crucial when accuracy can’t be compromised, resembling a careful surgeon’s hand. Its stability under heat keeps every curve and angle precise.
Key Advantages of H13 Steel:
- Thermal Stability: Keeps shape under heat.
- Wear Resistance: Stands strong against plastic melt erosion.
- Uniform Structure: Allows for accurate molding over extended periods.
Discover more about H13 steel3
H13’s reliability is like a rock-solid foundation for complex projects.
Multiple Color Effects with NAK80 Steel
NAK80 steel acts as an artist’s canvas for playing with colors. It supports techniques like two-color injection molding, becoming vital when variety is needed. It’s about bringing creative visions to life with vivid colors and special effects.
Conclusion
Choosing the right material isn’t just about meeting specs; it’s about shaping experiences and telling stories through design. Each material—S136, P20, H13, or NAK80—brings unique strengths ensuring that products not only meet expectations but also inspire. It’s like creating a symphony where every instrument plays its part to compose a masterpiece.
S136 steel is ideal for high-gloss products.True
S136 steel's polishability enhances surface smoothness, boosting gloss.
P20 steel cannot create textured surfaces.False
P20 steel supports intricate textures via EDM and etching processes.
How Does Steel Type Affect Texture and Pattern Creation?
Have you ever thought about why the steel type is so important when creating textures and patterns?
Steel type has a crucial role in creating texture and patterns. It affects machinability, polishability and durability. For instance, P20 steel is special. It meets the needs of textured designs. S136 steel stands out for high-gloss finishes.
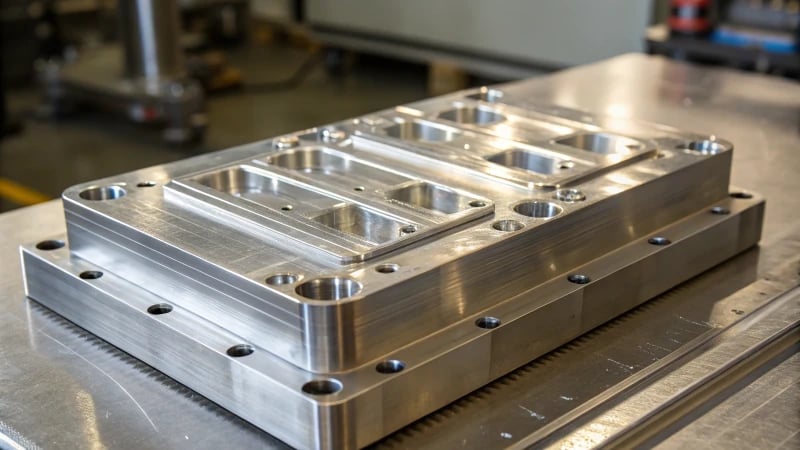
Influence of Steel Type on Textures
I remember when I first researched which steel type4 to choose for a project. It felt like picking the best superpower for a superhero! P20 steel, for example, works wonderfully for creating the fine textures seen in car interiors. Its machinability is excellent. Tools can replicate precise textures without wearing out quickly. This balance often leads me to pick P20 for detailed patterns.
-
Steel Type Texture Use P20 Intricate textures S136 High gloss finishes
P20’s moderate hardness (HRC30-36) shows its strength in processes like EDM and etching.
Creating Patterns with Steel
Steel choice is important for creating patterns too. Different steels5 offer varied advantages. S136 steel offers high polishability. I prefer it for projects needing a mirror-like finish, such as optical lenses. Once, I worked on products where clarity was very important. S136’s resistance to rust kept the look perfect and made the product last long.
This steel’s corrosion resistance ensures longevity and appearance retention, even under harsh conditions involving chemicals or moisture.
Steel Characteristics in Pattern Formation
Every steel type has its strengths in pattern-making. NAK80, for instance, suits projects with complex designs or multi-color effects. Its polishability like a mirror has helped me with many plating and painting tasks.
Steel Type | Ideal Use |
---|---|
NAK80 | Multi-color effects |
H13 | Dimensional precision |
Steel choice impacts more than looks. Durability and functionality matter too. I learned that knowing these details truly affects design success. Crafting a sleek smartphone case or a detailed car part? Understand your steel types—they may be your secret weapon.
Discover more about pattern creation techniques6.
P20 steel is ideal for intricate textures.True
P20's machinability and hardness balance make it suitable for detailed textures.
S136 steel is unsuitable for high-gloss finishes.False
S136 is preferred for high-gloss finishes due to its polishability.
Why Is Precision Important for Dimensional Accuracy?
When I first began working with molds, I quickly understood that accuracy means everything. Precision is critical. It’s not only about fitting parts together. It’s also about safety in every product. Reliability really matters in what we create.
Precision holds great importance for dimensional accuracy. Each component needs to meet exact specifications. Precision reduces deviations. Consistency really improves. Industries relying on precise measurements are affected in both functionality and safety.
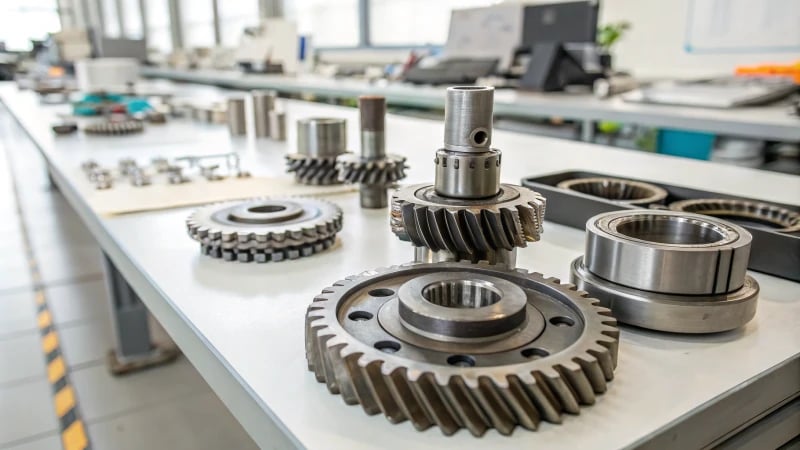
Understanding Precision and Dimensional Accuracy
When I started in mold design, I noticed that precision and dimensional accuracy seemed very similar. Precision means having the same measurements every time, while dimensional accuracy7 is about reaching exact specified sizes. In my work area, these ideas are very important for quality checks.
Precision in Material Selection
I remember working with S136 steel for a project needing high gloss and transparency. This steel’s ability to polish well helped us meet the shiny, clear look we wanted. On another project, P20 steel’s easy machining allowed detailed textures. Choosing the right materials is really vital for consistent quality8.
Material | Characteristics | Usage |
---|---|---|
S136 | High gloss, corrosion-resistant | Transparent products |
P20 | Easy texturizing, good machinability | Patterned surfaces |
H13 | Thermal stability, wear resistance | Precision parts |
NAK80 | Mirror finish, release properties | Multi-color effects |
The Role of Precision in High Precision Appearance
One tough project used H13 steel for electronic equipment cases. H13’s thermal stability kept components accurate during injection molding heat. This consistency is crucial for making reliable products like precision electronic equipment9 housings.
Consistency Across Products
Achieving precision reduces differences between products. In the aerospace industry, where I help develop pieces that must fit perfectly, any difference might cause problems or safety concerns. Precision minimizes variability, ensuring each product is identical.
Factors Influencing Dimensional Accuracy
I discovered that factors like thermal expansion and machining accuracy impact dimensional accuracy. Materials like H13 with low thermal expansion help reduce size changes over time.
Learn more about how materials affect precision10 in demanding industries where precision is a must. Every day, these choices guide us toward excellence.
Precision ensures dimensional accuracy in manufacturing.True
Precision reduces measurement deviations, ensuring components meet specifications.
P20 steel is used for transparent products due to high gloss.False
P20 is used for textured surfaces; S136 is for high gloss transparent products.
How Do Material Properties Influence Multi-Color Effects?
Do you ever wonder how some products shine with many colors? The answer is the materials used.
Material properties are very important for multi-color effects. They affect how light touches pigments. NAK80 steel, popular for its excellent mirror-like finish, provides many aesthetic options in manufacturing.
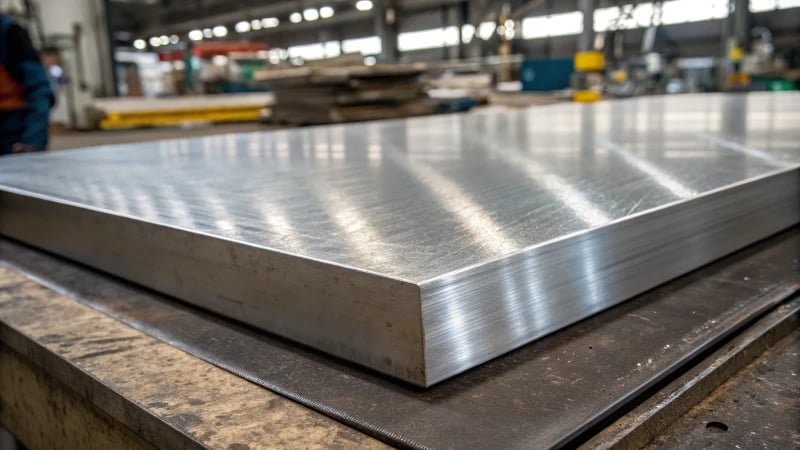
Understanding How Materials React to Light
I remember the first time I entered a room full of colorful gadgets and wondered why each sparkled differently in the light. Different materials react uniquely to light. Reflectivity, transparency, and surface texture are key. For example, NAK80 steel11 is famous for creating amazing looks because it handles mirror processing very well. It’s like giving your product a ticket to a world of detailed two-color molding and metallization processes.
Picking the Perfect Material for the Desired Effect
Choosing the right material is like finding the perfect pair of jeans – it needs to fit perfectly. NAK80 steel, for instance, has a hardness of HRC37 – 43. This allows it to be polished to a high-quality mirror finish. This quality is crucial when a product gets surface treatments like plating or painting as it increases color brightness.
Material | Properties | Applications |
---|---|---|
NAK80 Steel | High polishability, good release properties | Two-color molding, surface metallization |
S136 Steel | High gloss, transparent | Optical lenses, clear containers |
P20 Steel | Texturizing capability | Patterned phone cases |
Influence of Surface Texture on Color Perception
Surface texture can dramatically alter how we see color – much like how music can change the atmosphere of a room. P20 steel is useful here, especially for products with textures like leather-patterned interiors. This material’s machinability lets intricate patterns form accurately, adding depth and variety to what we see. Understanding these details12 can change products from good to amazing.
Effect of Material Properties on Creating Products
Sometimes, looks aren’t everything; precision is crucial too. In situations demanding high accuracy, like making parts for precise electronics, H13 steel is exceptional. It stays stable under thermal stress during injection molding and keeps colors clear and correctly positioned. Discover more about how material choice affects production13.
Conclusion: Discovering a World of Possibilities
Discovering the array of material properties opens endless chances for multi-color effect innovation. Designers and manufacturers find understanding these complexities very valuable. It’s not solely about nice looks; it’s about expanding the limits of design possibilities. Trying materials like NAK80 or H13 isn’t solely about aesthetics; it’s about meeting high quality and precision standards too.
NAK80 steel is ideal for two-color injection molding.True
NAK80 steel's high polishability and mirror processing capabilities make it suitable.
P20 steel is unsuitable for texturized products.False
P20 steel is excellent for texturizing, allowing complex pattern replication.
How Can You Ensure Long-Term Mold Performance?
Molds need more than just an initial investment. They must work excellently over time. Performance remains crucial. Molds should continue to operate with precision and durability. This helps guarantee success in the long run.
For long-lasting mold performance, choose suitable materials like S136 and H13. Conduct regular maintenance. Think about the impact of the environment. These steps maybe increase durability and efficiency.
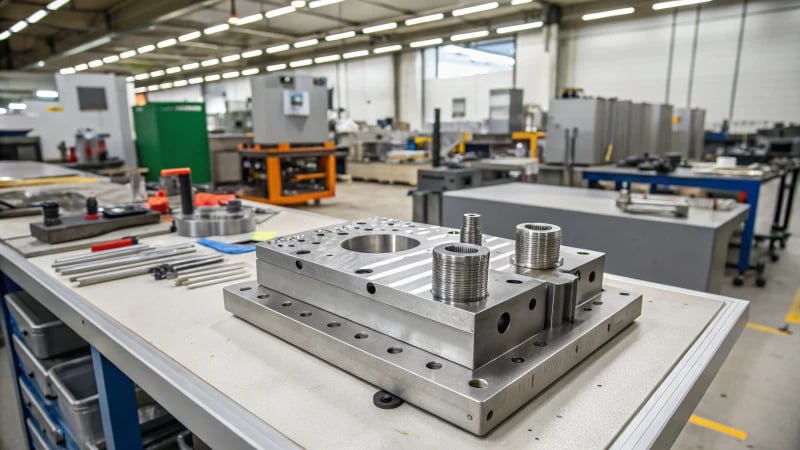
Material Selection
In the beginning, working with molds taught me a crucial lesson. Choosing the right material is like laying a really strong foundation for a house. S136 steel is my favorite when I need high gloss and transparency due to its superb polishability and corrosion resistance. Imagine creating clear plastic containers or optical lenses that remain pristine over time. S136 makes that dream real.
Material | Application | Advantages |
---|---|---|
S136 | High gloss/transparent products | High polishability, corrosion resistance |
P20 | Textured/patterned surfaces | Easy machinability, texture clarity |
H13 | High precision requirements | Thermal stability, strength at high temperatures |
Maintenance Practices
I remember when I first understood the importance of regular maintenance. The mold jammed during an important production run because I neglected cleaning schedules. Regular maintenance prevents this kind of trouble by ensuring timely cleaning to prevent residue buildup, proper lubrication to reduce wear, and periodic inspections for wear and tear. Implementing a maintenance schedule14 can prolong mold lifespan.
Environmental Considerations
Weather changes were just small talk until I saw their impact on mold accuracy. High humidity secretly causes corrosion while temperature fluctuations lead to expansion or contraction problems. Since then, selecting materials with great thermal properties and corrosion resistance is a must for me as environmental factors matter a lot.
Texture and Pattern Requirements
For intricate textures or patterns like leather-like car interiors, P20 steel is my go-to choice due to its machinability which allows for complex designs through EDM or etching. It ensures that aesthetic standards are always met consistently.
High Precision Needs
Seeing a product exactly as designed is truly satisfying. For tight dimensional tolerances, H13 steel is unbeatable as it maintains precise cavity dimensions even with temperature changes due to its low thermal expansion properties.
Explore more about high precision needs15 in mold performance and how different steels compare in practical applications.
Understanding these factors helps me optimize mold performance by improving product quality and reducing operational costs over time. It’s really about getting the most out of each mold where quality and efficiency matter a lot.
S136 steel is ideal for high gloss products.True
S136 steel offers high polishability and corrosion resistance, making it suitable for high gloss products.
P20 steel is unsuitable for textured surfaces.False
P20 steel is actually ideal for textured surfaces due to its easy machinability and texture clarity.
Conclusion
Choosing the right mold material, such as S136 for gloss, P20 for textures, H13 for precision, and NAK80 for colors, is crucial for achieving desired product appearances.
-
This link provides insights into how different materials interact with light to enhance product gloss. ↩
-
Explore how P20 steel is used in creating intricate textures for consumer products. ↩
-
Understand why H13 steel is favored for its precision and durability in mold applications. ↩
-
Learn how different steel types impact the creation of textures, influencing both functionality and aesthetics. ↩
-
Discover which steel types are best suited for pattern making to enhance your project’s precision and appearance. ↩
-
Explore various techniques used in metalworking to create patterns, expanding your knowledge and skills. ↩
-
Learn about dimensional accuracy, a key concept that ensures components are manufactured to precise specifications. ↩
-
Discover why maintaining consistent quality is crucial in manufacturing processes, ensuring reliability and customer satisfaction. ↩
-
Find out more about materials used for precision electronic equipment housings to ensure functionality and durability. ↩
-
Understand how different materials influence precision in manufacturing processes, affecting overall product quality. ↩
-
Discover how NAK80 steel’s properties make it ideal for multi-color effects in product design. ↩
-
Understand how surface texture influences color perception and enhances visual depth. ↩
-
Learn why choosing the right material is crucial for efficient manufacturing processes and quality outcomes. ↩
-
Discover maintenance practices that extend mold lifespan and efficiency. ↩
-
Understand different steels’ roles in achieving high precision in molds. ↩