Navigating the intricate world of injection molding is no small feat. With complex shapes that challenge even the most seasoned professionals, having the right strategies can turn frustration into success.
The best mold design strategies for complex-shaped injection molding products include thorough product analysis, careful material selection, strategic mold structure design, and meticulous manufacturing and debugging processes.
While this summary offers a quick glance at essential strategies, diving deeper into each aspect reveals invaluable insights that could dramatically enhance your manufacturing outcomes. Continue reading for expert tips and techniques tailored to address the unique challenges of intricate injection molding designs.
Material selection impacts mold design efficiency.True
Material properties dictate mold design decisions, affecting efficiency.
How Does Product Analysis Influence Mold Design?
Understanding product features deeply is vital in crafting molds that meet exacting specifications and ensure high-quality output.
Product analysis significantly impacts mold design by identifying crucial shape, material, and performance requirements, ensuring optimal mold structure and function.
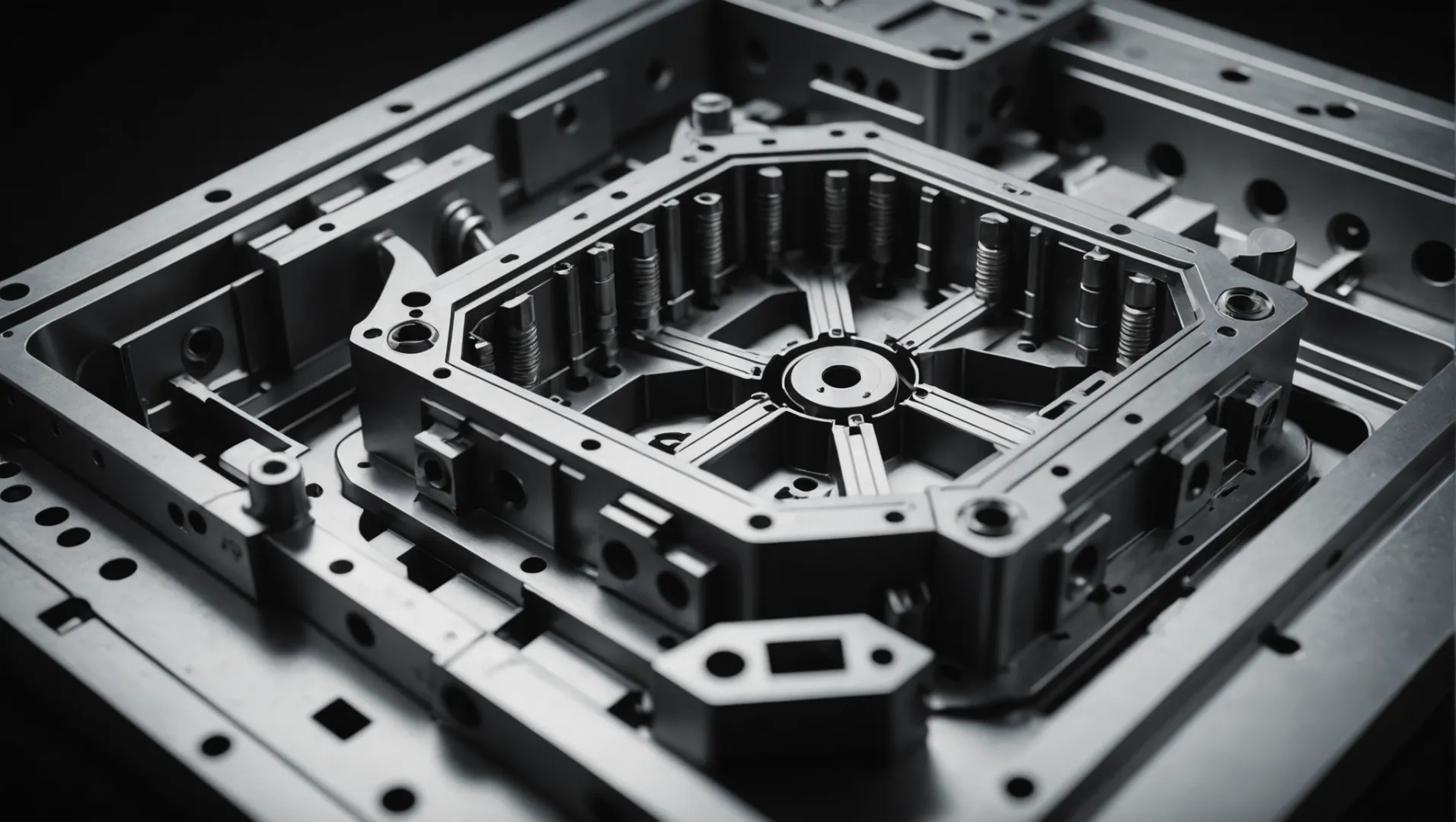
Understanding Product Shape
One of the most critical steps in product analysis is comprehending the complex geometries involved. This involves examining geometric characteristics like curved surfaces, chamfers, and holes, which directly influence the mold’s structural design. For instance, products with intricate shapes may require multiple parting surfaces1 to facilitate efficient demolding.
A thorough analysis of wall thickness distribution is also crucial. Products with uneven wall thickness may suffer from defects such as shrinkage marks or warping. The transition between thick and thin walls must be managed carefully to ensure uniformity, avoiding these common pitfalls.
Material Selection Impacts
Choosing the right material for injection molding is another key aspect of product analysis. The selected material’s properties — including fluidity, shrinkage, and mechanical characteristics — dictate many mold design decisions. For example, materials with low thermal stability may necessitate special cooling systems to maintain mold integrity.
Moreover, understanding the material’s chemical corrosion resistance and machinability is vital for ensuring the mold’s longevity and the product’s quality. In some cases, advanced engineering plastics2 might be preferable for their superior properties, impacting the overall design strategy.
Performance Requirements
Product analysis doesn’t stop at shape and material; it extends to performance expectations. This includes dimensional accuracy and surface finish quality, which dictate specific design choices in mold structure. Complex products may require advanced techniques like hot runner systems for efficient filling or specialized cooling channels for temperature control.
Incorporating these performance requirements into the design phase helps in preemptively addressing potential issues like local filling insufficiency or over-pressure, ultimately leading to a robust design that meets production demands without compromising on quality.
Each of these elements — shape understanding, material selection, and performance considerations — contribute to a well-rounded product analysis that informs effective mold design strategies.
Product analysis affects mold's structural design.True
Product analysis ensures the mold meets shape and material requirements.
Material selection has no impact on mold design.False
Material properties like shrinkage influence mold design decisions.
What Role Does Material Selection Play in Mold Design?
Choosing the right material for mold design is crucial for achieving product quality and longevity. It impacts everything from fluidity to durability.
Material selection is fundamental in mold design as it dictates fluidity, shrinkage, and mechanical properties, influencing both the molding process and final product quality.
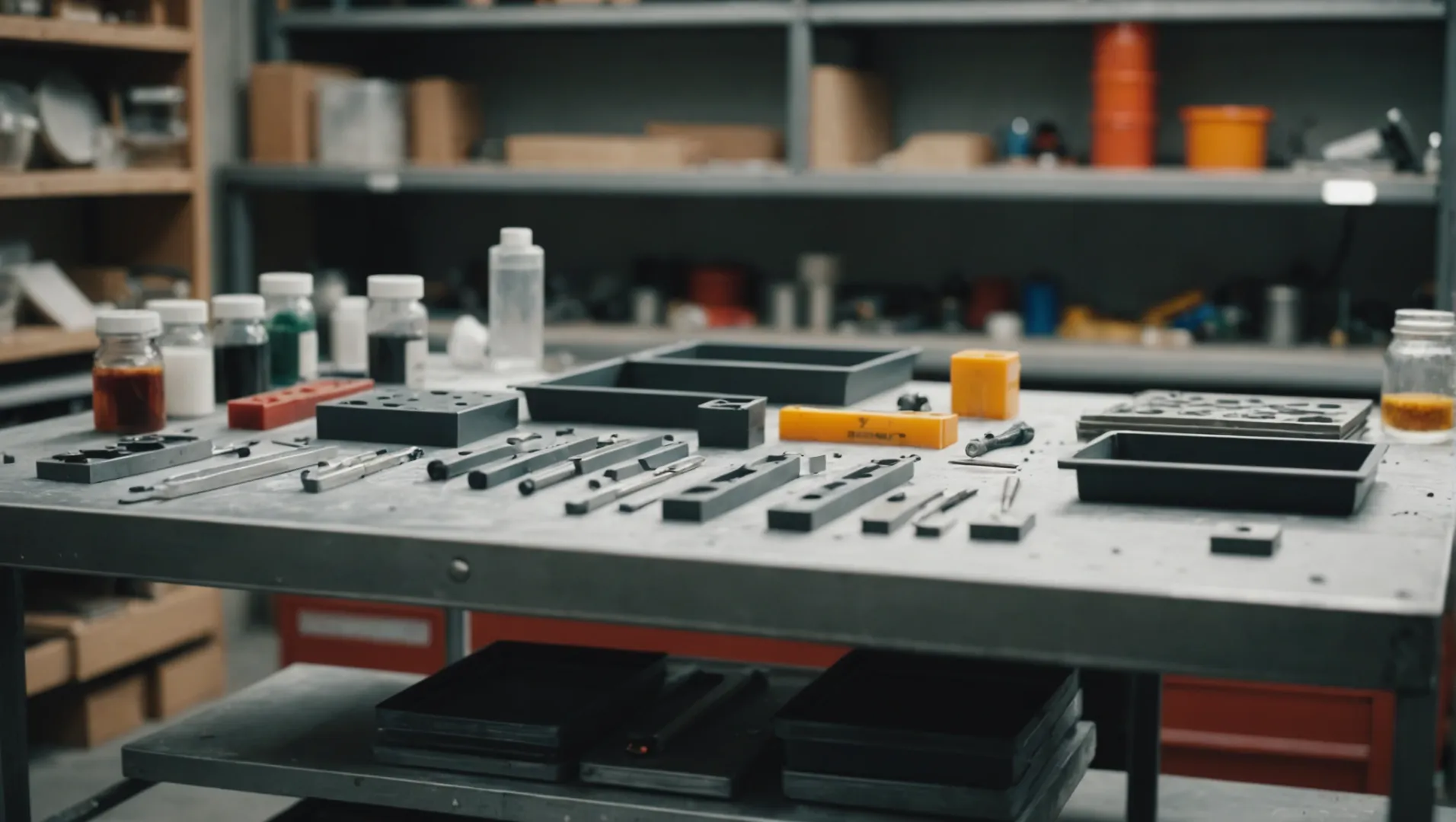
Understanding Material Properties
Material selection begins with a deep understanding of its intrinsic properties. Different materials offer varying levels of fluidity, shrinkage, and mechanical strength. For example, polycarbonate3 is known for its high impact resistance and transparency, whereas polypropylene4 offers excellent chemical resistance and flexibility.
- Fluidity: Materials with higher fluidity fill mold cavities more efficiently, which is essential for intricate designs.
- Shrinkage: Understanding the shrinkage rate helps in predicting dimensional changes post-molding.
- Mechanical Properties: Strength, toughness, and flexibility influence how the product performs under stress.
Thermal and Chemical Considerations
Thermal stability and chemical resistance are pivotal. Mold materials must withstand high temperatures without degrading or distorting. Metals like stainless steel5 are often preferred for their excellent heat resistance and durability.
- Thermal Stability: Ensures that the mold maintains its shape and functionality even after repeated exposure to high temperatures.
- Chemical Resistance: Critical for molds used in environments where they are exposed to aggressive chemicals.
Machinability and Cost Efficiency
The machinability of a material affects the ease of mold manufacturing. While harder materials offer better wear resistance, they are also more challenging and costly to machine. Balancing cost with performance is key.
Material | Machinability | Cost Efficiency |
---|---|---|
Aluminum | High | Moderate |
Steel | Moderate | High |
Brass | Low | Low |
Understanding these factors can lead to more informed choices that ensure not only product quality but also manufacturing efficiency. Selecting the right material can minimize defects like warping or shrinkage marks while maximizing mold longevity and productivity.
Polycarbonate has high impact resistance in mold design.True
Polycarbonate is known for its high impact resistance, making it ideal for durable molds.
Aluminum offers low machinability in mold manufacturing.False
Aluminum is highly machinable, making it easier to work with in mold manufacturing.
Why Is Cooling System Design Crucial for Complex Shapes?
A well-designed cooling system is pivotal for maintaining precision and efficiency in injection molding, especially with complex shapes.
The cooling system in injection molding for complex shapes ensures uniform temperature distribution, preventing defects like warping and shrinkage, thus ensuring high-quality production.
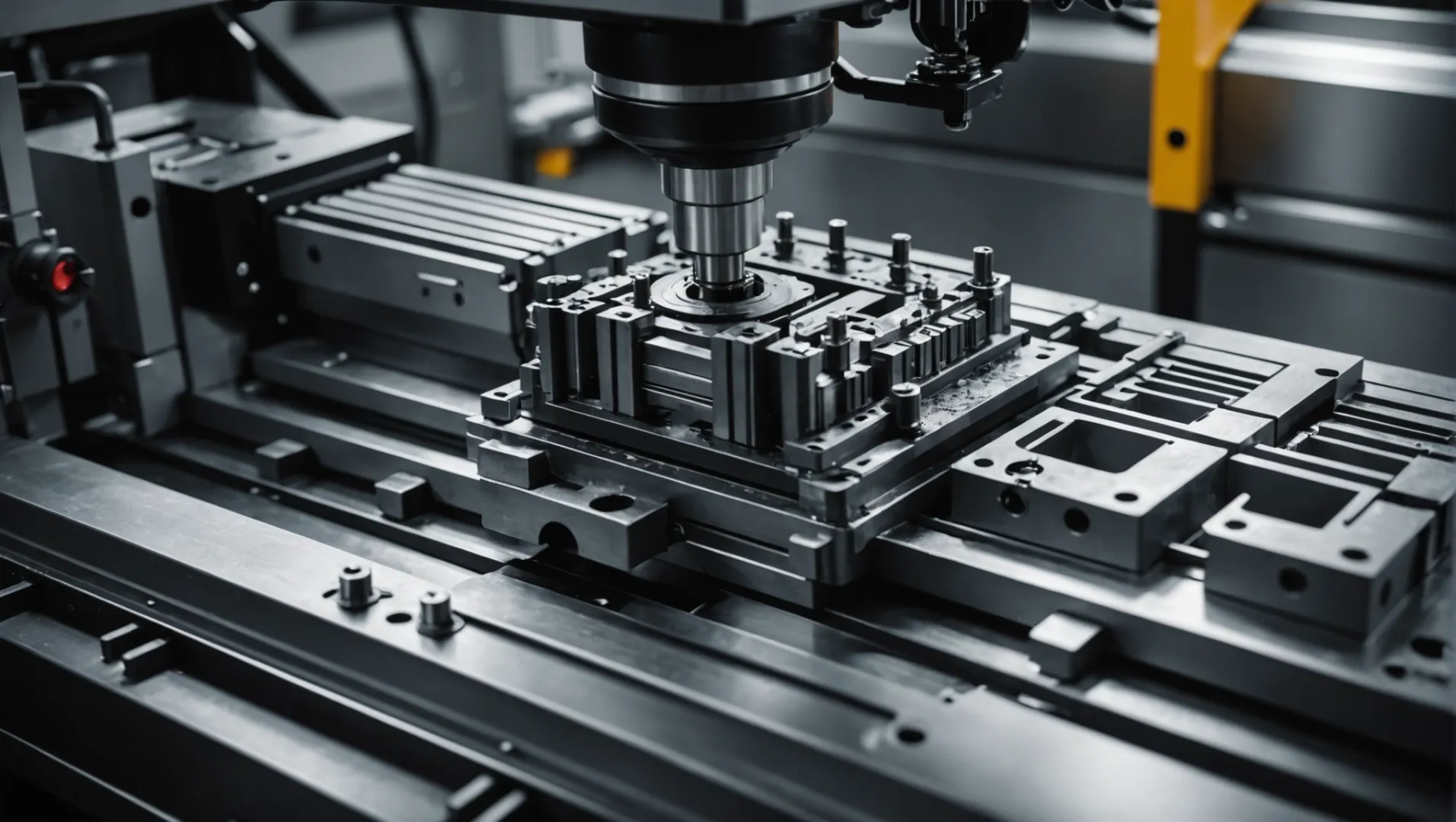
Understanding the Importance of Cooling Systems
In injection molding, the cooling system6 plays a crucial role by dissipating heat from the molten plastic as it forms within the mold. This is particularly important for complex shapes, where uneven cooling can lead to issues such as warping, dimensional inaccuracies, and poor surface finish. A well-optimized cooling system ensures that the entire mold cools uniformly, maintaining the intended shape and dimensions of the product.
Challenges with Complex Shapes
Complex shapes often have varying wall thicknesses and intricate geometries. These factors pose challenges for uniform cooling. For instance, thicker sections may retain heat longer than thinner ones, leading to uneven cooling rates across the product. This can cause internal stresses and defects.
Designers must consider these complexities when planning the cooling channels. A strategically laid-out cooling system7 can manage these variations by ensuring efficient heat removal, reducing cycle times and improving product consistency.
Designing Efficient Cooling Channels
The design of cooling channels must be tailored to the geometry of each complex shape. Here are some strategies:
- Conformal Cooling: This involves creating cooling channels that closely follow the contour of the part. This method is particularly effective for complex shapes as it provides more uniform cooling.
- Baffle and Bubblers: These components can be used in areas that are difficult to reach with standard straight channels, ensuring thorough heat removal.
- Simulation Tools: Utilizing simulation software can predict how the plastic will flow and cool, allowing designers to optimize channel placement and diameter before manufacturing.
Balancing Cooling Efficiency and Cost
While enhancing cooling efficiency is crucial, it’s also important to balance this with cost-effectiveness. Advanced methods like conformal cooling can be more expensive due to sophisticated manufacturing techniques like 3D printing or EDM (Electrical Discharge Machining). However, the benefits often outweigh the costs by reducing cycle times and improving product quality.
Case Studies: Success in Complex Mold Cooling
Several industries have successfully implemented advanced cooling systems for complex shapes. For example, in the automotive sector, manufacturers have used conformal cooling to achieve superior surface finishes in intricate engine components. Similarly, in consumer electronics, precise cooling has been pivotal in producing high-quality casings that fit complex internal circuitry snugly.
In conclusion, while designing a cooling system for complex shapes in injection molding presents challenges, employing innovative strategies and tools can significantly enhance efficiency and quality.
Uniform cooling prevents warping in complex shapes.True
Uniform cooling ensures even temperature distribution, preventing warping.
Complex shapes do not require specialized cooling channels.False
Complex shapes need tailored cooling channels to manage heat effectively.
How Can Demolding Mechanisms Be Optimized for Intricate Designs?
Creating intricate designs in injection molding demands sophisticated demolding mechanisms to ensure smooth and damage-free part ejection.
Optimizing demolding mechanisms for intricate designs involves using multiple techniques like sliders, inclined ejectors, and curved parting lines to facilitate smooth part removal without damage.
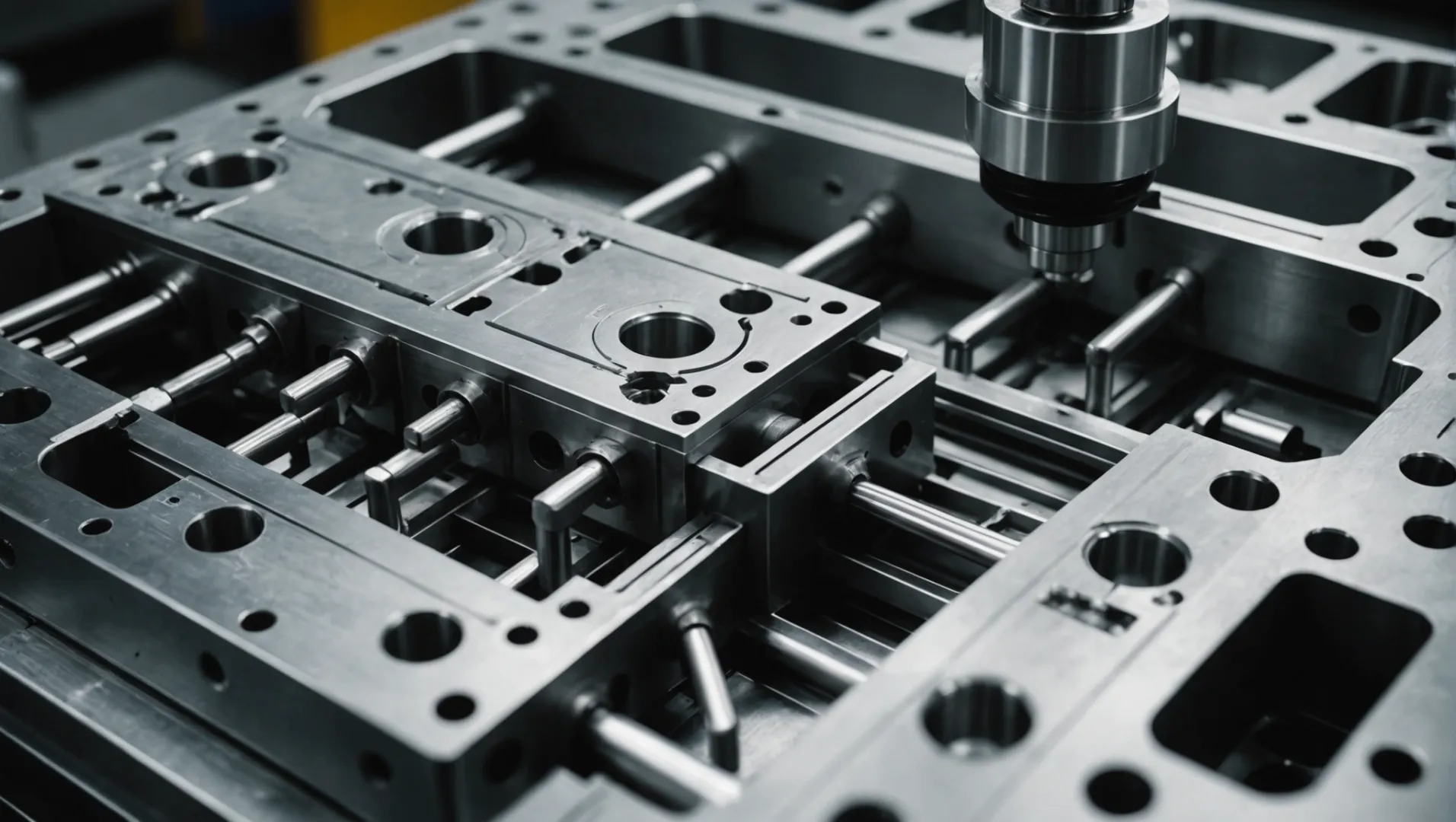
Understanding the Challenges of Intricate Designs
When it comes to complex geometries in injection molding, the demolding process can become challenging. These challenges arise from factors such as undercuts, deep cavities, and delicate features that can be damaged if not handled correctly.
Key Strategies for Optimizing Demolding Mechanisms
-
Utilizing Sliders and Lifters
Sliders and lifters are integral components in molds designed for intricate shapes. They allow for the smooth release of parts with undercuts or side features. By incorporating sliders8 into the mold, the mold can move horizontally to clear any undercuts before the main ejection occurs.
-
Inclined Ejectors and Curved Parting Lines
For complex designs, inclined ejectors can be utilized to apply force in a specific direction, minimizing stress on fragile features. Additionally, employing curved parting lines9 allows for easier separation of complex parts, reducing the risk of damage.
-
Multiple Ejection Systems
In cases where a single ejection system may not suffice, implementing multiple systems can help ensure that all parts of the product are adequately released. This method helps distribute the ejection force evenly across the part.
Feature | Demolding Solution | Benefits |
---|---|---|
Undercuts | Sliders | Prevents part damage |
Fragile Features | Inclined Ejectors | Reduces stress on delicate areas |
Complex Cavities | Multiple Ejection Systems | Ensures complete release |
-
Advanced Simulation Tools
Using simulation software during the design phase can predict potential issues in the demolding process. This allows designers to adjust the mold design before manufacturing begins, ensuring a smoother production process.
-
Regular Maintenance and Calibration
Regular maintenance of demolding mechanisms is essential to prevent wear and tear that can lead to failures during the ejection process. Calibration ensures that all parts move as intended, maintaining the quality and precision of the mold.
By adopting these strategies, manufacturers can enhance their ability to produce complex-shaped injection molded products with high efficiency and minimal defects.
Sliders prevent damage in undercut designs.True
Sliders allow horizontal movement to clear undercuts before ejection.
Curved parting lines increase stress on parts.False
Curved parting lines reduce stress, aiding in smooth part separation.
Conclusion
Successful mold design for complex shapes relies on thorough analysis, strategic planning, and precise execution. Implement these best practices to improve product quality and efficiency.
-
Learn why multiple parting surfaces are essential for complex molds.: During injection, two mold halves touch each other at the parting surface, or the parting line. The number of parting lines can be increased if … ↩
-
Discover benefits of using advanced plastics in mold design.: AEMT in business since 1973, exceeds customer expectations with custom plastic injection molding, insert, compression and transfer molding expertise. ↩
-
Explore polycarbonate’s properties for high-impact resistance in mold design.: Polycarbonate has a high viscosity which makes it necessary to heat the plastic to a high temperature and inject it quickly into the mold to … ↩
-
Learn about polypropylene’s benefits like flexibility and chemical resistance.: Polypropylene (PP) is a thermoplastic addition polymer, which is used predominantly in injection molding applications. PP is inexpensive and easy to access. ↩
-
Discover stainless steel’s superior heat resistance in mold applications.: And of course, another relevant feature that mold steel needs is good thermal stability. A mold steel will continually be exposed to a high-temperature material … ↩
-
Explore how cooling systems prevent defects in injection molding.: An improper injection mold cooling process, then, will almost always result in part defects that require rework or discard. The cooling process … ↩
-
Discover effective methods for optimizing cooling channel designs.: The goals in the design and optimization of CC channels are to ensure uniformity in the temperature distribution, reduce the cooling time needed to reach the … ↩
-
Understand the role of sliders in managing complex undercuts.: Copyright reserved by https://www.ecomolding.com/ Due to the special requirements of a … ↩
-
Learn how curved parting lines aid in efficient demolding.: This guide explores the different types of parting line in injection molding, providing valuable insights on designing an effective one. ↩