Remember the first time you felt that rush of creating something that just worked perfectly?
Polypropylene is ideal for durable living hinges due to its flexibility, fatigue resistance, and cost-effectiveness, making it perfect for parts that undergo constant bending.
While polypropylene is a top contender, there’s a whole world of materials that might be the perfect fit for your specific needs. Think about it: the right choice can significantly impact not just the hinge’s lifespan but also how smoothly your product comes together. Let’s explore these materials further and see what each brings to the table.
Polypropylene is the most cost-effective for living hinges.True
Polypropylene is known for its cost-effectiveness and flexibility.
Nylon is more flexible than polypropylene for living hinges.False
Polypropylene generally offers better flexibility and fatigue resistance.
- 1. How Do Living Hinges Work and Why Are They Important?
- 2. Why is Polypropylene Preferred for Living Hinges?
- 3. Is Polyethylene a Good Choice for Living Hinges?
- 4. How Do Material Properties Affect Living Hinge Performance?
- 5. What Are the Best Practices for Designing with Living Hinges?
- 6. What New Materials Are Emerging for Living Hinges?
- 7. Conclusion
How Do Living Hinges Work and Why Are They Important?
Ever wondered how those flip-top lids on shampoo bottles work so smoothly? It’s all thanks to the magic of living hinges.
Living hinges are flexible plastic sections that connect two parts, allowing them to move. Crafted from polypropylene, they’re key in packaging and consumer products for their flexibility and durability.
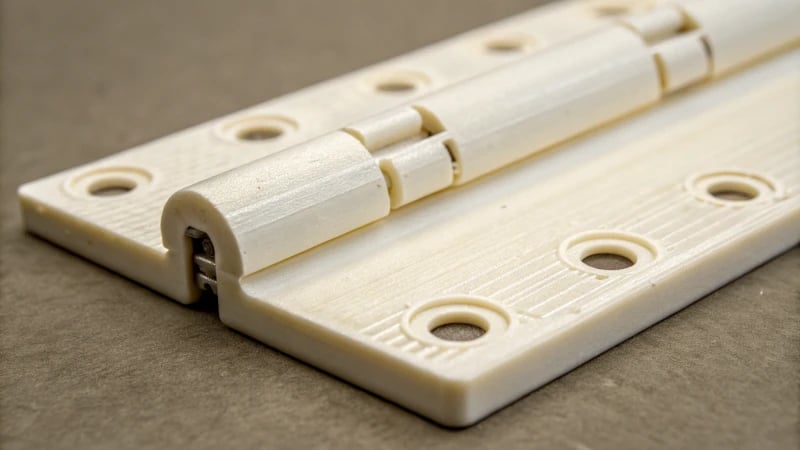
Understanding Living Hinges
Living hinges might sound like something out of a sci-fi movie, but they’re actually a marvel of everyday engineering. These flexible, tiny miracles are what keep the lids of your shampoo bottles or the covers of your remote controls working seamlessly, without ever breaking a sweat. I remember my first project involving living hinges—it was like unlocking a new level of design possibilities! They are crafted from a single piece of material, usually polypropylene, which is as tough as it is flexible, ensuring a perfect union of form and function.
Key Characteristics
- Material: Polypropylene reigns supreme here due to its incredible flexibility and resilience.
- Design: The secret sauce lies in the precise mold design, where every detail matters—from thickness to geometry. I’ve spent countless hours perfecting these in CAD simulations.
Material | Benefits |
---|---|
Polypropylene | Flexibility, Durability |
Nylon | Strength, Resilience |
HDPE | Chemical Resistance |
How Living Hinges Work
The true genius of living hinges is their ability to endure endless bending without snapping. This is due to the way polymer chains align during the molding process—a trick I’ve come to master over years of trial and error. When done right, these hinges can survive thousands of cycles, making them a cost-effective solution by eliminating the need for additional hinge components.
- Flexibility: They can handle high flexural stress with ease.
- Cost-Effective: No extra parts mean lower material costs—a win-win!
Applications in Product Design
In the world of design, living hinges are like the unsung heroes. Whether it’s securing closures in packaging or facilitating access in medical devices, their importance cannot be overstated. Just think about the convenience they bring to our everyday lives!
- Packaging: Those flip-top lids that make life easier.
- Consumer Goods: The humble yet vital battery covers.
- Medical Devices: Pill dispensers that open effortlessly.
Designing with Living Hinges
When it comes to incorporating living hinges into your projects, several factors come into play:
- Thickness: Finding that sweet spot for optimal flexibility and strength.
- Radius: Larger radii help reduce stress concentration—I learned this the hard way in my early designs!
- Cycle Life: Estimating how many flex cycles your design will endure.
With the power of computer-aided design (CAD1), it’s possible to simulate how these hinges will perform under various conditions before you even begin production. This technology is a game-changer, allowing us designers to push the boundaries of what’s possible with living hinge technology.
Polypropylene is the most common material for living hinges.True
Polypropylene offers flexibility and durability, ideal for living hinges.
Living hinges require separate components to function effectively.False
Living hinges are made from a single piece of material, no separate parts.
Why is Polypropylene Preferred for Living Hinges?
Ever wonder why polypropylene is the go-to material for living hinges? Its blend of flexibility and durability makes it a favorite among designers.
Polypropylene is ideal for living hinges due to its superior flexibility, fatigue resistance, and affordability, making it perfect for designs needing frequent bending without breaking.
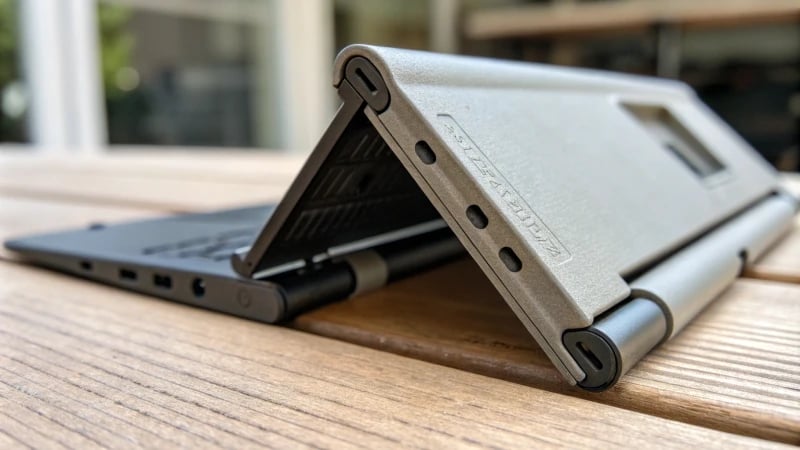
The Unique Flexibility of Polypropylene
When I first started working with living hinges, I quickly realized the importance of choosing the right material. It’s like trying to find the perfect partner who can bend without breaking—literally! Polypropylene’s molecular magic allows it to flex thousands of times without giving in to stress. For a designer2 like me, this flexibility is a game-changer, ensuring my creations can handle the wear and tear of everyday use.
Property | Polypropylene | Other Plastics |
---|---|---|
Flexibility | High | Medium |
Fatigue Resistance | Excellent | Good |
Resistance to Fatigue
I remember one of my earliest projects where we tested various materials for hinges in a consumer gadget. Many materials failed the repetitive open-close tests, except for polypropylene. Its resistance to fatigue means it holds up under pressure—ideal for products that are constantly in motion. Engineers3 and designers like myself value this trait for its long-term reliability, which is crucial in consumer electronics.
Cost-Effectiveness
Budget constraints are always looming in manufacturing. In one project, I was tasked with cutting costs without compromising quality. Polypropylene was my knight in shining armor. Its cost-effectiveness, due to easy processing and low raw material expenses, made it an attractive option. Plus, it allowed our team to stick to our budget without sacrificing performance. Manufacturers4 enjoy these savings too, making polypropylene a smart choice.
Balancing these factors is what makes polypropylene my go-to material for living hinges—offering not just functional benefits but also economic advantages.
Polypropylene has high fatigue resistance.True
Polypropylene maintains integrity over many cycles, crucial for living hinges.
Polypropylene is more expensive than other plastics.False
Polypropylene is cost-effective, offering economic advantages in manufacturing.
Is Polyethylene a Good Choice for Living Hinges?
Ever wondered if polyethylene is the right choice for those flexible living hinges? You’re not alone. Let’s dive into its potential and see if it meets the mark.
Polyethylene is suitable for living hinges, with high-density polyethylene (HDPE) being preferred for its superior flexibility and durability over low-density options.
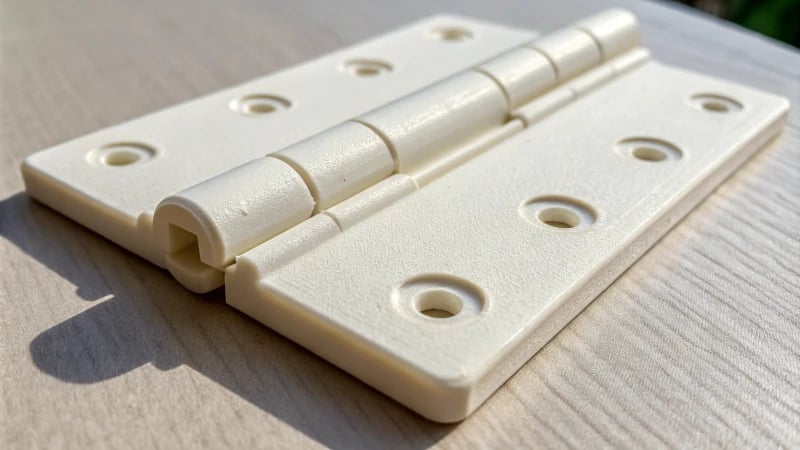
Understanding Living Hinges
I remember when I first stumbled upon the concept of living hinges. It was like discovering a secret passage in design—a thin, flexible hinge made from a single piece of plastic. Imagine the magic of creating something that bends and folds without any extra parts! In my work designing caps and flip-lids, this became an exciting puzzle to solve.
Living hinges are commonly used in applications like caps, containers, and flip-lids. The flexibility and durability of living hinges depend significantly on the material used.
Properties of Polyethylene
Polyethylene quickly became a staple in my toolkit. It’s a versatile polymer with qualities I came to appreciate: impact resistance, chemical stability, and ease of processing. Whether I was dealing with high-density polyethylene5 (HDPE) or low-density polyethylene6 (LDPE), each had its own charm.
Type | Density | Flexibility | Durability |
---|---|---|---|
HDPE | High | Moderate | High |
LDPE | Low | High | Moderate |
Advantages of Using Polyethylene
- Cost-Effectiveness: As someone who needs to watch project budgets closely, polyethylene’s affordability is a godsend compared to materials like polypropylene.
- Ease of Processing: Its moldability is a dream for creating intricate designs without breaking a sweat.
- Chemical Resistance: Its resilience against chemicals means longer-lasting products, something my clients always appreciate.
Limitations and Considerations
Despite its perks, I’ve learned there are a few caveats:
- Flexural Fatigue: LDPE’s limits become apparent when facing repeated bending—something polypropylene handles better.
- Temperature Sensitivity: Any significant temperature shifts can tweak its properties, which can be tricky to manage.
- Design Complexity: For those precise hinge designs, I often find myself needing advanced molding techniques.
Comparing Polyethylene with Other Materials
In my experience, polypropylene often edges out polyethylene in the living hinge department due to its fatigue resistance. Here’s a quick rundown:
Property | Polyethylene | Polypropylene |
---|---|---|
Fatigue Resistance | Moderate (HDPE) | High |
Temperature Range | Moderate | Wide |
Flexibility | High (LDPE) | Moderate |
If you’re designing something that demands extreme durability and frequent use, polypropylene7 might be your go-to. But remember, every project has its nuances—cost constraints, environmental factors, and more play into the decision.
Before settling on polyethylene for your living hinge project, I’d advise testing prototypes extensively. It’s fascinating how different molding techniques and material blends can tweak performance. Sometimes consulting with materials experts or diving deep into market research can open up new pathways you hadn’t considered before. In my journey, staying curious and experimenting has often led to the most rewarding discoveries.
Polyethylene is more cost-effective than polypropylene for hinges.True
Polyethylene is generally cheaper, making it a cost-effective choice for living hinges.
Polypropylene has better fatigue resistance than polyethylene.True
Polypropylene is preferred for living hinges due to its superior fatigue resistance.
How Do Material Properties Affect Living Hinge Performance?
Ever marveled at the magic behind those flexible plastic hinges in everyday items? Dive into the world of living hinges, where material properties make all the difference in performance.
Material properties like flexibility, tensile strength, and fatigue resistance impact living hinge performance. Choosing appropriate materials, such as polypropylene, enhances durability and functionality in product design.
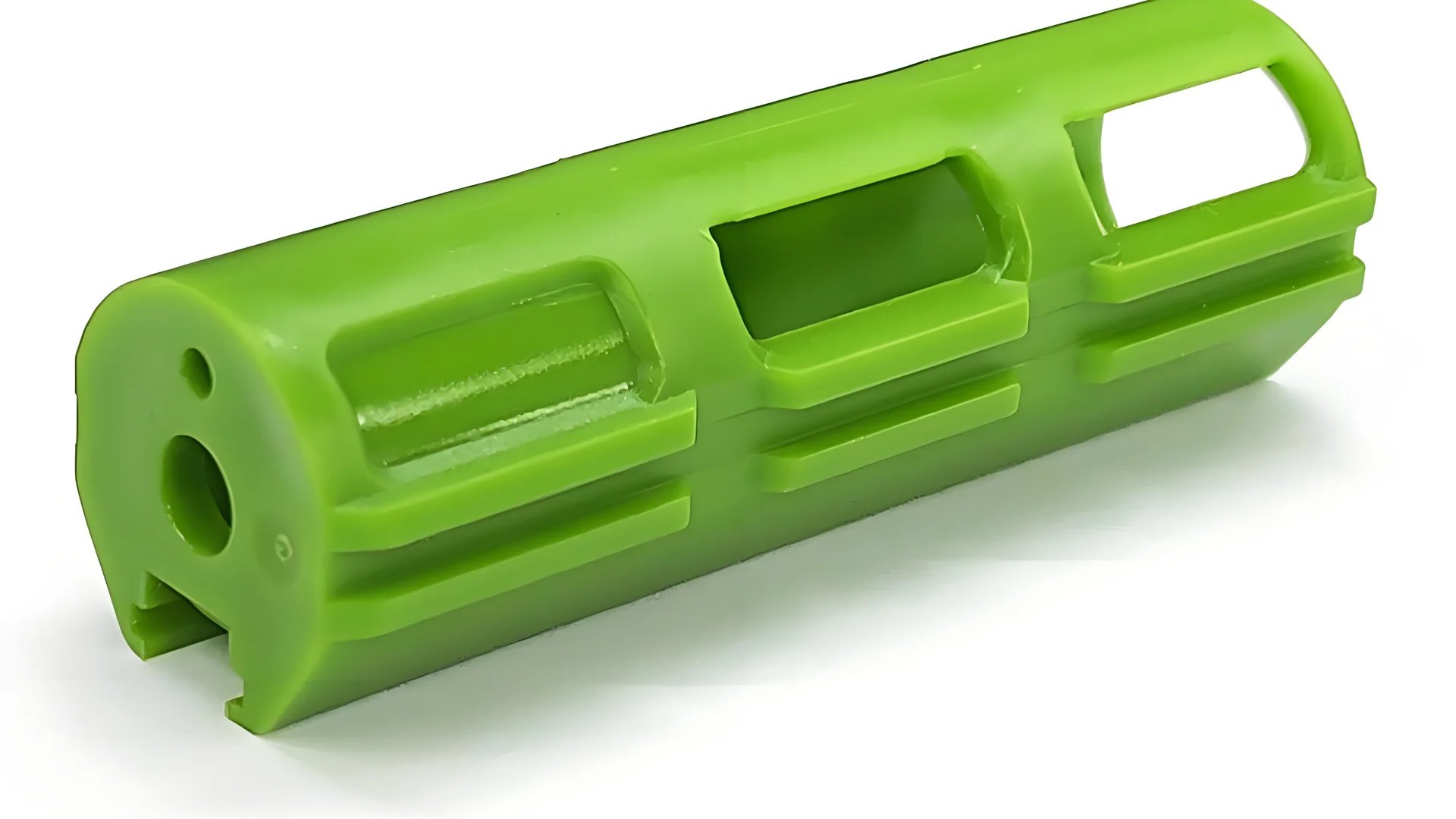
Key Material Properties Impacting Living Hinges
I remember the first time I encountered a living hinge in one of my designs. It was this simple, yet ingenious feature that made a world of difference. When designing a product with a living hinge, understanding the material properties is crucial. The primary properties to consider include:
-
Flexibility and Elasticity: There’s something almost magical about how materials like polypropylene can bend and flex repeatedly without breaking. Imagine a hinge that snaps back perfectly after each use—that’s what flexibility8 ensures.
-
Tensile Strength: Picture the strain a hinge undergoes in daily use. A high tensile strength means it won’t snap under pressure, keeping everything intact even when life gets a little rough.
-
Fatigue Resistance: It’s like running a marathon every day. Over time, repeated use can lead to material fatigue. Choosing a material with good fatigue resistance ensures your hinge keeps going strong for years.
-
Impact Resistance: Think of the occasional knock or bump your product might face. Opting for materials with higher impact resistance means your hinge can take it all in stride without cracking.
Material Selection: A Comparative Table
Property | Polypropylene | Polyethylene | Nylon |
---|---|---|---|
Flexibility | High | Moderate | Low |
Tensile Strength | Moderate | Moderate | High |
Fatigue Resistance | High | Low | High |
Impact Resistance | Moderate | High | Low |
Understanding Application Requirements
Once, while working on a consumer electronics project, I had to prioritize aesthetics and durability. For such applications, polypropylene’s balance of flexibility and strength made it the perfect choice. Understanding the specific application9 requirements is key to making the right call.
Innovations in Material Science
The field of material science is constantly evolving, bringing new possibilities to the table. I’m continually amazed at how emerging plastics offer superior durability10 and resilience, opening up fresh avenues for design innovation.
Exploring these materials and understanding their properties can vastly improve product design and functionality. By aligning material choices with design objectives, designers like us can achieve optimal performance in living hinges.
Polypropylene has high flexibility for living hinges.True
Polypropylene is preferred for its excellent flexibility, crucial for bending.
Nylon offers low fatigue resistance in living hinges.False
Nylon has high fatigue resistance, making it suitable for repeated use.
What Are the Best Practices for Designing with Living Hinges?
Designing with living hinges is like unlocking a whole new level of innovation for your products. Dive into these best practices to create designs that are not only cutting-edge but also stand the test of time.
For effective living hinge design, focus on choosing flexible materials such as polypropylene, ensuring uniform thickness in hinge geometry, and conducting thorough durability testing.
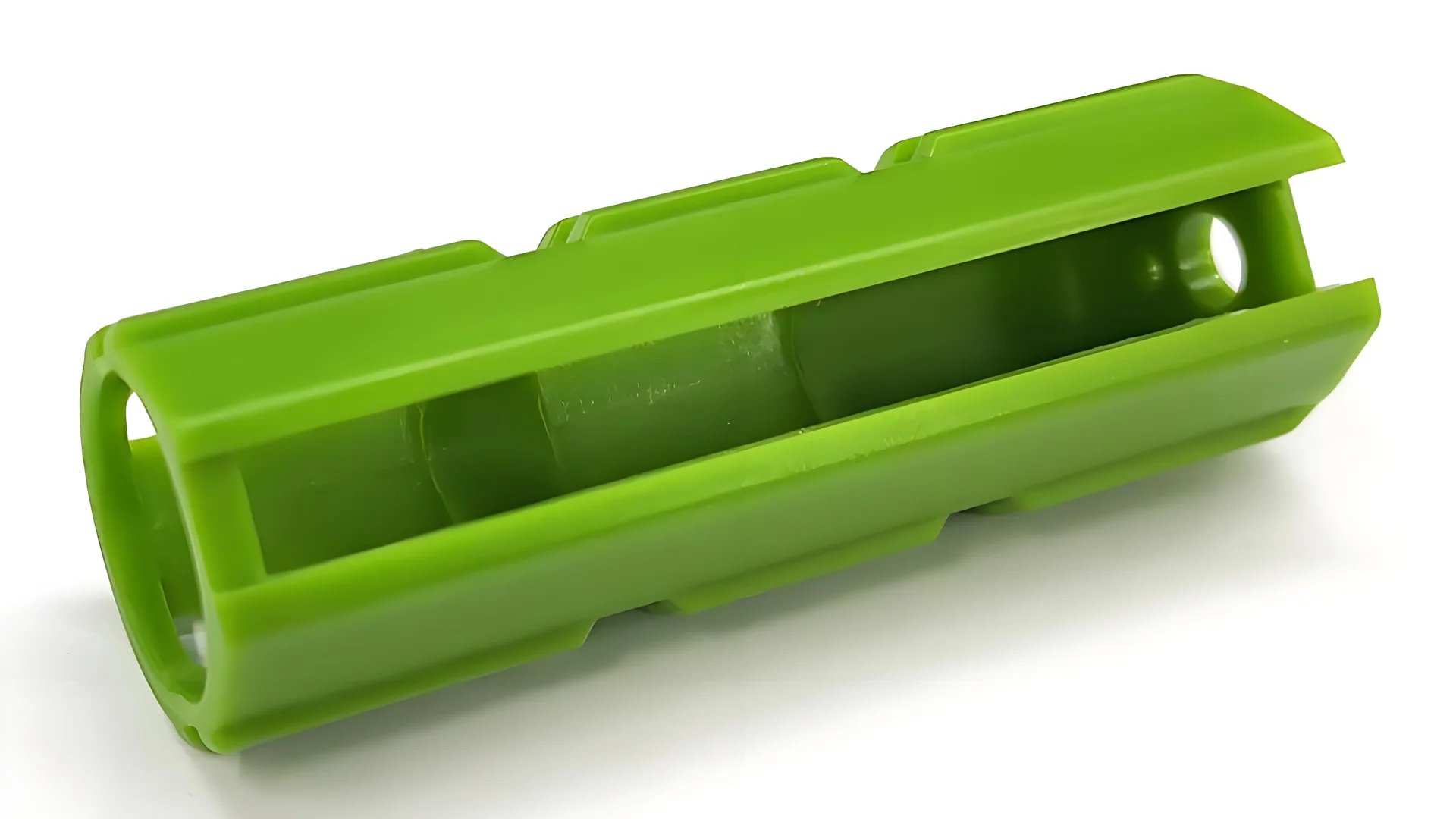
Material Selection
When I first started working with living hinges, I quickly learned that choosing the right material is everything. I remember a project where I picked a less flexible plastic just because it was cheaper, and boy, did I regret it when the hinge snapped after a few uses. Now, I stick to trusty options like polypropylene or polyethylene, known for their excellent flexibility and fatigue resistance. These materials can bend over and over without breaking, making them ideal for this kind of application. Take some time to explore the properties11 of different plastics to find the perfect match for your design.
Hinge Geometry
The geometry of the hinge is just as important as the material. I learned this lesson the hard way after my design’s sharp corners led to stress fractures. Since then, I’ve made sure to design with uniform thickness and add gentle radii instead of sharp edges. This approach helps distribute stress evenly and enhances the overall strength of the hinge. Utilizing CAD software12 can be a game-changer here; it allows you to visualize and perfect the geometry before moving forward.
Prototyping and Testing
Ah, prototyping—the phase where potential issues reveal themselves before they become costly mistakes. I always prototype my designs using 3D printing, which lets me identify weaknesses early on. One time, I skipped this step due to a tight deadline, only to find that my design didn’t perform well under repetitive motion. Since then, I’ve committed to conducting extensive testing, including cycle tests, to ensure durability. A comprehensive guide13 can offer valuable insights into refining your prototyping process.
Design Tips Table
Aspect | Best Practice |
---|---|
Material | Polypropylene or polyethylene for flexibility and fatigue resistance |
Thickness | Uniform thickness for even stress distribution |
Testing | Conduct cycle tests to ensure durability |
Geometry | Use radii instead of sharp corners to reduce stress concentrations |
Applications
Living hinges are everywhere once you start looking—plastic bottle caps, laptop covers, you name it. I often draw inspiration from these everyday examples when brainstorming new designs. Seeing how other products integrate hinges so seamlessly into their functionality never fails to spark new ideas in me. Exploring real-world examples14 might just give you that lightbulb moment for your next project.
Understanding these best practices is vital for getting the most out of your living hinge designs. Keep experimenting and pushing boundaries—you might just discover innovative ways to elevate your product’s design and functionality.
Polypropylene is ideal for living hinges.True
Polypropylene offers excellent flexibility and fatigue resistance, making it ideal for living hinges.
Sharp corners enhance hinge strength.False
Sharp corners increase stress concentrations, weakening the hinge's strength.
What New Materials Are Emerging for Living Hinges?
Ever marveled at how some parts bend without snapping? That’s the magic of living hinges, and they’re getting a makeover with new materials.
Innovative advanced polymers and bio-based plastics are emerging for living hinges, enhancing flexibility, durability, and sustainability while offering improved performance and environmental benefits.
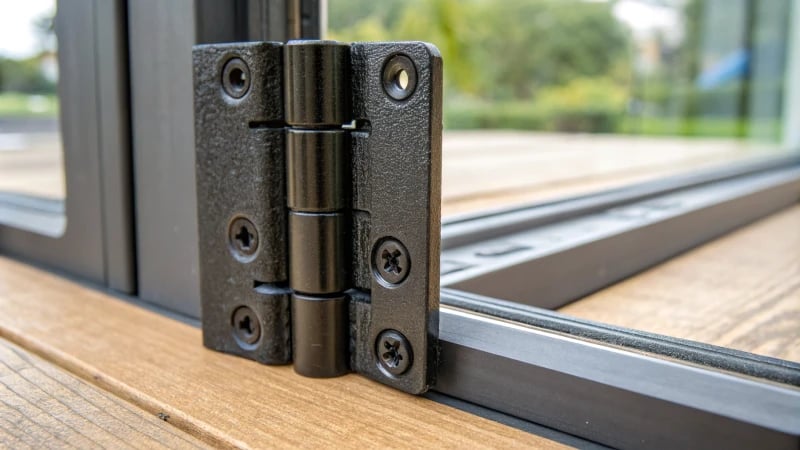
Advances in Polymer Science
Let me take you back to a time when I first stumbled upon the wonders of polymer science. I was knee-deep in a design project, struggling with brittle components. Then, I discovered thermoplastic elastomers (TPE). These incredible materials offer the flexibility of rubber but with the strength of plastic. It was a game-changer for applications needing constant bending.
Material | Key Properties | Applications |
---|---|---|
TPE | Flexibility, Resilience | Consumer electronics, toys |
Discover more about innovative materials15 for living hinges.
Bio-Based Plastics
Sustainability is more than just a buzzword—it’s an imperative. I remember my first encounter with bio-based plastics like polylactic acid (PLA). These materials come from renewable resources, like corn starch. They’re fantastic because they cut down on carbon emissions and yet maintain essential mechanical properties. It was fascinating to see how these could be integrated into eco-friendly product designs.
Explore how bio-based materials16 are reshaping our industry.
Additive Manufacturing and Customization
Ah, the joys of 3D printing! It’s like having a magic wand for prototyping. When I first used thermoplastic polyurethane (TPU) in 3D printing, I was amazed by its customizable strength and flexibility. This technology lets us design living hinges without the need for expensive molds.
Learn about 3D printing technologies17 transforming our design landscape.
Future Potential and Innovations
The future holds such promise with ongoing research into nanocomposites. Imagine polymers enhanced with nanoparticles for improved strength and thermal stability! It’s thrilling to think about the hybrid materials that could merge traditional durability with modern efficiency.
Stay informed on future material trends18 shaping our beloved living hinges.
TPE is more flexible than traditional polypropylene.True
TPE combines rubber and plastic properties, offering superior flexibility.
PLA is a synthetic plastic used in living hinges.False
PLA is a bio-based plastic, not synthetic, used for eco-friendly applications.
Conclusion
Polypropylene is the ideal material for durable living hinges due to its flexibility, fatigue resistance, and cost-effectiveness, essential for applications requiring repeated bending without failure.
-
Learn how CAD software aids in the design and simulation of living hinges, optimizing their performance and longevity. ↩
-
Understanding flexibility’s role helps designers create more durable products by selecting materials like polypropylene that endure frequent bending. ↩
-
Learning about fatigue resistance aids engineers in selecting materials that withstand repeated stress, ensuring longevity in applications. ↩
-
Exploring cost benefits reveals how polypropylene’s economical aspects make it a preferred material for manufacturers. ↩
-
Learn about HDPE’s characteristics and why it’s preferred for living hinges. ↩
-
Understand the flexibility and limitations of LDPE in hinge applications. ↩
-
Discover why polypropylene might be more suitable for durable living hinges. ↩
-
Polypropylene is widely used for its flexibility, making it ideal for living hinges that require durability over repeated use. ↩
-
Understanding application requirements helps in selecting materials that meet specific needs, ensuring product efficiency and longevity. ↩
-
Innovations in material science can significantly enhance hinge performance, making it beneficial to explore new options. ↩
-
Understanding plastic properties helps select materials that enhance hinge flexibility and durability. ↩
-
Discovering effective CAD tools can optimize the hinge design process through accurate modeling. ↩
-
A prototyping guide aids in identifying design weaknesses before full-scale production. ↩
-
Seeing real-world applications offers practical insights into successful hinge integration. ↩
-
Discover how modern polymers enhance living hinge design by improving flexibility and durability. ↩
-
Understand how sustainable materials like PLA are being integrated into product design. ↩
-
Explore the role of 3D printing in customizing and prototyping living hinges. ↩
-
Stay informed on emerging materials that may redefine living hinge applications. ↩