At the beginning of my product design journey, I quickly understood choosing the correct materials for molding processes is crucial. Selecting the right materials is very important for the success of a project. Let me share what I learned during this time.
Blow molding typically uses polyethylene (PE), polypropylene (PP), and PVC, while injection molding is best suited for polycarbonate (PC), nylon (PA), and ABS. Each material offers unique properties, making material selection crucial for successful product design and manufacturing.
I explored the world of molding. I found that polyethylene (PE), polypropylene (PP) and polyvinyl chloride (PVC) work well for blow molding. These materials have special traits. They suit different uses. For injection molding, polycarbonate (PC), nylon (PA) and ABS are popular. Knowing these choices helps in creating better products. It also improves how manufacturing proceeds. Understanding is crucial.
Polyethylene is ideal for blow molding processes.True
Polyethylene (PE) is favored in blow molding due to its flexibility and durability, making it suitable for various applications.
Nylon is the best material for blow molding.False
Nylon is primarily used in injection molding, not blow molding, as it has different properties suited for that process.
What Should I Consider When Choosing Molding Materials?
Selecting the proper molding material goes beyond technical choices. This step involves discovering the best option for your vision and project. Let’s explore the crucial factors in this important decision.
When selecting molding materials, think about their mechanical strength. Assess how they handle processing techniques. Identify the needs of the application. Consider the environmental impact. Examine how cost-effective the materials are. Check the reliability of the supplier. Every factor is crucial. Each aspect helps your projects succeed. You want them to meet functional goals. Aesthetic requirements are important too.
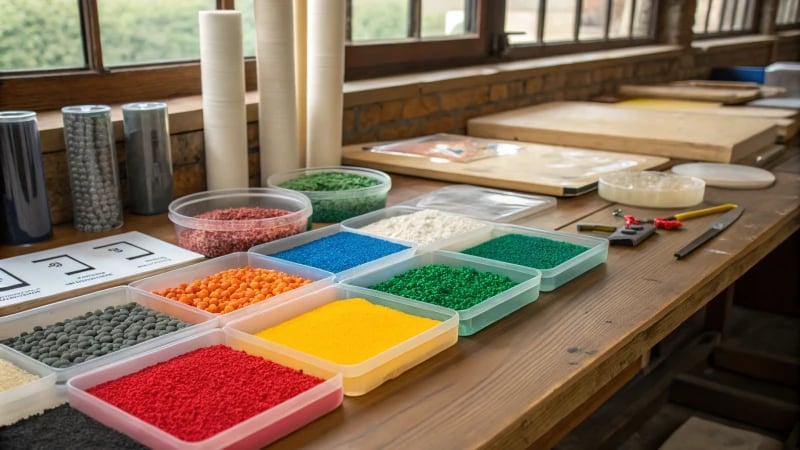
When I began with product design, I stood before a wall full of materials. Choices overwhelmed me. This taught me how important selecting the correct molding material is. It affects how well our products work and their quality. Here are key factors I learned to think about:
Material Properties
Knowing the basic properties of molding materials is crucial. For example:
- Mechanical Strength: Nylon (PA) often impresses me with its strong and durable nature. It performs well in challenging situations where one cannot afford to fail.
- Chemical Resistance: In some projects, I like to use Polypropylene (PP). It resists harsh chemicals well. It lasts long even in hard environments.
Processing Techniques
The technique for molding affects material choice greatly:
- Blow Molding: Polyethylene (PE) and Polyvinyl Chloride (PVC) offer flexibility. They process easily and help me create hollow parts. They never let me down in terms of quality.
- Injection Molding: Polycarbonate (PC) and Acrylonitrile-Butadiene-Styrene Copolymer (ABS) are favorites. They often achieve precise sizes and complex shapes for my designs. They succeed repeatedly.
Molding Technique | Suitable Materials | Key Characteristics |
---|---|---|
Blow Molding | PE, PVC | Flexibility, ease of processing |
Injection Molding | PC, ABS | High precision, complex shapes |
Application Requirements
Your exact needs guide material choice:
- Temperature Tolerance: Checking if products need to endure high heat is always on my mind. PP remains my choice for staying strong under heat.
- Aesthetic Qualities: Appearance often matters. Materials like PC provide transparency and a shiny finish. They are really essential.
Environmental Considerations
Sustainability has recently become very important to me:
- Recyclability: I choose materials like HDPE whenever I can. They perform well and lower waste by recycling.
- Additives Impact: In past projects with PVC, I learned to be careful about additives. They might cause environmental problems.
Cost vs. Performance
Balancing cost and performance is essential:
- I have faced projects where expensive materials tempted me. Yet, I found that LDPE often fits my needs without costing too much while keeping good quality.
Supplier Reliability
Reliable suppliers are very valuable:
- Consistent quality and material availability influence my production timing. It affects project success significantly.
For more information on materials for blow molding and injection molding, explore our resources on material selection1 and processing techniques2. They have helped me greatly in decision-making. They lift my designs to a higher level.
Nylon is known for its high mechanical strength and durability.True
Nylon (PA) offers exceptional strength, making it ideal for demanding applications where durability is crucial.
PVC is suitable for injection molding due to its flexibility.False
PVC is primarily used in blow molding, while injection molding favors materials like PC and ABS for precision.
What Are the Key Differences Between Blow Molding and Injection Molding?
Let’s explore the interesting world of plastic manufacturing! Knowing the differences between blow molding and injection molding is very important. This knowledge, especially if trying to improve production, helps meet specific design needs.
Blow molding inflates a hot tube of plastic inside a mold. This process forms empty plastic parts. It works well for materials like polyethylene. Injection molding, on the other hand, injects melted plastic into molds. This creates solid parts. It fits detailed shapes and different materials very effectively.
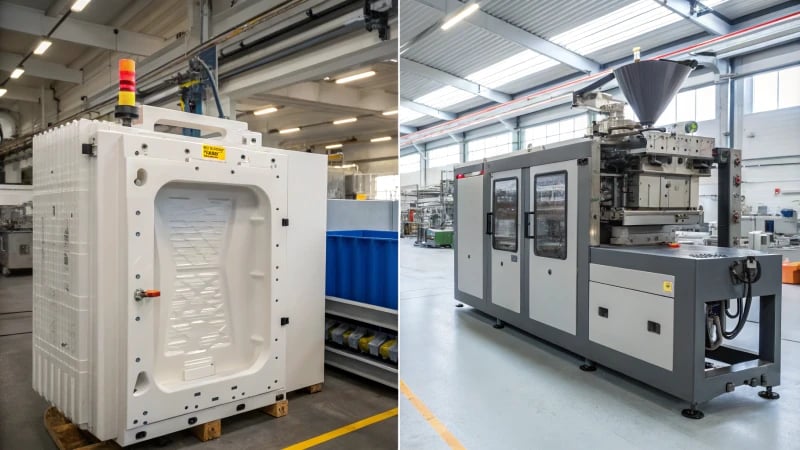
Understanding Blow Molding
In my journey as a designer, I often faced choices between blow molding and injection molding for projects. Each method has unique strengths. Knowing when to choose each is really important for the final product. Let’s explore these two techniques together!
Blow molding is a manufacturing process primarily used for producing hollow plastic parts. This method is well-suited for materials like Polyethylene (PE) and Polypropylene (PP), which are commonly used to create items like bottles and containers. The blow molding process involves creating a parison, which is a heated tube of plastic that is inflated to fill a mold. This allows for the production of products with consistent wall thickness and various shapes.
For example, Low-Density Polyethylene (LDPE) is often used in the production of flexible plastic bags due to its excellent flexibility and transparency. In contrast, High-Density Polyethylene (HDPE) is preferred for durable items like industrial barrels because of its high strength and resistance to wear.
Exploring Injection Molding
Injection molding is different. The first time I saw it, it felt magical! This method injects molten plastic into a mold to form solid parts. It’s wonderful for making complex shapes with high precision. Materials such as Acrylonitrile-Butadiene-Styrene (ABS) and Nylon (PA) excel in this process.
When I design electronic device components, I use Polycarbonate (PC) for its impact resistance and clarity. PC fills every mold detail perfectly, creating flawless products that meet strict standards. It’s perfect for things like automotive parts where strength and detail are essential.
Comparison of Materials Used
Here’s a comparative table summarizing the suitable materials for each process:
Process | Material | Key Characteristics | Common Applications |
---|---|---|---|
Blow Molding | Polyethylene (PE) | Flexible, transparent | Plastic bags, containers |
Low-density polyethylene (LDPE) | Good flexibility, uniform wall thickness | Films, small hollow containers | |
High-density polyethylene (HDPE) | High strength, good wear resistance | Trash cans, industrial barrels | |
Polypropylene (PP) | Heat resistant, good fluidity | Food packaging, chemical containers | |
Injection Molding | Polycarbonate (PC) | High transparency, impact resistance | Electronic housings, optical lenses |
Nylon (PA) | Good mechanical properties, wear resistance | Automotive parts, gears | |
Acrylonitrile Butadiene Styrene (ABS) | High hardness, toughness | Toys, appliance housings |
Cost and Efficiency Considerations
In different projects, I learned that cost and efficiency guide the choice between blow molding and injection molding. Blow molding is more affordable for large volumes of hollow parts like big bottles or containers. Injection molding offers precision for intricate designs. It’s like choosing between a cozy sweater and a tailored suit; each suits different needs.
If you’re curious about these techniques and want to learn more for your own projects, explore Blow Molding Techniques3 or Injection Molding Insights4. We can expand our knowledge and application of these key manufacturing processes!
Blow molding is ideal for hollow plastic products.True
Blow molding efficiently produces hollow items like bottles by inflating a heated tube of plastic, making it suitable for materials like polyethylene.
Injection molding can create more complex shapes than blow molding.True
Injection molding allows for intricate designs and high precision, making it better suited for complex parts compared to blow molding.
What Are the Environmental Impacts of Different Molding Materials?
Do you ever think about the materials we use in designs and their effect on Earth? Let’s explore how choosing different materials helps create a more sustainable future for everyone.
Environmental impacts of molding materials differ greatly. Polyethylene, for instance, offers recyclability and is widely used. However, PVC creates major worries because it produces toxic emissions throughout its life. Knowing these effects is vital. It is very crucial for designers to choose sustainable options.
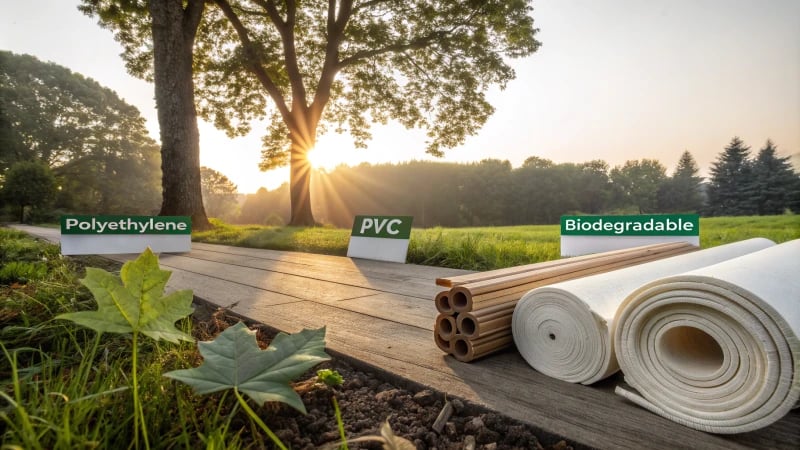
Understanding the Environmental Impact of Molding Materials
The environmental impacts of different molding materials are crucial for making informed decisions in product and mold design. Each material not only affects the final product’s performance but also has distinct ecological footprints.
For example, polyethylene (PE), often used in blow molding, is known for its recyclability. However, its production can contribute to significant greenhouse gas emissions. In contrast, polyvinyl chloride (PVC) poses concerns due to chlorine content, raising issues about dioxin emissions during its lifecycle. To understand the balance between performance and sustainability, let’s explore various materials used in both blow and injection molding.
Blow Molding Materials and Their Environmental Footprints
Material | Key Properties | Environmental Concerns |
---|---|---|
Polyethylene (PE) | Lightweight, flexible | Recycling challenges, emissions during production |
Low-Density Polyethylene (LDPE) | Good flexibility, soft texture | Low recyclability compared to HDPE |
High-Density Polyethylene (HDPE) | Strong and durable | Energy-intensive production process |
Polypropylene (PP) | Chemical stability, heat resistance | Often not recycled, contributing to landfill waste |
Polyvinyl Chloride (PVC) | Flexible, versatile | Toxic emissions during processing, hard to recycle |
When I think of LDPE, plastic bags come to mind. They are everywhere but tough to recycle. Meanwhile, HDPE feels like a dependable friend. It is strong and used for things like trash cans5 and barrels. However, producing it requires a lot of energy. Then there’s polypropylene (PP). It is common in food packaging. Yet, its recycling problems trouble me.
Injection Molding Materials and Their Ecological Impact
Material | Key Properties | Environmental Concerns |
---|---|---|
Polycarbonate (PC) | High impact resistance | Not widely recyclable, energy-intensive production |
Nylon (PA) | Durable, chemical resistant | Environmental degradation from production processes |
Acrylonitrile-Butadiene-Styrene (ABS) | Good toughness, color processing | Difficult to recycle, hazardous waste in production |
I worked on a project with polycarbonate. Its strength amazed me for applications like electronic covers6. Still, the environmental cost of making it is significant. Similarly, ABS works well for products like toys and appliance cases but poses recycling challenges that contribute to plastic pollution.
Sustainable Alternatives and Practices
To mitigate these impacts, many companies are exploring sustainable alternatives such as bio-based plastics or implementing recycling programs. For instance, I now look into options like biodegradable materials for a tiny project I once did; it made me feel like I was really helping the planet. Little steps like this maybe lead to big changes.
By examining these materials’ properties and their effects on the environment through studying them closely,
designers probably make better choices. Sustainable design principles encourage balancing functionality with ecological responsibility. This approach not only promotes better environmental practices but also caters to the growing consumer demand for eco-friendly products.
Polyethylene is a recyclable molding material.True
Polyethylene (PE) is known for its recyclability, making it a preferable choice among molding materials despite its production emissions.
PVC has low environmental concerns compared to other materials.False
PVC poses significant environmental issues due to dioxin emissions and challenges in recycling, making it less favorable than other materials.
What Innovations Are Emerging in Molding Material Technologies?
Interested in the latest progress in shaping materials? Exciting developments are changing the industry. These advancements are creating new paths for eco-friendly and effective production.
Molding material innovations include advanced polymer mixes. These mixes are really strong and last longer. Smart materials react to changes in the environment. This is very impressive. Gas-assisted injection molding is an enhanced technique in processing. It improves efficiency. New developments focus on recyclable and biodegradable materials. Environmental sustainability truly matters in material technology.
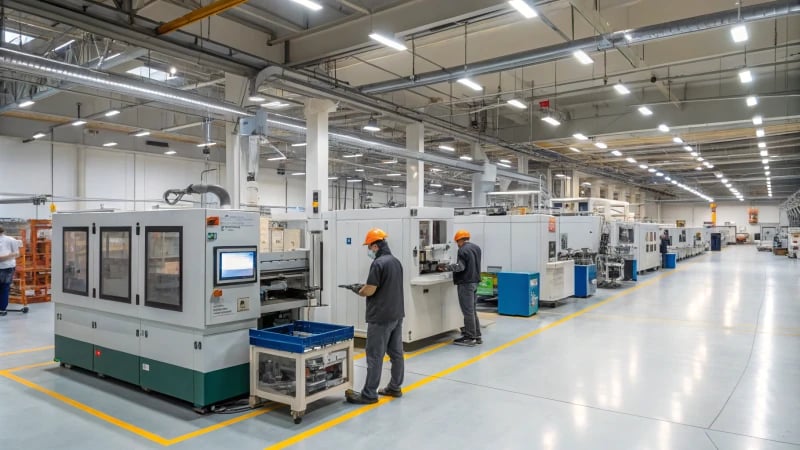
Emerging Innovations in Molding Materials
The field of molding material technologies is experiencing rapid advancements driven by the demand for more efficient, versatile, and sustainable solutions. Here are some of the key innovations emerging in this domain:
1. Advanced Polymer Blends
Innovations in polymer blending techniques are leading to materials that combine the best properties of different plastics. For instance, blends of Polycarbonate (PC) and Acrylonitrile-Butadiene-Styrene (ABS) are becoming popular due to their enhanced impact resistance and aesthetic appeal. These blends are ideal for products that require both durability and attractive finishes, such as electronics housings.
Additionally, companies are exploring bio-based polymers, which not only reduce reliance on fossil fuels but also offer a lower carbon footprint. The move towards more sustainable materials is driven by both consumer demand and regulatory pressures. For detailed insights into the sustainability aspects of these materials, see sustainable polymer innovations7.
2. Smart Materials
The integration of technology into molding materials is another exciting innovation. Smart polymers that can respond to environmental stimuli (such as temperature or pH changes) are being developed for various applications, including medical devices and packaging. These materials can change properties dynamically, offering enhanced functionality and user interaction.
For example, researchers are developing shape-memory polymers that can revert to a pre-defined shape upon heating. This capability opens up new avenues in product design and manufacturing processes. To explore more about smart materials, check out smart polymers and their applications8.
3. Enhanced Processing Techniques
New processing techniques such as gas-assisted injection molding and microcellular foam technology are revolutionizing traditional molding processes. These methods allow for lighter products with improved structural integrity and reduced material usage.
- Gas-assisted injection molding introduces gas into the mold during the injection process, creating hollow sections in parts which significantly reduces weight without compromising strength.
- Microcellular foam technology involves creating a foamed structure within the material, allowing for better insulation properties and further weight reduction.
The table below summarizes the advantages of these advanced processing techniques:
Technique | Advantages | Applications |
---|---|---|
Gas-Assisted Injection Molding | Lightweight, strong structures | Automotive parts, consumer goods |
Microcellular Foam Technology | Better insulation, reduced weight | Packaging, electronic components |
To learn more about these processing techniques, see advancements in injection molding9.
4. Recyclable and Biodegradable Materials
The push for sustainability is prompting innovation in the development of fully recyclable and biodegradable materials. Companies are now focusing on creating plastics that can be easily recycled or that break down naturally in the environment.
Examples include new formulations of Polyethylene (PE) and Polypropylene (PP) that incorporate additives to enhance biodegradability without compromising their mechanical properties. This innovation is crucial for reducing plastic waste and meeting global environmental standards.
For more on recycling technologies and biodegradable options, refer to recycling advancements in plastics10.
Advanced polymer blends improve product durability and aesthetics.True
Combining materials like PC and ABS enhances impact resistance and visual appeal, ideal for electronics housings.
Smart materials can change properties with environmental stimuli.True
Innovations like shape-memory polymers allow products to adapt dynamically, enhancing functionality in various applications.
Conclusion
This article explores the best materials for blow and injection molding processes, highlighting key properties and environmental considerations to guide effective product design.
-
Explore in-depth guides on how to choose the best molding materials based on application needs and processing techniques to enhance your design projects. ↩
-
Learn about the properties of different molding materials to make informed choices that align with your production requirements. ↩
-
Discover detailed comparisons between blow molding and injection molding processes to enhance your manufacturing knowledge. ↩
-
Learn about the best practices for selecting between blow molding and injection molding for your specific project needs. ↩
-
Explore the recycling challenges associated with various molding materials and learn about eco-friendly options. ↩
-
Learn about sustainable practices in product design that can minimize environmental impacts when selecting molding materials. ↩
-
Explore cutting-edge advancements in molding materials that could elevate your design projects and enhance production efficiency. ↩
-
Dive into smart material technologies that can transform product design and manufacturing processes. ↩
-
Find out how advanced processing techniques are changing the landscape of injection molding. ↩
-
Learn about sustainable materials that are making waves in the industry while benefiting the environment. ↩