Choosing the right material for mold crafting might feel confusing. You might stand and stare at all the choices, unsure about what to select. How does someone find the best option?
Choosing the best material for your mold depends on factors like durability, thermal conductivity, and the type of product. Common options include steel, aluminum, and pre-hardened steel. Consider cost, production volume, and material compatibility to select the optimal choice for performance and longevity.
In this post, I share important insights that have guided me through challenging situations. Early in mold design, I did not realize the importance of considering the specific needs of each mold. Each situation, like small batches or large-scale production, required its own method. I once needed a mold for a prototype, so I chose aluminum alloy for its affordability and easy processing. It worked really well! However, high-quality mold steel like P20 was necessary for mass production to guarantee long-lasting strength and accuracy.
Knowing the material’s performance is very important. I discovered this when a material I used was not tough enough for injection molding. Cracks appeared, reminding me that strength truly matters. Cost is another crucial element. I often balanced material choices with budget limits. Sometimes I got creative with my designs to pick a cost-effective yet efficient option. By considering these aspects, I have grown more confident in selecting materials for my projects. I hope these insights help you too!
Aluminum alloys are best for small batch mold making.True
Aluminum alloys offer cost-effectiveness and efficiency for producing molds in small quantities, making them ideal for limited production runs.
High-quality mold steels are unnecessary for low-volume production.True
For low-volume production, high-quality mold steels may not be required, as they are more suited for mass production due to their durability and cost.
What Factors Should You Consider When Choosing Mold Materials?
Selecting the right mold materials might seem confusing. However, it does not need to be. Key factors guide you to the best choice for your manufacturing needs. Are you ready to explore?
When choosing mold materials, think about how you will use them. Consider batch size. Consider precision needs. Hardness and toughness are important too. Keep cost in mind. Balancing quality and budget is very important. This balance is essential for successful manufacturing.
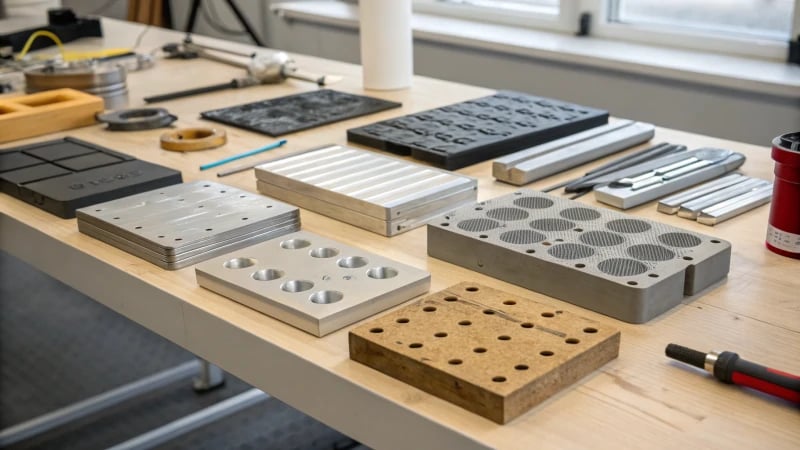
1. Use Requirements of the Mold
When selecting mold materials, it’s essential to consider the use requirements of the mold. Factors such as the batch size of molded products play a significant role in material choice.
For small batches, you might opt for flexible materials like aluminum alloy, which is cost-effective and easy to process. In contrast, mass production demands stronger materials, such as high-quality mold steel like P20, which withstands numerous cycles and ensures precision.
Precision Requirements
High-precision molds require materials with low thermal expansion coefficients. Beryllium bronze is an excellent choice as it maintains dimensional stability under temperature variations, making it suitable for precision components.
Complexity of Molded Products
Complex shapes necessitate materials with excellent toughness and machinability. H13 steel is ideal for intricate designs, providing the necessary strength to avoid cracking during production.
Molding Pressure and Temperature
Materials must withstand the conditions under which they will be used. For high-pressure and temperature applications, ceramic materials shine due to their stability in extreme environments.
2. Performance Characteristics of the Material
Performance characteristics of mold materials are critical in ensuring durability and effectiveness.
Characteristic | Importance | Example Material |
---|---|---|
Hardness and Strength | Resists wear and prevents deformation | Cr12MoV steel |
Toughness | Withstands impact and stress | 45 steel |
Corrosion Resistance | Maintains integrity when molding corrosive plastics | 304 stainless steel |
Thermal Conductivity | Aids in rapid heat dissipation, improving efficiency | Copper alloys |
Hard materials like Cr12MoV resist wear during the molding process, while tough materials like 45 steel prevent cracking from rapid injections of plastic melt. If working with corrosive components, opting for stainless steel ensures longevity.
3. Cost Factors
Cost considerations are paramount in material selection, balancing quality with budget constraints. Different materials carry various price tags; high-performance steels tend to be pricier compared to carbon steels.
Processing Costs also play a crucial role; some materials may be affordable but challenging to process, leading to higher overall costs.
Material | Base Cost | Processing Difficulty | Total Cost Estimate |
---|---|---|---|
High-Performance Steel | High | Moderate | High |
Carbon Steel | Low | Easy | Moderate |
Titanium Alloys | Very High | Very Difficult | Very High |
For projects on a budget, optimizing the mold design can allow for the use of lower-cost materials without compromising functionality.
Aluminum alloy is ideal for mass production molds.False
Aluminum alloys are cost-effective for small batches but not suitable for mass production due to their lower strength compared to high-quality mold steel.
H13 steel is suitable for complex molded shapes.True
H13 steel offers excellent toughness and machinability, making it ideal for intricate designs that require durability during production.
How Do Different Materials Compare in Terms of Cost and Performance?
Moving through the world of materials feels overwhelming. It is, however, important for choosing wisely in product design. Join me. Explore with me how costs and performance compare. I will share insights from my own journey in this fascinating field.
Compare materials by looking at cost and performance. Examine factors like batch size, precision needs, complexity and processing expenses. These considerations help in selecting the best option for your project.
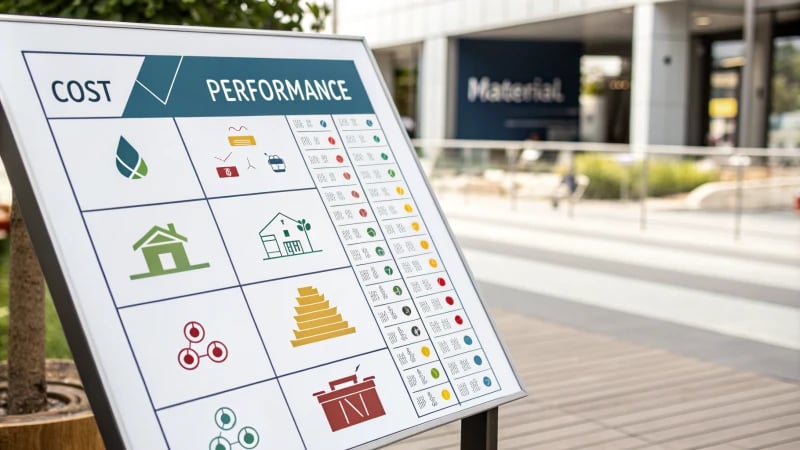
Evaluating Material Use Requirements
The selection of materials for molds is significantly influenced by their intended use. For instance, if you’re working on a batch of molded products, the choice of material can vary greatly.
- Small Batches: When producing molds in small batches, flexibility in material selection is essential. A common choice here is aluminum alloy, which offers good processing performance at a lower cost. This makes it ideal for quick manufacturing without sacrificing quality.
- Mass Production: In contrast, for large-scale production, high-quality mold steel, such as P20 steel, is often necessary. This material provides excellent hardness, ensuring dimensional accuracy and surface quality over numerous molding cycles.
- Precision Requirements: For high-precision components, materials like beryllium bronze are recommended due to their low thermal expansion coefficient, which helps maintain accuracy during temperature fluctuations.
- Complex Shapes: If the mold requires intricate designs, the toughness and machinability of the material become crucial. Materials like H13 steel are suitable for such applications, providing the necessary durability and resistance to thermal fatigue.
Performance Characteristics of Materials
The performance characteristics of different materials are fundamental to their effectiveness in molding applications. Here’s a breakdown:
Characteristic | Description | Example Material |
---|---|---|
Hardness and Strength | High hardness resists wear; strength prevents breakage under pressure. | Cr12MoV steel |
Toughness | Good toughness allows materials to withstand impact and stress. | 45 steel |
Corrosion Resistance | Materials must resist corrosion from certain plastics. | 304 stainless steel |
Thermal Conductivity | Efficient heat dissipation during molding improves quality and efficiency. | Copper alloys |
Cost Considerations in Material Selection
Cost plays a pivotal role in determining which materials to use. Different materials come with varying price tags:
- High-Performance vs. Cost-Effective: While high-performance mold steels can be expensive, options like ordinary carbon steels might be more budget-friendly. For projects constrained by finances, optimizing mold design can help utilize less costly materials without compromising essential performance metrics.
- Processing Costs: It’s important to consider that some materials, despite being inexpensive, may incur high processing costs due to their complexity. For example, titanium alloys offer excellent performance but can be challenging and costly to work with.
Conclusion: Balancing Cost and Performance
Selecting the right material involves a careful balancing act between cost and performance. Various factors—including batch size, precision requirements, complexity, and inherent material properties—must be meticulously evaluated to make informed decisions. To explore these factors further, you can refer to resources such as material comparison tools1 or best practices for material selection.
Aluminum alloy is ideal for small batch mold production.True
Aluminum alloy's flexibility and lower cost make it suitable for producing molds in small batches without compromising quality.
P20 steel is best for high-precision components.False
P20 steel provides excellent hardness, ensuring dimensional accuracy for high-precision molding applications.
What Are the Advantages of Using Advanced Materials for Mold Making?
Did you ever think about how advanced materials change the mold process? I have thought about it. Believe me, the advantages are huge! These materials improve your production and save money over time.
**Advanced materials definitely improve mold production. They increase product quality, raise efficiency and cut costs over time. These materials offer strength and reduce maintenance. Complex designs become easier to create and meet modern demands. So, projects become less troublesome and more successful for us!
Let’s explore why these materials are so important for designers and engineers!
Improved Performance
Performance in mold making reminds me of a project with P20 steel. This material had high hardness and strength. Our molds lasted through many cycles without wear. This resulted in fewer replacements and repairs. A real dream in a busy work setting.
Materials with high thermal conductivity, like copper alloys, also impressed me. They managed heat well during molding. Production efficiency increased and product quality improved, with less shrinkage and deformation. Truly a win-win situation!
Cost Efficiency
At first, advanced materials may seem expensive. Trust me, they are worth it. I remember choosing P20 steel over cheaper options. This choice saved us money in the long run because of its durability. Here’s a simple comparison of different materials꞉
The right material really changes how you balance budget and quality.
Flexibility in Design
Advanced materials offer very flexible design options. In several projects, beryllium bronze was vital. It kept shape under temperature changes. This mattered a lot for precise electronic components. Our designs exceeded my past attempts!
Lower Maintenance Needs
Let’s chat about maintenance. Everyone loves it, right? Joking aside, using strong materials like 45 steel has really cut our maintenance needs. These materials survive impacts during production, increasing uptime and productivity. Just last week, operations ran much smoother with fewer mold repairs.
Ceramic composites are superb for high-temperature uses. They resist breakdowns better than older materials. This means less trouble and more time for creativity and innovation in designs!
Conclusion꞉ A Smart Choice
Picking advanced materials in mold making isn’t just about technology. It’s part of a big plan focusing on efficiency, strength and design flexibility. Designers like Jacky aim to craft superb components for consumer electronics. Understanding these benefits is crucial for wise decisions. If curious about selecting materials better, consider advanced material benefits . You won’t regret it!
In my mold-making experience, learning about material choice has shaped my design ideas. It led to more successful projects. Let’s embrace these advancements together!**
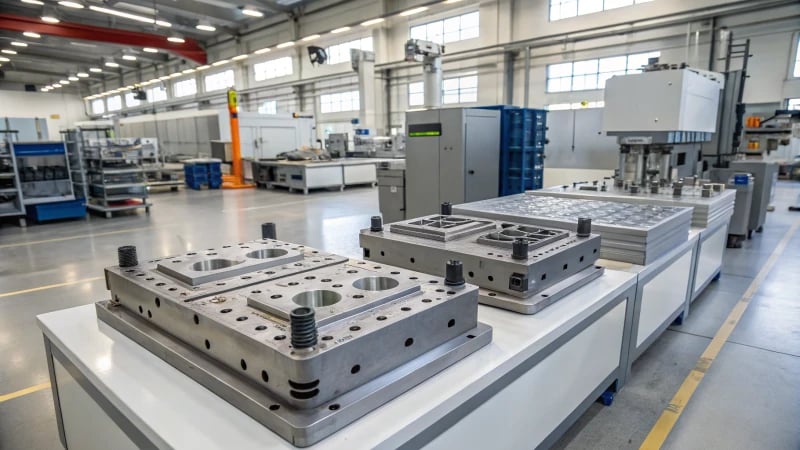
Advanced Materials in Mold Creation
Advanced materials in mold creation offer more than just following trends. They represent a very improved work process that truly benefits us. I recall my early years as a designer when the variety of materials confused me. Today, selecting the right materials allows for molds with longer life and enhanced performance. I’m eager to share these insights with you!
Enhanced Performance
Using advanced materials in mold making offers significant improvements in performance. For instance, materials like P20 steel possess high hardness and strength, enabling molds to endure numerous cycles without deformation.
This durability translates into a longer lifespan for the mold, thus reducing the need for frequent replacements or repairs. Furthermore, materials with high thermal conductivity, such as copper alloys, assist in effective heat dissipation during the molding process. This not only improves production efficiency but also enhances the quality of the molded products, reducing shrinkage and deformation.
Cost Efficiency
While advanced materials can be more expensive initially, they can lead to cost savings over time. The table below illustrates the cost-benefit relationship of various materials used in mold making:
Material Type | Initial Cost | Durability | Processing Cost | Long-term Savings |
---|---|---|---|---|
Aluminum Alloy | Low | Moderate | Low | Medium |
P20 Steel | Medium | High | Medium | High |
H13 Steel | Medium | High | Medium | High |
Titanium Alloys | High | Very High | High | Low |
Choosing the right material based on your production needs and budget can optimize long-term savings.
Flexibility in Design
Advanced materials allow for more complex mold designs. For example, using beryllium bronze can maintain dimensional stability under temperature fluctuations, which is crucial for high-precision applications like electronic components. This flexibility leads to better product designs that were previously challenging to achieve.
Reduced Maintenance Needs
The use of tough materials, such as 45 steel, enhances mold resilience against impacts during production. This toughness minimizes wear and tear and reduces maintenance requirements, leading to increased uptime and productivity.
Advanced materials such as ceramic composites are also resistant to high temperatures and pressures, making them suitable for demanding applications. This resistance translates into fewer breakdowns and repairs, further enhancing efficiency in production processes.
Conclusion: A Strategic Choice
Selecting advanced materials for mold making is not just about immediate performance; it encompasses a broader strategy of efficiency, durability, and design flexibility. As product and mold designers like Jacky seek to create high-quality components for consumer electronics, understanding these advantages is crucial in making informed decisions. For further insights into material selection strategies, consider exploring advanced material benefits2.
Advanced materials improve mold performance and lifespan.True
Using materials like P20 steel enhances durability, allowing molds to withstand more cycles without deformation, leading to longer lifespans and fewer replacements.
Advanced mold materials are always cost-effective initially.False
While advanced materials may have higher initial costs, their durability and efficiency lead to long-term savings, making them cost-effective over time.
How Can I Optimize My Mold Design for Better Material Selection?
If you are exploring mold design, you might ask how to select suitable materials for your projects. Some key strategies really helped me in my own path as an engineer. Let’s look at them together.
Understand the use requirements to choose the best material for your mold design. Learn about the performance characteristics of different materials. Consider cost factors carefully. Assess these elements thoughtfully. This approach helps improve efficiency and product quality in injection molding. Your product quality gets better.
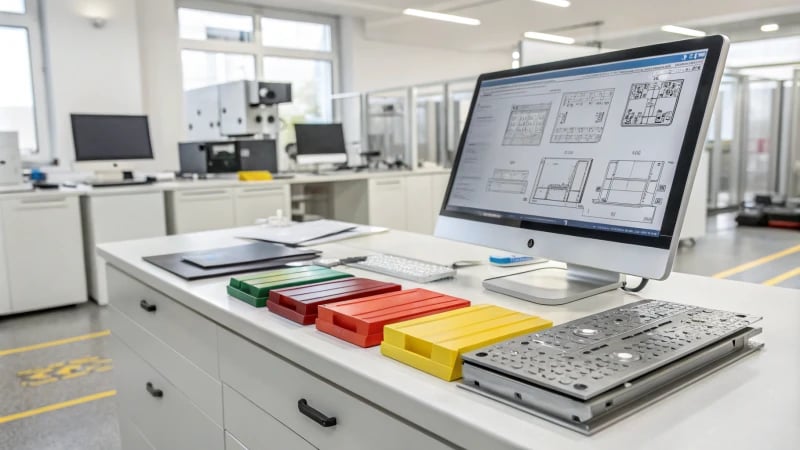
Consider the Use Needs of the Mold
Understanding mold usage is essential. Different products need different materials based on several factors. This starts with how many items you want to produce.
- Batch of Molded Products: For small batches, I noticed that aluminum alloy is very helpful. It’s cheap and processed quickly without losing much performance. For mass production, high-quality mold steels like P20 are crucial. They really survive long-term use and keep molds accurate and smooth.
- Precision Needs: For products that need high accuracy, I prefer materials like beryllium bronze. It handles temperature changes well. Once, I worked on electronic parts where this stability was very important.
- Complexity of Molded Products: Design complexity affects material choice too. For complex molds, I pick H13 steel. Its strength prevents cracks during shaping. This is very important when making complex car parts.
- Molding Pressure and Temperature: Think about process pressure and temperature. Ceramic materials worked well for high temperatures. They handle extreme conditions and are perfect for thermosetting plastics.
Material Performance Characteristics
Now let’s explore how material performance influences mold design:
Property | Recommended Materials | Use Case |
---|---|---|
Hardness and Strength | Cr12MoV steel | Molds requiring wear resistance |
Toughness | 45 steel (heat treated) | Avoiding cracks during injection |
Corrosion Resistance | Stainless steel | Protecting molds from corrosive elements |
Thermal Conductivity | Copper alloys | Enhancing cooling efficiency in molds |
- Hardness and Strength: I turn to Cr12MoV steel for molds that handle heavy use. It’s very strong against plastic melt erosion.
- Toughness: For injection impacts, tough materials like heat-treated 45 steel stop production cracks. I’ve seen their effectiveness firsthand.
- Corrosion Resistance: For products with corrosive elements, stainless steel protects molds from wear. It has saved my molds many times!
- Thermal Conductivity: Don’t dismiss thermal conductivity. Copper alloys in cooling systems significantly improved my cooling and product quality.
Cost Factors in Material Choice
Finally, let’s discuss cost. Balancing budget with performance is key:
- Material Costs: I’ve juggled costs and performance needs. High-performance steels cost more, but simpler mold structures sometimes allow cheaper materials without losing quality.
- Processing Costs: Some materials may look cheap initially but are expensive during processing. Titanium alloys are great but hard to work with, increasing costs a lot.
Conclusion
By considering these factors when designing molds, you’ll improve your material choices and raise production efficiency and product quality. If eager to learn more about advanced design techniques, don’t hesitate to explore more guides on material properties and their uses in injection molding. Learn more about optimizing mold design3.
I hope my experiences help guide you in creating effective molds!
Aluminum alloy is ideal for small batch mold production.True
Aluminum alloy is cost-effective and performs well for small production batches, making it a suitable choice for such applications.
Titanium alloys are the cheapest option for mold materials.False
While titanium alloys offer excellent performance, their high processing complexity makes them more expensive than other options, contradicting this claim.
Conclusion
Selecting the best material for mold making requires evaluating batch size, precision needs, complexity, performance characteristics, and costs to ensure optimal production efficiency.
- This link provides an overview of different materials used in manufacturing, their costs, and performance metrics. ↩
- Explore how advanced materials can transform your mold-making process, improving efficiency and product quality. ↩
- This link provides in-depth information on material properties essential for optimizing mold design, enhancing your decision-making process. ↩