I remember the first time I needed to change the injection speed for a complex mold. It felt like solving a puzzle. Every piece played a critical role in success.
Finding the best injection speed involves checking the type of plastic, the mold design and what quality the product needs. Adjusting these factors helps reach good flow, reduce flaws and improve size precision.
Back then, I experimented a lot to find the right method. I set an initial range depending on the material – PE at 100-300mm/s and PC at 30-100mm/s. Watching the melt flow was very important. When it came out too soon, lowering the speed helped greatly. During a project with small electronic parts, I reduced the speed to 80mm/s to prevent defects.
The mold’s structure influenced the process too. Large gates permitted faster speeds, while smaller gates required a slower approach. For example, in hot runner systems, I discovered that speeds up to 300mm/s worked well because of reduced friction.
Balancing speed with quality presented another problem. Products like car interiors called for moderate speeds (50-150mm/s) to achieve a smooth finish. Precision parts needed slower speeds (40-100mm/s) to keep exact measurements. The key was finding the right balance. Yes, finding that balance was the key.
Injection speed affects product quality in molding.True
Injection speed directly impacts the precision and appearance of molded products.
All plastics require the same injection speed settings.False
Different plastics have unique properties requiring specific injection speeds.
How Do Material Properties Affect Injection Speed?
Have you ever thought about how the materials you pick could completely change your molding process? I have experienced it and knowing this truly changes your production strategy.
Material properties such as viscosity, thermal conductivity and density are crucial for deciding injection speed in molding. Speeds matched to these properties improve flow. Defects become fewer and product quality becomes higher. Very important facts.
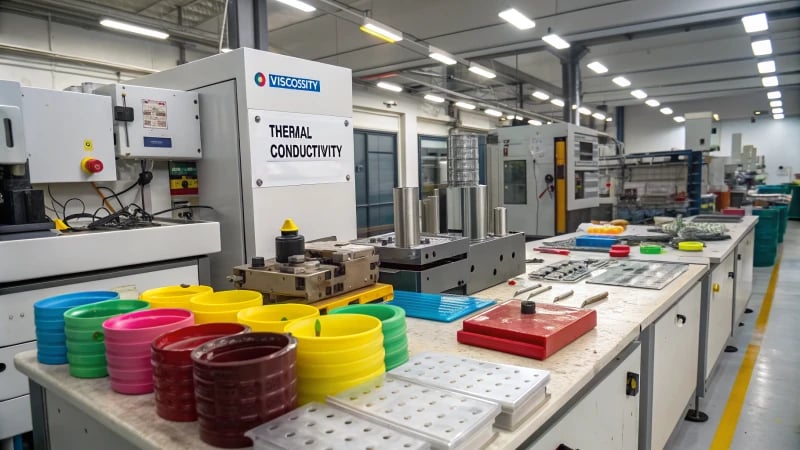
Understanding Material Viscosity
I recall my first experience with high-viscosity materials in injection molding1. It felt like squeezing honey through a straw – slow and steady was really important. High-viscosity materials need slower injection speeds to prevent flow marks or air pockets. Recently, I used polycarbonate, which required more patience than polyethylene due to its higher thickness.
Thermal Conductivity Considerations
Thermal conductivity is very intriguing. Materials that spread heat quickly let you use faster injection speeds. It’s like how a summer breeze cools you faster than a warm jacket. Polyethylene allows higher speeds than polycarbonate because it loses heat better.
Material Type | Thermal Conductivity (W/mK) | Suggested Speed (mm/s) |
---|---|---|
Polyethylene (PE) | 0.46 | 100-300 |
Polycarbonate (PC) | 0.20 | 30-100 |
The Role of Density
Density matters a lot. Denser materials can be challenging – they often need slower speeds for even spreading without defects. It’s like packing a bag; if you rush, you create a mess.
Trial Mold and Test Procedures
Trial molds are the practice before the real event. I set starting parameters based on the material type – like 100-300mm/s for PE – and adjust them based on the trial results. The goal is to find the perfect balance where the melt fills the cavity smoothly without ejection problems.
Conducting a trial mold2 is essential for setting initial parameters.
Mold Structure Adaptations
Gate and runner designs are very important when changing mold structures. Larger gates mean faster speeds, while smaller ones require care to avoid melt ejection. Last week, I had to slow down with a cold runner system to reduce friction heat and pressure loss.
Hot runner systems facilitate higher speeds compared to cold runners, which may require speed reduction due to increased friction.
Product Quality Requirements
The search for quality never ends. Products needing high-quality surfaces require moderate speeds to avoid defects like silver streaks—it’s like cooking; if you rush, you spoil the dish. For exact dimensions, controlled speeds lower residual stresses so everything fits perfectly.
For further advice, explore mold exhaust conditions3 to see how changing speed settings can probably improve final product quality by controlling trapped gases well.
High-viscosity materials need slower injection speeds.True
High-viscosity materials resist flow, requiring slower speeds to prevent defects.
Polycarbonate can be injected faster than polyethylene.False
Polycarbonate requires slower speeds due to its higher viscosity compared to polyethylene.
How Does Mold Design Affect Injection Speed?
Have you ever thought about how mold design affects the speed of injection molding? Mold design means a lot. Mold design matters significantly.
Mold design is very important for controlling injection speed. This happens by shaping how material flows inside the mold cavity. Gate size, runner systems and exhaust conditions are key to this process. These elements need close attention to find the best injection speeds. Quality production depends on it. This is really essential.
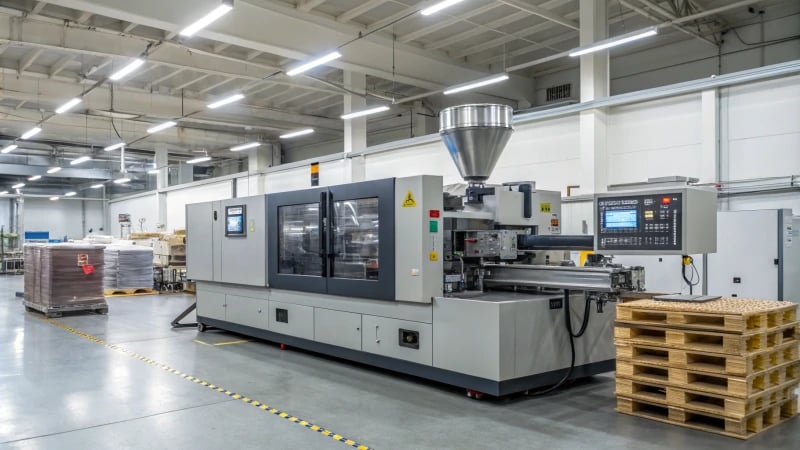
Material Trial Mold and Test
Starting a material trial mold and test4 feels like preparing for a performance. Setting the initial parameters based on your plastic type is extremely important. For example, when using polyethylene (PE), I adjusted speeds between 100-300mm/s. Polycarbonate (PC) required between 30-100mm/s, needing a gentler approach.
Initial Parameter Setting
- Material Type: Determines the starting speed range.
- Trial Mold Adjustment: Monitors melt flow and changes speed to avoid flaws.
Mold Structure Adaptation
The mold structure5 is like a machine’s skeleton, guiding every movement. The gate type, runner system, and exhaust conditions are crucial.
Mold Feature | Impact on Injection Speed |
---|---|
Large Gates | Faster speeds (120-200mm/s) |
Small Gates | Slower speeds (30-80mm/s) |
Runner System Considerations
Experience taught me that a good hot runner system allows faster speeds (100-300mm/s). Cold runner systems need a gentler speed, often between 40-120mm/s.
Product Quality Requirements
- Appearance: Products like sleek car interiors need moderate speeds (50-150mm/s).
- Dimensional Accuracy: Precision parts require slower speeds (40-100mm/s) to reduce stress.
Mold Exhaust Condition
Poor exhaust can ruin a product. I learned this when defects appeared because gases didn’t escape quickly. Changing from 180mm/s to 100-120mm/s and altering the exhaust design with grooves or breathable steel helped greatly.
By understanding these factors, manufacturers adjust injection speeds to improve product quality6 and efficiency. This flexibility is very important in molding processes where even small changes can lead to big improvements in quality and consistency.
Large gates allow faster injection speeds.True
Large gates facilitate higher flow rates, enabling faster injection speeds.
Cold runner systems support high injection speeds.False
Cold runner systems typically require slower speeds due to increased resistance.
How Does Injection Speed Affect Product Quality?
Injection speed plays a very key role in molding. This speed decides how quickly melted material goes into a mold. Fast speed can help fill the mold completely. Slow speed might create problems like bubbles or lines on the product. Good speed balance is crucial. Very important for good quality.
Injection speed directly affects how molten plastic fills the mold. This influences surface finish, size accuracy and overall strength. Speed changes based on material type and mold shape are important. These changes help reduce mistakes and produce very high-quality items.
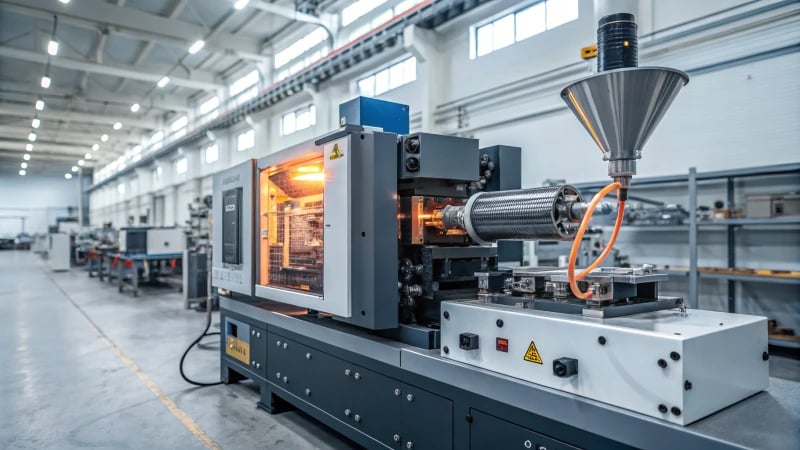
The Role of Material in Injection Speed
Imagine baking a cake, but instead of using flour and eggs, you work with melted plastic. Just like each type of flour requires a different mixing speed, every kind of plastic needs its own injection speed. For example, with polyethylene (PE), I set speeds between 100-300mm per second. However, when using polycarbonate (PC), I lower it to 30-100mm per second. This initial choice is important because each material flows differently.
Mold Structure and Speed Changes
Gate and Runner Factors
When I began designing molds, I realized quickly that the mold’s gate size greatly affects injection speed. Larger gates allow faster speeds, similar to pouring a thick smoothie through a wide straw. On the other hand, smaller gates need a slower speed to avoid problems like spraying. It’s like sipping hot coffee through a thin straw.
Gate Size | Recommended Speed |
---|---|
Large | 120-200mm/s |
Small | 30-80mm/s |
Impact on Product Quality
Appearance Quality
I worked on a project that needed perfect car parts with no flaws. Moderate speeds (50-150mm per second) were ideal to avoid marks and streaks. It’s like getting cake icing just right.
Dimensional Accuracy
Precision matters, especially for parts that need exact measurements. High speeds might create stress, affecting size accuracy, similar to misplacing puzzle pieces when rushing. Controlled speed of 40-100mm per second works well.
Testing for Optimal Speed
Running trial molds is like practicing before the main event. I start at 150mm per second and reduce if needed, aiming to avoid defects, similar to testing light settings for the perfect photo.
Trial mold adjustment7 ensures smoother cavity filling without defects.
Additional Factors: Exhaust and Runner Systems
In my early days, mold exhausts caused defects. Slower speeds and better exhaust designs – like using grooves or breathable steel – improved product quality significantly.
A hot runner system allows higher speeds due to reduced pressure loss; generally between 100-300mm/s can be used here compared to cold runner systems which might require slower speeds due to potential pressure losses.
Knowing these factors helps us choose better injection speeds. This improves efficiency and quality in manufacturing processes whether new or experienced in the field; mastering these changes is crucial to succeed in molding.
Polyethylene requires injection speeds of 100-300mm/s.True
Polyethylene typically needs 100-300mm/s for optimal flow and quality.
Cold runner systems allow higher injection speeds than hot runners.False
Cold runners generally require lower speeds due to pressure loss issues.
How Do You Fine-Tune Injection Speed for Different Gate Types?
Ever thought about how the speed of injection affects a molding process? It’s really crucial. Different gate types require specific adjustments. Here’s the secret to doing it correctly.
To change injection speed for different gate types, begin with starting settings based on material traits. Modify during mold tests. Think about gate size and mold design. This method keeps quality high. Defects stay low.
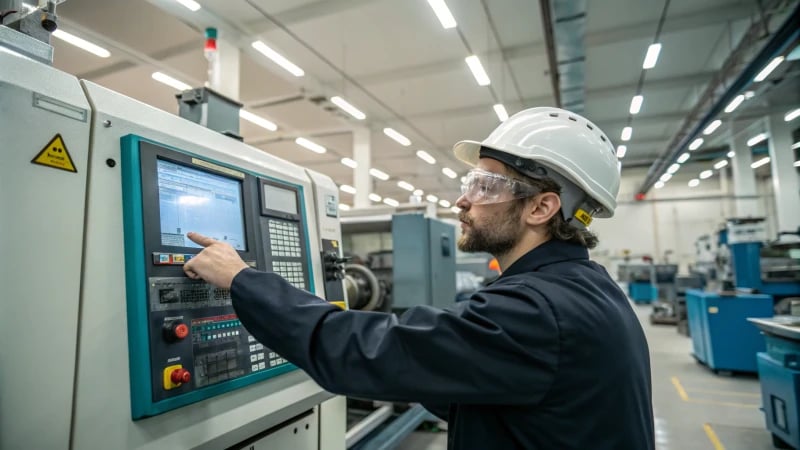
Setting the Stage: Basic Start Points with Material
Begin by setting the injection speed according to the type of plastic material. For instance, polyethylene (PE) usually requires speeds between 100-300mm/s, while delicate plastics such as polycarbonate (PC) need a slower range of 30-100mm/s. These numbers really matter; they keep things smooth and easy to handle.
Trial Mold and Testing: Watching Closely
Conduct a trial mold much like going on a first date—filled with excitement and observation. Watch how the melt behaves, especially through small gates. High speed could cause unexpected problems, like eruptions similar to geysers when starting at 150mm/s. Clearly, this calls for slowing down to 80-100mm/s. It’s akin to tuning a musical instrument perfectly.
Keeping Up Appearances: Quality is Important
For projects needing very high surface quality, such as sleek phone covers, start with moderate speeds between 50-150mm/s. Flow marks were initially problematic; however, by gradually decreasing speeds from 200mm/s step by step, I finally achieved a smooth finish. Precision and patience worked together beautifully.
Understanding Gate and Runner Dynamics
Every gate type tells its own story:
Gate Type | Recommended Speed (mm/s) |
---|---|
Large Gates | 120-200 |
Small Gates | 30-80 |
Big ones, like side gates, handle faster speeds of 120-200mm/s. Smaller gates need slower speeds around 30-80mm/s to prevent melt spray. Visualizing the melt’s path helped me adjust speeds for smooth flow.
Mold Structure: Addressing All Possibilities
Consider the runner system when adjusting speed. Once, bad exhaust in a mold surprised me by causing ugly pores; reducing speed to 100-120mm/s fixed the problem. Listening for mold "breathing" and designing better exhausts with grooves or special steel became routine for me.
Precision in Practice: Getting Dimensions Right
Working with exact dimensions felt like threading a needle—it needed focus and steady hands. Speeds between 40-100mm/s kept stress low and accuracy high. Measuring, adjusting, and repeating until correct made it more than just work; it showed real skill.
Further Reading
- Learn how material features affect injection molding settings8.
- Discover how gate design influences mold function9.
Each change taught me something new about molding; every project had its own needs and lessons.
Polycarbonate requires slower injection speeds than polyethylene.True
Polycarbonate needs 30-100mm/s, while polyethylene needs 100-300mm/s.
Large gates require slower injection speeds than small gates.False
Large gates handle faster speeds (120-200mm/s) than small gates (30-80mm/s).
Conclusion
Determining the best injection speed for molding involves considering material properties, mold design, and product quality requirements to optimize flow and reduce defects.
-
Learn how different viscosities impact injection speed and quality, ensuring better control over the molding process. ↩
-
Understand why trial molds are crucial for setting initial parameters and ensuring defect-free products. ↩
-
Discover how proper exhaust conditions prevent defects and improve the efficiency of the injection process. ↩
-
Learn about setting initial injection speed parameters based on material type during trial mold tests. ↩
-
Discover how different mold structures impact the required injection speeds for optimal molding outcomes. ↩
-
Explore how adjusting injection speeds influences the overall quality of molded products. ↩
-
Discover methods for adjusting trial molds to perfect injection speed. ↩
-
Learn about the relationship between plastic material properties and their effect on injection speed settings. ↩
-
Understand how different gate designs affect the overall efficiency and quality of the molding process. ↩