When I first delved into the world of plastic molding, I quickly realized that injection speed is a game changer.
The best injection speed depends on factors such as the shape and size of the parts, material properties, mold design, and cooling system capabilities. Typically, thin-walled parts require higher speeds, while thick-walled parts benefit from lower speeds to minimize defects.
But understanding these nuances can dramatically enhance your production outcomes. Let’s dive deeper into how each factor influences injection speed and explore expert insights into optimizing your injection molding process.
Thin-walled parts require higher injection speeds.True
Higher speeds prevent defects by ensuring quick mold filling for thin walls.
How Does Part Geometry Influence Injection Speed?
The geometry of a plastic part plays a crucial role in determining the appropriate injection speed during molding.
Part geometry affects injection speed by dictating how quickly the plastic can fill the mold. Thin-walled parts need higher speeds to prevent defects, while thick-walled parts require slower speeds to reduce stress and warping. Proper speed ensures quality, efficiency, and reduces material waste.
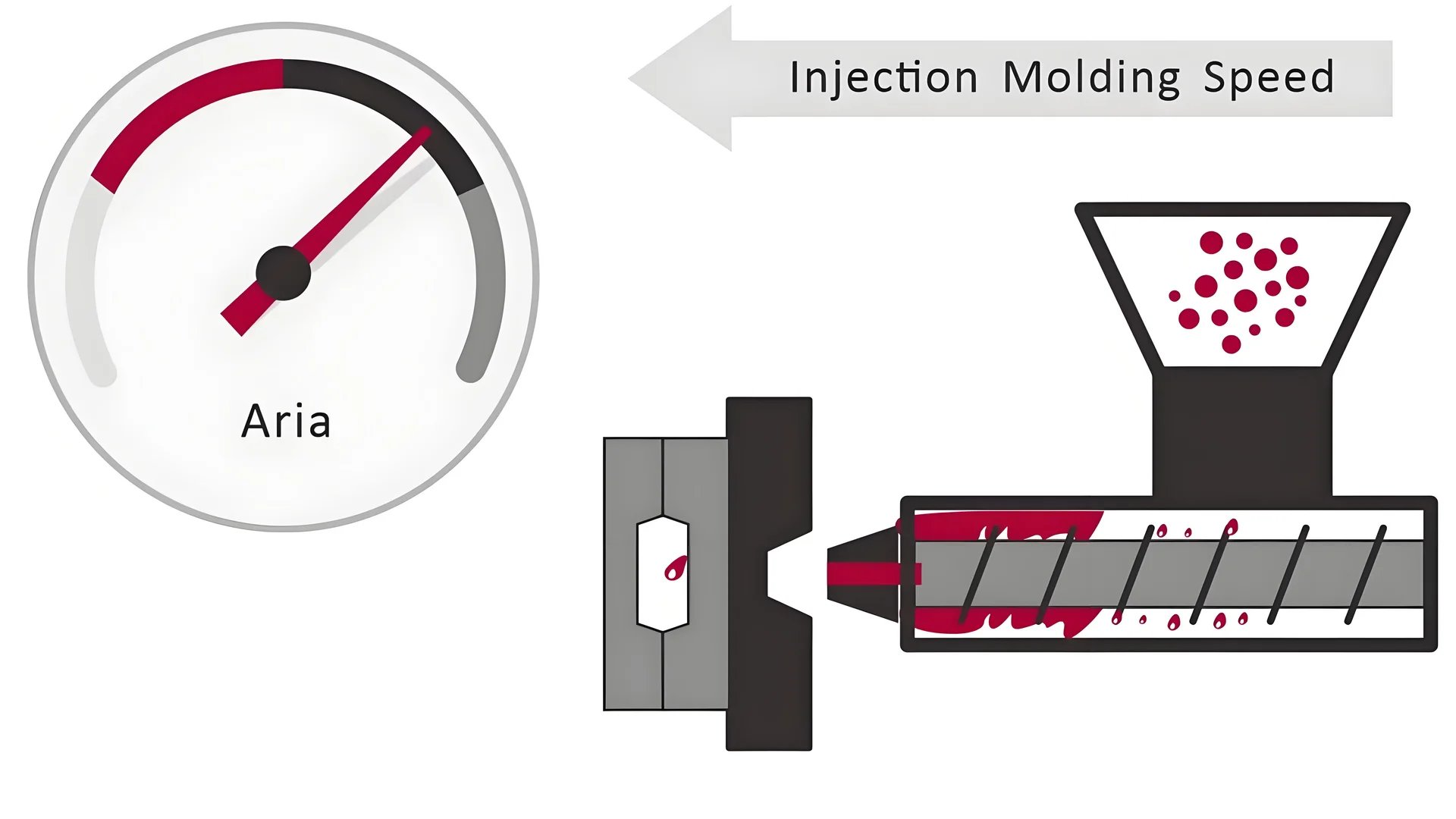
Impact of Wall Thickness on Injection Speed
When considering thin-walled components1, it’s essential to understand that a higher injection speed is usually necessary. This is primarily because thin walls require the melt to fill the cavity swiftly to avoid defects like short shots or material shortages. A rapid fill helps maintain a higher melt temperature, crucial for quality outcomes.
Conversely, with thick-walled components2, the injection speed should be reduced. Thicker sections cool more slowly, and a high-speed fill can introduce excessive internal stress, leading to warping or deformation. A slower injection allows for better heat and pressure distribution, minimizing these risks.
Wall Thickness | Recommended Injection Speed | Potential Defects |
---|---|---|
Thin | High | Short shots |
Thick | Low | Warping |
Influence of Complex Geometries
Complex geometries present additional challenges. For intricate mold designs, a high injection speed might result in turbulence within the cavity. This can affect the final part’s structural integrity and surface finish. Instead, a moderate speed allows for smoother flow, reducing turbulence and ensuring the part forms correctly.
Geometric Features and Their Effects
Certain geometric features, such as ribs or bosses, also influence the optimal injection speed. Ribs may necessitate a moderate speed to ensure proper filling without introducing stresses. Meanwhile, deep cavities or undercuts might demand adjustments in speed to balance flow and pressure throughout the mold.
Understanding these principles can significantly enhance your production strategy by aligning injection speed with part geometry effectively.
Thin walls require higher injection speeds.True
Higher speeds prevent defects like short shots in thin-walled parts.
Thick parts need faster injection speeds to avoid warping.False
Thick parts require slower speeds to reduce stress and warping.
Why Material Properties Matter in Injection Speed Selection?
The choice of injection speed is crucial in molding processes, and material properties significantly influence this decision.
Material properties such as fluidity and viscosity determine the optimal injection speed. High-fluidity materials like polyethylene require higher speeds, while low-fluidity materials like polycarbonate need lower speeds to prevent defects.
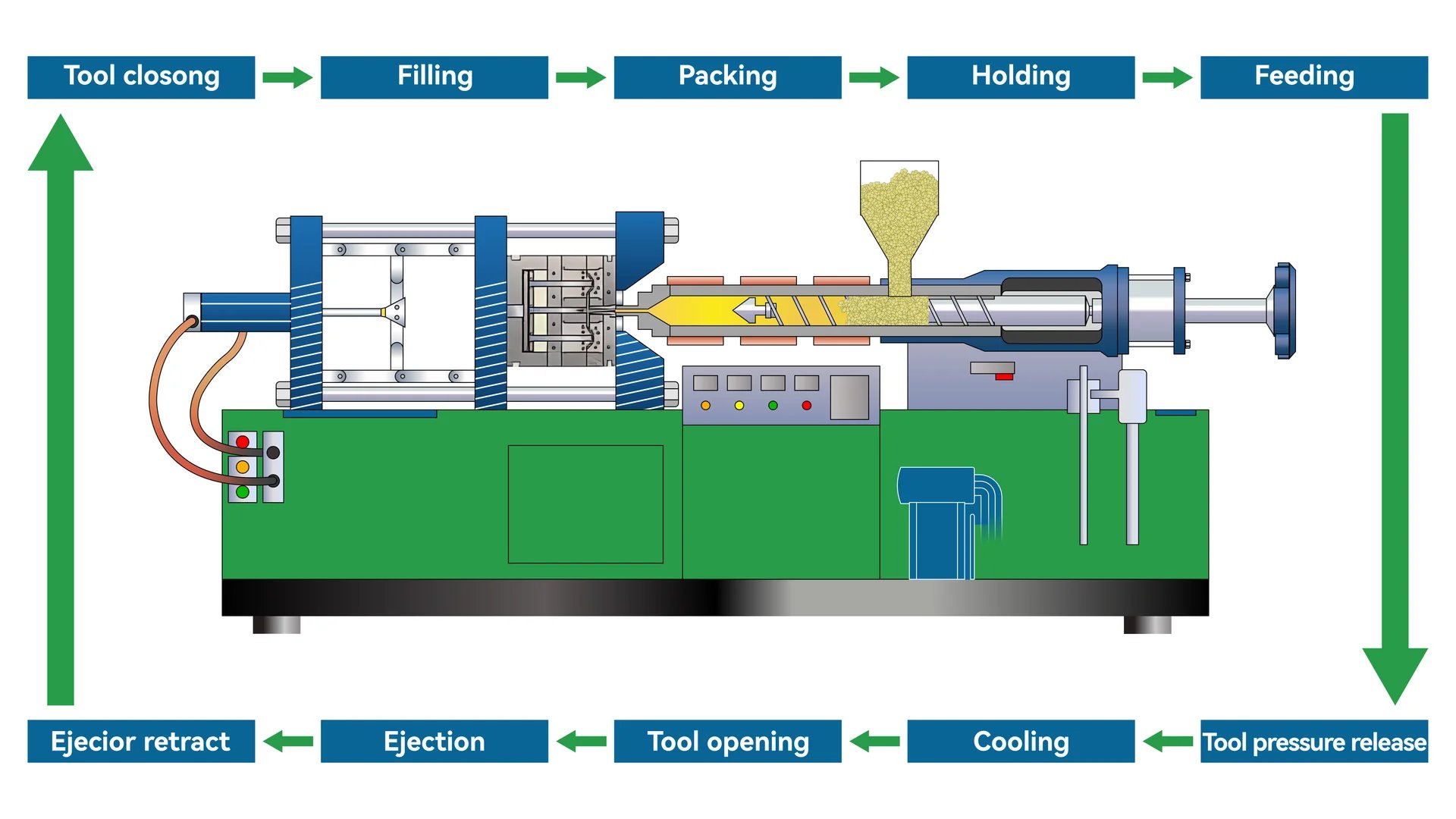
Importance of Material Fluidity
The fluidity of a material plays a pivotal role in determining its injection speed. Materials with high fluidity, such as polyethylene3 and polypropylene, are often injected at higher speeds. This is because their low viscosity allows them to move swiftly through the mold cavity without generating excessive shear forces.
Conversely, materials with poor fluidity, like polystyrene and polycarbonate4, require slower injection speeds. These materials are more viscous, and rapid injection can lead to increased shear forces, resulting in defects like bubbles or degradation.
Table: Material Fluidity and Suggested Injection Speeds
Material Type | Example Materials | Suggested Injection Speed |
---|---|---|
High Fluidity | Polyethylene, Polypropylene | High |
Low Fluidity | Polystyrene, Polycarbonate | Low |
Viscosity Impact
Viscosity, a measure of a fluid’s resistance to flow, directly impacts the injection speed. Materials with high viscosity require more time to flow into the mold, necessitating a lower speed to ensure smooth filling and minimal defects.
For instance, consider polycarbonate’s high viscosity: injecting it at a high speed can lead to significant shear stress, potentially causing material degradation. A slower speed allows the melt to fill the mold more gently, preserving the material’s integrity.
Effects on Production Efficiency
Selecting the right injection speed based on material properties can also enhance production efficiency. High-speed injection for suitable materials reduces cycle times, thereby increasing throughput. However, balancing speed with quality is crucial. While high-speed injection boosts efficiency, it should not compromise the quality of the plastic part.
For materials with lower fluidity, maintaining a moderate pace ensures that the parts are defect-free, even if it means longer cycle times. This trade-off between speed and quality must be carefully managed to optimize overall production efficiency.
Conclusion: Tailoring Speeds for Material Types
Understanding the material properties is essential for optimizing injection speeds. By tailoring speeds according to fluidity and viscosity, manufacturers can achieve better part quality while maintaining efficient production cycles. This nuanced approach to injection molding enhances both product reliability and operational efficacy.
High-fluidity materials need higher injection speeds.True
High-fluidity materials like polyethylene require higher speeds for optimal molding.
Polycarbonate requires high-speed injection to prevent defects.False
Polycarbonate's low fluidity needs slower speeds to avoid defects.
What Role Does Mold Design Play in Determining Injection Speed?
Mold design is pivotal in determining the injection speed in plastic molding, affecting quality and efficiency.
Mold design dictates injection speed by influencing melt flow and cooling efficiency. Complex molds require slower speeds to prevent defects, while well-designed cooling systems allow faster speeds for enhanced production.
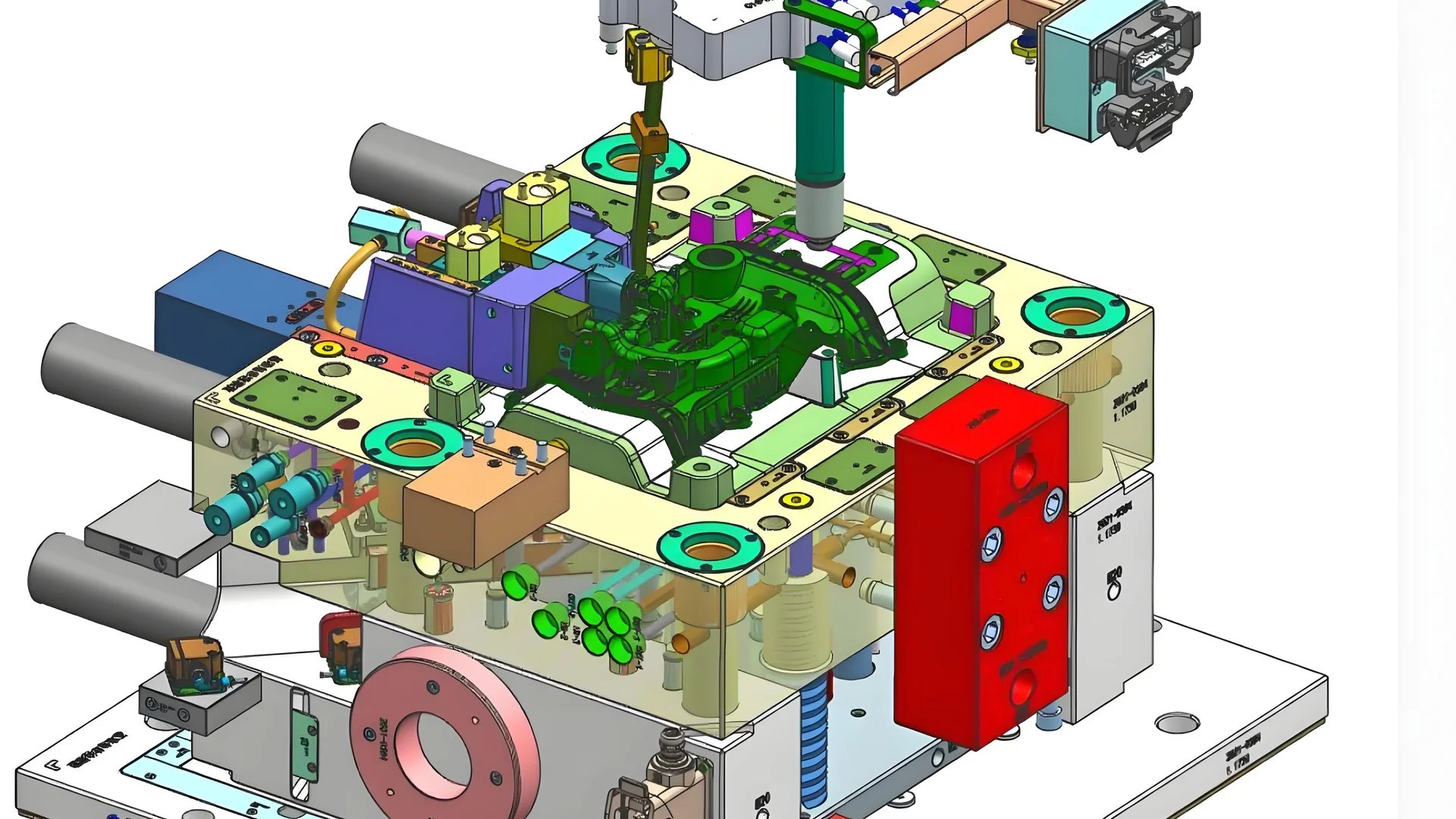
Influence of Mold Complexity on Injection Speed
When it comes to injection molding, the complexity of a mold is a critical factor that impacts the injection speed. For molds with intricate designs or multiple cavities, the flow path for the melt can be considerably complicated. This intricacy often necessitates a slower injection speed to ensure that the melt fills each cavity completely without causing issues such as turbulence or air entrapment.
For instance, a complex mold structure5 with sharp corners or thin ribs may obstruct the melt flow if the speed is too high, leading to incomplete filling or surface defects. Therefore, adjusting the injection speed to match the mold complexity can significantly enhance the quality of the final product.
The Role of Mold Cooling Systems
A well-designed cooling system within a mold can dramatically influence the optimal injection speed. Efficient cooling systems help remove heat quickly and evenly from the molten plastic, allowing for faster cycle times and higher production efficiency.
For molds equipped with advanced cooling channels or conformal cooling techniques, a higher injection speed may be employed. This is because the rapid dissipation of heat reduces the risk of defects such as warping or shrinkage, which are common with inadequate cooling. As a result, manufacturers can maintain faster speeds without compromising on quality.
Mold Feature | Impact on Injection Speed |
---|---|
Complex Structures | Slower speeds to prevent defects |
Advanced Cooling System | Allows faster speeds, better quality |
Balancing Mold Design with Equipment Capabilities
While mold design is crucial, it’s essential to consider the limitations of the injection molding equipment. High-speed injection might be desirable for certain molds; however, if the machinery cannot sustain such speeds without overheating or excessive wear, adjustments must be made.
Thus, understanding and balancing mold design with equipment capabilities is vital for achieving optimal injection speed. It involves not just assessing the physical attributes of the mold but also accounting for the operational parameters of the molding machine itself.
Ultimately, mold design plays a multifaceted role in determining injection speed by influencing both the flow dynamics and cooling efficiency. By considering these factors alongside equipment capabilities, manufacturers can optimize their processes for better quality and productivity outcomes.
Complex mold designs require slower injection speeds.True
Intricate designs need slower speeds to avoid defects and ensure quality.
Efficient cooling systems decrease injection speed.False
Efficient cooling allows for faster injection speeds by reducing defect risks.
How Can Cooling Systems Affect Injection Molding Speeds?
Cooling systems are pivotal in determining injection molding speeds, influencing efficiency and part quality.
Cooling systems significantly impact injection molding speeds by affecting cycle times and part quality. A well-designed cooling system can reduce cooling time, allowing for faster cycles and improving overall production efficiency. Conversely, inadequate cooling can lead to defects and longer cycle times.
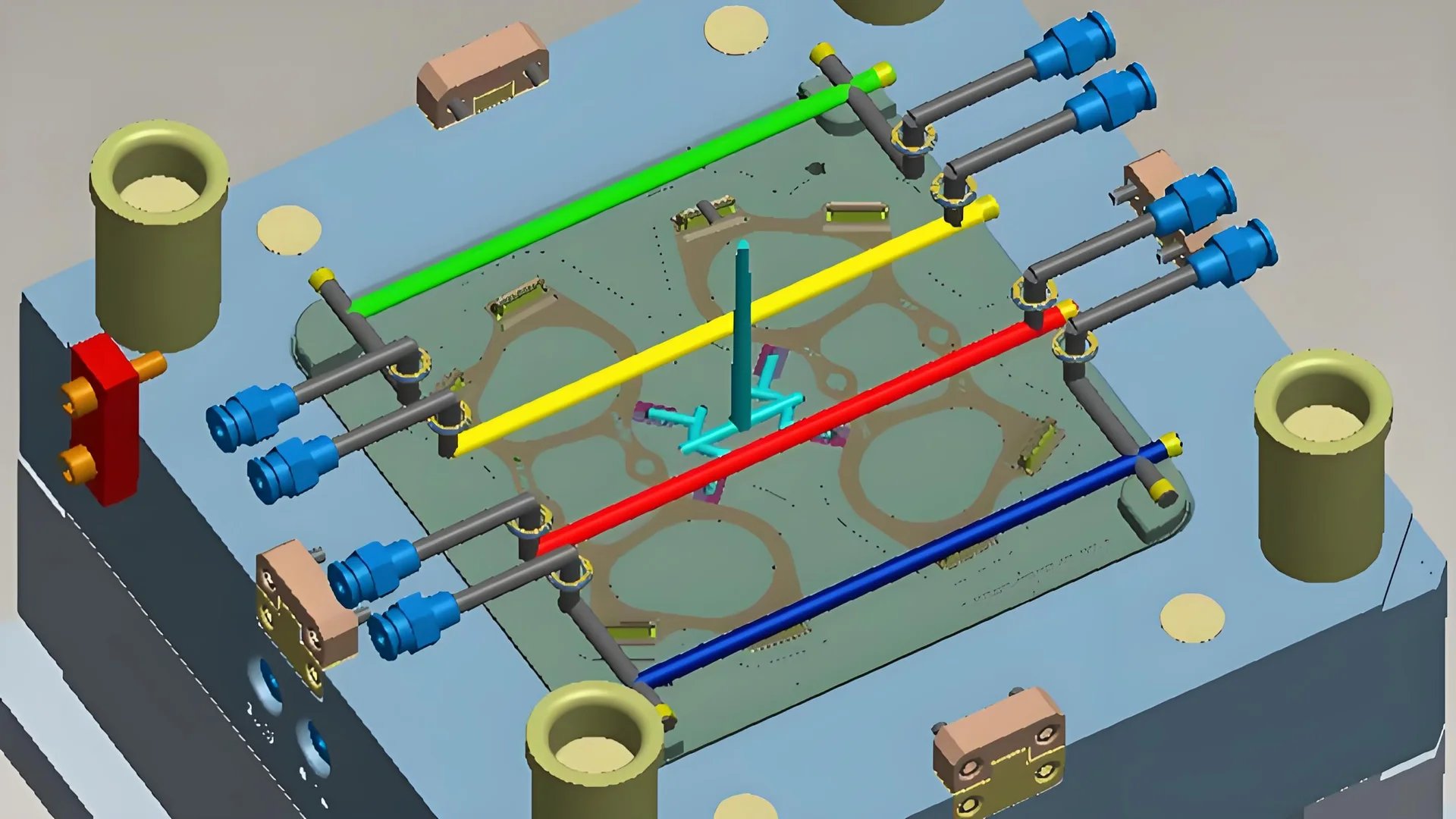
Understanding the Basics of Cooling Systems
In injection molding, cooling systems are responsible for removing the heat generated during the molding process. Their effectiveness can dramatically alter cycle times, which is why understanding their role is crucial.
The Relationship Between Cooling Systems and Cycle Time
The cycle time in injection molding comprises several stages, with cooling being one of the most time-consuming. Efficient cooling systems can significantly reduce this time, allowing for quicker mold ejections and shorter overall cycle durations.
Factor | Impact on Cycle Time |
---|---|
Efficient Cooling | Reduces cycle time, increases productivity |
Poor Cooling | Increases cycle time, lowers efficiency |
A well-designed cooling system reduces the risk of defects like warping or shrinkage by ensuring uniform temperature distribution within the mold.
Enhancing Cooling Efficiency
-
Optimizing Cooling Channel Design
The design of cooling channels within a mold is critical. Channels that are too narrow or poorly positioned can lead to uneven cooling. Optimizing these channels ensures that the heat is evenly distributed and dissipated efficiently.
-
Using Advanced Cooling Techniques
Techniques such as conformal cooling, where channels follow the shape of the part, provide more consistent and rapid cooling. This method is particularly useful for complex molds.
-
Selecting Appropriate Coolants
The choice of coolant can also affect cooling efficiency. Water is commonly used due to its high heat transfer capabilities, but other fluids might be more suitable depending on specific material properties or production requirements.
Impact on Production Efficiency and Quality
An effective cooling system not only speeds up production but also enhances the quality of the molded parts. Faster cooling leads to less stress within the material, reducing the likelihood of defects such as:
- Warping
- Sink marks
- Internal stresses
Advanced Solutions6 for Cooling System Optimization
With technological advancements, solutions such as simulation software can help predict and optimize cooling performance before the production phase begins. These tools allow manufacturers to experiment with different designs and configurations virtually, saving time and resources.
Optimizing cooling systems is a continuous process that combines engineering insight with innovative technologies to ensure that injection molding processes remain efficient and high-quality.
Efficient cooling reduces injection molding cycle time.True
Efficient cooling systems shorten the cycle time by reducing cooling duration.
Poor cooling increases injection molding efficiency.False
Inadequate cooling leads to longer cycles and reduced production efficiency.
Conclusion
Selecting the right injection speed based on comprehensive factors can elevate both quality and efficiency in production.
-
Learn why thin walls require faster fill rates to avoid defects.: Do control injection speed: Control the injection speed to maintain consistent part quality. High injection speeds are usually required for thin … ↩
-
Understand how speed affects stress and warping in thick parts.: The injection speed essentially determines the degree of molecular orientation and, thus, affects the adhesion, orientation, and shrinkage. ↩
-
Explore how polyethylene’s fluidity affects its injection speed.: PE molecular chain is flexible, the inter-bonding force is small, the melt viscosity is low, and the fluidity is excellent, so the molding does … ↩
-
Learn about polycarbonate’s viscosity and its impact on molding.: Viscosity, 800000 – 800000 cP @Temperature 320 – 320 °C, 800000 – 800000 cP … Overview of materials for Polycarbonate, Impact Modified · Overview of … ↩
-
Explore how intricate mold designs impact injection speeds and quality.: The feeding system of an injection mold primarily transports the plastic melt from the nozzle of the injection molding machine to each cavity. ↩
-
Discover cutting-edge tools and methods to enhance cooling system efficiency.: Explore and apply advanced technologies such as conformal cooling and microchannel cooling to further improve cooling efficiency and product … ↩