Crafting the perfect parting surface in injection molding can be a game-changer for product quality. But how do you nail it every time?
Optimal design techniques for injection mold parting surfaces emphasize product shape, appearance, and processing ease, ensuring smooth demolding, minimal defects, and efficient manufacturing.
You know, when I first started working with injection molds, I was overwhelmed by all the details that needed attention. It felt like assembling a complex puzzle where each piece had to fit perfectly to create something truly remarkable. Over time, I realized that mastering the design of parting surfaces is like finding that last piece of a puzzle—it’s crucial for achieving a flawless finish.
Let’s dive into some strategies that have helped me refine my approach. For simple shapes, like a cylindrical cup, positioning the parting surface along the maximum contour simplifies the mold structure. But when dealing with complex shapes, ensuring smooth demolding becomes key. I’ve learned that using side core pulling mechanisms for undercuts or stepped parting surfaces for varying features can make all the difference.
Appearance also plays a huge role, especially with high-quality surfaces like automotive interiors. Avoiding parting lines can prevent unsightly flash and weld marks. And don’t forget about processing convenience. Choosing plane surfaces over curves makes for easier milling and grinding—lessons I learned the hard way during late nights in the workshop.
Incorporating these techniques not only enhances the quality of the molded product but also streamlines the manufacturing process. Trust me, once you’ve nailed these designs, your projects will move from good to great in no time.
Parting surfaces influence product appearance quality.True
Proper design of parting surfaces minimizes visible defects, enhancing appearance.
Ignoring shape in design leads to efficient demolding.False
Considering shape is crucial for smooth demolding and avoiding defects.
- 1. How Does Product Shape Influence Parting Surface Design?
- 2. Why Are Appearance Requirements Crucial for Parting Surfaces?
- 3. What Are the Processing and Assembly Considerations for Parting Surfaces?
- 4. How Does the Injection Molding Process Affect Parting Surface Design?
- 5. What Are the Common Challenges and Solutions in Parting Surface Design?
- 6. Conclusion
How Does Product Shape Influence Parting Surface Design?
Ever wonder how the shape of a product can dictate the entire design of its mold? Let me walk you through this fascinating aspect of manufacturing.
Product shape impacts parting surface design by determining mold complexity and demolding ease. Simple shapes allow straightforward parting lines, while intricate forms require complex designs to manage features like undercuts.
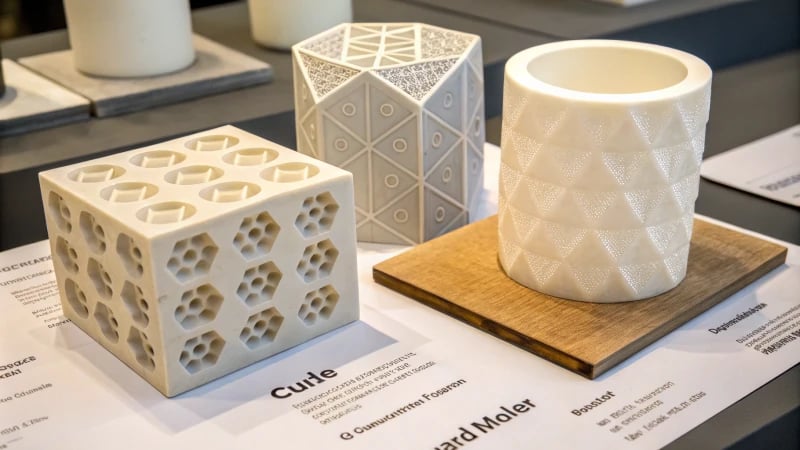
The Basics of Parting Surface Design
I still remember my first hands-on experience with injection molding. I was just starting out, and the idea of crafting a parting surface seemed daunting. Picture this: the parting surface1 is where two halves of the mold meet, crucial for allowing the product to be easily removed. It’s amazing how much the shape of a product influences this configuration.
Simple vs. Complex Shapes
When I first dealt with simple shapes—think cylinders or cuboids—the process was more straightforward. You can often align the parting line along the largest contour, which simplifies the mold’s construction and reduces costs. I remember a cylindrical cup project where aligning the parting line with the central axis made everything click into place. It’s almost like finding that perfect puzzle piece.
Shape Type | Considerations |
---|---|
Simple | Align with maximum contour |
Complex | Ensure smooth demolding |
But when it comes to complex shapes, like those with undercuts or multiple directional features, it gets trickier. I once tackled a project with intricate features that required side core pulling mechanisms—imagine those as little mold ninjas working behind the scenes to handle tricky spots.
Impact on Appearance and Functionality
For products needing high aesthetic quality, such as consumer electronics, hiding or minimizing parting lines is crucial. I’ve learned this the hard way when even the slightest weld mark stood out on a sleek gadget case. For transparent materials, it’s even trickier; defects at the parting surface can be glaringly obvious, affecting both transparency and optical properties.
Processing and Assembly Challenges
Considering both processing convenience and assembly requirements is vital in parting surface design2. I often use locating pins or keys to maintain alignment during assembly. It’s a bit like setting up Lego blocks—you want everything to snap together perfectly for seamless operation.
Injection Molding Process Considerations
Finally, the parting surface must support efficient plastic flow and venting during injection molding. I’ve seen firsthand how properly positioned gates and venting channels can prevent issues like short shots or trapped gases, which can degrade product quality.
Balancing all these factors isn’t just about technical know-how; it’s about understanding how every choice impacts both production efficiency and product quality. It’s a puzzle where every piece matters.
Simple shapes allow easy parting line placement.True
Simple shapes like cylinders enable straightforward parting line alignment.
Complex shapes never require side core mechanisms.False
Complex shapes often need side cores for demolding intricate features.
Why Are Appearance Requirements Crucial for Parting Surfaces?
Ever wondered why the look of your parting surfaces is such a big deal? Let’s dive into how appearance affects both the quality and aesthetics of molded products.
Appearance requirements for parting surfaces are crucial for enhancing the visual appeal and functionality of plastic products by preventing defects such as flash and weld marks, resulting in a more attractive product.
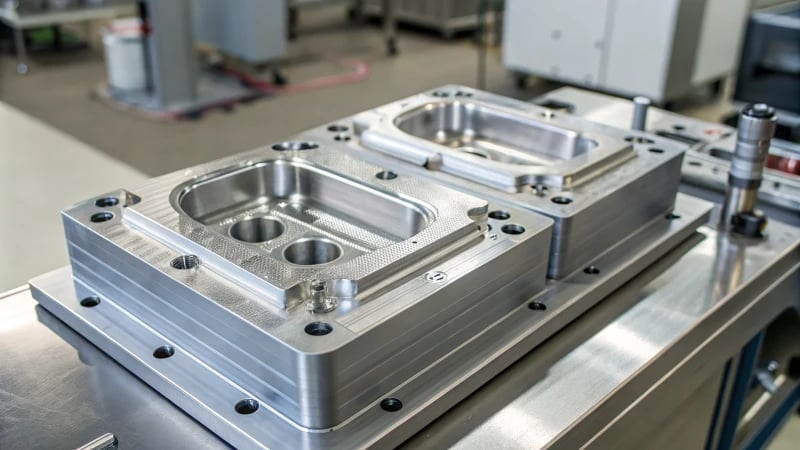
Understanding Parting Surfaces and Their Role
When I first delved into the world of injection molding3, I quickly learned that the parting surfaces—where two halves of a mold meet—are pivotal. The way these surfaces are designed can make or break the manufacturing process, impacting the final product’s look. If the design is off, you might end up with flash—excess material that seeps out—or visible weld lines, both of which can ruin a product’s aesthetic.
Balancing Functionality and Aesthetics
I remember working on a project for a sleek electronic gadget. The stakes were high because any blemish could turn off potential buyers. For such high-stakes products, especially those with transparent materials, ensuring flawless parting lines is crucial. Even a tiny imperfection can catch the eye and spoil the whole look. This means getting the mold and gate placement just right to dodge these blemishes.
Factors Influencing Parting Surface Design
Consideration | Description |
---|---|
Shape of Product | Simple shapes allow easier design; complex shapes may need advanced techniques like side core pulling. |
Material Type | Transparent materials demand careful consideration to avoid defects affecting clarity. |
Mold Processing | Precision is key; curved surfaces might require special equipment like EDM machines. |
Practical Tips for Designers
From my experience, choosing flat planes for parting surfaces simplifies both processing and assembly. Take cuboidal shapes, for instance; positioning parting surfaces along their maximum contour makes the mold straightforward and production smoother.
When reinforcing ribs come into play, aligning parting lines parallel to them is key to not disrupting their structure. By sticking to these strategies, I’ve found it much easier to produce designs that are both functional and pleasing to the eye.
Poor parting surface design causes flash defects.True
Flash defects occur when excess material seeps out due to improper mold closure.
All materials have the same parting surface requirements.False
Different materials, especially transparent ones, require specific considerations to avoid defects.
What Are the Processing and Assembly Considerations for Parting Surfaces?
Have you ever wondered why parting surfaces in mold design are such a big deal?
Choose parting surfaces carefully to optimize mold processing, ease assembly, and maintain product quality, considering shape, aesthetics, processing simplicity, and venting needs.
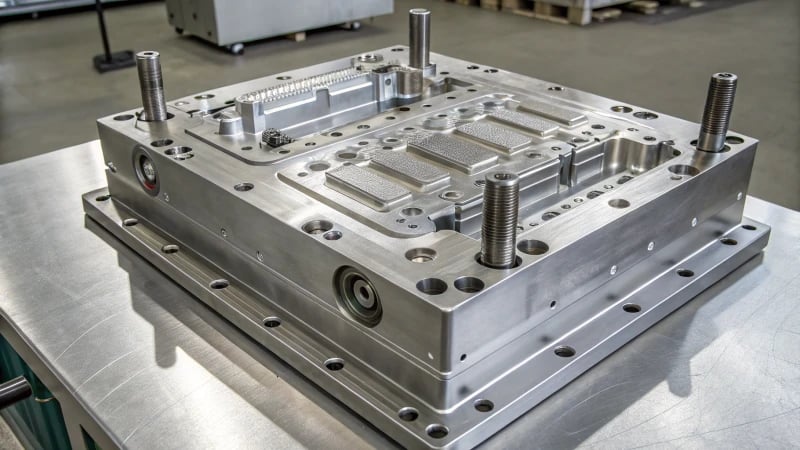
Product Shape Considerations
I remember my first project involving a simple cylindrical product. Aligning the parting surface with the maximum contour4 was a game-changer. It not only simplified the mold design but also made processing a breeze. For more complex shapes, like ones with undercuts, I learned the hard way that a stepped parting surface could work wonders, allowing different features to mold at varying depths.
Appearance Requirements
There was this time when I worked on a high-quality automotive interior piece. The parting surface placement was critical to avoid unsightly weld marks or flash, which could ruin the product’s look. I’ve found that for transparent items, positioning latent gates5 carefully can drastically improve transparency by stabilizing the melt flow.
Processing and Assembly Ease
I’ve always aimed for plane parting surfaces whenever possible because they simplify processing with conventional milling techniques. However, when the job called for curved surfaces, I had to rely on specialized equipment like EDM. The assembly became so much easier when locating pins were involved, ensuring everything aligned perfectly.
Injection Molding Process
The flow of plastic melt within a mold cavity6 has always fascinated me. I once struggled with short shots until I realized the importance of strategic gate positioning to guide the melt evenly across the cavity. Proper venting is also crucial—one project taught me that well-designed venting channels can prevent defects from trapped air, especially in high-speed injection molding.
Aspect | Consideration |
---|---|
Shape | Simple vs. Complex |
Appearance | High-quality vs. Transparent |
Processing | Plane vs. Curved Surfaces |
Assembly | Alignment & Ease of Opening |
Injection Molding | Flow & Venting Requirements |
These insights have been invaluable in refining my approach to mold design, ensuring both functionality and aesthetics meet industry standards, especially in demanding fields like consumer electronics and automotive manufacturing.
Simple shapes require complex parting surfaces.False
Simple shapes like cylinders align with maximum contour, simplifying mold.
Parting surfaces affect injection molding flow.True
Design impacts plastic melt flow, preventing short shots or stagnant areas.
How Does the Injection Molding Process Affect Parting Surface Design?
Ever wondered how something as simple as a parting surface can impact the entire injection molding process?
Injection molding affects parting surface design by influencing demolding, plastic flow, and appearance. Correct parting line placement improves mold performance and product quality.
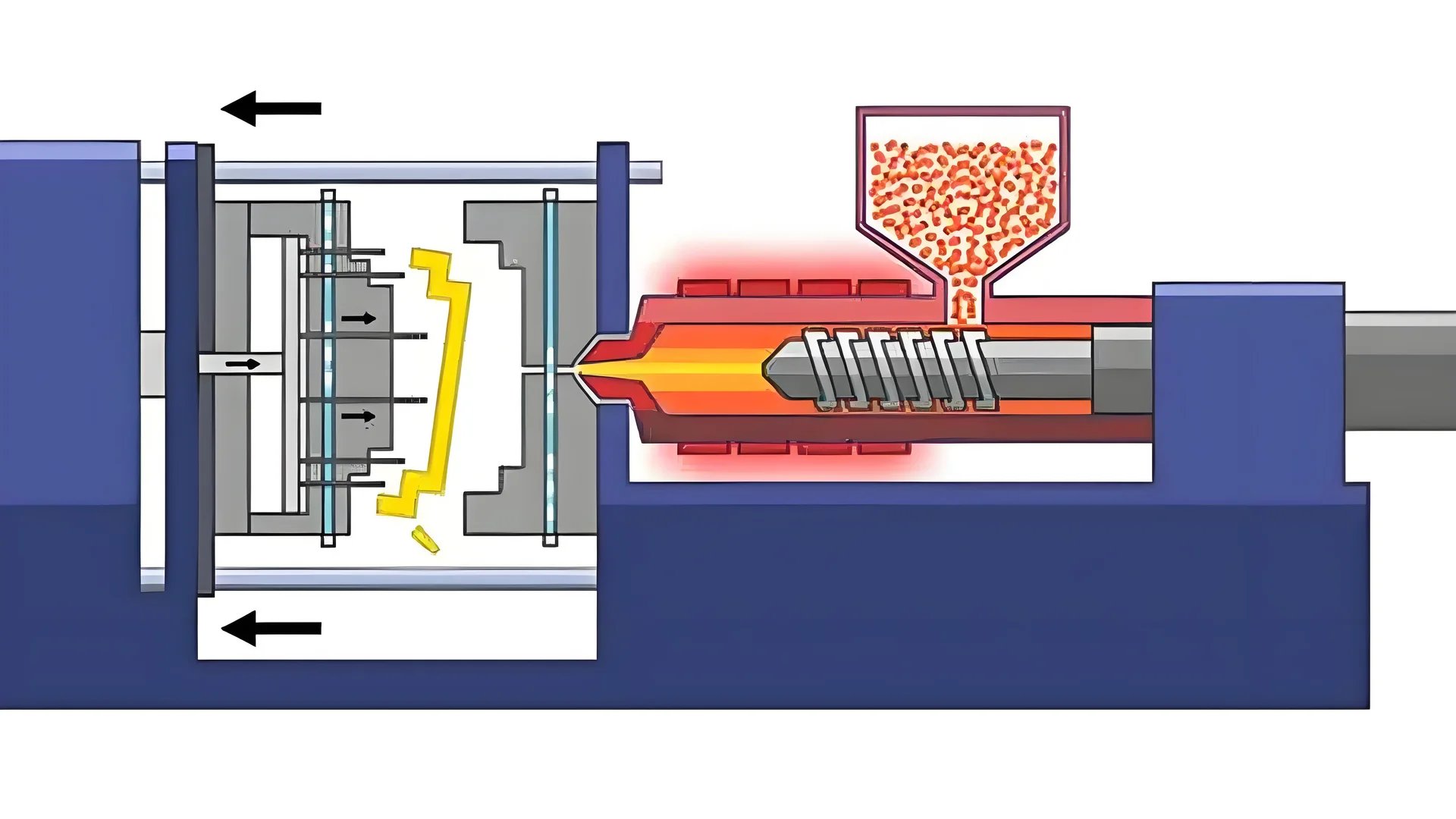
When I first got into mold design, I never imagined how intricate the process would be, particularly the design of the parting surface. It seemed straightforward at first, but as I delved deeper, I realized it’s an art form that demands attention to detail and a good understanding of the product’s requirements.
Key Considerations in Parting Surface Design
Designing a parting surface requires balancing multiple factors to ensure effective mold operation and high-quality products. Let’s explore some essential considerations:
1. Product Shape and Complexity
The shape of the plastic product heavily influences the parting surface design. For products with simple shapes7 like a cylindrical cup, positioning the parting line at the maximum contour simplifies life immensely. It’s like finding the perfect seam on a piece of fabric—everything just falls into place.
But then there are complex shapes, full of undercuts and features that remind me of solving a 3D puzzle. These require special mechanisms, like side core pulling, to ensure everything demolds smoothly. If feasible, forced demolding can be an option, provided the material’s elasticity supports it.
2. Appearance Requirements
Aesthetic requirements significantly impact parting surface decisions, especially for high-visibility products such as automotive interiors or electronic housings. The pressure was on to hide the parting lines to prevent flash and weld marks from ruining that pristine look.
For transparent products, every little defect is magnified—almost like a fingerprint on glass. Using latent gates becomes crucial to stabilize flow and keep those parting lines invisible.
3. Processing and Assembly
Ease of processing and assembly is another critical aspect. When processing parts with planar surfaces, simple milling or grinding does the trick.
Conversely, when you’re working with curves, it’s like stepping into a whole new world where EDM and CNC machines become your best friends. In assembly, aligning everything with locating pins ensures all puzzle pieces fit perfectly without interference.
4. Injection Molding Dynamics
The dynamics of plastic flow during injection molding are pivotal in parting surface design. A well-planned surface should promote even cavity filling to prevent short shots or stagnant areas.
It’s all about guiding the plastic flow efficiently across the cavity with well-planned gate positions relative to the parting line.
Venting Considerations
Effective venting during injection molding is vital to prevent defects caused by trapped air or gas decomposition. A well-designed parting surface doubles as a vent channel; hence designing vent grooves or leveraging natural gaps between surfaces can improve mold performance.
With these insights, designing a parting surface becomes more than just a technical task; it’s about crafting a piece of art that meets both manufacturing and aesthetic goals. If you’re curious to learn more about these considerations, dive into additional resources8.
Parting surface design affects mold complexity.True
A well-designed parting surface simplifies mold structure, reducing complexity.
Curved parting surfaces are easier to process than planar ones.False
Curved surfaces require specialized processes like EDM, unlike planar ones.
What Are the Common Challenges and Solutions in Parting Surface Design?
Navigating the intricate world of mold design, I’ve faced my fair share of challenges, especially when it comes to crafting the perfect parting surface.
Parting surface design challenges include complex shapes and stringent standards. Solutions involve strategic surface selection, optimizing gates, and effective venting techniques to ensure quality mold production.
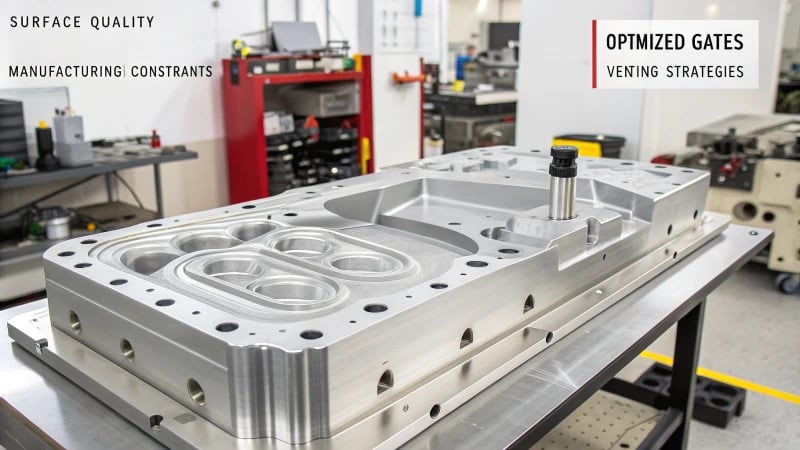
Understanding the Shape of Plastic Products
In my journey through the maze of injection mold parting surfaces9, I quickly learned that the shape of a plastic product dictates much of the design strategy.
-
Simple Shapes: For regular shapes like cuboids or cylinders, placing the parting surface at the maximum contour makes life so much easier. It simplifies mold structure and cuts down on processing headaches.
-
Complex Shapes: Challenges include undercuts that require side core mechanisms. I remember once tackling a project where forced demolding was necessary. It was nerve-wracking to ensure the material wouldn’t crack under pressure, but with careful planning, it all turned out well.
Appearance Requirements
Let’s not forget the pressure to meet high aesthetic standards, especially for automotive interiors or electronic housings.
-
High-Quality Surfaces: Every detail had to be perfect, minimizing parting surfaces to avoid those pesky defects like flash or weld marks. Optimize gate locations to reduce these issues.
-
Transparent Products: With transparent products, it was even trickier—every blemish stood out like a sore thumb. Select parting surfaces carefully as defects are more visible. Use latent gates for stable melt flow, enhancing transparency.
Mold Processing and Assembly
When it comes to processing and assembly, convenience is king.
-
Processing: Designing flat parting surfaces for precision milling saved me many headaches. Curved surfaces required more advanced CNC equipment, challenging my skills but rewarding in precision.
-
Assembly: Assembling molds is like piecing together a complex puzzle. Design for easy assembly with locating pins ensures everything aligns perfectly—it’s an absolute must to avoid interference, especially when dealing with slider mechanisms.
Injection Molding Process
A well-thought-out parting surface can make or break the efficiency of molding processes.
-
Flow Performance: Ensuring smooth plastic flow is crucial; I’ve learned this firsthand with thin-walled products where missteps led to short shots. Position parting surfaces to ensure smooth plastic flow and avoid short shots by considering flow path lengths.
-
Venting: Venting is another critical aspect; using parting surfaces as venting channels can vastly improve product quality by expelling trapped air and gases during molding. Implement venting grooves for larger products or high-speed processes to improve product quality.
Table: Common Challenges vs Solutions
Challenge | Solution |
---|---|
Complex shapes | Side core mechanisms or forced demolding |
High appearance demand | Minimize parting surfaces, optimize gate placement |
Processing difficulties | Flat surfaces, advanced machining for curves |
Venting issues | Parting surface venting channels |
By tackling these challenges head-on with strategic solutions, designers can significantly boost the quality and efficiency10 of molded products. My experiences have taught me that with each project, there’s always something new to learn and innovate upon.
Simple shapes require complex parting surfaces.False
Simple shapes benefit from straightforward parting surfaces, simplifying the mold.
Venting channels improve product quality in molding.True
Venting channels help exhaust air and gases, preventing defects.
Conclusion
Effective design techniques for injection mold parting surfaces enhance product quality by considering shape, appearance, processing convenience, and injection molding dynamics to ensure smooth demolding and minimize defects.
-
This link explores why correctly positioning parting lines is essential for mold effectiveness and production efficiency. ↩
-
Discover industry standards and best practices that guide effective parting surface design for various products. ↩
-
Learn how injection molding impacts manufacturing efficiency and product quality. ↩
-
Discover how aligning with maximum contour simplifies mold structure for efficient manufacturing. ↩
-
Learn how latent gates improve transparency by stabilizing plastic flow in molding processes. ↩
-
Understand how gate placement affects plastic flow efficiency in mold cavities. ↩
-
Learn about handling simple shapes in injection molding for easier processing and assembly. ↩
-
Discover effective venting strategies to improve mold performance and product quality. ↩
-
Explore methods to select effective parting surfaces that simplify mold design and improve production quality. ↩
-
Discover how optimized parting surfaces contribute to better product quality and increased manufacturing efficiency. ↩