As someone deeply invested in the world of manufacturing, I know that injection molds are the unsung heroes of our production lines. Their longevity isn’t just a matter of cost; it’s about quality, efficiency, and trust.
The best anti-corrosion treatment methods for injection molds include selecting corrosion-resistant materials like stainless or alloy steel, applying surface treatments such as electroplating or nitriding, and maintaining regular cleaning and lubrication routines.
Let’s dive deeper into each method and discover how these strategies can elevate the lifespan and performance of your molds.
Stainless steel is corrosion-resistant for injection molds.True
Stainless steel offers high corrosion resistance, ideal for humid environments.
How Does Material Selection Affect Mold Durability?
Choosing the right materials for your molds can significantly impact their lifespan and performance.
Material selection is crucial for mold durability, influencing resistance to wear, corrosion, and operational efficiency. Opt for materials like stainless or alloy steel, which offer high corrosion resistance and strength.
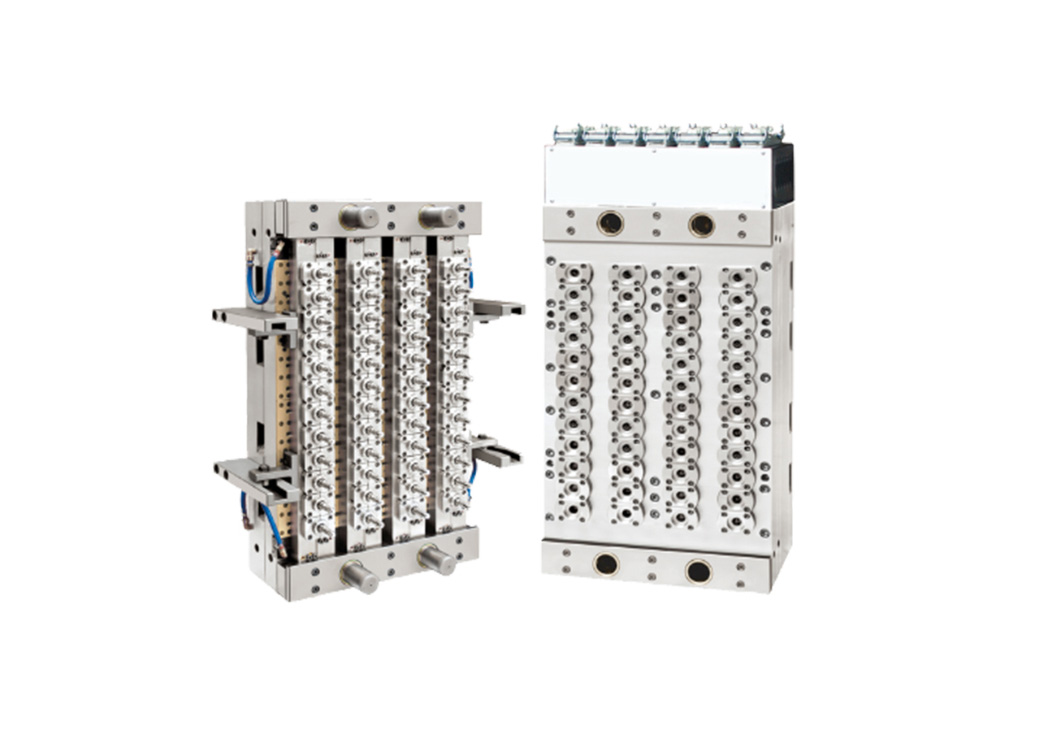
Understanding the Role of Material Selection
Material selection is a foundational aspect of mold design, affecting everything from production efficiency to product quality. When selecting materials, manufacturers should consider factors such as the environmental conditions the mold will face, the types of plastics being used, and the desired lifespan of the mold.
Key Material Options for Durability
-
Stainless Steel: Renowned for its excellent corrosion resistance, stainless steel is ideal for molds that are exposed to corrosive substances or operate in humid conditions. For instance, molds used with PVC or other chloride-based plastics benefit greatly from stainless steel.
-
Alloy Steel: Specially treated alloy steels provide a balance of strength and resistance to corrosion. These materials often contain elements like chromium or nickel, enhancing their protective properties against chemical erosion.
Material Type | Advantages | Ideal Applications |
---|---|---|
Stainless Steel | High corrosion resistance, longevity | Chloride-based plastics, humid settings |
Alloy Steel | Strength, tailored corrosion resistance | General-purpose molds |
Impact on Wear and Tear
Choosing the right material doesn’t just protect against corrosion; it also mitigates wear and tear. Hardness and toughness are crucial attributes:
-
Hardness: A harder material resists surface abrasions and deformations. For example, certain alloy steels can be treated to achieve higher surface hardness without compromising their structural integrity.
-
Toughness: This refers to a material’s ability to absorb energy and plastically deform without fracturing. Materials like maraging steel exhibit exceptional toughness, making them suitable for high-stress applications.
Customizing Material Properties
Beyond selecting from standard materials, manufacturers can enhance mold durability by tailoring material properties through treatments:
-
Heat Treatment: Processes such as annealing or quenching can adjust a material’s microstructure, improving its strength and hardness.
-
Surface Coating: Techniques like physical vapor deposition1 create a protective layer that reduces friction and enhances wear resistance.
By carefully choosing and treating mold materials, manufacturers can significantly extend the operational life of their molds, reduce maintenance costs, and improve product quality. To learn more about advanced material treatments, consider exploring coating techniques in injection molding2.
Stainless steel molds resist corrosion effectively.True
Stainless steel offers high corrosion resistance, ideal for humid or corrosive environments.
Alloy steel lacks strength compared to stainless steel.False
Alloy steel provides a balance of strength and corrosion resistance, often enhanced with treatments.
What Are the Benefits of Electroplating for Molds?
Electroplating molds significantly enhances their durability and performance by offering superior surface protection.
Electroplating provides molds with improved corrosion resistance, enhanced wear protection, and a smoother surface finish, ensuring longer lifespan and better performance.
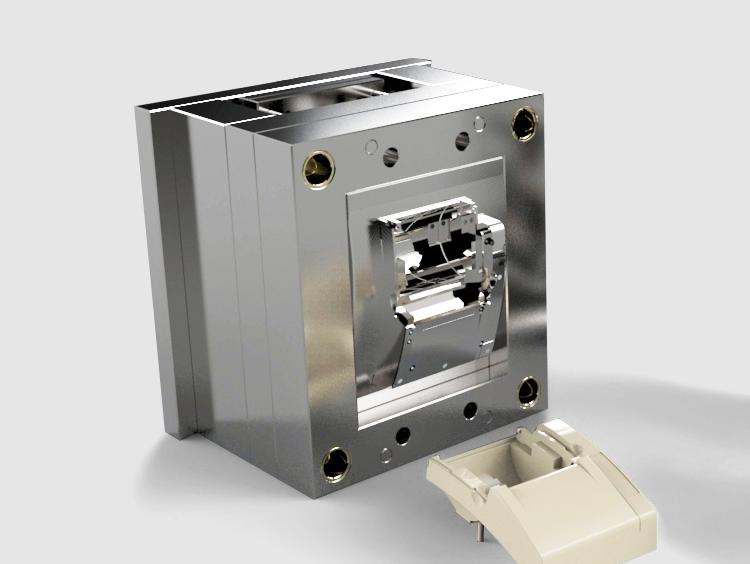
Enhanced Corrosion Resistance
One of the primary benefits of electroplating molds is the increased corrosion resistance it offers. By applying a layer of metal, such as chromium or nickel, onto the mold surface, electroplating acts as a protective barrier against corrosive substances found in certain plastics. This is especially critical when dealing with materials or environments that are naturally corrosive.
-
Chromium Plating: This type of plating forms a hard, smooth, and corrosion-resistant layer that can withstand various chemicals. It is ideal for molds exposed to aggressive substances during production.
-
Nickel Plating: Similar to chromium, nickel plating provides robust corrosion protection while also enhancing the surface hardness of the mold.
Improved Wear Protection
Electroplating not only shields molds from corrosion but also significantly improves their wear resistance. A plated mold can endure repeated use without suffering from the wear and tear typically seen with uncoated surfaces. This is crucial for maintaining the precise dimensions and smooth operation of molds over time.
Type of Plating | Corrosion Resistance | Wear Resistance |
---|---|---|
Chromium | High | Very High |
Nickel | Moderate | High |
Enhanced Surface Finish
A smoother surface finish is another benefit of electroplating. The coating fills in microscopic imperfections on the mold’s surface, resulting in a smoother finish that can reduce friction during the molding process. This can lead to easier demolding and less material buildup on the mold.
Additional Considerations
While electroplating offers numerous benefits, it’s essential to choose the right type of plating based on the specific requirements of your production environment. Factors such as temperature, pressure, and the types of materials being molded should be considered. Additionally, regular maintenance routines3 are necessary to ensure the longevity and effectiveness of the plated layer.
Exploring further into electroplating techniques4 can provide insights into selecting the best approach tailored to your needs.
Electroplating improves mold surface finish.True
Electroplating fills imperfections, resulting in a smoother finish.
Nickel plating offers better wear resistance than chromium.False
Chromium has very high wear resistance compared to nickel.
Why is Regular Mold Maintenance Critical?
Regular mold maintenance is crucial to extend mold life and ensure product quality.
Regular mold maintenance prevents corrosion, reduces downtime, and enhances product quality by ensuring molds function efficiently over their lifespan.

The Importance of Regular Cleaning
Regular cleaning of molds is vital to prevent the accumulation of plastic residues and dirt, which can lead to corrosion and defects in molded products. Effective cleaning involves using specialized cleaning agents and tools, such as copper brushes and compressed air, to maintain a pristine mold surface. This not only prevents corrosion but also ensures that the mold performs consistently, avoiding any interruptions in the manufacturing process.
Rust-Proofing Techniques
Applying rust-proof treatments during mold storage is essential for preventing damage from moisture and oxygen. Coating the mold with rust inhibitors or oils forms a protective layer, safeguarding it from corrosion. For long-term storage, using sealed packaging with a desiccant is recommended to keep the environment dry. These measures ensure that the mold remains in optimal condition when not in use, ready to produce quality products once back in operation.
Significance of Proper Lubrication
Lubrication plays a pivotal role in reducing wear and friction between moving parts of the mold. Applying the right lubricating oils or greases helps prevent corrosion and ensures smooth operation. It’s crucial to select products without corrosive elements and to regularly check and replace them to maintain their efficacy. This regular attention keeps the mold functioning efficiently, minimizing the risk of unexpected breakdowns.
Adhering to Operating Specifications
Properly controlling injection molding parameters like temperature, pressure, and speed is essential to prevent excessive wear and corrosion. Excessive temperatures can accelerate chemical reactions that corrode the mold, while high pressures can cause deformation. By optimizing these parameters according to specific materials and product requirements, manufacturers can significantly reduce wear on molds, enhancing their longevity and performance.
Regular maintenance practices are integral in maintaining mold integrity5 and ensuring that production lines remain efficient. Operators should also be trained in correct handling techniques to avoid damage during installation or disassembly, thus preserving the mold’s structural integrity. By adhering to these maintenance strategies, manufacturers can extend mold lifespan, improve product quality, and reduce operational costs over time.
Regular cleaning prevents mold corrosion.True
Cleaning removes residues that cause corrosion, ensuring longevity.
Ignoring lubrication reduces mold lifespan.True
Lack of lubrication increases wear, leading to premature mold failure.
How Can Operating Specifications Prevent Corrosion?
Operating specifications play a pivotal role in preventing corrosion in injection molds, ensuring longevity and efficiency.
By controlling injection molding parameters, avoiding corrosive materials, and ensuring proper handling, operating specifications minimize corrosion risks and enhance mold lifespan.

Control Injection Molding Process Parameters
Operating specifications primarily involve precise control over the injection molding process parameters such as temperature, pressure, and speed. Excessive temperatures can accelerate chemical reactions that lead to corrosion, while high pressure can cause wear and deformation.
For instance, optimizing parameters based on specific plastic materials can reduce stress on molds. Implementing a controlled cooling cycle prevents thermal shock, which is crucial in minimizing surface stress and potential corrosion. Operators should monitor these parameters consistently using advanced sensors and automated systems to maintain optimal conditions.
Avoid Using Corrosive Materials
Material selection is critical in operating specifications to prevent corrosion. Corrosive elements in raw materials, such as halogens or sulfur, can significantly damage molds. Therefore, selecting materials that do not react adversely with the mold’s surface is essential.
When usage of such materials is unavoidable, enhance the mold’s protective measures. Consider applying a corrosion-resistant coating or opt for materials that offer inherent resistance like stainless steel. Moreover, always aim to use additives and pigments free from corrosive elements.
Correctly Operate the Mold
Proper mold operation is another fundamental aspect of operating specifications. Operators should be trained thoroughly on the correct handling procedures to avoid unnecessary damage.
Table: Key Practices for Mold Operation
Practice | Description |
---|---|
Professional Training | Ensure all operators receive professional training on mold handling to reduce risks of physical damage and subsequent corrosion. |
Gentle Handling | During installation or disassembly, handle molds gently to prevent surface damage. |
Force Management | Avoid excessive force and rough operations to protect against scratches and other forms of physical wear. |
By integrating these specifications into daily operations, manufacturers can substantially extend the lifespan of their molds, leading to improved efficiency and reduced costs.
Explore corrosion prevention techniques6 for more insights into maintaining your manufacturing assets.
High pressure in molding causes corrosion.False
High pressure causes wear but not directly corrosion.
Corrosive materials damage injection molds.True
Materials like halogens or sulfur can corrode mold surfaces.
Conclusion
By adopting these anti-corrosion techniques, you can significantly enhance your injection molds’ longevity and performance. Reflect on your current practices and consider integrating these solutions to maintain high product standards.
-
Explore how PVD enhances mold surfaces against wear and corrosion.: One of the most significant aspects of PVD is its non-chemical nature, which means that no new substances are produced during the deposition. ↩
-
Discover advanced coatings that improve mold longevity and performance.: The Baking Approach. A common non-stick coating material used in injection molding applications is PTFE, polytetrafluoroethylene (say that three times fast). ↩
-
Learn why consistent maintenance is crucial for preserving electroplated molds.: Communication with your texturing and plating sources is key to properly maintaining the mold surface. ↩
-
Explore various electroplating methods suitable for diverse molding applications.: There are two basic types of plating – electrolytic and electroless. Electrolytic plating requires electricity to make the process occur. There … ↩
-
Explore how maintaining mold integrity boosts manufacturing efficiency and product quality.: Consistency and Precision: Quality control measures in injection mold manufacturing ensure the consistent production of precise plastic parts. ↩
-
Discover comprehensive techniques for prolonging mold lifespan.: Learn how to develop the best rust prevention strategy to prevent corrosion on your injection molds, including mold sprue bushings and bases with tips from … ↩