I once stood inside a busy factory, amazed by the skill and craft in each product.
Multi-stage injection molding resembles a hidden advantage. It provides precise control. This control helps products look better by lowering surface flaws and inner stress. It suits complex designs well. This process means greater efficiency. It means better quality in manufacturing.
I remember when I first found out about the magic of multi-stage injection molding. It was like discovering a secret tool that could change my production line completely. This technique truly provides great benefits. By adjusting each part of the injection process, I noticed a big drop in flow marks and silver streaks, which were always a problem when making high-quality plastic shells.
Also, this method helped me fix internal product stresses. These stresses sometimes cause warping and instability in size. Controlling speed and pressure at each stage allowed even complicated parts, like intricate plastic pieces with different wall thicknesses, to be perfect. It felt like reaching a new level in my manufacturing world. And let’s remember the extra benefit of matching material properties perfectly. Each component could meet its design purpose without losing performance.
Multi-stage injection improves product appearance.True
It offers enhanced control over the injection process, leading to better aesthetics.
Multi-stage injection increases internal stress in products.False
The technique actually reduces internal stress by optimizing the process.
How does multi-stage injection reduce surface defects?
Ever thought about how molded items look perfect? I’ll guide you through multi-stage injection molding. This method changes product quality by reducing annoying surface flaws. It truly changes everything.
Multi-stage injection molding reduces surface problems. It controls how fast and hard material enters the mold at different times. This method really decreases flow marks and silver streaks. It improves the look. It also improves the function of molded items. Functionality gets better. Aesthetic appeal increases.
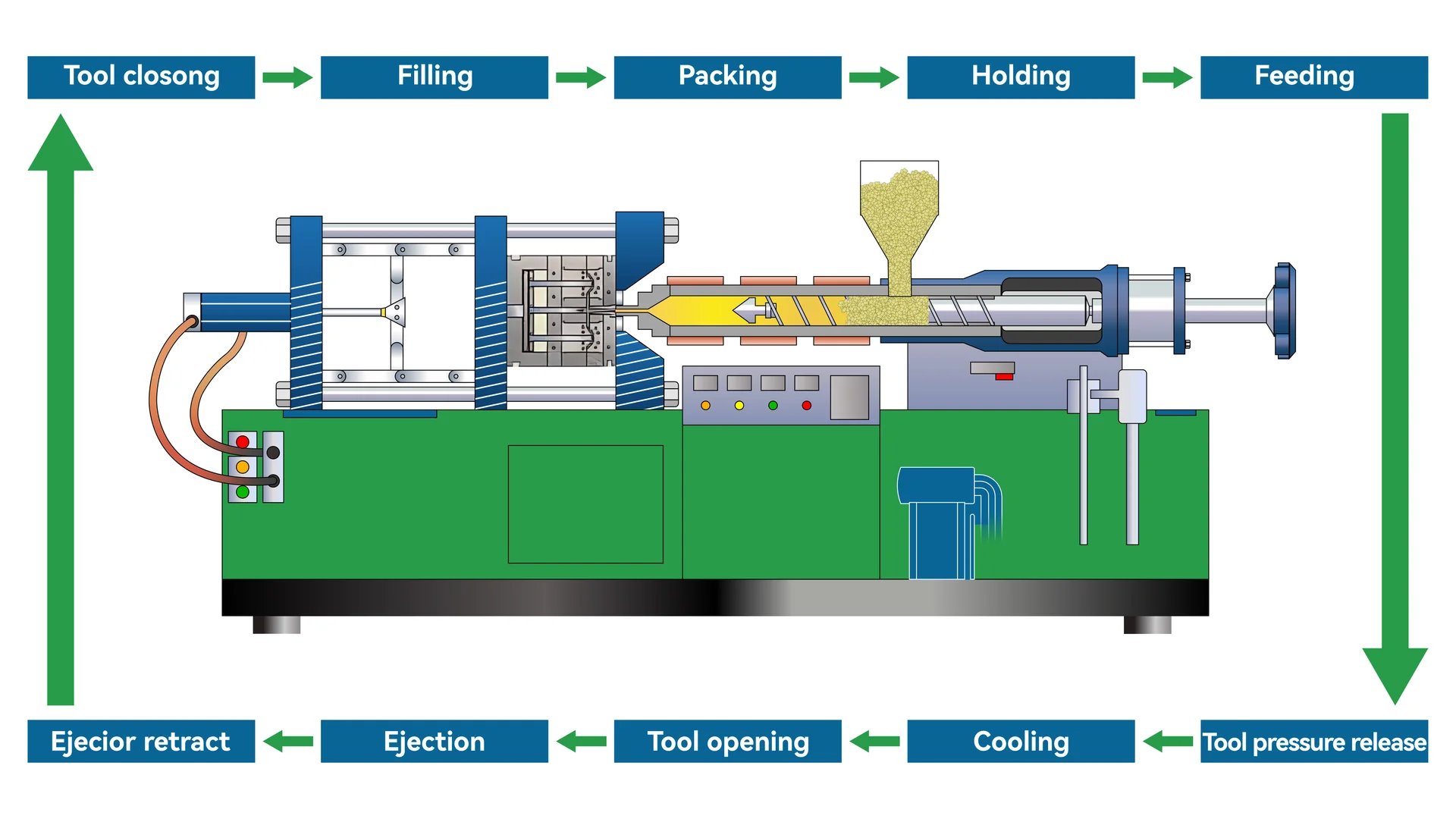
Understanding Multi-Stage Injection
Feeling that something finally fits perfectly is great. This is my experience with multi-stage injection molding. This method is not just about filling a mold with plastic; it involves coordinating each stage like a well-tuned orchestra. By adjusting the speed and pressure during injection, plastic products become not only useful but also beautiful.
Reducing Flow Marks
Flow marks are like those unexpected wrinkles causing trouble in the look of a molded product. Starting injection at a slower pace, around 30-50mm/s, helps the plastic melt enter smoothly. It is like gently entering a pool instead of jumping in. This prevents instability at the melt front, which is vital for sleek plastic shells.
Injection Stage | Speed (mm/s) | Benefits |
---|---|---|
Initial | 30-50 | Smooth entry of melt, reduced flow marks |
Subsequent | Adjusted | Ensures complete filling |
Controlling each step ensures every product has a smooth, perfect surface. A smooth surface is very important.
Preventing Silver Streaks
Silver streaks sound fancy, but they are unwanted on plastic items. These streaks show up from trapped gas during fast filling, like small hiccups in the process. Slowing the filling to 30-70mm/s lets the gas escape properly. This matters a lot for clear products where seeing everything clearly is key.
Enhancing Surface Accuracy
Imagine crafting beautiful textures but facing poor detail replication. Multi-stage injection helps here by managing initial injection speed to about 40mm/s so that the melt accurately fills detailed areas, capturing every detail clearly.
Internal Quality Improvements
Inside quality matters too, not just how things look outside. Careful speed and pressure adjustments lower internal stress, improve density and keep uniformity, especially in thick items. This stops problems like warping, ensuring the product performs well and looks good.
Moreover, even distribution keeps mechanical traits of strong engineering plastics steady and trustworthy.
Adapting to Complex Structures and Material Properties
Every product is unique, just like us. Multi-stage injection adjusts speed for different parts:
- Thin sections use lower speeds to avoid spraying,
- Thick areas need higher speeds for complete filling.
Understanding your plastics is crucial:
- Polyethylene handles higher speeds well due to its flow,
- Polycarbonate needs careful settings to avoid issues.
Material | Rapid Filling Speed (mm/s) | Characteristics |
---|---|---|
Polyethylene | 100-200 | Good fluidity |
Polycarbonate | 50-100 | High heat sensitivity |
Multi-stage injection provides a flexible method to optimize product appearance1, improve internal quality and fit easily with complex designs and materials.
Multi-stage injection reduces flow marks.True
Controlled speeds in multi-stage injection minimize flow marks by ensuring smooth melt entry.
Silver streaks are caused by slow filling stages.False
Silver streaks occur due to trapped gas, not slow filling; slower speeds help release gas.
How Can Multi-Stage Injection Enhance Product Quality?
Have you ever thought about improving the quality of your products during their production? Multi-stage injection molding offers a powerful solution. This method can change how products are created, leading to better results.
Absolutely! Multi-stage injection really improves the quality inside the product by reducing leftover stress. It also increases density and uniformity. This method allows very precise control during the filling process. Complex structures and unique material features are handled easily.
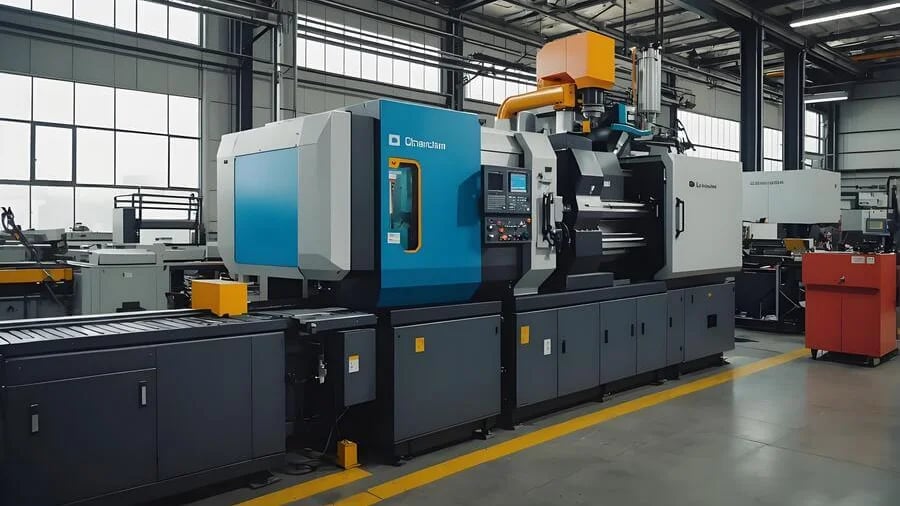
Personal Thoughts on Easing Internal Pressure
I recall the first moment I understood how vital reducing internal pressure was for product balance. During a project with thick-walled products, distortion caused big problems. We tried multi-stage injection to control speed at several phases – slowing down after fast filling to lower leftover stress. This method really changed the game in stopping warping.
Precision matters a lot. Even a tiny strain can create chaos. Multi-stage injection allowed dynamic adjustments of settings like speed and pressure to achieve better stability. For example, in a project with large, thick-walled plastic items2, managing speed changes became key to achieving great results.
Improving Density and Evenness Through Experience
Reaching even density was once a puzzle for me. Then, I found the magic of multi-stage injection. By carefully controlling melt spread, especially with high-performance engineering plastics, internal pores reduced dramatically. This method started slow so the melt could settle evenly, then picked up speed for full cavity filling.
In one notable project, this step-by-step tactic made sure the melt was perfectly blended3, raising the product quality beyond expectations. It was a fantastic success.
Navigating Complex Patterns
Working with detailed designs felt like solving a maze. Yet with multi-stage injection, dealing with different thicknesses within one piece became easier. I vividly remember a product with both thin-walled parts and thicker ones. A slower start stopped melt spraying in thin parts, while a faster pace ensured full filling of thicker areas.
This ability made producing complex designs a real, rewarding challenge, not just a possibility.
Adapting to Material Qualities
Various materials often brought specific hurdles in injection molding. Multi-stage injection let me tailor processes for different materials effortlessly. For example, polyethylene (PE), known for easy flow, needed a faster initial fill, while thicker materials like polycarbonate (PC) required slower speeds to avoid damage.
Tweaking these settings allowed me to improve molding quality to match both performance and appearance needs. This flexibility really helped when working with diverse materials in manufacturing settings.
Here’s a quick comparison of speed settings:
Material | Initial Speed (mm/s) | Rapid Fill Speed (mm/s) |
---|---|---|
Polyethylene (PE) | 100 – 200 | 100 – 200 |
Polycarbonate (PC) | 50 – 100 | 50 – 100 |
Understanding these techniques has been crucial in my role as a product designer. Insights into using multi-stage injection for better internal product quality have not only enhanced results but also brought more joy and reward to the process.
Multi-stage injection reduces internal stress in products.True
Adjusting speeds during injection minimizes residual stress, preventing warping.
Multi-stage injection cannot adapt to complex product structures.False
It allows speed adjustments for varying thicknesses, suiting complex designs.
How Does Multi-Stage Injection Revolutionize Complex Product Design?
Do you ever think about why certain products stand out in quality and design? Let me show you how multi-stage injection transforms the way complex products get designed.
Multi-stage injection plays a crucial role in complex product design. It improves surface quality and strengthens the product inside. This method precisely manages intricate structures and material properties.
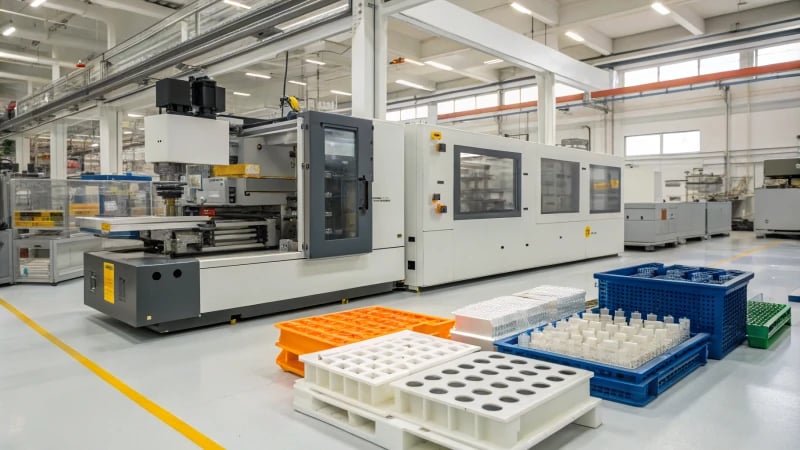
Optimizing Surface Quality
That satisfying feeling when a product feels just right? Multi-stage injection often creates that effect. This process is like a tool for designers, reducing unwanted flow marks and silver lines. Slowing the first injection to around 30-50mm/s allows the melt to smoothly enter the mold, giving a perfect surface4. Picture molding a plastic cover that’s as smooth as glass for your latest gadget. This technique achieves it.
Worked on a project needing a flawless finish? The joy of a perfect surface is truly hard to describe. It’s like flawlessly flipping a pancake – satisfying every time!
Improving Internal Product Integrity
Let’s shift to the inside of products. Multi-stage injection doesn’t only improve looks; it strengthens the core. Alternating fast and slow filling stages balances internal tension, increasing density and strength. It’s like a book with a strong story inside, not just a pretty cover.
When dealing with thick-walled products, this approach became crucial for me. It stopped warping and improved size stability. Like assembling the perfect puzzle.
Here’s how the stages might be controlled:
Stage | Speed (mm/s) | Benefits |
---|---|---|
Initial | 30-70 | Prevents silver streaks |
Subsequent | 100-200 | Ensures complete filling |
Accommodating Complex Structures and Material Properties
For complicated designs with thin and thick parts, multi-stage injection offers real help. It gets every detail right, much like your favorite song sounding good both live and recorded.
Plastics behave differently. Polyethylene prefers high speeds, while polycarbonate likes slow speeds. Selecting the right speed is like choosing the perfect playlist5 for exercising.
This careful control matters in molding quality. It lets products meet and even go beyond design goals, making them serve their purpose just right.
Multi-stage injection reduces flow marks in plastic products.True
By controlling injection speed, flow marks are minimized, enhancing surface quality.
Polycarbonate requires high initial speeds in multi-stage injection.False
Polycarbonate needs lower speeds to avoid degradation during the injection process.
How Does Multi-Stage Injection Adapt to Different Material Properties?
Ever wondered how multi-stage injection molding can make your product dreams a reality?
Multi-stage injection molding adjusts to different materials by changing settings such as speed and pressure. These adjustments match with the material’s flow, thickness and heat sensitivity. The result is a product that looks good and lasts long. Durability really matters.
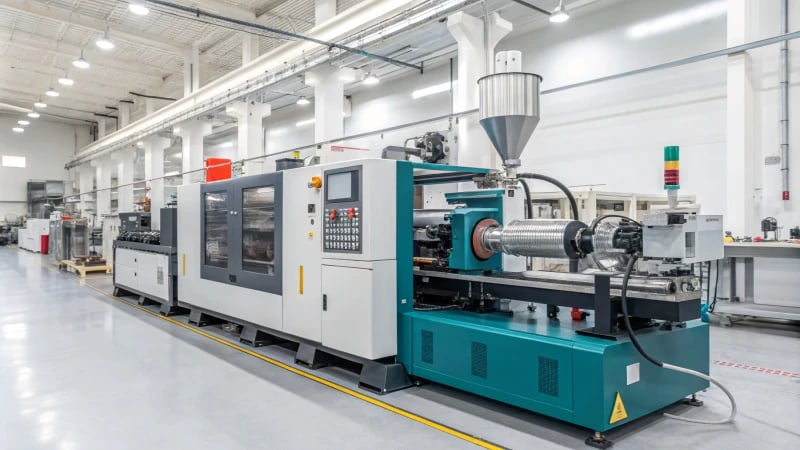
Adjusting to Material Changes
I remember the first challenge with various plastic types. It felt like meeting new friends, each with unique habits.
Material | Speed (mm/s) |
---|---|
Polyethylene | 100-200 |
Polycarbonate | 50-100 |
Polyethylene (PE) is that friend who is always on time – fast and smooth. A higher speed, between 100 – 200 mm/s, fills it perfectly without issues. Very effective.
Polycarbonate (PC) feels like a friend who needs extra care but is very valuable. Its poor flow and sensitivity to heat require a gentle approach. Slower speeds stop decomposition and keep quality high. It’s all about understanding your materials, like understanding friends.
Handling Material Thickness
Viscosity is another challenge. Imagine handling a very thick milkshake; it needs perfect balance. Multi-stage injection helps find that balance – adjusting settings for smooth flow. Slower speeds with thick materials reduce stress and defects, ensuring final products are just right.
By setting a controlled injection speed in the initial stages, manufacturers can minimize potential damage to the material’s properties.
Controlling Heat Sensitivity
Heat sensitivity? That’s when the work gets exciting. Think of slowly heating a delicate soufflé; you don’t want it to collapse or burn. By managing temperature and pressure carefully, multi-stage injection avoids overheating.
For example, by gradually increasing the temperature and pressure during each stage, the risk of overheating or degrading the material can be minimized. This ensures the final product maintains its designed mechanical properties6.
Improving Surface Finish
Surface quality matters a lot for look and feel. I worked on a project needing a perfect plastic surface. Adjusting speed early on helped avoid flow marks and silver lines.
Lower speeds in initial stages help in avoiding flow marks on products with high surface requirements7. The controlled speed ensures that gases escape effectively during the filling process, reducing visible defects.
Each project has unique problems, but multi-stage injection molding adapts to any material traits, making sure our creations function and look excellent.
PE requires high injection speed for smooth filling.True
Polyethylene (PE) benefits from 100-200 mm/s speed to avoid defects.
PC can be injected at the same speed as PE.False
Polycarbonate (PC) needs slower speeds due to poor fluidity.
Conclusion
Multi-stage injection molding enhances product quality by reducing surface defects, internal stress, and improving density. It adapts to complex designs and material properties for optimal manufacturing results.
-
This link provides detailed insights into how multi-stage injection enhances both visual and structural quality of plastic products. ↩
-
Learn techniques for minimizing residual stress in thick-walled plastics to improve stability and reduce warping. ↩
-
Discover effective methods to improve density and uniformity in injection molded parts for enhanced mechanical properties. ↩
-
Understanding how to minimize flow marks is crucial for achieving a high-quality surface finish in injection molded products. ↩
-
Exploring material properties aids in choosing the right settings for different plastics, enhancing product quality and performance. ↩
-
Explore methods to preserve mechanical properties during injection molding, crucial for high-performance applications. ↩
-
Discover techniques for achieving superior surface finishes in molded products, enhancing appearance quality. ↩