Have you ever thought about how to turn your product designs into effective, top-notch results? I found Mold Flow Analysis like a hidden treasure in the world of manufacturing. This tool really helps in creating great products.
Mold Flow Analysis enhances mold design and product quality by simulating the injection molding process, offering insights into plastic flow, cooling, and warping. It significantly boosts production efficiency.
I explored this technology deeply and saw that Mold Flow Analysis is a very influential tool for product design. It simulates the injection molding process. This provides crucial insights into how plastic flows, cools and warps. Designers refine mold designs before production. I recall my first project using this analysis. It was exciting to see that a few adjustments reduced defects and improved product quality significantly. Understanding these benefits will really empower design decisions. This holds true whether you are a veteran or just starting out.
Mold Flow Analysis improves product quality during manufacturing.True
This claim is true as Mold Flow Analysis helps identify issues early, leading to better quality products.
Mold Flow Analysis is not useful for optimizing mold design.False
This claim is false; Mold Flow Analysis is crucial for optimizing mold design and efficiency.
What is Mold Flow Analysis and How Does It Work?
Did you ever think about how factories get that perfect shine on plastic products? I want to tell you about Mold Flow Analysis. This process is really important in injection molding.
Mold Flow Analysis is a simulation tool used in injection molding to optimize mold design. It predicts plastic flow to reduce defects, improve product quality, and enhance production efficiency by analyzing filling, packing, cooling, and warping.
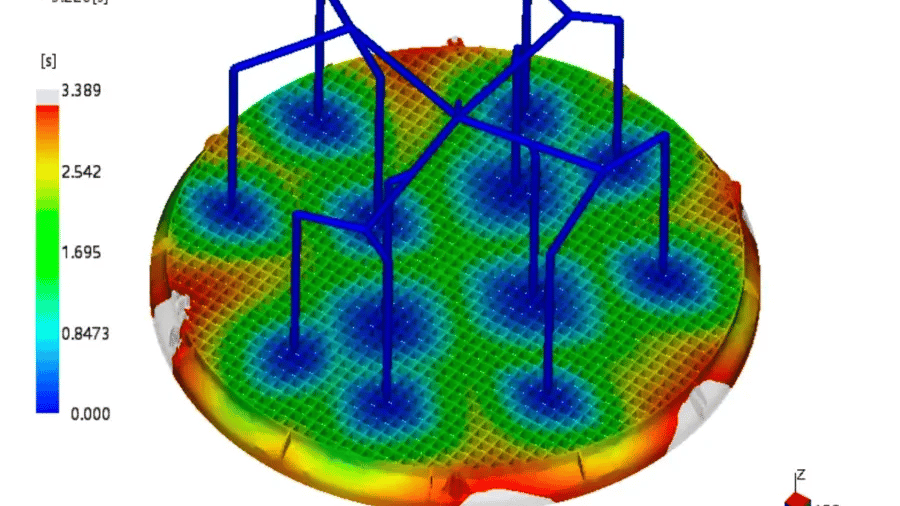
Understanding Mold Flow Analysis
Mold Flow Analysis has become a favorite technology in plastic injection molding. I remember when I first used it during a project with ongoing production problems. It felt like finding a secret power that let us simulate the injection before touching the molds. This technology allows engineers and designers to predict possible issues, optimize designs, and enhance product quality before production begins.
At its heart, Mold Flow Analysis uses ideas from computational fluid dynamics (CFD) to model how molten plastic moves in a mold cavity. By looking at different stages like filling, packing, cooling, and warping, I predict how plastic behaves under various conditions. It feels like having a crystal ball to see the future of each product we design.
Basic Principles of Mold Flow Analysis
Numerical Simulation
Numerical simulation forms the backbone of Mold Flow Analysis. With complex mathematical models, I replicate the behaviors of a special type of fluid. Let me simplify:
- Key Equations:
- Continuity Equation: Keeps mass constant during flow.
- Navier-Stokes Equation: Explains momentum.
- Energy Conservation Equation: Models temperature changes in the melt.
Solving these equations lets me simulate how the melt flows into complex mold shapes. For example, in a project with intricate design, simulation showed areas likely to trap air. This saved us from defects.
Main Analysis Contents
Filling Analysis
Filling analysis is key to understanding how well plastic fills the mold. This step uncovers:
- Flow Front Advancement: How fast and evenly does the melt flow?
- Defect Prediction: Are issues like short shots or flash expected before production?
Defect Type | Description |
---|---|
Short Shots | Melt fails to fill the entire cavity |
Flash | Melt overflows the cavity |
Recently, I used filling analysis to find the best gate locations for a thin-walled part. Without this, we probably would have faced uneven flow and delays due to changes.
Packing Analysis
After filling, packing analysis starts. It evaluates:
- Pressure Distribution: Is there enough pressure during cooling and shrinkage?
- Density Changes: How do density differences affect quality?
Good packing reduces shrink marks and deviations. I recall a time when lack of pressure led to concave surfaces. It was a valuable lesson!
Optimizing Mold Design and Product Quality
Mold Flow Analysis not only finds potential issues but also optimizes design. Adjusting gate locations and runner designs based on analysis results can significantly reduce costs and development time.
This technology really improves product quality by predicting defects early. It fine-tunes process settings like the best injection speed and cooling times for efficiency and consistency. For instance, optimizing the cooling system often prevents warping in sensitive parts. This is very important in automotive and electronics industries.
Summary of Advantages
Using Mold Flow Analysis in design processes offers many benefits:
- Optimized Mold Design: Less trial and error in mold development.
- Improved Product Quality: Early defect predictions during design.
- Efficient Process Parameters: Better production efficiency and consistency.
In my experience, Mold Flow Analysis saves time and raises the quality of final products. It is truly an essential tool in modern manufacturing that every designer should use.
Mold Flow Analysis predicts defects before production starts.True
By simulating the injection process, Mold Flow Analysis helps identify potential defects like short shots early in the design phase, enhancing product quality.
Mold Flow Analysis uses basic fluid mechanics principles only.False
Mold Flow Analysis employs advanced computational fluid dynamics and complex mathematical models, not just basic fluid mechanics principles, for accurate simulations.
How Can Mold Flow Analysis Improve Product Quality?
Have you ever found defects in your products even after spending many hours designing them? I completely understand that feeling. Mold flow analysis plays a crucial role. It really improves product quality in injection molding. It helps to identify issues before they cause problems.
Mold flow analysis enhances product quality by predicting injection molding defects, optimizing design, ensuring even cooling, and improving dimensional accuracy, ultimately reducing production costs and increasing product distinctiveness.
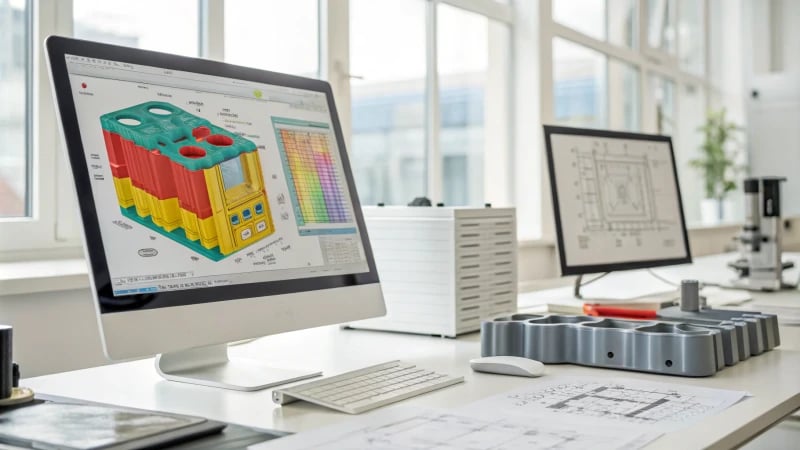
Understanding Mold Flow Analysis
Mold flow analysis is very important for anyone in injection molding. This powerful technology simulates the injection molding process, providing valuable insights into how materials behave under various conditions. By utilizing numerical simulation1 based on computational fluid dynamics (CFD), it helps manufacturers to predict potential issues before they arise.
Key Components of Mold Flow Analysis
-
Filling Analysis
This step looks at how plastic fills the mold cavity. Filling analysis assesses how the plastic melt fills the mold cavity and can identify defects like short shots and flash. For instance, optimizing gate locations ensures even melt flow, minimizing cavitation . -
Packing Analysis
Pressure is very important in this step. During the packing stage, maintaining the right pressure is crucial. Insufficient pressure can lead to concave surfaces, while excessive pressure may cause demolding issues. Predicting pressure distribution through mold flow analysis is essential for quality assurance . -
Cooling Analysis
Cooling needs to be effective. Effective cooling is vital in the injection molding process. Mold flow analysis calculates temperature distribution, helping to optimize the cooling system layout. A good cooling system shortens the cycle and prevents warping. I worked on a temperature-sensitive part and optimizing cooling was key. -
Warping Analysis
Warping can destroy a perfect part. Warping can significantly affect the quality of molded parts; analyzing filling, holding, and cooling processes helps predict warping issues. This is critical for precise parts in cars and electronics.
Benefits of Mold Flow Analysis for Product Quality
Benefit | Description |
---|---|
Optimize Mold Design | Allows designers to adjust parameters before manufacturing, reducing trial-and-error costs. |
Predict Defects Early | Identifies potential problems like shrinkage marks and warpage, enabling preemptive solutions. |
Enhance Efficiency | Improves injection molding process stability by fine-tuning parameters such as speed and pressure. |
Increase Dimensional Accuracy | Ensures products meet aesthetic and functional specifications through comprehensive analysis. |
From my experience, using mold flow analysis improves product quality significantly; it really increases market competitiveness and customer satisfaction by optimizing processes before production begins.
Mold flow analysis can predict potential defects before production.True
By simulating the injection molding process, manufacturers can identify issues like warpage and shrinkage early, allowing for timely corrections.
Cooling analysis is unnecessary in mold flow analysis.False
Cooling analysis is vital for optimizing temperature distribution, preventing warping, and ensuring product quality during the injection molding process.
How Can Mold Flow Analysis Help Lower Manufacturing Costs?
Have you faced surprise expenses in manufacturing? I definitely have! This experience made me very excited to learn about mold flow analysis. It is really important for lowering costs in injection molding. Let’s explore this interesting topic together!
Mold flow analysis reduces manufacturing costs by predicting defects, optimizing mold design, and improving cycle times, ensuring high product quality throughout the injection molding process.
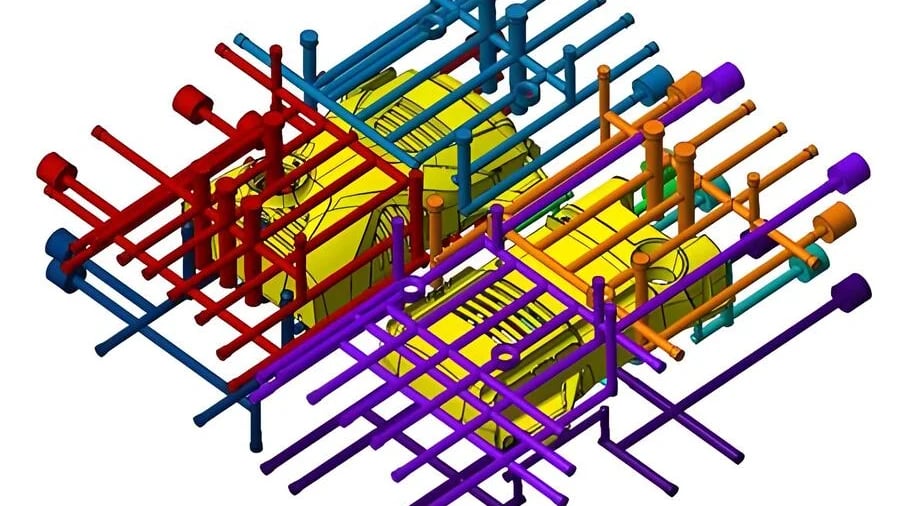
Understanding Mold Flow Analysis
Mold flow analysis is pivotal in optimizing the injection molding process, directly influencing cost reduction. It simulates the behavior of plastic during the molding phase, allowing designers to foresee potential issues.
By leveraging computational techniques like Computational Fluid Dynamics (CFD), it offers insights into flow, pressure, and cooling, ultimately enhancing efficiency. This predictive capability can significantly reduce the need for costly adjustments during production.
Key Benefits of Mold Flow Analysis
- Optimized Mold Design
Using mold flow analysis helps in refining mold designs before actual manufacturing begins.- Reduced Trials: Fewer trials lower costs and decrease stress.
- Gate Optimization: By adjusting the position and size of gates, manufacturers can ensure optimal filling and minimize defects.
Benefit | Description |
---|---|
Reduced Development Costs | Fewer iterations on molds lead to cost savings. |
Enhanced Filling | Improved melt flow reduces short shots and flashes. |
- Improved Product Quality
The software can predict various defects that may arise during the injection process, such as short shots and warpage.- Quality Assurance: Anticipating issues enhances product quality and dimensional accuracy.
Defect Type | Impact on Cost |
---|---|
Short Shots | Increases scrap and rework costs. |
Warpage | Leads to product rejection rates. |
- Efficient Process Parameters
Mold flow analysis aids in determining optimal parameters like injection speed and cooling time, enhancing overall production efficiency.- Cycle Time Reduction: Faster cycles lead to increased output without compromising quality.
Parameter | Effect on Cost |
---|---|
Injection Speed | Higher speeds can decrease cycle time. |
Cooling Time | Shorter cooling times improve throughput. |
Conclusion
Mold flow analysis plays a critical role in reducing costs by optimizing mold design, improving product quality, and enhancing production efficiency. By utilizing this powerful tool, manufacturers can achieve significant cost savings while maintaining high standards of quality in their products. For those interested in diving deeper into this subject, resources on mold design optimization2 and defect prevention strategies3 can provide additional insights into effective practices in this field.
Mold flow analysis reduces the need for costly adjustments.True
By predicting issues before production, mold flow analysis minimizes expensive changes during the manufacturing process, leading to cost savings.
Mold flow analysis guarantees defect-free products.False
While it improves quality and reduces defects, it cannot guarantee that all products will be defect-free due to other variables in production.
How Can Mold Flow Analysis Transform Design for Different Materials?
Have you ever wondered why some designs work perfectly in production? Mold Flow Analysis probably helps a lot. This technique plays a key role in improving designs. Different materials in injection molding benefit from it. Mold Flow Analysis is truly crucial.
Mold Flow Analysis enhances design by simulating injection processes to predict defects and optimize parameters like filling and cooling, improving efficiency and product quality across different materials.
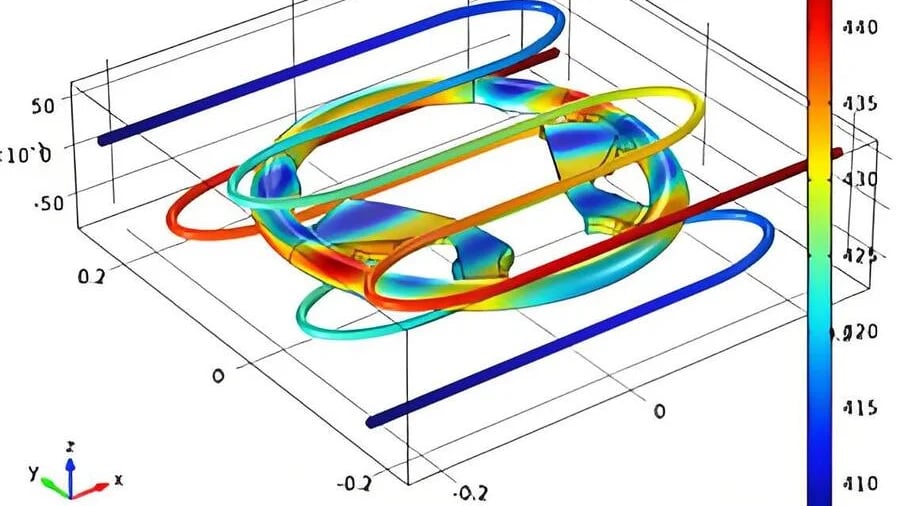
Understanding Mold Flow Analysis
Mold Flow Analysis is a big change in injection molding. I first learned about it at my previous job during a project. We had problems with defects in plastic parts. A mentor then suggested Mold Flow Analysis. The experience was very enlightening.
Mold Flow Analysis is like having a crystal ball for injection molding. Designers use it to see how liquid plastic fills a mold. They use complex simulations based on fluid dynamics and heat transfer. It models how the plastic behaves. We deal with this plastic every day.
When I saw the simulations, I was amazed. Changing pressure, speed or temperature could really alter the results. It seemed like a superpower. We could spot issues early, before they became expensive problems.
How Does It Optimize Design?
- Filling Analysis
Filling analysis is where the magic happens. It shows how well plastic fills the mold. By simulating flow front advancement, potential problems can be predicted. Issues like short shots or overflowing are identified.
Issue | Description | Solution |
---|---|---|
Short Shots | Melt fails to fill the cavity | Optimize gate location |
Overflow | Melt overflows the cavity | Adjust injection speed |
I remember facing short shots in one project. By adjusting the gate location according to our filling analysis, fill rates improved a lot.
-
Packing Analysis
Packing analysis is very important. Pressure must stay steady to handle volume changes during cooling. Pressure predictions help in setting the right holding pressures.- Insufficient holding pressure may lead to concave surfaces, while excessive pressure can cause demolding difficulties.
-
Cooling Analysis
Cooling is where design meets efficiency. Improving the cooling process can maybe reduce cycle times greatly. Cooling analysis calculates temperature distributions and helps design an effective cooling system layout.- By analyzing cooling pipe arrangements, designers can ensure even cooling across all areas, avoiding warping.
-
Warping Analysis
Warping can damage dimensional accuracy. Warping analysis takes shrinkage and stresses into account to predict changes.
Material Type | Susceptibility to Warping | Solutions |
---|---|---|
High-precision parts | High | Adjust molding parameters |
Thin-walled parts | Moderate | Optimize gate design |
Advantages of Using Mold Flow Analysis
- Design Optimization: Before making molds, I optimize gate, runner and cooling designs which really reduces trials and costs.
- Quality Improvement: Predicting defects lets me adjust to improve quality and precision.
- Process Parameter Optimization: Encourages finding the right balance of pressure, speed and cooling times for better operations.
In summary, Mold Flow Analysis is not just a tool; it is a very valuable asset that plays an important role in design for injection molding. My journey taught me it provides insights beyond simulations that improve both production quality and efficiency.
Mold Flow Analysis predicts injection defects effectively.True
It simulates the injection process to identify potential issues like short shots or flash, allowing for timely adjustments to design.
Cooling analysis in Mold Flow reduces cycle times.True
By optimizing cooling system layouts, it ensures even cooling, which enhances efficiency and minimizes warping during production.
Conclusion
Mold Flow Analysis optimizes injection molding by predicting defects, enhancing product quality, and improving production efficiency through advanced simulations.
-
Discover how mold flow analysis can significantly reduce production defects and improve quality standards. ↩
-
Explore detailed insights on mold flow analysis benefits to enhance production efficiency and reduce costs in manufacturing processes. ↩
-
Learn about practical strategies and case studies on implementing mold flow analysis for cost efficiency in injection molding. ↩