Remember the first time you realized the impact of quality standards on production efficiency?
ISO 9001 certification for injection molding enhances efficiency, product quality, and customer satisfaction, aligning processes with global standards to strengthen market presence and client trust.
Thinking back, when I first delved into ISO 9001, it felt like opening a door to endless possibilities. Sure, the path to certification seemed daunting, but witnessing the transformation in operational processes was nothing short of remarkable. Let’s explore how ISO 9001 can be a game-changer for your injection molding business, drawing inspiration from success stories of those who’ve walked this path before.
ISO 9001 certification improves product quality in injection molding.True
ISO 9001 ensures processes meet international quality standards.
ISO 9001 certification decreases customer satisfaction in molding.False
The certification actually increases customer satisfaction by ensuring quality.
- 1. How Does ISO 9001 Enhance Operational Efficiency in Injection Molding?
- 2. How Does ISO 9001 Influence Product Quality?
- 3. How Can ISO 9001 Certification Enhance Customer Satisfaction?
- 4. How Does ISO 9001 Certification Influence Market Positioning?
- 5. What are the costs involved in achieving ISO 9001 certification?
- 6. How Do Companies Benefit from ISO 9001 in the Injection Molding Industry?
- 7. Conclusion
How Does ISO 9001 Enhance Operational Efficiency in Injection Molding?
Back when I first started in the mold industry, understanding standards like ISO 9001 felt like deciphering an ancient script. But once I grasped its potential, it revolutionized our operations.
ISO 9001 boosts operational efficiency in injection molding by ensuring consistent quality, reducing waste, and optimizing processes, leading to better resource utilization and higher customer satisfaction.
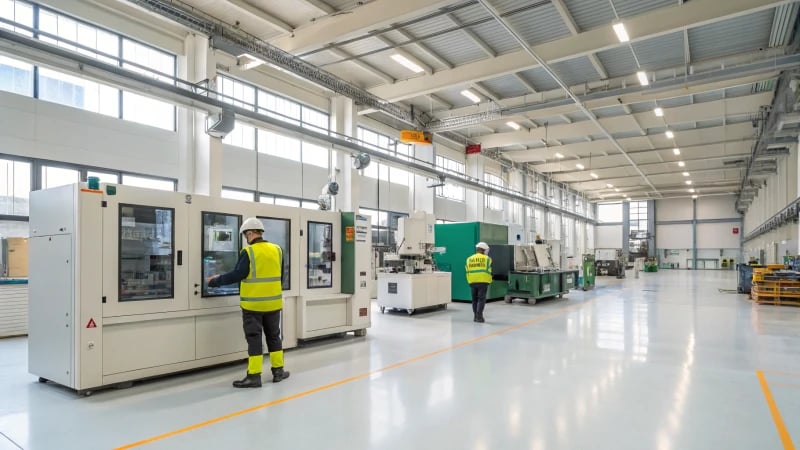
Standardization of Processes
When I first implemented ISO 9001, it was like finally tuning an orchestra after years of cacophony. Standardizing processes in injection molding means that each production run becomes as predictable as a sunrise. For me, this consistency was a game-changer. Suddenly, I could rely on each batch meeting the same high standards, which made my job—and the lives of everyone down the line—a lot easier. This standardization1 ensured that each step was clearly outlined, making training new team members smoother and more efficient.
Process | Description |
---|---|
Design Validation | Verifying product meets requirements |
Tool Calibration | Ensuring equipment precision |
Production Control | Monitoring process parameters |
Waste Reduction
I remember those early days when waste seemed like an inevitable evil. With ISO 9001, however, it felt like finding a hidden map to treasure. By focusing on continuous improvement2, I learned to spot inefficiencies that I hadn’t even realized were draining resources. Techniques like root cause analysis helped me dig deeper into problems that seemed superficial at first.
- Identify – Spot waste sources.
- Analyze – Understand waste causes.
- Improve – Implement waste reduction strategies.
Enhanced Product Quality
The rigorous quality checks under ISO 9001 became my secret weapon for superior product quality. There was a time when customer complaints about defects were an uncomfortable part of my monthly routine. Implementing these systematic procedures meant those complaints dwindled, and trust blossomed with each successful delivery. This consistent quality control3 reduced rework costs and boosted our reputation.
Improved Resource Management
Resource management under ISO 9001 was like discovering a new app that organized my life. It emphasized optimal use of materials and machinery, leading to impressive cost savings. Better scheduling and forecasting meant I could allocate resources with the precision of a master chef measuring spices, ensuring everything was in its right place at the right time.
Increased Customer Satisfaction
Finally, adhering to ISO 9001 was my gateway to happier customers. Delivering high-quality products consistently wasn’t just about meeting expectations; it was about exceeding them and building loyalty. This approach opened up new market opportunities, ensuring our competitive edge in the industry remained sharp.
In conclusion, embracing ISO 9001 was not just about enhancing operational efficiency; it was about paving the way for sustainable growth and innovation in the injection molding sector.
ISO 9001 standardizes injection molding processes.True
ISO 9001 provides guidelines that ensure consistency in production.
ISO 9001 increases waste in injection molding.False
ISO 9001 focuses on continuous improvement, reducing waste effectively.
How Does ISO 9001 Influence Product Quality?
ISO 9001 is like the compass guiding a ship through stormy seas, ensuring every product reaches the shore of quality and consistency.
ISO 9001 improves product quality by standardizing processes, enhancing customer satisfaction, and promoting continuous improvement, leading to consistent products, fewer defects, and better manufacturing efficiency.
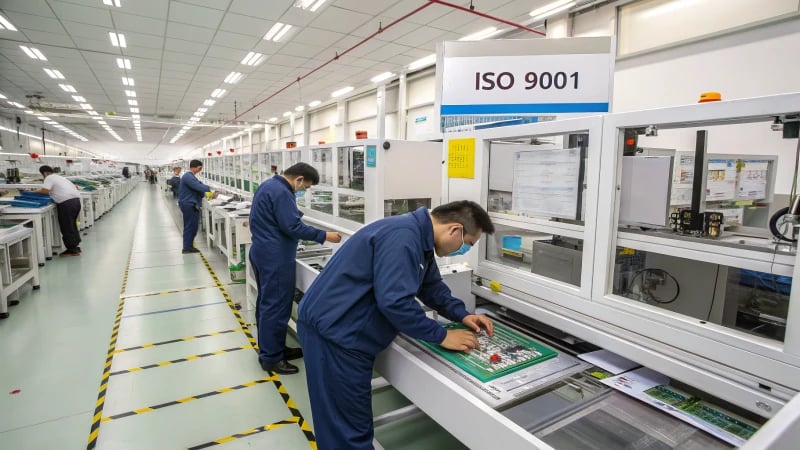
Understanding ISO 9001’s Core Principles
When I first dove into the world of quality management, ISO 9001 felt like learning a new language. It’s all about adopting a process-driven approach to quality management4. Imagine setting clear objectives, assessing risks like a seasoned navigator, and crafting procedures that promise consistent outcomes. Embracing ISO 9001 means meeting customer expectations with every product shipped.
Benefits of ISO 9001 on Product Quality
I remember a time when we had to comb through heaps of documentation to streamline operations. With ISO 9001, this documentation becomes a lifeline. It’s our blueprint for identifying improvement areas and taking corrective actions. Following these guidelines has been instrumental in reducing variability in our production processes.
Benefit | Description |
---|---|
Consistency | Ensures uniformity in production, reducing defects |
Efficiency | Optimizes resources, lowering operational costs |
Customer Satisfaction | Aligns products with customer expectations, enhancing loyalty |
Real-World Examples of ISO 9001 Impact
Picture this: a mid-sized company specializing in consumer electronics, much like the one I work in. After adopting ISO 9001, we witnessed a remarkable drop in production errors. It wasn’t just about numbers; it translated into happier customers and more repeat business. This is how ISO 9001 nurtures a culture of continuous improvement5.
Challenges and Considerations
Implementing ISO 9001 isn’t without its hurdles. I’ve seen firsthand how changes can stir up resistance among employees. The certification process can be quite demanding, requiring substantial resources6 to succeed.
Adopting ISO 9001 demands commitment to ongoing education and adaptation. Training our team and keeping documents up-to-date are crucial steps in leveraging its full potential for improving product quality.
ISO 9001 guarantees improved product quality.False
ISO 9001 sets a framework for quality management but does not guarantee outcomes.
ISO 9001 reduces production process variability.True
The standard's guidelines help identify and correct deviations, reducing variability.
How Can ISO 9001 Certification Enhance Customer Satisfaction?
ISO 9001 certification might sound like a formal business term, but it could be the secret ingredient to happier customers. Here’s why it matters.
ISO 9001 certification enhances customer satisfaction by ensuring consistent quality, fostering continuous improvement, and building trust, aligning business processes with customer needs to boost loyalty and satisfaction.
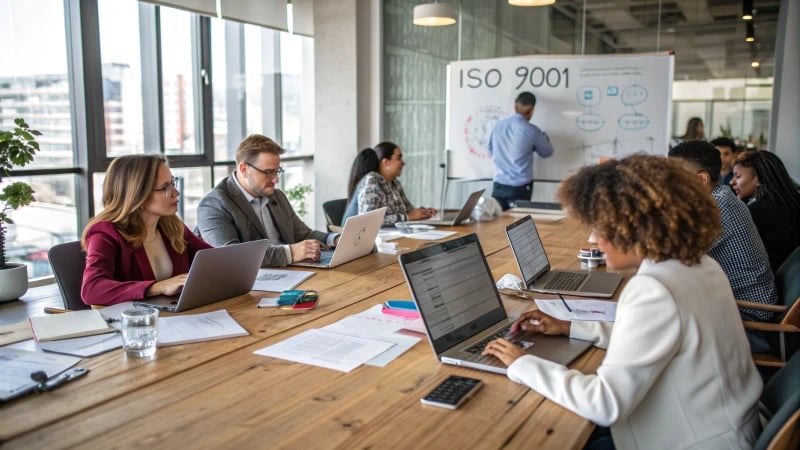
Understanding ISO 9001 Certification
I remember when I first heard about ISO 9001. It seemed like just another box to tick off on the compliance checklist. But digging deeper, I found that it’s an international standard that sets out criteria for a quality management system (QMS). When companies like mine decide to get certified, it’s not just about meeting regulatory requirements—it’s about proving we can consistently deliver what our customers need.
Key Benefits of ISO 9001
- Consistency: Implementing ISO 9001 means documenting, monitoring, and refining processes. This ensures the products and services we offer are reliable, which in turn builds trust with our customers.
- Continuous Improvement: The standard isn’t static; it pushes us to keep improving. This focus is crucial for enhancing customer experience7 over time.
How Does It Impact Customer Satisfaction?
Benefit | Impact on Customers |
---|---|
Enhanced Quality | Fewer defects and returns, leading to satisfaction. |
Reliability | Builds trust and fosters long-term relationships. |
Responsiveness | Improved service response times and issue resolution. |
Real-world Examples
In my journey, I’ve seen firsthand how companies across various industries have reported higher customer satisfaction after getting ISO 9001 certified. For example, in the world of manufacturing, firms often see a direct link between QMS implementation and customer loyalty. Case studies8 reveal that certified companies typically score higher in customer satisfaction surveys than those without.
Challenges and Considerations
Of course, implementing ISO 9001 isn’t without its hurdles. There are costs involved, time commitments, and a need for employee training. But from where I stand, the long-term benefits in customer satisfaction make these challenges worth tackling.
If you’re interested in exploring how ISO 9001 affects various sectors9, take a look at some industry-specific examples and strategies to make certification work for you.
ISO 9001 ensures fewer product defects.True
ISO 9001's focus on quality management reduces defects, enhancing satisfaction.
ISO 9001 certification guarantees customer loyalty.False
While it can improve satisfaction, other factors influence customer loyalty.
How Does ISO 9001 Certification Influence Market Positioning?
When I first learned about ISO 9001 certification, I realized it was more than just a fancy title. It was a powerful tool that could truly elevate a company’s market presence. Here’s how this certification can impact competitiveness and customer trust.
ISO 9001 certification enhances market positioning by demonstrating a commitment to quality, increasing consumer trust, unlocking business opportunities, and improving operational efficiency.
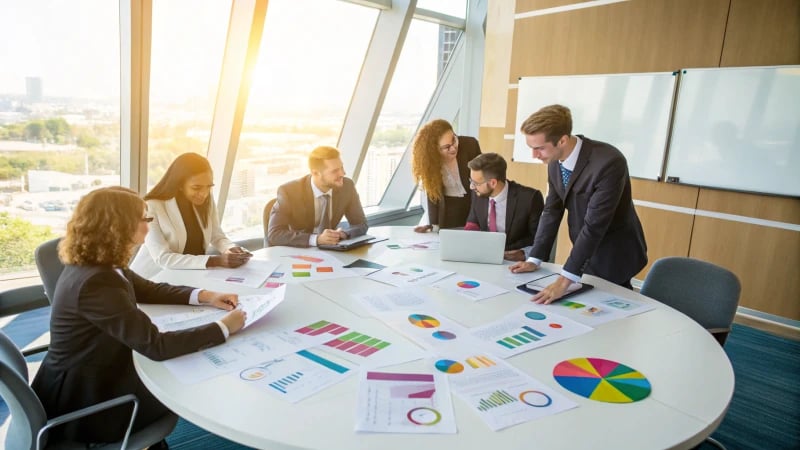
Understanding ISO 9001 Certification
When I first delved into the realm of ISO 9001, I was fascinated by how it serves as a benchmark for quality management systems (QMS) worldwide. Companies with this certification aren’t just ticking boxes; they’re proving they can consistently deliver products and services that meet high customer and regulatory standards. It’s this consistency that acts as a catalyst in strengthening a company’s position in the market.
Enhancing Customer Trust
I’ve seen firsthand how obtaining ISO 9001 certification can significantly boost customer trust. When a company is certified, it’s like they’re wearing a badge that screams reliability and commitment to quality. This perception of trust is invaluable—it often translates into increased customer loyalty and a bolstered brand reputation10. In my experience, these elements are the bedrock of effective market positioning.
Benefits of ISO 9001 | Description |
---|---|
Increased Credibility | Certification acts as proof of a company’s commitment to quality. |
Market Expansion | Access to new markets that require ISO certification. |
Operational Efficiency | Streamlined processes improve overall efficiency. |
Access to New Markets
I remember discussing with colleagues how many industries set ISO 9001 certification as a baseline requirement for suppliers. This can be a game-changer for companies looking to break into international markets. For instance, sectors like automotive and aerospace often mandate this certification, opening up expansive opportunities for certified companies to broaden their customer base11.
Improving Operational Efficiency
Implementing ISO 9001 standards prompted us to meticulously document our processes, revealing efficiencies we hadn’t tapped into before. This led to reduced waste and costs while boosting product quality. Such improvements not only fortified our internal operations but also amplified our standing in the marketplace.
Competitive Advantage
In an arena teeming with competitors, standing out is crucial. ISO 9001 certification offers a distinct edge by signaling adherence to global quality standards. I found this particularly impactful when competing against non-certified companies, as it made us an attractive option for clients seeking assured quality.
Feature | Certified Company | Non-Certified Company |
---|---|---|
Quality Assurance | Internationally recognized | Varies by company |
Market Opportunities | Broader | Limited |
Customer Perception | High trust | Uncertain |
The strategic advantages that come with ISO 9001 certification make it indispensable for any company aiming to enhance its market positioning and secure long-term success. By embracing consistent quality, we didn’t just refine our internal processes; we also crafted an enhanced external image and market presence.
ISO 9001 certification improves customer trust.True
ISO 9001 certification signals reliability and commitment to quality.
Non-certified companies have broader market opportunities.False
ISO 9001 certification often opens access to new markets.
What are the costs involved in achieving ISO 9001 certification?
Have you ever found yourself staring down the path to ISO 9001 certification and wondering about the financial toll it might take?
ISO 9001 certification costs vary by organizational size, complexity, and preparedness, covering certification fees, consulting, internal resources, and training. Careful budgeting is crucial for a successful certification process.
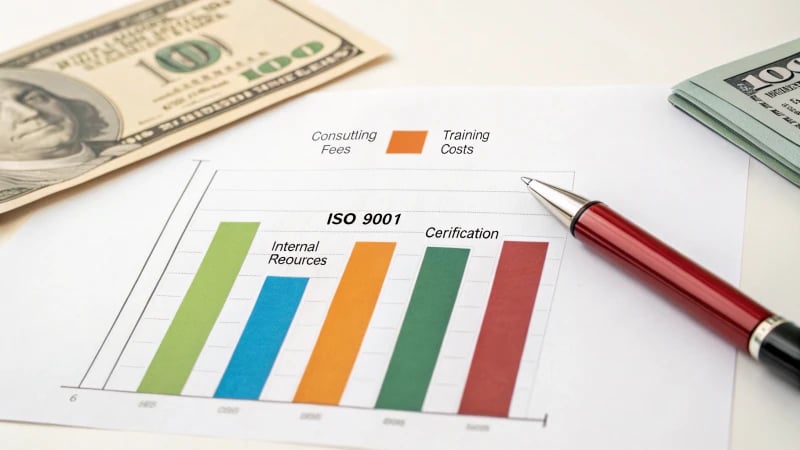
Understanding the ISO 9001 Certification Costs
Let’s dive into the nitty-gritty of what getting that ISO 9001 badge might really cost us. Back when I first started considering it for my company, I felt like I was trying to piece together a financial puzzle. Here’s what I’ve learned about the potential expenses:
-
Certification Fees: These fees go to the certifying body, covering application processing, auditing, and the actual certificate itself. When I looked into it, I found that the size and complexity of my company were major factors in determining how much we’d pay.
-
Consulting Costs: The whole process can seem daunting, which is why many—myself included—turn to consultants. These experts can guide us through developing a quality management system, conducting pre-assessment audits, and training our staff.
-
Internal Resource Allocation: This was a bit of an eye-opener for me. Preparing documentation and implementing necessary changes takes time and effort from our team, which can add up, especially if it means shifting focus from existing responsibilities.
-
Training Expenses: Training our employees on ISO standards is non-negotiable. The costs might include materials, sessions, and the time invested by our team.
Factors Influencing Costs
As I navigated through this journey, I realized several factors could swing the costs one way or another:
Factor | Impact on Costs |
---|---|
Organization Size | Larger organizations may face higher certification fees. |
Complexity of Operations | Complex processes might require more intensive audits. |
Current Readiness | Companies closer to compliance spend less on consultancy. |
It’s worth exploring options with different certifying bodies and consultants to manage costs effectively. For insights on how organization size impacts costs, you might want to dive into our in-depth guide12.
Budgeting for ISO 9001 Certification
Budgeting strategically is where the magic happens. As I tackled this in my company, I learned to:
- Conduct a Cost-Benefit Analysis: Weighing the benefits of certification against expenses helped me justify every penny spent.
- Plan Financially: Spreading the budget over several fiscal periods eased cash flow pressures.
For an in-depth look at financial planning strategies for ISO 9001, take a peek at this resource13. It could be just the thing you need to make your journey smoother.
Certification fees depend on company size.True
Larger organizations typically face higher certification fees due to complexity.
Consultants are unnecessary for ISO 9001 certification.False
Consultants help streamline the process, making them beneficial for many companies.
How Do Companies Benefit from ISO 9001 in the Injection Molding Industry?
Remember the feeling when everything just falls into place? That’s what ISO 9001 brings to the injection molding world.
ISO 9001 benefits injection molding companies by enhancing product quality, streamlining processes, and improving customer satisfaction, leading to better market positions and increased client trust.
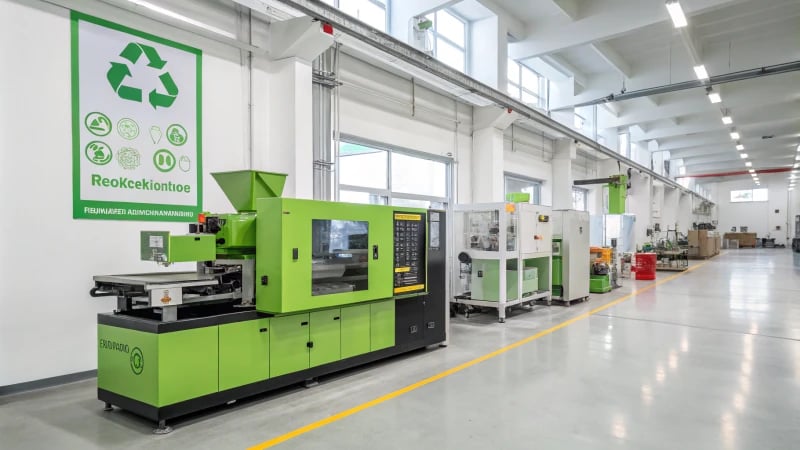
Enhancing Product Quality
I remember the first time I realized how crucial quality was in our industry. It was during a project where a single oversight could’ve cost us our biggest client. That’s when I truly appreciated the value of ISO 9001. For injection molding companies like ours, it’s all about meeting those exacting specifications every time. This standard ensures we’re not just producing parts but creating products that consistently meet high-quality benchmarks. It’s reassuring for us and, more importantly, for our clients, who trust that their expectations will always be met or even exceeded.
One of the foremost benefits of ISO 9001 for injection molding companies is the enhancement of product quality. By adhering to these standards, companies can consistently produce parts that meet exact specifications, reducing defects and rework. This ensures that customer satisfaction14 remains high, as products meet the desired quality expectations.
Operational Efficiency and Cost Reduction
There’s nothing quite like seeing a streamlined process in action. ISO 9001 taught us the magic of efficiency—how cutting down waste not only saves money but also sharpens our competitive edge. Implementing standardized procedures meant fewer headaches over wasted resources and more focus on what really matters: delivering top-notch products on time. In fast-paced sectors like consumer electronics15, this efficiency is not just beneficial; it’s essential.
ISO 9001 encourages the establishment of efficient processes that lead to cost reduction. By implementing standardized procedures, companies can minimize waste and optimize resource use. This not only reduces production costs but also shortens lead times, which is critical in meeting tight deadlines common in the consumer electronics sector.
Benefit | Description |
---|---|
Consistent Quality | Reduces defects and rework |
Cost Efficiency | Minimizes waste and optimizes resources |
Shortened Lead Times | Critical for meeting tight deadlines |
Boosting Customer Trust and Market Position
I remember sitting across from a potential client, sensing their skepticism melting away as soon as they saw our ISO 9001 certification. It’s more than just a piece of paper; it’s a promise of quality and reliability. This certification has opened doors for us, allowing us to stand out in a crowded marketplace and giving clients the confidence that we’re up to any challenge they throw our way.
ISO 9001 certification acts as a trust signal to clients and stakeholders. It assures them that the company follows rigorous quality management standards, which enhances credibility. This can be a decisive factor when clients are selecting suppliers for large projects, thus improving a company’s competitive advantage16.
Strategic Decision-Making
With ISO 9001, we’ve become data-driven decision-makers. Collecting and analyzing data is no longer a chore; it’s a tool for transformation. It empowers us to pinpoint improvement areas and adapt swiftly to shifting market demands. This strategic agility has been a game-changer for us.
Implementing ISO 9001 helps companies collect and analyze data effectively, leading to informed decision-making. Companies can identify areas for improvement and monitor performance metrics regularly, enabling them to adapt strategies swiftly to changing market demands.
Employee Engagement and Satisfaction
Finally, there’s the impact on our team. Implementing ISO 9001 wasn’t just about systems and processes; it was about people. Our staff became more engaged, seeing how their efforts directly contribute to high-quality outcomes. The pride in their work is palpable, boosting morale and job satisfaction across the board.
ISO 9001 fosters an environment of continuous improvement and accountability, which often leads to higher employee engagement. When employees see the impact of their work on quality outcomes, it boosts morale and job satisfaction.
For more insights on how ISO 9001 transforms manufacturing strategies17, we often engage in comprehensive training programs to ensure our staff are aligned with quality objectives.
ISO 9001 reduces defects in injection molding.True
ISO 9001 enhances product quality by standardizing processes, reducing defects.
ISO 9001 increases production costs for companies.False
ISO 9001 minimizes waste and optimizes resources, reducing production costs.
Conclusion
ISO 9001 certification enhances injection molding operations by improving product quality, operational efficiency, and customer satisfaction, ultimately leading to stronger market presence and increased client trust.
-
Explore how standardized processes improve efficiency and consistency, crucial for maintaining high-quality production. ↩
-
Discover effective strategies within ISO 9001 to minimize waste and improve operational processes. ↩
-
Understand how rigorous quality control practices ensure defect-free production and enhance customer satisfaction. ↩
-
Understanding how ISO 9001 improves quality management helps organizations ensure their processes align with international standards. ↩
-
Continuous improvement is vital for maintaining competitive advantage, making this insight crucial for businesses. ↩
-
Identifying necessary resources ensures successful adoption and integration of ISO 9001 practices. ↩
-
Explore how consistent quality management practices enhance overall customer experience. ↩
-
Learn from real-world examples of companies that improved customer satisfaction post-certification. ↩
-
Discover how ISO 9001 certification impacts various sectors differently. ↩
-
Explore how ISO 9001 certification strengthens brand reputation and why it’s crucial for market differentiation. ↩
-
Learn about new business opportunities available through ISO 9001 certification and how it aids in market expansion. ↩
-
Discover how the size of your organization influences certification expenses. ↩
-
Learn effective financial planning strategies to manage ISO certification costs. ↩
-
Discover how ISO 9001 enhances customer satisfaction through consistent quality assurance. ↩
-
Learn how ISO 9001 aids in meeting the stringent requirements of consumer electronics. ↩
-
Explore how ISO 9001 certification provides a competitive edge in the marketplace. ↩
-
Understand how ISO 9001 influences strategic planning in manufacturing. ↩