In the ever-evolving world of manufacturing, finding that competitive edge can feel like a treasure hunt. That’s where gas assist injection molding comes into play—this innovative technique is reshaping the way we create products, and its benefits are simply too good to ignore!
Gas assist injection molding improves product quality by reducing surface defects, optimizes material usage by creating hollow structures, and increases production efficiency through faster cooling cycles.
But hold on! There’s so much more to uncover beyond these highlights. Let’s delve deeper into the many advantages that gas assist injection molding offers—your manufacturing processes might just be on the brink of a revolution!
Gas assist injection molding reduces material use by 50%.True
Gas assist creates hollow sections, cutting raw material needs by up to 50%.
How Does Gas Assist Injection Molding Improve Product Quality?
Gas assist injection molding is transforming product manufacturing by enhancing quality through innovative techniques. Curious how it achieves this?
Gas assist injection molding enhances product quality by minimizing defects like shrinkage and warpage, improving surface aesthetics, and increasing structural integrity.
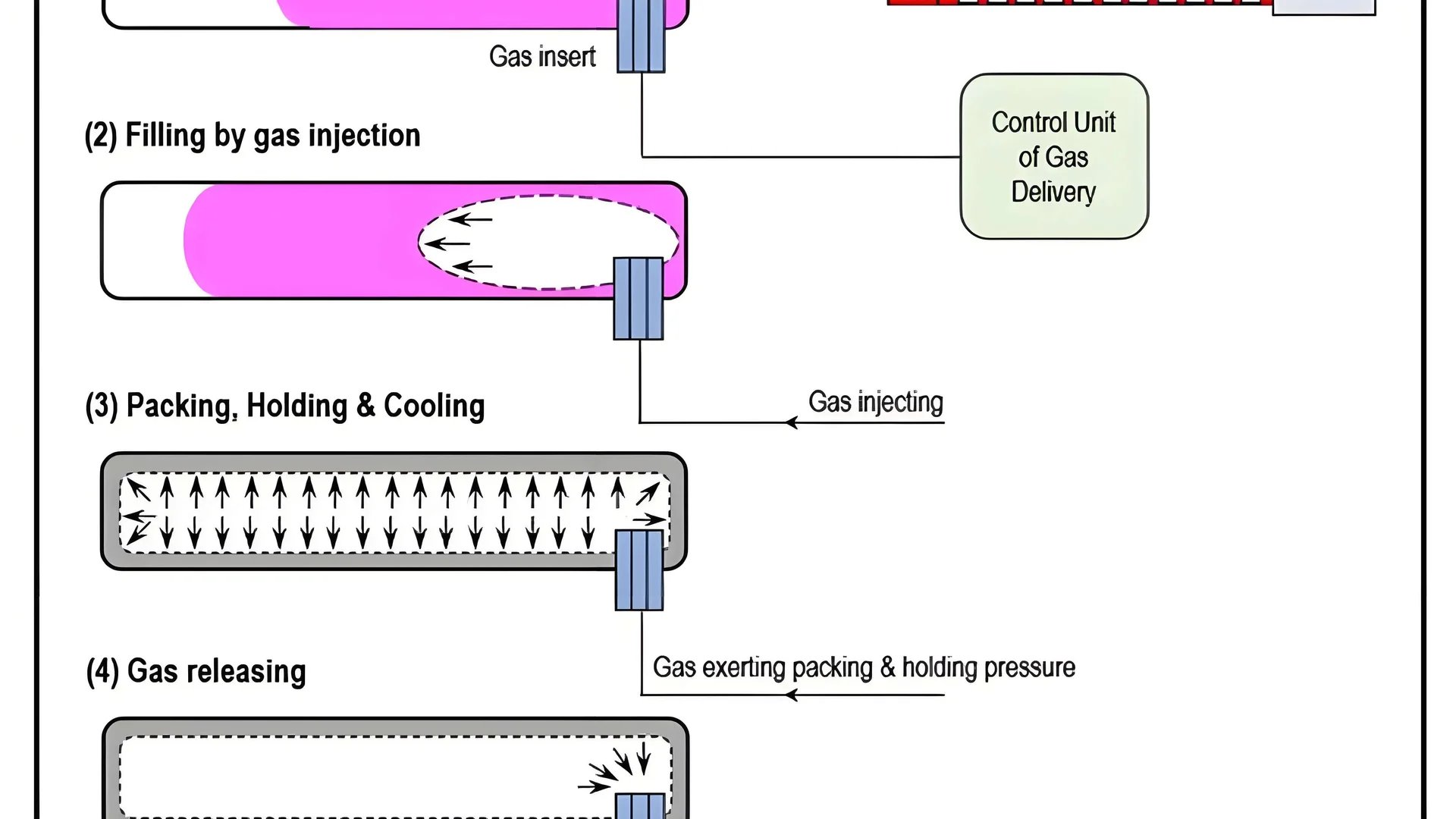
Understanding Gas Assist Injection Molding
Gas assist injection molding involves injecting an inert gas, usually nitrogen, into molten plastic within a mold. This process creates hollow sections within the part, which can reduce material use and enhance quality.
Minimizing Surface Defects
One of the primary benefits of this technique is its ability to reduce surface shrinkage and warpage1. The gas forms a hollow core, applying uniform pressure on the molten plastic. This uniform pressure compensates for shrinkage as the plastic cools, leading to smoother surfaces and better dimensional stability.
Additionally, this method can significantly improve weld lines and ripples. The gas drives the molten plastic more evenly throughout the mold cavity, reducing these common surface defects and enhancing the product’s appearance.
Enhancing Structural Integrity
The uniform internal pressure not only minimizes surface defects but also enhances the structural integrity of products. By decreasing internal stress during cooling, the risk of warping is reduced, which results in higher precision and dimensional accuracy. This is particularly beneficial for products requiring tight tolerances or complex geometries.
Improving Aesthetic Quality
Gas assist injection molding also contributes to superior aesthetic quality. By reducing weld lines and ripples, products appear more visually appealing. This can be crucial for consumer goods where appearance significantly impacts marketability.
Practical Examples
Imagine a plastic chair manufactured using traditional methods; it might suffer from visible shrink marks or uneven surfaces. However, employing gas assist injection molding ensures a smoother finish and consistent quality, enhancing both functionality and aesthetic appeal.
This technology’s adaptability to a wide range of thermoplastics like polypropylene and polycarbonate further extends its application across various industries.
In conclusion, gas assist injection molding offers substantial improvements in product quality by addressing both structural and aesthetic concerns. By incorporating this advanced technique, manufacturers can achieve higher-quality products that stand out in the competitive market.
Gas assist injection molding reduces material usage.True
The process creates hollow sections, using less material.
Gas assist injection molding increases surface defects.False
It minimizes defects like shrinkage and warpage, improving aesthetics.
In What Ways Does This Technique Optimize Material Use?
Gas assist injection molding not only enhances product quality but also significantly optimizes material use, making it a cost-effective choice.
Gas assist injection molding optimizes material use by forming hollow sections within parts, reducing raw material consumption by up to 50%. This technique maintains structural integrity while minimizing waste, effectively lowering production costs.
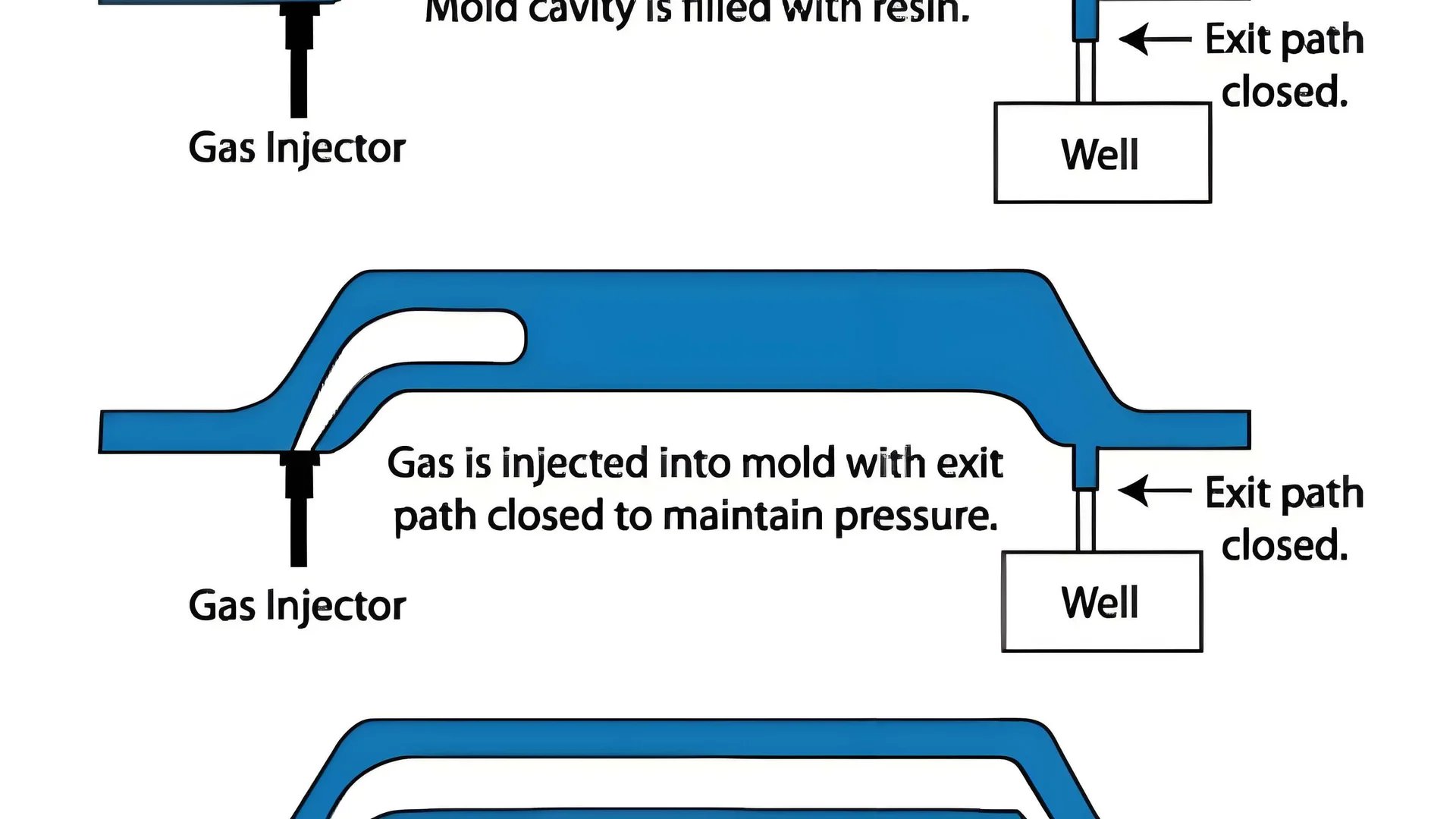
Efficient Raw Material Utilization
One of the standout benefits of gas assist injection molding is its ability to drastically reduce raw material usage. By creating hollow structures within the product, this technique can lower the amount of plastic required by an impressive 40% to 50%. Such efficiency is particularly advantageous for manufacturing large or thick-walled products, where material savings translate into substantial cost reductions.
This reduction doesn’t compromise the strength or performance of the final product. The hollow sections are strategically designed to maintain the necessary structural integrity, ensuring that the product meets all performance standards. This capability allows manufacturers to deliver high-quality products while keeping production expenses in check.
Design Simplification and Cost Reduction
The innovative use of gas assist injection molding also leads to simpler and more cost-effective mold designs. Previously complex structures that were necessary to ensure quality can now be simplified thanks to the pressure-equalizing effects of gas assistance. This simplification not only reduces mold manufacturing costs but also decreases the overall processing difficulty.
Simpler molds mean quicker turnaround times and fewer resources spent on mold creation and maintenance. Consequently, manufacturers can produce more products at a lower cost, enhancing their competitive edge.
Enhanced Production Flexibility
Gas assist injection molding provides manufacturers with the flexibility to work with a variety of thermoplastics, including popular choices like polypropylene (PP), ABS, and polycarbonate (PC). This versatility extends the applicability of this technique across diverse industries, from automotive to consumer electronics.
Moreover, the reduced mold cavity pressure inherent in gas-assisted processes allows for the use of smaller tonnage injection molding machines. This capability not only saves on equipment costs but also enables the use of multi-cavity molds, further boosting production efficiency and material savings.
Through these multifaceted approaches—efficient material usage, simplified mold design, and enhanced production flexibility—gas assist injection molding offers manufacturers a significant opportunity to optimize their operations and reduce waste. For more insights into how this technology impacts other areas2 of manufacturing, explore additional resources that highlight its wide-ranging benefits.
Gas assist injection molding reduces material use by 50%.True
It forms hollow sections, cutting raw material use by up to 50%.
Simpler mold designs increase production costs.False
Simpler molds reduce manufacturing costs and processing difficulty.
What Impact Does Gas Assist Injection Molding Have on Production Efficiency?
Gas assist injection molding is transforming manufacturing with its efficiency-enhancing capabilities. But how exactly does it impact production processes?
Gas assist injection molding enhances production efficiency by shortening cycle times, enabling multi-cavity molds, and reducing equipment costs.
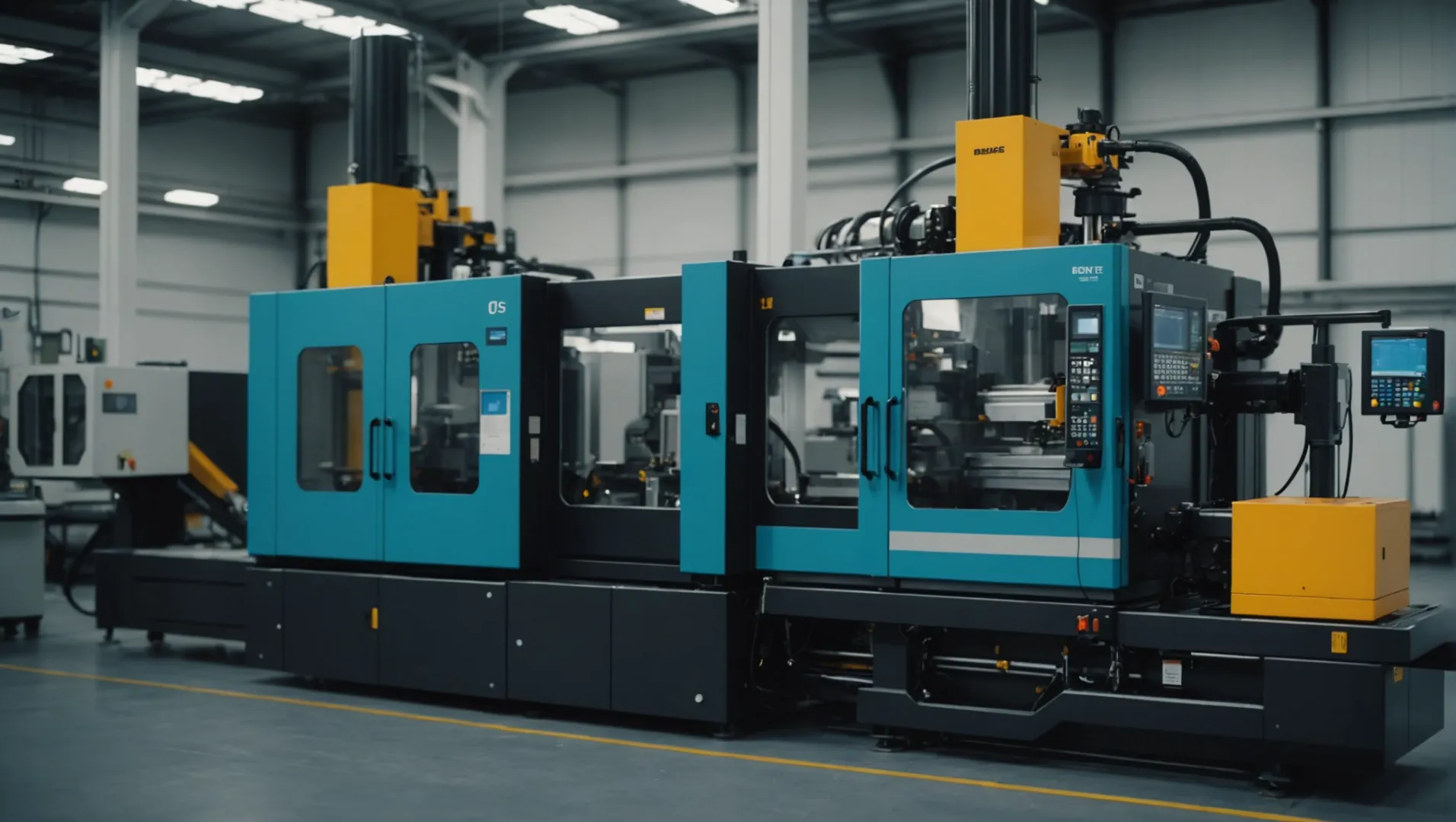
Shortening Production Cycle Times
One of the standout benefits of gas assist injection molding3 is its ability to shorten production cycles significantly. The technique promotes faster cooling, thanks to the hollow sections created within the product. This enhanced heat dissipation translates to reduced cooling times, leading to quicker turnover from mold to finished product.
For instance, products that traditionally took an hour for cooling may now take a fraction of that time. This reduction in cooling time not only boosts throughput but also enables manufacturers to meet high demand without compromising on quality.
Enabling Multi-Cavity Molds
The reduction in mold cavity pressure is another crucial factor contributing to improved efficiency. Lower pressures mean that a single mold can accommodate multiple cavities without risking structural integrity or precision loss. This capability allows manufacturers to produce more units per cycle, effectively doubling or tripling output depending on the mold design.
The table below illustrates the potential increase in output using multi-cavity molds:
Number of Cavities | Traditional Injection Molding Output | Gas Assist Injection Molding Output |
---|---|---|
1 | 100 units | 100 units |
2 | 180 units | 200 units |
4 | 320 units | 400 units |
Reducing Equipment and Operational Costs
Gas assist injection molding can operate efficiently on smaller tonnage machines due to decreased mold pressure. This reduction means that manufacturers can invest in less expensive equipment and save on operational costs related to machine maintenance and energy consumption.
Moreover, the simplification in mold design reduces the complexity and cost of mold manufacturing. As a result, companies can allocate resources more effectively, investing in other areas such as quality control or innovation.
In summary, gas assist injection molding offers substantial gains in production efficiency through faster cycles, enhanced mold capabilities, and lower operational costs. These advantages not only improve throughput but also provide a competitive edge in cost management and resource allocation.
Gas assist molding shortens production cycles.True
Gas assist molding reduces cooling time, speeding up production.
Multi-cavity molds increase output in gas assist molding.True
Lower pressure allows more cavities, boosting production per cycle.
How Environmentally Friendly is Gas Assist Injection Molding?
As industries strive for greener practices, evaluating the environmental impact of gas assist injection molding becomes crucial. How does this innovative technique fare in sustainability?
Gas assist injection molding is environmentally friendly due to its efficient use of materials, reduced energy consumption, and potential for recycling gases, aligning with eco-friendly manufacturing practices.
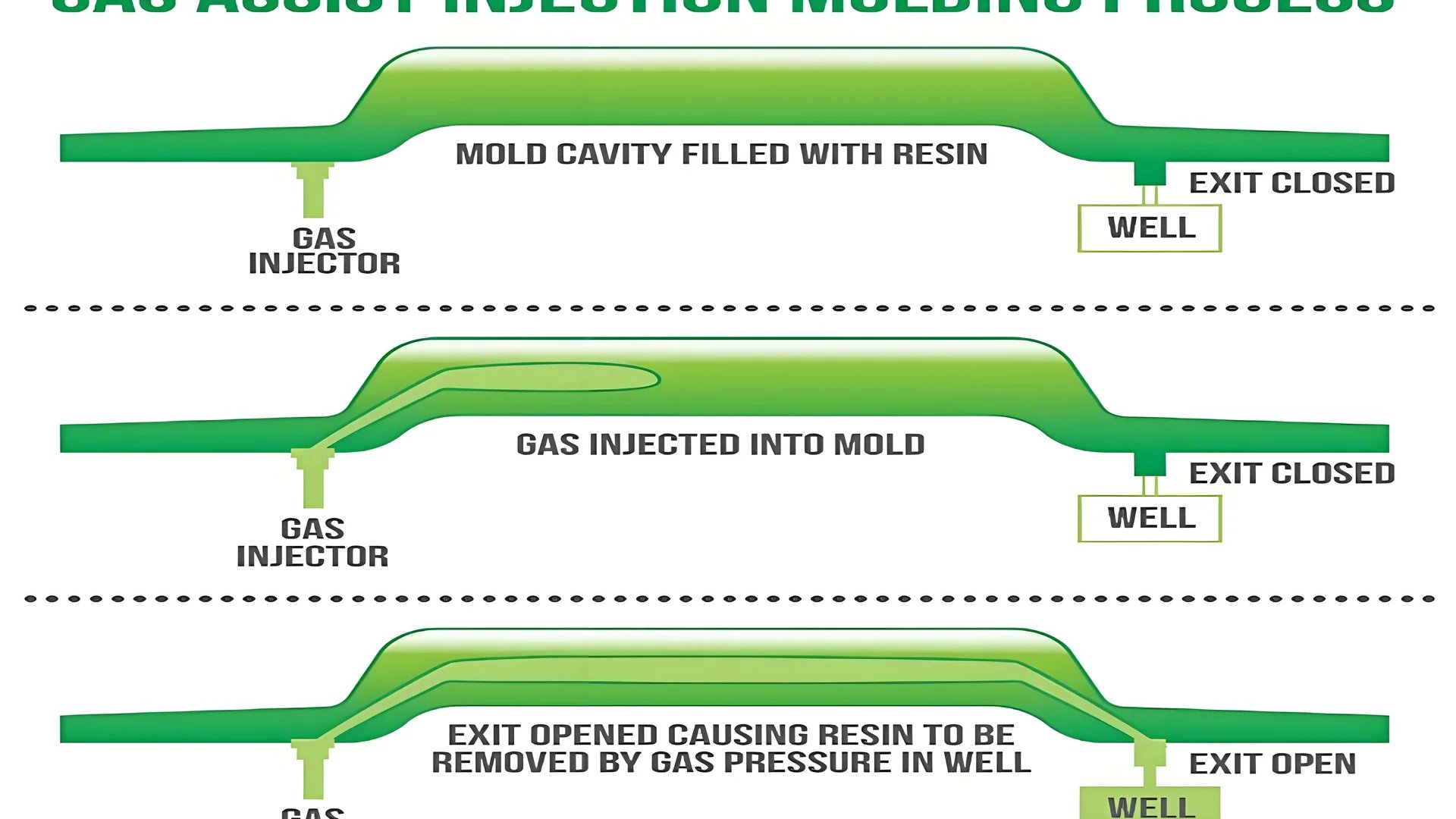
Efficient Use of Materials
Gas assist injection molding significantly reduces the amount of raw plastic required. By forming a hollow structure within the mold, it uses up to 50% less material without compromising product strength or integrity. This efficiency not only lowers costs but also decreases the environmental footprint by minimizing plastic waste.
Energy Consumption and Efficiency
The energy savings associated with gas assist injection molding are substantial. The technology’s ability to shorten cooling cycles directly translates to reduced energy use. Less energy is required for heating and cooling during the production process, which lowers the overall carbon emissions associated with manufacturing. As a result, manufacturers can achieve energy-efficient production4 that meets modern environmental standards.
Recycling and Reusability
Another key environmental advantage is the potential for recycling gases used in the process. Unlike traditional methods, where the materials are often single-use, gas assist techniques can recycle and reuse gases like nitrogen, further reducing waste. This aspect is crucial for companies aiming to minimize their ecological impact by adopting sustainable production methods5.
Broader Environmental Impacts
Beyond immediate manufacturing benefits, gas assist injection molding contributes to broader environmental goals. By reducing material waste and energy consumption, the technology aligns with initiatives aimed at lowering industrial carbon footprints. Moreover, it supports the creation of lighter products that require less fuel for transportation, thus contributing to reduced emissions during product distribution.
Challenges and Considerations
While gas assist injection molding offers numerous environmental benefits, certain challenges persist. For example, the initial investment in specialized equipment and training can be a barrier for some companies. Additionally, ensuring that gases are efficiently recycled requires careful monitoring and management. Nonetheless, these challenges are outweighed by the long-term environmental advantages and cost savings.
In conclusion, while gas assist injection molding isn’t without its hurdles, its potential to drive more sustainable manufacturing practices is undeniable.
Gas assist molding uses up to 50% less material.True
This method forms hollow structures, reducing raw plastic use by 50%.
Gas assist injection molding increases energy consumption.False
It reduces energy use by shortening cooling cycles, lowering emissions.
Conclusion
In summary, gas assist injection molding is not just about improving product quality; it also reduces costs and promotes sustainability. Embracing this technology could be your key to innovative and efficient manufacturing.
-
Explore detailed mechanics behind minimizing shrinkage and warpage effectively.: The result is a part with less shrinkage and reduced warpage. Part weight can also be reduced by creating hollowed out areas. ↩
-
Explore additional benefits across various manufacturing aspects.: Several advantages of gas assist injection molding include the following: better dimensional quality, improved efficiency, less material, lighter product weight … ↩
-
Learn how this technique speeds up manufacturing by reducing cooling time.: Shorter Cycle Times: By removing thicker core materials, the process reduces cooling times by up to 50%, speeding up production. … can get clogged by molten … ↩
-
Learn how gas assist reduces energy use in manufacturing processes.: The use of an all-electric injection molding machine and hybrid injection molding machine, with excellent energy-saving effect, can save 20-80%. ↩
-
Explore how recycling gases enhances sustainability in production.: Gas assist injection molding is a low-pressure injection molding technique. It fills an injection mold under pressure, first with plastic and then a gas ( … ↩