Finding the right balance between hardness and toughness in mold steel is both a technical challenge and an art form. Your creations probably last if you achieve this balance.
Achieving the perfect balance in mold steel involves selecting high-quality alloys, optimizing heat treatment processes, and applying effective machining and surface treatments to enhance both hardness and toughness.
I remember my first time facing this dilemma. It felt like choosing between a rock and a hard place. The right mold steel depends a lot on the task. Molds that face constant high-impact battles, like die-casting, need special steel. H13 steel, with its strong toughness and thermal fatigue resistance, is my favorite. On the other hand, molds that deal with intense pressure and friction require different steel. D2 steel is really good for its hardness. Picking the steel is just the beginning. Treating it well is really important.
Heat treatment is like baking a cake. Get the temperature wrong and you lose everything. I learned this the hard way. Quenching too quickly can be a disaster. Now, I use graded quenching to fix this. It helps me get the right hardness and keep the toughness. Tempering is very important too. It stabilizes the steel.
Machining and surface treatment are like adding the final touches to art. Proper forging ratios maintain uniformity in the steel. Nitriding strengthens the surface without harming the inside. These methods turn basic mold steel into a champion of durability and reliability.
Heat treatment is crucial for mold steel toughness.True
Heat treatment optimizes the microstructure, enhancing toughness and durability.
Surface treatments reduce mold steel hardness.False
Surface treatments often increase hardness by creating a wear-resistant layer.
Why Do Alloying Elements Matter in Mold Steel?
Have you ever thought about why mold steel is so tough? The secret lies in the magic of alloying elements.
Alloying elements, such as chromium and molybdenum, are the secret ingredients in mold steel. They increase hardness, wear resistance and toughness. These elements change the steel’s microstructure. Mold steel becomes very strong and durable. It can handle different operational challenges.
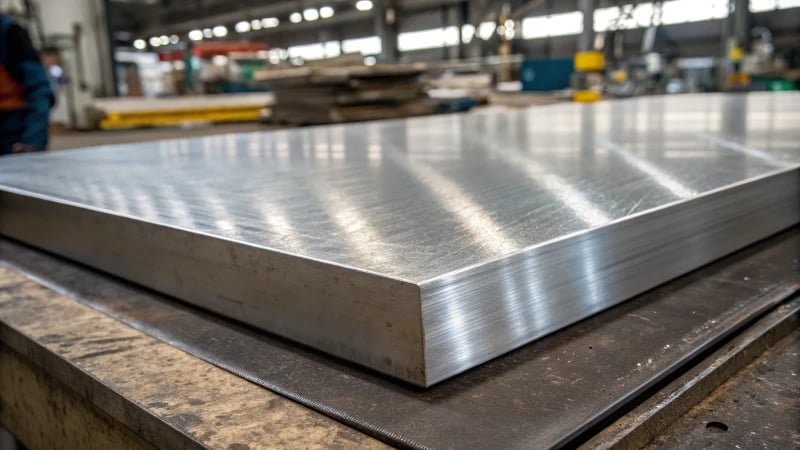
Diving Into Alloying Elements in Mold Steel
I recall when I first started learning about mold steels. The mix of elements seemed like a secret recipe. Each ingredient was vital to the final outcome. These elements are added to steel compositions1 to change its strength and other qualities. I learned this is key for good performance.
-
Chromium (Cr):
Chromium acts like the backbone for increasing hardness and resistance to wear. It keeps steels like H13 strong without becoming brittle. Many designers often say chromium helps create stable carbides. -
Molybdenum (Mo):
Molybdenum is an unsung hero that provides thermal stability. It offers extra protection when the heat rises. -
Carbon (C):
Carbon brings hardness, though too much may reduce toughness. It’s like adding the right amount of spice – overdoing it might disturb the balance.
Comparing Alloying Effects in Different Steels
Now, let’s look at H13 and D2 steels. This comparison shows how these elements shape different steels:
Element | H13 Steel | D2 Steel |
---|---|---|
Chromium | 4-5% | 11-13% |
Molybdenum | 1-1.5% | Minimal |
Carbon | Moderate | High |
The table above showcases how varying element compositions in different steels cater to distinct operational needs. For instance, D2, with higher chromium levels, suits cold work tasks by focusing on wear resistance.
Real-World Applications and Considerations
Every time I pick mold steel, the specific job guides my choice:
-
High Impact Loads:
For molds facing frequent impact, like die-casting molds, H13 is my favorite. It tolerates high heat without deforming due to its optimized chromium and molybdenum content. -
High Friction Environments:
In contrast, D2’s high carbon content suits high-pressure tasks where wear resistance is essential. Yet, it’s crucial to balance hardness with toughness through heat treatment.
By focusing on alloying elements2, we can adjust steel’s characteristics to fulfill specific needs. This adjustment increases durability and efficiency in production, selecting materials strategically crafts strong solutions for challenging conditions.
Chromium increases mold steel's corrosion resistance.True
Chromium forms stable carbides, enhancing hardness and corrosion resistance.
High carbon always increases mold steel's toughness.False
High carbon increases hardness but can reduce toughness if not balanced.
How Does Heat Treatment Affect Mold Steel Properties?
Have you ever thought about how heat treatment turns mold steel into a fantastic material for production?
Heat treatment completely changes mold steel properties by changing its microstructure. Techniques such as quenching and tempering adjust the steel’s hardness. These processes improve toughness and wear resistance. The steel becomes perfect for many mold applications.
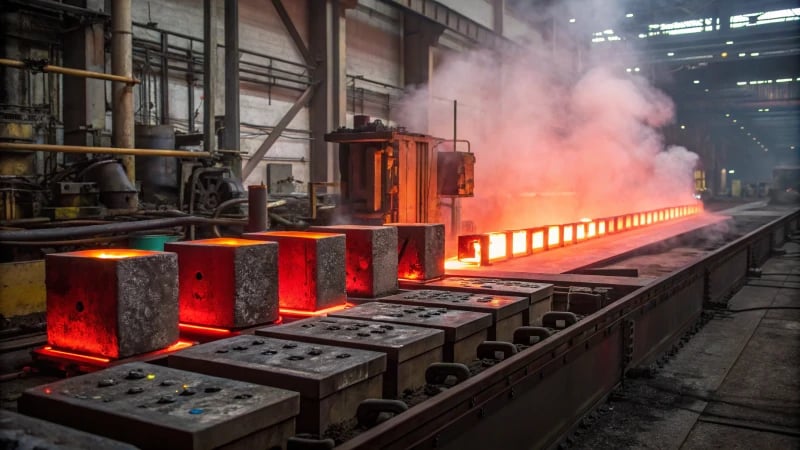
The Role of Quenching in Mold Steel
Quenching is like discovering a secret way to transform plain steel into something special. It involves heating steel to a really high temperature and then cooling it rapidly, forming a hard structure called martensite. For instance, Cr12MoV steel serves as an example; quenching it from 1020 – 1050°C creates a perfect mix of hardness and toughness. I remember a project where this method gave us the durability we needed for a high-pressure mold.
Tempering for Toughness
Tempering brings back memories of my first big project dealing with toughness issues in H13 steel. After quenching, tempering was used to remove internal stresses and increase toughness. H13 steel usually gets tempered between 550 – 650°C. Using tempering multiple times makes its structure steady.
Steel Type | Tempering Temp (°C) | Cycles |
---|---|---|
H13 | 550 – 650 | 3 |
In one project, we tempered the steel three times to achieve the right balance of hardness and toughness.
Influence of Surface Treatments
Surface treatments significantly change how long molds last. I recall applying nitriding to a mold facing tough conditions. Nitriding involves a gas process at 500 – 550°C, creating a hard layer on the surface without altering the core properties. This step increases durability while preserving internal toughness.
- Nitriding Process: Gas nitriding forms a high-hardness layer on the surface without impacting core properties, ensuring longer mold life.
- Temperature Range: Performed typically at 500 – 550°C.
These treatments ensure molds can withstand demanding conditions without compromising integrity.
Selecting the Right Mold Steel
Choosing the correct steel feels like carefully matching partners; you must truly understand the mold’s needs:
- High Impact Loads: For die-casting molds requiring excellent toughness, I often select H13 steel.
- High Pressure and Friction: D2 steel works great under these conditions due to its high carbon content enhancing hardness.
Explore mold steel selection3 considering alloying elements such as chromium and molybdenum. Chromium provides hardness and wear resistance, while molybdenum improves thermal stability and toughness.
Quenching forms a martensitic structure in mold steel.True
Quenching rapidly cools heated steel, creating a hard martensitic structure.
Nitriding decreases the surface hardness of mold steel.False
Nitriding increases surface hardness by forming a hard layer on the steel.
Why Is Surface Treatment Crucial for Mold Longevity?
I remember the first time I discovered surface treatment. It totally transformed how long molds last!
Surface treatment is very important for making mold last longer by improving surface hardness and reducing wear. Techniques like nitriding create a tough outer layer that really increases durability. This hard layer does not reduce the mold’s inner toughness. Such strength is essential for molds under high stress.
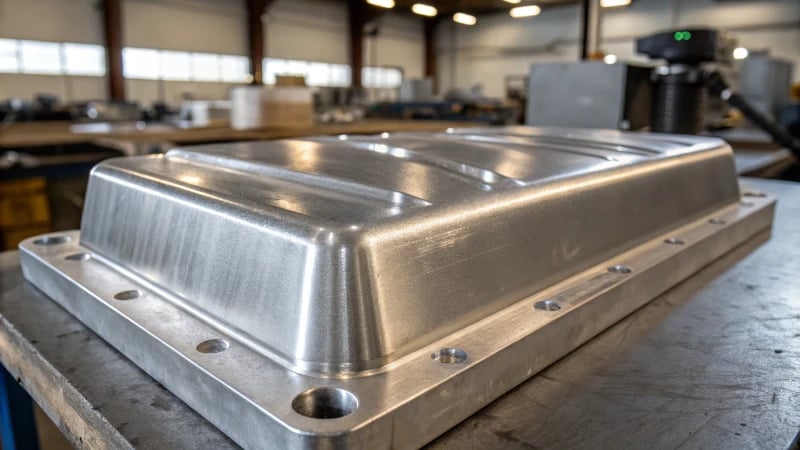
Understanding the Role of Surface Treatment
I have worked for many years in the mold industry. I know that surface treatment is very important for molds to survive longer. It is not only about keeping them longer but also making them work well under pressure. Treatments are really effective. They protect against wear, corrosion, and heat stress.
Surface treatment techniques play a critical role in prolonging the lifespan of molds by enhancing their durability and efficiency4. These treatments provide a protective layer that increases the mold’s resistance to wear, corrosion, and thermal stress.
Types of Surface Treatments
-
Nitriding: The first time I watched nitriding, I found it fascinating. This process adds nitrogen to the mold steel’s surface. It creates a very hard layer while keeping the core strong. It is like giving the mold strong armor. It is perfect for tough environments like die-casting.
This process involves diffusing nitrogen into the surface of the mold steel to form a hard nitrided layer. It enhances surface hardness, typically achieving values up to HV1000, without affecting the core toughness.
-
Coatings: Advanced coatings, such as PVD or CVD, put down a thin but powerful layer. This really increases wear resistance and reduces friction. These coatings help molds last much longer by protecting against abrasive materials.
Advanced coatings like PVD (Physical Vapor Deposition) or CVD (Chemical Vapor Deposition) add a thin, hard layer that improves wear resistance and reduces friction5.
-
Polishing: Polishing is very important but sometimes people forget it. I once skipped this step and got a mold full of tiny defects. A smooth finish helps parts exit easily and reduces defects.
While often overlooked, polishing is essential for removing micro-defects on the mold surface that could lead to stress concentrations.
Benefits of Surface Treatment
-
Increased Surface Hardness: Techniques such as nitriding really increase surface hardness without losing the core’s strength. This balance is crucial when molds face constant stress.
-
Improved Wear Resistance: By lowering friction and stopping material movement during molding operations, surface treatments create fewer defects and give better finishes.
-
Corrosion Protection: Protective coatings fight corrosive elements, prolonging their usability in harsh manufacturing environments.
Treatment | Benefits | Suitable For |
---|---|---|
Nitriding | Enhances hardness without losing toughness | High-stress molds |
Coatings | Improves wear resistance, reduces friction | Abrasive material applications |
Polishing | Removes micro-defects, ensures smooth finish | High-quality part production |
Selection of Mold Steel Materials
The choice of mold steel affects how well surface treatments work. For example:
- H13 steel’s toughness and thermal stability make it suitable for high-temperature applications6.
- D2 steel’s hardness makes it perfect for situations with high friction.
Understanding these details helps in choosing the best treatment methods.
Choosing steel materials wisely and using surface treatment smartly help molds stay strong over time—less downtime and fewer repairs save costs—improving production efficiency significantly.
Nitriding increases mold surface hardness to HV1000.True
Nitriding enhances surface hardness to HV1000 without affecting toughness.
Polishing is unnecessary for high-quality part production.False
Polishing removes micro-defects, ensuring smooth finishes and quality parts.
How Can Machining Processes Boost Mold Steel Durability?
Ever thought about how to help your mold steel survive longer and work better? Dive into the world of machining techniques that achieve exactly this!
Improving mold steel durability involves using smart machining techniques. Forging and rolling probably change the steel’s internal structure for the better. Surface treatments like nitriding increase hardness on the surface. This happens without losing toughness.
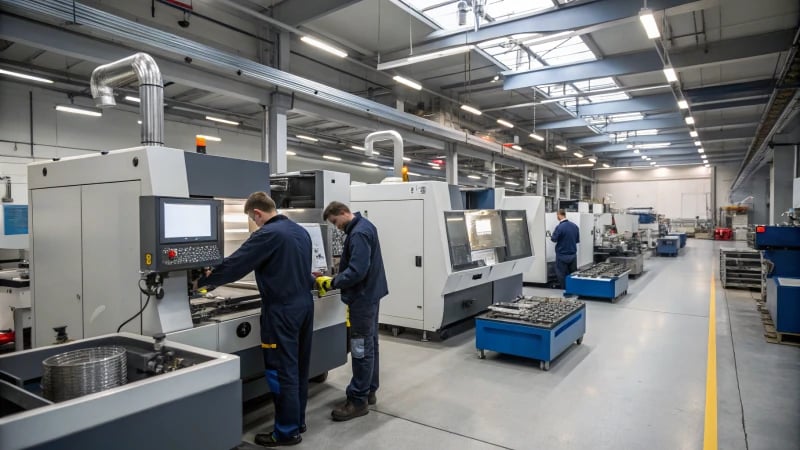
The Role of Forging and Rolling
I was really surprised when I first worked with mold steel. The right machining processes transformed everything. Forging and rolling do more than just shape metal; they strengthen it. These methods refine the inside of the metal, breaking down coarse carbides and carefully adjusting the grain structure to boost toughness.
For instance, we adjusted the forging ratio7 to between 3 and 5. It was like magic happened—the steel’s internal structure became more uniform. This uniformity created an excellent base for future heat treatments and long-lasting use. Precise cutting parameters controlled machining stress, pretty much guaranteeing that the steel stayed strong under pressure.
Influence of Surface Treatments
Surface treatments amazed me when I started in the field; they were another discovery. Methods like nitriding significantly increase the surface hardness of your mold while keeping the mold’s core strong. During gas nitriding, we heated the steel to 500-550°C, allowing nitrogen atoms to enter the surface and form iron nitride compounds. The result? Incredible increases in surface hardness to around HV1000 without losing toughness.
This method balances a hard exterior with a tough core, extending mold life considerably—an important factor for our production schedules.
Key Considerations in Machining Processes
Choosing the right materials and processes really matters depending on the mold’s working conditions. For example, in die-casting molds that face high-impact loads, using H13 steel is helpful due to its toughness and resistance to thermal fatigue.
Conversely, for cold work molds under high pressure and friction, D2 steel shines with its high-carbon, high-chromium composition providing excellent hardness and remarkable wear resistance. However, correct heat treatments are essential for reaching optimal performance.
Process | Impact on Durability |
---|---|
Forging | Refines grains, improves toughness |
Rolling | Enhances uniformity, reduces defects |
Nitriding | Increases surface hardness |
Quenching | Balances hardness and toughness |
Incorporating these machining processes isn’t just about extending lifespan; it is about achieving performance and cost-efficiency in manufacturing operations. Learn more about advanced techniques8 that can probably revolutionize your projects.
Forging refines grains in mold steel.True
Forging breaks coarse carbides and refines grains, enhancing toughness.
Nitriding reduces mold steel's core toughness.False
Nitriding increases surface hardness without affecting core toughness.
Conclusion
Achieving the perfect balance of hardness and toughness in mold steel involves selecting appropriate materials, optimizing heat treatment, and applying effective machining and surface treatments for durability.
-
Explore how alloying elements are incorporated into steel to improve mechanical properties such as strength and resistance. ↩
-
Discover how specific alloying elements enhance mold steel’s performance in various industrial applications. ↩
-
Discover how alloying elements like chromium and molybdenum influence steel’s mechanical properties. ↩
-
Explore how surface treatments enhance mold performance by reducing wear and increasing durability. ↩
-
Learn about various coating techniques that improve wear resistance and reduce friction in molds. ↩
-
Discover why H13 steel is preferred for high-temperature and high-impact molding applications. ↩
-
Understanding forging ratios helps in selecting appropriate metalworking techniques for improving material properties. ↩
-
Explore innovative machining methods that offer new ways to enhance mold durability. ↩