Ever wondered what makes Bakelite so unique in the world of plastics?
Bakelite injection molding differs from other plastic molding by its unique screw configuration and higher mold temperatures (150-180°C). It uses a 1:1 screw compression ratio, unlike the 1:3-1:4.5 ratios in thermoplastics, as Bakelite fuses particles rather than melting.
I remember the first time I worked with Bakelite, I was fascinated by how it didn’t melt like other plastics. Instead, the particles seemed to magically come together under heat—a bit like watching a cake rise in the oven! This process is quite different from typical thermoplastics where melting is key. Understanding these differences not only helped me optimize my designs but also improved the production efficiency in our factory. The unique 1:1 screw compression ratio required for Bakelite molding was initially a challenge, but with a little patience and a lot of trial and error, it all started to make sense. If you’re in product design or manufacturing, delving into these nuances will open up new avenues for creating innovative solutions.
Bakelite requires a 1:1 screw compression ratio.True
Bakelite uses a 1:1 screw compression ratio due to its unique properties.
Thermoplastics melt at higher temperatures than Bakelite.False
Thermoplastics melt at lower temperatures compared to Bakelite's fusing range.
What Makes Bakelite So Unique?
Ever held a piece of Bakelite and wondered what makes it so special? This early synthetic plastic revolutionized industries with its unique properties.
Bakelite is unique due to its thermal stability, electrical non-conductivity, and high compression strength. Unlike thermoplastics, it fuses rather than melts, enhancing its durability for industrial use.
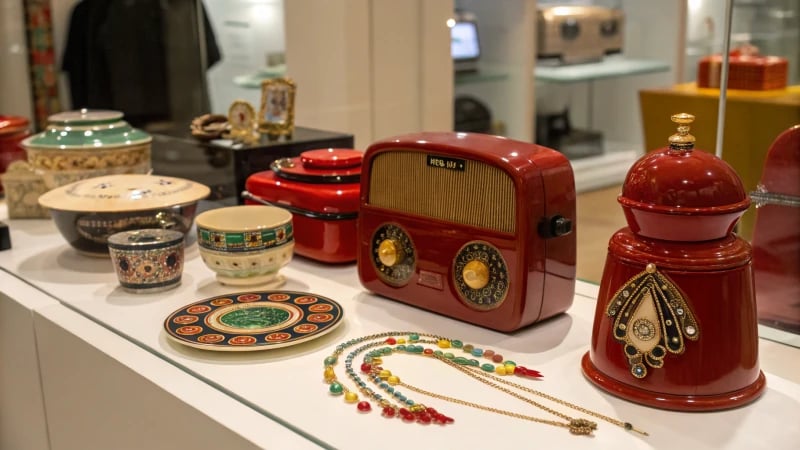
Thermal Stability and Molding Process
Let me take you back to a time when I was first introduced to Bakelite. I was a budding designer, fresh out of college, and working on a project that involved vintage radios. These radios were encased in Bakelite, which was fascinating due to its ability to withstand high temperatures without losing form. Unlike thermoplastics1, which need to melt for molding, Bakelite goes through a fusing process. This quirky characteristic means it can endure heat up to 180°C, making it ideal for components like electrical insulators and automotive parts.
Material Type | Molding Temperature |
---|---|
Thermoplastics | 60-100°C |
Bakelite | 150-180°C |
Electrical Non-conductivity
I remember when I first realized the importance of Bakelite’s electrical non-conductivity. It was during a brainstorming session on designing safer home appliances. We needed a material that could prevent electrical hazards, and Bakelite emerged as the hero. Its insulating properties make it perfect for switches and sockets, ensuring the safety and reliability that are paramount in the electronics industry2.
Compression Strength and Screw Configuration
When discussing Bakelite’s mechanical strengths, I can’t help but recall a conversation with a fellow engineer about its compression strength. Bakelite’s screw configuration gives it a compression ratio of 1:1, much lower than the 1:3 or more typical of thermoplastics. This attribute enhances its structural integrity and resilience, making it suitable for heavy-duty applications.
Versatility in Applications
Reflecting on Bakelite’s versatile nature, I recall a time when we were tasked with designing durable kitchenware. Bakelite’s ability to maintain its structure under heat made it an obvious choice. Whether in consumer electronics3 or kitchenware, its unique properties continue to prove invaluable.
Bakelite’s blend of thermal stability, electrical non-conductivity, and strong compression resistance sets it apart in numerous industries. From its historical applications to modern uses, Bakelite remains unmatched by other materials. This journey into Bakelite’s world has not only enriched my professional life but also deepened my appreciation for materials science.
Bakelite can withstand temperatures up to 180°C.True
Bakelite's thermal stability allows it to withstand high temperatures, ideal for insulators.
Bakelite has a higher compression ratio than thermoplastics.False
Bakelite has a lower compression ratio (1:1) compared to thermoplastics (1:3 or higher).
Why is Screw Configuration Crucial in Molding?
Ever wonder why some molded products turn out perfect while others miss the mark? It might just come down to the unsung hero of molding: screw configuration. Let’s dive into how this hidden factor makes a world of difference.
Screw configuration in molding is vital as it influences material melting, mixing, and uniformity. Proper configurations account for compression ratios, temperature settings, and material types, ensuring optimal results.
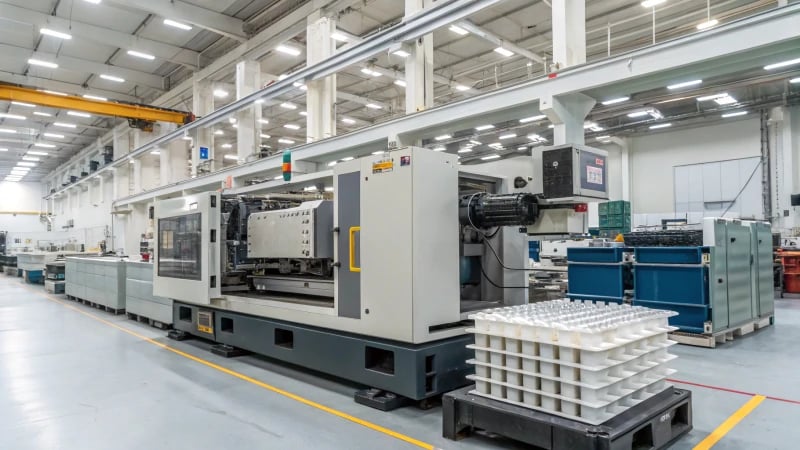
Compression Ratios and Material Specifics
I’ve always been fascinated by how a tiny change can have such a big impact, much like adjusting the compression ratio4 in screw configurations for different materials. It’s like fine-tuning a guitar string to get that perfect pitch. For instance, Bakelite typically requires a 1:1 compression ratio because it needs just enough pressure to fuse without melting. On the other hand, thermoplastics, which need to melt for molding, demand a more varied ratio between 1:3 and 1:4.5. These differences aren’t just numbers—they’re reflections of the unique personalities of each material.
Process Variations in Molding
Imagine baking cookies. With thermoplastics, it’s like getting the dough to melt into the mold just right before it hardens, akin to letting cookie dough spread and set. But with Bakelite, it’s more about coaxing the particles to bond without changing their fundamental nature—like gently pressing cookie crumbs together to form a crust.
Material | Process |
---|---|
Thermoplastics | Melting |
Bakelite | Fusing |
This distinct approach in screw design ensures that both materials achieve their best possible form.
Temperature Control and Its Effects
Temperature has always been the silent conductor in the symphony of molding processes. For thermoplastics, I think of it like managing a delicate simmer—barrel temperatures around 180°C and molds between 60-100°C ensure everything melts smoothly. But for thermosets like Bakelite, you need a more intense heat—150-180°C—to coax those particles into a perfect embrace. The right screw configuration is your baton, orchestrating this precise control over heat, ensuring every note of your final product is pitch-perfect.
The Role of CAD in Screw Design
As someone deeply embedded in the world of design, I can’t overstate the importance of tools like CAD software. They are my canvas and brush, allowing me to visualize and sculpt screw designs that cater to specific molding needs. For someone like Jacky, who juggles aesthetic and functional demands daily, CAD is indispensable. It offers a detailed playground for analysis and modification, ensuring that every screw configuration is not just suitable but exceptional.
Understanding screw configuration tailored to material properties isn’t just about enhancing efficiency—it’s about crafting quality at every turn of the screw. For those of us in manufacturing, keeping abreast of these technical details isn’t just useful; it’s essential for making informed decisions that fuel success in our industry.
By considering these factors, we can better navigate the complex landscape of molding processes and achieve outcomes that resonate with modern production standards and demands.
For more insights on the nuances of screw configurations in injection molding, check out our detailed guide on screw design considerations5.
Bakelite requires melting in the molding process.False
Bakelite undergoes fusing, not melting, during molding.
Thermoplastics have a higher compression ratio than Bakelite.True
Thermoplastics typically have a compression ratio of 1:3 to 1:4.5.
Why Is Temperature Control Crucial in Molding Processes?
Remember that time when your perfectly planned project went sideways because of one small oversight? That’s exactly what happens in molding without proper temperature control.
Temperature control in molding is crucial to ensure materials flow smoothly, solidify properly, and bond effectively, preventing defects and maintaining product quality and structural integrity.
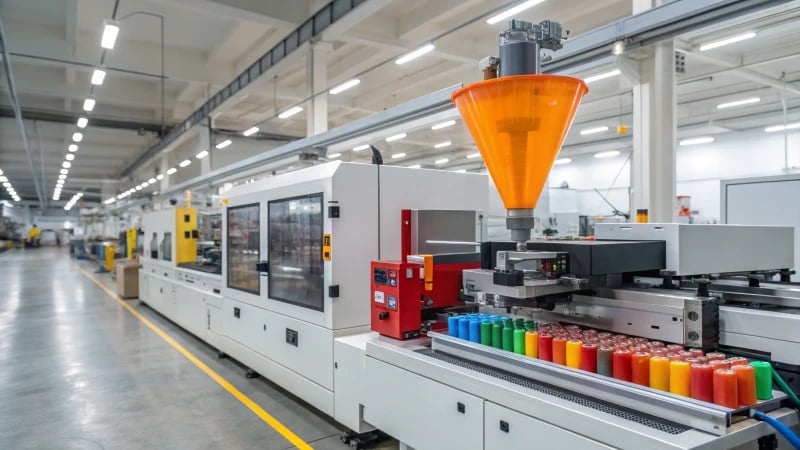
Understanding Material Behavior
Temperature plays a starring role in how materials behave during the molding process6. It’s like baking a cake; you can’t just wing it with any oven temperature. Imagine working with thermoplastics. You need the mold to be between 60-100°C and the barrel at around 180°C to get that perfect melt and shape. Think of thermosets as your no-bake cookies—they don’t melt but need a consistent mold temperature of 150-180°C to fuse correctly.
Here’s a quick comparison:
Material Type | Mold Temperature (°C) | Barrel Temperature (°C) |
---|---|---|
Thermoplastics | 60-100 | 180 |
Thermosets | 150-180 | N/A |
Importance of Consistent Temperature Control
It’s like making sure your soup doesn’t boil over or get cold too soon—consistency is key. Inconsistent temperatures in molding can cause issues like warping or weak bonding, which can be a nightmare if you’re molding thermosets like bakelite. Here, maintaining temperature is non-negotiable because it relies on fusing particles, not melting them.
Screw Configuration and Its Role
Did you know the screw in your molding machine is as crucial as the recipe you’re following? For instance, bakelite demands a 1:1 screw compression ratio, whereas thermoplastics need somewhere between 1:3 and 1:4.5. This setup affects how heat distributes during the process, much like how stirring affects your cooking.
Real-World Implications
Picture this: you’re designing a sleek new gadget housing. You can’t just slap it together and hope for the best. Understanding temperature control can save you from costly production hiccups and ensure your designs don’t just look good but perform well, too. This is especially true if you’re in consumer electronics, where efficiency and reduced waste can make or break your bottom line.
For more on how temperature influences other manufacturing processes, check out additional resources7.
Thermoplastics melt at mold temperatures of 150-180°C.False
Thermoplastics melt at mold temperatures of 60-100°C, not 150-180°C.
A 1:1 screw ratio is used for thermoset molding.True
Bakelite, a thermoset, requires a 1:1 screw compression ratio.
What Are the Common Applications of Bakelite and Thermoplastics?
Ever wondered how everyday items like your toaster or smartphone case come to life? Dive into the world of Bakelite and thermoplastics to uncover their fascinating roles.
Bakelite is used in electrical insulators and kitchenware for its heat resistance. Thermoplastics are ideal for packaging, automotive parts, and electronics due to their moldability and durability.
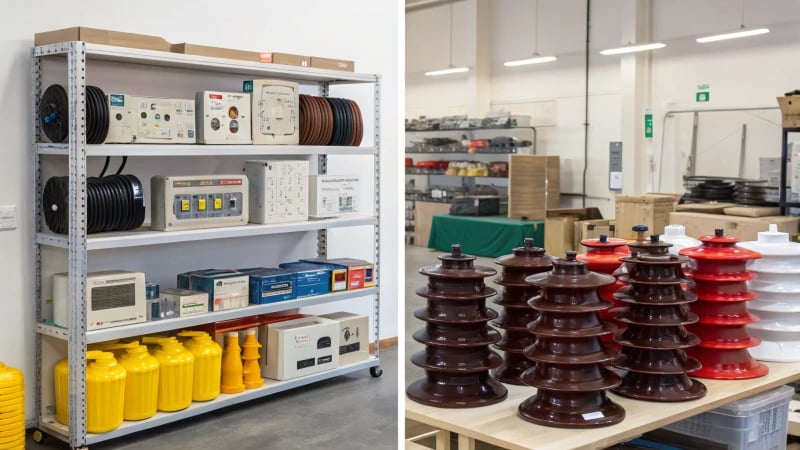
Bakelite Applications
I still remember the first time I learned about Bakelite during a college project. Its heat resistance was a revelation to me, especially when I discovered its role in electrical insulators8. These insulators are unsung heroes, preventing electrical mishaps that could lead to fires or short circuits. It’s Bakelite’s durability and non-conductive nature that make it indispensable here.
Another memory that stands out is rummaging through my grandmother’s kitchen and finding old Bakelite saucepan handles. I was amazed at how this material could withstand high temperatures without degrading, ensuring both safety and longevity in kitchenware. It’s no surprise it extends to radios and telephone casings too, where sound dampening and wear resistance are key.
Thermoplastics Applications
Thermoplastics have always fascinated me with their versatility. Imagine the countless packaging solutions we rely on daily—bottles, containers—all made possible by the moldability of thermoplastics. Their ability to be reshaped under heat allows for the innovation we see in protecting and preserving products.
In the automotive industry, my experience with thermoplastics has been nothing short of transformative. From dashboards to bumpers, these materials allow for lightweight yet durable designs. The precision molding required here is achieved thanks to their excellent compression ratio of 1:3-1:4.5, a crucial factor I always consider in my designs.
And let’s not forget consumer electronics. Thermoplastics offer aesthetic versatility and strength, creating everything from phone cases to laptop components—ensuring they’re lightweight yet robust enough for our everyday use.
Comparing Processing Techniques
The molding processes of Bakelite and thermoplastics couldn’t be more different. Bakelite involves fusing particles without melting, which was quite a concept for me to grasp initially. In contrast, thermoplastics require melting—a process I became well-acquainted with early in my career.
Here’s a comparison:
Material | Molding Process | Temperature Requirement |
---|---|---|
Bakelite | Fusing | 150-180°C |
Thermoplastics | Melting | 60-100°C (mold), 180°C (barrel) |
Understanding these processes is crucial for selecting the right material for specific applications, ensuring product efficacy and safety.
Exploring Future Applications
With technology advancing at breakneck speed, the applications of both materials continue to expand. For instance, I’ve seen thermoplastics revolutionize prototyping and custom designs with 3D printing, opening up new possibilities every day.
Bakelite’s potential remains robust, especially where heat resistance is essential. This opens doors for innovation in both traditional applications and exciting new sectors.
Staying abreast of current trends9 and technological advancements has been pivotal in my work. By leveraging these materials strategically, we can craft future-ready solutions that enhance product quality and efficiency.
Bakelite is used in saucepan handles due to heat resistance.True
Bakelite's ability to withstand high temperatures makes it suitable for kitchenware.
Thermoplastics are unsuitable for automotive components.False
Thermoplastics are used in making lightweight, durable automotive parts.
Conclusion
Bakelite injection molding differs from thermoplastics in screw configuration, process dynamics, and temperature requirements, offering unique advantages in durability and application across various industries.
-
Understand the fundamental differences in how thermoplastics and Bakelite are molded to appreciate their distinct applications. ↩
-
Explore how Bakelite’s electrical insulation properties are utilized in modern electronics. ↩
-
Discover the various applications of Bakelite in consumer electronics and why it’s favored for durability and heat resistance. ↩
-
Understanding compression ratios helps optimize screw design for specific materials. ↩
-
Explore detailed considerations for effective screw configurations. ↩
-
Discover how temperature variations affect different molding processes and their outcomes. ↩
-
Explore broader implications of temperature control across various manufacturing processes. ↩
-
This link provides detailed examples of Bakelite’s use in electrical insulators. ↩
-
Explore emerging trends and future possibilities for Bakelite and thermoplastics applications. ↩