Bakelite’s legacy in the world of materials is legendary, thanks to its robustness and insulating prowess.
Bakelite is suitable for injection molding with precise temperature control, pressure, and curing time due to its thermosetting properties, unlike thermoplastics.
While Bakelite’s injection molding process is more complex compared to typical thermoplastics, understanding the nuances can unlock its potential for various applications. I remember the first time I dealt with Bakelite—it felt like taming a wild horse. With its unique demands for temperature, pressure, and curing time, each step felt like orchestrating a delicate dance. But once you get it right, the results are incredibly rewarding. Let’s dive deeper into what makes Bakelite molding both challenging and rewarding.
Bakelite requires specialized handling in injection molding.True
Bakelite's thermosetting nature demands precise temperature and pressure control.
Bakelite is a type of thermoplastic material.False
Bakelite is a thermosetting plastic, not a thermoplastic.
- 1. What Makes Bakelite Unique in Injection Molding?
- 2. How Does Bakelite’s Thermosetting Nature Affect Molding?
- 3. What Are the Key Process Requirements for Bakelite Injection Molding?
- 4. What are the unique mold design considerations for Bakelite?
- 5. How Does Bakelite Compare to Other Materials in Injection Molding?
- 6. Conclusion
What Makes Bakelite Unique in Injection Molding?
Ever wondered how a century-old material like Bakelite still holds its ground in modern manufacturing?
Bakelite is unique in injection molding due to its thermosetting nature, offering superior heat resistance and durability through precise temperature, pressure, and curing control.
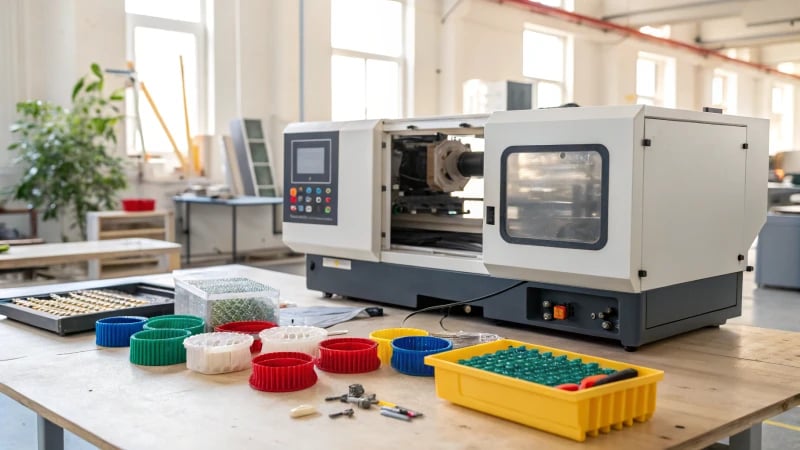
The Thermosetting Advantage
Let me tell you, Bakelite’s been around the block and back—it was the first synthetic plastic to hit the scene! What really sets it apart in the world of injection molding is its thermosetting property. I remember when I first learned about this; it’s fascinating how Bakelite becomes permanently hard when cured. This quality makes it superbly heat-resistant and sturdy, offering superior durability1 compared to those thermoplastics that can be melted down and reshaped like a candy bar left in a hot car.
Process Requirements
Temperature Control
When I first started working with Bakelite, temperature control seemed like walking a tightrope. You’ve got to get it just right. Initially, you heat the resin to 70-100°C so it flows into the mold. Then, you crank up the temperature to 150-180°C to kick off the cross-linking reaction. It’s like baking a cake—get the oven temp wrong, and you’re left with a mess instead of a masterpiece.
Pressure and Curing Time
Pressure’s another biggie here. Imagine trying to fill every nook and cranny with thick syrup. That’s what it’s like ensuring Bakelite fills the mold cavity completely. Proper pressure is crucial to avoid any voids. And then there’s the waiting game—allowing for adequate curing time ranging from a few minutes to much longer depending on the thickness of the part.
Mold Considerations
Mold Aspect | Requirements |
---|---|
Heat Transfer | Efficient heat transfer to ensure even curing. |
Ventilation | Proper ventilation to release volatile by-products and prevent defects. |
I can’t stress enough how important mold design is when working with Bakelite. The molds have to handle high temperatures while also being efficient at heat transfer. And don’t forget about ventilation! Letting those gases escape during curing is key, or you’ll end up with defects.
Why Choose Bakelite?
Why go through all this hassle for Bakelite? Because it’s worth it! Its ability to withstand high heat and remain dimensionally stable makes it a top choice for things like electrical insulators and automotive parts—where performance under pressure is non-negotiable, requiring high heat resistance2. Sure, it’s more complex than using thermoplastics, but when you need something that won’t buckle under stress, Bakelite’s your go-to.
Exploring modern uses of Bakelite makes me appreciate its resilience even more. It supports industries needing materials that can handle tough conditions without losing their integrity or performance.
Bakelite can be remelted like thermoplastics.False
Bakelite is a thermosetting plastic, becoming irreversibly hard upon curing.
Bakelite requires high temperature for cross-linking.True
Post-injection, Bakelite's temperature is raised to 150-180°C for curing.
How Does Bakelite’s Thermosetting Nature Affect Molding?
Ever wondered how Bakelite’s unique properties revolutionize the molding process?
Bakelite’s thermosetting nature requires precise temperature and pressure control during molding, as it hardens permanently when heated, ensuring quality and durability.
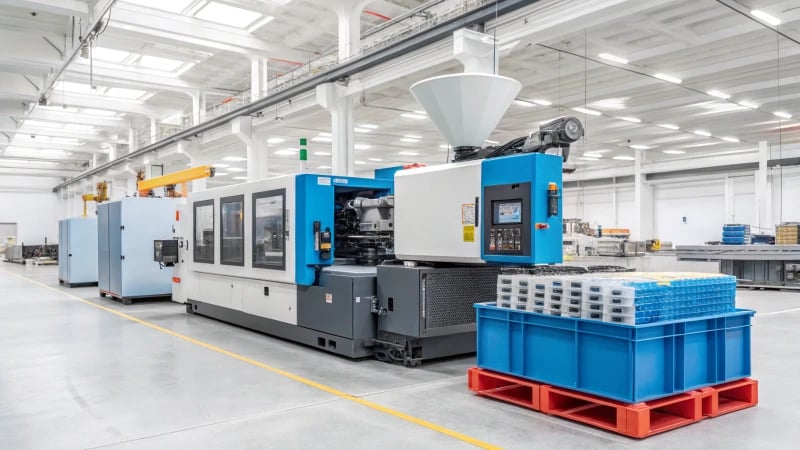
The Science Behind Thermosetting Plastics
Have you ever marveled at how your grandmother’s old Bakelite radio still looks so pristine? That’s the magic of thermosetting plastics! Unlike thermoplastics3, which can be reshaped multiple times, Bakelite undergoes a transformation that makes it set in its shape forever once it’s heated. This transformation, or curing, is like a caterpillar turning into a butterfly; there’s no going back to the original state.
Process Requirements for Bakelite Molding
-
Temperature Control: I remember my first encounter with Bakelite molding—quite the trial by fire! The precision needed in temperature control was a lesson in patience and precision. During the injection phase, the resin must be heated to 70-100°C, just enough to coax it into the mold. But then, like baking the perfect soufflé, you have to hit that sweet spot of 150-180°C to ensure the cross-linking reaction happens seamlessly.
-
Pressure Requirements: Imagine squeezing a tube of toothpaste evenly into a tiny mold—except this isn’t minty fresh gel; it’s a viscous resin that demands consistency and finesse to prevent voids.
-
Curing Time: Curing can take minutes to tens of minutes, depending on part thickness. This time is vital for achieving Bakelite’s desired mechanical and chemical properties.
Mold Considerations
Aspect | Requirement |
---|---|
Heat Transfer | Efficient heat-transfer capabilities in molds |
Ventilation | Proper ventilation to release volatile by-products |
Creating molds for Bakelite is like designing the perfect pie crust—it has to conduct heat evenly to ensure consistent curing. And don’t forget ventilation! Without it, those pesky gases released during curing could ruin the whole batch, leaving voids and imperfections.
Challenges and Solutions
Working with Bakelite can feel like navigating a maze of complexities. I recall one project where maintaining precise temperature control4 and pressure seemed impossible until we revamped our mold design. Innovations in material selection and design helped us overcome these hurdles, ensuring top-notch quality.
Understanding these intricate details transforms challenges into opportunities for excellence. With each project, I learn more about optimizing processes to create products that aren’t just functional but also stand the test of time—a true testament to the legacy of Bakelite in industries like electronics and automotive manufacturing.
Bakelite melts upon reheating.False
Bakelite is a thermosetting plastic that does not melt when reheated.
Curing Bakelite requires temperatures of 150-180°C.True
The curing process for Bakelite needs this temperature range for cross-linking.
What Are the Key Process Requirements for Bakelite Injection Molding?
Imagine crafting something so intricate that even a slight temperature shift could change the outcome. That’s Bakelite injection molding for you!
Bakelite injection molding requires precise temperature control, adequate pressure, specific curing times, efficient heat transfer, and proper mold ventilation to ensure high-quality results.
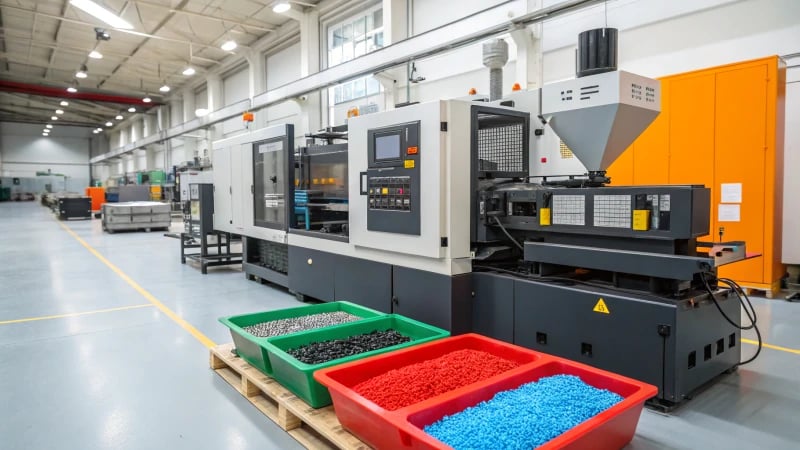
Temperature Control in Bakelite Molding
When I first started dabbling with Bakelite5, the whole temperature thing seemed almost like trying to crack a secret code. You see, to get Bakelite to behave just right, you’ve got to treat it like a diva – keep it warm enough at 70 – 100°C so it flows smoothly into the mold, but then crank up the heat to around 150 – 180°C to let it cross-link and strut its stuff.
Process Step | Temperature Range (°C) |
---|---|
Injection Phase | 70 – 100 |
Curing Phase | 150 – 180 |
Pressure Requirements
I remember the first time I dealt with Bakelite’s pressure needs. It was like coaxing toothpaste out of a stubborn tube—frustrating yet necessary. Adequate pressure ensures that this viscous material fills every nook and cranny of the mold, eliminating voids and ensuring a perfect finish. It’s like baking a cake – too little pressure, and your cake collapses; too much, and it’s a mess.
Curing Time Considerations
Curing is where the magic truly happens. I once compared it to making pottery in a kiln – you can’t rush it. Depending on the thickness of your part, this can take anywhere from a few minutes to an hour. It’s during this time that Bakelite gains its final properties, becoming the sturdy material we all love.
Mold Considerations
Heat Transfer Efficiency
Heat transfer is the unsung hero in this whole process. Without efficient heat distribution, you’d end up with a product that’s half-baked, quite literally! The mold needs to be made of materials that not only withstand high temperatures but also distribute heat evenly to avoid any weak spots.
Ventilation Requirements
And let’s not forget ventilation. I’ve had my fair share of surprises with trapped gases—think of it like trying to bake bread without punching down the dough first. Proper mold ventilation ensures these gases have an escape route, preventing voids or imperfections. Ensuring proper ventilation6 can make all the difference in achieving that flawless finish.
Bakelite resin is injected at 150 - 180°C.False
Bakelite resin is injected at 70 - 100°C, not 150 - 180°C.
Efficient heat transfer in molds ensures even curing.True
Efficient heat transfer allows for consistent thermal distribution during curing.
What are the unique mold design considerations for Bakelite?
I remember the first time I worked with Bakelite—its quirks and challenges were a revelation. Let me walk you through what makes this material unique in mold design.
Bakelite mold design requires precise temperature control, efficient heat dispersion, and proper ventilation to ensure correct curing and minimize flaws due to its thermosetting properties.
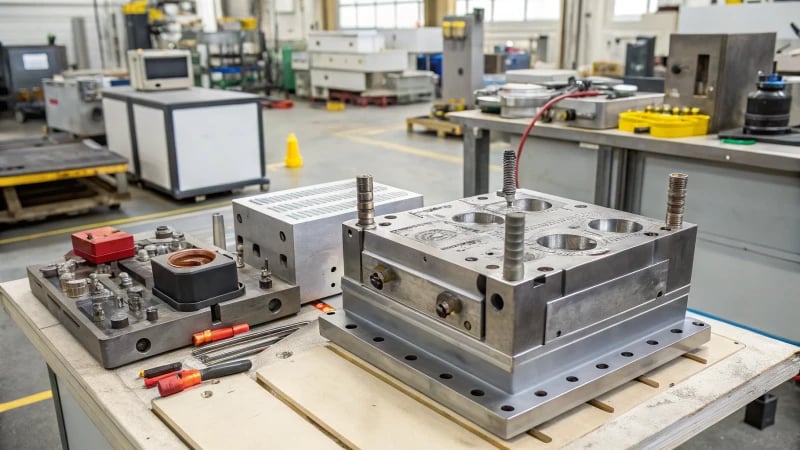
Understanding Thermosetting Molding
Bakelite is unlike any other material I’ve worked with. Being a thermosetting polymer, it permanently hardens when heated, offering no second chances like thermoplastics that can be re-melted. The first time I encountered this, it felt like a ‘one-shot’ deal, where everything needed to be just right. As mold designers, we have to be incredibly precise with temperature control7 because even the slightest deviation can lead to incomplete curing or defects.
Key Process Requirements
Temperature Control: When working with Bakelite, you start by heating it to about 70-100°C to make sure it flows into every nook and cranny of the mold. But that’s just the beginning. After injection, the curing temperature needs to be bumped up to 150-180°C to set off the cross-linking reaction. It’s like baking a cake—too hot or too cold, and you’ll ruin it.
Pressure Considerations: The first time I tried molding Bakelite, I underestimated how much pressure was needed. Adequate pressure is crucial because it ensures the viscous material fills the mold without leaving voids, achieving those fine details that make all the difference.
Curing Time: Unlike thermoplastics, which can be fast-tracked, Bakelite demands patience. Curing time can range from a few minutes to tens of minutes depending on factors like part thickness. This is something you absolutely have to factor into your production schedule.
Mold Design Considerations
Aspect | Consideration |
---|---|
Heat Transfer | Molds should use materials with good thermal conductivity for uniform curing. |
Ventilation | Proper ventilation allows volatile by-products to escape, reducing defects. |
Material Selection for Molds
Selecting the right materials is another puzzle piece. You need something that can stand up to high curing temperatures and facilitate efficient heat transfer. Steel or aluminum are my go-to choices because of their durability and excellent thermal properties.
The Role of Ventilation
Bakelite releases gases during curing—something I learned the hard way during one of my initial projects. Without proper gas escape channels, you’re at risk for voids or blemishes in your final product. Strategic vent placement is critical here.
In essence, moving from thermoplastic to Bakelite molding8 is all about understanding these key differences. Every aspect, from temperature control to material selection, contributes to achieving high-quality outcomes.
Bakelite requires a curing temperature of 150-180°C.True
Bakelite needs this range to trigger cross-linking, ensuring its properties.
Thermoplastics can be re-melted unlike Bakelite.True
Thermoplastics soften when heated, while Bakelite permanently hardens.
How Does Bakelite Compare to Other Materials in Injection Molding?
Imagine a world where a single material revolutionized manufacturing—a world where Bakelite paved the way for modern plastics.
Bakelite in injection molding requires precise temperature control and longer curing times, unlike thermoplastics, which have simpler processes and are remoldable.
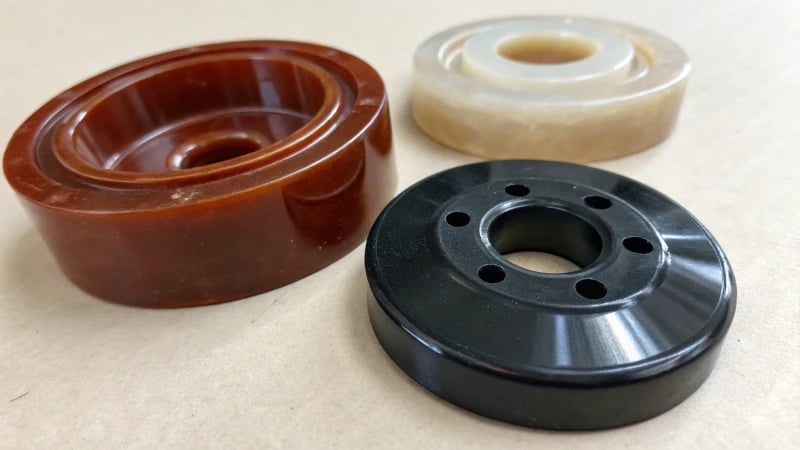
Understanding Bakelite’s Thermosetting Nature
When I first encountered Bakelite, it was like meeting a relic from the past that still had a vibrant story to tell. This thermosetting polymer9 isn’t just any plastic; it undergoes a transformative chemical change during curing, becoming permanently hard and steadfast. Unlike many modern materials that can be reshaped with heat, Bakelite’s commitment is unwavering once it sets.
Process Requirements
Think of working with Bakelite like crafting the perfect soufflé—it demands precision and patience. The temperature must be just right, with the resin initially flowing between 70-100°C, only to cure at a higher range of 150-180°C. Applying enough pressure ensures the resin fills every nook and cranny of the mold, while the curing time, which varies, is critical for achieving its unique characteristics.
Comparing Bakelite to Thermoplastics
Aspect | Bakelite | Thermoplastics (e.g., Polypropylene) |
---|---|---|
Nature | Thermosetting | Thermoplastic |
Curing | Requires heating and curing | Simple melting and cooling |
Reusability | Non-recyclable | Recyclable and remoldable |
Mold Considerations for Bakelite
Designing molds for Bakelite is akin to engineering an intricate puzzle. Efficient heat transfer10 is crucial for uniform curing, and proper ventilation is essential to release gases produced during the process. Without these, you’re left with imperfections that echo with the ghosts of trapped air.
- Heat Transfer: It ensures every part of the mold gets the same attention, crucial for a high-quality end product.
- Ventilation Needs: Just like letting steam escape from a boiling pot, ventilation prevents defects by allowing volatile by-products to escape.
Advantages and Challenges
Bakelite’s high heat resistance and exceptional electrical insulation make it a go-to choice for electrical components, despite its more complex molding process. Handling this material requires skill and specific machinery, but for those who master it, the rewards are immense. It’s like learning to play an old instrument—challenging but incredibly satisfying.
Dive deeper into injection molding processes11 across various materials to discover how each one can shape your next project. Every choice in material carries its own set of stories and outcomes, influencing designs in ways that can be as subtle as they are significant.
Bakelite is a thermoplastic used in injection molding.False
Bakelite is a thermosetting polymer, not a thermoplastic.
Bakelite molds need efficient heat transfer for even curing.True
Efficient heat transfer ensures uniform curing and product quality.
Conclusion
Bakelite is suitable for injection molding, requiring precise temperature control, adequate pressure, and specific curing times due to its thermosetting nature, making the process more complex than thermoplastics.
-
This link will explore the durability of Bakelite compared to thermoplastics, highlighting its superior performance under heat. ↩
-
Discover how Bakelite’s heat-resistant properties make it ideal for demanding industrial applications. ↩
-
Understand the fundamental differences between thermosetting plastics like Bakelite and thermoplastics, aiding in material selection. ↩
-
Learn why precise temperature control is vital in molding processes, especially for thermosetting plastics like Bakelite. ↩
-
Understanding temperature control is crucial for optimizing Bakelite molding processes, ensuring resin flows properly and cures effectively. ↩
-
Proper mold ventilation prevents defects by allowing gases to escape during curing, ensuring higher quality end products. ↩
-
Explore why temperature control is crucial in thermosetting processes to ensure proper curing and material integrity. ↩
-
Learn about the unique challenges and considerations when molding Bakelite compared to typical thermoplastics. ↩
-
Discover why thermosetting polymers like Bakelite are used in high-stress applications, highlighting their unique properties. ↩
-
Learn about the role of efficient heat transfer in achieving uniform curing and high-quality molded products. ↩
-
Gain insights into various injection molding techniques used across industries for diverse materials. ↩