Have you ever wondered how a seemingly small parameter like back pressure can make a world of difference in injection molding?
Back pressure in injection molding refers to the resistance against the screw’s backward movement during the plasticizing stage. It enhances material homogeneity, reduces voids, and controls flow characteristics, ultimately impacting the product’s quality and performance.
But there’s more to back pressure than just its definition. Let’s dive deeper into how it affects various aspects of injection molding, from plastic mixing to void formation.
Back pressure reduces voids in injection molding.True
Back pressure compresses molten plastic, expelling trapped air and minimizing voids.
What Role Does Back Pressure Play in Plastic Mixing?
Back pressure is a pivotal factor in plastic mixing within the injection molding process, influencing material quality and consistency.
Back pressure enhances plastic mixing by applying shear forces, improving homogeneity, density, and reducing defects like voids and air bubbles.
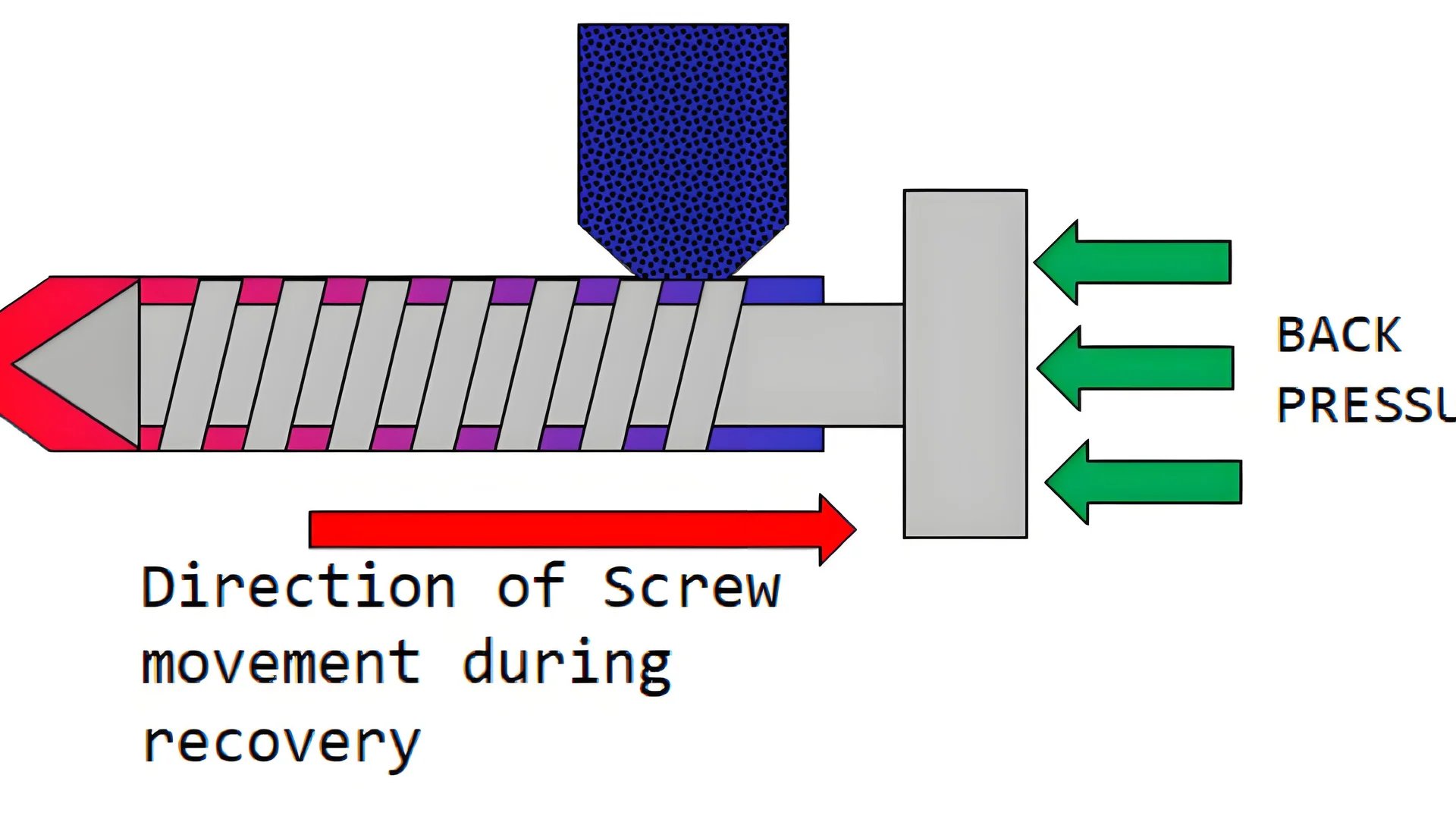
Understanding Back Pressure in Plastic Mixing
Back pressure is the resistance encountered by the screw when it moves backward during the plasticizing phase of injection molding. This resistance is not just a mechanical hindrance but a crucial component of the mixing process. By applying back pressure, the screw imparts additional shear forces onto the molten plastic. This action enhances the mixing and homogenization of the material, ensuring that additives are uniformly distributed and that colorants are consistently integrated throughout the batch.
Enhancing Material Homogeneity
One of the primary roles of back pressure in plastic mixing is to improve material homogeneity. The increased shear forces help break down any agglomerates in the plastic, leading to a more uniform melt. This results in molded parts with consistent properties, reducing variations and enhancing overall product quality.
Improving Density and Reducing Voids
Back pressure not only aids in mixing but also plays a significant role in enhancing the density of the molded product. As the back pressure compresses the molten plastic, it forces out trapped air, effectively reducing voids and minimizing air bubbles. This compression ensures that the final product is solid and free from defects, which is especially crucial for products requiring high structural integrity.
Controlling Flow Characteristics
Another critical aspect influenced by back pressure is the control over flow characteristics. By adjusting back pressure, manufacturers can manipulate the viscosity of the molten plastic, facilitating better flow through complex mold geometries. This control is vital for achieving accurate dimensional specifications and ensuring that intricate designs are filled correctly without imperfections.
Optimal Back Pressure Settings
Determining the optimal back pressure settings requires careful consideration of several factors, including the type of plastic material, mold design, and processing conditions. Each of these variables can significantly influence how back pressure affects mixing and, consequently, the quality of the final product. Manufacturers often rely on trial and error or empirical data to fine-tune these settings for optimal results.
By understanding how back pressure impacts plastic mixing1, manufacturers can enhance product quality and performance, making this parameter a critical focus in injection molding processes.
Back pressure reduces voids in molded plastics.True
Back pressure compresses molten plastic, forcing out air and reducing voids.
High back pressure decreases material homogeneity.False
High back pressure increases shear forces, enhancing material homogeneity.
How Does Back Pressure Influence Void Formation?
Void formation is a common issue in injection molding that can compromise the integrity and appearance of products.
Back pressure minimizes voids by compressing the molten plastic, expelling trapped air, and ensuring uniform material density during the molding process.
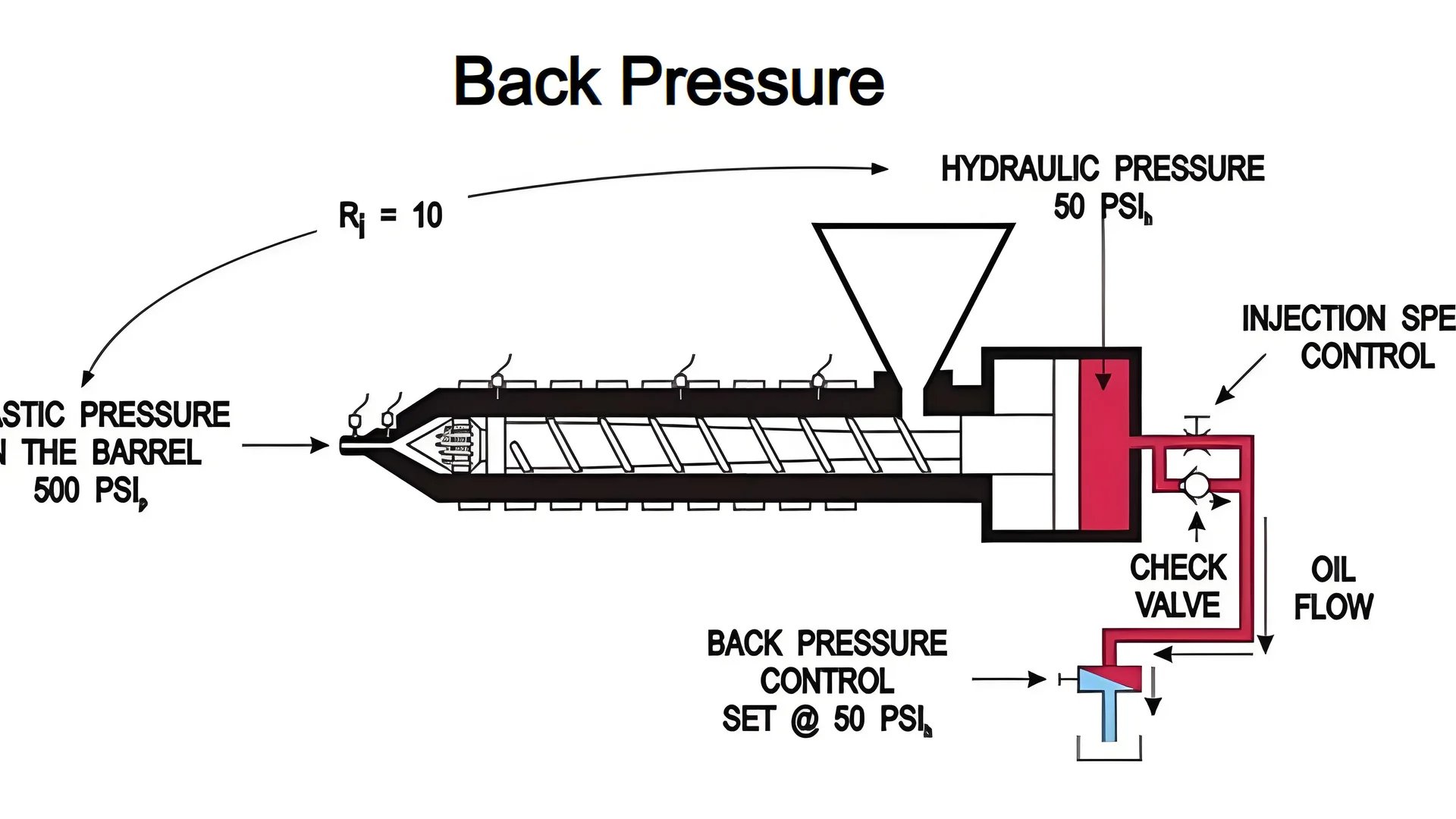
The Mechanism of Back Pressure in Void Reduction
Back pressure is crucial in mitigating voids within injection molded parts by enhancing the densification of the material. As the screw retreats, it faces resistance known as back pressure, which is intentionally applied to improve the quality of the molten plastic. This resistance increases the shearing action on the plastic, leading to better mixing and homogenization.
This compression of the molten plastic helps expel trapped air, a primary cause of voids. By eliminating these air pockets, back pressure ensures that the material fills the mold cavity more completely and uniformly.
Effects on Material Density
By enhancing material compaction, back pressure also improves the density of the molded part. Increased density is directly associated with reduced occurrence of voids. Higher back pressure results in a denser material, which fills every crevice of the mold, thus minimizing air entrapment and potential voids.
For example, in complex mold designs or when using materials with higher viscosity, adjusting back pressure can significantly enhance part quality by ensuring all regions are filled uniformly.
Finding the Balance: The Role of Material Properties
The optimal back pressure setting often depends on several factors, including material type and mold complexity. For instance, materials with a tendency to retain air might require higher back pressure settings to effectively mitigate void formation. However, excessive back pressure can lead to other issues such as increased cycle time or potential degradation of sensitive materials.
Injection molding experts recommend balancing back pressure settings by conducting trials under various conditions to achieve optimal results.
In summary, understanding how back pressure influences void formation is vital for producing defect-free injection molded products. By exploring material characteristics2 and experimenting with pressure settings3, manufacturers can fine-tune their processes for enhanced product quality.
Back pressure reduces voids in injection molding.True
Back pressure compresses molten plastic, expelling trapped air and minimizing voids.
Higher back pressure decreases material density.False
Higher back pressure increases material density by enhancing compaction.
In What Ways Does Back Pressure Affect Flow Characteristics?
Understanding the influence of back pressure on flow characteristics is crucial for achieving precision in injection molding.
Back pressure affects flow characteristics by controlling viscosity and flow rate, enabling better filling of complex molds and improved dimensional accuracy.

The Role of Back Pressure in Viscosity Control
Back pressure is a critical factor in managing the viscosity of molten plastic4. By adjusting the back pressure, molders can alter the shear rate applied to the plastic material. This adjustment influences the plastic’s viscosity, making it either more fluid or more resistant to flow. For example, higher back pressure typically increases the shear rate, reducing viscosity, thus allowing the plastic to fill intricate mold features with greater ease.
Enhancing Mold Filling
Efficient mold filling is another significant aspect affected by back pressure. When dealing with complex mold geometries, achieving uniform flow and complete cavity filling is paramount. Properly adjusted back pressure helps in maintaining a consistent flow rate throughout the molding cycle. This consistency is crucial for preventing defects such as short shots, where parts of the mold are not completely filled.
Dimensional Accuracy and Stability
Back pressure contributes to the dimensional accuracy of molded parts. By exerting control over flow characteristics, manufacturers can ensure that the material evenly fills the mold, leading to more stable and dimensionally accurate products. Consistent flow rates prevent warping and shrinkage, which are common issues arising from uneven material distribution within the mold.
Balancing Back Pressure for Optimal Results
Striking the right balance in back pressure settings is essential. Excessive back pressure can lead to increased cycle times and energy consumption due to the additional force required to move the screw. Conversely, insufficient back pressure might result in poor mixing and material inconsistencies. Therefore, understanding the precise requirements of each material and mold design is crucial for optimizing back pressure settings.
To sum up, back pressure significantly influences flow characteristics by managing viscosity and ensuring efficient mold filling. These effects are instrumental in producing high-quality, dimensionally accurate injection molded parts.
Higher back pressure reduces viscosity in injection molding.True
Higher back pressure increases shear rate, reducing viscosity for better mold filling.
Low back pressure leads to uniform flow in complex molds.False
Insufficient back pressure can cause poor mixing and uneven flow, not uniformity.
How Can You Optimize Back Pressure for Better Injection Molding?
Optimizing back pressure in injection molding can significantly enhance the quality and consistency of your products. Learn how to fine-tune this critical parameter for optimal results.
To optimize back pressure in injection molding, adjust based on material type and mold design. Balancing these factors ensures improved material homogeneity, reduces defects, and enhances product consistency.

Understanding Material Characteristics
When optimizing back pressure, the type of plastic material being used is crucial. Different plastics have varying viscosities and flow characteristics, affecting how back pressure should be applied. For instance, high-viscosity materials may require greater back pressure to ensure proper mixing and homogenization. It’s important to consult material-specific guidelines to determine ideal settings.
Evaluating Mold Design
Mold design also plays a significant role in determining optimal back pressure. Complex molds with intricate details might need higher back pressure to ensure the plastic fills all cavities completely. Conducting mold flow analysis5 can provide insights into how different back pressure levels affect the filling process, helping to fine-tune settings for specific designs.
Experimentation and Fine-Tuning
Given the variability of materials and molds, experimentation is often necessary to identify the best back pressure settings. Start with manufacturer-recommended values and make incremental adjustments, observing changes in the quality of the molded parts. Document each change and its outcomes to develop a tailored approach that consistently yields high-quality results.
Monitoring and Feedback
Continuous monitoring of the injection molding process is essential. Implement sensors to provide real-time data on back pressure and its effects. Use this feedback to adjust settings dynamically, ensuring optimal conditions are maintained throughout production. This approach minimizes defects like voids and improves overall product quality.
Training and Development
Investing in training for personnel involved in the injection molding process can lead to better optimization of back pressure settings. Understanding how different parameters interact allows for more informed decision-making. Consider workshops or training programs6 that focus on the intricacies of back pressure management in injection molding.
High-viscosity materials need greater back pressure.True
High-viscosity materials require more force for proper mixing.
Mold design doesn't affect back pressure optimization.False
Complex molds may need higher back pressure for complete filling.
Conclusion
Optimizing back pressure is key to achieving high-quality injection molded products. By understanding its effects, manufacturers can enhance both product quality and efficiency.
-
Explore detailed mechanisms of how back pressure affects plastic mixing.: This reflects the increase in melt density with backpressure. In this particular example, a choice of 600 psi of plastic pressure can be used … ↩
-
Learn about how different materials influence void formation.: Voids tend to appear on thicker part surfaces and can occur when the outside layer of the part cools off and solidifies faster than the internal which can in … ↩
-
Discover effective techniques for adjusting back pressure.: As a general rule, the amount of decompression should not exceed 1 ½ times the travel of the check ring. As backpressure is increased, the time for the screw to … ↩
-
Understand how back pressure adjustments impact plastic viscosity control.: Material melting and colour dispersion can be improved with the use of high backpressures, but it also increases stress on the injection … ↩
-
Learn how mold flow analysis aids in optimizing back pressure.: The predictive process of mold flow analysis can uncover design issues, save resources, provide for preemptive correction, and speed up overall … ↩
-
Explore training programs that enhance understanding of injection molding processes.: The American Injection Molding (AIM) Institute is a world leader in education and training for the plastic injection molding industry. ↩