Brittle cracking in plastic parts during frigid conditions can feel like an ominous threat to manufacturers. But fear not! With the right knowledge and strategies, we can conquer this challenge.
To prevent brittle cracking in plastic injection molded parts at low temperatures, select materials with good low-temperature resistance, optimize injection molding parameters, and enhance product design with reinforcements and rounded corners.
But this is just the tip of the iceberg. Let’s delve deeper into each strategy so you can truly master preventing brittle cracking.
Polycarbonate is ideal for low-temp plastic molding.True
Polycarbonate maintains toughness and strength in cold conditions.
What Are the Best Materials for Low-Temperature Plastic Molding?
Choosing the right materials is essential for effective low-temperature plastic molding. Discover which materials excel under these conditions.
For low-temperature plastic molding, engineering plastics like polycarbonate (PC) and polyamide (PA) are ideal due to their toughness and strength. Adding low-temperature resistant additives further enhances their performance.
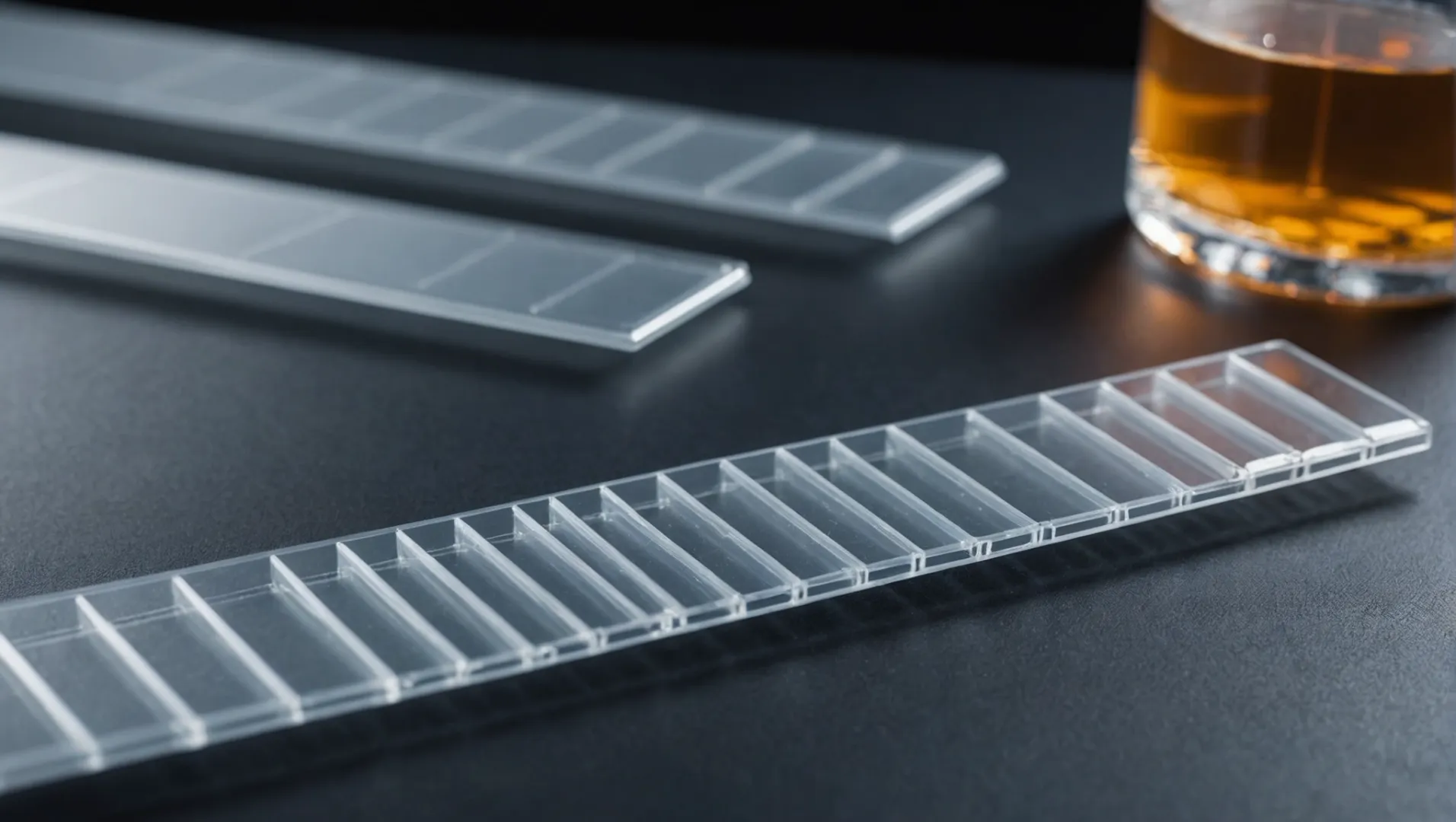
Selecting the Right Engineering Plastics
When dealing with low-temperature environments, the choice of plastic materials1 plays a critical role in ensuring product durability and functionality. Engineering plastics, particularly polycarbonate (PC) and polyamide (PA), are known for their exceptional low-temperature resistance.
Polycarbonate (PC)
PC is favored for its impact resistance and strength even at low temperatures. This makes it suitable for applications where durability is paramount, such as in automotive components exposed to cold climates. Its molecular structure provides resilience against temperature-induced stress.
Polyamide (PA)
Commonly known as nylon, PA is another excellent option for low-temperature applications. It offers flexibility and toughness, preventing brittle failure when subjected to cold conditions. Its versatility makes it suitable for a variety of industrial applications, from mechanical parts to consumer goods.
Enhancing Material Properties with Additives
While selecting robust engineering plastics is crucial, incorporating low-temperature resistant additives2 can significantly improve material performance.
Toughening Agents
These additives enhance the flexibility of plastics by modifying their molecular chains, reducing the risk of cracking under stress. They are particularly effective in applications where plastic parts experience frequent mechanical stress at low temperatures.
Cold Resistant Agents
Cold resistant agents are designed to maintain the integrity of the plastic’s structure by preventing crystallization at low temperatures. They help maintain the elasticity and toughness of plastics, making them essential for products exposed to extreme cold.
Importance of Understanding Material Characteristics
To fully leverage the benefits of these materials and additives, manufacturers must thoroughly understand their characteristics and limitations3 in specific environments. This involves:
- Testing and Evaluation: Conducting detailed assessments to determine how materials react under varying temperature conditions.
- Customization: Tailoring material properties to suit specific application needs, ensuring optimal performance and longevity.
- Collaboration with Suppliers: Working closely with material suppliers to develop bespoke solutions that align with design and functional requirements.
Through informed selection and strategic enhancement of materials, manufacturers can effectively mitigate the challenges posed by low-temperature environments and produce high-quality, durable plastic products.
Polycarbonate is ideal for low-temp plastic molding.True
Polycarbonate's impact resistance and strength make it suitable for cold environments.
Nylon is unsuitable for low-temperature applications.False
Nylon, or polyamide, offers flexibility and toughness in cold conditions.
How Does Injection Molding Temperature Affect Part Durability?
The temperature used in injection molding can significantly influence the durability of the resulting plastic parts, impacting their performance and longevity.
Injection molding temperature affects part durability by influencing the material’s molecular structure, mechanical properties, and potential for defects. Proper temperature management ensures optimal toughness and resistance to environmental stressors.
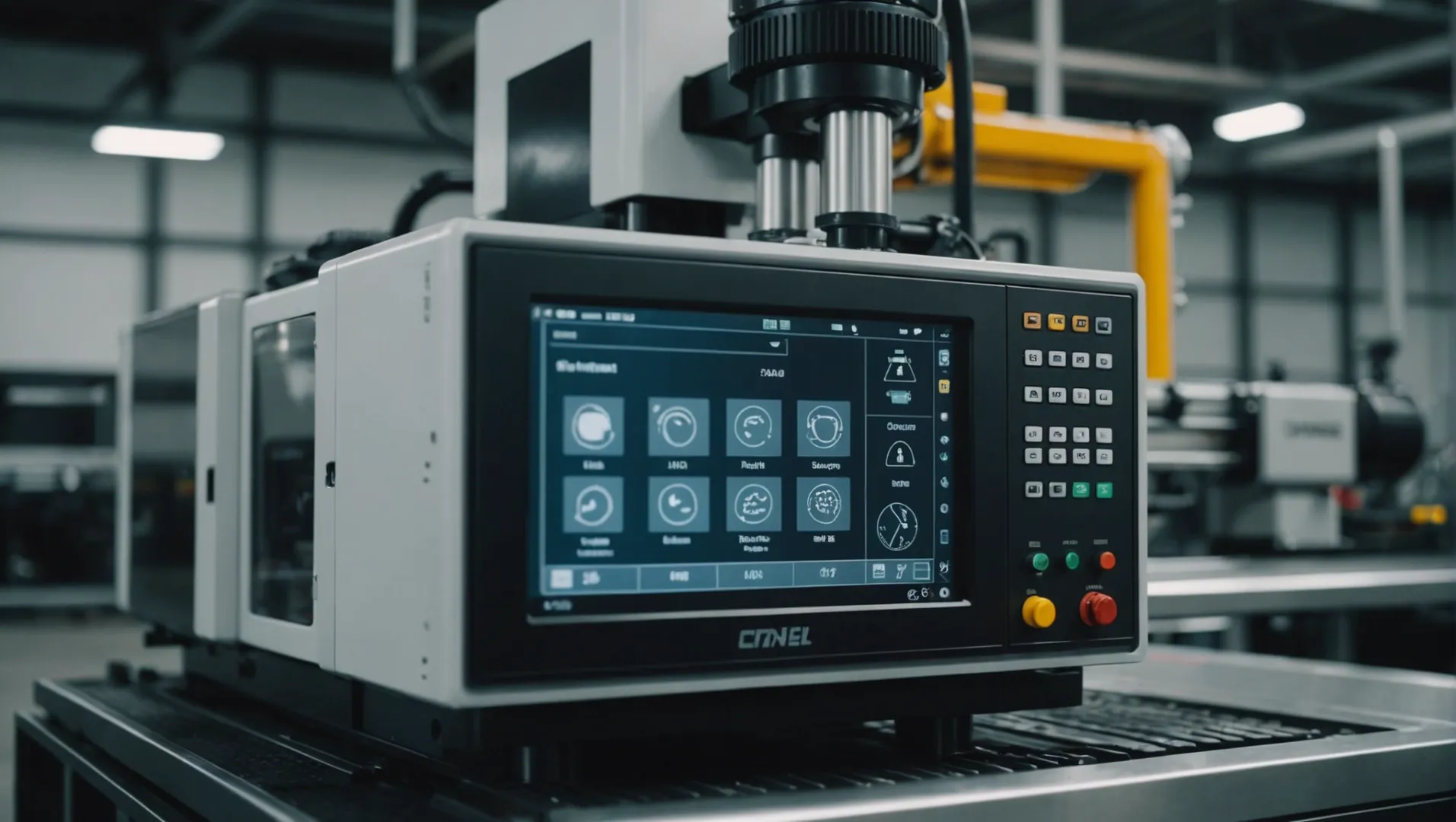
The Role of Temperature in Injection Molding
Injection molding temperature is a critical parameter that directly impacts the molecular structure of plastic materials. When the temperature is adequately controlled, it allows polymer chains to become more flexible, resulting in better toughness and resilience.
-
Molecular Flexibility: Higher temperatures can make polymer chains more mobile, improving the material’s ability to absorb impact without fracturing. However, excessive temperatures risk degrading the polymer, leading to reduced mechanical properties.
-
Avoiding Defects: Proper temperature control helps prevent defects such as warping and incomplete filling, which can compromise durability. A study on molding temperatures4 shows how finely-tuned adjustments can minimize these issues.
Balancing Temperature for Optimal Durability
Achieving the perfect balance in molding temperature is crucial. Here are some expert-recommended strategies:
-
Optimize According to Material: Each plastic type has a specific temperature range where it performs best. For example, engineering plastics like polycarbonate have distinct requirements compared to polyamides.
-
Consider Product Requirements: Adjust the temperature according to the product’s end-use environment to ensure it withstands operational stresses effectively.
Material | Ideal Molding Temperature (°C) | Key Benefits |
---|---|---|
Polycarbonate | 280 – 320 | High toughness, clarity |
Polyamide | 230 – 280 | Excellent strength, fatigue resistance |
Practical Implications
Manufacturers need to tailor injection molding temperatures based on both material properties and product design. In environments where parts are subject to low temperatures, maintaining higher molding temperatures during production can enhance part durability.
- Impact on Long-term Use: Properly molded parts demonstrate superior performance in demanding conditions. For instance, products designed for cold climates can benefit from tailored temperature settings during their production phase.
For further insights, exploring resources on advanced injection techniques5 provides valuable knowledge on maximizing part durability through precise temperature control.
Higher molding temperatures improve polymer flexibility.True
Higher temperatures increase polymer chain mobility, enhancing impact resistance.
Excessive molding temperatures do not degrade polymers.False
Too high temperatures can degrade polymers, reducing mechanical properties.
Why Is Product Design Crucial for Preventing Cracking?
Product design plays a pivotal role in ensuring plastic parts remain crack-free, especially under challenging conditions. By focusing on specific design elements, manufacturers can significantly enhance the durability and longevity of their products.
Effective product design prevents cracking by eliminating stress concentration through rounded corners, consistent wall thickness, and strategic reinforcement structures.
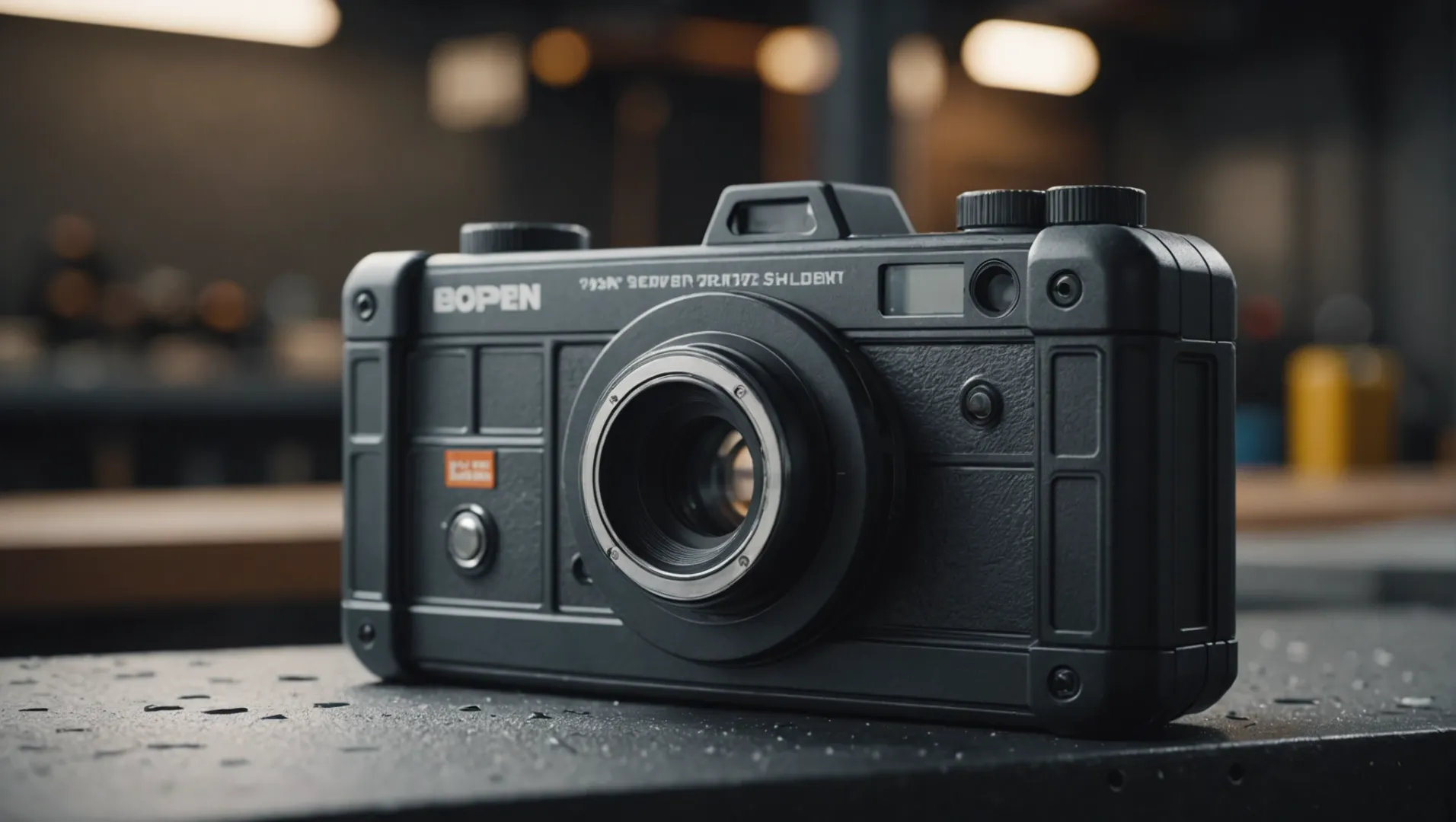
Understanding Stress Concentration
Stress concentration occurs when stress within a material is intensified at certain points, often leading to cracks. In plastic parts, sharp corners and thin-walled structures are primary culprits. These features create localized high-stress areas where cracks can initiate, especially in low-temperature environments.
Designers can mitigate these risks by incorporating rounded corners and maintaining uniform wall thickness. Rounded transitions help distribute stress evenly throughout the part, reducing the likelihood of failure.
The Role of Reinforcement Ribs
Reinforcement ribs and support structures are crucial for enhancing part rigidity and strength. They provide additional support, minimizing deformation and the potential for cracking. For instance, ribs should be strategically placed along the length of a part to bear loads efficiently without adding excessive weight or cost.
Table: Design Features to Reduce Cracking Risk
Design Feature | Benefit |
---|---|
Rounded Corners | Distributes stress evenly |
Uniform Wall Thickness | Minimizes stress concentration |
Reinforcement Ribs | Increases structural rigidity |
Analyzing Real-World Applications
Consider industries where low-temperature environments are prevalent, such as automotive or outdoor equipment manufacturing. Here, effective product design6 is not just a preference but a necessity to ensure safety and performance.
In automotive applications, for example, dashboard components must withstand extreme temperature variations without cracking. By employing design principles like those mentioned above, manufacturers can produce parts that remain intact under stress.
Strategic Design Adjustments
Adjustments in product design should be based on comprehensive analysis and testing. Utilizing simulation tools7 can provide insights into stress distribution and identify potential failure points before production begins. This proactive approach allows designers to make necessary modifications early in the development process.
Moreover, involving cross-functional teams in the design phase ensures that all aspects of product performance are considered, from material choice to post-processing methods.
In conclusion, a well-thought-out design is indispensable for preventing cracking in plastic parts. By addressing stress concentration through strategic design choices, manufacturers can enhance part durability, ensuring reliability across various applications.
Rounded corners reduce stress concentration in plastic parts.True
Rounded corners distribute stress evenly, minimizing crack risk.
Thin walls in plastic parts enhance durability against cracking.False
Thin walls increase stress concentration, leading to potential cracks.
What Post-Processing Techniques Enhance Low-Temperature Resistance?
Optimizing post-processing techniques can significantly enhance the low-temperature resistance of plastic parts, ensuring durability and performance in challenging environments.
To enhance low-temperature resistance in plastic parts, employ annealing to reduce internal stresses and apply protective surface coatings. These techniques improve toughness and stability.
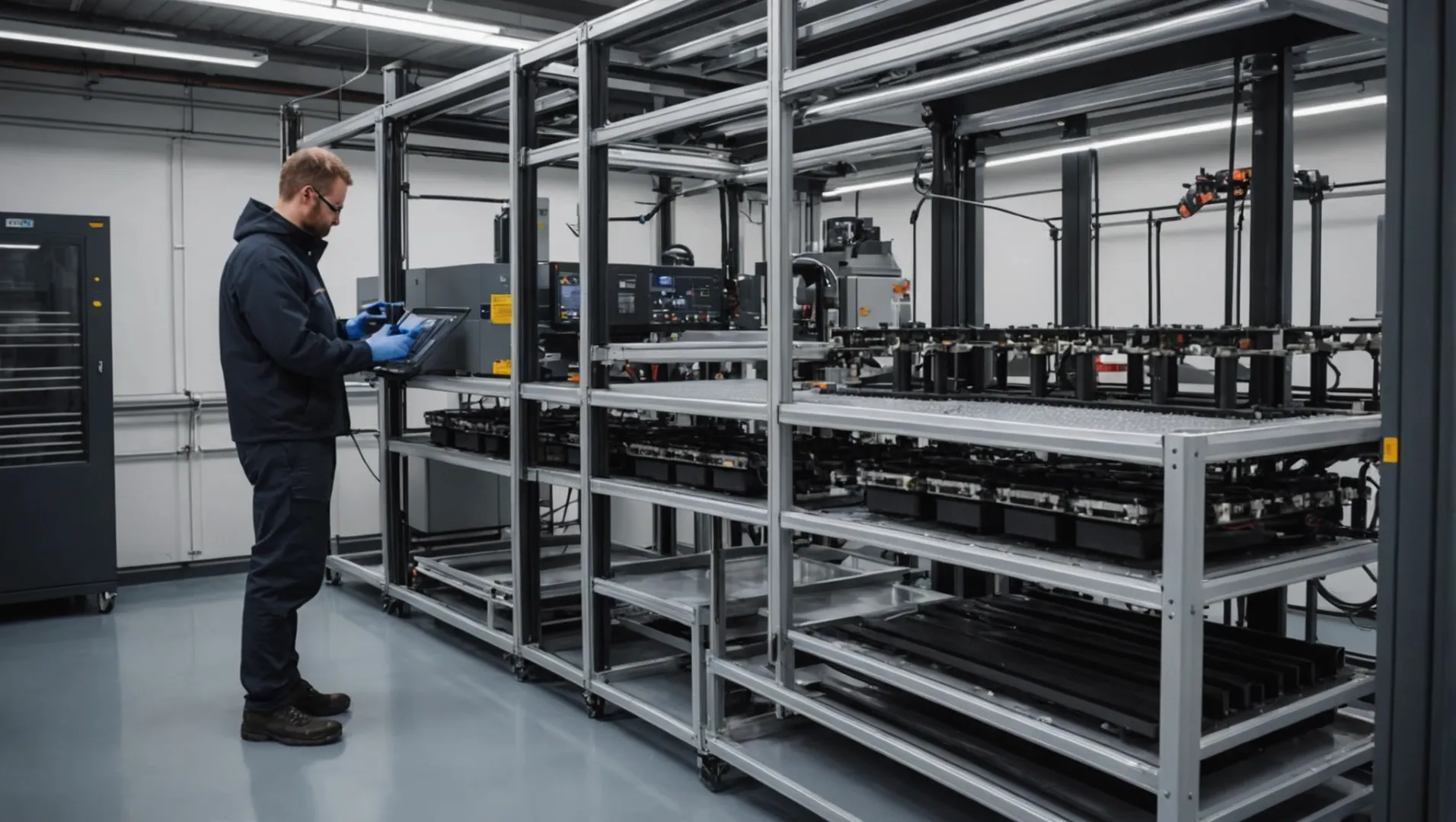
Annealing Treatment
One of the most effective post-processing techniques to enhance low-temperature resistance in plastic parts is annealing. This process involves heating the plastic part to a specific temperature below its melting point and then slowly cooling it. The aim is to relieve internal stresses that can accumulate during the molding process.
When internal stresses are reduced, the material’s toughness and stability at low temperatures are significantly improved. The specific annealing temperature and duration depend on the type of plastic used. For example, polycarbonate (PC) might require different conditions compared to polyamide (PA). It’s crucial to tailor the annealing process to each material’s unique properties for optimal results.
Surface Coating
Applying a surface coating is another valuable technique for enhancing low-temperature resistance. A well-chosen coating can act as a protective barrier against environmental stressors, such as moisture and cold, that might otherwise cause brittle cracking.
The key is selecting a coating material that adheres well to the plastic and offers substantial low-temperature resistance. For instance, polyurethane coatings are known for their excellent flexibility and toughness at low temperatures. It’s important to ensure that the coating does not compromise the part’s dimensional tolerance or add excessive weight.
Comparative Analysis
Technique | Key Benefits | Considerations |
---|---|---|
Annealing | Reduces internal stress; enhances toughness | Requires precise temperature control |
Surface Coating | Provides external protection; prevents cracking | Selection of suitable coating material |
Both techniques serve distinct purposes but can be used synergistically to maximize low-temperature resistance. By combining these post-processing methods, manufacturers can create parts that withstand harsh conditions while maintaining structural integrity. For further insights into practical applications and expert recommendations, consider exploring annealing processes for plastics8 or effective surface coating strategies9.
Annealing reduces internal stresses in plastics.True
Annealing heats and cools plastics to relieve molding stresses.
Surface coatings add excessive weight to plastic parts.False
Coatings are designed to protect without adding significant weight.
Conclusion
By optimizing materials, processes, and designs, we can significantly reduce brittle cracking risks in low temperatures. Reflect on your practices and embrace these strategies for enhanced part reliability.
-
Learn about top-performing plastics ideal for cold environments.: Most engineering plastics are generally well suited to low temperatures, the extent to which depends on the material and the specific application. ↩
-
Explore additives that enhance plastic toughness at low temperatures.: High-performance UHMW (TIVAR 88) · ABS (acrylonitrile butadiene styrene) · PTFE (Teflon) · PEEK · PEI (POLYETHERIMIDE). ↩
-
Discover methods for assessing plastic performance in cold settings.: Assessing the performance of plastics in a low temperature application is therefore a complex task. As with any plastics application, essential factors such as … ↩
-
Learn about minimizing defects with proper temperature settings.: First, if the mold temperature is too low, it will reduce the melt flowability, possibly leading to incomplete filling. It affects the … ↩
-
Explore techniques to optimize injection processes for durability.: A review of current advancements in high surface quality injection molding: Measurement, influencing factors, prediction, and control. ↩
-
Explore strategies to enhance durability through effective product design.: Define the product before it’s created · Give insight into what will make the product successful · Help you understand what you should design. ↩
-
Discover tools to predict stress distribution in product designs.: Stress Analysis has been mainly applied for designers to observe stress distribution inside parts and part inserts. The stress distribution has a significant … ↩
-
Discover how annealing reduces stress and improves durability.: Annealing is a heat treatment method used to eliminate any unacceptable stress that may result from the manufacturing process, improve dimensional stability. ↩
-
Learn about selecting coatings that enhance toughness at low temperatures.: Adhesion improvement is the most common application but other surface characteristics, such as wettability, water- and chemical resistance, nonfouling, … ↩