Imagine creating something complex. Every tiny detail really matters. A single mistake might ruin everything.
The lifter release angle in injection molds is very important for the quality of molded parts. The right angle lets parts come out smoothly. This reduces problems like shrink marks, size errors and stress spots. However, a wrong angle risks both how the parts look and how strong they are. A bad angle can cause serious issues.
I recall my first deep dive into injection molding. It felt like solving a difficult puzzle. Each piece had to fit perfectly. Every element mattered. The lifter release angle was especially important. This angle greatly affects the final product. It is not just a small detail. It is a crucial factor in the molding process.
A proper release angle stops annoying shrink marks. These marks can ruin parts that were once beautiful. A small angle change impacts the look and strength of products. High-precision part designs require accuracy. Even a tiny change means success or failure.
The lifter angle also affects stresses and structure inside the material. A wrong angle can focus stress and lead to early breaking. I faced this with sports equipment parts. A good angle keeps everything strong. It helps the product last longer.
These challenges revealed the art in this science. Getting the lifter release angle correct is powerful. Do not ignore it when working on electronics cases or car interiors.
Shrink marks are caused by excessive tensile force.True
Shrink marks occur when the demolding angle is too small, increasing tensile force.
Proper demolding angle reduces stress concentration.True
An appropriate demolding angle minimizes internal residual stress, reducing stress concentration.
- 1. What Are Shrink Marks and How Do They Occur?
- 2. Why is Dimensional Accuracy Crucial in Injection Molding?
- 3. How Does Stress Concentration Affect Molded Part Longevity?
- 4. How Does Microstructure Affect Injection Molded Parts?
- 5. How Can I Optimize the Lifter Release Angle for Better Quality?
- 6. Conclusion
What Are Shrink Marks and How Do They Occur?
Have you ever seen those annoying little lines on your plastic things and wondered how they appeared?
Shrink marks are tiny and annoying surface flaws on injection molded parts. Uneven cooling often causes them. Stretching during the demolding process also leads to these imperfections. These blemishes affect the look of the product. The functionality of the final product can also be compromised.
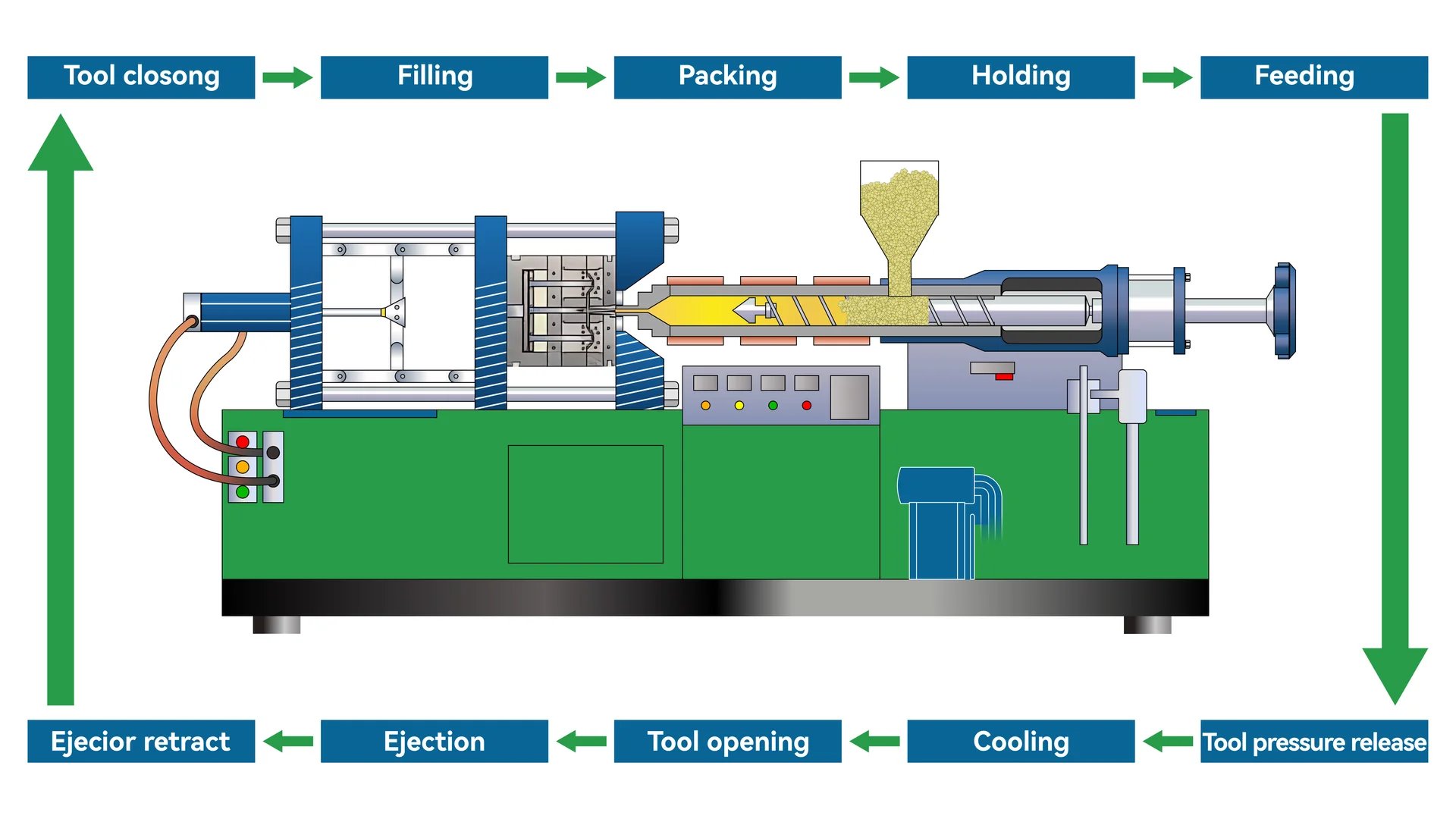
Understanding Shrink Marks
Shrink marks often sneak up on injection molded parts1. They appear as small dents or lines on a smooth surface. These marks usually result from uneven cooling and hardening of the plastic. The surface becomes uneven and may lose its quality. Once, I noticed these marks on a new gadget. It was like seeing a scratch on a new car.
Causes of Shrink Marks
Shrink marks often come from a wrong demolding angle. A small angle makes the lifter grip too tightly and pull the plastic too much. This pulling causes indentations during cooling. This is a big problem for products that must look as good as they function, like gadgets or car interiors. I once worked on a project where looks were very important and shrink marks were a real headache.
Dimensional Impacts
Shrink marks aren’t just visual. They mess with size accuracy2, too. I had an incident where a wrong part didn’t fit in its assembly. It had warped slightly but enough to ruin everything. Precision components like those in medical devices probably suffer from this issue.
Stress and Internal Structure
Stress concentration is another concern. A small demolding angle needs more force during removal, creating stress points that might crack. I learned this when a component cracked under pressure; stress weakened the internal structure, changing fiber orientation and filler distribution.
Prevention Strategies
How to stop these annoying marks? Correct demolding angle is key. Adjusting cooling times and redesigning molds help control temperature differences. Simulation tools predict shrinkage well, making the process smoother by ensuring parts look good and work well.
By fixing these issues, the appearance of injection molded parts can improve significantly while enhancing structural integrity to extend their life span against external forces effectively.
For those focusing on improving their injection molding skills3, studying mold design adjustments and choosing the right materials is very valuable.
Shrink marks affect injection molded part appearance.True
Shrink marks are caused by excessive stretching during cooling, affecting flatness.
Improper demolding angle enhances injection part strength.False
Improper angles cause deformation and stress, weakening the part's structure.
Why is Dimensional Accuracy Crucial in Injection Molding?
Think about a time when a puzzle piece did not match. That is how manufacturing feels without dimensional accuracy.
Dimensional accuracy helps injection molded parts fit perfectly. These parts work correctly and meet quality standards. Good precision reduces defects. It also lessens waste.
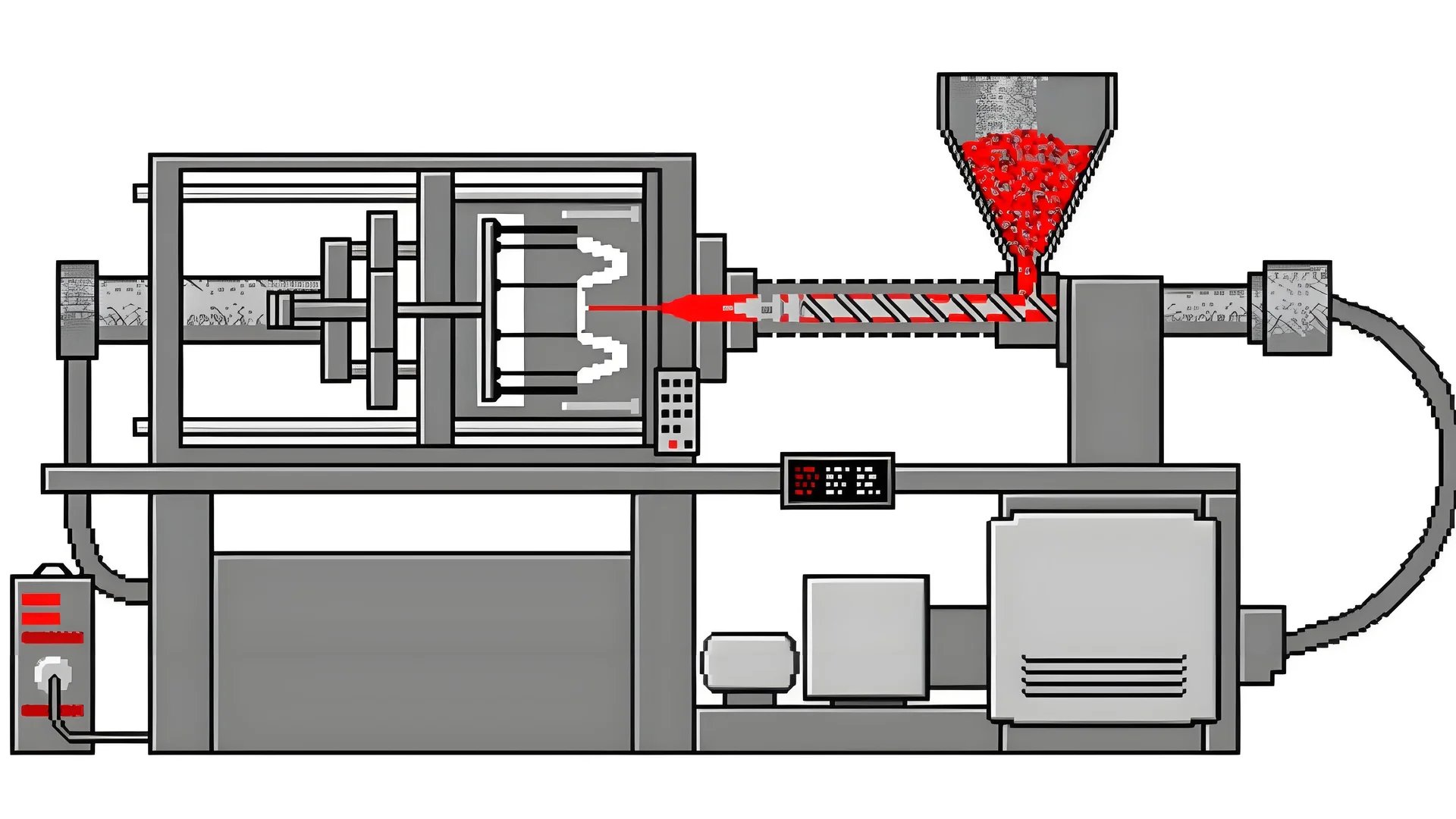
Impact on Product Fit and Functionality
Dimensional accuracy in injection molding directly influences the ability of parts to fit and function as intended. I once worked on creating custom-fit parts for a high-tech gadget, realizing that even a tiny error in size might cause problems. For instance, a plastic buckle that changed its shape didn’t fit properly, almost causing a product recall. The importance of precision4 cannot be overstated when it comes to these critical applications.
Quality and Appearance Considerations
People often judge products by their appearance first. Wrong dimensions can lead to visible defects such as ugly marks on the surface, which are unacceptable in products with high aesthetic standards like phone cases or car interiors. Accurate molding ensures parts look great and work well, thereby enhancing their market appeal.
Internal Structural Integrity
I remember when a mistake in removing parts led to cracks in plastic tool handles, making them weak. Handles subjected to high stress need to be strong; therefore, maintaining dimensional accuracy is crucial. Understanding demolding effects5 on stress distribution is essential for durable product design.
Material Efficiency and Waste Reduction
In one project, we focused on cutting waste to save money and help the environment. Getting the size right was key; by staying true to the design, we accepted more parts and used fewer resources. This focus on precision leads to efficient manufacturing6 processes that optimize resource use.
Influence on Microstructure
In a project with glass fiber parts, an incorrect angle messed up the fiber distribution, weakening the part’s structural integrity. Proper control ensures material properties are retained, thereby enhancing performance and lifespan in its application environment.
Shrink marks indicate poor demolding angle.True
Shrink marks occur when the demolding angle is too small, causing excessive tensile force.
Proper demolding angle prevents stress concentration.True
A correct demolding angle reduces stress concentration, preventing cracks and prolonging part life.
How Does Stress Concentration Affect Molded Part Longevity?
Do you know why some molded parts break right when you need them?
Stress in molded parts often causes cracks and breaks. This reduces their lifespan. Adjusting demolding angles is crucial. A strong design is important. These steps really increase durability. They also stop early failures.
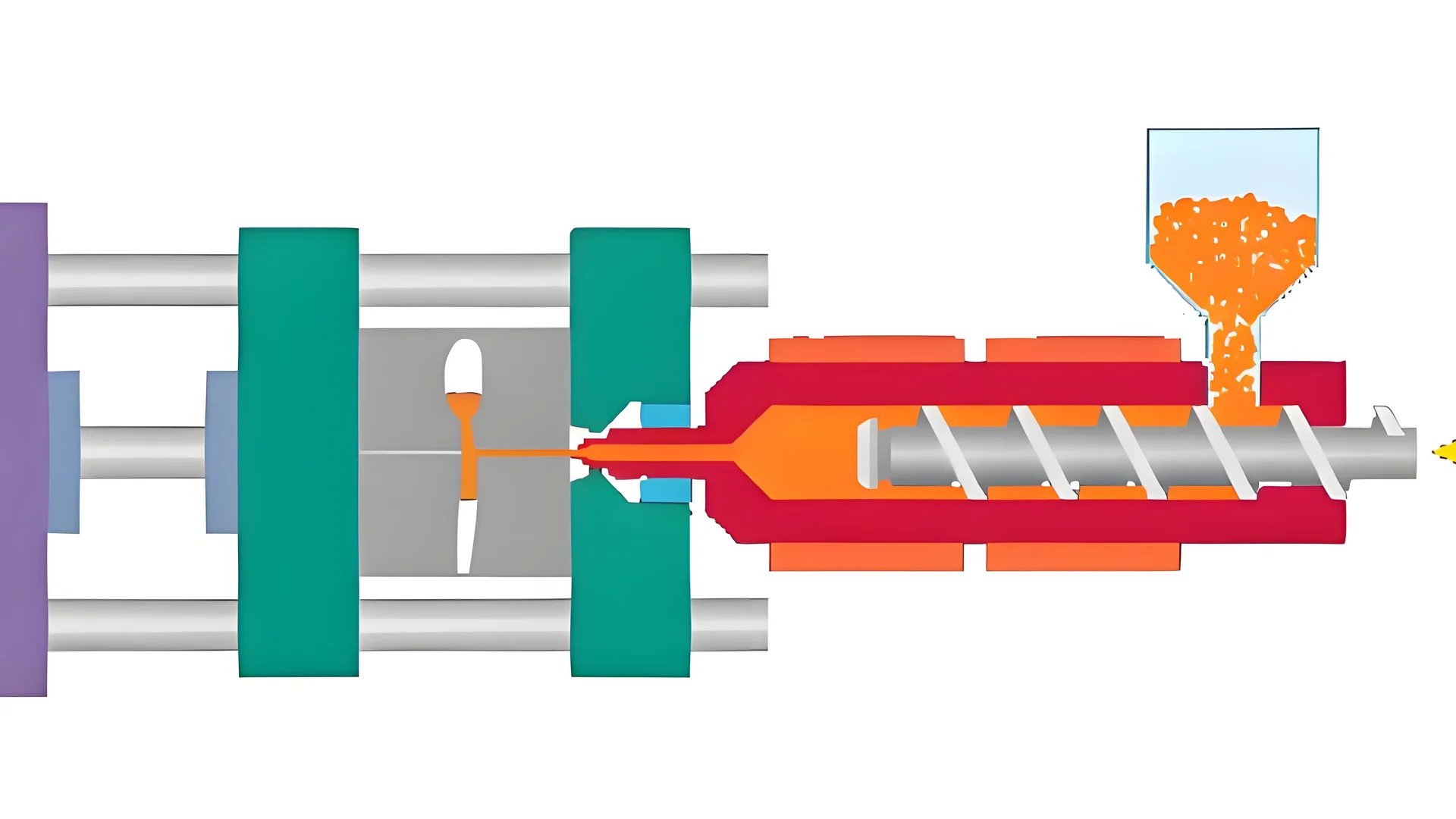
Appearance Quality Impact
I worked on a project with little time. During this work, I saw stress ruin the look of molded parts. The angle for removing the mold was too small, so ugly shrink marks appeared. These marks mocked us every time we looked at them. These were more than just ugly spots; they hurt the flatness and surface quality7. This was especially bad for products needing high visual appeal, like electronic covers and car insides.
Dimensional Accuracy Concerns
In another project, we made parts for a medical device. Each small size error felt huge. Wrong mold angles led to parts bending badly. This was alarming because precision is key for parts needing exact sizes. It showed me how important every detail is in design where dimensional accuracy8 is crucial.
Internal Structure and Stress
While working on tough mechanical parts, I understood stress impact on inner structures. High mold forces twisted fiber directions, causing cracks to appear early. This was scary in parts needing durability, like mechanical components9. It highlighted how managing stress well is very critical.
Deformation During Demolding
Once, a plastic lid caused a lot of trouble. It wouldn’t fit right because of bending when released from the mold. It twisted and force couldn’t make it sit properly. This taught me the need for correct angles to keep product life long as product longevity10 is very important here.
Microstructural Integrity
Our team struggled with fiber-reinforced materials once. Wrong mold angles messed up molecular structures, weakening strength and toughness over time. Keeping this structure intact is crucial for material strength against wear and impact as maintaining strength and toughness11 are really important.
Small demolding angle causes shrink marks.True
A small demolding angle increases tensile force, leading to shrink marks.
Dimensional deviation is unaffected by demolding angle.False
Improper angles can cause deformation, affecting dimensional accuracy.
How Does Microstructure Affect Injection Molded Parts?
Have you ever thought about how small details affect the quality of molded parts? Tiny details really matter! They probably make all the difference.
Microstructure in parts made by injection molding is very important. It affects how strong the parts are, their size accuracy and how they look. Manufacturers adjust processing conditions. They control fiber alignment and filler distribution. This process increases strength. It reduces flaws like shrink and stretch marks.
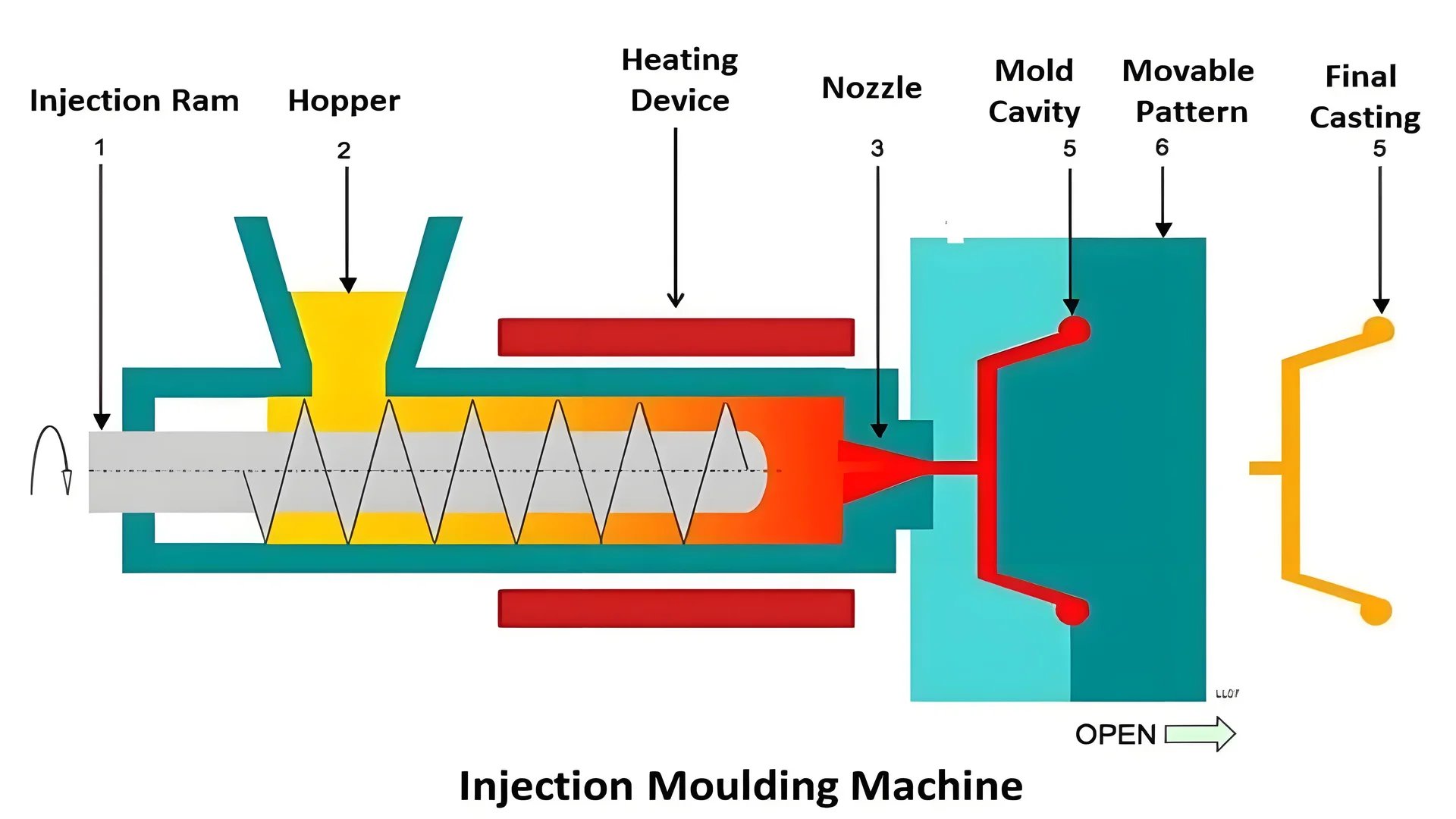
Influence on Mechanical Properties
Microstructure strongly affects mechanical properties. Imagine building a bridge, but only some beams are there. Uneven filler spread, like glass fibers breaking apart, weakens parts. Weaker parts wear out easier. I faced this problem when a project failed due to ignored microstructural issues. This taught me a hard lesson: every fiber must align and spread evenly.
The arrangement of molecular chains and the distribution of fillers such as glass fibers can dramatically affect strength and toughness12. For example, if glass fibers are not evenly distributed or if they break during the demolding process due to improper angles, the reinforcing effect diminishes, making parts susceptible to wear and impact.
Impact on Dimensional Accuracy
Microstructure also affects dimensional accuracy. A wrong demolding angle causes parts to warp, like a cake not fitting its mold. I’ve seen parts that wouldn’t fit because of slight mistakes. These small errors prove how crucial each detail is in engineering.
A suitable demolding angle can prevent deformation, ensuring that the part retains its designed dimensions. Conversely, an improper angle can lead to dimensional deviations13, affecting the part’s fit with other components.
Appearance Quality Concerns
Once, I admired an electronic casing’s smooth look until I saw stretch marks on the back. Poor microstructural handling often causes these marks. Getting a smooth surface requires careful attention to molding angles; otherwise, stress marks appear.
Improper demolding angles can cause shrink or stretch marks, detracting from the part’s appearance—critical for consumer-facing products like electronic casings. Maintaining microstructure helps in preserving a smooth surface finish, meeting high aesthetic standards.
Internal Quality and Stress Concentration
Stress concentration hides inside molded parts. Some areas handle more stress and can crack if ignored. Bad microstructural alignment creates stress points that weaken the part’s life.
The internal quality of injection molded parts can be compromised by stress concentration if microstructural integrity is not maintained. This stress can lead to cracks under load, particularly in areas near inverted buckles.
By focusing on these tiny details during manufacturing, engineers improve products and reduce failures by understanding materials and mastering processes—a deep understanding of material science principles is essential to optimize product lifecycle14. I value this more with each project I do.
Shrink marks indicate poor demolding angle.True
Shrink marks form due to excessive tensile force from a small demolding angle.
Proper demolding angle ensures no deformation.True
A correct angle prevents unnecessary deformation, maintaining part integrity.
How Can I Optimize the Lifter Release Angle for Better Quality?
Have you ever wondered how something tiny has a huge effect on quality? I often think about this, especially with lifter release angles in injection molding.
I adjust the lifter release angle carefully. It should not be too small or too large. A good angle avoids defects. These defects include shrink and stretch marks. Keeping the dimensions accurate is important. This reduces stress in the part. The part’s internal structure stays intact.
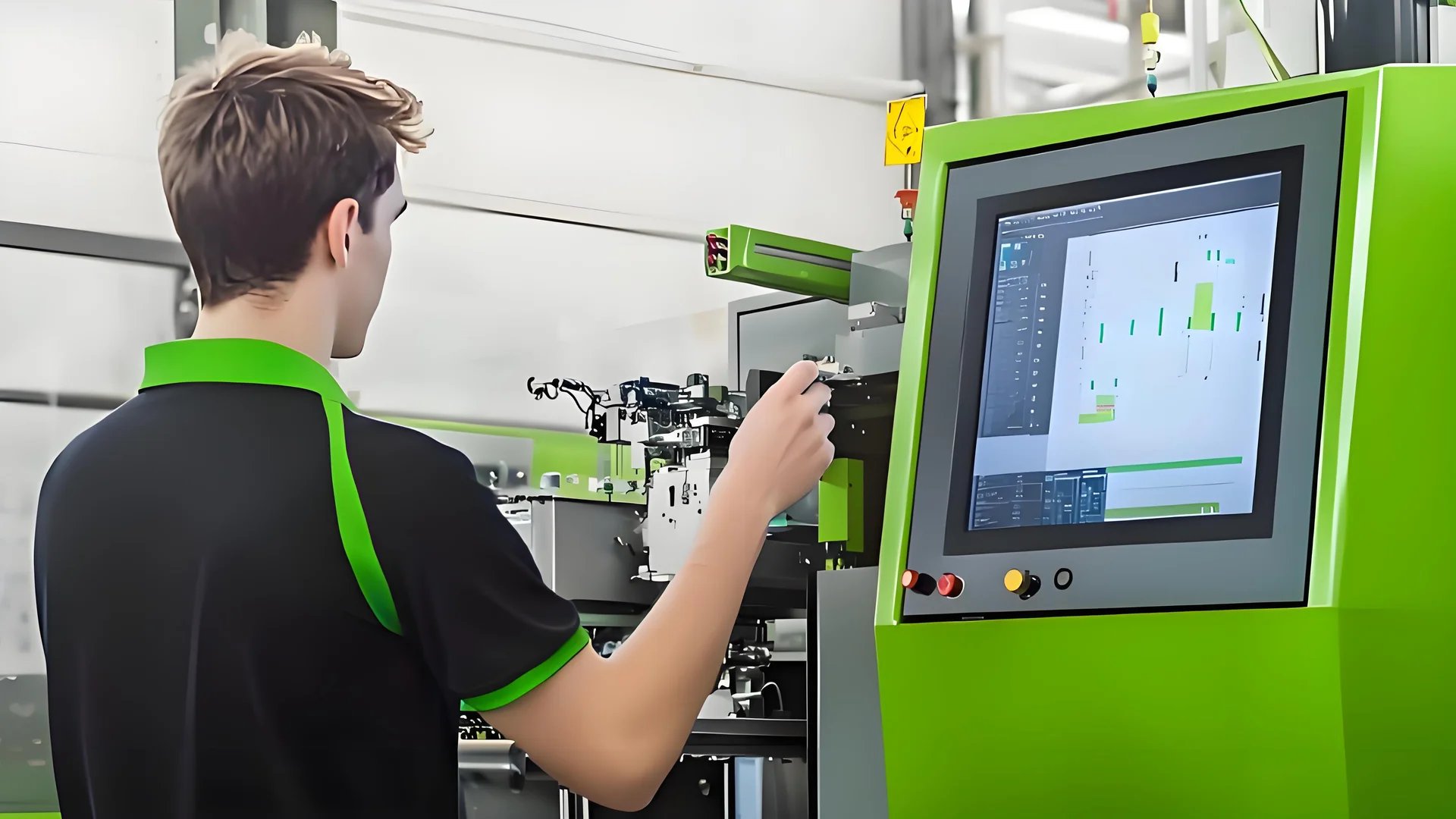
Appearance Quality
I first noticed tiny shrink marks on a molded part. They looked like small scars. These marks appear when the lifter angle is too tight, stretching the part during removal. It’s like pulling off a fitted sheet that’s too small for the bed. Stretch marks appear when the angle isn’t correct. They create friction and leave noticeable marks. Surfaces like electronic casings or car interiors really need a smooth appearance.
Dimensional Accuracy
In one project, parts didn’t fit properly, despite careful design. The lifter angle was slightly wrong, causing size errors. It’s like baking a cake and it turns out a bit off. For parts needing exact sizes, like medical devices, small errors become big issues. Even tiny mismatches matter a lot.
Internal Quality Aspects
Cracks appeared in unexpected spots on molded parts. The wrong demolding angle caused stress. It’s like putting your weight on one foot and feeling pain later. For things like tool handles or sports gear that face stress, the right angle is very important for long-lasting products. Durable products do not fail early.
Stress and Deformation
A wrong angle led to a deformed part once. It should’ve been flat but looked warped. The material felt too much stress. With the correct angle, parts stay smooth and strong. They keep their shape, just like how a well-tuned piano hits the right notes.
Microstructure Considerations
I don’t overlook the microstructure of parts now. A wrong angle can disturb molecular chains or fillers, especially with fiber-reinforced parts—it’s like trying to build a sandcastle with mixed sand; it just collapses. With the right angle for removal, parts stay strong and durable.
Best Practices in Optimization
Using simulation tools15 before starting production helps me greatly as they predict how angles affect the outcome. I also inspect and maintain lifters often; keeping them smooth reduces defects—it’s akin to keeping shoes polished and in top shape.
Shrink marks indicate improper demolding angle.True
Shrink marks occur when the demolding angle is too small, causing stress.
Correct demolding angle reduces internal stress in parts.True
A proper angle minimizes residual stress, enhancing part durability.
Conclusion
The lifter release angle in injection molds is crucial for preventing defects like shrink marks and ensuring dimensional accuracy, internal quality, and overall durability of molded parts.
-
Learn more about how injection molding shapes manufacturing. ↩
-
Understand how shrink marks can alter dimensional precision. ↩
-
Discover strategies to enhance injection molding efficiency. ↩
-
Learn why precision is critical for high-quality molded parts. ↩
-
Understand how demolding impacts part stress and durability. ↩
-
Discover strategies for reducing waste and improving efficiency. ↩
-
Understand how shrink marks affect surface aesthetics and quality. ↩
-
Learn why precision is vital for medical components. ↩
-
Explore how stress affects mechanical parts under load. ↩
-
Discover how deformation impacts product lifespan. ↩
-
Learn about maintaining toughness through microstructure integrity. ↩
-
Explores how microstructural arrangements influence mechanical properties. ↩
-
Learn about factors affecting precision in molded parts. ↩
-
Discover how microstructure optimization extends product life. ↩
-
Learn how simulation tools aid in optimizing lifter angles. ↩