Did you ever have problems with uneven wall thickness in your injection molded products? Many people have. This issue often troubles many. It is a common challenge. It affects the quality. It also causes defects.
Ensure uniform wall thickness in injection mold design by adjusting gate position and shape, using a balanced runner system, developing an effective cooling system, and optimizing mold cavity features. Each step is crucial for consistency.
I want to share what I have learned over the years about finding that difficult balance. Success begins with smart gate design. I remember setting a gate in the middle of a flat product for the first time. The melt filled the mold evenly. This simple option brought great results. A balanced runner system is also very important. It guarantees each cavity receives the same material, which I always check carefully during my design.
An effective cooling system is equally vital. I once placed cooling channels around a round product. I felt really happy to see it cool evenly. Mold cavity design is also essential. I always adjust for shrinkage to keep wall thickness consistent everywhere.
I am excited to explore these key design ideas further in this blog post. I will share useful insights to improve your injection molding projects.
Uniform wall thickness prevents defects in injection molded products.True
Consistent wall thickness is crucial for quality control and minimizing production defects in injection molding.
Gate location does not affect wall thickness in mold design.False
The position and type of gate significantly influence the uniformity of wall thickness during injection molding.
What Are the Key Factors Affecting Wall Thickness Uniformity?
Some molded products look perfect, while others show uneven thickness. Various factors probably affect wall thickness uniformity. These elements play a vital role in creating high-quality designs.
Key factors for wall thickness uniformity in injection molding are gate design, runner system design, cooling system design, and mold cavity design. These elements are crucial for maintaining consistent product quality.
Gate Design
Gate design is very important in molding. I remember learning about it for the first time. I was working on a flat product. I discovered that placing the gate in the center changed everything. This position allowed the melt to spread evenly, which is crucial for uniform wall thickness. For complex shapes, using multi-point gates really works wonders. They let the melt fill from multiple directions at once. It’s like a beautiful symphony where every note harmonizes the final product.
Different gate types offer unique benefits. Needle point gates create a powerful jet effect for thin-walled products requiring a high-quality finish. Submerged gates control flow direction well. They ensure consistency, eliminating those pesky inconsistencies.
Runner System Design
The runner system really needs proper design. I remember a project with a balanced runner design for a multi-cavity mold. Each cavity received the same amount of melt. This achieved wall thickness uniformity and it made my clients thrilled. It’s like a well-planned highway with smooth flowing lanes and no bottlenecks.
The smoothness of the runner surface is another crucial element. Polishing the surfaces minimized flow resistance, improving melt flow consistency significantly. It’s impressive how small details can result in big wins in product quality!
Cooling System Design
Cooling systems are often underappreciated heroes in this process. When I designed cooling channels for a cylindrical product, even distribution around the mold cavity brought significant improvements. It ensured uniform heat dissipation, preventing wall thickness differences from uneven cooling. Avoiding those discrepancies relies on investing time in the cooling layout.
Layered or localized intensive cooling designs are my favorite solutions for parts with varying wall thicknesses. They enable thick and thin areas to cool at synchronized rates, promoting uniformity. It’s like giving each section a tailored cooling treatment!
Mold Cavity Design
Finally, mold cavity design requires thinking outside the box sometimes. During a project, I had to adjust cavity dimensions to account for material shrinkage. Slightly enlarging thick-walled areas reduced shrinkage marks. The final product came out very uniform, much more than I originally anticipated.
Keeping cavity surfaces flat and smooth is crucial too. Fine machining prevents uneven wall thickness. High-precision CNC machining technology helps me maintain strict dimensional tolerances. This is something I take pride in when delivering quality products.
For detailed insights, explore this resource to understand injection molding processes and wall thickness considerations better. Mastering these elements probably transforms your designs from good to exceptional!
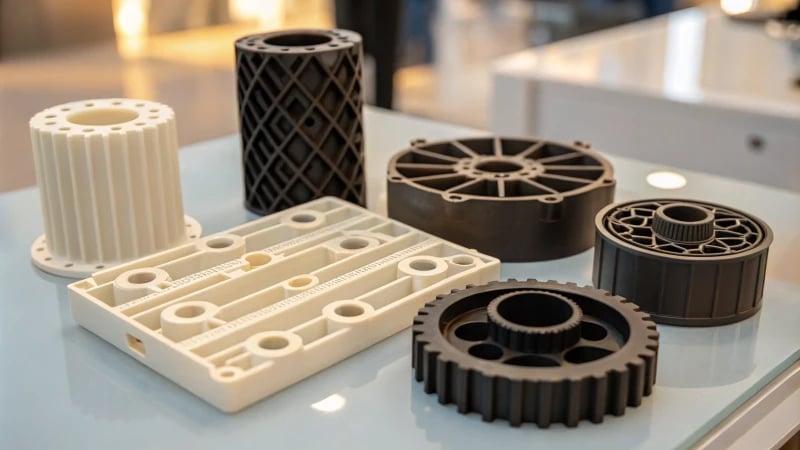
Main Content
Comprehending the significance of even wall thickness is very essential. It doesn’t only lead to high-quality molded products. I have personally experienced this in multiple projects. Each aspect we explore here has offered me countless lessons. I’m really excited to share these with you!
Gate Design
Gate design plays a crucial role in achieving uniform wall thickness in molded products.
Gate Location Selection: The positioning of the gate significantly impacts the melt flow. For example, central gates help in even filling for flat products, while multi-point gates enhance flow for complex shapes. This strategy ensures that the melt radiates evenly, reducing thickening due to path differences.
Gate Type Considerations: Different gates can yield varying effects on wall thickness. Needle point gates promote an efficient melt jet, ideal for high-quality, thin-walled products. Conversely, submerged gates can effectively control melt direction and mitigate wall thickness inconsistencies.
Runner System Design
The runner system must be carefully crafted to facilitate uniform melt distribution.
Balanced Runner Design: In multi-cavity molds, a balanced runner system is essential. It ensures each cavity receives equal amounts of melt, enhancing wall thickness uniformity. For instance, using runners of identical diameter and length connects multiple cavities effectively.
Runner Surface Treatment: A smooth runner surface minimizes flow resistance. Implementing polishing techniques can lead to a smoother surface that promotes even melt flow, which is crucial for achieving uniformity in wall thickness.
Cooling System Design
Cooling systems must ensure uniform cooling to maintain consistent wall thickness across products.
Uniform Cooling Layout: Designing cooling channels that distribute evenly around the mold cavity is fundamental. For instance, surrounding a cylindrical product with circular cooling channels ensures equal heat dissipation.
Cooling Design Considering Wall Thickness Difference: For parts with varying wall thicknesses, specific designs like layered cooling can be employed to synchronize cooling rates between thick and thin areas, ensuring uniformity throughout the product.
Mold Cavity Design
Proper mold cavity design is essential for compensating wall thickness variations during production.
Wall Thickness Compensation Design: This involves adjusting cavity dimensions to account for material shrinkage. For thick-walled areas prone to shrinkage marks, slightly enlarging these sections can yield a more uniform final product.
Cavity Surface Treatment: The quality of the cavity surface significantly influences wall thickness. Ensuring flat and smooth surfaces through fine machining can prevent unevenness in the final product’s dimensions. Using high-precision CNC machining technology helps in maintaining strict dimensional tolerances, thereby controlling wall thickness uniformity effectively.
For more detailed insights on these factors, consider exploring this resource1 to enhance your understanding of injection molding processes and wall thickness considerations.
Gate design significantly affects wall thickness uniformity.True
The selection of gate location and type influences melt flow, which is critical for achieving uniform wall thickness in molded products.
Cooling systems have no impact on wall thickness uniformity.False
Uniform cooling layouts are essential for maintaining consistent wall thickness across products during the molding process.
How Does Material Selection Influence Wall Thickness?
Have you ever thought about how the choice of materials decides the success of a design? In my experience as a product designer, I discovered that selecting materials involves more than just looks. It’s also about strength, function and lasting durability. Material choice really impacts wall thickness. Let’s explore how.
Material selection significantly impacts wall thickness in product design, influencing strength, durability, and manufacturing processes. Understanding these relationships allows designers to optimize for performance and cost.
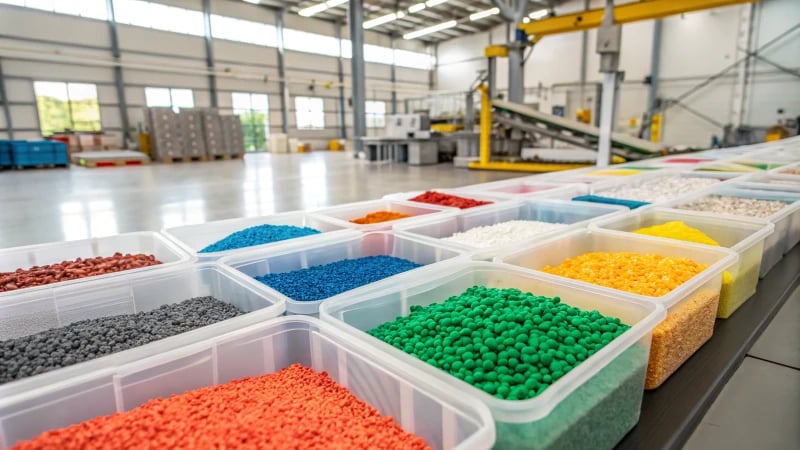
Understanding Material Properties
Material selection plays a critical role in determining wall thickness. The properties of materials, such as tensile strength, ductility, and thermal expansion, directly influence how thick or thin the walls of a product can be.
For instance, materials with high tensile strength can often allow for thinner walls without compromising structural integrity. Conversely, materials that are more brittle may require thicker walls to avoid failure under stress. This relationship highlights the importance of selecting the right material for the intended application.
The Impact of Manufacturing Processes
Different manufacturing processes also necessitate varying wall thicknesses based on material selection.
- Injection Molding: In injection molding, the choice of plastic can determine not only the wall thickness but also the uniformity of that thickness. For example, polycarbonate2 is often selected for products requiring durability but may need thicker walls compared to more flexible materials like polyethylene.
- Extrusion: Extruded products may have different wall thickness requirements based on the extrusion method and material viscosity.
Design Considerations in Wall Thickness
Designers must take into account the interaction between material properties and wall thickness during the design phase.
Material Type | Recommended Wall Thickness | Reason for Thickness |
---|---|---|
Metal | Thinner if weight isn’t a concern | Strong but heavy allows thinner walls |
Polyethylene | 1-2 mm | High ductility allows thinner walls |
ABS | 2-3 mm | Balanced strength and impact resistance |
Nylon | 1.5-2 mm | Good tensile strength, thinner possible |
Polycarbonate | 3-5 mm | High impact resistance requires more thickness |
Gate Design and Material Selection
The design of the gate in injection molding affects how material fills the mold cavity, which in turn influences wall thickness uniformity. The selection of material with appropriate flow properties is essential here.
For instance, using a needle point gate can help achieve better melt dispersion for materials that require thin walls, enhancing the overall aesthetic quality of the finished product.
Cooling System and Wall Thickness Control
Proper cooling design is vital in managing wall thickness uniformity across molded parts.
- Cooling Rate: The material’s thermal properties will dictate how quickly it cools. Thicker walls may retain heat longer, requiring careful design of cooling channels to prevent uneven contraction.
- Localized Cooling: For thicker sections of a product, localized intensive cooling can help maintain consistent wall thickness, particularly when using materials that experience significant shrinkage during cooling.
Conclusion: Material Selection as a Critical Factor
While we will not draw conclusions here, it’s clear that material selection is a fundamental factor in determining wall thickness in product design. Each decision influences not only manufacturability but also performance and cost-effectiveness in real-world applications.
High tensile strength materials allow for thinner walls.True
Materials with high tensile strength can support thinner wall designs without sacrificing structural integrity, optimizing material use and reducing weight.
Brittle materials require thinner walls to avoid failure.False
In contrast, brittle materials often necessitate thicker walls to prevent breakage under stress, highlighting the importance of material selection.
Why Is Mold Maintenance Important for Consistent Results?
Ever wondered why keeping molds in good condition is so crucial for stable production in injection molding? I will share some insights and experiences to highlight its importance.
Mold maintenance ensures consistent injection molding results by enhancing product quality, reducing repair costs, and minimizing downtime through improved mold efficiency.
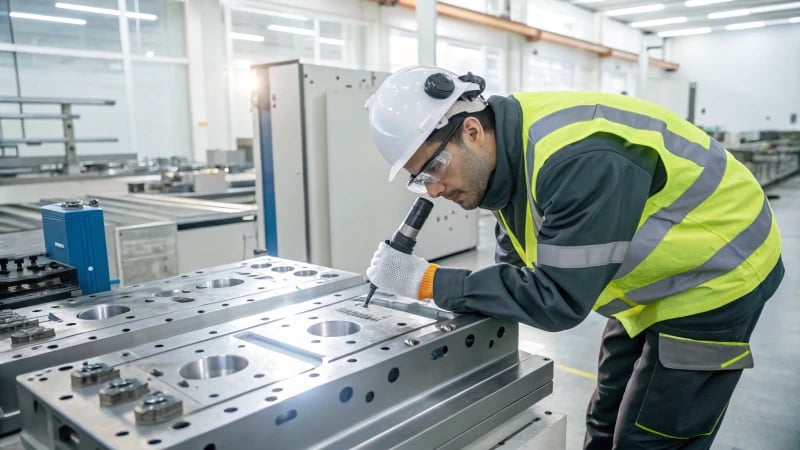
Understanding the Role of Mold Maintenance
Mold maintenance plays a central role in manufacturing, especially in injection molding. Precision and consistency are essential. Regular maintenance helps molds to perform properly, leading to high-quality products.
Neglected molds can create problems like uneven wall thickness and faulty parts. I once witnessed a batch of products fail quality checks due to a poorly maintained mold. It was frustrating. This experience taught me the significance of proper gate design. The gate’s placement strongly impacts the evenness of plastic distribution in the mold cavity. For flat molded items, a central gate allows plastic to spread evenly, minimizing wall thickness variations.
By maintaining gates and runners, manufacturers can reduce variations in wall thickness that may lead to product failures.
Importance of Runner System Maintenance
The runner system design is also crucial. A balanced runner design is key when dealing with multi-cavity molds. I recall designing a mold for a small plastic part where each cavity had equal-size runners. This precision ensured each cavity received the same amount of plastic, achieving uniform wall thickness.
Common runner issues include uneven melting and flow problems. Here’s a table showing the effects of poor runner maintenance:
Issue | Consequence |
---|---|
Clogged runners | Uneven melt distribution |
Worn surfaces | Increased resistance to melt flow |
Misalignment | Inconsistent wall thickness |
Clean and polished runner surfaces reduce flow resistance significantly, enhancing mold performance.
Cooling System Effectiveness
Over the years, I learned about cooling system effectiveness. A uniform cooling layout helps maintain consistent product quality. Blocked or poorly designed cooling channels create uneven cooling, affecting wall thickness.
Key practices for cooling system maintenance include:
- Conducting regular inspections for blockages
- Keeping cooling channels free of debris
- Adjusting layouts for new designs
Mold Cavity Design Considerations
Mold cavity design impacts final product quality significantly. Early in my career, I often overlooked this area until I faced shrinkage problems. Using a wall thickness compensation design helped handle shrinkage during cooling, greatly improving product uniformity.
High-precision CNC machining for cavity surfaces has been very useful as it maintains dimensional accuracy, ensuring our products meet customer expectations.
Conclusion on Ongoing Maintenance Practices
Although we have not concluded formally, ongoing mold maintenance clearly ensures consistent production quality. It improves product quality and reduces repair and downtime costs. Mold maintenance indeed brings many rewards. For more insights on best practices in mold maintenance, explore mold maintenance tips3.
Regular mold maintenance prevents product defects in manufacturing.True
Consistent upkeep of molds ensures optimal function, reducing risks of defects like uneven wall thickness and defective parts during production.
Clogged runners can lead to inconsistent product quality.True
When runner systems are blocked, it disrupts melt flow balance, resulting in variations in the final product's quality and consistency.
How Can Simulation Tools Aid in Design Optimization?
Engineers turn brilliant ideas into reality with precision. They use simulation tools for this task. These tools help visualize and test designs before production begins. Efficiency and accuracy in engineering really improve through these tools.
Simulation tools enhance design optimization by allowing engineers to test and evaluate virtual designs, improving precision, reducing costs, and accelerating development, ultimately leading to high-quality products.
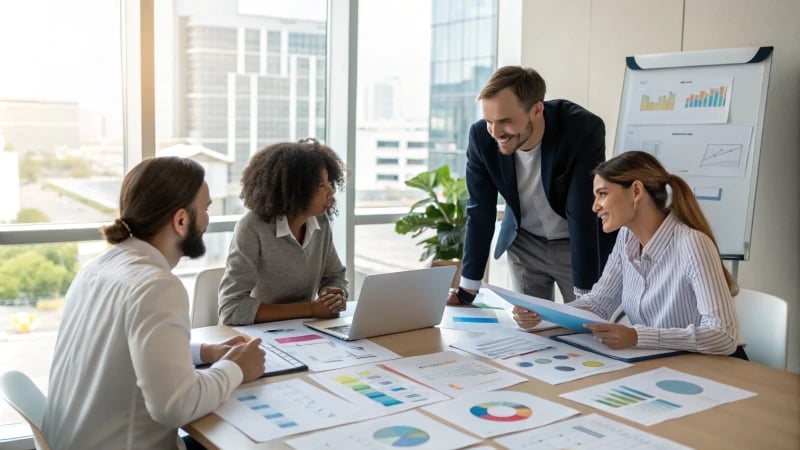
Understanding Simulation Tools in Design Optimization
Simulation tools have really changed how I look at design optimization in my job. These tools provide a great virtual space to create, test and improve designs before turning them into products. This saves time and reduces costs. Designers truly value this.
I once worked on a project that needed even wall thickness in a plastic part. With simulation software, I saw how different gate designs affected the plastic flow. This helped me choose the best gate spots and types for even filling. The design met our quality standards and wowed our clients. Witnessing such seamless designs is truly exciting.
Benefits of Simulation Tools
The advantages of simulation tools are many and each feels like a small win for designers like me.
Benefit | Description | Example |
---|---|---|
Cost Reduction | Minimizes expensive physical prototyping by allowing virtual testing of designs. | Reduced material waste in mold trials. |
Enhanced Accuracy | Increases precision in design adjustments through detailed simulations of various scenarios. | Accurate predictions of thermal profiles. |
Time Efficiency | Speeds up the design process by allowing rapid iterations and testing of multiple variables. | Quicker decision-making for product launches. |
Risk Mitigation | Identifies potential design flaws before production, reducing the risk of costly recalls. | Simulation predicts failure points in molds. |
Case Studies of Effective Use
In my career, I have watched various industries use simulation tools to improve their design processes. In automotive engineering, simulations refine vehicle shapes for better aerodynamics. I participated in a project using computational fluid dynamics (CFD) to cut drag. It was fascinating to watch small changes increase fuel efficiency.
In consumer electronics, designers often use simulation tools to perfect plastic parts. By simulating cooling systems, I achieve even cooling throughout the product. This is crucial for keeping both style and structure intact. Knowing our products are excellent drives my motivation.
Challenges and Considerations
Sure, it’s not always easy. There are challenges with simulation tools that I have faced:
- Complexity of Software: Advanced features seem daunting at first. Mastering them takes dedication; training has been important for me.
- Data Management: Handling large datasets from simulations can feel overwhelming; good data management is crucial.
- Integration with Existing Workflows: These tools need to fit seamlessly into our current design processes for the best use.
Despite these hurdles, simulation tools truly improve our design results. Curious about these challenges? Check out our resource about integrating simulation tools4. It might offer insights to improve your workflow!
Simulation tools reduce the need for physical prototypes.True
By enabling virtual testing, simulation tools minimize the reliance on costly physical prototypes, leading to significant cost savings in design processes.
All simulation software is easy to use without training.False
Most advanced simulation software requires specialized training due to its complexity, making it challenging for users without prior experience.
Conclusion
This blog post discusses strategies for achieving uniform wall thickness in injection molding through effective gate design, balanced runner systems, optimized cooling channels, and precise mold cavity adjustments.
-
Clicking this link will provide you with expert insights into injection molding processes, enhancing your understanding of wall thickness control. ↩
-
Explore how different materials impact wall thickness to enhance your design process and ensure structural integrity. ↩
-
Exploring this link provides practical insights into mold maintenance procedures that can enhance your manufacturing processes. ↩
-
This resource will help you understand best practices for integrating simulation tools into existing workflows. ↩