Ever seen a plastic part and wondered, "What happened?" I really have. Common issues in injection molding usually cause this.
Common flaws in injection molded items include flash, shrinkage, weld marks, flow marks, silver streaks, poor gloss and bubbles. Mold design errors, material problems and process misconfigurations cause these issues. They affect both looks and use.
I remember my first big project at the factory where I work. We spent weeks perfecting a design, only to face problems like flash and shrinkage. Flash means those thin flakes at the edges of a mold. It happens from high injection pressure or poor mold separation. Shrinkage leaves dents when plastic doesn’t fill the space as it cools.
Recognizing these problems was very important. It wasn’t just about seeing them. Understanding why they happened and finding solutions mattered. Each defect tells a story. It speaks of mold design, material choices and special details in processing. Looking into these details feels like solving a puzzle. It really improves both product quality and production efficiency.
Flash occurs due to excessive injection pressure.True
Excessive injection pressure causes material to seep out, creating flash.
Shrinkage is unrelated to mold design.False
Shrinkage can occur due to poor mold design affecting cooling rates.
How Does Flash Affect Product Quality?
Have you ever seen tiny flaws in your favorite devices? Flash probably changes them.
Flash impacts product quality by forming ugly extra pieces on parts. It reduces both appearance and function. This issue often stems from too much injection pressure or molds not aligning properly.
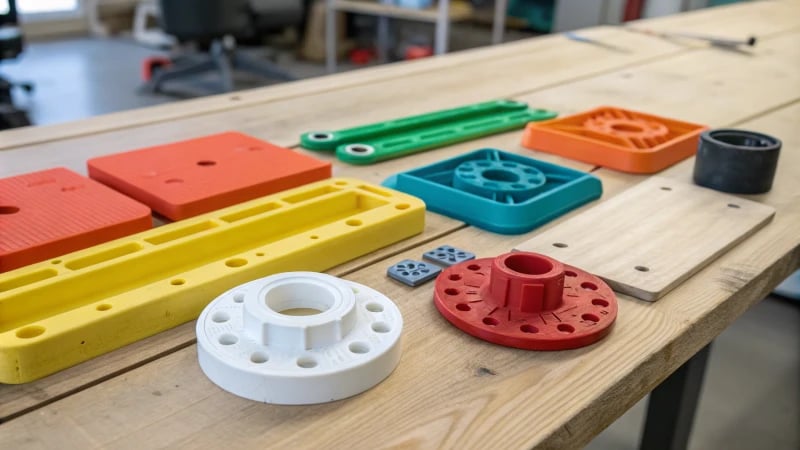
Flash in Injection Molding
Flash occurs when plastic leaks out during molding, creating thin edges. Imagine a puzzle piece with extra bits that won’t fit correctly. Overflow happens because of high pressure or misaligned molds. These unwanted artifacts1 not only affect the aesthetic appeal of the product but may also require additional post-processing to remove.
Causes of Flash
- High Injection Pressure: It’s like pouring too much water; extra pressure pushes plastic into unwanted places. When the injection pressure exceeds the clamping force, the plastic melt escapes into unwanted areas, forming flash.
- Mold Inaccuracies: Closing a door in a crooked frame is tough. Bad mold alignment has the same effect. A gap in the mold parting surface or poor insert matching can lead to flash.
- Material Fluidity: Some plastics flow too easily, creating trouble. Excessive fluidity of the plastic material can also contribute to flash.
Implications of Flash
Flash not only looks bad, but it also causes problems during assembly. Parts may not fit well together, which is really annoying, especially in electronics where details matter a lot.
Aspect | Impact |
---|---|
Aesthetics | Reduced visual appeal |
Functionality | Interference in assembly |
Cost | Increased post-processing |
Minimizing Flash
Stopping flash needs careful control of molding:
- Pressure Control: Maintain proper injection pressure to prevent leaks and ensure that injection pressure is within safe limits to prevent excess material overflow.
- Mold Design Precision: Regular checks help all parts fit perfectly. Accurate mold design and regular maintenance are vital to prevent gaps at parting lines.
- Material Selection: Choose materials that reduce unwanted flow with appropriate fluidity to reduce flash likelihood.
By understanding these details, companies probably improve product quality2 and ease manufacturing processes. For people like me, fixing flash is vital for making excellent products every time.
Dealing with flash problems transforms manufacturing results. It helps both producers and users by addressing such challenges effectively, leading to significant improvements in production quality3, benefiting both manufacturers and end-users alike.
Flash reduces aesthetic appeal of products.True
Flash creates visible excess material, detracting from product aesthetics.
High injection pressure prevents flash formation.False
Excessive injection pressure causes flash by forcing material into gaps.
Why Do Shrinkage Dents Occur in Injection Molding?
Shrinkage dents happen in injection molding. These dents change a perfect part into a tough problem. I recall the first time I faced them. I understood finding the root causes is key to fixing them.
Shrinkage dents in injection molding appear due to walls that are not evenly thick. Insufficient pressure during the process also contributes to the problem. Additionally, cooling is often not managed well. These factors prevent the plastic melt from filling thick areas properly as it cools. This results in dents.
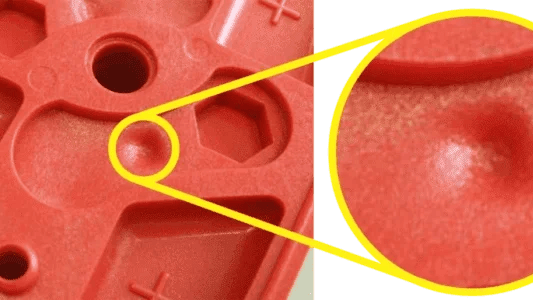
Reasons for Shrinkage Dents
In my early days of designing molds, facing shrinkage dents really confused me. Those small dips were unexpected. Learning about these defects was difficult, but I found out some important things.
1. Uneven Wall Thickness
I once designed a part with walls of different thicknesses. I thought it was clever. But thicker sections cooled more slowly, causing those annoying shrinkage dents. Lesson learned? Keep wall thickness the same during design to avoid this problem. Uniform thickness is key.
2. Not Enough Holding Pressure
I sometimes missed how crucial holding pressure was during cooling. Without enough pressure, my material didn’t fill thicker sections, leading to dents. Adjusting the pressure changed everything. Mold needs correct packing.
3. Managing Cooling Time
I realized rushing cooling causes part warping. If the part is ejected too soon, it might not be solid. Finding the right cooling time is crucial for strong parts. Timing is essential.
Common Injection Molding Defects Due to Shrinkage
Defect Type | Description | Cause |
---|---|---|
Flash (overflow) | Excess plastic forms at mold edges | High injection pressure or poor mold design |
Weld marks | Linear marks with color variance | Improper gate position or poor venting |
Flow marks | Wave-like surface marks | Uneven flow speed or low melt temperature |
My experiences with different molding defects were enlightening. Each defect taught me individually that fixing one defect didn’t solve another.
For example, changing injection speed4 worked for weld marks but didn’t clear shrinkage issues.
Choosing Materials
Picking the right material is also vital. Some plastics shrink more because they flow easily. Knowing material properties5 helped me a lot in designs.
Trying new materials or adding elements really decreases shrinkage chances. This forward-thinking can result in improved product success6. I always aim for this in each project.
Uneven wall thickness causes shrinkage dents.True
Thick sections cool slower, leading to insufficient filling and dents.
High injection pressure prevents shrinkage dents.False
High pressure can cause flash, not prevent shrinkage dents.
Why Do Weld Marks Appear on Molded Products?
Think back to when you poured your heart into designing the ideal molded product. Those annoying weld marks probably stared back at you.
Weld marks happen when plastic melt divides and comes back together inside the mold. This commonly occurs because of poor gate design, not enough vents or wrong injection settings.
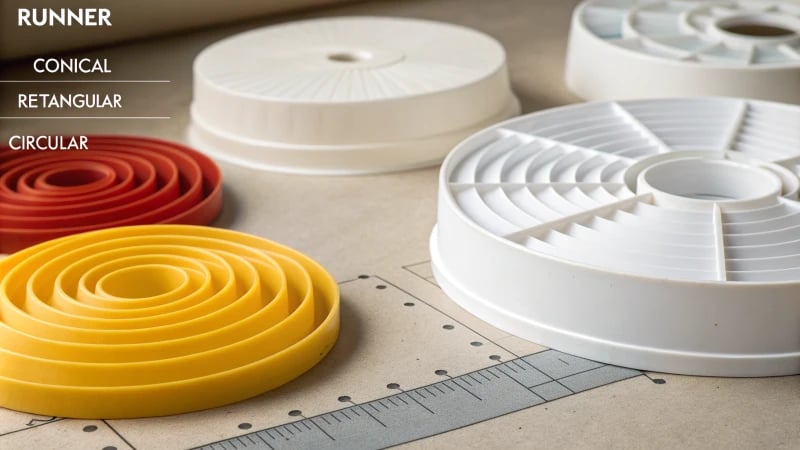
Understanding Weld Marks
I remember my first encounter with weld marks vividly. It was like a ghost had drawn a faint line across my otherwise perfect creation. These marks show up as lines on molded products, caused by the separation and joining of the plastic melt. This division and merging create lines that stand out or shine differently from the rest of the item.
Causes of Weld Marks
1. Gate Design:
I once made a part with a gate in the wrong place, which pushed the melt to split and come together, leaving behind weld marks. Proper gate design7 ensures uniform flow and prevents this issue.
2. Mold Venting:
Poor venting traps air at flow points and stops full fusion of molecular chains. I learned this the hard way when one of my designs failed quality tests. Better venting can remove these annoying lines by allowing complete air evacuation.
3. Injection Molding Parameters:
Changing settings like melt temperature and injection speed is key. I found that low temperatures or speeds could result in poor fusion, causing weld marks. Adjustments must be made based on material characteristics.
Other Contributing Factors
Factor | Description |
---|---|
Material Flow | Inadequate flow causes partial fusion. |
Part Geometry | Complex shapes increase likelihood of weld marks. |
Material Type | Some plastics are more prone to weld issues. |
Mitigating Weld Marks
To reduce weld marks, effective design and process management really help:
- Improved Gate Positioning8: Correct gate placement reduces split flows.
- Better Venting: Allows complete removal of air.
- Adjusting Settings: Find the right temperature and speed for each material.
Using these strategies, I probably increase product quality and reduce weld marks, allowing me to meet both the aesthetic and functional standards our industry expects.
Improper gate position causes weld marks.True
Improper gate design forces melt to split and rejoin, creating marks.
All plastics are equally prone to weld marks.False
Different plastics have varying susceptibilities to weld issues.
How Can I Minimize Flow Marks?
Have you ever spent hours creating the ideal plastic product, only to face ugly flow marks? Yes, me too. Let’s solve this problem together and keep our designs perfect.
I reduce flow marks in injection molding by adjusting the melt flow. This involves fine-tuning the temperature, speed of injection and finish of the mold surface. These changes help achieve a smoother and more appealing final product. A smoother and more appealing product is the result.
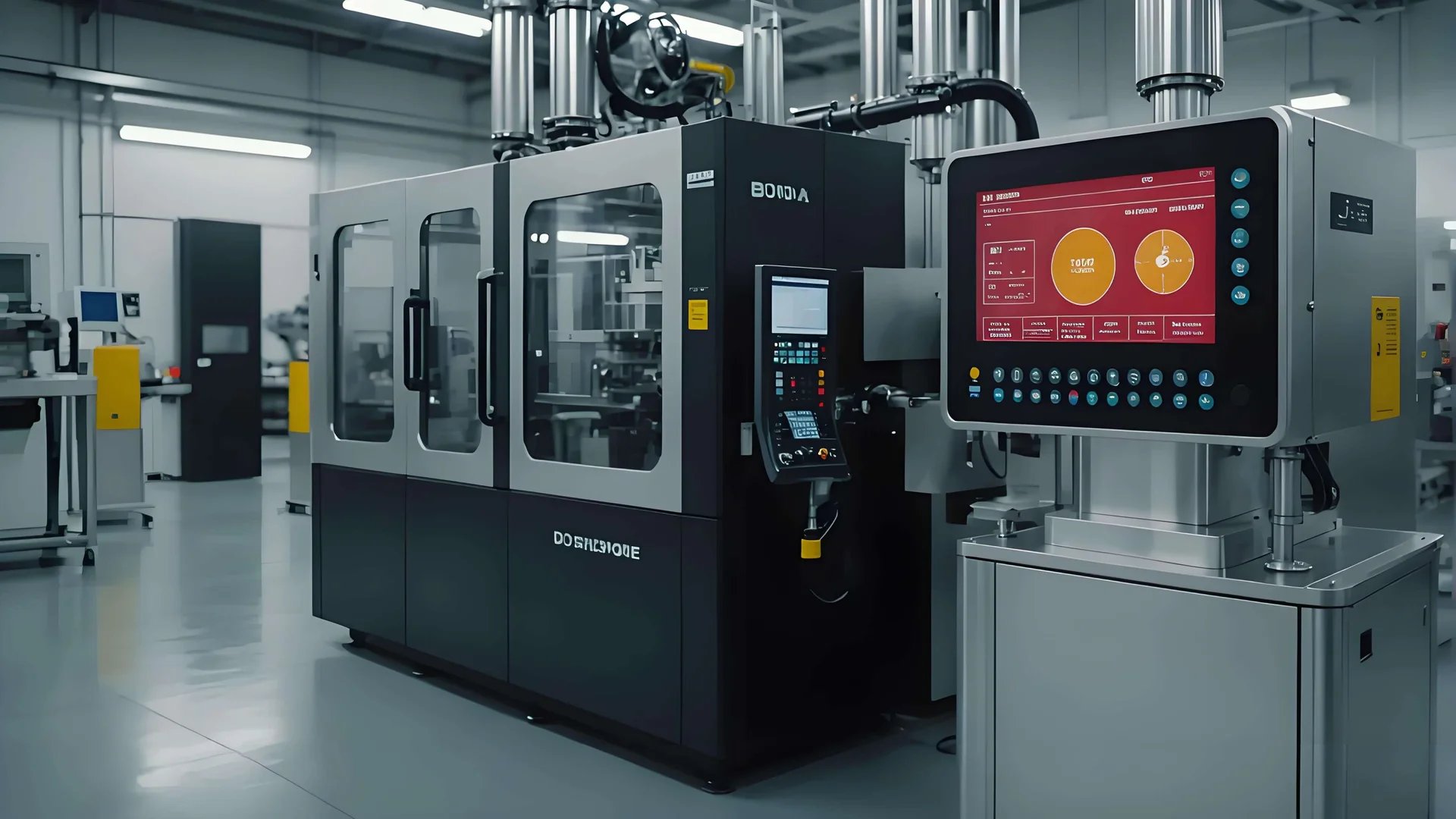
Understanding Flow Marks
I encountered flow marks for the first time on a project. A large flat piece had waves and stripes everywhere. These marks appear because the melt flow is not even, detracting from both the appearance and function of the products.
Optimizing Process Parameters
Getting the process parameters right is important to minimize flow marks:
- Melt Temperature: Slightly increasing the melt temperature improves fluidity. This must be balanced to avoid damaging the material.
- Injection Speed: Steady injection speed keeps the melt flow smooth.
Parameter | Recommended Action |
---|---|
Melt Temperature | Increase for better fluidity |
Injection Speed | Optimize for consistent flow |
Improving Mold Design
Better mold design is another trick I use to reduce flow marks:
- Gate Design: Correct gate placement distributes the melt evenly. This has changed things for me.
- Surface Finish: Polishing the mold surface reduces friction, leading to a smoother flow.
Learn more about effective mold design techniques9 to combat flow marks.
Addressing Material Properties
The type of plastic used has a big effect on flow characteristics:
- Plastic Type: Choosing materials with good flow properties prevents many problems.
- Additives: Sometimes, additives improve fluidity and decrease resistance.
Explore material selection strategies10 for better molding outcomes.
Regular Maintenance
Molds must stay in good condition. This is something I always do:
- Cleaning: Regular cleaning prevents buildup, which can disrupt flow.
- Inspection: Periodic checks catch wear and tear early before they cause trouble.
Adopt a mold maintenance checklist11 to keep your equipment in top condition.
Understanding these root causes—from injection parameters12 to mold conditions—helps me find precise solutions. This approach has reduced defects for me significantly, leading to superior products every time.
Increasing melt temperature reduces flow marks.True
Higher melt temperatures improve fluidity, minimizing uneven flow.
Uneven gate design increases flow marks.True
Improper gate placement leads to uneven distribution of plastic melt.
How Can I Fix Silver Streaks in Transparent Plastics?
Those annoying silver streaks in clear plastic products often catch the eye. They aren’t just ugly; they might also mean poor quality. The problem needs a closer look. It’s time to tackle it properly.
Silver lines in clear plastics happen due to moisture or gases when molding. One solution is to dry the materials first. Another is to adjust the temperature settings. Also, vents in the mold need to work well.
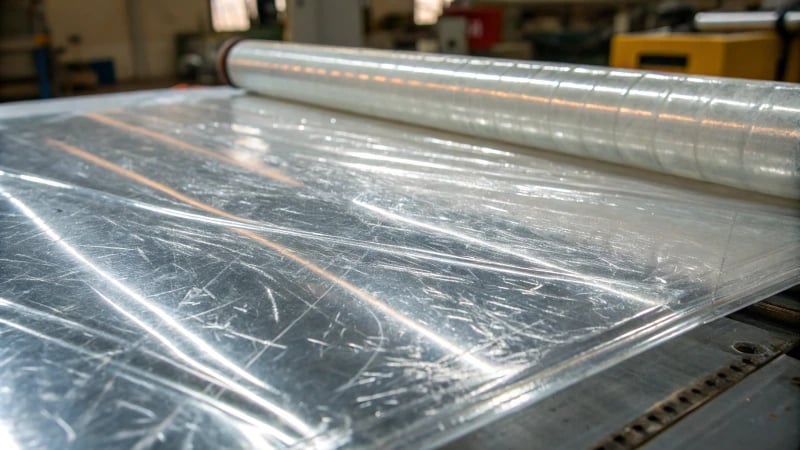
Understanding the Causes
Silver streaks occur when moisture or volatile substances in the plastic material form gas during the injection molding process. These gases create silver or bright lines on the product surface as the melt flows, particularly noticeable in transparent plastics.
Problem | Cause |
---|---|
Silver Streaks | Moisture or volatiles in plastic form gas during injection, creating visible lines |
Pre-drying Plastic Materials
Before injection molding, plastic materials should be thoroughly dried to eliminate moisture content. This step is crucial as moisture in materials like ABS and polycarbonate can cause degradation and silver streaks. Implementing moisture control measures13 can significantly reduce this issue.
Optimizing Processing Parameters
Adjusting processing parameters is another effective strategy:
- Temperature: Ensure the barrel temperature is not excessively high to avoid material decomposition. Monitor the mold temperature as well to maintain consistent flow.
- Injection Speed: Slow down the injection speed to allow gases to escape efficiently.
Enhancing Mold Design
Proper mold design is critical in preventing silver streaks:
- Mold Venting: Ensure the mold has adequate venting to allow trapped air to escape. Inadequate venting leads to increased pressure and potential gas formation.
- Gate Design: Optimize gate locations to facilitate uniform flow and minimize gas entrapment. Explore advanced mold design techniques14 for complex designs.
By understanding these solutions, manufacturers can enhance product quality and minimize defects, ensuring transparent plastic components meet both aesthetic and functional standards.
Pre-drying plastic materials prevents silver streaks.True
Pre-drying removes moisture that causes gas formation during molding.
High barrel temperature reduces silver streaks in plastics.False
High temperatures can cause decomposition, increasing gas formation.
Conclusion
This article explores common defects in injection molded products, including flash, shrinkage, weld marks, flow marks, silver streaks, and their causes and solutions to improve product quality.
-
Learn more about why flash occurs and strategies to prevent it in injection molding processes. ↩
-
Explore how flash impacts overall product quality and strategies for improvement. ↩
-
Discover various methods for improving production quality by managing defects like flash. ↩
-
Learn about adjusting injection speed to minimize weld marks, improving product quality through better process control. ↩
-
Discover material properties influencing shrinkage to select suitable plastics for your injection molding projects. ↩
-
Find out how choosing the right material can enhance product performance and reduce common defects like shrinkage. ↩
-
Optimizing gate positioning can reduce defects, enhancing the structural and aesthetic quality of your products. ↩
-
Understanding mold venting techniques can help you eliminate air entrapment, improving product quality. ↩
-
Discover how proper gate design and mold polishing can significantly minimize flow marks. ↩
-
Find materials with optimal flow properties to enhance molding efficiency. ↩
-
Implement a maintenance routine to ensure consistent mold performance. ↩
-
Learn which injection settings most effectively prevent flow mark formation. ↩
-
Exploring moisture control techniques can help prevent defects like silver streaks by ensuring optimal material conditions. ↩
-
Advanced mold design techniques provide insights into optimizing gate placement and venting to minimize defects like silver streaks. ↩