Have you ever wondered how the seemingly small details of injection molding can make or break a product?
Injection speed refers to the rate at which molten material fills the mold cavity, while injection pressure is the force applied to push this material into the mold. Both are vital for ensuring optimal product quality and production efficiency.
But understanding these definitions is just the start! Let’s dive deeper into their real-world implications on your product quality and production effectiveness.
Injection speed affects product surface quality.True
Proper injection speed ensures smoother surfaces by reducing defects.
How Does Injection Speed Affect Product Quality?
Injection speed significantly influences both the aesthetic and structural integrity of molded products. Getting it right ensures smoother surfaces and stronger internal structures.
Injection speed, the rate molten material enters the mold, affects product surface smoothness and internal stress. Optimal speed prevents defects like flow marks and ensures dimensional stability, while excessively fast speeds can reduce mechanical properties.
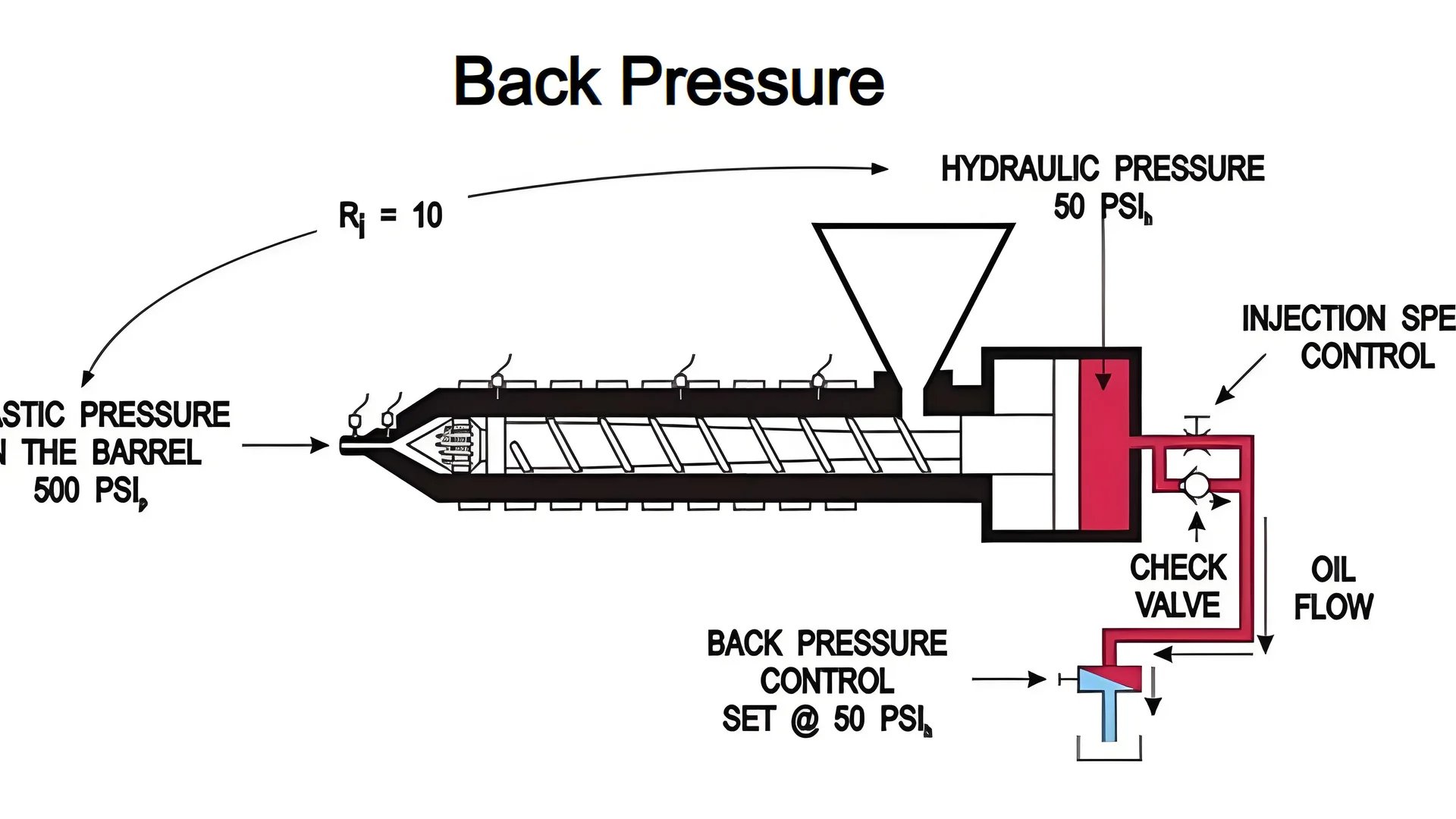
Understanding Injection Speed
Injection speed refers to how quickly the molten material is injected into the mold cavity. It’s a crucial parameter in injection molding1 because it directly impacts the final product’s quality.
When the injection speed is increased appropriately, the molten material fills the mold more swiftly, resulting in a smoother surface finish and fewer defects such as flow marks or weld lines. This is because faster filling ensures that the material flows evenly throughout the mold, reducing issues caused by uneven cooling.
Impact on Surface Quality
A well-optimized injection speed can significantly enhance surface quality. For instance, increasing the speed reduces the chance of flow marks and weld lines. These are common defects that occur when different flow fronts of molten material meet and do not merge properly, often due to excessive local cooling.
However, an excessively high injection speed can lead to other problems. It might cause increased internal stress within the product, which can adversely affect its mechanical properties and dimensional stability.
Internal Structure and Stress
The internal structure of a molded product is sensitive to injection speed adjustments. If the speed is too high, it may introduce higher internal stresses, weakening the product’s mechanical properties. Conversely, if it’s too slow, there could be issues like short shots or shrinkage holes, which compromise the structural integrity.
To illustrate:
Injection Speed | Potential Issues |
---|---|
Too High | Increased stress, reduced mechanical properties |
Optimal | Smooth surface, balanced stress levels |
Too Low | Short shots, shrinkage holes |
Production Efficiency vs. Equipment Wear
While a higher injection speed can shorten the molding cycle, improving production efficiency, it also increases wear on the mold and machinery. This trade-off must be carefully managed to balance production goals with equipment longevity.
Molds and machines subjected to high speeds may require more frequent maintenance or replacement, leading to higher operational costs. Therefore, optimizing injection speed is not only about product quality but also about managing resources efficiently.
In conclusion, while injection speed is pivotal in defining product quality, achieving the right balance requires a nuanced understanding of how it interacts with other factors like mold design and material properties.
Optimal injection speed enhances surface smoothness.True
Proper speed ensures even material flow, reducing surface defects.
Excessive injection speed improves mechanical properties.False
Too fast speeds increase internal stress, weakening product strength.
What Is the Role of Injection Pressure in Molding Efficiency?
Understanding injection pressure’s role in molding efficiency is pivotal for improving manufacturing outcomes and product quality.
Injection pressure ensures molten material fully fills the mold, affecting product accuracy, quality, and production efficiency. Proper management can enhance output while safeguarding equipment.
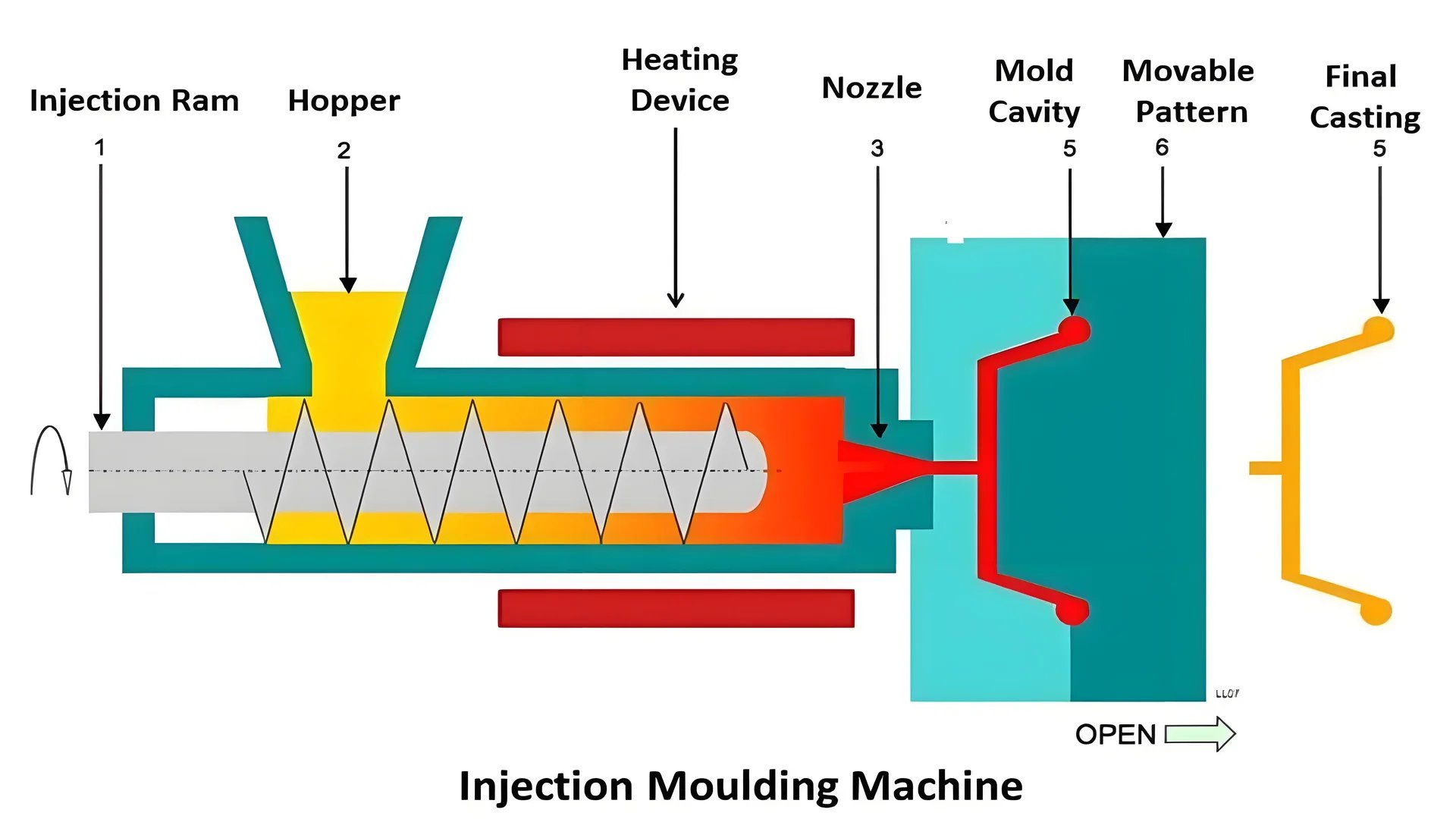
Understanding Injection Pressure in Molding
Injection pressure is a critical parameter that ensures the molten material fills the mold cavity completely, avoiding defects such as short shots or insufficient material filling. In essence, it represents the force exerted by the injection molding machine’s screw on the molten material, usually measured in megapascals (MPa).
Impact on Product Quality
- Filling Capacity: A higher injection pressure is essential for ensuring complex shapes and thin-walled products are adequately filled. This helps in avoiding issues like short shots and incomplete filling.
- Dimensional Accuracy: The injection pressure directly influences the product’s dimensional precision. While high pressure might lead to overfilling, causing oversized products, insufficient pressure might result in undersized parts.
Effect on Production Efficiency
- By ensuring that the mold cavity is filled correctly and quickly, appropriate injection pressure can significantly improve production efficiency. This parameter reduces cycle times and enhances output rates.
Influence on Mold Life
- However, it is crucial to balance injection pressure, as excessive pressure can lead to increased wear and stress on molds, particularly at weak points like gates and parting surfaces. This can shorten mold life significantly.
Impact Area | High Injection Pressure | Low Injection Pressure |
---|---|---|
Product Quality | Potential overfilling; may cause dimensional inaccuracies | Risk of short shots; inadequate filling of mold cavity |
Production Efficiency | Faster cycle times; improved output | Longer cycle times; potential for increased waste |
Mold Longevity | Increased wear and stress on mold | Reduced wear but may lead to quality issues |
Managing Injection Pressure for Optimal Results
Adjusting injection pressure effectively requires understanding its interplay with other factors such as screw speed, diameter, and melt temperature. For instance, increasing melt temperature can lower melt viscosity, thereby reducing the required injection pressure.
Moreover, leveraging the injection molding machine’s adjustable parameters allows for precision tuning to meet specific product requirements. Balancing these parameters is key to optimizing both product quality and mold longevity.
To delve deeper into how these parameters can be adjusted effectively for optimal results, explore our in-depth guide on injection parameters2. For a broader perspective on challenges faced during adjustments, consider reading common challenges in molding3.
High injection pressure can cause oversized products.True
Excessive pressure leads to overfilling, causing dimensional inaccuracies.
Low injection pressure reduces mold wear significantly.True
Lower pressure results in less stress on molds, extending their life.
How Can Injection Parameters Be Optimized for Better Results?
Optimizing injection parameters is crucial for enhancing product quality and production efficiency in molding processes. Learn how to achieve the best results.
To optimize injection parameters, adjust injection speed and pressure based on product requirements, mold design, and material properties. This ensures high-quality output and efficient production.
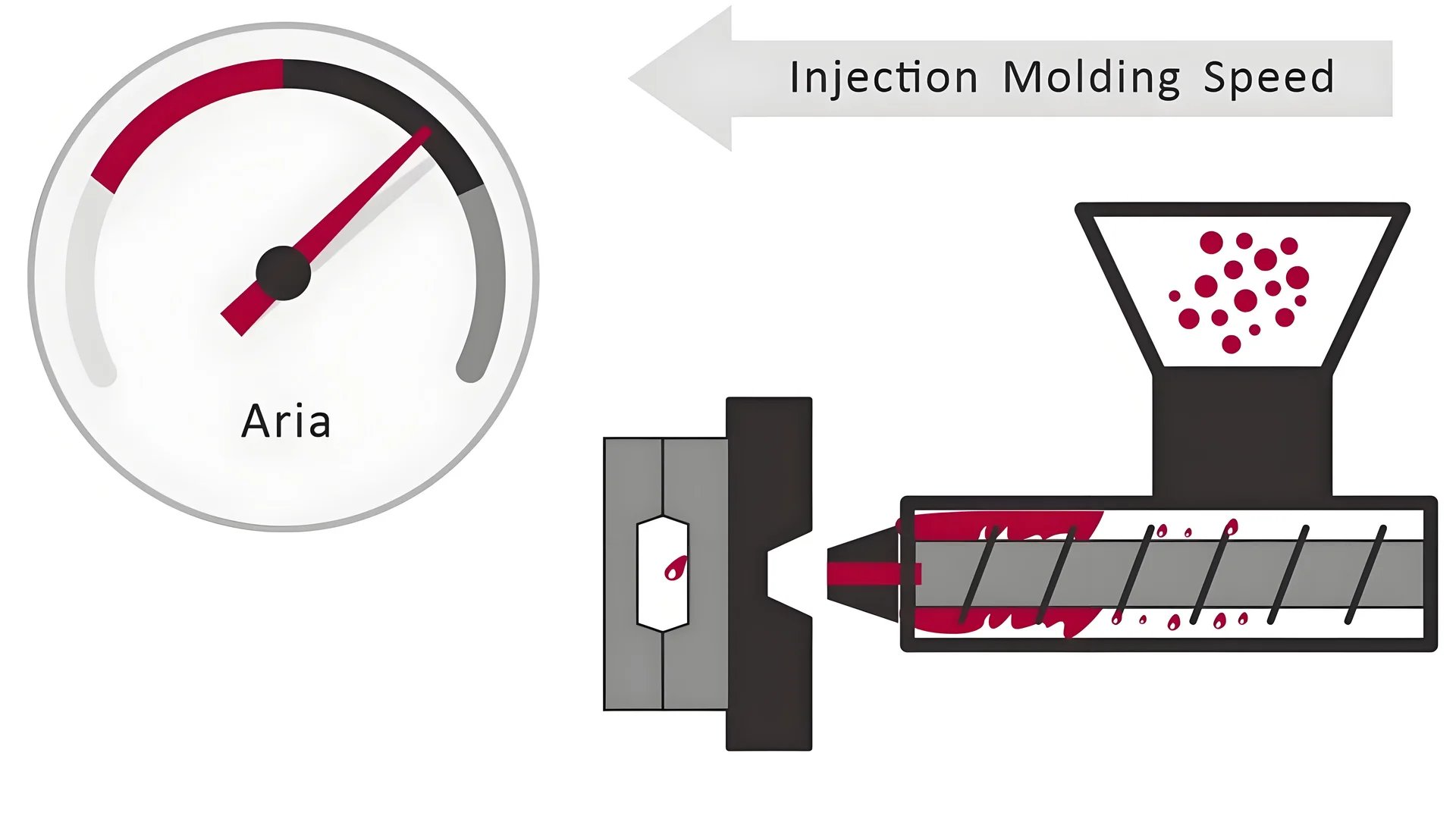
Understanding the Importance of Optimization
In the realm of injection molding, optimizing parameters like injection speed and pressure is pivotal for achieving superior product outcomes. These parameters influence not only the quality but also the efficiency of the production process.
Balancing Injection Speed
Injection speed significantly affects both the surface and internal quality of molded products. A well-adjusted speed ensures smoother surfaces and minimizes defects such as flow marks. However, it’s crucial to strike a balance; excessive speed can lead to internal stresses and reduced mechanical properties. Adjusting the injection speed can also enhance production efficiency by shortening the cycle time.
Key Factors to Consider:
- Material Flow: Adjusting the speed helps control the rate at which molten material fills the mold, impacting surface texture and internal integrity.
- Cycle Time: Faster speeds can reduce cycle times but may increase wear on machinery.
Fine-tuning Injection Pressure
Injection pressure determines how effectively molten material fills the mold cavity. Proper adjustment ensures complete filling, especially for complex or thin-walled designs. However, overly high pressure can lead to oversized products and increased mold wear.
Factors Influencing Pressure Optimization:
- Material Viscosity: Higher melt temperatures reduce viscosity, allowing lower pressure settings.
- Product Complexity: Complex shapes require precise pressure adjustments to avoid defects.
Techniques for Parameter Adjustment
- Using Multi-Stage Settings: Modern machines allow for multi-stage speed and pressure settings, enabling gradual adjustments during different phases of injection.
- Mold Design Modifications: Altering gate sizes or locations can optimize flow patterns, impacting both speed and pressure.
Practical Insights for Effective Optimization
Achieving optimal results involves a nuanced understanding of how these parameters interact with various factors such as material properties and mold design. Regularly reviewing and adjusting these settings based on feedback and performance data is essential.
Consider engaging with resources like Injection Molding Optimization Techniques4 to gain deeper insights into practical approaches for parameter adjustments. This will equip you with strategies to enhance both product quality and operational efficiency.
Injection speed affects product surface quality.True
Adjusting injection speed can smooth surfaces and minimize defects.
High injection pressure reduces mold wear.False
Excessive pressure increases mold wear and can oversize products.
What Are Common Challenges When Adjusting Injection Speed and Pressure?
Adjusting injection speed and pressure in molding processes presents unique challenges that can impact product quality and efficiency.
Common challenges include balancing product quality with production efficiency, managing mold wear, and ensuring dimensional accuracy. Improper adjustments can lead to defects, increased maintenance costs, and compromised mechanical properties.
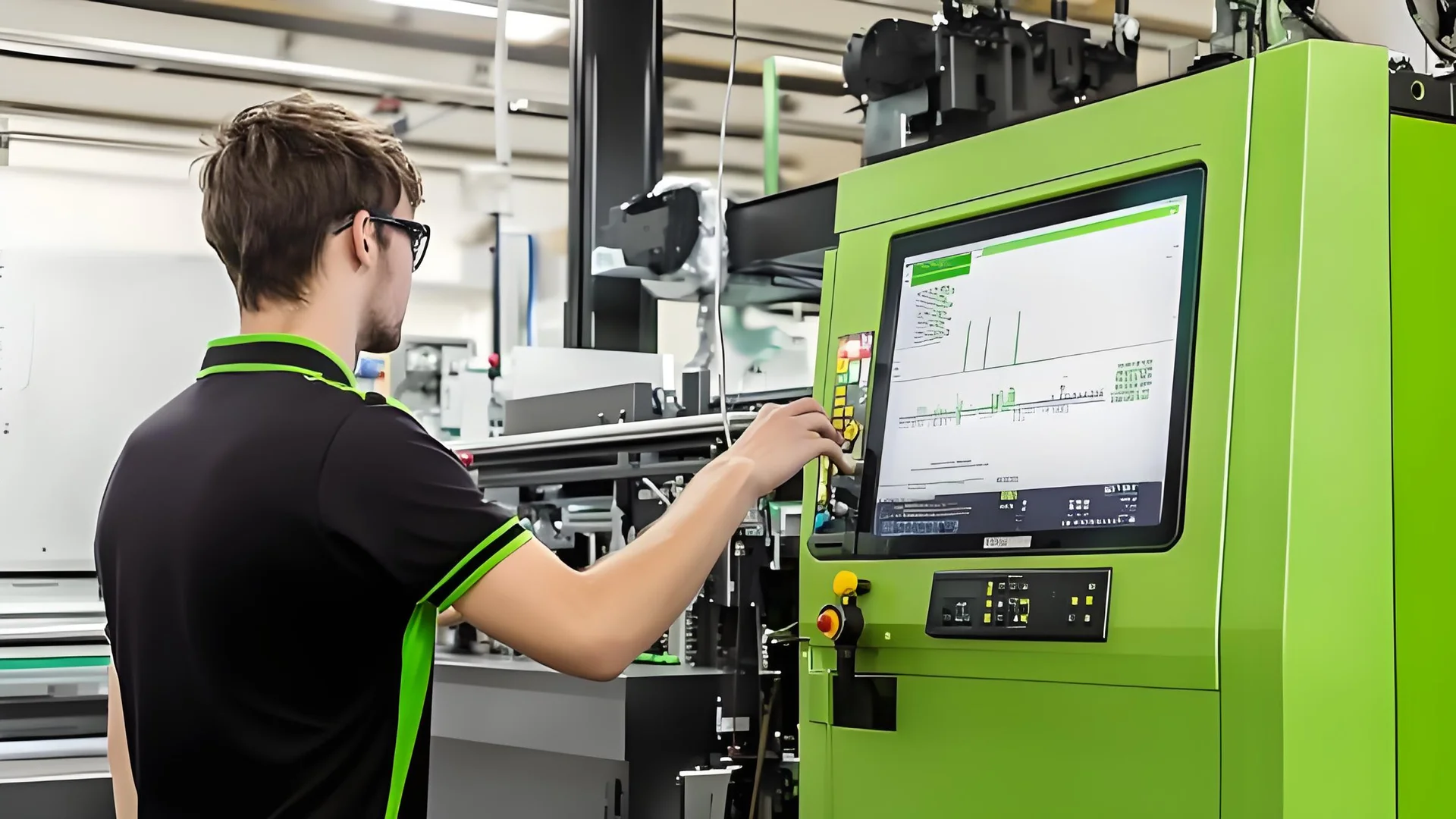
Balancing Product Quality and Production Efficiency
One of the primary challenges is striking the right balance between product quality5 and production efficiency. Increasing injection speed can boost efficiency but may compromise the internal structure of the product. Conversely, slower speeds improve internal strength but extend production times.
Managing Mold Wear
High injection speeds and pressures can lead to excessive mold wear. This is particularly problematic at the gate and parting surfaces, where the mold is most vulnerable. To mitigate this, operators must carefully monitor wear patterns and adjust parameters accordingly to extend mold life.
Ensuring Dimensional Accuracy
Achieving precise dimensions is crucial for product functionality. High injection pressure ensures complete cavity filling but can also cause overfilling, resulting in oversized products. On the other hand, low pressures might lead to incomplete filling. Adjusting injection pressure6 requires careful calibration to maintain dimensional accuracy without compromising mold integrity.
Mitigating Stress and Defects
Rapid filling from high injection speeds can introduce stress within the product, potentially leading to defects like warping or cracking. Adjustments must consider the thermal and mechanical stress levels to avoid these issues. By optimizing parameters and conducting regular quality checks, these risks can be minimized.
Adapting to Different Product Requirements
Every product has unique specifications that demand tailored injection parameters. Factors such as material type, product complexity, and wall thickness dictate the optimal settings for speed and pressure. Operators need to adapt quickly to these changing requirements to maintain consistent quality across different production runs.
Understanding these challenges is key to mastering the art of injection molding. By employing a strategic approach to parameter adjustments, manufacturers can enhance both product quality and production efficiency.
High injection speeds increase mold wear.True
Rapid speeds cause friction and stress, leading to faster mold deterioration.
Low injection pressure always ensures complete cavity filling.False
Low pressure might result in incomplete filling, affecting product dimensions.
Conclusion
In mastering injection speed and pressure adjustments, I can significantly enhance both product quality and operational efficiency.
-
Learn more about the fundamental process of injection molding.: Injection molding is a complex manufacturing process. Using a specialized hydraulic or electric machine, the process melts, injects and sets … ↩
-
Discover strategies for fine-tuning injection parameters effectively.: The 8 Key Parameters in Injection Molding Process Optimization to Avoid Defects · 1. Temperature Control: · 2. Injection Speed: · 3. Cooling … ↩
-
Identify typical issues encountered when modifying molding settings.: We’ve created a cheat sheet with the most common injection molding problems you might encounter and how to fix them. ↩
-
Explore advanced strategies to enhance injection molding efficiency and product quality.: 1. Temperature Control: · 2. Injection Speed: · 3. Cooling Time: · 4. Plastic Material Selection: · 5. Screw Speed and Back Pressure: · 6. Injection … ↩
-
Explores how speed variations impact surface and internal quality.: Injection speed: The injection speed should be set reasonably, otherwise it will affect the product quality. If the injection speed is too … ↩
-
Discusses the importance of pressure for precise product dimensions.: Generally, at the same injection speed, higher injection pressure improves the plastic’s flow capability, enhancing the dimensional precision … ↩