Do you often think about whether nitriding your molds is a good use of money?
Nitriding molds is expensive. Equipment, gas, energy and labor all add to the cost. Initial expenses are high. Batch processing, however, probably reduces the cost for each unit. This method really improves mold life and quality. It is a wise investment.
I remember when I first thought about nitriding for my molds. The high initial price surprised me. But looking closer at the details showed how early expenses could save money later. The biggest cost was the equipment. Special furnaces cost tens of thousands. Understanding batch processing savings changed my view. Batch processing spreads gas and energy costs over many molds. This really lowers the cost for each mold. It was like buying in bulk at a warehouse store. You pay more at first, but it’s really worth it over time.
Nitriding furnace maintenance costs are negligible.False
Maintenance involves regular inspections, repairs, and replacements, incurring costs.
Batch processing can reduce nitriding cost per mold.True
Spreading fixed costs over multiple molds lowers the cost per unit.
What are the Key Equipment Costs in Nitriding?
Exploring the details of nitriding expenses is often surprising. This is especially true during crucial manufacturing choices.
Key equipment costs in nitriding involve buying, keeping and considering the wear and tear of special furnaces. These activities really influence your total expenses. The furnaces have a big impact.
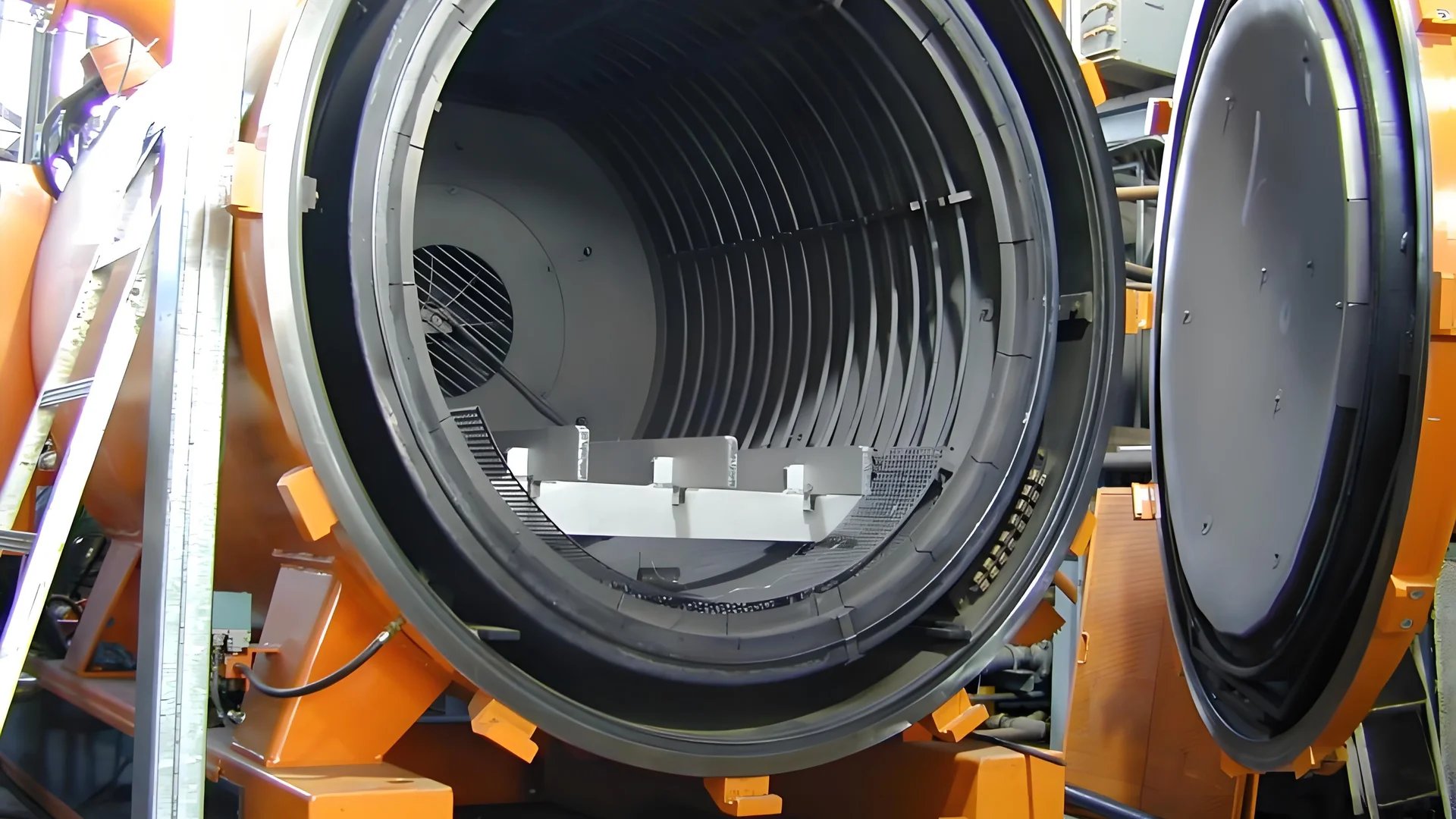
Equipment Acquisition Costs
When I thought about adding nitriding to my work, the high price took me by surprise. Buying special nitriding furnaces1 felt like getting a lot of fancy cars. Prices are all over the place – small machines might cost a few thousand, while big and powerful ones shoot up to tens of thousands. For a small business like mine, these costs are not tiny; they are very big choices that affect future growth.
Equipment Maintenance Costs
I remember when our furnace first needed a fix. It was like seeing an important racehorse needing a doctor. Regular repairs are a must if you want these machines to work well. Tasks like changing heating parts and adjusting sensors seem like endless challenges. There is always the thought of the machine losing value over time. It’s like saving for old age, but for your machines.
Depreciation Considerations
Depreciation is not just for accountants; it’s a cold fact on your money books. As the value of these furnaces drops over time, it changes everything—it affects plans and budget. Knowing how depreciation affects cost is now easy for me. This knowledge really helps me choose wisely where to put resources.
Looking into these equipment costs is really important in judging if nitriding fits my business. By balancing initial spending with long-term gains like stronger molds, I can choose wisely. These choices should match my bigger plans for production.
Nitriding furnaces cost tens of thousands of dollars.True
High-performance nitriding furnaces can reach tens of thousands.
Batch processing increases nitriding cost per mold.False
Batch processing reduces the nitriding cost per unit mold.
How Do Gas and Energy Impact Nitriding Costs?
Have you ever thought about how much of your nitriding cost is due to gas and energy? It’s probably more than you realize!
Gas and energy strongly affect nitriding costs. Gas nitriding uses ammonia or similar gases. Prices vary by location. Energy costs come from the electricity needed to heat furnaces. These costs depend on temperature and time settings.
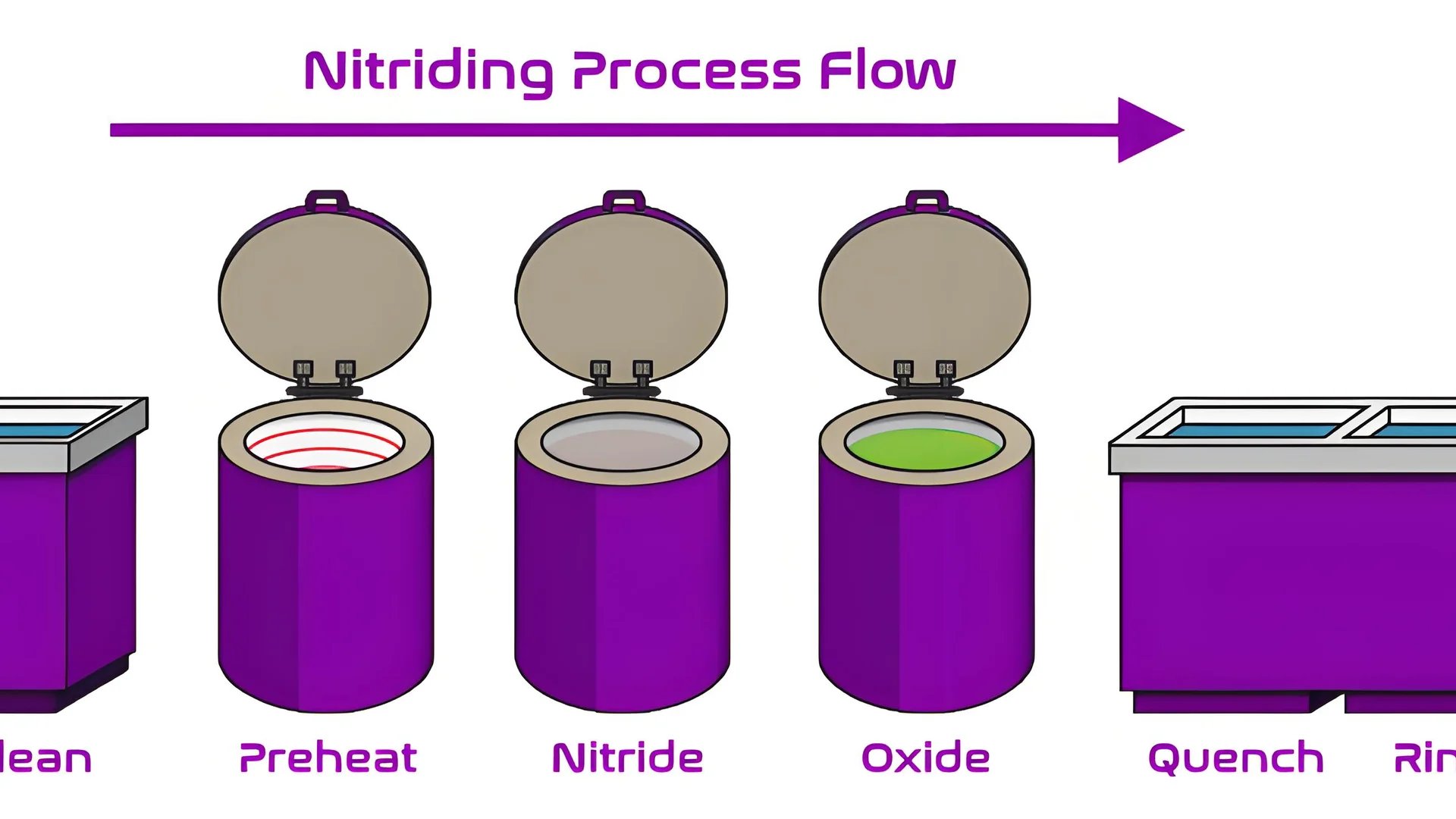
Gas Costs in Nitriding
Think about this: you’re planning a backyard barbecue, but each store has different prices for propane. This is similar to buying ammonia for nitriding. Ammonia is the main gas in this process and plays a crucial role, reacting with the metal surface to enhance hardness and wear resistance. The cost of ammonia can vary significantly based on regional availability and market demand. In areas with high demand, prices rise even more.
Other gases like hydrogen and nitrogen might be required, adding to the expense. The consumption rate of these gases depends on factors like the specific nitriding technique and desired material properties.
To manage these costs effectively, local suppliers might be a good option as they sometimes provide better prices or suggest cheaper alternative gases that maintain quality without compromising results.
Energy Consumption in Nitriding
Consider your electricity bill after a hot summer – it hurts. That’s how energy costs in nitriding feel. The process requires maintaining high temperatures within the nitriding furnace for extended periods, which can lead to substantial electricity usage. This energy requirement is dictated by the size of the components being treated and the chosen process parameters such as heating rate and holding time.
For instance, larger molds or batch processing might necessitate longer heating cycles, thereby increasing energy consumption. Conversely, optimizing these parameters can lead to reduced energy usage. Buying energy-efficient equipment is smart too—this is like replacing old bulbs with LEDs—and incorporating smart energy management practices can contribute to lowering overall energy costs.
Balancing Costs with Efficiency
Managing gas and energy expenses in nitriding is like balancing a seesaw—it is possible! Smart planning is crucial here. While these components represent a significant portion of overall expenses, their impact can be mitigated through strategic planning.
Batch processing lowers costs by spreading them over many units; arranging batch processing to treat multiple molds simultaneously can distribute the costs more evenly across units, effectively reducing the per-unit nitriding cost.
Trying different nitriding methods is useful; evaluating different methods like switching from traditional gas nitriding2 to plasma nitriding could offer energy efficiency benefits and thus impact cost structure favorably.
It’s about balancing cost and quality—you need both! Watching these factors keeps production costs low while achieving great results.
Nitriding furnace equipment is inexpensive to acquire.False
Nitriding furnaces are costly, ranging from thousands to tens of thousands.
Batch processing reduces nitriding cost per mold.True
Batch processing spreads fixed costs over multiple molds, reducing cost per unit.
Why does labor play a crucial role in nitriding costs?
Have you ever thought about why labor costs so much in nitriding? Skilled technicians play a huge role in this detailed process.
Nitriding labor expenses are high because skilled technicians are needed. These technicians expertly handle complex procedures and equipment. Their role is very important for accuracy and safety. They set parameters and supervise the process. This affects total costs greatly.
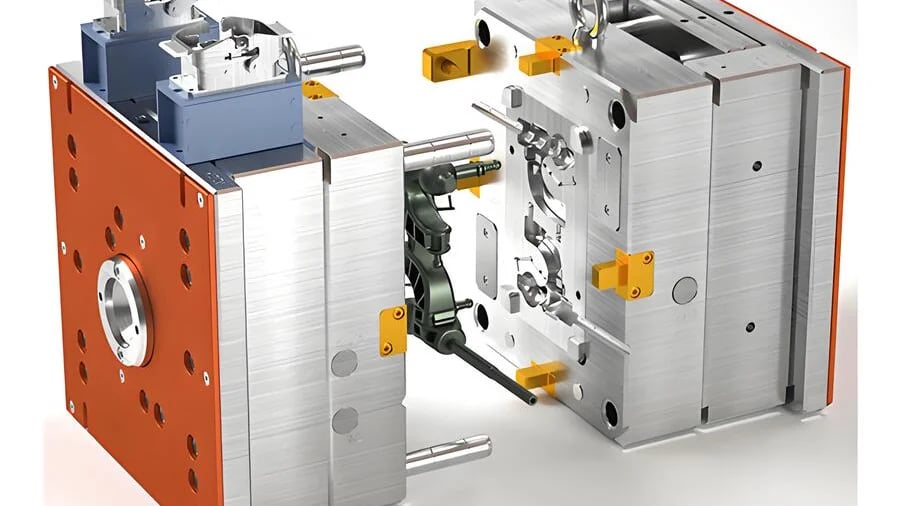
Skill in Heat Treatment
When I first discovered nitriding, I was really surprised by the skill needed to do it correctly. It isn’t just about turning knobs. Technicians need a deep understanding of the heat treatment process. They are like hidden heroes in the background. They adjust settings with great accuracy and watch every small change. One technician told me, "A single mistake and the whole batch is ruined." This fact truly impressed me.
This expertise is essential to prevent costly errors3, as improper settings can lead to defects in the final product.
Watching and Changing
Technicians stay alert for many hours. They are ready to change things quickly. Their focus is like that of an air traffic controller, keeping everything on track. This careful work is not cheap, but it is very important.
Throughout the nitriding process, continuous monitoring is required to ensure that everything proceeds according to plan. The ability to swiftly address issues minimizes potential downtime, which can otherwise increase processing costs4.
Differences Across Regions and Companies
Labor costs really vary depending on location and the company. In places where skilled workers are few, wages go up because companies try to attract talent.
In regions where skilled labor is in short supply, wages may be higher to attract qualified personnel. Similarly, companies that prioritize quality and safety might offer more competitive salaries to retain top talent, thereby influencing the overall labor cost structure5.
Learning and Growth
Learning never ends in nitriding. Companies put a lot of money into training to keep up with new technology.
As nitriding technology evolves, staying updated with the latest advancements is crucial. This commitment not only enhances efficiency but also reinforces safety standards, reflecting in higher overall labor expenses.
I met a technician who often attended workshops not just for efficiency but also for safety. This ongoing learning means higher labor costs but it’s very important for keeping quality high.
Training helps people tackle new challenges well; they become crucial to nitriding processes efficiently—a key factor in maintaining quality standards in nitriding processes6.
Looking at all these points, it’s clear: Labor might seem a big cost at first, but it really is an investment in quality and precision.
Nitriding furnace equipment is inexpensive.False
Nitriding furnace equipment is costly, ranging from thousands to tens of thousands of dollars.
Batch processing reduces nitriding costs per mold.True
Batch processing shares fixed costs across multiple molds, lowering cost per unit.
How Can Batch Processing Reduce Nitriding Costs?
Have you ever thought about how to save a lot on nitriding expenses? Batch processing completely changed the situation for me.
Batch processing lowers nitriding costs. It spreads fixed expenses like equipment and energy over several molds. This approach is more cost-effective. The process really cuts expenses.
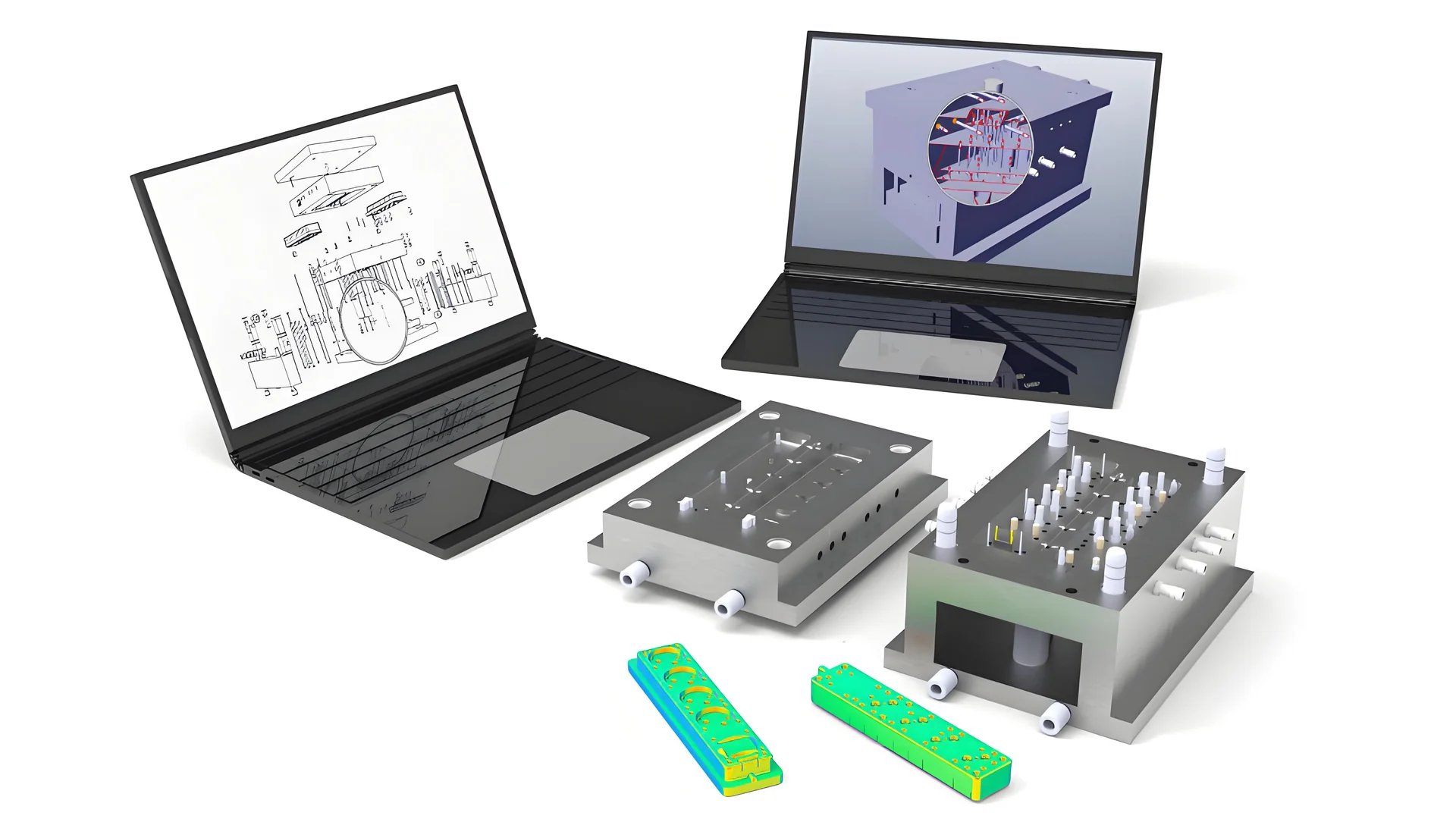
Equipment-Related Cost Sharing
When I bought a nitriding furnace, it seemed very expensive. Later, I learned about batch processing. By treating several molds at the same time, I spread the high equipment costs7 over more units. This made the purchase feel more reasonable and also lowered maintenance work. Fixing the furnace when not in use saved money. It was a smart strategy.
Process Cost Efficiency
I looked at gas bills and knew there must be a better way. Batch processing helped me by allowing many molds to be treated together, which shared the gas costs8 for ammonia and other gases. This reduced the cost per unit. Grouping heat treatments improved electricity bills as well, with the furnace’s energy spread across multiple molds.
Labor Cost Optimization
My team spent many hours on setup and monitoring before adopting batch processing, which allowed us to reduce labor costs significantly. Fewer sessions meant less setup time, giving technicians more opportunity to focus on other important tasks. Learning batch treatment management really improved their skills.
Improving Processing Efficiency
Batch processing greatly enhanced our workflow by aligning nitriding sessions with production schedules so that molds were treated quickly. This lowered the treatment time cost9. Finding the right batch size was key—big enough for cost efficiency but small enough to maintain quality.
Through this journey, I learned about nitriding cost savings through good planning and balance with batch processing, which saves money while making work easier and more efficient.
Batch processing reduces nitriding costs per mold.True
Batch processing spreads fixed costs over multiple molds, reducing cost per unit.
Nitriding treatment time is less than one hour.False
Nitriding usually takes several hours, not less than one hour.
Conclusion
Nitriding molds incurs high costs due to equipment, gas, energy, and labor. However, batch processing can reduce per-unit expenses, making it a worthwhile investment for improved mold durability.
-
Understand the financial scope before purchasing nitriding equipment. ↩
-
Understand gas nitriding’s process and cost implications in detail. ↩
-
Avoiding common errors can save significant time and resources. ↩
-
Understanding adjustments helps optimize process efficiency. ↩
-
Regional differences affect labor cost structures significantly. ↩
-
Well-trained technicians ensure high-quality nitriding outcomes. ↩
-
Explore how equipment costs influence overall nitriding expenses. ↩
-
Understand how gas expenses impact nitriding cost calculations. ↩
-
Learn about variables affecting treatment duration and costs. ↩