Finding the right balance between strength and shrinkage in plastic production often feels challenging. Many describe it as walking on a tightrope.
Strengthening plastic products that suffer from too much shrinkage involves picking suitable materials. Glass fibers work well as reinforcements. Adjusting the processing details like injection pressure is crucial. Mold temperature is also essential.
When I first began dealing with these problems, I discovered that small changes in process details led to surprisingly great results. Changing mold shapes and trying out various materials felt like solving a tricky puzzle. However, seeing these changes boost product performance was very satisfying. Now, let’s dive into some modern strategies to further increase the quality and strength of plastic items.
Glass fibers increase plastic product strength.True
Adding glass fibers enhances the structural integrity and durability of plastics.
Higher mold temperature reduces plastic shrinkage.True
Increasing mold temperature can help control the shrinkage rate in plastics.
How does choosing the right material reduce shrinkage?
Do you ever think about how the materials you pick probably affect your product’s quality?
Material choice affects shrinkage by changing heat flow and structure. Engineering plastics such as PC–ABS alloys help reduce shrinkage. Adding reinforcements, like glass fibers, also decreases shrinkage and improves strength. It really helps.
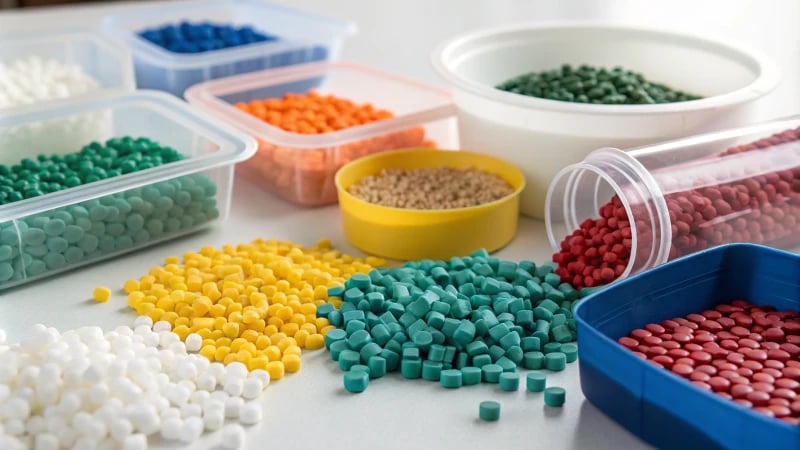
Understanding Material Properties and Shrinkage
I remember facing a tough design challenge. A plastic piece needed to handle heat without bending. That day, I learned how important the right material is. Materials like polycarbonate1 and ABS don’t expand much with heat. This means they don’t shrink much, which is really helpful. Their low shrinkage and strong nature brought big improvements to the product.
Impact of Material Composites
Exploring material science further, I found that composites change everything. Glass fiber, for example, is not just fancy stuff; it’s a real game-changer. Adding 30% glass fiber to polypropylene greatly increased its strength. It became much stronger.
Table 1 highlights the effect of adding glass fibers to polypropylene:
Material | Glass Fiber (%) | Tensile Strength Increase |
---|---|---|
Polypropylene | 30% | 2-3 times |
This kind of reinforcement is vital for long-lasting designs.
Process Parameter Considerations
Material choice is not the only factor for controlling shrinkage. Adjusting process factors like injection pressure and speed taught me a lot. Increasing these helped the plastic fill the mold completely, reducing flaws. Overdoing it, though, brings problems like extra material or internal stress.
For instance, increasing injection pressure from 60MPa to 80MPa can enhance product strength when combined with speed adjustments.
Mold Design Adjustments
Matching materials with clever mold design strategies2 can achieve great results. Optimizing gate designs and runner systems improves melt flow and cuts down shrinkage well. Small changes in gate position or runner size can fill molds evenly and reduce local shrinkage.
Implementing multi-point gates or adjusting runner diameter can help achieve uniform filling and mitigate local shrinkage effects.
Utilizing Innovative Materials
Material innovation is always moving forward. New alloys combining strong plastics with creative fillers are intriguing. They might cut shrinkage while keeping strength.
This exploration of innovative materials3 could be crucial for the future of manufacturing.
These materials open new design options, and embracing these changes is important for perfection-seeking designers.
Using these insights has changed my design approach—it’s not only about good looks but about creating durable products through wise material choices and strategic designs.
Polycarbonate has a low thermal expansion coefficient.True
Polycarbonate is known for its low thermal expansion, reducing shrinkage.
Increasing injection pressure reduces flash formation.False
Higher injection pressure can increase flash if not balanced correctly.
How Do Process Parameters Affect the Strength of Plastic Products?
Ever thought about changing a few settings to create stronger plastic products?
Changing process settings like injection pressure, speed and mold temperature greatly affects the strength of plastic products. Adjusting these factors carefully improves material qualities and reduces flaws. This leads to better quality. Better quality is the result.
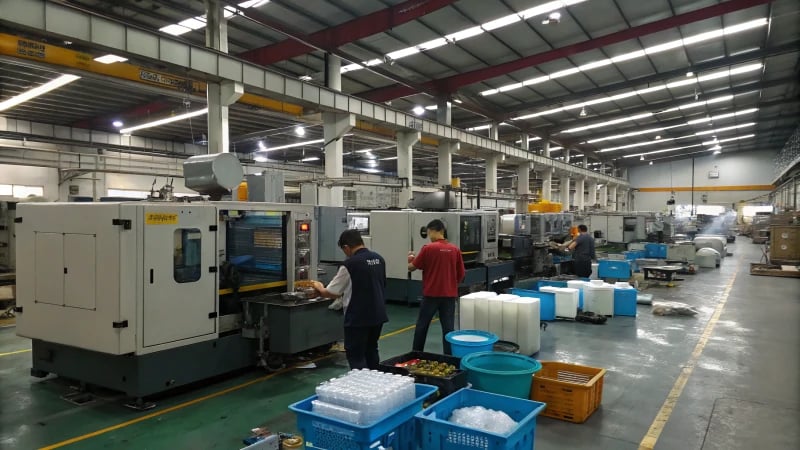
Material Selection and Optimization
Choosing plastic materials is like picking the best ingredients for cooking. It changes everything in the final product. I remember switching from regular plastics to a mix of polycarbonate (PC) and acrylonitrile-butadiene-styrene (ABS), which really improved our product’s strength. Adding reinforcement materials4 like glass fiber can greatly increase the tensile strength. This results in tough products that last a long time.
Process Parameter Adjustment
- Injection Pressure and Speed: One time, I had trouble with PP products shrinking. Increasing the injection pressure from 60MPa to 80MPa and adjusting the speed was like opening a gate. The melt filled every part of the mold, making the product a lot stronger.
- Press Holding Parameters: Extending the press holding time from 5 seconds to 8 seconds felt like letting the product settle more. This improved its thickness and reduced ugly shrinkage marks.
- Mold Temperature Control: Changing the mold temperature is like setting your oven just right. For crystalline plastics, raising the mold temperature from 30°C to 50°C improved crystallization. This gave the product a stronger inner structure.
Mold Design Improvement
Creating a good mold is like making a perfect suit. Every detail counts:
- Gate Design Optimization: Optimizing gate design with multiple gates helps spread the material evenly, reducing shrinkage.
- Runner System Adjustment: I realized that making the runner system wider reduced flow resistance, allowing smoother entry into the cavity.
- Reinforcement Rib Design: Adding ribs increased rigidity and kept wall thickness even, preventing uneven cooling.
Process Parameter | Effect on Strength | Example Adjustment |
---|---|---|
Injection Pressure | Improves filling | Increase from 60MPa to 80MPa |
Mold Temperature | Enhances crystallization | Increase from 30°C to 50°C |
Press Holding Time | Reduces shrinkage | Extend from 5s to 8s |
These adjustments are very important, especially for designers like Jacky5, who want products to look good and work well in mass production. With these changes, plastic product quality improves greatly, just like refining an old family recipe.
Higher mold temperature improves plastic strength.True
Increasing mold temperature enhances melt crystallization, boosting strength.
Reducing injection pressure increases product density.False
Lower injection pressure can lead to incomplete filling and defects.
What mold design improvements can mitigate shrinkage?
Have you ever felt frustrated when a good design loses shape because of shrinking defects? Let’s discuss a few mold design tips that really help.
To fight shrinkage in molded parts, good gate designs are important. Tweaking runner systems also helps. Reinforcement ribs add support. These adjustments improve how the material moves. They strengthen the structure, significantly reducing shrinkage problems. Shrinkage issues decrease significantly.
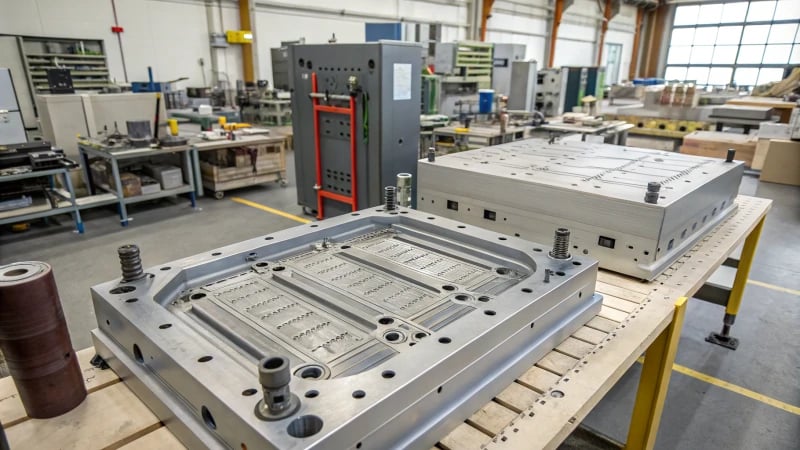
Gate Design Optimization
Gate design is very important. Imagine filling a mold through a tiny gate – like pouring syrup through a straw. Using multi-point gates6 or fan gates lets material flow more evenly. This reduces shrinkage. Bigger projects need more gates to shorten flow paths, leading to smoother distribution.
Design Element | Potential Benefit |
---|---|
Multi-point Gates | Uniform filling and reduced shrinkage |
Fan Gates | Better flow control |
Runner System Adjustments
The runner system works like a material highway. Simple changes here bring great results. Making the diameter bigger and the path simpler reduces resistance. I once increased the flow channel diameter7 from 4mm to 6mm. What a difference! The melt flowed smoothly, reducing shrinkage significantly.
Reinforcement Ribs and Wall Thickness Design
Reinforcement ribs add stability, not just strength. Adjusting wall thickness for even cooling prevents unwanted deformations. Even wall thickness isn’t just about looks – it keeps products strong.
Feature | Impact |
---|---|
Reinforcement Ribs | Enhanced rigidity |
Uniform Wall Thickness | Consistent cooling |
Material Selection and Optimization
Choosing the right material sometimes feels like solving a puzzle. Plastics with lower shrinkage, like polycarbonate (PC) or ABS alloys, are important. Glass fibers added to polypropylene improved my projects. They gave strength but kept flexibility.
For instance, adding 30% glass fiber8 to polypropylene increases its tensile strength significantly.
Process Parameter Adjustment
Fine-tuning process parameters is like being a scientist. Adjusting injection pressure, speed, and mold temperature takes patience, but it’s worth it.
- Injection Pressure & Speed: Completes filling; don’t use too much pressure to avoid problems.
- Press Holding: Longer time and more pressure minimize shrinkage.
- Mold Temperature: Cools slowly for crystalline plastics, improving structure.
These methods improved the quality of my molded products, saving me from the defects caused by shrinkage. Trust me, every small improvement is very valuable when reaching for perfection.
Multi-point gates reduce shrinkage in molded parts.True
Multi-point gates ensure uniform filling, minimizing shrinkage.
Increasing runner length decreases flow resistance.False
Shorter runners reduce flow resistance, enhancing melt flow.
How Can We Make Plastics Stronger?
Have you ever wondered how plastics become stronger and last more years? Look at these new techniques to strengthen plastics for factories.
To increase plastic strength, explore advanced techniques like choosing the right materials, adjusting processes and improving mold design. These methods really boost the durability and performance of plastic products. They truly help.
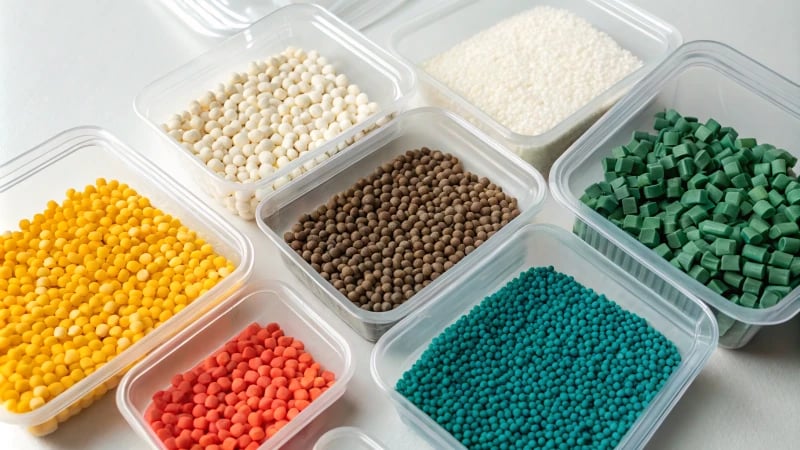
Material Selection and Optimization
I find it fascinating to choose the right plastic materials9 for better product strength. Picture mixing polycarbonate (PC) with acrylonitrile-butadiene-styrene (ABS). Think of these like two superheroes – PC gives strength, while ABS offers flexibility and easy shaping. Adding reinforcement materials like glass fiber is like giving your plastic a suit of armor. Very strong. Sometimes, it’s twice or even three times as strong.
Material | Reinforcement | Strength Improvement |
---|---|---|
Polycarbonate + ABS | Glass Fiber | 2-3x Increase |
Carbon or mineral fibers are significant too. They can really change things depending on needs and budget.
Process Parameter Adjustment
Adjusting parameters is like tuning a musical instrument. You find the right balance. More injection pressure and speed ensure every part of the mold fills up. Imagine making sure cake batter reaches every part of the mold. Increasing pressure from 60MPa to 80MPa and speeding from 30mm/s to 40mm/s can really change things.
Press holding is important too. Maybe extend time from 5 seconds to 8 seconds. More pressure helps; go from 40MPa to 50MPa. This lowers shrinkage marks, similar to letting bread dough rise longer for better texture.
Moreover, mold temperature is crucial. Raising it from 30°C to 50°C improves internal structure, akin to adjusting oven heat for the perfect bake.
Mold Design Improvement
Improving mold design feels like solving a puzzle where each piece has a role. Multi-point gates help melt flow evenly, reducing shrinkage—imagine directing traffic smoothly at a busy intersection; more gates smoothen flow.
Enhancing runner systems by increasing diameter from 4mm to 6mm makes fluid move better with less shrinkage.
Adding reinforcement ribs10 is like strengthening a bridge with extra beams, increasing stiffness and cutting down chances of deformation.
Every change improves plastic strength and reliability—these methods are secrets in plastic engineering waiting to be discovered.
Glass fiber doubles plastic tensile strength.True
Glass fiber reinforcement can double or triple the tensile strength of plastics.
Higher mold temperature decreases product quality.False
Increasing mold temperature can improve the internal structure and quality.
Conclusion
Enhancing plastic strength while minimizing shrinkage involves selecting suitable materials, adjusting processing parameters, and optimizing mold design for improved durability and performance in manufacturing.
-
Explore how engineering plastics reduce shrinkage and improve strength, offering practical solutions for manufacturing challenges. ↩
-
Learn about optimizing gate design in molds to improve material flow, reduce shrinkage, and enhance product quality. ↩
-
Discover new materials that offer solutions for reducing shrinkage and enhancing performance in plastic manufacturing. ↩
-
Discover various reinforcement materials that enhance plastic strength and learn how they can be applied to your projects. ↩
-
Learn about the typical profile of a product designer in the plastic industry and how they optimize design for production. ↩
-
Learn how multi-point gates improve uniformity in mold filling and reduce shrinkage issues. ↩
-
Discover how increasing flow channel diameter enhances melt fluidity and reduces shrinkage. ↩
-
Understand how glass fiber reinforcement can significantly increase tensile strength in plastics. ↩
-
Understanding material selection can guide you in choosing the most suitable plastics for enhanced strength. ↩
-
Learn how reinforcement ribs can improve structural integrity and rigidity of plastic components. ↩