Curious about how to craft injection molded products that are stronger and last longer? Let me share some lessons from my path in the world of molds.
To increase the strength of injection molded products, select the right materials, fine-tune processing settings and improve mold design. Choose materials with care. Adjust injection pressure and speed. This really helps. Improve mold design, too. Products become more durable. Performance becomes better.
Looking back on my experience in the mold industry, I think about facing the challenge of making our products stronger. My work involved more than choosing hard materials or adjusting machines. Decisions involved a careful balance of choices and changes. These expert tips from my years in the field will really help improve your production results.
Material choice affects injection molded product strength.True
Selecting appropriate materials is crucial for enhancing durability.
Injection speed has no impact on product durability.False
Injection speed influences the internal stress and strength.
What Are the Best Materials for High-Strength Injection Molding?
Do you ever think about how some plastic parts seem impossible to break? Advanced injection molding plays its role. Special materials create this tough nature.
Materials such as polyamide (PA), polyoxymethylene (POM) and polycarbonate (PC) are very good for creating strong mechanical parts. Thermoplastic elastomers (TPE) really work well for products requiring added toughness. Plastics modified to handle impact are also excellent. They’re great for very durable items.
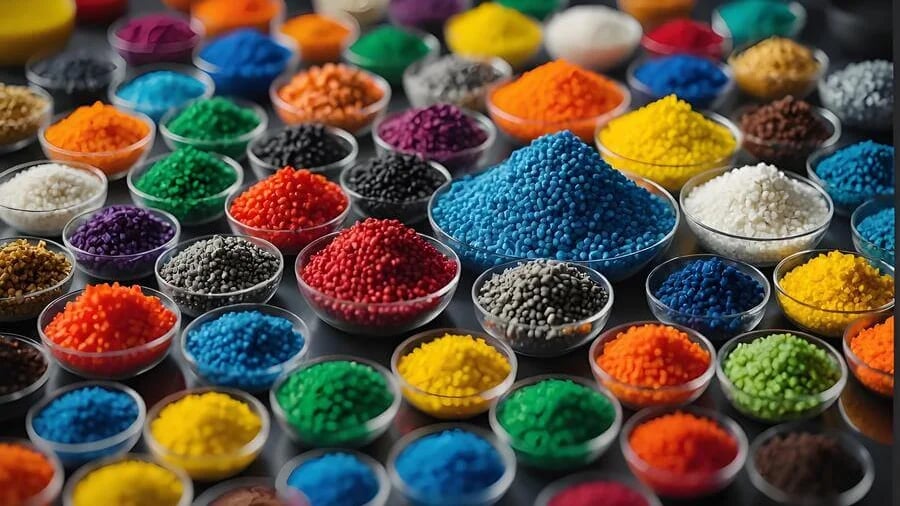
Material Selection and Processing
I remember when I first chose a material for a project. It felt like picking a teammate in a race – you need someone strong who won’t fail you. Selecting the right material for injection molding1 is very important. Strong materials matter. I often choose polyamide (PA), polyoxymethylene (POM), or polycarbonate (PC) for mechanical parts. These plastics feel like a reliable friend – strong and ready to support you.
For products needing extra flexibility and toughness, like sports gear, thermoplastic elastomers (TPE) or impact-modified plastics work well. These materials act tough and bend easily, ready for any challenge. Quality control matters a lot. Checking material purity is important, just like making sure your team is ready for a game. I pick high-quality raw materials and carry out thorough checks. Inspections matter; it’s like preparing your gear before starting an adventure.
Material | Ideal Use | Key Properties |
---|---|---|
Polyamide (PA) | Mechanical parts | High strength, wear resistance |
POM | Gears, bearings | Low friction, high stiffness |
PC | Electrical components | Impact resistance, clarity |
TPE | Flexible components | Elasticity, resilience |
Optimization of Injection Molding Process Parameters
Adjusting process settings feels like tuning a musical instrument – it creates a big difference. Increasing injection pressure helps the melt fill the mold fully but avoiding excess stress is necessary. I adjust injection speed based on the product shape and thickness; for thin walls, faster speeds prevent early cooling.
Holding pressure and time support the product during cooling, like wrapping up in a warm blanket after a long day. This practice lessens flaws and really improves density. Specific values come from tests and inspections so everything fits perfectly.
Control of mold temperature is crucial for plastics like PP and PA. Finding the right balance helps improve crystallization and product strength – much like a chef refining recipes for great taste and consistency.
Mold Design and Improvement
Optimizing mold design feels like solving a puzzle where each part counts. Proper gate size and position spread stress evenly; gates should stay near stress areas to really increase local strength.
Improving runner systems by using short, thick runners lowers flow resistance – it’s like making a process efficient. Maybe I would use a hot runner system2 for better temperature control.
Exhaust systems need enough grooves to stop melt flow blockages. Setting them according to material features or choosing breathable steel can change the game in tough spots.
Design Aspect | Considerations |
---|---|
Gate Design | Size and position for stress distribution |
Runner System | Short, polished runners; consider hot runners |
Exhaust System | Adequate grooves; consider breathable materials |
By understanding these aspects, designers achieve high-strength injection molding through smart material selection and process settings. Explore further3 to improve your designs.
Polyamide (PA) is ideal for flexible components.False
Polyamide is best for mechanical parts, not flexible components.
High injection speed prevents premature cooling in thin walls.True
Increasing speed helps the melt fill thin wall molds before cooling.
How do process parameters influence product strength?
Have you ever thought about how small changes in the way you produce things give products more power? Come with me as I explain the secrets of materials and mold tricks.
Process details are crucial in deciding product strength. They affect which materials to use, mold design and how to improve the process. Important factors are material quality, injection pressure, mold temperature and cooling time.
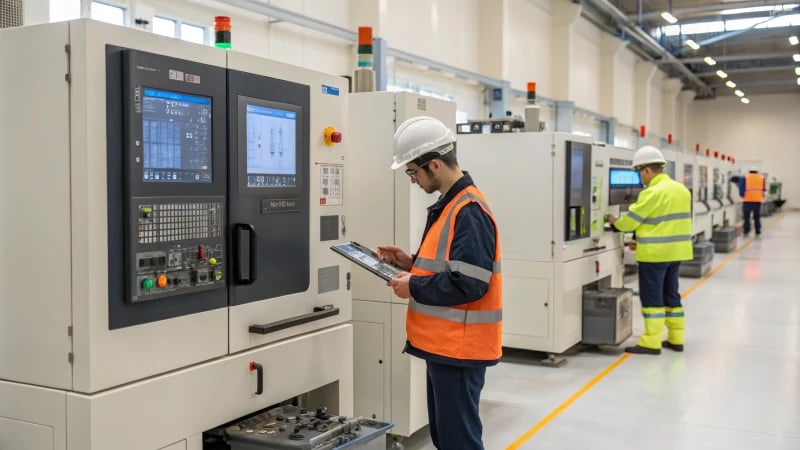
Material Selection and Quality Control
Material selection rests at the heart of strong product creation. Choosing the right materials, such as polyamide (PA) or polycarbonate (PC), resembles picking the perfect ingredients for a complex recipe. For example, using these materials greatly improves load-bearing capacity. Ensuring material purity by avoiding impurities is essential for maintaining consistent quality. This includes inspecting raw materials and managing the use of recycled materials.
For instance, hygroscopic materials like nylon (PA) require thorough drying before injection molding to reduce moisture content below 0.2% for PA6 and 0.1% for PA66. Proper material pretreatment4 ensures the final product’s durability.
Optimizing Injection Molding Process Parameters
Adjusting injection pressure and speed is like tuning a musical instrument. Adjusting pressure helps fill every part of the mold cavity, increasing product density. I discovered this while working on thin-walled items, where controlling speed really helped prevent early cooling.
Parameter | Thin-Walled Products | Thick-Walled Products |
---|---|---|
Injection Speed | Increase | Control |
Holding Pressure | Increase | Increase |
Cooling Time | Shorten | Extend |
Prolonged holding pressure and time lower shrinkage during cooling, similar to baking – leaving it in a bit longer offers perfection. Mold temperature is another crucial factor; raising it promotes crystallization in crystalline plastics like polypropylene (PP), which enhances strength.
Mold Design and Improvement
Optimizing gate design is like playing chess – every move is planned. Deciding on size and position based on product dimensions is key, giving stress-heavy parts a uniform fill. Enhancements in the runner system, such as using a hot runner system, maintain melt temperature and reduce pressure loss – a move that brought many successes in mold design.
Proper exhaust system design is just as crucial; it’s like ensuring an engine breathes well. Setting correct exhaust grooves or using breathable materials prevents gas obstruction in the cavity.
By grasping and improving these process parameters5, manufacturers can significantly increase product strength, meeting both aesthetic and practical needs in various uses.
Increasing injection pressure enhances product density.True
Higher pressure fills the mold completely, increasing product density.
Shortening cooling time reduces strength in thick-walled products.True
Extended cooling prevents shrinkage, maintaining strength in thick walls.
How Does Mold Design Impact Product Strength?
Have you ever thought about how something as basic as mold design could really change your product’s strength?
Mold design is very important for product strength. It optimizes how materials flow, reduces defects and spreads pressure evenly. Designers place gates with care. They also plan the runners well. This design greatly increases how strong products are.
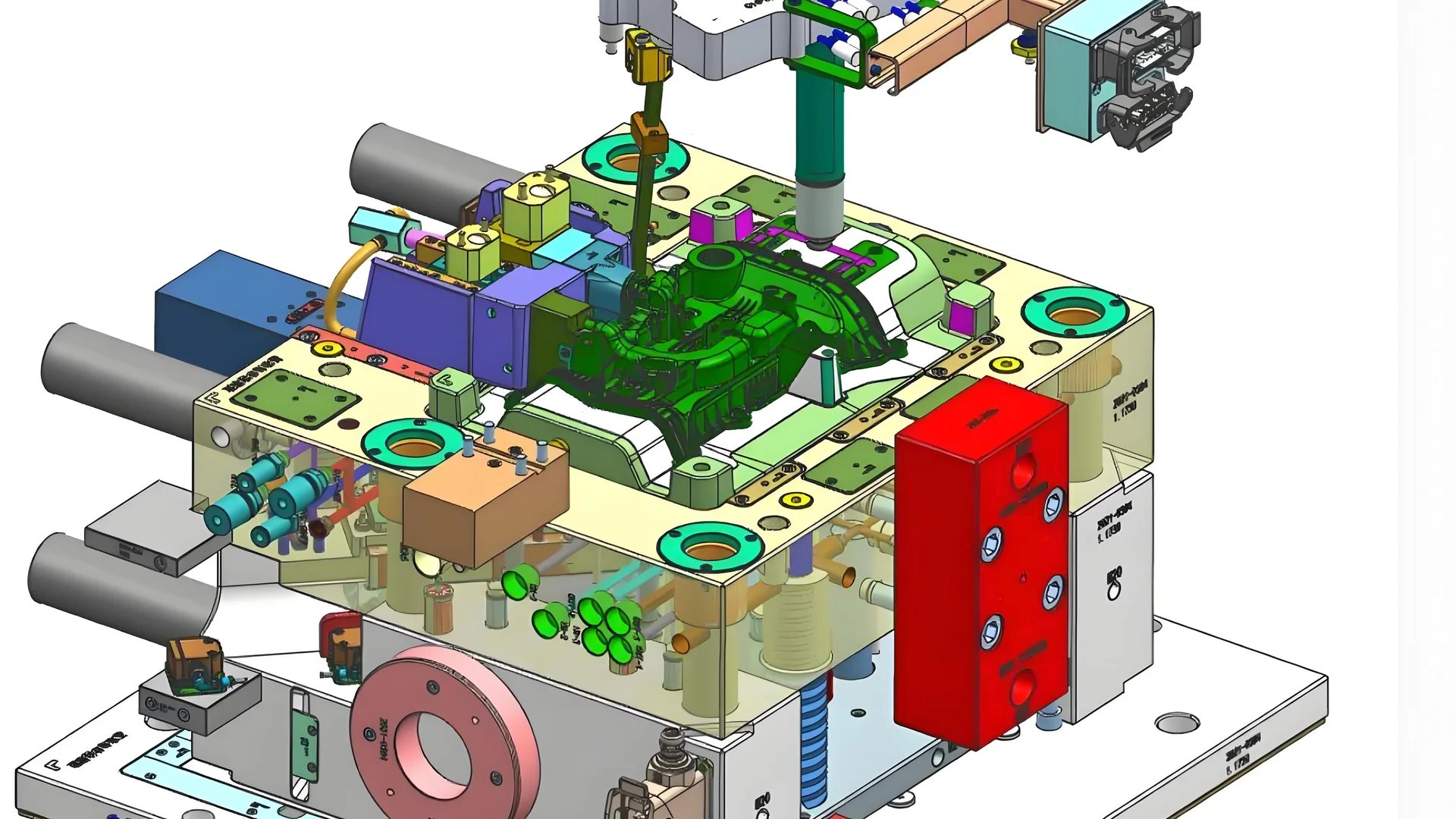
Understanding Material Selection and Processing
I want to share a moment when choosing the right materials became crucial for me. Picture a project needing parts that handle high pressure. I picked strong plastics like polyamide (PA) or polycarbonate (PC). This choice really helped our product last under tough conditions. The pretreatment process6 was a lesson. Have you ever had a batch ruined by moisture? I did! Now, I always dry materials like nylon carefully before molding.
Injection Molding Process Optimization
Trying and failing many times showed me the importance of adjusting process settings.
- Injection Pressure and Speed: It’s tricky. Increasing them too much causes internal stress. But getting it right feels perfect, like a smooth piano note.
- Holding Pressure: I’ll never forget when adjusting holding pressure fixed shrinkage during cooling. Our products became stronger and more solid.
- Mold Temperature: Controlling mold temperature can really improve results. Adjusting it helped us with polypropylene to boost strength without losing quality.
Mold Design Enhancements
Gate Design Optimization
I remember a night spent on gate design, realizing its size and position were crucial. It felt like solving a puzzle. Once the gate allowed smooth flow, especially in stressed areas, the product’s strength increased greatly.
Runner System Improvements
Figuring out efficient runners was a breakthrough. Short, thick, polished runners cut down flow resistance. Using a hot runner system maintained the right melt temperature, which strengthened the product.
Feature | Benefit |
---|---|
Gate Design | Smooth melt flow, improved local strength |
Runner Design | Reduced resistance, better melt temperature |
Exhaust System Efficiency
Good exhaust systems matter a lot. During one project, improper exhaust caused gas to get trapped – a real issue! Now, proper exhaust paths or breathable materials are a must.
Refining these parts of mold design transforms product strength and durability, meeting various needs with precision. Anyone curious about runner system improvements7 should explore advanced design techniques for strong product outcomes.
Gate design impacts the strength of molded products.True
A well-designed gate ensures smooth melt flow, enhancing strength.
Mold temperature does not affect product crystallization.False
Proper mold temperature promotes crystallization, improving strength.
How Can Cooling Time and Mold Temperature Affect Durability?
Have you considered how cooling time and mold temperature affect the strength of your injection-molded creations? These factors greatly influence durability. Absolutely crucial!
Cooling time and mold temperature are very important for the durability of injection-molded products. They affect crystallinity, strength and stability in size. Adjusting these settings improves quality and lifespan. Quality depends on these variables. Quality and longevity can really benefit.
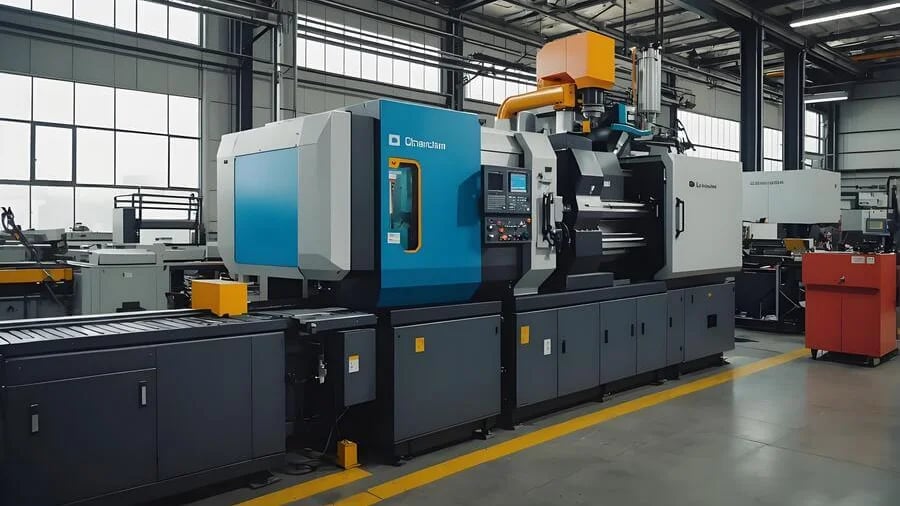
The Science Behind Cooling Time
In the early days of learning injection molding, I discovered the delicate art of cooling time. Cooling time isn’t just waiting until things aren’t hot anymore. It is crucial. This period allows the material to become solid before we take it out of the mold. Once, I hurried this step and ended with a bent product. It couldn’t keep its form. Thick parts need more time to solidify evenly.
The optimal cooling time varies based on material selection8 and product thickness.
Importance of Mold Temperature
Now, let’s talk about mold temperature. Don’t ignore its importance. I learned valuable lessons with polypropylene (PP) and polyamide (PA). Higher mold temperatures create better crystals, leading to a stronger product with a more regular structure. It’s like baking at the right heat – too low and you get a soggy middle.
Example Table: Mold Temperature Effects
Material Type | Low Temperature Effect | High Temperature Effect |
---|---|---|
Crystalline | Incomplete crystallization | Enhanced crystal structure |
Non-crystalline | Poor molecular orientation | Better molecular alignment |
Balancing Cooling Time and Mold Temperature
Balancing cooling time with mold temperature feels tricky; it’s like walking on a tightrope. Once, I increased the mold temperature but reduced the cooling time. This way, the material gained enough crystallinity without going too far. With lower temperatures, I gave more cooling time for stability.
Practical Considerations
Material Pretreatment: I won’t forget the time I didn’t dry nylon enough. Moisture caused defects that bothered me for weeks—really annoying! Keeping nylon moisture under 0.2% is key to avoid such troubles.
This process influences both cooling and mold temperature settings.
For example, nylon should maintain moisture content below 0.2%.
Process Parameters: Adjusting injection pressure, speed, and temperature is like leading an orchestra—a well-tuned system helps maintain smooth melt flow and cuts stress.
Too much pressure brings internal stress; hence, harmony in process parameters is essential for achieving optimal durability.
Utilizing an optimized runner system9 helps maintain consistent melt flow, reducing stress concentrations that can compromise durability.
Knowing how cooling time and mold temperature work together opens up improvements in product durability. It’s not just about making something functional; it’s about creating something that truly lasts.
Longer cooling time increases product durability.True
Longer cooling times allow complete solidification, reducing warping.
Higher mold temperatures decrease material strength.False
Higher mold temperatures improve crystallization, enhancing strength.
Conclusion
Enhance the strength of injection molded products by selecting appropriate materials, optimizing processing parameters, and improving mold design for durability and performance.
-
Discover comprehensive techniques to optimize the injection molding process for stronger, more durable products. ↩
-
Learn how hot runner systems enhance temperature control and reduce material wastage during injection molding. ↩
-
Gain insights into cutting-edge mold design techniques that improve efficiency and product quality. ↩
-
Explore effective pretreatment methods to enhance material performance and reduce moisture-related issues. ↩
-
Understand how adjusting process parameters can improve the strength of injection-molded products. ↩
-
Learn how proper material pretreatment prevents defects and enhances product quality. ↩
-
Explore techniques to optimize runner systems for better melt flow and strength. ↩
-
Explore this link to understand how different materials require specific cooling times for optimal molding results. ↩
-
This link provides insights into designing effective runner systems to enhance product durability and reduce manufacturing defects. ↩