Some plastic items appear perfect. The secret lies in the surface treatment!
Improving the surface quality of injection molded plastic products involves careful design, smart material choices and exact control of molding and treatment processes. Good design helps. Right materials matter. Exact control during manufacturing guarantees even coating and fewer flaws. Product performance really improves.
I remember my first project. The design had too many sharp corners. I quickly learned rational structure was important. Imagine trying to coat something with sharp edges and curves. It’s a nightmare for even coverage. Now, smoother transitions are my focus.
Material choice is important too. If plating is needed, I prefer ABS plastic over PP. ABS bonds better with metal ions. This choice changes the final product’s appearance and strength.
The injection molding process is also crucial. I have spent many hours adjusting temperature and pressure to avoid flaws like flow marks. It’s like baking a perfect cake. One mistake can ruin everything.
By focusing on these details, I have seen how surface quality improves. Products look better and really withstand their use.
ABS plastic is better for plating than PP plastic.True
ABS plastic allows better metal ion deposition, enhancing plating quality.
Sharp inner corners improve surface treatment results.False
Sharp corners cause uneven coating and stress concentration, reducing quality.
- 1. How Does the Design Phase Influence Surface Treatment Quality?
- 2. How Does Material Selection Affect Surface Treatment Success?
- 3. Why is Injection Molding Process Control Crucial for Surface Quality?
- 4. How Can I Optimize the Surface Treatment Process?
- 5. How Can Quality Inspection and Control Systems Improve Outcomes?
- 6. Conclusion
How Does the Design Phase Influence Surface Treatment Quality?
Have you ever thought about how the planning step defines the product’s ultimate appearance and texture?
The product design stage is vital for good surface treatment. It decides the structure’s complexity, picks materials and sets process controls. These steps keep the coating uniform and reduce flaws. Good design is key. It is really important.
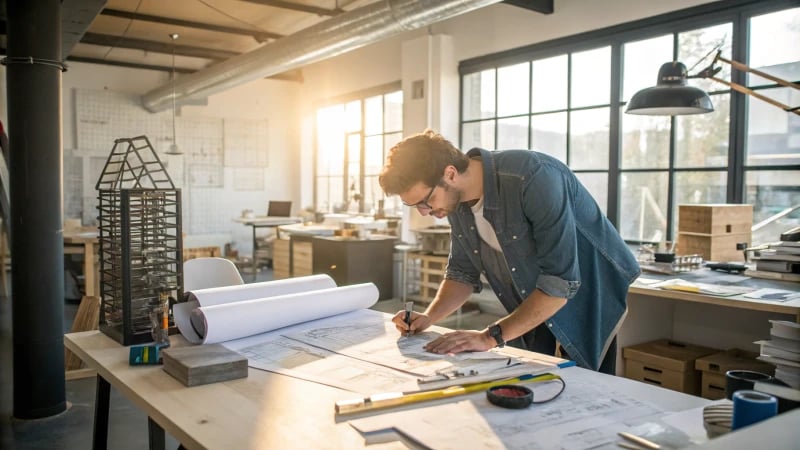
Understanding the Impact of Structural Design
In my early days in product design, I learned something quickly. Every curve and corner affects the quality of surface finishes. Picture painting a small toy car; sharp corners often collect too much paint, while smooth edges look perfect. This idea applies to bigger projects. Logical structural design1 keeps treatments like painting and plating even. Complex shapes are difficult for getting a smooth coating.
Consider the following table illustrating the impact of different structural elements:
Structural Element | Surface Treatment Impact |
---|---|
Sharp inner corners | Causes stress concentration, uneven coating |
Rounded edges | Promotes even coating distribution |
Complex shapes | Challenges in uniform coating application |
Material Selection and Compatibility
Choosing the right material is like selecting the right tool. Some materials fit better with certain surface treatments. I remember needing to choose between ABS and PP plastic for plating. ABS was clearly better as it holds onto metal ions well, resulting in a shiny and strong finish.
The table below showcases different materials and their treatment compatibility:
Material | Treatment Compatibility |
---|---|
ABS Plastic | Highly compatible with plating processes |
PP Plastic | Less compatible; may affect plating quality |
Understanding these compatibility factors helps in optimizing material choices during the design phase.
Injection Molding Process Control
Working with injection molding taught me the value of precision. It’s similar to baking; without controlling the oven’s temperature, the cake gets burnt outside and remains raw inside. In the same way, managing temperature, pressure, and speed in injection molding matters for achieving a glossy finish.
Additionally, maintaining mold quality through regular maintenance ensures smoother surfaces and reduces imperfections. Employ high-precision equipment for texturing to meet design standards, ensuring accurate reproduction on molded surfaces.
Injection molding process control2 ensures a smooth product surface, laying a solid foundation for subsequent treatments.
Pre-treatment and Post-treatment Parameters
Surface prep is where the magic starts. Imagine ultrasonic cleaning giving your product a "spa day" before its debut. It removes impurities, offering a clean base for treatments to stick nicely.
Post-treatment care holds importance too. It’s like letting painted nails dry fully to avoid smudges. Proper curing prevents cracking or discoloration later on.
By focusing on these details, I’ve realized how crucial the design phase is for achieving excellent surface treatments. It is a critical step to ensure every product looks good and works well too. This insight has really changed my path in product development and production.
ABS plastic is better for plating than PP plastic.True
ABS has better metal ion deposition, improving plating quality.
Sharp inner corners improve coating thickness uniformity.False
Sharp corners cause uneven coating thickness and stress concentration.
How Does Material Selection Affect Surface Treatment Success?
Ever thought about how the correct material affects your success with surface treatments?
Selecting the correct material is vital for successful surface treatment. It impacts how well things stick, how good the coating is and how long it lasts. Materials that work well with certain treatments provide the best outcomes. This helps avoid problems like bending or weak sticking.
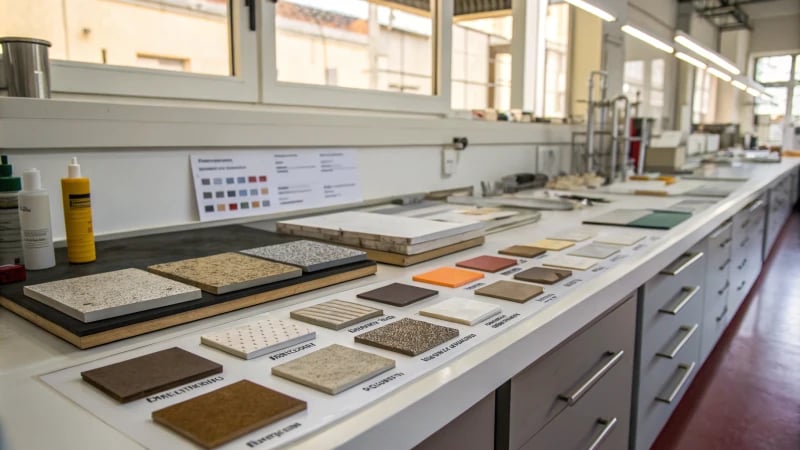
The Role of Material Compatibility
Material compatibility is fundamental for successful surface treatment. Different materials react uniquely to processes such as plating, painting, or coating3. For instance, ABS plastic is preferred over PP for plating because its surface allows better metal ion deposition.
Material Compatibility Table
Material | Suitable Treatments | Considerations |
---|---|---|
ABS | Plating, Painting | Good ion deposition |
PP | Limited Plating, Painting | Poor ion adherence |
Aluminum | Anodizing, Powder Coating | Excellent corrosion resistance |
Steel | Galvanizing, Electroplating | Requires thorough pretreatment |
Impact of Physical Properties
The physical properties of a material, such as its coefficient of thermal expansion, affect its behavior during surface treatment. Materials that expand excessively under heat may deform, impacting the final quality of the surface finish.
Consideration of thermal expansion4 is crucial in processes like heat curing and transfer. Mismatched properties between the base material and coating can lead to stress points and eventual failure.
Designing for Surface Treatment
Product design plays a pivotal role in the success of surface treatments. A rational structural design that avoids sharp corners and complex shapes allows even coating distribution and reduces stress concentration.
When designing products requiring texture treatment5, plan the direction and area of texture in advance to ensure accurate replication without affecting demolding.
Design Considerations Table
Aspect | Design Tip |
---|---|
Complex Shapes | Avoid; opt for rounded edges |
Sharp Corners | Avoid; increase uniformity of coating |
Texture Direction | Plan to ensure replication accuracy |
Pre-Treatment and Process Control
Effective pre-treatment is key to successful surface treatment. Cleaning processes like ultrasonic or chemical cleaning remove impurities ensuring optimal coating adherence. Control over injection molding parameters6 such as temperature and pressure also lays a foundation for high-quality surface finishes.
Using precise parameters prevents defects like flying edges or flow marks that become apparent post-treatment.
By understanding these aspects, you can better select materials and design processes that enhance surface treatment success.
ABS plastic is better for plating than PP plastic.True
ABS allows better metal ion deposition, enhancing plating quality.
Sharp inner corners improve coating thickness distribution.False
Sharp corners cause uneven coating and stress concentration issues.
Why is Injection Molding Process Control Crucial for Surface Quality?
Ever thought about how a flawless plastic item comes to life? Mastery of injection molding process control is essential.
Controlling the injection molding process is vital for good surface quality. This process includes handling temperature, pressure and speed. Managing these factors helps stop defects. Perfect surfaces are important for later treatments.
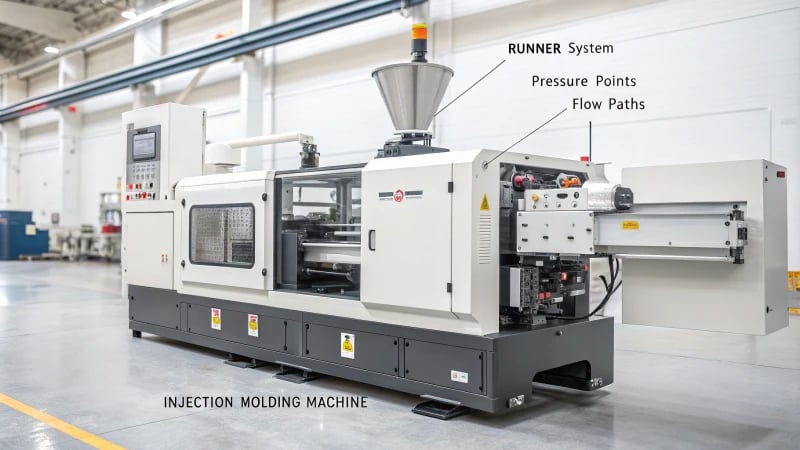
The Role of Injection Molding Parameters
Precise control over injection molding parameters is essential to achieving high-quality surface finishes.
Temperature Control
Temperature management resembles baking a cake. Too hot or too cold leads to failure. The flow of plastic melt decides if the product’s surface shines brightly or looks poorly done. Experiencing high-gloss finishes taught me the importance of mold and melt temperature.
- Temperature Management: Affects the plastic melt’s fluidity7 and ultimately determines the smoothness of the product’s surface.
Pressure and Speed Optimization
Pressure and speed feel like driving a car. Push too hard or speed up too fast, and control slips away. Mistakes here mean defects like flying edges or flow marks. Achieving balance took many trials and a lot of coffee.
Parameter | Effect on Surface Quality |
---|---|
Temperature | Ensures fluidity and smoothness |
Pressure | Prevents flying edges |
Speed | Avoids flow marks |
- Optimization: These parameters should be determined through mold trials and systematic optimization8.
Mold Quality Assurance
Mold quality directly affects the final product. Regular maintenance is vital. Polished molds turn flaws into smooth surfaces.
- Surface Finish: Like sanding wood, polishing molds can reduce imperfections on the molded product.
- Texture Precision: High-precision tools capture every tiny detail perfectly with high-precision equipment9.
Impact of Material Selection
Choosing the right material resembles finding the perfect recipe ingredient. ABS plastic is very effective if you plan to plate because it deposits metal ions better than PP.
Material Considerations
- Thermal Expansion: Pay attention to avoid surprises during heat treatment by considering the material’s coefficient.
- Compatibility: Make sure your material matches your surface treatment plans, aligning with intended processes.
Process Monitoring and Feedback Systems
Setting up a strong monitoring system feels like having a GPS for manufacturing. Tools like Statistical Process Control (SPC)10 help analyze quality trends.
- Quality Standards: Gloss, color consistency, and adhesion standards set the rules of the game.
- Monitoring Points: Checkpoints ensure everything stays on track for continuous feedback and improvement.
ABS plastic is better for plating than PP plastic.True
ABS has better metal ion deposition, improving plating quality.
High injection pressure always improves surface quality.False
Excessive pressure can cause defects like flying edges and flow marks.
How Can I Optimize the Surface Treatment Process?
Do you ever look at a dull product finish and wonder what happened?
Optimizing the surface treatment process means paying attention to product design. Designers select suitable materials. Controlling injection molding is important. Pretreatment must be done carefully. Precise process control is very necessary. Quality inspection should be thorough. Each step is vital. Each step really helps. Every action leads to a smooth finish and strong adhesion.
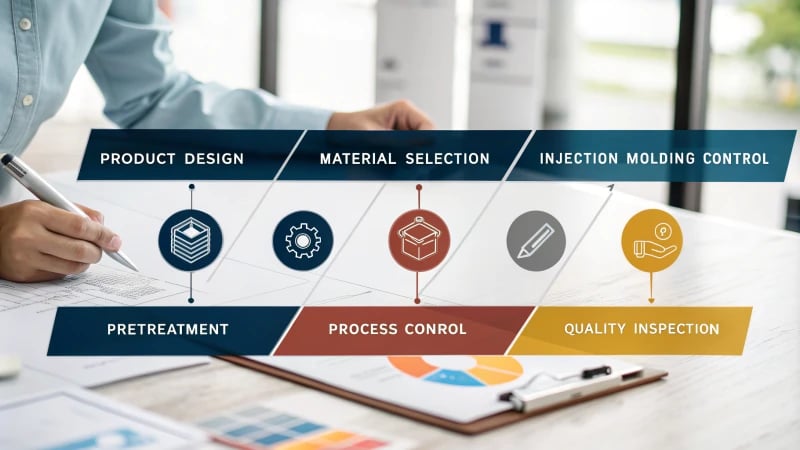
Product Design Considerations
I soon understood that making shapes simpler and avoiding sharp edges was essential for a smooth finish. It’s like shaping clay – rounded edges allow paint to cover nicely. My work with plastic housings11 benefited greatly from this, saving a lot of time.
Consideration | Description |
---|---|
Shape | Avoid sharp corners |
Texture | Plan texture direction |
Material Selection
Choosing materials is crucial. It’s like picking ingredients for a dish. ABS is usually my favorite for plating due to its good bond with metal compared to PP. Thermal properties are crucial too; warped pieces from heat are a nightmare.
- ABS vs PP: ABS bonds better for plating.
- Thermal Properties: Pick materials stable in heat.
Injection Molding Process Control
Adjusting settings for injection molding was tough at first. However, tweaking temperature, pressure, and speed really improves the surface. It’s like fine-tuning an instrument; every little detail counts.
Parameter | Impact |
---|---|
Temperature | Affects fluidity |
Pressure | Can cause defects |
Pre-treatment Techniques
Early on, I overlooked pretreatment’s value. Removing impurities with ultrasonic cleaning or chemical baths is like preparing a clean canvas. This step very much helps the coating stick well.
- Cleaning: Combine methods for deep cleaning.
- Roughening: Experiment for best results.
Precise Process Parameter Control
I learned that even small changes in spraying distance or thickness cause bad finishes. Precision is key. It’s like making a perfect espresso shot. Careful attention to each part is needed for top quality.
Quality Inspection and Control
Strict inspection standards are now instinctive. Tools like gloss meters and adhesion testers confirm high quality. It’s like double-checking a letter before mailing. Every aspect is vital.
- Gloss Meter: Checks product shine.
- Adhesion Tester: Confirms coating sticks well.
Using Statistical Process Control12 guides me to maintain steady quality. It helps map out the process, predicting and fixing problems early. A reliable map is very helpful.
ABS plastic is better for plating than PP plastic.True
ABS plastic deposits metal ions better, enhancing plating quality.
Sharp inner corners improve coating thickness uniformity.False
Sharp corners cause uneven coating thickness and stress concentration.
How Can Quality Inspection and Control Systems Improve Outcomes?
Ever experienced that annoying time when a product fails to perform as you thought it would?
Quality inspection and control systems improve results by continually finding defects. These systems keep processes consistent and increase product reliability. Manufacturers offer high-quality products because these systems regularly watch and adjust production methods.
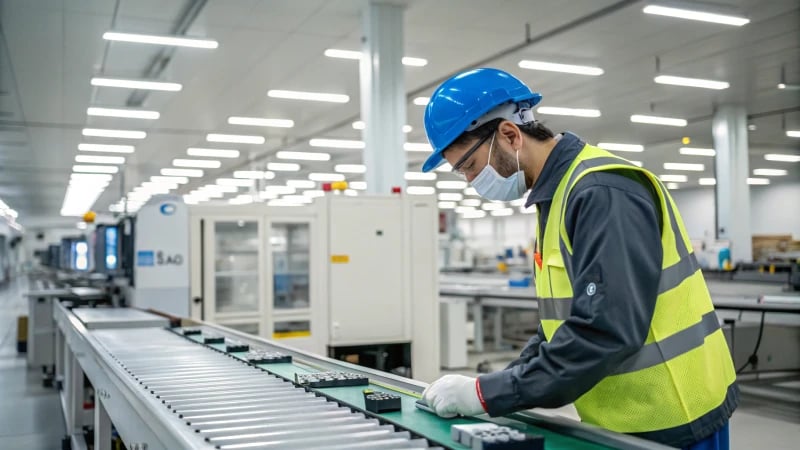
Benefits of Quality Inspection Systems
In my early industry days, I missed a small defect that led to a huge product recall. That mistake taught me the huge importance of a quality inspection system. Now, with real-time checks, defects get caught before they grow into big problems. This isn’t just about skipping costly recalls; it’s about cutting waste and making customers happy. In fields like cars and planes, safety standards are very strict.
Implementing a robust quality inspection system can drastically improve product reliability and customer satisfaction. By integrating real-time monitoring, manufacturers can identify and address defects early in the production process. This proactive approach not only reduces waste but also minimizes costly recalls13.
A well-designed inspection system ensures compliance with industry standards and regulations. This compliance is crucial for maintaining market credibility and avoiding legal repercussions.
Creating Process Consistency
Consistency truly matters. Quality control systems bring a steady flow to manufacturing by setting precise test rules.
Quality control systems contribute to process consistency by establishing detailed testing standards at various stages of production.
Phase | Action | Outcome |
---|---|---|
Design | Rational structural design | Even coating distribution |
Material Selection | Match material with design needs | Optimal surface treatment |
Injection Molding | Optimize parameters (temperature, pressure) | Smooth product surface |
During the product design phase14, specific guidelines are set to ensure the product is designed for manufacturability.
Impact on Product Design and Material Choice
Material choice is crucial in design. Match plastic to the product’s conditions and needs. I once mistakenly chose ABS over PP for plating. That choice made a big difference because of metal compatibility.
During the product design phase, considerations such as rational structural design help avoid defects like uneven coating thickness.
By setting clear inspection criteria in the early stages, issues can be preemptively addressed, ensuring smoother downstream processes.
This approach aligns with a broader systematic strategy15 in quality management.
Monitoring and Feedback Systems
Continuous monitoring and feedback really changed things for me. Statistical Process Control (SPC) techniques let me spot trends and fix issues before they grow.
Here’s how a feedback loop works:
- Inspection: Check regularly at important stages.
- Analysis: Use SPC to look at data.
- Adjustment: Change processes as needed.
- Verification: Check improvements with follow-up inspections.
Continuous monitoring and feedback loops are essential components of effective quality control systems. Utilizing techniques like Statistical Process Control (SPC), manufacturers can predict quality trends and identify potential issues before they escalate.
By maintaining this loop, manufacturers can enhance their process efficiency while maintaining high-quality standards through precise control of process parameters.
ABS plastic is better for plating than PP plastic.True
ABS plastic deposits metal ions better, improving plating quality.
Sharp inner corners are ideal for surface treatments.False
Sharp corners cause uneven coating thickness and stress concentration.
Conclusion
Enhancing surface treatment quality in injection molded plastics requires careful design, material selection, precise molding control, effective pre-treatment, and thorough quality inspection to ensure optimal performance and aesthetics.
-
Discover how design choices influence coating quality, reducing potential defects. ↩
-
Learn how controlling injection molding parameters affects the final product’s surface finish. ↩
-
Learn Analysis of coating treatment of injection molding products. ↩
-
Explore how thermal expansion affects materials during surface treatments like curing and heat transfer. ↩
-
Understand how to design products with texture treatments in mind, ensuring precise replication and ease of manufacturing. ↩
-
Discover why controlling injection molding parameters is crucial for achieving smooth surfaces ready for further treatment. ↩
-
Discover how temperature control enhances plastic melt fluidity, ensuring smooth surfaces. ↩
-
Learn techniques for optimizing injection parameters to prevent defects. ↩
-
Find out about high-precision equipment that maintains texture quality. ↩
-
Explore how SPC analyzes and predicts trends for better quality outcomes. ↩
-
Rounded edges ensure even coating distribution during surface treatments, preventing issues like stress concentration. ↩
-
SPC helps predict quality trends and detect potential issues early, ensuring consistent surface treatment quality. ↩
-
Discover how early defect detection can save costs and prevent product recalls. ↩
-
Learn why designing for manufacturability is crucial for product success. ↩
-
Understand the role of systematic strategies in improving quality management. ↩