Draft angles are a critical aspect of mold design, influencing both the manufacturing process and the quality of the final product.
To ensure accurate draft angles in mold design, employ 3D modeling software such as SolidWorks and simulation tools like Moldflow to model and analyze product demolding. This ensures optimal draft angles are set, preventing issues such as product deformation during ejection.
While the initial setup of draft angles is essential, ongoing adjustments and considerations throughout the mold design and manufacturing process can significantly enhance the accuracy and efficiency of production. Dive deeper into each stage to learn how to implement these best practices effectively.
3D modeling software can simulate product demolding.True
Software like Moldflow simulates demolding, not 3D modeling software.
Draft angle accuracy is crucial for mold design.True
Ensuring accurate draft angles prevents issues like part sticking.
What Role Does 3D Modeling Play in Setting Draft Angles?
Discover how 3D modeling revolutionizes the setting of draft angles in product design.
3D modeling plays a crucial role in setting draft angles by providing accurate simulations and analyses, enabling designers to optimize mold design and ensure efficient product demolding.
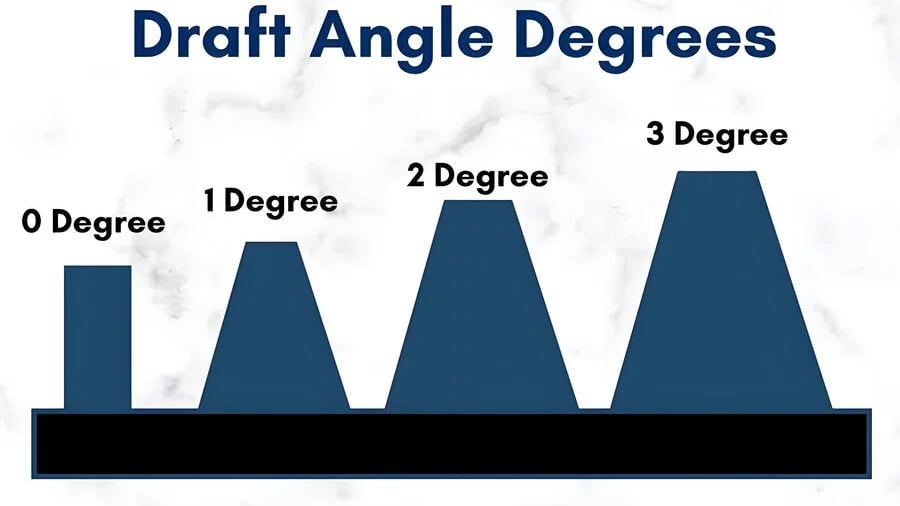
Accurate Product Design and Analysis
3D modeling software like Pro/E, UG, and SolidWorks are vital tools in accurately designing product geometry, including complex surfaces and internal structures. In the early stages of mold design, these tools help set the draft angle according to product shape and size. For example, if a product has inverted parts, the software’s draft analysis function can simulate demolding at various draft angles, identifying the optimal inclination. This precision is essential for maintaining product quality and reducing production costs1.
Product Demolding Simulation Analysis
Simulation tools such as Moldflow allow designers to simulate the demolding process. By inputting material properties and mold parameters, these tools predict potential demolding issues like excessive clamping force or deformation. Based on these results, designers can optimize the draft angle to meet demolding requirements. For instance, if a certain part is difficult to demold due to insufficient draft angle, increasing the angle can resolve this issue, ensuring smooth production and preventing defects2.
Reasonable Mold Structure Design
Designing a mold’s parting surface and integrating mechanisms like sliders or lifters are crucial steps in setting draft angles. A well-designed parting surface should facilitate easy demolding along the mold opening direction. For products with inclined surfaces, positioning the parting surface at the largest contour can leverage the shape characteristics, simplifying the draft angle setting. Similarly, designing lifter mechanisms involves precise calculations of angle and stroke to provide adequate force and an accurate draft angle during ejection, which is critical to avoid product damage3.
Mold Manufacturing Process Planning
The mold manufacturing process requires meticulous planning to ensure draft angles are processed with precision. For high-precision molds used in electronics, processing accuracy must reach ±0.01mm using CNC machining centers. Regular inspections with high-precision equipment like CMMs ensure that any deviation in the draft angle can be corrected promptly through methods such as EDM or grinding. This meticulous attention to processing accuracy ensures high-quality molds that meet design requirements, thus enhancing production efficiency4.
3D modeling software aids in draft angle optimization.True
3D modeling software like SolidWorks helps design optimal draft angles for molds.
Moldflow cannot predict demolding issues.False
Moldflow simulates and predicts potential demolding problems, aiding design.
How Does Simulation Software Aid in Draft Angle Optimization?
Draft angle optimization is crucial in mold design, ensuring smooth demolding and reducing defects. Simulation software plays a pivotal role in this process.
Simulation software aids draft angle optimization by providing accurate analysis and predictions during mold design, using tools like Moldflow to simulate demolding and adjust angles as needed.
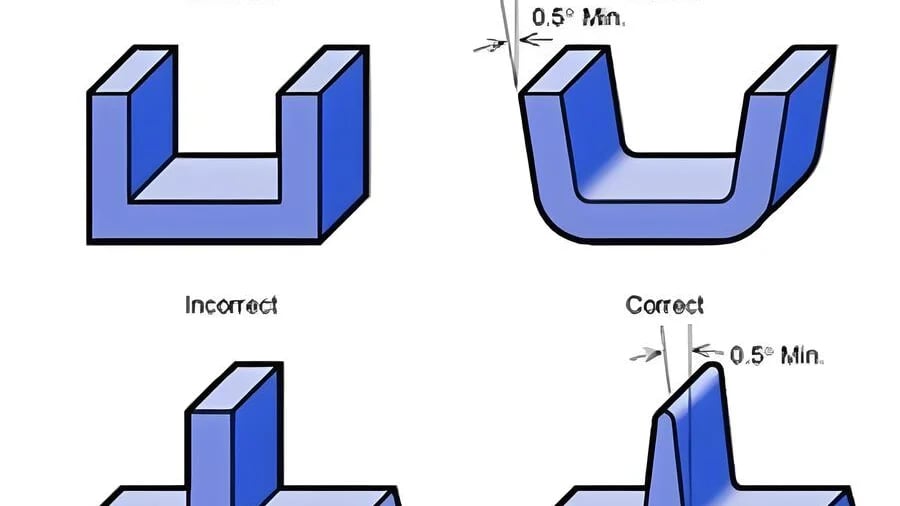
The Role of 3D Modeling Software
Accurate product design begins with 3D modeling software applications like Pro/E, UG, and SolidWorks. These tools allow designers to accurately model complex geometries, including intricate surfaces and internal structures. By pre-setting reasonable draft angles during the modeling phase, designers can anticipate how different angles will affect demolding. For instance, products with inverted parts can benefit from the software’s draft analysis function, which simulates demolding scenarios at various angles to identify optimal draft inclination5.
Product Demolding Simulation Analysis
Simulation software such as Moldflow offers insights into potential demolding challenges by simulating the process with specific material properties and mold structure parameters. This predictive analysis helps in identifying issues like excessive clamping force or deformation, allowing for draft angle adjustments to meet demolding requirements accurately. For example, if simulations reveal difficult demolding due to insufficient angles in certain sections, adjustments can be made to ensure seamless ejection6.
Designing Reasonable Mold Structures
Mold structure design significantly influences draft angle settings. The parting surface should be designed to align with the largest contour of inclined surfaces, leveraging the product’s shape to simplify angle adjustments and ensure accuracy. In cases where conventional methods fail, sliders or lifters are designed with precise calculations of mating dimensions and trajectories to provide sufficient demolding force and appropriate draft angles. This meticulous design process ensures that mechanisms7 like lifters can prevent strain or damage during product ejection.
Planning the Mold Manufacturing Process
Precision in processing is paramount for draft angle accuracy. High-precision molds require CNC machining centers with tolerances of ±0.01mm. During manufacturing, precision tools and cutting parameters ensure mold surface quality. Regular inspections using high-precision equipment like CMM detect any deviations, allowing for timely corrective measures such as EDM or grinding to maintain draft angle precision. These steps are integral in maintaining mold quality and functionality throughout the production process8.
3D modeling software ensures precise product geometry.True
Software like SolidWorks models complex surfaces accurately, aiding design.
Simulation software cannot predict demolding issues.False
Tools like Moldflow simulate demolding, identifying potential problems.
Why Is Mold Structure Design Important for Draft Angle Accuracy?
Precision in mold structure design ensures products are manufactured efficiently and defect-free, especially regarding draft angles.
Mold structure design is crucial for draft angle accuracy because it directly impacts the ease of demolding and product integrity. Using 3D modeling and simulation software allows designers to preset and optimize draft angles, ensuring smooth production processes and high-quality outcomes. Proper mold design reduces defects and enhances efficiency.
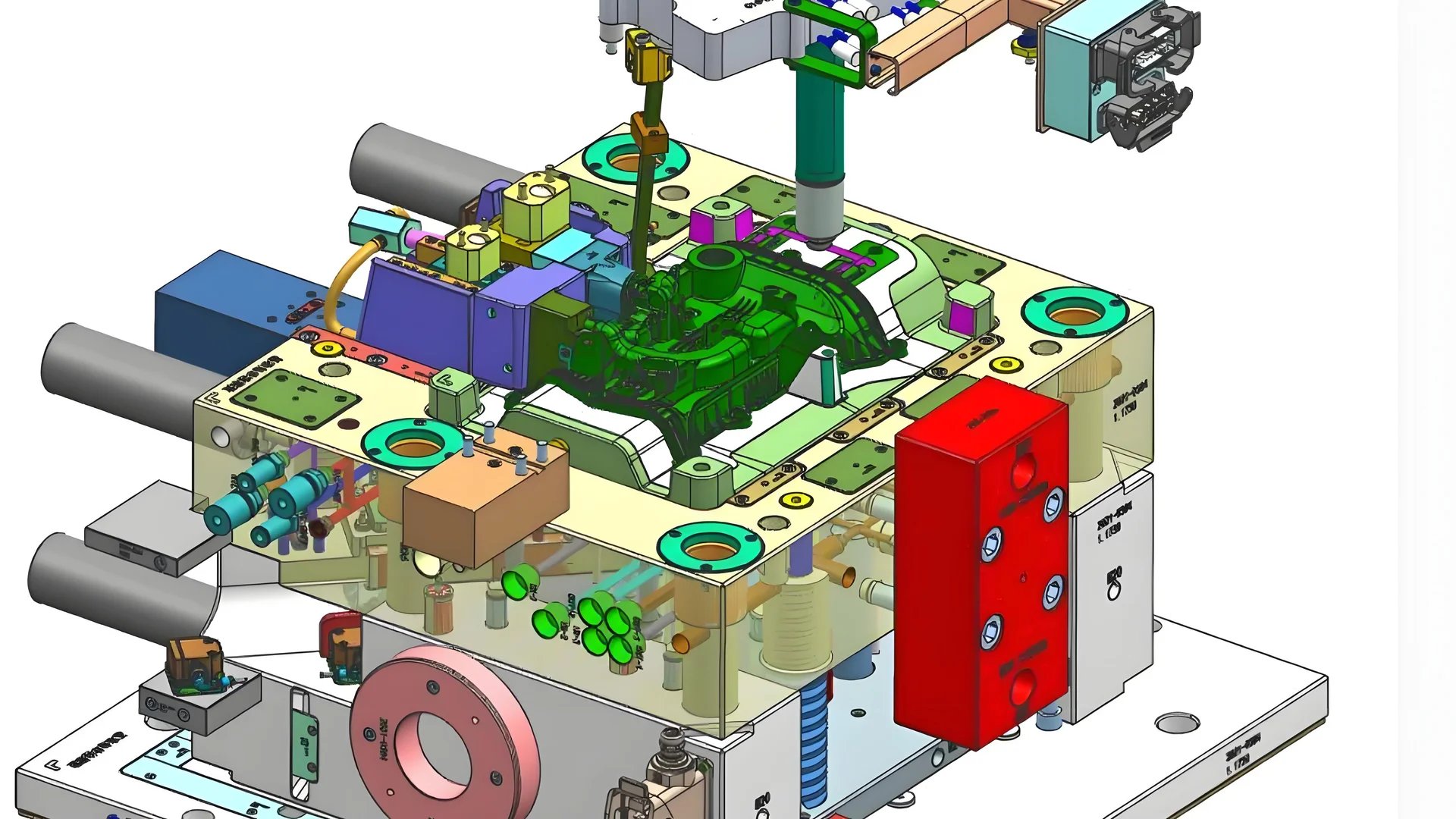
Importance of Accurate Product Design and Analysis
In the initial stages of mold design, precise product modeling is essential. Professional 3D modeling software such as Pro/E, UG, and SolidWorks are pivotal in crafting detailed product designs. These tools allow for the accurate representation of complex surfaces and internal structures, which is crucial for determining the appropriate draft angle. For instance, the 3D modeling software application9 offers a draft analysis feature to simulate various demolding scenarios, facilitating the determination of the optimal draft angle for products with intricate designs.
Furthermore, product demolding simulation analysis is performed using advanced software like Moldflow. By inputting specific material properties and mold parameters, potential demolding issues such as excessive clamping force or product deformation can be predicted. Adjustments to the draft angle based on these simulations ensure the mold meets the necessary requirements for seamless demolding.
Role of Reasonable Mold Structure Design
A critical aspect of mold structure design is the strategic planning of the molding surface. The location and shape of the molding surface significantly affect the draft angle settings. A well-designed parting surface ensures that the product can be smoothly demolded in the direction of mold opening. For example, placing the parting line at the largest contour of inclined surfaces can leverage the product’s inherent shape, reducing difficulties in setting an accurate draft angle.
When dealing with structures that conventional methods cannot demold, such as inverted buckles, specialized mechanisms like sliders or lifters are designed. These mechanisms require precise calculation of dimensions and trajectories to deliver sufficient demolding force and accurate draft angles. For instance, designing the lifter mechanism10 involves careful calculation of its angle and stroke to ensure flawless demolding.
Mold Manufacturing Process Planning
The manufacturing process demands strict adherence to processing accuracy requirements. High-precision molds, especially for electronic equipment injection molds, necessitate equipment precision of up to ±0.01mm. This ensures that draft angles are processed with accuracy using CNC machining centers, high-precision tools, and appropriate cutting parameters to maintain mold surface quality.
Routine inspections with high-precision equipment such as CMM are conducted to verify draft angle accuracy throughout manufacturing. If deviations occur, corrective measures like electric discharge machining (EDM) or grinding are employed to align with design specifications. An efficient detection and correction strategy11 is vital to maintaining accuracy during mold production.
3D modeling software ensures accurate product geometry.True
Software like SolidWorks models complex surfaces accurately, aiding design.
Draft angles are irrelevant in mold design.False
Draft angles are crucial for demolding, preventing deformation and defects.
What Are the Best Practices for Monitoring and Correcting Draft Angles?
Ensuring the proper draft angle is crucial in manufacturing processes like injection molding. Here’s how to monitor and correct them effectively.
Use 3D modeling software for initial draft angle setting, simulate demolding with tools like Moldflow, design suitable mold structures, and employ precise manufacturing processes to maintain accuracy.
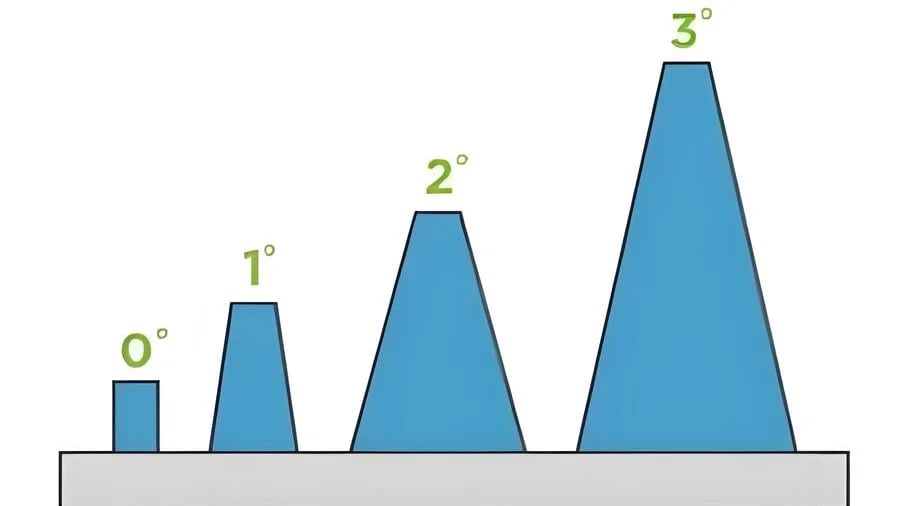
Utilizing 3D Modeling Software
In the early stages of mold design, employing professional 3D modeling software such as Pro/E, UG, or SolidWorks is essential. These tools allow for accurate product design and analysis by simulating various draft angles. Pre-setting reasonable draft angles based on the product’s geometry is crucial. For example, products with inverted parts benefit significantly from draft analysis functions12 that simulate different demolding scenarios to determine optimal draft inclinations.
Simulating Product Demolding
Simulation software, like Moldflow, plays a pivotal role in predicting potential demolding issues. By inputting plastic material properties and mold parameters, the software identifies problems such as excessive clamping force or product deformation. Adjustments to the draft angle can then be made to meet demolding requirements. Increasing the draft angle in problem areas can significantly enhance the ease of demolding.
Designing Reasonable Mold Structures
The design of the molding surface directly impacts draft angle settings. A well-planned parting surface ensures that products are smoothly demolded in the direction of mold opening. Products with inclined surfaces benefit when the parting surface aligns with the largest contour of these surfaces. For complex structures, slider and lifter mechanisms13 should be designed with precision to provide sufficient demolding force and appropriate draft angles.
Implementing Precision in Mold Manufacturing
Accurate draft angles are achieved through meticulous process planning. High-precision equipment, like CNC machining centers, should be used to achieve tight tolerances, typically ±0.01mm for high-precision molds. During the machining process, using suitable cutting parameters and high-precision tools ensures quality and accuracy.
Conducting Regular Inspections
Developing a comprehensive inspection plan is essential for maintaining draft angle accuracy. Regular checks using high-precision equipment such as CMMs ensure compliance with design specifications. If deviations are detected, corrective actions like electric discharge machining (EDM) or grinding can restore the required draft angles. This proactive approach prevents potential issues in the final product demolding process14.
3D modeling software ensures accurate draft angles.True
Software like SolidWorks models products, optimizing draft angles for demolding.
Moldflow cannot simulate product demolding issues.False
Moldflow predicts demolding problems and helps optimize draft angles.
Conclusion
Accurate draft angles in mold design are ensured through 3D modeling, simulation tools, reasonable mold structure design, and meticulous manufacturing processes to prevent defects and enhance production efficiency.
-
Learn how 3D modeling optimizes processes to cut costs. ↩
-
Discover techniques to avoid defects in molding. ↩
-
Find effective ways to protect products during molding. ↩
-
Explore methods to boost efficiency through precise design. ↩
-
Understand how SolidWorks aids in precise draft angle analysis. ↩
-
Learn how Moldflow predicts and resolves demolding challenges. ↩
-
Explore designing sliders and lifters for effective demolding. ↩
-
Discover techniques ensuring high precision in mold manufacturing. ↩
-
Learn how 3D modeling software aids in precise draft angle design. ↩
-
Discover how lifter mechanisms contribute to accurate demolding. ↩
-
Understand strategies for maintaining draft angle precision. ↩
-
Learn how to effectively simulate and analyze draft angles. ↩
-
Explore advanced techniques for designing mold structures. ↩
-
Discover inspection strategies to ensure successful demolding. ↩