DESIGN
blog & article
read our latest newsletter
Whether you’re curious about material selection, product design, mold design, mold making and injection molding, feel free to ask us anything. Our team is ready to provide the guidance and insights you need.
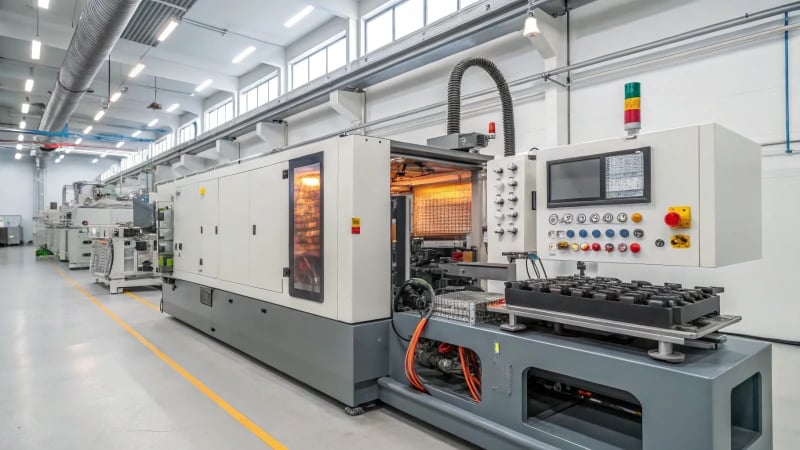
What Key Design Considerations Ensure Success in Injection Molding High-Temperature Parts?
This article explores essential design considerations for injection molding high-temperature parts. It emphasizes the importance of selecting appropriate materials like PPS and PEEK based on temperature tolerance, ensuring uniform wall thickness to prevent thermal stress, and implementing effective heat dissipation ...
DESIGN
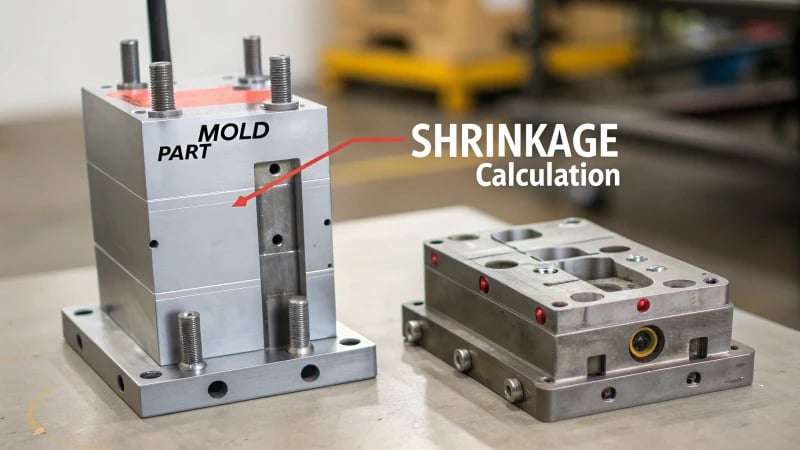
How Do You Calculate Shrinkage in Injection Molding?
Calculating shrinkage in injection molding is crucial for achieving accurate part dimensions. This article outlines the formula for shrinkage calculation and discusses factors influencing it, including material properties, mold design considerations, and processing conditions. By understanding these elements, designers can ...
DESIGN
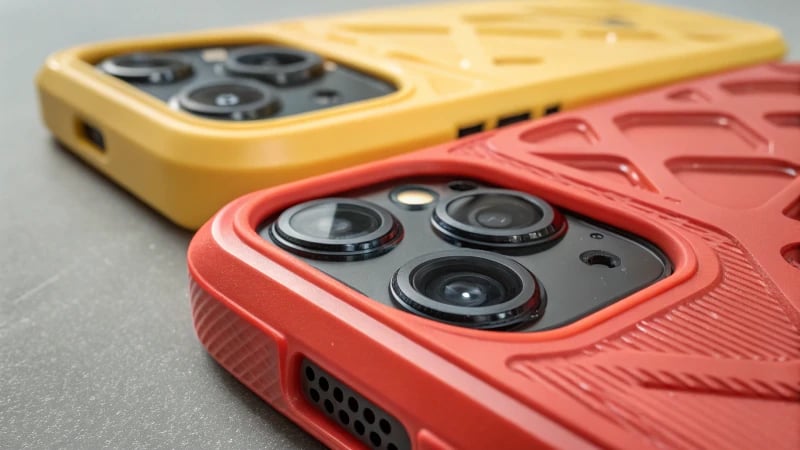
What Key Factors Should You Consider When Designing Molds for Overmolding Applications?
Designing molds for overmolding applications requires careful consideration of several key factors. Material compatibility is crucial to ensure proper bonding and prevent delamination. Precise mold design enhances product quality by ensuring accurate dimensions and effective venting. Additionally, optimizing process parameters ...
DESIGN
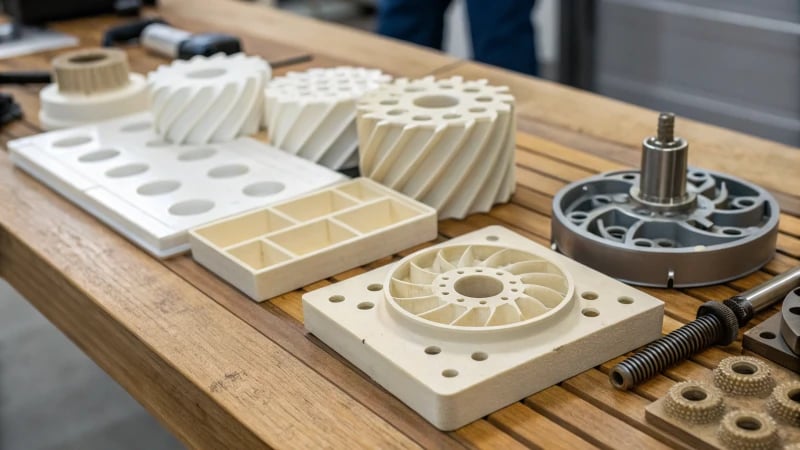
What Are the Best Techniques for Creating Complex Structures in Injection Molding?
This blog post delves into the best techniques for creating intricate structures in injection molding. Key methods discussed include mold flow analysis to optimize material usage and reduce defects, the use of advanced materials for enhanced performance and durability, 3D ...
DESIGN
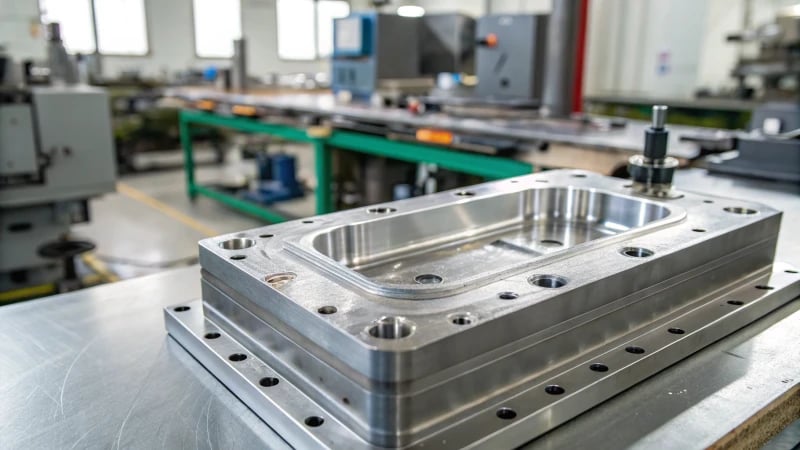
How Do You Design Molds for Achieving High-Gloss Surface Finishes?
Creating high-gloss finishes in molded parts is an intricate process that combines art and engineering. Key factors include choosing the right materials like stainless steel or aluminum, employing advanced polishing techniques, and adhering to industry standards such as SPI. Mold ...
DESIGN
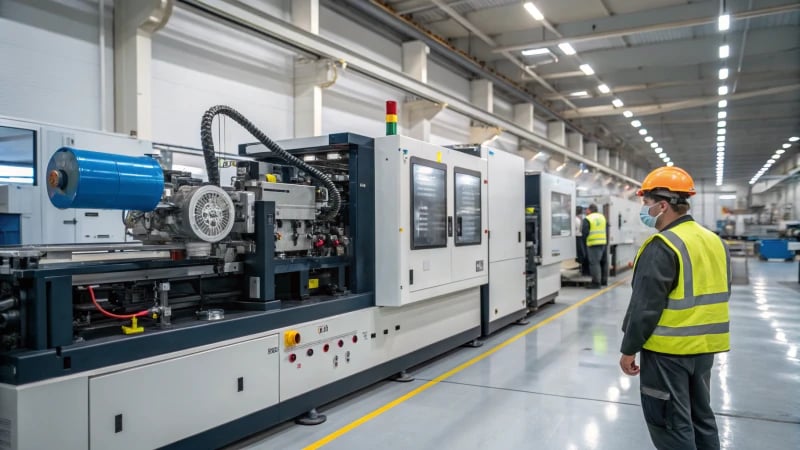
How Can Gas-Assisted Injection Molding Enhance Mold Design?
Gas-assisted injection molding revolutionizes traditional manufacturing by optimizing mold designs. This innovative technique reduces material usage, enhances surface finish, minimizes shrinkage, and allows for intricate geometries. It significantly improves production efficiency while maintaining product integrity. Designers can achieve lightweight components ...
DESIGN
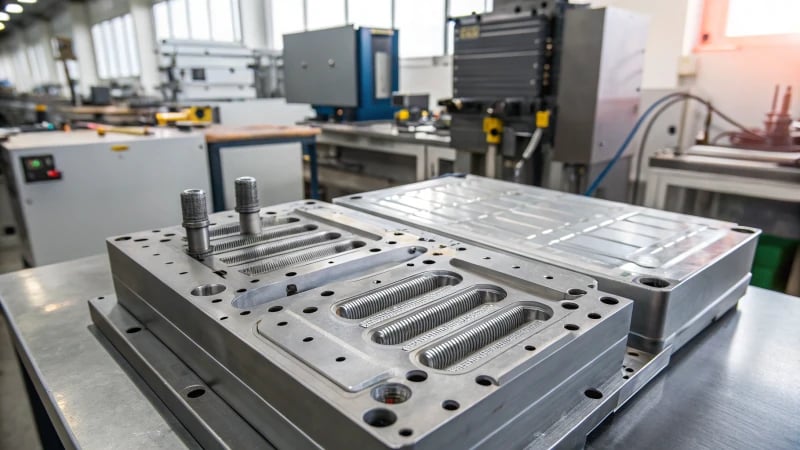
How Can Venting Enhance the Efficiency of Injection Mold Designs?
Venting plays a vital role in injection mold design by facilitating the escape of trapped air and gases during the injection process. This essential step helps reduce defects such as burn marks and voids, improves material flow, and optimizes cycle ...
DESIGN
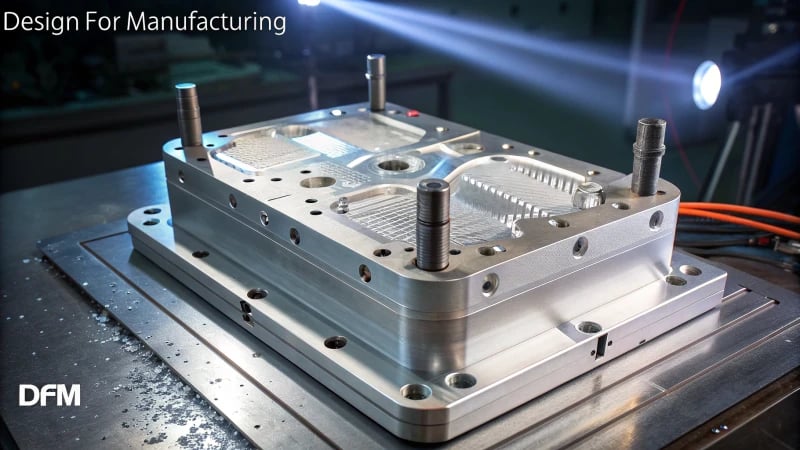
How Can DFM Principles Enhance Injection Mold Design?
Design for Manufacturing (DFM) principles significantly improve injection mold design by streamlining production processes, minimizing costs, and enhancing product quality. By focusing on simplicity, standardization, and ease of assembly, DFM helps designers create molds that are not only functional but ...
DESIGN
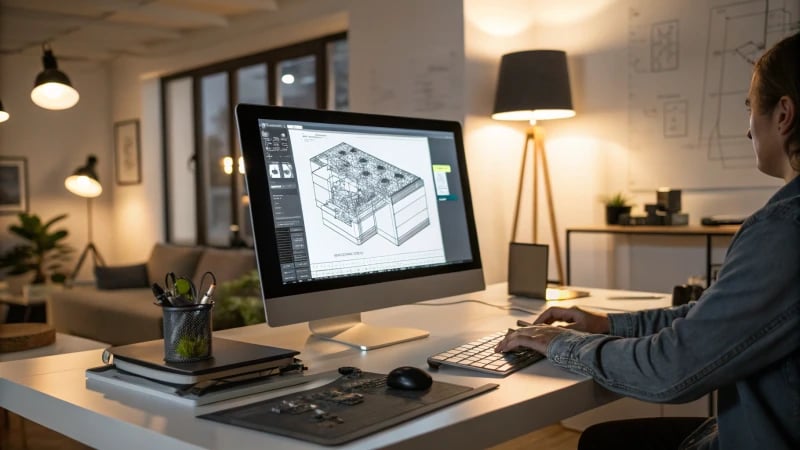
How Does CAD Software Enhance the Design of Injection Molds?
CAD software significantly enhances the design of injection molds by improving precision and efficiency. Key features include 3D modeling for accurate visualization, simulation tools to predict performance, and automated documentation that streamlines communication. These capabilities not only reduce design time ...
DESIGN
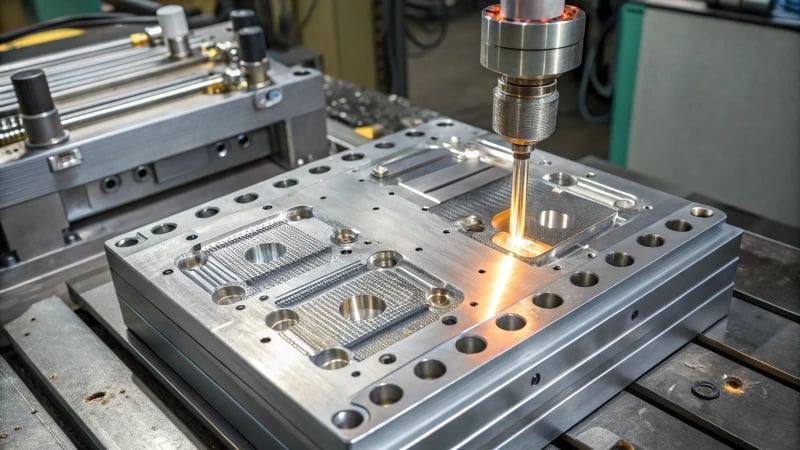
What Are the Essential Factors in Designing Injection Molds for High-Volume Production?
Designing injection molds for high-volume production involves a blend of art and science. Essential factors include careful material selection, optimizing cooling systems, ensuring uniform wall thickness, and precise construction. Utilizing advanced technologies like CAD software streamlines the design process by ...
DESIGN
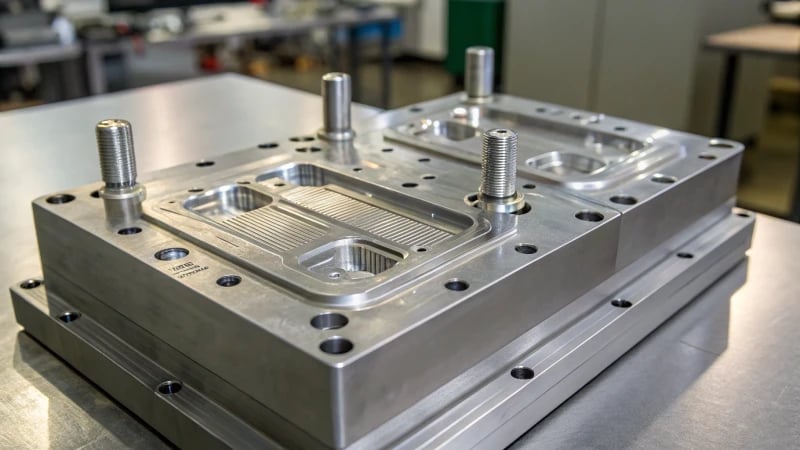
How Can You Design Effective Molds for Thin-Wall Injection Molding?
Designing effective molds for thin-wall injection molding involves several key strategies. Focus on optimizing material flow and ensuring uniform wall thickness to prevent defects like warping or shrinkage. Precise temperature control is crucial for consistent results, while selecting appropriate materials ...
DESIGN
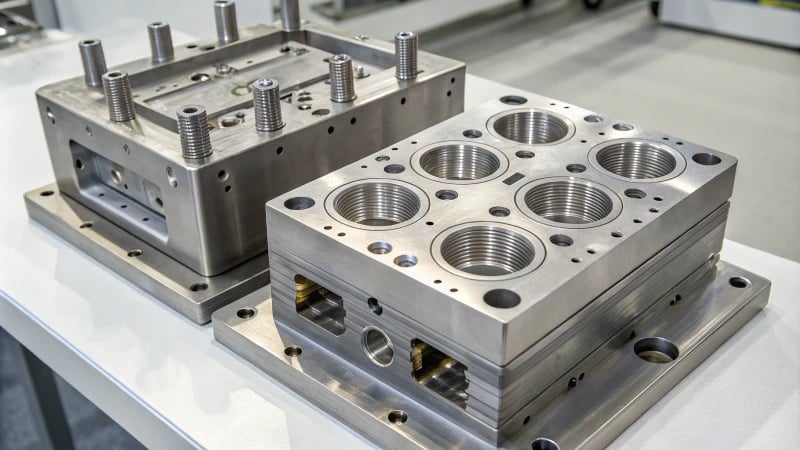
What Are the Essential Factors in Designing Multi-Cavity Molds?
Designing multi-cavity molds requires understanding essential factors such as material selection, cavity balance, cooling system design, and efficient ejection methods. These elements are crucial for achieving high production efficiency and consistent product quality. Material choices impact durability and cost-effectiveness while ...
DESIGN
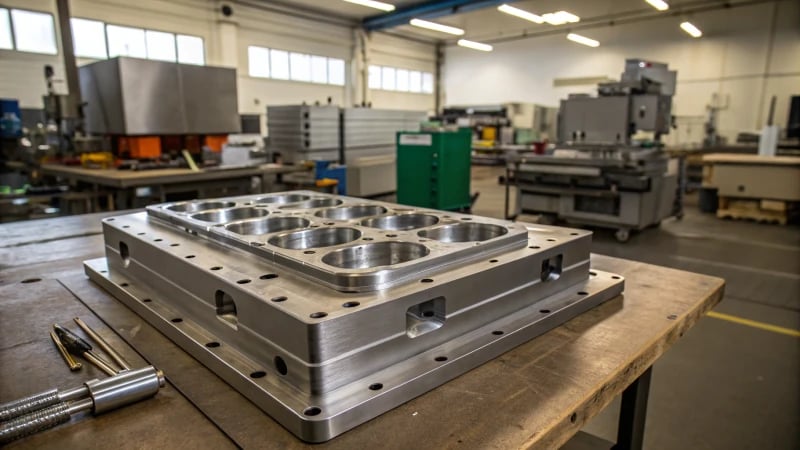
What Are the Key Factors to Consider When Designing Multi-Cavity Molds?
When designing multi-cavity molds, focus on optimizing cavity layout, balancing material flow, implementing effective cooling strategies, and minimizing defects. These key factors ensure efficiency and high-quality output in large-scale manufacturing processes. By mastering these elements, designers can significantly improve production ...
DESIGN
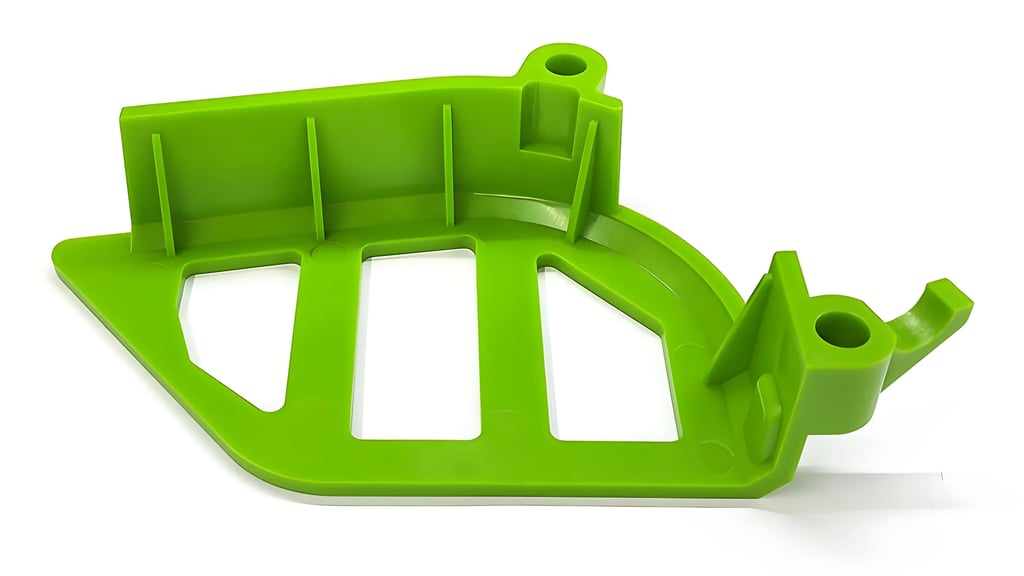
How Do Plastic Ribs Enhance Injection-Molding Design?
Plastic ribs are crucial in injection-molding design, offering essential structural support while minimizing material use. They enhance part stability, reduce warping, and allow for thinner designs without compromising strength. By optimizing rib dimensions and placement, designers can improve product durability ...
DESIGN
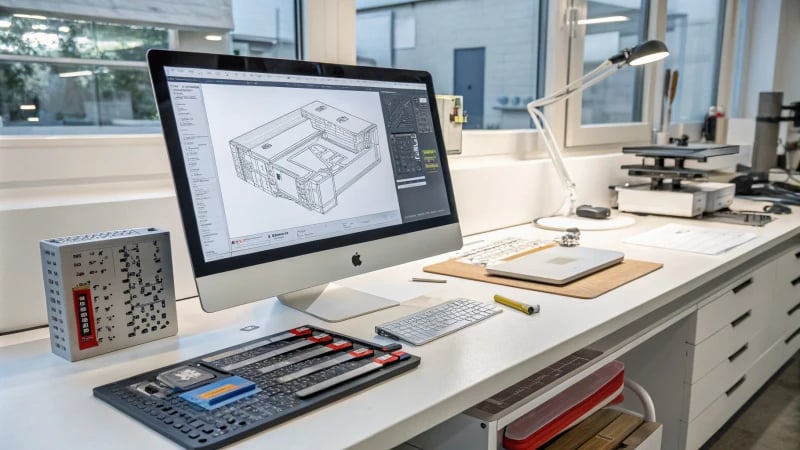
How Can CAD/CAM Enhance Your Mold Design Process?
CAD/CAM technology revolutionizes the mold design process by improving accuracy, reducing lead times, and facilitating collaboration. This integration allows designers to create intricate molds with minimal errors while optimizing workflows and cutting costs. By automating complex calculations and enhancing visualization ...
DESIGN
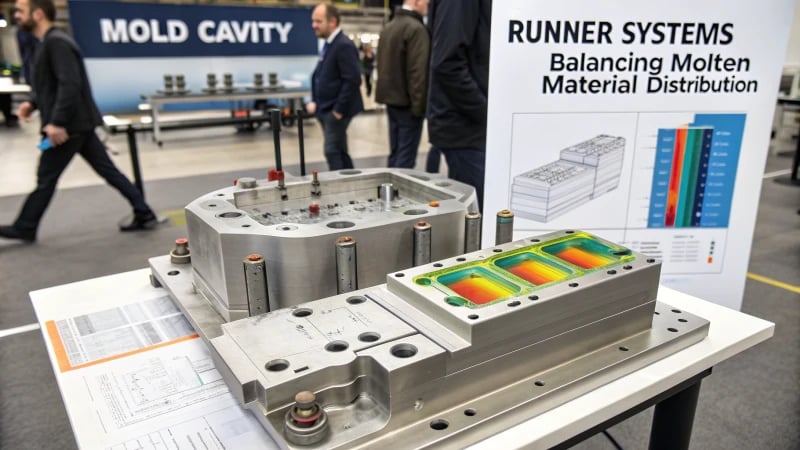
How Can You Efficiently Balance Runners in Multi-Cavity Molds?
Balancing runners in multi-cavity molds is crucial for ensuring even distribution of molten plastic, which directly impacts part quality and production efficiency. Utilizing simulation software can predict flow patterns, allowing designers to optimize runner systems effectively. This article explores the ...
DESIGN
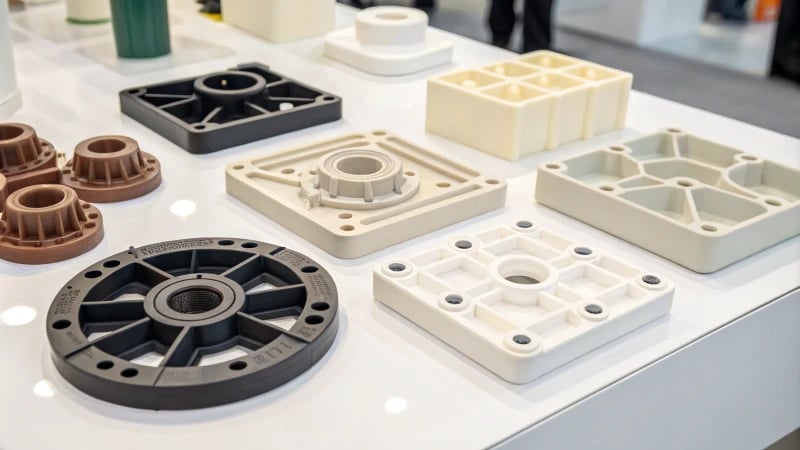
How Can You Design Injection Molded Parts for Seamless Assembly?
This blog post explores effective strategies for designing injection molded parts that ensure seamless assembly. Key principles include maintaining uniform wall thickness, incorporating draft angles, optimizing rib design, and selecting appropriate materials. The importance of tolerances in engineering is highlighted ...
DESIGN
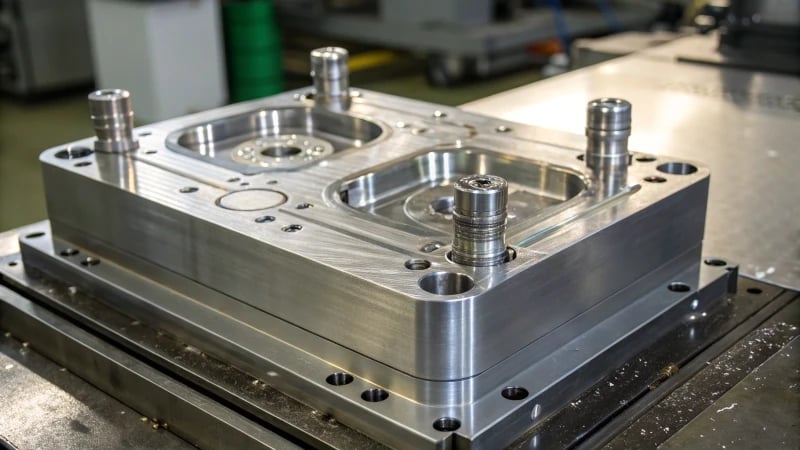
What Are the Best Practices for Designing Overmolding in Multi-Step Processes?
Designing overmolding in multi-step processes requires careful consideration of material compatibility, mold design, and process parameters. This guide explores essential techniques such as surface preparation and adhesion methods to ensure strong layer bonding and optimal product performance. By focusing on ...
DESIGN
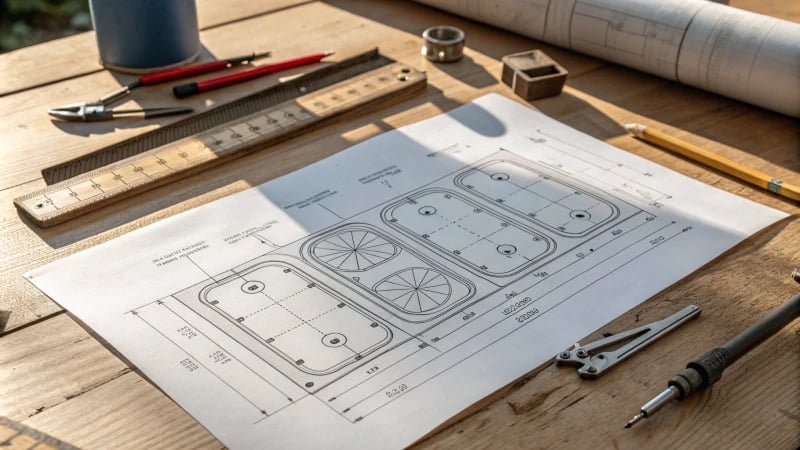
What Are the Essential Tips for Effective Mold Design?
This blog post explores essential tips for effective mold design, emphasizing the importance of understanding material properties, optimizing cooling channels, and ensuring proper venting. These strategies are crucial for improving production efficiency and product quality in industries like consumer electronics. ...
DESIGN
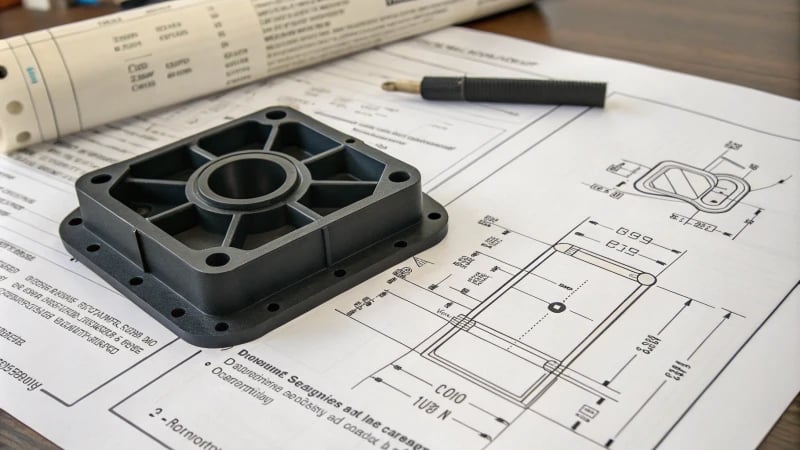
What Factors Should You Consider When Choosing Plastic B Side Features?
When selecting plastic B side features, designers must consider various factors including material properties, structural integrity, manufacturability, and cost efficiency. Each element plays a crucial role in ensuring that designs are not only visually appealing but also functional and efficient ...
DESIGN
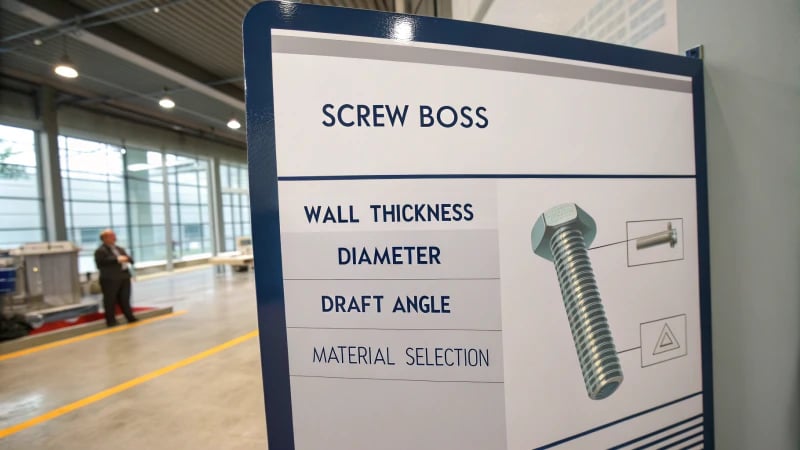
What Are the Key Steps to Designing an Effective Screw Boss?
This guide explores the essential steps for designing effective screw bosses in plastic components. Key factors include wall thickness, diameter, draft angles, and material selection. Proper design ensures structural integrity and efficient manufacturing processes while avoiding common pitfalls such as ...
DESIGN
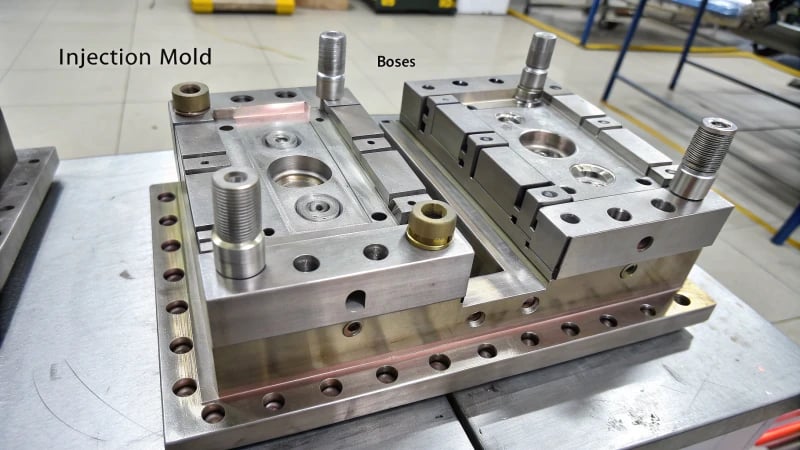
What Role Does a Boss Play in Injection Mold Design?
In injection mold design, bosses play a vital role by providing structural support, ensuring proper alignment and load distribution. These features are essential for accommodating fasteners and enhancing the durability of molded components. Understanding the guidelines for boss design—including dimensions, ...
DESIGN
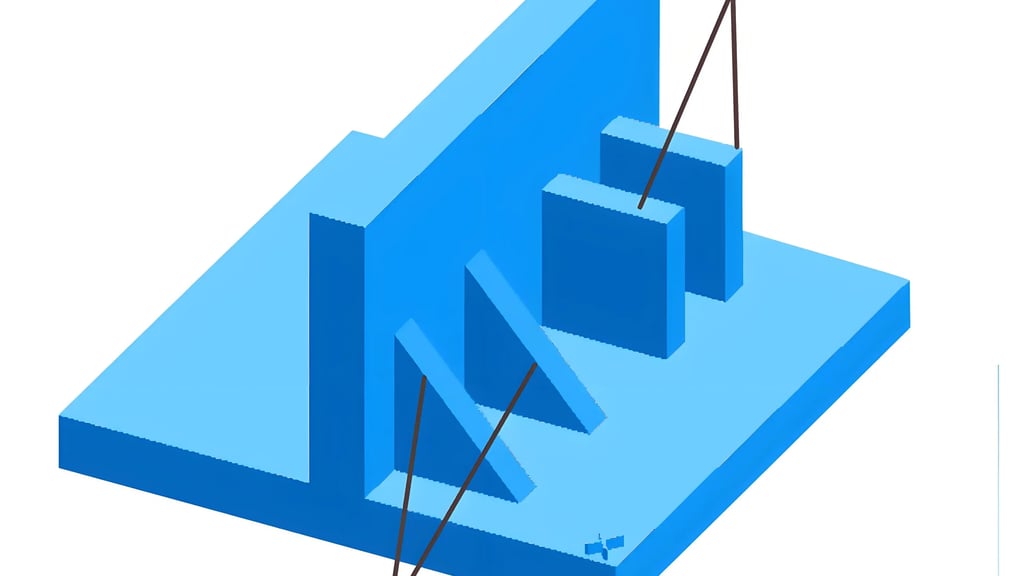
What is the Ideal Rib-to-Wall Ratio for Injection Molding?
Achieving the right rib-to-wall ratio in injection molding is essential for successful product design. Typically, this ratio should be between 0.5 to 0.6 times the nominal wall thickness, which helps minimize sink marks and maintain structural integrity. Factors such as ...
DESIGN
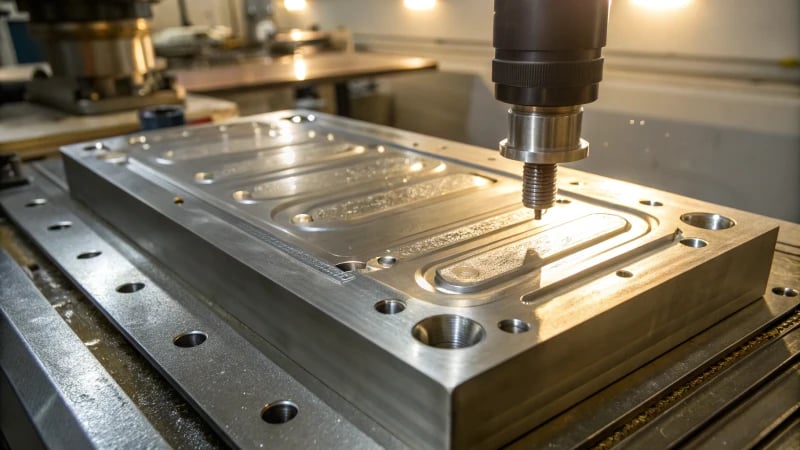
What Are the Best Design Techniques for Injection Mold Parting Surfaces?
Designing effective parting surfaces in injection molding is crucial for product quality. Key considerations include the shape of the plastic product, aesthetic requirements, processing ease, and venting needs. Simple shapes allow straightforward parting line placement, while complex shapes may require ...
DESIGN
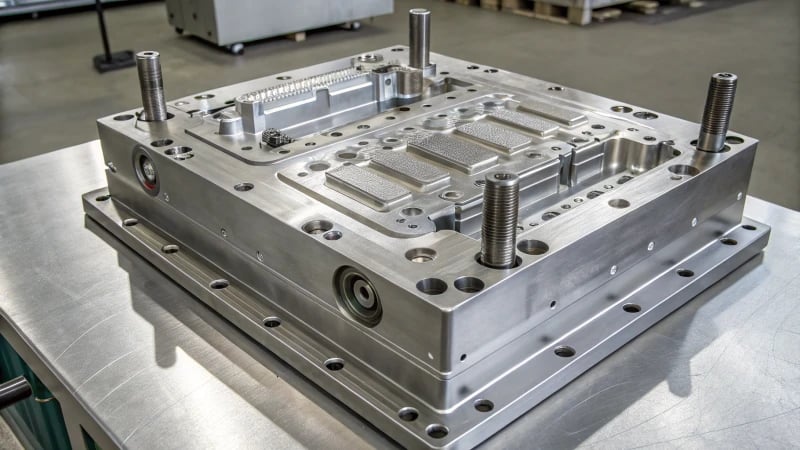
What Are the Key Advantages of Hot Runner Mold Design?
Hot runner molds revolutionize plastic manufacturing by significantly boosting production efficiency. They reduce cycle times from 20-30 seconds to 10-15 seconds, minimize material waste, and enhance product quality through consistent melt flow and temperature control. By selecting the right hot ...
DESIGN
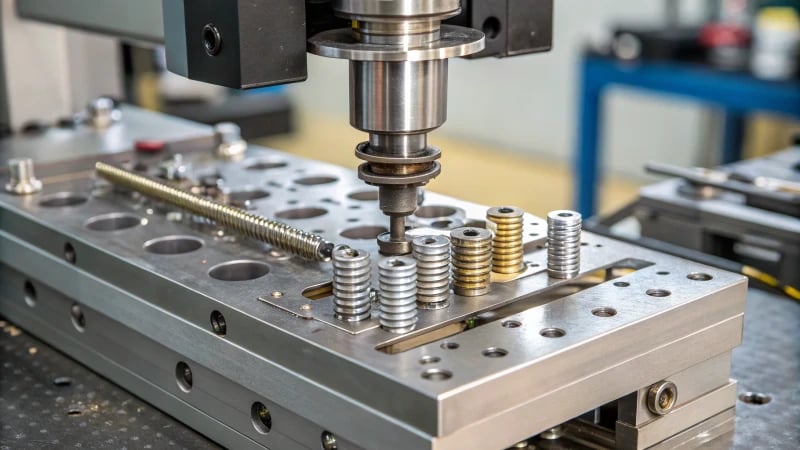
What Are the Best Practices for Designing the Ejection Mechanism of an Injection Mold?
Designing an effective ejection mechanism for injection molds involves understanding the product's shape and material properties, choosing suitable ejection methods like push rod or push plate, calculating necessary ejection forces, and ensuring proper positioning to avoid damage. Key considerations include ...
DESIGN
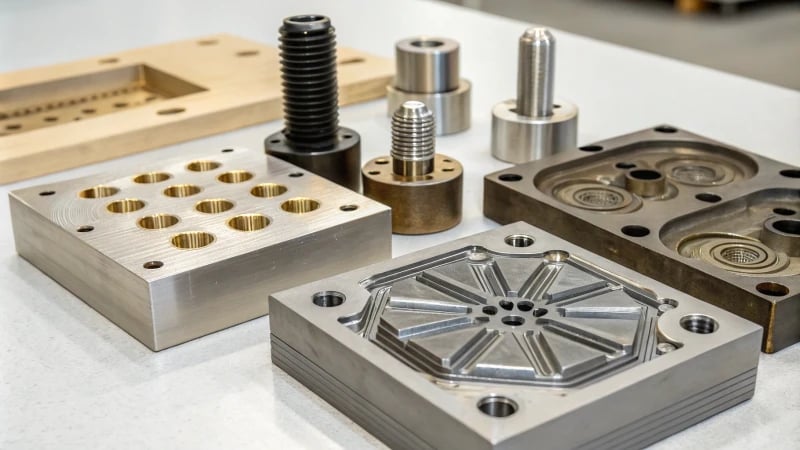
How Are Mold Inserts Designed and What Are Their Applications?
Mold inserts are crucial components in manufacturing that improve product quality and efficiency. Designed with precision, they enhance mold functionality by allowing intricate shapes and features without compromising the overall structure. Material selection plays a significant role in durability and ...
DESIGN
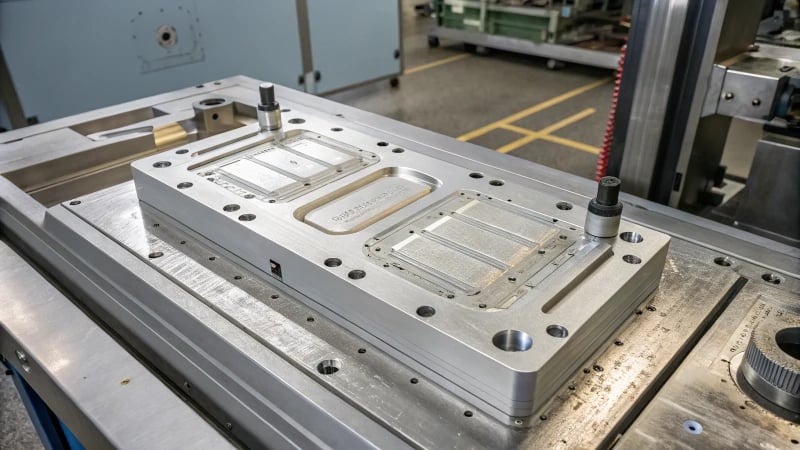
How Can You Ensure Uniform Wall Thickness in Your Injection Mold Design?
Ensuring uniform wall thickness in injection mold design is crucial for product quality. Key factors include gate design, runner systems, cooling layouts, and mold cavity adjustments to minimize defects.
DESIGN
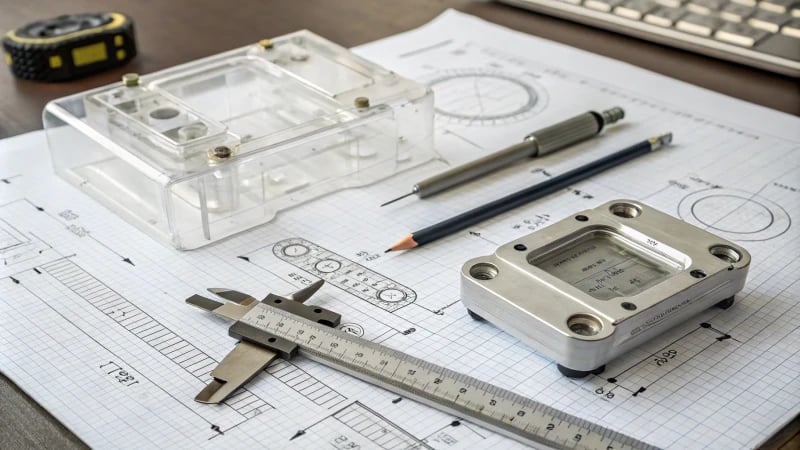
What Key Factors Should You Consider When Designing an Injection Mold?
Designing an injection mold requires careful consideration of product shape, size, wall thickness, precision needs, cooling system design, and cost management to ensure efficient production and high-quality outputs.
DESIGN
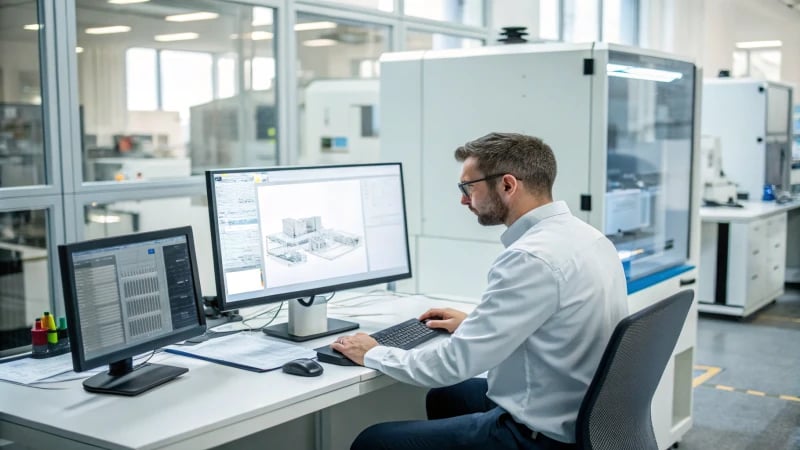
How Do Mold Flow Analysis Results Guide Injection Mold Design?
Mold flow analysis is essential for optimizing injection mold design, influencing gate placement, runner systems, and cooling channels. It enhances production efficiency and product quality by predicting potential defects.
DESIGN