Have you ever thought about why some products have very smooth edges and others seem a bit rough?
Optimal parting line quality depends on precise alignment, mold design, material flow, and temperature control. Proper venting, uniform pressure, and ideal processing conditions further ensure smooth, defect-free parting lines.
I remember my first project with parting lines. It felt like solving a complex puzzle. Each piece needed to fit perfectly. Mold design and material choice were important. I learned that mold accuracy is crucial. Even a tiny error causes flash or misalignment. It is like a jigsaw piece that does not belong.
Designing molds requires careful planning. Every curve and angle must be exact. Complex surfaces easily lead to errors without precision. Materials also play a crucial role. Choosing the right plastic is very important. It is like finding the perfect fabric for a bespoke suit. The plastic needs to mold well and shrink evenly.
Then came a breakthrough with injection parameters. Tuning pressure and speed really changed things. Adjustments were like turning knobs on an amplifier for perfect sound. These insights transformed my approach. I began to create parts that were functional and beautifully finished.
Mold accuracy is crucial for parting line quality.True
Precise mold design ensures minimal defects and optimal parting line quality.
Material properties do not affect parting lines.False
Material properties significantly impact the formation and quality of parting lines.
How Does Mold Accuracy Affect Parting Line Quality?
Have you ever wondered why some plastic items have smooth edges and others have ugly seams? Mold accuracy is very important in injection molding. It decides how your product looks and works.
Mold accuracy directly affects parting line quality with a perfect fit between mold surfaces. Gaps appear if there are any inaccuracies. These gaps cause flash or burrs to form. High precision is essential. Creating seamless parting lines depends on this precision.
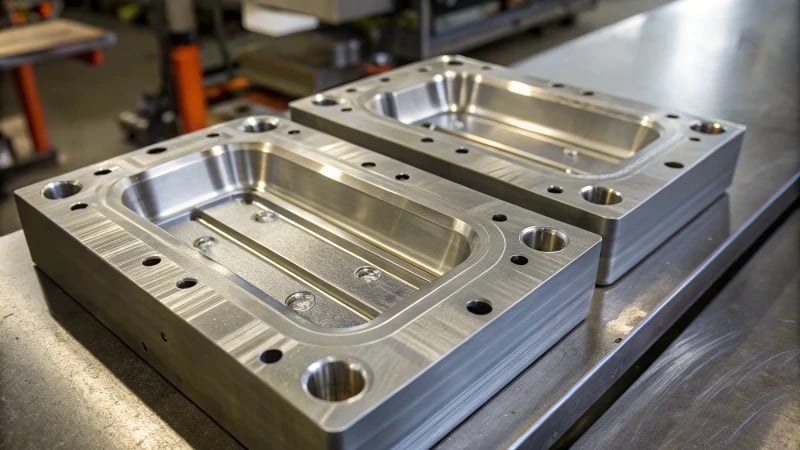
Mold Accuracy and Its Impact on Parting Lines
Mold accuracy serves as the foundation for creating perfect parting lines in injection molding. I recall my first project in a manufacturing plant where a tiny error in mold processing1 caused a visible seam on our prototype. This experience taught me that processing accuracy is really crucial. Misaligned mold surfaces can cause issues like flatness errors, which can result in serious problems.
For instance, precision is essential for things like electronic equipment housings. They need micron-level accuracy to hide parting lines. I once worked on a project where a small mismatch in guide pins and sleeves led to noticeable misalignments, disrupting our product’s smooth finish.
Mold Factor | Effect on Parting Line |
---|---|
Flatness Error | Causes gaps leading to flash |
Guide Mechanism Misalignment | Results in uneven seams |
Mold Structure Design Considerations
Designing a mold resembles crafting a detailed piece of art. The mold structure impacts the quality of a parting line. I’ve encountered challenges with complex curved surfaces that needed extra care during manufacturing, while managing simple flat surfaces is easier. However, curves raise the stakes significantly.
Additionally, the demolding mechanism’s design must be precise. I remember when poorly designed sliders put unnecessary stress on the parting surfaces, causing deformations. This example highlights that accurate design is essential for maintaining parting line integrity.
Material and Heat Treatment
Choosing the right mold material is like selecting the perfect tool for the job. Inadequate hardness results in quick wear, damaging the parting line’s appearance. I’ve learned that proper heat treatments, such as quenching and tempering2, probably improve material performance by increasing hardness and durability.
Injection Molding Process Variables
Pressure and Speed: Balancing these feels like walking on a tightrope. I once saw how high injection pressures led to plastic melt overflow, causing unwanted flash. Excessive speed created turbulence and made seams uneven.
Holding Pressure and Time: Finding the right balance avoids deformations or shrinkage marks on the parting line. Too much pressure caused deformities in some projects, while too little led to sinking issues.
Process Factor | Effect on Parting Line |
---|---|
High Pressure | Promotes flash formation |
Fast Injection Speed | Causes seam unevenness |
Influence of Plastic Material Properties
Understanding plastic properties is like knowing the material’s character. High fluidity materials might overflow, while materials with significant shrinkage form noticeable seams. I once had to adjust mold temperatures very carefully to manage different plastics’ unique rheological properties3. Knowing the material helps minimize defects at parting lines.
Mold flatness errors cause parting line gaps.True
Flatness errors lead to gaps, causing flash in the parting line.
High injection speed reduces seam unevenness.False
Excessive speed causes turbulence, increasing seam unevenness.
How Does Injection Molding Pressure Affect Parting Line Defects?
Did you ever think about how pressure might either shape or ruin a perfectly designed part?
Injection molding pressure has a very important impact on parting line defects. It affects the seal of the mold and the movement of the plastic. Correct control of this pressure avoids flash, burrs and misalignment. This is really crucial for creating high-quality molded parts.
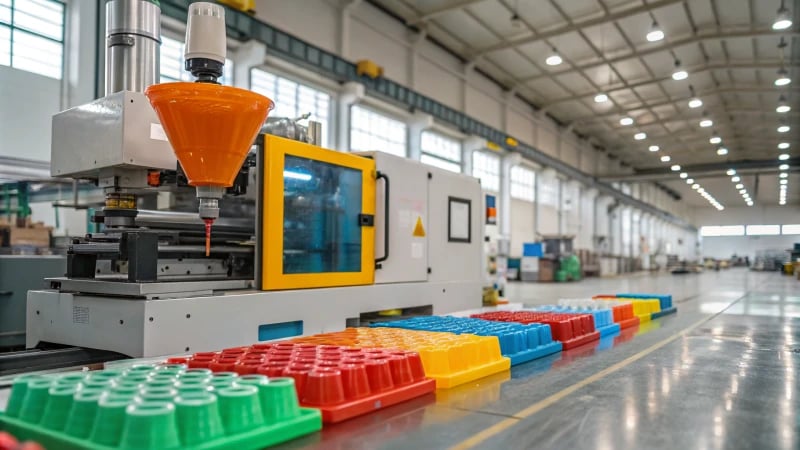
Understanding Injection Molding Pressure
I want to share a story from my early projects where I learned that injection molding pressure is really tricky. It was late in the evening, and I struggled to fix several broken parts. The problem? Each part had ugly burrs at the lines where the mold pieces met. After many cups of coffee and some headaches, I found the problem was incorrect pressure control. The plastic didn’t move smoothly into every corner. When the pressure jumped, it pushed the mold apart slightly, leaving those annoying marks.
The Mechanics of Pressure and Parting Lines
Think about trying to push a thick milkshake through a straw. Too much force might break the straw; too little and nothing moves. It’s the same with molding. When pressure is too high, the mold can’t stay closed, causing flash or burrs. This happened in my project with thick walls. But if the pressure is too low, molds don’t fill up, leaving them incomplete.
Pressure Level | Potential Defect |
---|---|
Too High | Flash/Burrs |
Too Low | Incomplete Filling/Short Shot |
Speed and Holding Pressure
Speed is another difficult factor. Once, we sped up the injection process to save time on a tight deadline. What a big mistake! Fast speed created turbulence, causing an uneven line at the surface. Adjusting holding pressure is also really important. Too much of it can deform the parting line, while too little causes shrinkage marks.
Material Fluidity and Temperature
Different plastics have their own personalities. Some, like polypropylene—known for high fluidity—are easygoing but can exacerbate flash when not managed correctly (learn more4). Their behavior changes with pressure, fluidity, and temperature.
Balancing Pressure with Mold Design
It’s like tuning a musical instrument – every tweak affects the harmony of the final product (explore misalignment issues5). Balancing pressure with mold design truly matters as high-precision molds require perfect alignment to prevent misalignment at the parting lines.
By mastering these dynamics, I’ve seen how manufacturers really improve product quality and probably reduce waste by understanding each part’s role in the symphony of injection molding.
High injection pressure causes mold flash.True
Excessive pressure forces plastic against mold edges, causing flash.
Low injection pressure prevents short shots.False
Low pressure can lead to incomplete filling, causing short shots.
Why Is Choosing the Right Plastic Essential for Parting Line Quality?
Have you ever finished a project thinking it was perfect, but later learned it had flaws? This situation is common when selecting the right plastic for parting lines in molding.
Selecting the right plastic is very important for perfect parting lines in injection molding. The flow and shrinkage of the plastic directly affect the clarity of these lines. Clean lines require careful material selection.
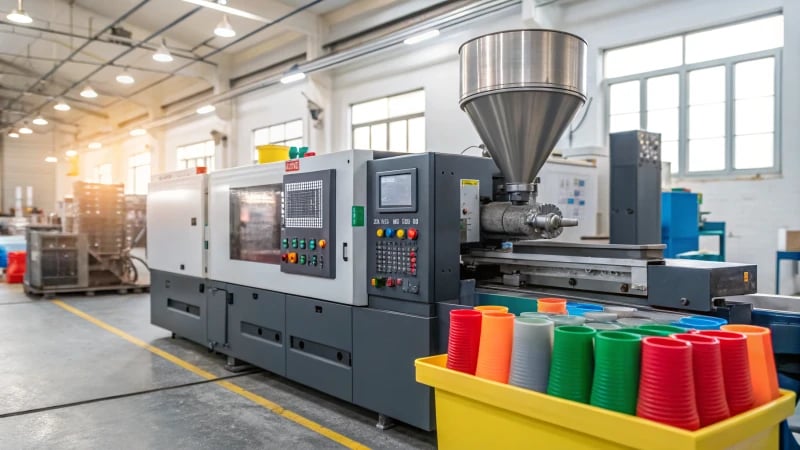
Understanding Plastic Fluidity
Plastic fluidity plays a critical role in how well the material fills the mold, directly affecting the parting line’s appearance. I remember my first big project where I underestimated this aspect. I thought polypropylene was perfect due to its easy use; however, the flash at the parting lines showed something different.
Plastic Type | Fluidity Level | Potential Issues |
---|---|---|
Polypropylene | High | Flash at parting lines |
Modified Plastics | Low | Insufficient filling |
High fluidity fills cavities well, yet too much fluidity causes overflow and unwanted flash at the parting surface6. In contrast, materials with low fluidity might not fill all areas properly. Temperature impacts fluidity, so understanding rheological properties is essential for better processing7.
Plastic Shrinkage and Its Effects
Once, I chose nylon without knowing its shrinking behavior. Watching shrinkage marks along the parting lines taught me a lesson. Plastics like nylon shrink a lot when cooling, which can create visible defects.
Plastic Material | Shrinkage Level | Common Defects |
---|---|---|
Nylon | High | Shrinkage marks |
ABS | Moderate | Uneven surfaces |
Sometimes, shrinkage occurs differently in various directions, leading to uneven surfaces. Understanding these behaviors helps design molds that lower defects and improve quality.
The Role of Temperature Control
Temperature control during molding changes everything. I learned this when excessive flash happened because my mold temperature was too high. Mold temperature influences plastic melt flow; high temperatures raise fluidity and risk of flash while low temperatures can result in poor filling.
- High Mold Temperature: Raises fluidity, increases flash risk.
- Low Mold Temperature: Lowers fluidity, causes short shots.
Proper temperature management ensures that materials maintain ideal flow characteristics, preserving the integrity of parting lines.
Choosing the right plastic requires understanding its behavior under different conditions. Evaluating factors like fluidity and shrinkage keeps parting lines as clean as possible. For more insights on injection molding techniques8, explore our comprehensive resources.
Polypropylene has high fluidity in molding processes.True
Polypropylene is known for its high fluidity, filling molds easily.
Nylon has low shrinkage levels during cooling.False
Nylon exhibits high shrinkage, leading to potential defects.
How Can Mold Temperature Control Improve Parting Lines?
Have you ever wondered why some molded products have smooth and flawless finishes, while others just don’t meet the standard?
Controlling mold temperature controls the fluidity and cooling speed of plastic melts. It probably reduces issues like flash and seams at parting lines. This improves the appearance and strength of molded parts. Appearance and strength really improve.
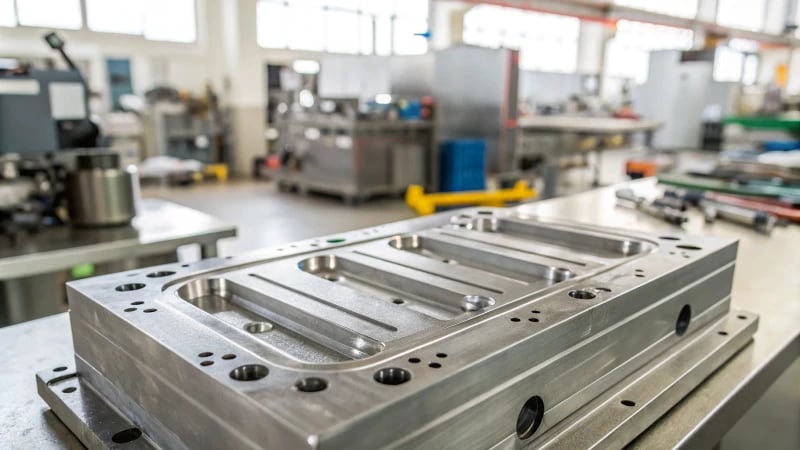
The Impact of Mold Temperature on Plastic Fluidity
When I started studying injection molding, mold temperature surprised me with its importance. Picture pouring syrup on a cold pancake – it won’t spread well. Low temperatures make plastic less fluid, leading to incomplete fills. If the temperature rises too much, plastic can overflow at the meeting line, causing flash. Achieving balance is crucial.
Mold Temperature | Plastic Fluidity | Potential Issues |
---|---|---|
High | High | Flash formation |
Low | Low | Incomplete filling |
Learn more about plastic fluidity9 to optimize mold settings effectively.
Cooling Rate and Its Influence on Parting Lines
Think about cooling a pie too fast from the oven. The crust might crack or shrink. Fast cooling can cause parting lines to deform similarly. Slow and careful cooling keeps everything aligned, like a perfect pie crust.
- Rapid Cooling: Causes uneven shrinkage.
- Controlled Cooling: Keeps parting surfaces intact.
Practical Example: Mold Design Considerations
Designing molds for precise items, like electronics, showed me that every degree is crucial. Temperature settings must match the material’s thermal properties10. Complex surfaces become troublesome if not controlled correctly. It is like trying to iron a shirt without flattening it first.
The mold structure design also influences how temperature variations affect parting lines. A simple flat surface is easier to manage than complex curves, which are prone to errors in cooling and temperature control.
Temperature Control Techniques
Over time, I developed techniques to keep mold temperatures steady:
- Thermal Sensors: My eyes and ears inside the mold, continuously checking and adjusting.
- Water Jackets: These distribute temperature evenly across the mold.
- External Heating/Cooling Systems: These act as climate control for the mold.
These methods have been very important for me in keeping high-quality parting lines during injection molding11. Whether I handle a simple or complex design, observing temperature changes everything.
High mold temperature increases flash risk.True
Excessive fluidity from high temperatures causes overflow at parting lines.
Rapid cooling prevents shrinkage at parting lines.False
Rapid cooling can cause uneven shrinkage and deformation, affecting appearance.
Conclusion
The quality of parting lines in injection molding is influenced by mold accuracy, design, material properties, and process parameters like pressure and temperature, affecting both appearance and functionality.
-
Learn how processing accuracy directly impacts parting line quality and prevents common defects. ↩
-
Discover how heat treatment enhances mold durability and maintains precision. ↩
-
Understand how plastic flow behavior affects molding outcomes. ↩
-
Learn how to adjust injection settings based on the fluidity of different materials. ↩
-
Discover strategies to maintain proper mold alignment and reduce defects. ↩
-
Explore common reasons behind flash formation at parting surfaces during injection molding processes. ↩
-
Learn techniques to adjust processing parameters for various plastics to improve product quality. ↩
-
Discover advanced techniques in injection molding that enhance parting line quality and reduce defects. ↩
-
Understanding plastic fluidity helps in setting optimal mold temperatures, reducing defects. ↩
-
Knowing material thermal properties aids in precise temperature settings for better mold outcomes. ↩
-
Exploring these systems provides insights into maintaining consistent temperatures for quality molds. ↩