Temperature control in injection molding acts as the heartbeat of quality production. It stays steady, precise and truly essential.
Injection molding machines control temperature with a mix of sensors, controllers and PID algorithms. Sensors watch real-time temperatures. Controllers change heating elements. PID algorithms perfect these changes. Temperature control remains stable and precise. It’s very important to keep this stability.
I remember when I first saw an injection molding machine working. It felt like watching a conductor leading an orchestra. Every part worked perfectly. Temperature sensors watch the barrel’s heat all the time. They’re like a friend who always checks to make sure everything is okay.
The temperature controller is the brain here. I picture it as a chef carefully controlling the flame to cook food just right. It gets messages from the sensors and changes the heat to match the right levels. When I learned about PID algorithms, it was like finding the key to controlling temperature. The algorithm constantly works to fix any changes quickly and correctly. This mix of technology brings out perfect plastic parts every single time. Perfect parts, every time.
Temperature sensors use thermocouples in injection molding.True
Thermocouples are common in temperature sensors for injection molding barrels.
PID control eliminates all temperature deviations instantly.False
PID control minimizes but does not instantly eliminate temperature deviations.
How Do Temperature Sensors Impact Injection Molding?
Have you ever wondered how small sensors have so much power in the field of injection molding?
Temperature sensors in injection molding are crucial. Sensors watch and keep exact barrel heat. They stop flaws. They keep production efficient. Real-time data help. PID control algorithms also help.
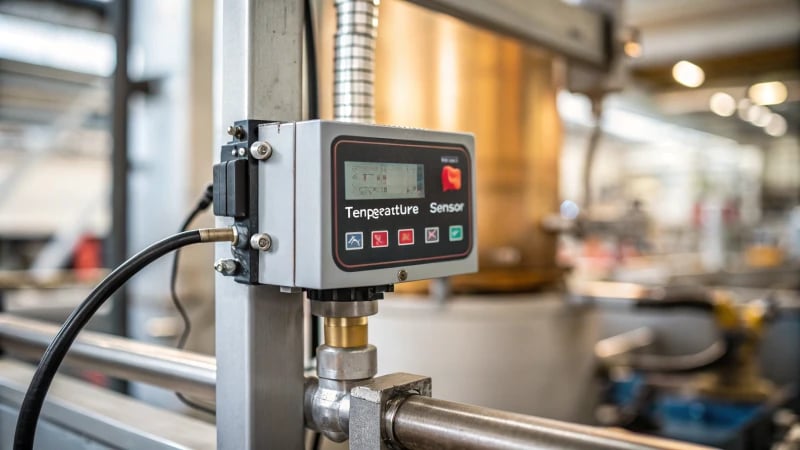
Watching Temperatures Right Away
I recall when I first saw why temperature sensors matter so much in molding. These small devices, often thermocouples or thermal resistors, are like unsung heroes. Placed in different parts of an injection molding machine’s barrel, they give live temperature data to the controller all the time. This flow of data helps track every production step, keeping each area at its best temperature. Very important.
Role of Temperature Controllers
The temperature controller acts like a strict conductor leading an orchestra. It keeps everything in sync. If a sensor shows that a section’s temperature is below our crucial 200°C line, the controller reacts, adjusting power to the heating coils like a conductor leading a big moment. This accuracy keeps the molding process smooth and mistakes are avoided.
Section | Temperature Control |
---|---|
Feeding | Monitors input material temperature |
Compression | Adjusts for melting and density changes |
Metering | Ensures consistent flow and pressure during ejection |
Use of PID Algorithms
Learning about PID (Proportional-Integral-Differential) control algorithms felt like finding a secret to better production. These algorithms help fine-tune how we adjust temperatures. The P part fixes immediate errors, the I part removes ongoing issues, and the D part predicts future changes to stop over-fixing. This combination keeps our product quality very high.
Effect on Product Quality
Precise temperature management is about more than avoiding errors – it’s about building reliability and high standards into each product. Wrong temperatures might cause warping or half-filled molds; that’s why advanced control systems with well-placed sensors are key for producing reliable and high-quality products consistently. Each product must reach its full potential from the beginning, changing results significantly.
Temperature sensors use thermocouples or thermal resistors.True
Temperature sensors in injection molding machines use these components.
PID control does not involve temperature prediction.False
The differential term in PID predicts temperature trends to adjust early.
How does a temperature controller manage to keep things just right?
Do you ever think about how your devices keep just the right temperature, as if they understand your needs?
A temperature controller keeps heat levels just right. Sensors track temperatures. The control system adjusts the heating elements. It leverages a PID algorithm. Precise control results from this method. Stability is very important.
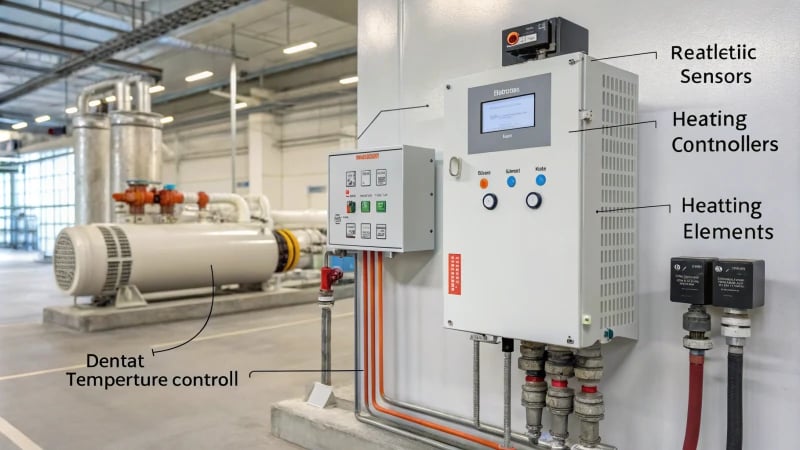
Monitoring with Temperature Sensors
Think of temperature sensors like tiny spies working inside your machines. They may be thermocouples or thermal resistors1. These devices closely watch how hot things get. Engineers place them in important parts like the feeding or compression areas of an injection molding machine. Sensors act like my eyes and ears. They turn temperature info into electrical signals and send it to the controller for analysis.
Regulation Functionality of Controllers
Controllers act as the brains in this operation. After receiving information from sensors, they decide whether to warm things up or cool them down. For instance, we desire 200℃, but sensors find only 180℃. The controller increases heating, similar to turning up a heater in cold weather. If it gets too hot, it reduces power. This keeps the temperature just right.
Application of the PID Control Algorithm
Learning about PID algorithms2 felt like finding the secret formula for perfect temperature control. This algorithm balances three parts:
- Proportional (P): For quick changes.
- Integral (I): To fix errors slowly.
- Differential (D): To predict future changes.
It’s like a smooth relay race where everyone knows their role. This helps things run well without mistakes.
Table: PID Parameter Effects
Parameter | Function |
---|---|
Proportional | Quick response to deviations |
Integral | Eliminates steady-state error |
Differential | Predicts changes to avoid overshoot |
Insights from Real-world Applications
In plastic molding, getting the temperature just right matters a lot for quality. I learned this through my years in consumer electronics design. This experience helps me know that every product must not only look nice but also work well. Understanding temperature controllers helps someone like me create products that are efficient and dependable by enhancing product design strategies3.
Temperature sensors convert heat to electrical signals.True
Sensors detect temperature changes and send electrical signals to controllers.
PID controllers only use proportional control.False
PID controllers use proportional, integral, and differential control for accuracy.
Why are PID Algorithms Crucial in Temperature Regulation?
Do you ever think about how those complicated systems control temperatures so well? Let’s explore the amazing world of PID algorithms!
PID algorithms are crucial for precise temperature control. They adjust heating or cooling nonstop. Error signals help guide them. Stable and accurate regulation results. Reliable consistency is achieved.
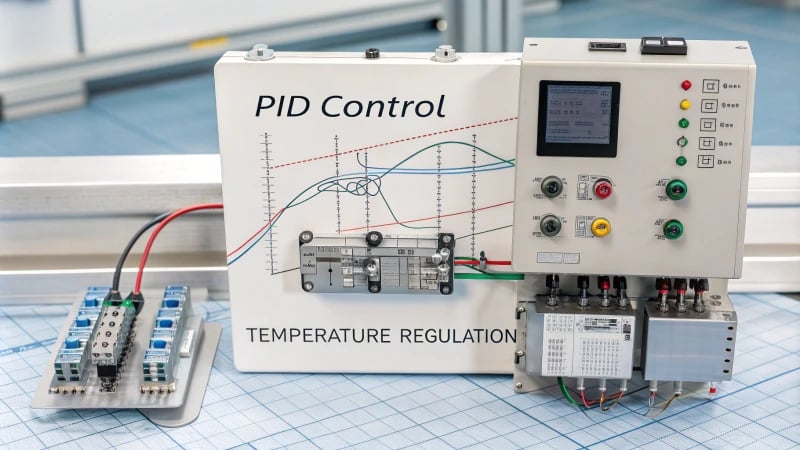
Understanding PID Control in Temperature Regulation
At first, learning about PID controllers felt like discovering a secret to perfect temperature control. These Proportional-Integral-Derivative (PID) controllers work like a helpful assistant, keeping every temperature setting just right. Here’s how they operate:
Picture trying to keep your coffee exactly warm. The PID controller acts like a quiet voice, constantly checking the heat and suggesting changes to prevent it from cooling or scalding. It looks at three things:
Proportional Control: This part reacts quickly when there’s a change, similar to grabbing a sweater when you feel a chill. Quick response is crucial.
Integral Control: Ever adjusted your home’s thermostat because it wasn’t comfortable over time? This section fixes those small errors gradually.
Derivative Control: Think of this as predicting weather shifts to smooth everything out. It anticipates changes and adjusts in advance.
Application in Injection Molding Machines
While working on injection molding machines, I noticed the value of these algorithms firsthand. These machines use temperature sensors placed in different areas like feeding, compression, and metering zones. These sensors act like scouts, sending live data to the temperature controller, which uses PID magic to maintain everything perfectly.
Section | Sensor Type | Function |
---|---|---|
Feeding Section | Thermocouple | Monitor initial material temperature |
Compression Zone | Thermal Resistor | Ensure material is melted uniformly |
Metering Section | Thermocouple | Maintain optimal flow characteristics |
Maintaining the correct temperature is key for quality. Adjusting those PID parameters felt like tuning a delicate musical instrument.
Benefits of PID Control
- Precision: Imagine adjusting the heat exactly as needed – PID does this automatically4.
- Stability: During a production run, I saw how steady temperatures kept everything smooth.
- Efficiency: It’s like having a clever thermostat that uses just the right amount of energy without waste.
Modern systems even allow remote monitoring and adjustments—it’s like having a smart home app but for industrial machines. This flexibility makes PID controllers really important5 in industries where precision matters greatly.
Temperature sensors detect barrel temperature in real-time.True
Thermocouples or resistors sense and transmit temperature data.
PID control eliminates all temperature deviations.False
PID reduces but doesn't completely eliminate temperature deviations.
How Can Designers Optimize Temperature Control Systems for Better Efficiency?
Ever thought about how temperature control systems work better and run more easily?
To get the best temperature control, I utilize precise sensors. Advanced controllers such as PID regulate the system. Real-time observation keeps track of changes. This setup responds quickly. Energy use becomes much more efficient, too. Efficient systems matter a lot for factories. Heating and cooling systems also rely on them.
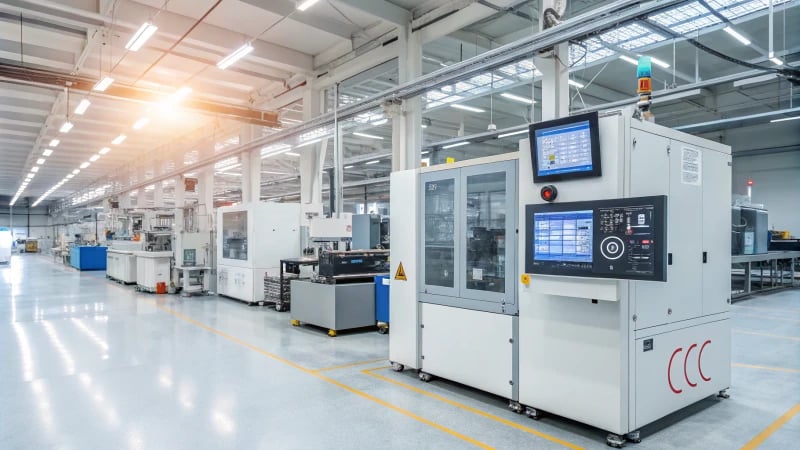
Monitoring with Temperature Sensors
I recall installing temperature sensors on an injection molding machine for the first time. It felt like granting the machine an extra sense. These sensors, which are usually thermocouples or thermal resistors, are vital for gathering live data from different parts of the system, including the feeding, compression, and metering areas. They convert temperature readings into electrical signals. This helps me maintain accurate temperature control. Understanding sensor placement6 is essential. It really is. It improves the efficiency and accuracy of temperature control.
Regulation via Temperature Controllers
While working on a project, the temperature controller looked like the brain of the system. It compares actual temperatures with preset values and adjusts the heating coil’s power as needed. Imagine a set temperature of 200℃ and a reading of 180℃; the controller simply increases the power to raise the temperature. If it’s too hot, the system reduces power or stops it completely. This method minimizes energy waste while keeping the desired temperature.
Function | Example Action | Outcome |
---|---|---|
Increase Power | Temperature < Set Value | Raises Temperature |
Decrease Power | Temperature > Set Value | Lowers Temperature |
Controller configuration7 is vital for optimal performance.
Application of PID Control Algorithm
The PID control algorithm amazes me. It precisely regulates temperatures by adjusting based on error calculations—the gap between set and actual temperatures. The proportional component reacts quickly to changes; the integral part removes steady-state errors; and the differential part anticipates shifts to avoid overshoot.
Benefits of PID Control:
- Proportional (P): Quick response to changes.
- Integral (I): Removes constant errors.
- Differential (D): Predicts shifts for proactive changes.
Proper tuning of PID parameters8 allows for fast and stable adjustments—very fast, very stable.
Understanding how to improve temperature control systems9 using these methods greatly boosts system efficiency, which is very important in industries like manufacturing and HVAC systems.
Temperature sensors monitor barrel areas in real-time.True
Sensors detect and transmit temperature data to controllers.
PID control algorithm is rarely used in temperature controllers.False
PID is commonly used for precise temperature control adjustments.
Conclusion
Injection molding machines utilize temperature sensors, controllers, and PID algorithms for precise temperature control, ensuring high-quality production by maintaining optimal heat levels throughout the process.
-
Explore detailed information on how thermocouples and thermal resistors function in temperature monitoring. ↩
-
Learn about the intricacies of PID algorithms in controlling temperature deviations effectively. ↩
-
Discover how maintaining optimal temperatures impacts design efficiency and product quality. ↩
-
Learn how PID controllers function to provide precise temperature adjustments in various applications. ↩
-
Discover how remote management can enhance efficiency and flexibility in industrial processes. ↩
-
Learn about strategic sensor placement to enhance system accuracy and efficiency. ↩
-
Discover techniques for configuring controllers to save energy and maintain precise temperatures. ↩
-
Explore methods to fine-tune PID settings for improved control system performance. ↩
-
Find strategies to enhance HVAC system efficiency through improved temperature control. ↩