Do you ever stop to consider the journey of the smooth plastic parts in your devices? It is a really interesting process!
Plastic mold makers design and create molds that shape plastic products for various industries, including automotive and healthcare. Their expertise ensures precise and efficient production of items like car parts and medical devices.
In this industry, I consider my experiences and recognize plastic mold creators as the hidden champions. They turn our wildest design dreams into actual, real products. Their work is crucial. The journey starts with the complex art of mold design. Each piece they skillfully craft becomes essential. It involves more than just machines and materials. They grasp the core purpose of a product. Every detail reflects their precise care.
Plastic mold makers only work with small gadgets and toys.False
This claim is false; plastic mold makers work across various industries, not just small items.
Mold maintenance is crucial for efficient plastic production.True
True, ongoing maintenance of molds ensures precision and efficiency in producing plastic components.
What are the key steps in mold design and manufacturing?
Ever wondered about the complex world of mold design and creation? Let’s explore the important steps that change an idea into a real product. These steps reveal the hidden secrets of the process.
Key steps in mold design and manufacturing include studying client requirements, designing mold structure (parting surfaces and runner systems), obtaining materials, precise parts processing, followed by assembly, testing, and continual upkeep for optimal performance.
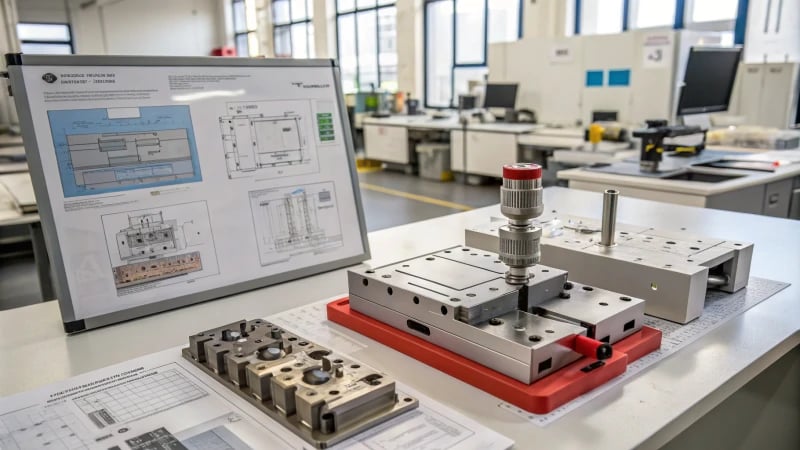
Understanding Mold Design Steps
The journey of mold design starts with a detailed product analysis. This step really fascinates me. I dive into deep conversations with clients to fully understand their needs. I remember working on a plastic mobile phone case mold. Every detail was very important. We talked about everything, from button placements to camera hole positions. Every requirement, both functional and aesthetic, mattered. I realize how important understanding the product’s environment is during these discussions. Every little detail shapes the early design phase. It’s thrilling to see how my ideas guide the project correctly.
Key Elements in Mold Structure Design
After analysis, we switch to designing the mold structure. It feels like solving a really complex puzzle. One key element is deciding on the mold’s parting surface, which separates the movable and fixed halves of the mold. Choosing it correctly leads to smoother demolding later.
Product Complexity | Parting Surface Type |
---|---|
Simple Shape | Planar |
Complex Shape | Non-Planar |
Designing the Runner System
Next is the runner system. It is crucial for perfect molten plastic flow into the mold cavity. It’s like conducting an orchestra; every runner needs to work together to create a perfect product. This includes thinking about the shape, size and position of the main runner, branch runners and gates. Cooling systems are also vital at this stage to prevent issues like deformation during production.
Transition to Mold Manufacturing
Once the design is firm, we proceed to mold manufacturing. This part is thrilling and very meticulous. I always choose materials with high hardness, strength and wear resistance, like high-quality mold steel for precision molds.
Material Type | Properties |
---|---|
Mold Steel | High hardness, wear resistance |
Aluminum | Lightweight, good thermal conductivity |
Processing Mold Parts
Next is mold parts processing where machines like CNC milling machines and EDM equipment are used for precise shaping of raw materials exactly as per specifications. Watching these machines shape raw materials exactly is mesmerizing; it feels like sculptors working with stone! Following design specifications strictly is key to top-quality results.
Assembling and Debugging Molds
After processing, the exciting part starts: mold assembly and debugging! This phase requires very careful attention to detail; every component must fit together precisely—like assembling a high-end watch! During trial runs, I watch closely for any issues such as flash or material short shots; adjustments continue until everything works perfectly.
Maintenance and Performance Optimization
Finally, mold maintenance is crucial—like a reliable car needing regular check-ups! Regular mold repair services are vital since wear and tear can cause problems over time; timely repairs can prevent bigger troubles down the line! Improving mold performance using customer feedback helps enhance product quality.
For those curious about these processes, exploring resources on mold design principles1 or advanced manufacturing techniques2 might be helpful.
Understanding these essential steps has given me invaluable knowledge over my years in product design—it’s a journey full of creativity and precision—a dance between art and engineering that I truly love.
Product analysis is essential for effective mold design.True
A thorough product analysis ensures that all functional and aesthetic requirements are met during mold design, facilitating better communication with clients.
Mold assembly does not require debugging after processing.False
Debugging is crucial after assembly to ensure optimal performance and address any issues like flash or material short shots that may arise.
How do plastic mold makers ensure product quality and precision?
Ever thought about how plastic mold makers consistently produce high-quality products? The world of mold work combines accuracy with a real dedication.
Plastic mold makers ensure quality and precision through careful mold design, high-quality materials, precise manufacturing, ongoing maintenance, detailed client communication, and thorough testing to meet strict standards.
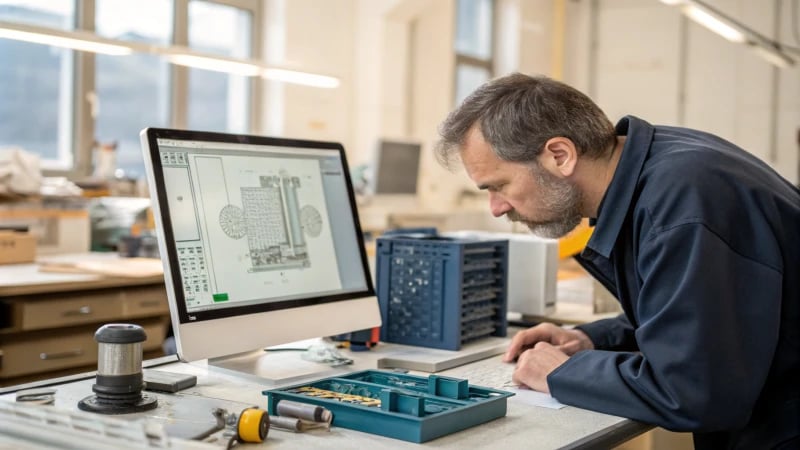
Understanding Mold Design
In my journey through the complex world of plastic mold creation, I often notice how every detail is crucial. It involves more than just machines and materials; it’s about knowing a product deeply.
The adventure starts with mold design. This is where magic truly starts. It feels like being a detective, gathering clues from clients to understand their needs. Once, I designed a mold for a phone case. I had long talks with the client about tiny details, like button placement, edge thickness and surface texture. We talked not only about looks but also about making the product comfortable to hold. These discussions went beyond appearances.
Mold Structure Design: The focus shifts to mold structure design. Think of it as crafting a puzzle where each piece must fit perfectly. The parting surface is essential – this is where the mold separates and it must be correct for smooth demolding. With complex designs, non-planar parting surfaces are sometimes used to deal with intricate shapes.
Aspect | Considerations |
---|---|
Runner System | Do not overlook the runner system – it guides the melted plastic evenly, much like a well-planned dance. Every runner, gate and cooling channel needs careful planning to avoid problems in the future. |
Cooling System | Ensure that cooling channels are designed properly to prevent deformation during solidification. |
Ejection Mechanism | Ensure mechanisms like push rods are effectively integrated for smooth ejection. |
The Manufacturing Process
Once the design is ready, mold manufacturing begins. This is where creativity meets engineering.
- Material Procurement: Selecting materials feels like choosing the best ingredients for a recipe. I prefer high-quality mold steel for its strength and durability, vital for precision work.
- Parts Processing: Picture me at a CNC machine, carefully tracking as it carves out cavities to perfection. Every detail must match our designs; it feels a bit like sculpting, where every cut is important.
- Assembly and Debugging: After milling, the next stage is assembly and debugging – an exciting phase where the pieces come to life. During trial runs, I hope everything fits well without any issues like flash or material shortages.
Maintenance and Continuous Improvement
The journey continues with mold maintenance. Similar to an artist revisiting their masterpiece, molds need regular care. I recall when one mold began wearing down; it was like watching a friend age. Techniques like grinding or repair welding brought it back to life, ensuring our products stayed top-notch.
Additionally, customer feedback forms an essential part of the process; each suggestion helps improve our molds. If a client demands better efficiency or quality, we adjust quickly by enhancing the runner system or optimizing cooling channels often reduces defects.
Conclusion
Through detailed steps – design, manufacturing and maintenance – I realize the dedication required to deliver high-quality products. Attention to detail is the secret; every decision influences our goal for precision and excellence.
For more insights, explore mold design techniques3 and mold maintenance strategies4.
Mold design requires effective communication with clients.True
Effective communication with clients ensures that mold designs meet specific functional and aesthetic requirements, leading to higher product quality.
Continuous feedback is unnecessary for mold performance improvement.False
Continuous feedback is essential for optimizing mold performance and enhancing product quality based on user experiences and needs.
What challenges do plastic mold makers face in their work?
I work as a plastic mold creator and have faced many obstacles on this complex path. Knowing these challenges improves our abilities. This probably raises the quality of our work. I want to share some experiences I’ve had and lessons I’ve learned during this journey.
Plastic mold makers face challenges in complex mold design, precision manufacturing, effective assembly, continuous maintenance, and client feedback, all crucial for producing high-quality items.
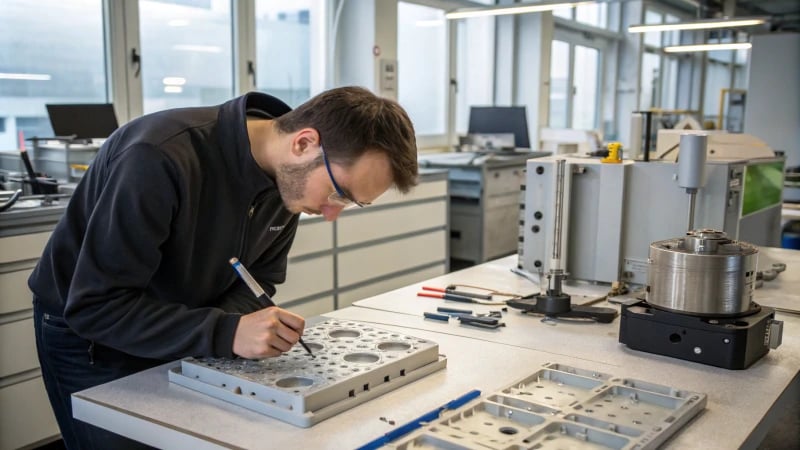
The Complexities of Mold Design
Plastic mold makers face difficulties with intricate design needs, precise manufacturing, effective assembly and debugging, and ongoing maintenance. They must also optimize performance based on feedback.
Entering the mold-making world, I immediately noticed the blend of creativity and engineering required. Key to this is understanding product details and communicating with clients. For example, consider the intricacies involved in designing a plastic mobile phone case mold. I worked on a plastic phone case, focusing on button positions and camera holes. The responsibility to perfect these details and enhance user experience was immense yet exciting.
Every detail in mold design matters. These include how a product is used, environmental factors, and assembly methods. Careful attention to these elements ensures molds meet expectations.
Mold Structure Design Challenges
Designing mold structures presents its own challenges. Placing parting surfaces often resembles solving a complex puzzle. A well-planned parting surface is vital for easy demolding. Intricate products may need non-flat surfaces.
Moreover, the runner system’s design adds more complexity. Hours were spent mapping the main runner, branch runner, and gate for efficient flow. Balancing function and efficiency felt like art. Cooling systems are equally crucial to prevent defects like warping; it’s very interesting how much detail goes into each stage!
Aspect | Consideration |
---|---|
Parting Surface | Non-planar designs for complex shapes |
Runner System | Efficient melt filling and layout |
Cooling System | Uniform cooling channels to reduce defects |
Ejection Mechanism | Smooth ejection using push rods or plates |
Manufacturing Process Hurdles
After finalizing the design, manufacturing poses new challenges. Material procurement plays a significant role as choosing the right materials is crucial for durability and precision. High-quality mold steel is commonly selected, but each task requires careful thought.
After choosing materials, sizing them is necessary before detailed machining; accuracy here is critical as mistakes can lead to expensive delays.
Precision in Mold Parts Processing
Strictly following design drawings is essential when processing mold parts. Advanced tools like CNC machines and EDM tools help create precise shapes; watching a design come to life is thrilling! But any error can cause major quality issues—precision isn’t just recommended; it’s necessary.
Assembly and Debugging Challenges
The assembly stage comes next, presenting its own set of challenges. Components must fit perfectly—like a well-tuned symphony! I spent hours once aligning movable and fixed sections to meet precisely.
Debugging through trial molds assesses performance and lets me adjust accordingly; this phase can be intense with pressure to fix issues like flash or warping. This iterative process though time-consuming is crucial for quality.
Ongoing Maintenance Issues
Maintenance is a continuous concern as molds naturally wear over time facing fatigue and damage; timely repairs prevent disruptions and costly downtime in production.
Improving mold performance based on feedback or trends is vital too—for instance enhancing runner systems or cooling improves efficiency and quality! By remaining adaptive and responsive has become key in my success.
Facing these challenges has enriched my understanding of this intricate craft—it has strengthened my resolve to excel in this dynamic field.
Mold design requires precise product analysis and client communication.True
Effective communication with clients is crucial for accurate mold design, ensuring all product specifications are met for successful outcomes.
Material procurement is unimportant in mold manufacturing.False
Choosing the right materials is essential for durability and precision in mold making, making procurement a critical step in the process.
Why is ongoing maintenance crucial for molds in production?
Do you ever think about why regular care for molds in production is so important? It’s more than a simple list. It’s about creating top quality and lasting a long time. Let’s explore this crucial part of manufacturing together.
Regular mold maintenance is vital in production to ensure product quality, extend mold lifespan, and enhance efficiency by preventing breakdowns and optimizing performance.
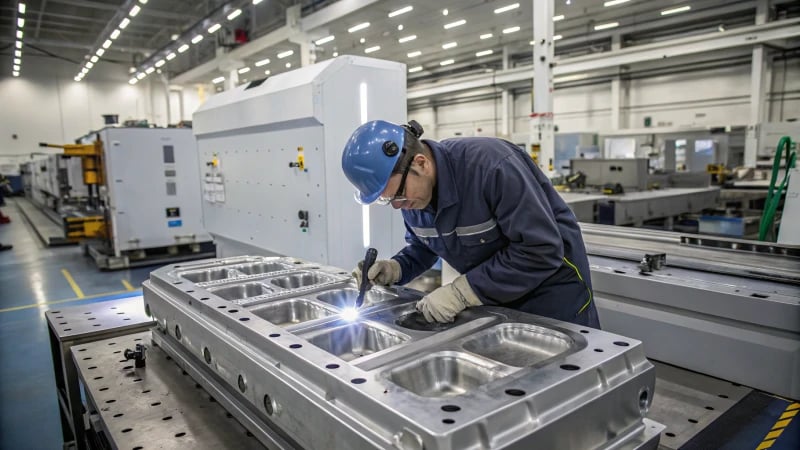
The Importance of Ongoing Maintenance for Molds
Ongoing maintenance is not just a good practice; it is essential for the longevity and performance of molds in production. Regular maintenance ensures that molds operate at peak efficiency, which is vital in injection molding processes. With proper care, molds can produce high-quality products consistently, minimizing defects and downtime.
Enhancing Product Quality
One of the main reasons for ongoing mold maintenance is the direct impact on product quality. Molds wear down over time, leading to issues such as:
Problem | Impact |
---|---|
Dimensional inaccuracies | Products may not meet specifications |
Surface defects | Affects aesthetic quality |
Increased cycle times | Reduces overall production efficiency |
By implementing a regular maintenance schedule, manufacturers can prevent these problems, ensuring that molds remain capable of producing high-quality products. For example, mold maintenance strategies5 include cleaning, lubrication, and timely repairs to worn parts.
Increasing Mold Longevity
Molds are significant investments for manufacturers. Therefore, extending their lifespan is crucial to maintaining profitability. Regular maintenance activities, such as:
- Inspection: Regular checks can identify wear before it becomes a larger issue.
- Repair services: Addressing problems like surface wear through grinding or welding can prolong mold life.
According to industry standards, molds that receive consistent maintenance can last 20-30% longer than those that do not. This increased longevity reduces the frequency of costly replacements and enhances overall production stability.
Boosting Production Efficiency
Efficiency in production is key to maximizing output and profitability. Ongoing maintenance helps in:
- Reducing downtime: Regular servicing prevents unexpected breakdowns that halt production.
- Optimizing cycle times: Well-maintained molds operate smoothly, allowing for faster injection and cooling processes.
For instance, optimizing the cooling channels within the mold through regular assessments can significantly decrease cycle times. Manufacturers often leverage advanced cooling techniques6 to improve efficiency further.
Adapting to Market Changes
With evolving market demands, molds must be adaptable. Regular maintenance allows for:
- Performance optimization: Adjustments based on customer feedback and market trends can be implemented more easily.
- Modifications: It’s easier to make changes to molds that are regularly maintained than those that have deteriorated significantly.
For example, upgrading the runner system or cooling channels based on new production requirements becomes feasible when ongoing maintenance is practiced. This adaptability is crucial for staying competitive in fast-paced industries like consumer electronics.
Regular mold maintenance enhances product quality significantly.True
Consistent upkeep prevents issues like dimensional inaccuracies and surface defects, ensuring high-quality production outcomes.
Molds can last 20-30% longer with ongoing maintenance.True
Routine care and timely repairs extend mold lifespan, reducing replacement frequency and costs for manufacturers.
Conclusion
Plastic mold makers are essential in transforming designs into quality products through precise mold design, manufacturing processes, and ongoing maintenance across diverse industries.
-
This link provides a comprehensive guide on best practices in mold design that can enhance your understanding. ↩
-
Explore advanced manufacturing techniques that can optimize your mold production process. ↩
-
Discover essential techniques that enhance product quality in plastic molding processes. ↩
-
Learn about effective maintenance strategies that prolong mold life and optimize performance. ↩
-
Discover essential mold maintenance practices that can significantly improve your production process and prevent costly downtimes. ↩
-
Learn how advanced cooling techniques can enhance your mold efficiency and product quality. ↩