I still remember my first project. Adjusting the temperature felt like a high-risk guessing game.
I search for the best processing temperatures for materials by examining their properties, such as crystallinity and thermal stability. Supplier data is my starting point. I then adjust settings through hands-on experiments. This approach achieves high-quality products. Very high quality.
When I first started, I relied on supplier data. It felt like having an experienced mentor offering you trusted temperature tips. But studying theory takes you only part of the way. Testing and observing taught me about how materials behave in different situations. For instance, adjusting the temperature during a mold trial showed a lot about the way plastic melt moves. Small changes, like raising or lowering temperatures by 5-10°C, often changed the final product quality significantly. These tiny details showed me the worth of mixing science with some art in dealing with materials.
Crystallinity affects processing temperature for plastics.True
Crystallinity influences melting and flow properties, crucial for setting temperatures.
Supplier data is irrelevant for determining processing temperatures.False
Supplier data provides initial guidance on temperature settings based on material properties.
Why is Supplier Data Essential for Determining Processing Temperatures?
Ever thought about why supplier information is the hidden champion in manufacturing?
Supplier data is very important for figuring out processing temperatures. It gives trustworthy temperature advice based on thorough research. This research probably allows manufacturers to reach the best product quality. Consistency is really crucial, too. This information sets exact processing temperatures. It matches top manufacturing practices.
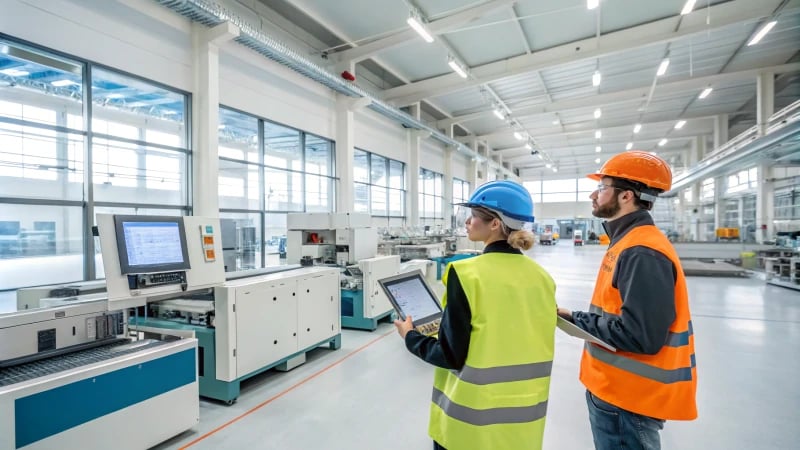
The Role of Supplier Data in Material Processing
Imagine working on a project and struggling to solve problems. I have faced the same, and there is one important lesson: supplier data is crucial. It’s like having a wise friend sharing important advice about processing features1. These details, like the right barrel temperature for polycarbonate (PC) or melting point information for polyethylene (PE), are essential for smooth production. Supplier data plays a vital role.
Analyzing Material Properties
Let me tell you about my experience with material properties. Imagine holding a piece of high-density polyethylene (HDPE). Knowing its melting point is the first step. Set your processing temperature just above it, and everything flows well.
Material Type | Example | Melting Point | Recommended Temperature Range |
---|---|---|---|
Crystalline | HDPE | 130-137℃ | 200-280℃ |
Non-Crystalline | PS | Tg ~ 100℃ | 180-280℃ |
However, with polystyrene (PS), things change. It has no clear melting point; just heat it slightly over its glass transition temperature. These small insights help a lot in understanding different materials.
Thermal Stability Considerations
I remember handling polyvinyl chloride (PVC) and realizing its weak thermal stability needs caution. A minor temperature mistake leads to major problems.
In contrast, polypropylene (PP) is more forgiving with its broad thermal stability, allowing for broader temperature ranges up to 270℃. Supplier details help navigate these complex situations by providing guidance on temperature settings2.
Experimentation and Adjustment Strategies
This is the practical part. Begin with supplier information and start experimenting. I have spent many hours gently tweaking temperatures and watching mold trials.
Using supplier data as a baseline involves starting with temperatures slightly above the material’s melting point or Tg, followed by mold trials to observe melt flow and product quality.
Adjustments are made in small increments (5-10℃) to optimize the process. Recording each trial’s results helps in fine-tuning the temperature settings, ensuring consistency and quality in production.
The combination of trustworthy supplier data and active testing secures quality and regularity in production by determining ideal processing conditions3 for each material type.
Supplier data is essential for setting processing temperatures.True
Supplier data offers researched temperature guidelines crucial for efficient material processing.
All materials have the same recommended processing temperature range.False
Different materials have specific temperature ranges due to varying properties and thermal stability.
How Do Material Properties Affect Processing Temperature Settings?
Ever thought about why your plastic creations sometimes don’t look right? The answer often hides in how material characteristics and temperatures interact.
Material features like crystallinity, thermal stability and viscosity directly influence the best temperature for processing. These traits help decide the perfect temperature range for molding or extrusion. They impact how well the material flows and the quality of the final product. Quality really depends on it.
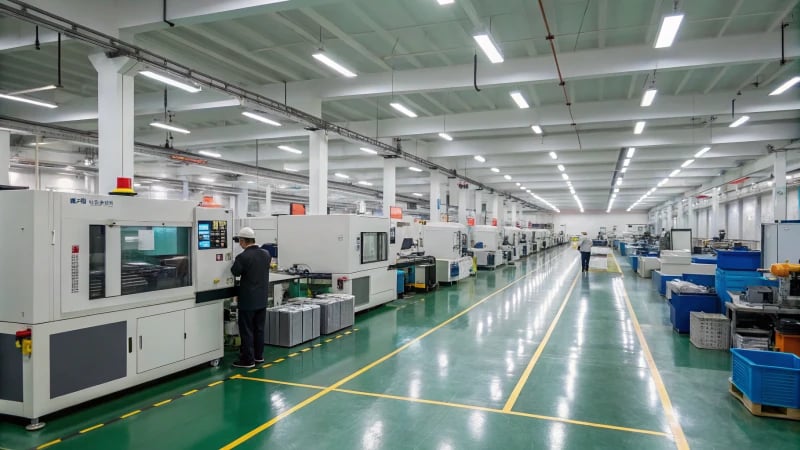
Material Crystallinity and Its Impact
Crystallinity significantly influences processing temperatures. For crystalline materials like polyethylene (PE) and polypropylene (PP), the melting point is a key reference point. The processing temperature should be higher than the melting point to ensure full melting and good fluidity. For instance, high-density polyethylene (HDPE) has a melting point of 130-137°C, while its processing temperature is around 200-280°C. In contrast, non-crystalline materials like polystyrene (PS) soften above their glass transition temperature (Tg), requiring settings above Tg for proper flow.
Material Type | Example Material | Melting Point (°C) | Processing Temperature (°C) |
---|---|---|---|
Crystalline | HDPE | 130-137 | 200-280 |
Non-Crystalline | PS | N/A (Tg ~100) | Adjusted Above Tg |
Thermal Stability Considerations
Thermal stability also dictates processing settings. Materials like polyvinyl chloride (PVC) decompose easily at high temperatures, requiring a narrow processing range. Rigid PVC typically has a barrel temperature of 160-190°C. Conversely, materials with better thermal stability, such as polycarbonate (PC), tolerate higher temperatures.
Flowability and Viscosity Effects
Flowability and viscosity are crucial for setting processing temperatures. Low-viscosity materials like low-density polyethylene (LDPE) need lower temperatures; LDPE is usually processed at 160-260°C. High-viscosity materials demand higher settings to enhance fluidity.
Experimental Test Methodology
Starting with material supplier data provides a baseline for temperature settings. By performing mold trials and observing plastic melt flow, one can adjust temperatures in small increments of 5-10°C for optimal results. It’s important to record observations after each adjustment for fine-tuning.
Consider using material supplier recommendations4 as a starting point to benefit from their extensive testing and experience.
By analyzing these properties, designers can create efficient production processes tailored to specific materials, ensuring both quality and functionality in the final product. Exploring case studies of successful implementations5 could further enhance knowledge in this area.
Crystalline materials require processing above melting point.True
Crystalline materials like HDPE need temperatures above their melting points for full melting.
Non-crystalline materials process below glass transition temperature.False
Non-crystalline materials require processing above their glass transition temperature for proper flow.
How Do I Set Initial Temperatures Correctly in My Experiments?
Sometimes experiments go wrong. The initial temperature setting might be the reason.
Set initial temperatures using material supplier data. Assess the properties of the materials. Conduct experimental trials too. These methods lead to the best temperature conditions. Precise experimental results depend on this.
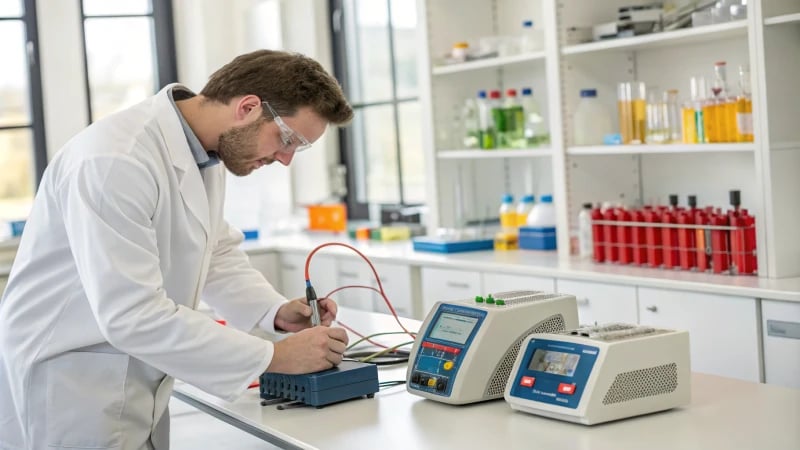
Reference to Material Supplier Data
I recall the first attempt at setting initial temperatures without guidance – it turned into chaos! Now, material supplier data is my trusted source. This information feels like having a wise companion. Suppliers share processing parameters6 based on thorough study and real production knowledge. As an example, polycarbonate (PC) generally needs a barrel temperature of 280-320°C. Trust me, following these guidelines helps avoid much trial and error.
Analyzing Material Properties
Crystallinity and Non-Crystalline Materials
Understanding the crystallinity of materials reminds me of knowing my cooking ingredients. Crystalline materials such as polyethylene (PE) and polypropylene (PP) require processing at temperatures above their melting points – imagine melting butter in a cold pan; it does not work!
Material | Melting Point (°C) | Processing Temperature (°C) |
---|---|---|
HDPE | 130-137 | 200-280 |
Polypropylene | 160-170 | 190-270 |
Non-crystalline materials like polystyrene (PS) and polymethyl methacrylate (PMMA) need temperatures above their glass transition temperature (Tg) for proper flow. It’s like warming honey; you need it just right for a smooth pour.
Thermal Stability
Materials such as polyvinyl chloride (PVC) react poorly to high temperatures. Picture a chocolate bar left in the sun – it melts quickly if you are not careful! Materials like PC withstand more heat, allowing more freedom with experimental settings.
Experimental Test Method
Starting Temperature Setting
Initial temperature setting by considering the melting point or Tg of the material is like preheating your oven before baking – crucial for success. Starting 30-50°C higher really helps achieve enough flow without risking material degradation7.
Mold Trial Observation
Conducting mold trials reminds me of fun science experiments in childhood – observing and tweaking were half the excitement! Watching melt behavior in the mold and adjusting the barrel temperature in modest steps (5-10°C) improves conditions without big changes.
Record and Optimization
Detailed records during each trial phase are like writing notes in a beloved cookbook. It’s vital for refining and optimizing the process parameters8. Noting changes in melt flow and product look is essential for the perfect outcome. Every little adjustment matters, bringing you closer to a flawless finish.
Polycarbonate requires a barrel temperature of 280-320°C.True
Material supplier data suggests PC needs this temperature range for processing.
PVC is flexible with high temperature settings.False
PVC is sensitive to high temperatures, requiring narrow ranges for stability.
How Do Mold Trials Enhance Processing Temperature Optimization?
Picture yourself in front of a huge machine. You wait eagerly to check if your new design appears perfectly. This is when mold trials become useful!
Mold trials hold great importance. They help adjust processing temperatures. Manufacturers tweak settings during these trials. Observing material behavior is crucial. It helps achieve excellent quality during injection molding. Quality really matters.
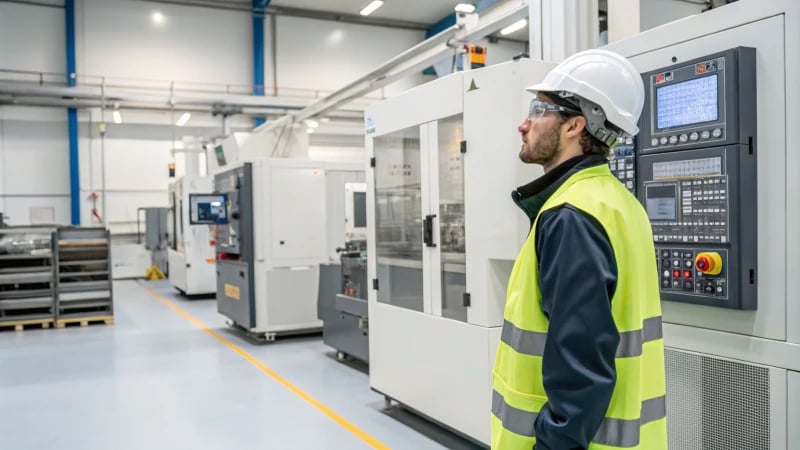
Understanding Material Supplier Data
When I first entered the industry, I really depended on material supplier data. It felt like a secret weapon, filled with years of study and actual production experience9. For example, with polycarbonate (PC), knowing the right barrel temperature is between 280-320℃ gives confidence to start without fear of mistakes. Confidence matters.
Analyzing Material Properties
Crystalline vs. Non-Crystalline Materials
Over time, I understood the differences between crystalline and non-crystalline materials. Crystalline materials like polyethylene (PE) need careful handling – just slightly above their melting points for good flow. My first trial with polyethylene felt like baking a soufflé without collapsing it! However, non-crystalline materials, like polystyrene (PS), appear more forgiving. They soften at temperatures above their glass transition point (Tg).
Thermal Stability and Viscosity
Some days, working with thermal stability and viscosity feels like playing temperature Tetris. I observed polyvinyl chloride (PVC) break down when taken too far, while polypropylene (PP) remained steady at high temperatures. It’s a constant quest for the perfect spot.
Conducting Experimental Tests
Initial Temperature Settings
Starting at the right temperature is like beginning a road trip with great music. I usually adjust to 30-50℃ above the melting point or Tg for a safe margin. Looking at similar materials helps choose initial mold temperatures wisely.
Material Type | Recommended Barrel Temp | Mold Temp |
---|---|---|
Crystalline | 200-280℃ | 40-80℃ |
Non-Crystalline | 180-280℃ | 40-80℃ |
Observing Mold Trials
During mold trials, watch the plastic melt’s flow carefully. Tweaks are like a dance – small and precise, avoiding mistakes. Recording each result brings certainty that settings are accurate.
Recording and Optimization
Documenting the outcome of every tweak on flow and quality feels like solving a complex puzzle. Each part matters. It defines a temperature range and increases confidence in delivering top-quality products.
Practical Application and Benefits
Implementing mold trials has genuinely changed production efficiency10. By fine-tuning processing temperatures, defects like flash and bubbles were reduced, leading to products to be proud of.
Mold trials deliver more than just better temperature settings. They reveal how material properties interact with temperature, eventually bettering the production process efficiency11. It’s a delicate dance of science and intuition that keeps me fascinated and hungry to learn more.
Polycarbonate requires a barrel temperature of 280-320℃.True
Material suppliers recommend this range for optimal processing.
Polypropylene decomposes easily at high temperatures.False
Polypropylene is stable and can withstand higher temperatures.
Conclusion
This article explores methods for determining optimal processing temperatures for materials, emphasizing the importance of supplier data, material properties, and experimental adjustments to achieve high-quality production.
-
Clicking this link provides insights into how processing parameters affect manufacturing efficiency and product quality. ↩
-
Explore strategies for setting optimal temperature ranges in plastic processing to achieve high-quality output. ↩
-
Learn about experimental techniques used to fine-tune processing conditions and improve manufacturing outcomes. ↩
-
Consulting material supplier data offers reliable temperature settings based on extensive research and experience. ↩
-
Case studies provide practical insights into how material properties influence processing settings, offering valuable real-world applications. ↩
-
Access supplier guidelines for processing polycarbonate effectively, ensuring accurate temperature settings in experiments. ↩
-
Learn strategies to avoid material degradation, crucial for maintaining experiment integrity. ↩
-
Explore techniques for optimizing injection molding processes through detailed parameter tracking. ↩
-
Gain insights from reliable supplier data that inform processing temperature settings. ↩
-
Understand the direct impact of mold trials on enhancing production efficiency. ↩
-
Explore how adjusting temperatures can enhance overall production outcomes. ↩