Have you ever thought about simplifying mold design for very high efficiency?
For the shortest main channel in mold design, I look at how to set up cavity layouts. I place the sprue bushing at the center. Choosing the right injection methods, like direct or side gates, is important. These steps shorten how far the material flows. They improve efficiency. They cut costs. Costs drop.
Over the years as a mold designer, I discovered that these strategies are only the beginning. Exploring each technique reveals more detailed ways to improve how molds work. Putting cavities close together in a balanced setup reduces channel length. It also gives uniform melt flow. Placing the sprue bushing in the center avoids unnecessary shifts, simplifying the whole process. These insights change mold design. Craftsmanship and creativity make it precise. Design becomes art.
Optimizing cavity arrangement shortens the main channel.True
Arranging cavities efficiently reduces the distance material must travel.
Side gates increase the main channel length.False
Side gates can reduce the main channel length by minimizing flow paths.
- 1. How Does Cavity Layout Affect Main Channel Length?
- 2. Why Does Sprue Bushing Positioning Matter in Mold Design?
- 3. Why Should You Consider Direct Gate Over Other Injection Methods?
- 4. How can I utilize the structural characteristics of molds?
- 5. Why are multi-layer mold designs beneficial?
- 6. Conclusion
How Does Cavity Layout Affect Main Channel Length?
Ever thought about how the arrangement of spaces in a mold changes the effectiveness of your designs? Let’s explore this interesting subject and discover some secrets to better flow dynamics.
The arrangement of cavities in a mold directly affects the main channel length. This influences how efficiently the material flows and how much material gets wasted. A smart and compact design probably shortens channels. This increases production speed and decreases waste. It really makes a difference.
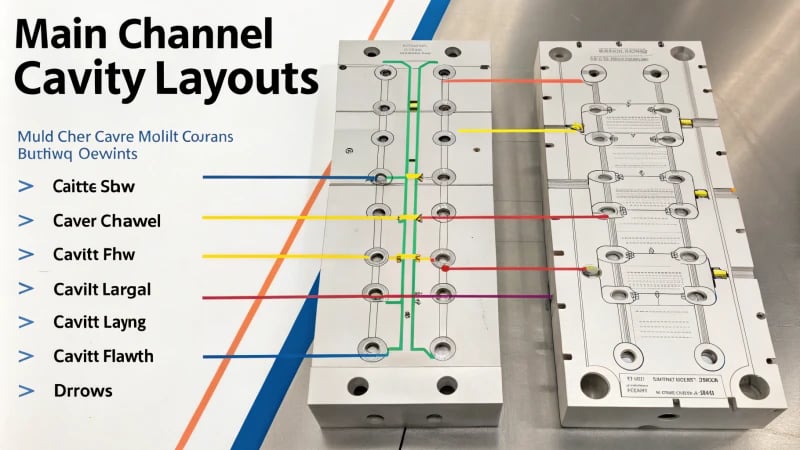
The Importance of Cavity Layout in Mold Design
Entering the injection molding world, I felt surprised by how cavity layout1 could change efficiency so much. Imagine a game like Tetris with mold cavities – putting them together tightly really helps reduce material use and improves flow.
Compact Arrangement of Cavities
One day, I designed a multi-cavity mold, placing cavities in a tight circle seemed hard at first. But similar to solving a jigsaw puzzle, putting them closer cut the channel length and spread the melt evenly. This saved time and material.
Optimizing Cavity Position
Positioning cavities is like arranging furniture in a room. It requires smart thinking. Based on the product’s shape and size, I tried rotating or mirroring cavity positions. It is similar to arranging books on a shelf to shorten distances and improve flow paths.
Sprue Bushing Positioning
The sprue bushing’s2 placement greatly affects efficiency. Putting it in the center or near the main cavity allows the melt to flow directly. It is like finding the right spot for a lamp to light the room evenly.
Avoiding Unnecessary Offset
In mold design, parting surfaces or cooling systems might move your sprue bushing. Keeping it aligned really matters for good flow and channel length.
Injection Methods and Their Impact
Deciding between a direct gate3 or side gate method feels like choosing an express or scenic route. For large molds, a direct gate shortens the channel length, much like an express lane cuts travel time.
Method | Benefits |
---|---|
Direct Gate | Minimizes flow distance |
Side Gate | Reduces total runner length |
Using Mold Structural Characteristics
Using a mold’s structural features is similar to using a building’s architectural traits. A hot runner system with centralized runners works like an efficient air conditioner, spreading flow perfectly in all areas.
- Hot Runner System: Acts like central heating, greatly focusing flow for better efficiency.
- Multi-layer Design: Vertical runners resemble elevators, cutting down horizontal movement and shortening main channel lengths.
By considering these factors, I’ve noticed how mold designers create molds that speed up processes and cut costs. It truly amazes what careful planning probably achieves!
Compact cavity layout shortens main channel length.True
A compact layout reduces the distance from the main channel to cavities.
Offset sprue bushing increases main channel length.True
An offset sprue bushing causes longer flow paths, increasing channel length.
Why Does Sprue Bushing Positioning Matter in Mold Design?
I remember the first time I held an injection molding project. I quickly realized how important sprue bushing positioning is. Very important.
Sprue bushing positioning is crucial for deciding how the melt moves into mold cavities. Correct placement allows the melt to reach all areas effectively. This reduces material waste significantly. Shorter cycle times occur when placement is optimal. Efficient distribution depends on good positioning.
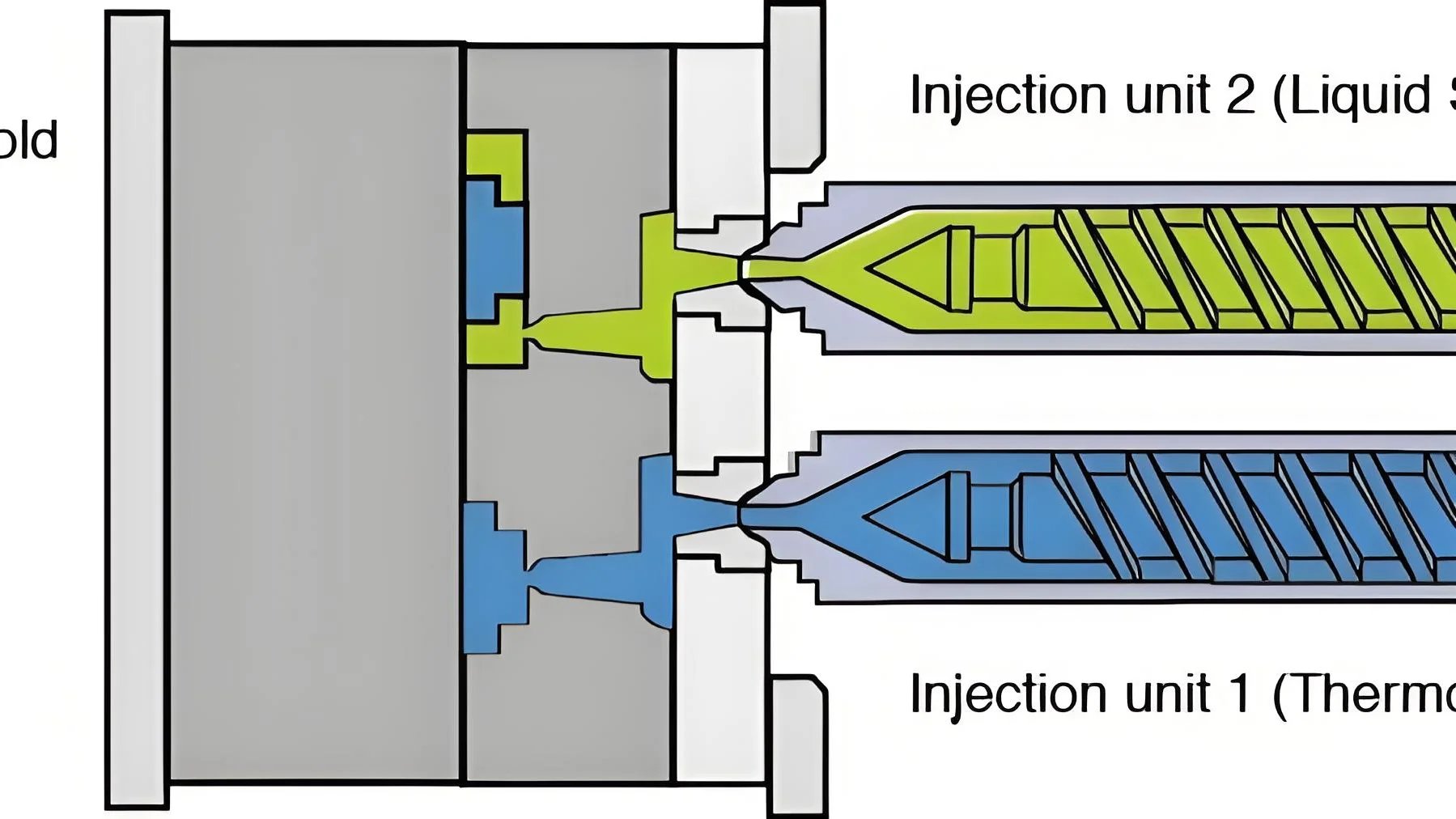
Importance of Sprue Bushing Placement in Mold Design
My mentor always stressed placing the sprue bushing in the center when I started working with molds. Think of it as the mold’s heart, giving energy to every part. Placing it near the center or the main cavity area shortens the runner path and quickens the melt flow4. It’s more than just being efficient; it’s like taking the quickest way home after a long day. It feels right and natural.
Balanced Layout for Multi-Cavity Molds
Creating a layout for multi-cavity molds can be tricky, like solving a jigsaw puzzle. On one project, arranging cavities in a tight, balanced way greatly reduced runner length and allowed even melt flow. We examined every detail, like arranging family photos on a wall – each piece had its perfect spot.
Layout Type | Benefits |
---|---|
Circular | Shorter runner paths |
Rectangular | Even distribution of melt |
Avoiding Unnecessary Offsets
A common issue is preventing unnecessary shifts in sprue bushing placement. It’s similar to parking a car in a tight space without scratching anything. One must consider everything around, like parting surfaces and cooling systems. A well-placed bushing lets the melt flow smoothly without detours.
Practical Applications and Considerations
Direct Gate Method: I recall working on large plastic container projects where a direct gate really changed things. It let the melt flow right into the cavity, speeding up production like a machine running perfectly.
Side Gate with Short Branch Channel: For multi-cavity molds, locating the side gate was essential. Putting it near the main runner kept the melt evenly spread and distances short, like finding the right balance in a team sport.
Injection Method | Use Case |
---|---|
Direct Gate | Large single-cavity molds |
Side Gate + Short Branch | Multi-cavity molds with side access |
Understanding these ideas is crucial for designers like Jacky5, focusing on product and mold design. This knowledge is about more than just better production; it’s about creating quality with precision and care.
Sprue bushing positioning affects melt flow efficiency.True
Proper sprue placement shortens runner length, enhancing melt speed.
Rectangular layouts always minimize runner paths in molds.False
Circular layouts typically result in shorter runner paths than rectangular ones.
Why Should You Consider Direct Gate Over Other Injection Methods?
Do you often feel overwhelmed by the many choices in injection molding? I do. Let me say, the direct gate approach truly transforms the process.
Direct gate injection suits single-cavity or large-scale molds well. It shortens the main channel length. Melt flow enters the cavity faster. Efficiency improves. Product quality grows better.
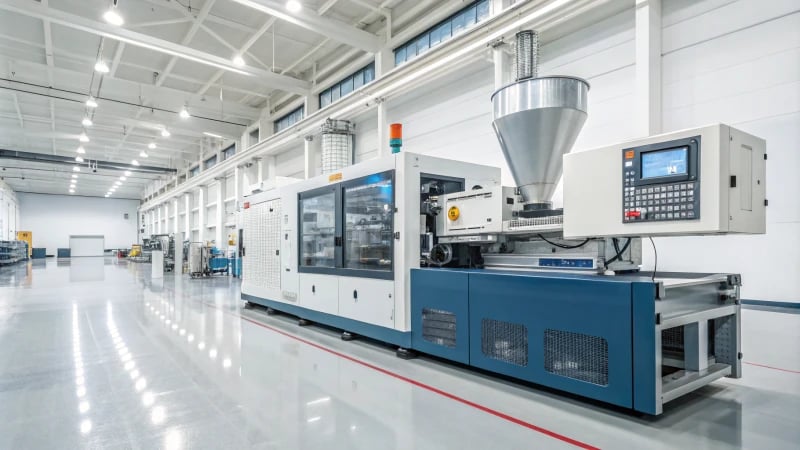
The Efficiency of Direct Gate Injection
I remember learning about direct gate injection6 for the first time. It was like a bright moment in my career as a mold designer. Direct gates cut the main channel short, using less material and speeding up cycle times. Manufacturers love this, especially for big or single-cavity molds where efficiency matters.
Advantages | Description |
---|---|
Reduced Channel Length | Direct gates connect the main channel directly to the cavity, minimizing path length. |
Cost Efficiency | Shorter paths mean less material usage, saving costs on raw materials. |
Enhanced Quality | Shortened flow paths reduce cooling time variance, improving the quality of the end product. |
Application in Large-scale Molds
Think of large plastic containers. Direct gates7 let the molten plastic fill the cavity quickly, cutting down cooling and hardening time. This ensures products have even thickness and consistency throughout.
By adopting a smart layout of mold cavities, manufacturers can further optimize this process. A compact setup helps the melt flow evenly, preventing defects like sink marks and warping.
Structural Considerations
Pairing a hot runner system8 with direct gates accelerates the process. Optimizing the hot runner plate’s design lowers the main runner length, allowing efficient melt flow to each cavity.
In molds with multiple layers, direct gates shorten horizontal flow distances across each layer, ensuring quick and even melt entry into each cavity or runner.
Balancing Design Needs
Balancing is crucial when considering direct gate injection benefits alongside design needs. For example, if a branch channel is necessary, combining a side gate with a short branch can be helpful. Positioning side gates near the main runner maintains efficiency even without using direct gating.
Choosing direct gate injection depends on understanding your project requirements—considering product size, mold complexity, and costs—making smart choices to reach manufacturing goals and achieve high-quality results.
Direct gate reduces material waste.True
Direct gate shortens the main channel, leading to less material use.
Direct gate is unsuitable for large-scale molds.False
Direct gate is ideal for large-scale molds due to efficient melt flow.
How can I utilize the structural characteristics of molds?
Have you ever thought about how complex mold designs improve production efficiency? Molds transform how things are produced, really changing the process. Let’s explore the fascinating world of molds and see the amazing features that create this magic.
Mold designs use special features. By changing cavity layouts, moving sprue bushings and picking the best injection methods, we get better results. This reduces waste and improves product quality. Efficiency very likely increases.
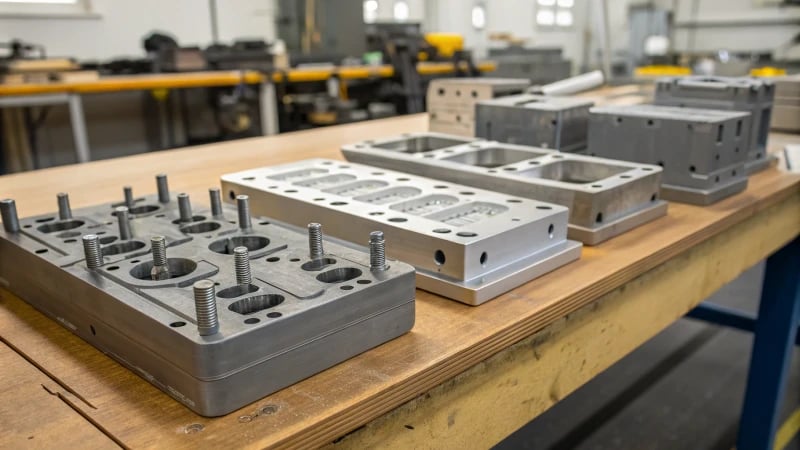
Rational Layout of Mold Cavities
I started in mold design thinking that layout was just a small detail. It’s really like placing furniture in a room. A cluttered setup makes everything feel tight. A tidy cavity pattern shortens the path from the main channel to the cavities and leads to smoother flow. My first circular design changed everything. Flow improved immediately, as if I had found the right spot for a sofa.
Short paths matter. Positioning cavities near the main channel cuts flow length, which really helps with odd-shaped items like long strips. It’s similar to discovering shortcuts in a video game. Every reduction counts.
Sprue Bushing Positioning
Placing sprue bushings accurately is essential. The center brings balance. Nozzle-to-cavity paths are shorter, leading to fewer issues. I once put parts incorrectly and disrupted the whole system. This taught me to keep components from blocking the best placement spots.
Example Layout: | Mold Part | Optimal Position |
---|---|---|
Sprue Bushing | Centered | |
Main Channel | Shortened Path | |
Cavity Arrangement | Compact |
Suitable Injection Methods
Picking injection methods wisely is important. Direct gate methods fit large molds well by sending melt straight into cavities, like taking the shortest route with no stops. If branch channels become necessary, using a side gate with a short branch distributes melt evenly.
Utilizing Structural Characteristics
Features like hot runner systems really help in directing melt quickly. Main runners, placed smartly in hot runner plates, speed up transport. Multi-layer mold designs make a big difference by organizing runners vertically, saving space and shortening the flow path.
Learning these structural tricks not only improves how a mold works but also raises production speed and product quality. Applying these ideas properly can really transform manufacturing steps9.
Circular cavity layout reduces main channel length.True
A circular layout shortens the main channel, improving flow efficiency.
Direct gate method increases flow distance in large molds.False
The direct gate method reduces flow distance by feeding melt directly.
Why are multi-layer mold designs beneficial?
Do you ever think about why multi-layer mold designs really revolutionize factories?
Multi-layer mold designs improve production by using vertical space effectively. These designs reduce cycle times and provide consistent quality for all products. The method allows for making many parts at the same time. This reduces costs and increases output. Costs go down and output rises.
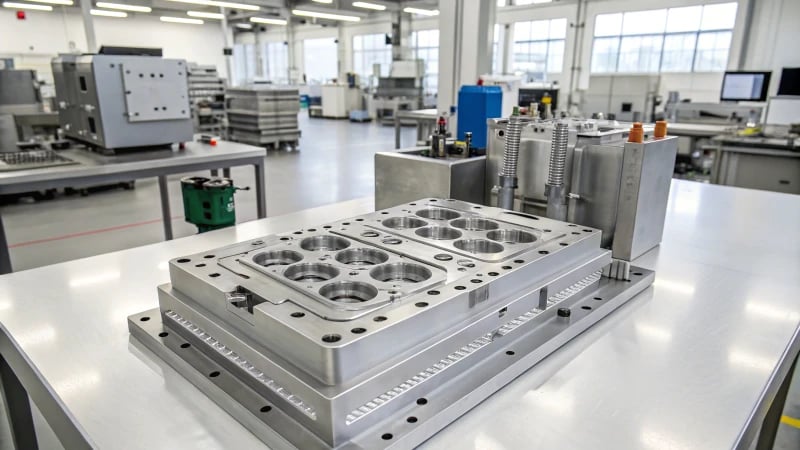
Optimized Space Utilization
I recall the first time I saw a multi-layer mold working; it was like watching a grand show in the world of manufacturing. These molds cleverly use space by stacking layers on top of each other. It reminded me of a tall building using every inch without needing more land. This method is very valuable in places where space is tight, such as space-constrained environments10.
Reduction in Cycle Time
However, what truly grabbed my attention was the quicker cycle time. Imagine producing several items at once – like baking many cakes in one oven, each perfectly baked. Multi-layer molds allow this by handling multiple spaces at the same time. I thought this might cut down production time for high-demand items, like plastic boxes.
Benefit | Impact |
---|---|
Reduced Cycle Time | Faster production per batch |
Space Efficiency | More parts produced per square foot |
Enhanced Product Quality
Consistency matters in manufacturing and these molds impress. They keep every product at the same high level by spreading material evenly over layers. By adopting a rational layout of mold cavities and optimizing the position of the sprue bushing, material flow is balanced across layers, reducing variance in product quality.
Cost-Effectiveness
The first cost of a multi-layer mold might appear high, but it benefits in the long run. I’ve seen how fewer machines are needed because each handles more output and efficient use of materials leads to much less waste. For instance, employing a hot runner system optimization can further reduce costs by minimizing material usage.
Applications Across Industries
Industries like car-making and electronics find these molds very flexible. Whether it’s for molding detailed parts or complex pieces, advanced injection methods give options such as advanced injection methods11. It’s exciting to watch how this technology changes industries, providing an edge by increasing output while keeping top-level quality.
These experiences show why multi-layer mold designs gain popularity. They’re about smarter manufacturing. For more about this design approach, see these insights on industrial applications12.
Multi-layer molds reduce production cycle time by 50%.True
Multi-layer molds process multiple parts per cycle, significantly lowering cycle time.
Multi-layer molds increase horizontal space requirements.False
They optimize vertical space, reducing the need for horizontal expansion.
Conclusion
Optimizing mold design through cavity arrangement, sprue bushing positioning, and injection methods enhances efficiency, reduces waste, and improves product quality in manufacturing processes.
-
Discover how arranging mold cavities compactly optimizes material usage and flow dynamics. ↩
-
Learn about effective sprue bushing placement for enhanced mold efficiency. ↩
-
Explore the benefits of using a direct gate method to minimize flow distance. ↩
-
Explores how sprue bushing impacts melt flow efficiency and product quality, offering insights into its strategic placement. ↩
-
Highlights the influence of sprue bushing on injection molding processes, detailing its role in optimizing production. ↩
-
Explore how direct gate injection can streamline manufacturing processes and enhance product quality. ↩
-
Learn how arranging mold cavities compactly can optimize injection molding efficiency. ↩
-
Discover how hot runner systems can improve material flow and reduce waste in injection molding. ↩
-
Discover how implementing structural features in molds can enhance manufacturing outcomes and product quality. ↩
-
Explore how vertical stacking optimizes limited space and increases production output. ↩
-
Discover cutting-edge injection techniques that enhance precision and efficiency. ↩
-
Learn how different industries leverage multi-layer molds for complex manufacturing. ↩