Have you ever thought about how pressure in injection molding shapes the finished item? Let’s explore how this process works!
Injection pressure influences the size precision of a part by deciding how thoroughly the plastic fills and packs in the mold. High pressure produces parts that are too large and stressed. Low pressure results in parts that are incomplete or uneven in size.
At the beginning of my journey into injection molding, the details surprised me. Even a tiny change could greatly affect product quality. Knowing these details is vital. The end product needs to match our goals and work well. Let’s dive into the mysteries of injection pressure. This step is key in shaping precise components.
High injection pressure increases product size.True
Excessive pressure compacts the melt tightly, expanding product dimensions.
Low injection pressure ensures uniform size.False
Insufficient pressure causes uneven cooling, leading to size variations.
- 1. What Happens When Injection Pressure Is Too High?
- 2. How Does Low Injection Pressure Affect Product Uniformity?
- 3. What Are the Consequences of Internal Stresses from Injection Molding?
- 4. How Can Injection Pressure Be Optimized for Precision Parts?
- 5. How does cooling affect dimensional accuracy?
- 6. Conclusion
What Happens When Injection Pressure Is Too High?
Have you ever thought about the effects of raising the pressure in injection molding? High pressure causes big changes in your product’s quality and performance. Let’s explore this impact.
High injection pressure causes the product to grow bigger. It really expands. Size increases and stress develops inside. This extreme pressing leads to unstable dimensions. After coming out of the mold, the product might change shape and warp.
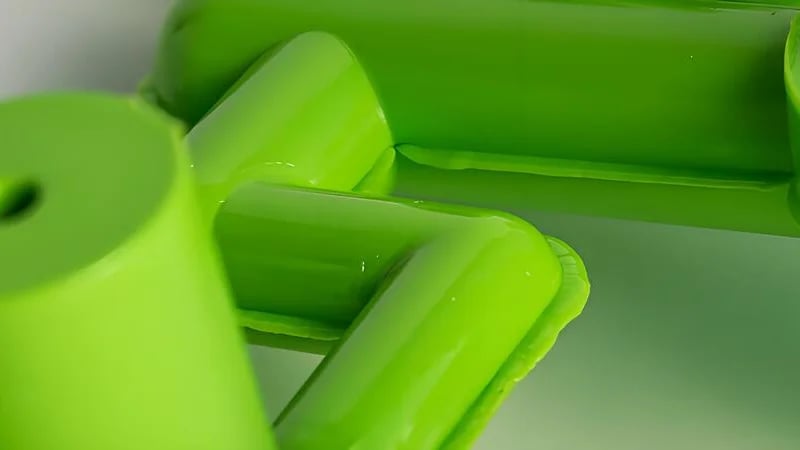
Impact on Dimensional Accuracy
I recall the first time I faced a problem with high injection pressure. It happened during a project with electronic casings, where we noticed increasing the pressure from 100 MPa to 120 MPa caused the parts to slightly grow. This made fitting them with other parts difficult. It showed clearly how too much pressure results in products being bigger than planned. Imagine expecting a tight fit and finding a puzzle piece that’s too large!
Pressure Level | Expected Dimension Increase |
---|---|
100 MPa | Nominal |
110 MPa | +1% |
120 MPa | +2% |
Dimensional Instability Concerns
High pressure impacts go beyond just larger size; they cause inside stress within the product. I once molded big plastic sheets and was shocked to see them warp a lot after cooling. Warp happened due to uneven stress distribution, badly affecting the flatness and quality1 of the final product.
- Internal Stress Release: Once out of the mold, these stresses may lead to unexpected size changes, complicating precision.
- Quality Implications: Warping or bending can lower the function and look of your product.
Comparing High vs. Low Injection Pressure
I have witnessed how both high and low injection pressures affect production. High pressure might cause over-expansion, while low pressure often results in too-small products due to incomplete mold filling. It is a fine balance.
Injection Pressure | Dimensional Effect |
---|---|
High | Larger |
Low | Smaller |
Understanding injection pressure2 is essential for anyone in manufacturing, especially if seeking precision without product damage. By carefully adjusting these settings, designs not only meet but often exceed quality hopes.
High injection pressure increases product size by 1% - 2%.True
Excessive pressure compacts the melt, expanding product dimensions.
Low injection pressure ensures uniform product dimensions.False
Insufficient pressure leads to uneven cooling and dimensional differences.
How Does Low Injection Pressure Affect Product Uniformity?
Do you ever think about why your carefully crafted injection-molded items sometimes lack uniformity?
Low injection pressure often results in incomplete filling of mold cavities. Products tend to be smaller and less uniform. This usually results in defects like uneven thickness. Surface deformations often occur. Product reliability is affected.
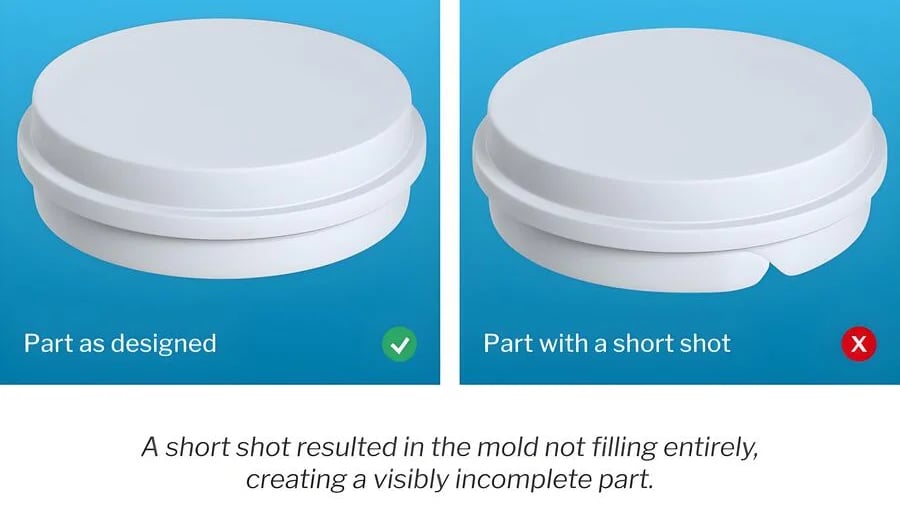
The Basics of Injection Pressure
When I first started learning about injection molding, pressure seemed confusing. Injection pressure is the force that pushes hot material into the mold. Without strong force, it feels like trying to fill a balloon with a tiny stream of water—slow and not effective.
Effects on Dimensional Accuracy
In my early days of designing products, I learned important lessons. When pressure is too weak, the material doesn’t fill the mold completely. Imagine you’re crafting plastic boxes with walls of a specific thickness. With low pressure, walls turn out as thin as paper, leading to major problems.
Component | Effect of Low Pressure |
---|---|
Wall Thickness | Reduced due to incomplete filling |
Overall Size | Smaller than expected |
Uniformity Challenges
Picture baking a cake that rises unevenly on one side. Low injection pressure causes similar issues. Different pressures lead to cooling and shrinking at different rates, which results in dents or surface marks. Those complex plastic structures with different wall sizes face trouble. Thin parts cool quicker than thick parts, causing problems—it’s like your precise designs slipping away.
Consider plastic products with both thin- and thick-walled sections: thin areas may solidify before the thick ones, creating inconsistencies. The result is a product that fails to meet design specifications.
Insights from Industry Practice
Experienced mold designers3 speak of finding the perfect pressure balance. Like a chef fine-tuning oven settings, they adjust how material flows and cools for a perfect outcome.
Exploring advanced injection methods4 is very interesting. By changing molds or material types, these problems can reduce. Understanding these details has given me strength—like Jacky, I improve our methods to create attractive and useful products.
High injection pressure increases product size.True
Excessive pressure compacts the melt, expanding dimensions by 1-2%.
Low injection pressure ensures uniform product size.False
Insufficient pressure causes uneven cooling, leading to size variations.
What Are the Consequences of Internal Stresses from Injection Molding?
Had a project that seemed flawless on paper but turned out differently in real life? Injection molding sometimes works that way too!
Internal stresses in injection molding often cause problems such as warping, changes in size and weaker products. Controlling the pressure during injection and the speed of cooling is very important to solve these issues. Reducing internal stresses is essential.
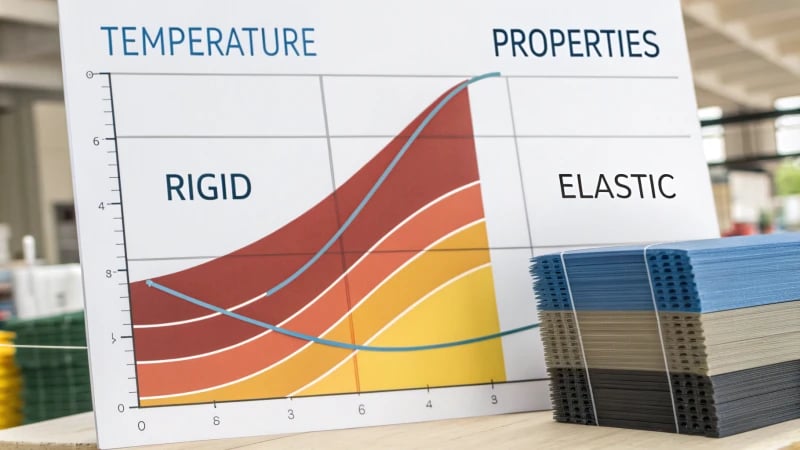
Effects of High Injection Pressure
I recall the first time I dealt with high injection pressure problems very clearly. It felt like trying to push toothpaste back into its tube. We molded electronic housings5 and when the pressure increased from 100 MPa to 120 MPa, the parts grew just 1-2% larger than necessary. This tiny size difference meant they couldn’t fit with other components, which created many future problems.
- Dimensional Instability: Too much pressure causes inner stresses, leading to warped products after cooling. Once, a batch of big plastic sheets twisted so much that they looked like potato chips. It showed me the importance of balancing pressure properly.
Effects of Low Injection Pressure
On the opposite end, low injection pressure brings different challenges. I worked on constructing plastic containers6 where pressure lacked strength, resulting in smaller than planned dimensions. It was really annoying to see containers that failed to meet design specs or hold their intended capacity.
- Uniformity in Size: Low pressure causes uneven melt flow, creating surface dents and size variations. I’ve noticed products with different wall thicknesses. Consistency became a huge challenge when precision was vital.
Addressing Internal Stresses
To resolve these issues, optimizing injection molding parameters7 holds great importance. Advanced monitoring tools during production play a significant role in keeping consistency and quality.
Parameter | Effect on Product | Recommendations |
---|---|---|
High Pressure | Larger dimensions | Use calibrated pressure settings |
Low Pressure | Smaller dimensions | Ensure complete cavity filling |
Uneven Cooling | Warping | Optimize cooling channels |
Focusing on these elements matters greatly for preserving the integrity and utility of plastic products. I constantly search for new technologies and systems, seeking improvement in our injection molded items so they match both design and functional needs.
High injection pressure increases product size.True
Excessive pressure compacts the melt, increasing product dimensions.
Low injection pressure leads to uniform product size.False
Insufficient pressure causes uneven cooling, affecting size uniformity.
How Can Injection Pressure Be Optimized for Precision Parts?
Do you ever think about achieving perfect precision in injection molding?
Optimize injection pressure for precise parts by balancing high and low pressures. Adjust injection speed and temperature. Also, modify mold design. These changes help avoid defects. Parts keep their exact shape this way.
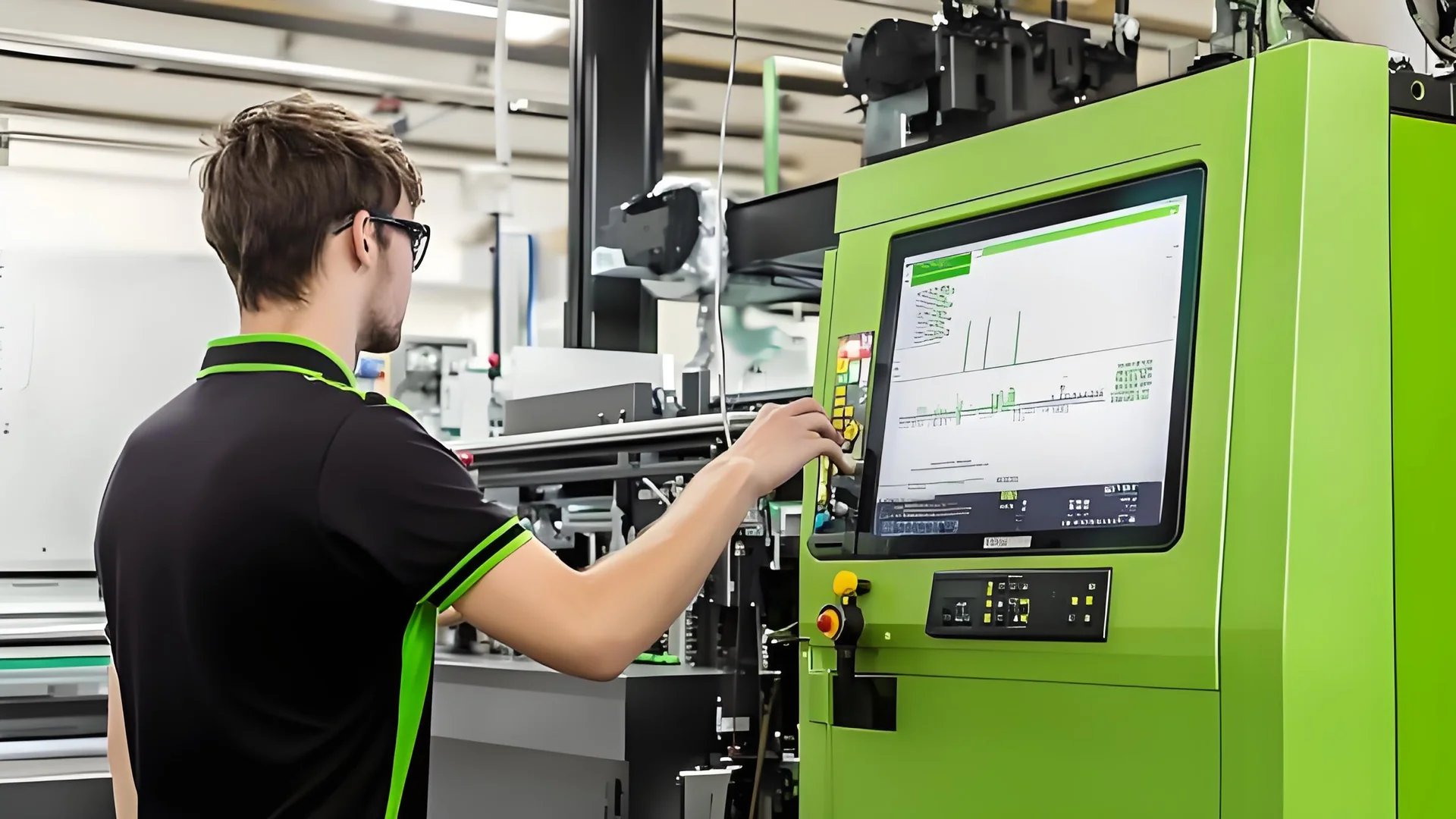
Understanding Injection Pressure Dynamics
When I started working with injection molding8, I quickly understood how important injection pressure was. It is like balancing on a tightrope – using too much pressure causes the product to expand too much; using too little leaves empty spaces. Injection pressure controls how materials move and fill the mold, which affects the final size of the product.
Effects of High Injection Pressure
I remember my first mistake with high injection pressure. We were creating casings for electronic parts, and I thought increasing the pressure would quicken the process. Instead, it caused the casings to grow larger than expected by about 2%. This situation showed me that too much pressure causes inner stress, leading to warping after unmolding. Picture trying to fit a square peg in a round hole.
Parameter | High Injection Pressure Effects |
---|---|
Dimension | Increases size |
Stress | Causes warping |
Effects of Low Injection Pressure
On the contrary, once we didn’t increase the pressure enough while molding plastic containers. The result was thin, weak walls that failed to meet design needs. This event taught me that not using enough pressure leads to improper filling of the cavity, impacting the size and strength of the structure.
Parameter | Low Injection Pressure Effects |
---|---|
Dimension | Decreases size |
Surface | Causes depressions |
Balancing Injection Pressure for Precision Parts
Finding the right injection pressure is like cooking a perfect steak – not too rare, not too done. I often change injection speed to control pressure and adjust temperatures so the melt flows correctly. Certainly, revisiting mold design9 is also important to fill everything evenly.
Using modern software tools10 truly changed the game for me. Simulation of outcomes helps us set precise pressures tailored to different materials and designs, saving resources while achieving perfect results.
Knowing these dynamics not only improves dependability but also lifts the performance of precision components11. It’s all about each piece fitting perfectly, just like a wonderful symphony where each note is spot on.
High injection pressure increases product size by 1-2%.True
Excessive pressure over-compacts the melt, expanding dimensions.
Low injection pressure ensures uniform product dimensions.False
Low pressure causes uneven flow and cooling, affecting uniformity.
How does cooling affect dimensional accuracy?
You know, there’s something almost magical about the role cooling plays in manufacturing.
Cooling affects the accuracy of size by managing how materials harden and get smaller. Good cooling leads to even shrinking, which cuts down on bending or twisting. This control keeps the size of parts exact during production.
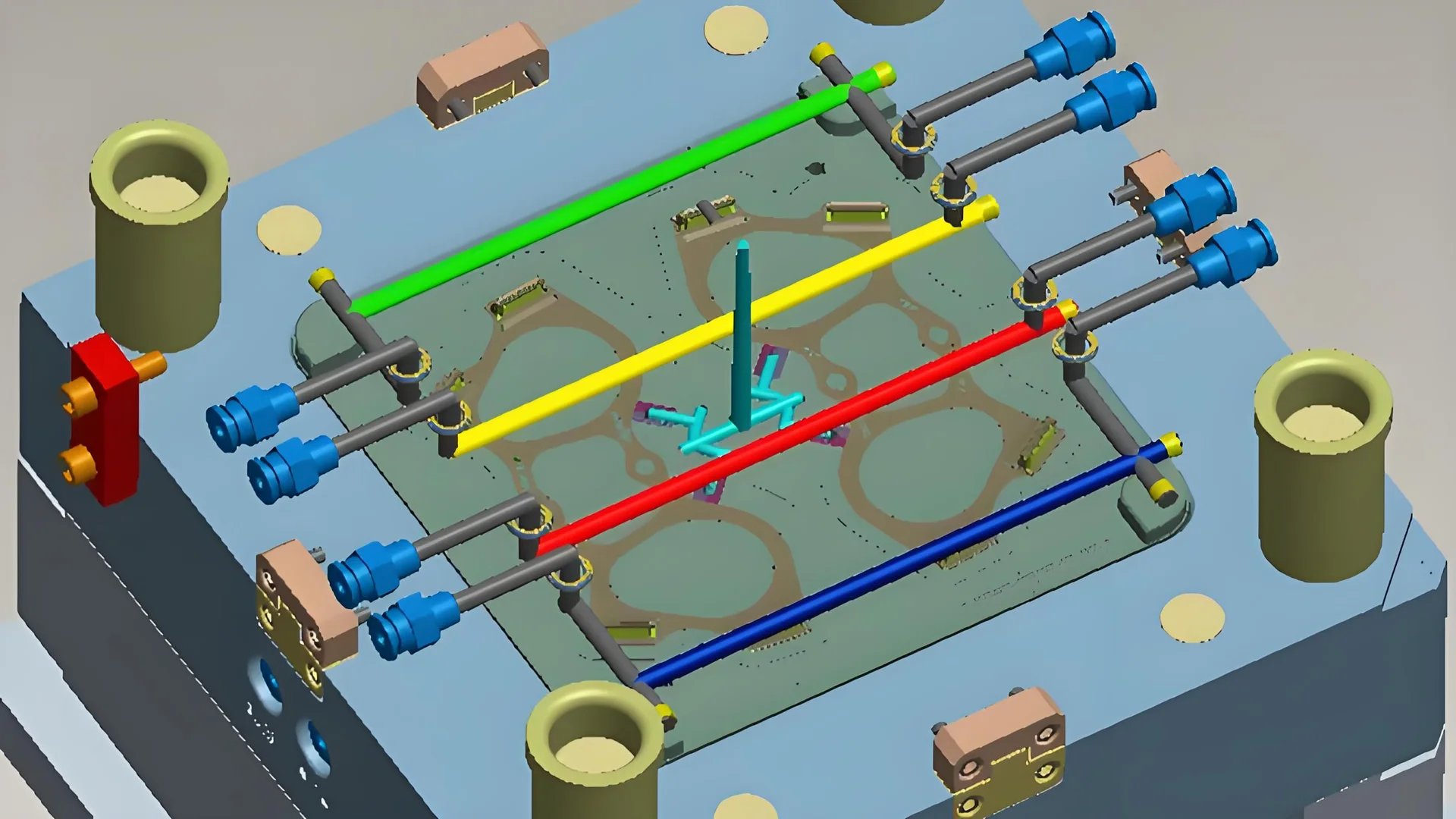
The Importance of Cooling Rates
Remember placing a hot cup of coffee on a cold windowsill? The top cooled unevenly, leaving a skin. This resembles manufacturing issues. Rapid cooling may lead to internal stress12 and shape changes after removing the item from the mold. Slow cooling helps everything shrink evenly and keeps the shape stable.
Cooling Rate | Impact on Dimensional Accuracy |
---|---|
Rapid | Increases risk of warping and deformation |
Moderate | Balances solidification and shrinkage |
Slow | Promotes uniform shrinkage, less warping |
Influence on Material Properties
Different materials respond uniquely to cooling. Think about ice cream and soup; ice cream softens faster. Plastics expand more than metals when heated, requiring careful cooling control. Excessive cooling causes problems like empty spaces or surface dents in plastics, while metals may crack inside if not cooled correctly.
- Plastics: Too much cooling creates voids or dents.
- Metals: Bad cooling forms micro-cracks and harms strength.
Cooling Techniques
Baking cookies shows how arrangement affects baking. Similarly, manufacturing uses molds with efficient cooling channels13 to control temperature gradients across parts.
- External Cooling Systems: These systems cool parts quickly to stop changes after shaping, reducing post-processing deformations.
- Thermal Imaging: Real-time monitoring of temperature distribution allows for adjustments as needed for optimal results.
Using these methods teaches us better product quality by controlling temperature accurately. More knowledge about good mold design shows how efficient cooling channels reduce flaws. Innovations like thermal imaging14 offer live check-ups on cooling processes, providing clear images of temperatures during production.
High injection pressure increases product size.True
Excessive pressure compacts the melt, expanding dimensions by 1-2%.
Low injection pressure ensures uniform product size.False
Insufficient pressure causes uneven melt flow, leading to size variations.
Conclusion
Injection pressure significantly affects the dimensional accuracy of molded products, with high pressure causing size increases and internal stresses, while low pressure leads to incomplete filling and smaller dimensions.
-
Understand how internal stresses influence the flatness and overall quality of molded products by exploring this resource. ↩
-
This link provides an overview of injection pressure dynamics, helping you optimize manufacturing processes for better product quality. ↩
-
Discover expert insights on why maintaining correct injection pressure is vital for achieving consistent product quality. ↩
-
Learn about innovative methods that can address uniformity issues related to low injection pressure. ↩
-
Discover how pressure variations impact high-precision plastic parts to enhance design accuracy. ↩
-
Learn about design considerations for plastic containers with low pressure settings to prevent defects. ↩
-
Explore techniques for optimizing injection molding parameters to reduce internal stresses. ↩
-
Exploring this link provides foundational knowledge on injection molding, crucial for optimizing processes. ↩
-
This link offers insights into maintaining stability, essential for high-quality precision parts. ↩
-
Discovering these tools can enhance prediction accuracy for optimal injection settings. ↩
-
Learn about the role precision plays in manufacturing excellence through this resource. ↩
-
Explore how internal stresses caused by cooling rates affect the dimensional accuracy and stability of manufactured parts. ↩
-
Learn how optimized mold designs can improve cooling efficiency and enhance the dimensional accuracy of products. ↩
-
Discover how thermal imaging technology aids in monitoring temperature distribution, improving cooling strategies, and ensuring precision. ↩