High humidity can wreak havoc on injection molded parts. Let’s explore how anti-deformation design can help combat this issue.
Anti-deformation design for injection molded parts in high humidity environments involves selecting materials with low hygroscopicity, optimizing structural and mold designs, and precise process control. These strategies mitigate moisture-related defects like warping, ensuring enhanced product reliability and durability.
Understanding the basics is just the tip of the iceberg. Dive deeper with me as we explore techniques that not only protect our designs but also enhance their performance under moisture-laden conditions.
Polycarbonate is a low-hygroscopicity plastic.True
Polycarbonate has low moisture absorption, making it suitable for humid environments.
- 1. What Role Does Material Selection Play in Anti-Deformation Design?
- 2. How Can Structural Design Mitigate Humidity-Induced Deformation?
- 3. Why Is Mold Design Crucial for Maintaining Dimensional Stability?
- 4. What Process Control Techniques Enhance Product Reliability in Moist Environments?
- 5. Conclusion
What Role Does Material Selection Play in Anti-Deformation Design?
Choosing the right material is pivotal in preventing deformation of injection molded parts in humid conditions.
Material selection in anti-deformation design involves choosing low-hygroscopicity plastics like polycarbonate (PC) and adding moisture-proofing agents to mitigate humidity-induced deformation.
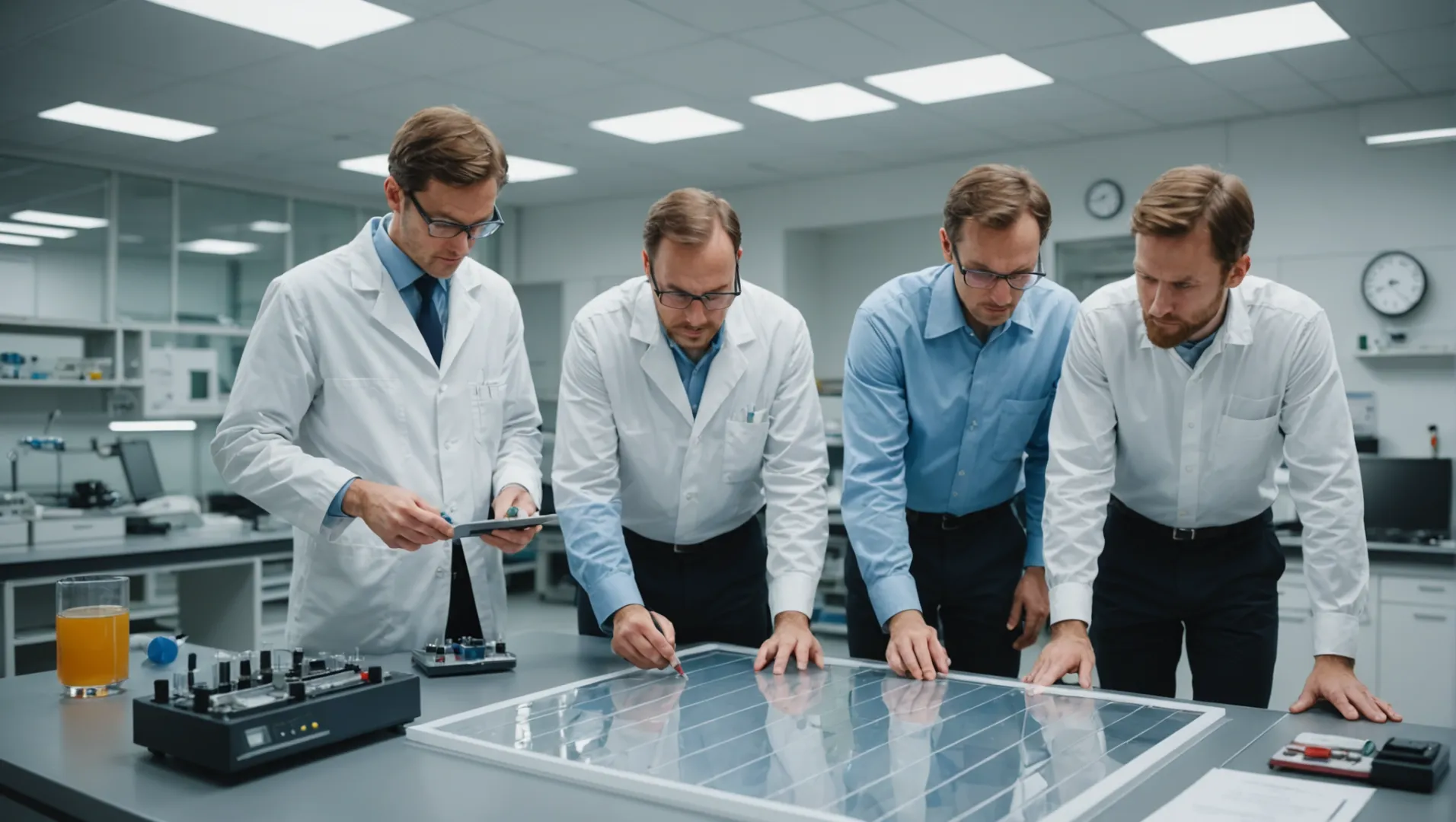
Understanding Hygroscopicity
Hygroscopicity refers to a material’s tendency to absorb moisture from the environment. In high humidity settings, this characteristic can lead to swelling, warping, and other forms of deformation in injection molded parts. Selecting materials with low hygroscopicity is vital for maintaining dimensional stability. Engineering plastics such as polycarbonate (PC), polyoxymethylene (POM), and polyphenylene sulfide (PPS) are preferred due to their resistance to moisture absorption.
When considering materials, engineers should consult technical datasheets from material suppliers to understand the hygroscopicity parameters. These documents provide crucial insights into how different materials will perform in specific environmental conditions. Learn about hygroscopicity parameters1.
Incorporating Moisture-Proofing Agents
In addition to selecting low-hygroscopicity materials, adding moisture-proofing agents can further enhance the material’s resistance to humidity. These agents work by absorbing internal moisture, thereby reducing the risk of deformation. However, it’s essential to consider how these additives might affect the overall properties of the material.
Engineers must ensure that the quantity of moisture-proofing agent is balanced; excessive amounts could alter mechanical properties or processing characteristics. It’s recommended to conduct trials to determine the optimal amount that ensures product quality without compromising performance.
Evaluating Material Properties
Selecting a material is not just about its hygroscopic characteristics. Engineers must evaluate various properties like mechanical strength, thermal resistance, and processability to ensure that the material meets the functional requirements of the component.
Property | Importance |
---|---|
Mechanical Strength | Ensures durability and performance under stress |
Thermal Resistance | Maintains integrity under varying temperatures |
Processability | Affects ease of manufacturing and cost-efficiency |
By balancing these properties with moisture resistance, engineers can optimize their design for both performance and longevity in humid environments.
Conclusion: A Holistic Approach
Material selection is a critical aspect of anti-deformation design in high humidity environments. By understanding hygroscopicity, employing moisture-proofing agents, and evaluating comprehensive material properties, engineers can effectively mitigate deformation risks. Integrating these considerations with advanced structural design techniques2 ensures robust product performance.
Polycarbonate (PC) is a low-hygroscopicity plastic.True
Polycarbonate is known for its low tendency to absorb moisture, making it suitable for anti-deformation design.
Moisture-proofing agents increase material hygroscopicity.False
Moisture-proofing agents decrease hygroscopicity by absorbing internal moisture, reducing deformation.
How Can Structural Design Mitigate Humidity-Induced Deformation?
Humidity-induced deformation is a significant challenge in structural design, especially for materials like plastics. Understanding how to mitigate this can enhance durability and performance.
Structural design mitigates humidity-induced deformation by ensuring uniform wall thickness, incorporating ribs and supports, and allowing for deformation tolerance. These strategies reduce warping and ensure product integrity under moisture-laden conditions.
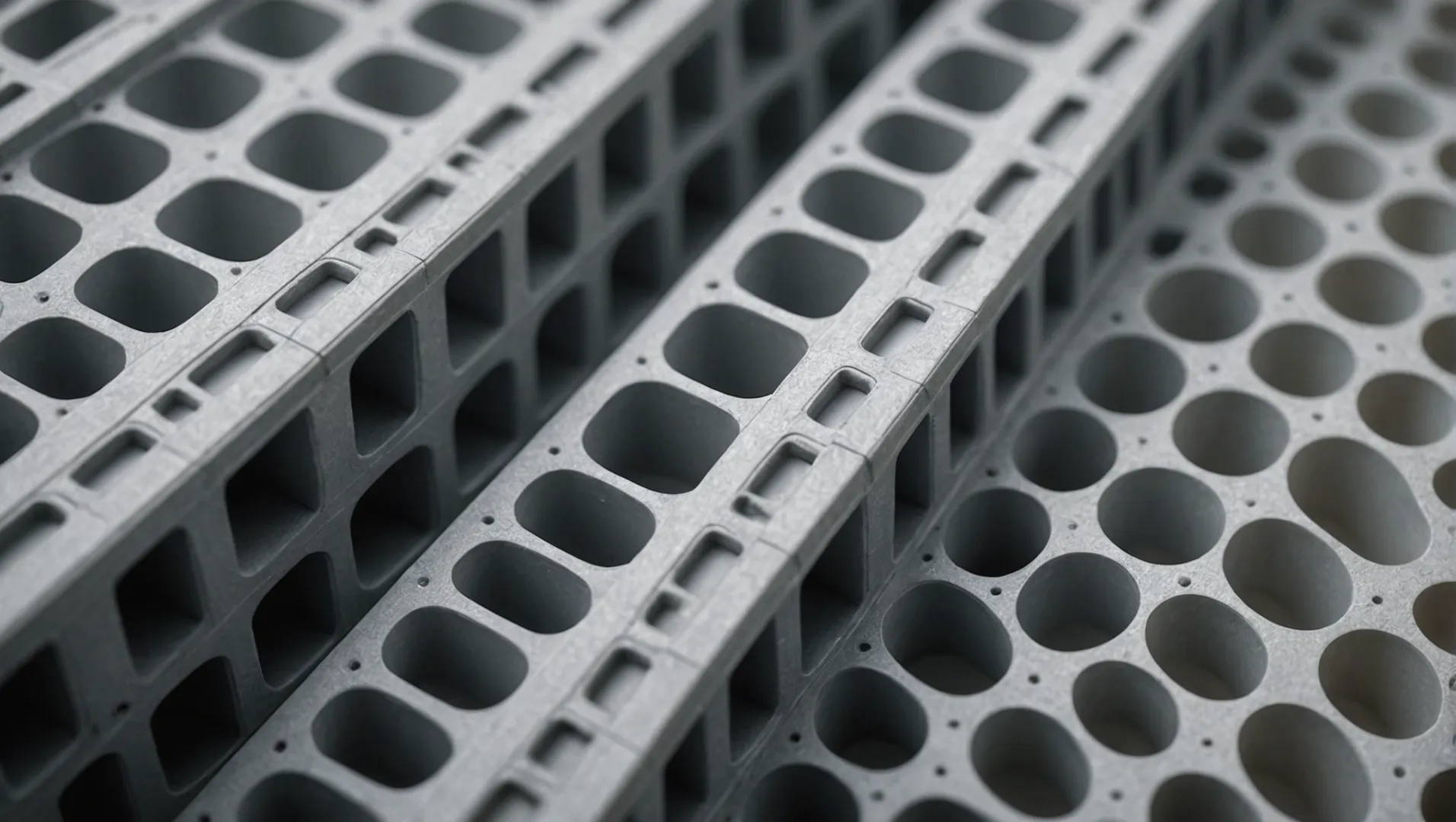
The Importance of Uniform Wall Thickness
One critical aspect of mitigating humidity-induced deformation is ensuring the uniformity of wall thickness in injection molded parts. Uneven wall thickness can lead to differential cooling and shrinkage, resulting in warping or bending. A consistent wall thickness helps in maintaining dimensional stability and reduces stress concentrations.
To achieve uniform wall thickness, designers can utilize advanced wall thickness analysis software3 that assists in optimizing the part geometry. This tool allows for precise adjustments to the design, ensuring even distribution and reducing potential deformation.
Incorporating Ribs and Support Structures
Another effective strategy involves the integration of ribs and support structures. These elements not only enhance the mechanical strength and rigidity of the component but also help resist the expansive forces introduced by moisture. Properly designed ribs can act as reinforcements, distributing loads evenly and minimizing areas prone to deformation.
The design guidelines for ribs suggest avoiding ribs that are excessively high or narrow, as these can cause defects like sink marks during the molding process. Instead, a balanced approach with appropriate rib height-to-thickness ratios4 is recommended to prevent such issues while maximizing structural integrity.
Designing for Deformation Allowance
Recognizing that some degree of deformation is inevitable in high humidity environments, designers often consider reserving a deformation allowance. This involves deliberately adjusting tolerances in areas requiring high precision so that any post-deformation dimensions still meet functional requirements.
Calculating deformation allowance requires a thorough understanding of the material’s response to moisture and environmental conditions. Engineers might use predictive modeling techniques to estimate the degree of expansion or contraction and adjust the design accordingly.
By adopting these structural design strategies, manufacturers can significantly enhance the resilience of their products against humidity-induced challenges. Such designs not only improve reliability but also extend the lifespan of components exposed to varying environmental conditions.
Uniform wall thickness reduces warping in plastics.True
Consistent wall thickness ensures even cooling and shrinkage, reducing deformation.
Ribs should be excessively high to prevent defects.False
Excessive rib height can cause defects; balanced ratios are recommended.
Why Is Mold Design Crucial for Maintaining Dimensional Stability?
Mold design is pivotal in maintaining the dimensional stability of injection molded parts, especially under high humidity conditions.
Optimizing mold design ensures uniform cooling and stress-free demolding, crucial for maintaining dimensional stability in injection molded parts. Implementing a multi-circuit cooling system and a carefully planned demolding mechanism are key strategies in reducing deformation and enhancing part quality.
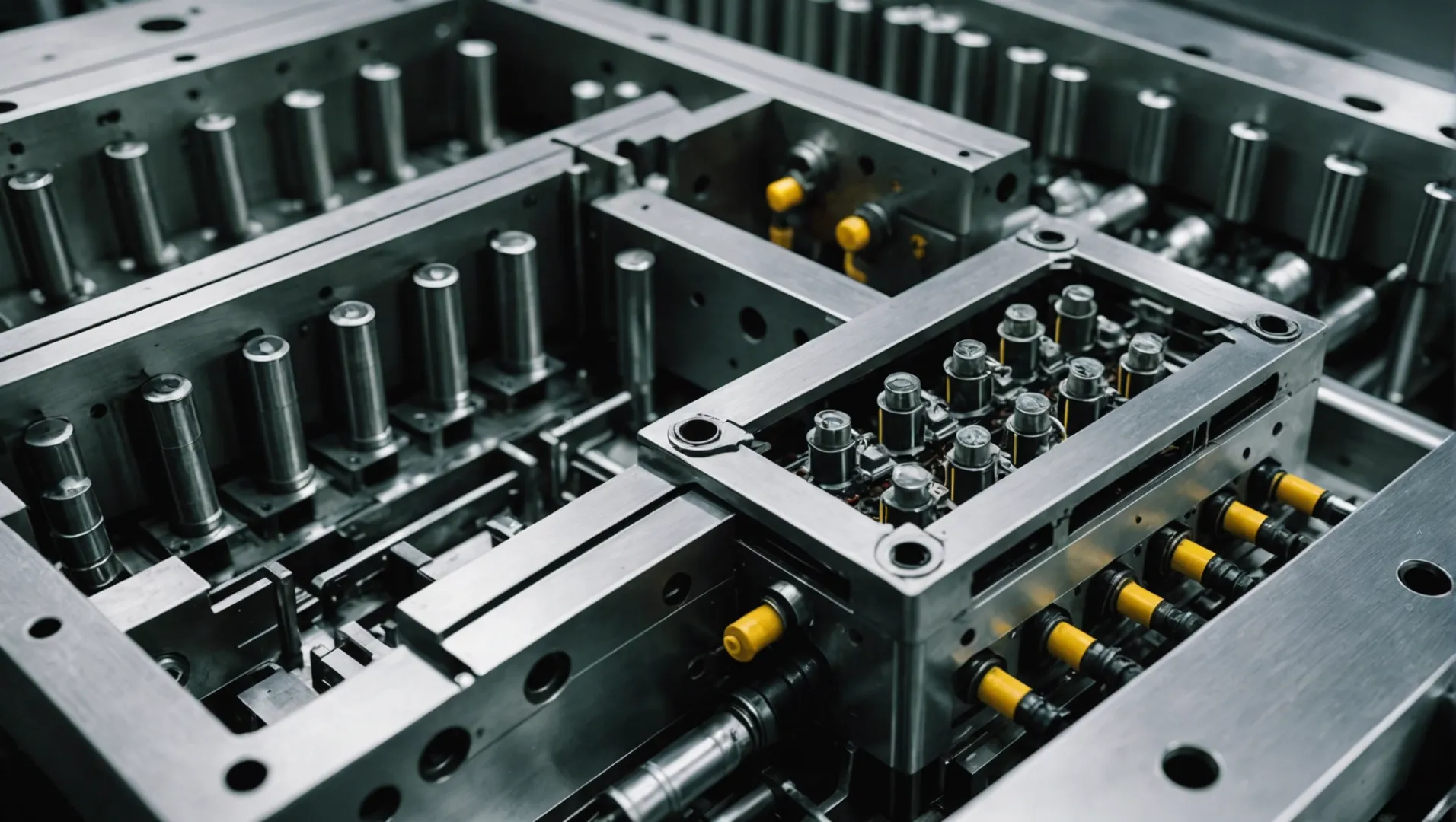
Optimizing the Cooling System
The cooling system in a mold plays a vital role in ensuring that injection molded parts shrink uniformly during the cooling phase. This uniformity is essential to maintain dimensional stability and reduce deformation, especially in environments with high humidity. A multi-circuit cooling system can be particularly effective as it ensures an even distribution of cooling across all sections of the mold. This prevents localized hotspots that could lead to uneven shrinkage and subsequent warping.
Additionally, attention must be paid to the layout of the cooling water circuits. An uneven layout can result in differential cooling rates, which may exacerbate warping issues. Therefore, designing a balanced and efficient cooling system is a critical aspect of mold design that directly impacts dimensional stability.
Designing an Effective Demolding Mechanism
A well-designed demolding mechanism is crucial to minimize the stress exerted on parts during removal from the mold. In high humidity environments, injection molded parts may become softer, making them more susceptible to deformation and damage during demolding. Utilizing methods such as pneumatic or hydraulic demolding can help reduce the stress exerted on parts, thereby minimizing the risk of deformation.
Moreover, designing the demolding mechanism to accommodate the specific characteristics of the material used is important. Each material reacts differently to stress, so tailoring the demolding process can help maintain the integrity of the part.
Case Study: Application of Mold Design Strategies
Consider a case where a manufacturer faced issues with warping in polycarbonate (PC) parts due to high ambient humidity. By redesigning their mold’s cooling system to include multi-circuit pathways and adjusting the demolding approach to use hydraulic systems, they managed to significantly reduce dimensional deviations.
This approach not only improved the consistency of the parts produced but also decreased waste and increased throughput. These strategies demonstrate how thoughtful mold design can effectively address the challenges posed by moisture-related deformation.
For more information on optimizing mold designs for dimensional stability, explore these resources: effective cooling systems5 and demolding techniques6.
Multi-circuit cooling prevents uneven shrinkage in molds.True
Multi-circuit systems ensure even cooling, reducing warping risks.
Hydraulic demolding increases stress on molded parts.False
Hydraulic demolding reduces stress, minimizing deformation risks.
What Process Control Techniques Enhance Product Reliability in Moist Environments?
Ensuring the reliability of products in moist environments necessitates precise process control techniques. These techniques mitigate issues like warping and deformation, common in high-humidity conditions.
Key process control techniques to enhance product reliability in moist environments include adjusting injection molding temperatures and pressures, optimizing drying protocols, and implementing post-processing treatments like annealing.
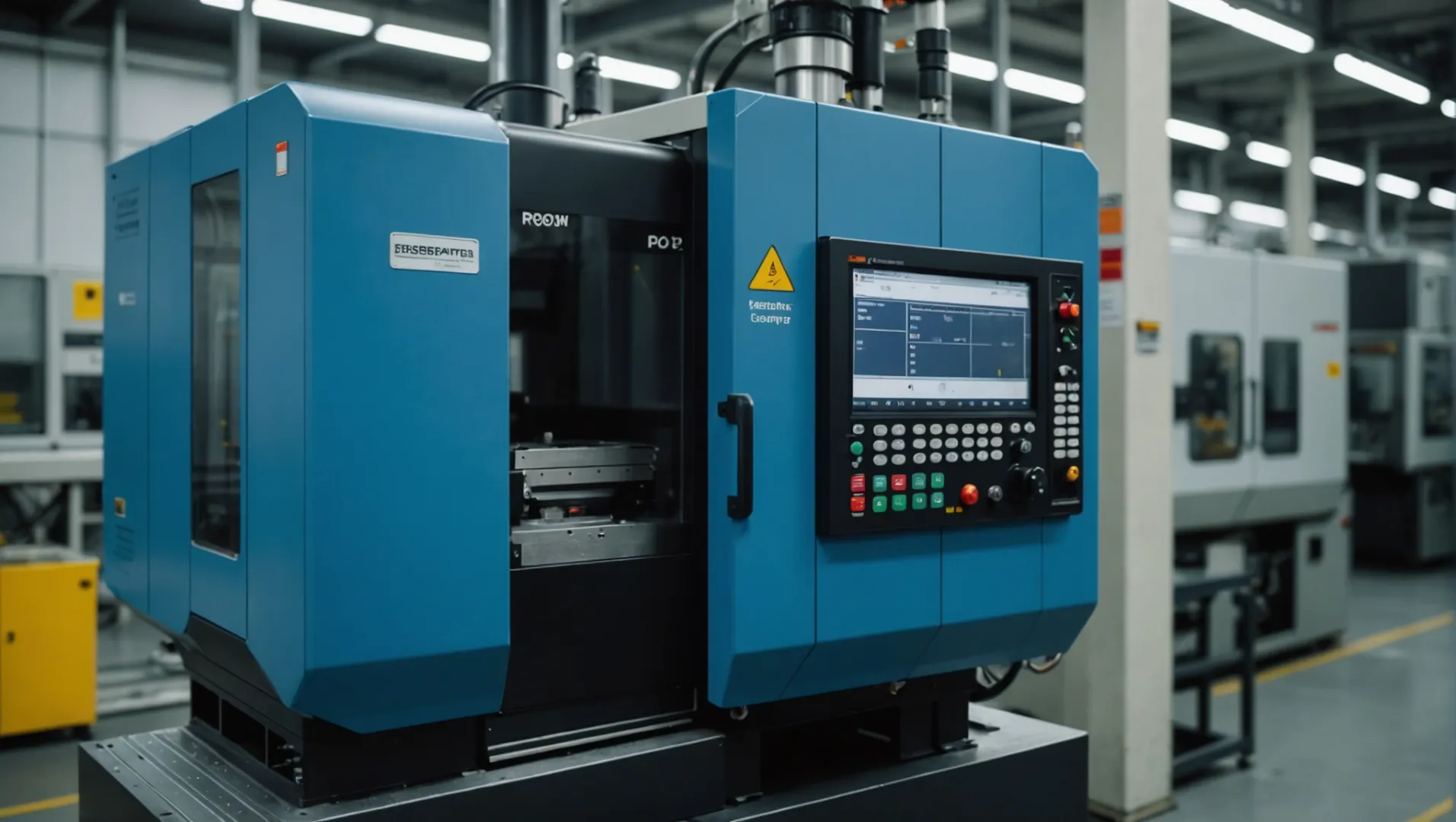
Controlling Injection Molding Temperature and Pressure
The temperature and pressure during the injection molding process are pivotal in dictating the quality and durability of molded parts. In moist environments, it’s essential to adjust these parameters to ensure that the material flows adequately while minimizing internal stress. For instance, setting the right molding temperature can improve the fluidity of the material, thereby ensuring complete cavity filling without defects.
Mold trials can be an effective way to determine the optimal temperature and pressure settings. By experimenting with different parameters, manufacturers can establish the most efficient conditions for specific materials, reducing the risk of deformation.
Optimizing Drying Time and Temperature
For materials with high hygroscopicity, controlling drying time and temperature is critical. In humid conditions, pre-drying materials can significantly reduce moisture absorption during processing. Generally, higher drying temperatures decrease the required drying time; however, excessive temperatures may deteriorate the material’s properties.
Consider using a drying schedule tailored to the specific material and environmental humidity levels. This approach ensures that moisture levels are kept within acceptable ranges, thus maintaining dimensional stability.
Material Type | Suggested Drying Temperature | Suggested Drying Time |
---|---|---|
Polycarbonate (PC) | 120°C | 3-4 hours |
Polyoxymethylene (POM) | 80°C | 2-3 hours |
Polyphenylene sulfide (PPS) | 150°C | 4-5 hours |
Implementing Post-Processing Techniques
Post-processing methods such as annealing can significantly enhance the dimensional stability of injection molded parts. Annealing helps relieve internal stresses that may have developed during molding, thus improving resistance to humidity-induced deformation.
Additionally, humidity adjustment is another technique that can be applied post-molding. By exposing parts to controlled humidity levels, manufacturers can stabilize material dimensions, ensuring long-term reliability even in challenging environments.
For more detailed insights into humidity adjustment methods, you might explore resources on humidity stabilization techniques7.
By integrating these process control techniques—temperature and pressure adjustments during molding, optimized drying protocols, and strategic post-processing—manufacturers can produce components that maintain their integrity and performance in moist environments.
Adjusting molding temperature reduces material defects.True
Proper temperature improves material flow, ensuring complete cavity filling.
Excessive drying temperatures improve material properties.False
High temperatures can deteriorate material properties, not improve them.
Conclusion
Embracing a holistic approach to anti-deformation design ensures that our injection molded parts thrive in high humidity, marrying reliability with longevity.
-
Explore how low-hygroscopicity plastics resist moisture absorption.: There are two groups of polymers: hygroscopic and non-hygroscopic. Each has with a set of processing characteristics and an attraction to moisture. ↩
-
Discover advanced structural design strategies to reduce deformation.: In this guide, we will discuss the principles of structural design and how they apply to plastic injection molded parts. ↩
-
Discover how software optimizes wall thickness to minimize deformation.: It is ideal for determining problem points in a part, such as where it will most likely break or cause malfunctions. ↩
-
Learn ideal rib designs to prevent sink marks and enhance strength.: As a general rule of thumb, ribs should not be thicker than 60% of the nominal wall thickness. Maintaining an appropriate rib-to-wall ratio is essential. ↩
-
Discover advanced cooling strategies to enhance mold performance.: Conformal cooling is a way of introducing cooling channels that closely follow the geometry of more complex parts. ↩
-
Learn about stress-reducing demolding methods for improved part quality.: Get active · Eat a healthy diet · Avoid unhealthy habits · Meditate · Laugh more · Connect with others · Assert yourself · Try yoga. ↩
-
Discover methods to stabilize dimensions in high-humidity settings.: The only solution is to add a dedicated dehumidification system to remove unwanted moisture while maintaining the desired room air temperature. ↩