Thinking about injection molding for your next project? This process really changes everything!
Injection molding efficiently produces high-quality plastic parts at low costs, allowing for complex designs and material versatility, making it ideal for innovative and cost-effective manufacturing.
As a person experienced in product design, I have personally witnessed how injection molding changes ideas into real objects. Injection molding transforms ideas into reality. This process is not just about technical details. It really allows freedom in creation. It lets you craft complex shapes and reach that ideal finish. Each benefit feels like a door opening to new opportunities. You might focus on efficiency or aim for high quality. Injection molding serves as a trustworthy partner in realizing your dreams.
Injection molding offers high production efficiency for projects.True
Injection molding is known for its ability to produce large quantities quickly, making it efficient for manufacturing.
Injection molding is always the cheapest manufacturing method.False
While injection molding is cost-effective, it may not always be the cheapest option depending on project specifics.
What Makes Injection Molding Stand Out Among Manufacturing Processes?
Injection molding is a popular way to manufacture products. Does it really compare well to other methods like CNC machining or compression molding? Let’s explore its unique strengths and weaknesses together. Stay with us and you might discover the insights you need!
Injection molding is very efficient. Short cycles allow fast production. It achieves precise dimensions. Complex shapes come out easily. Production costs remain low.
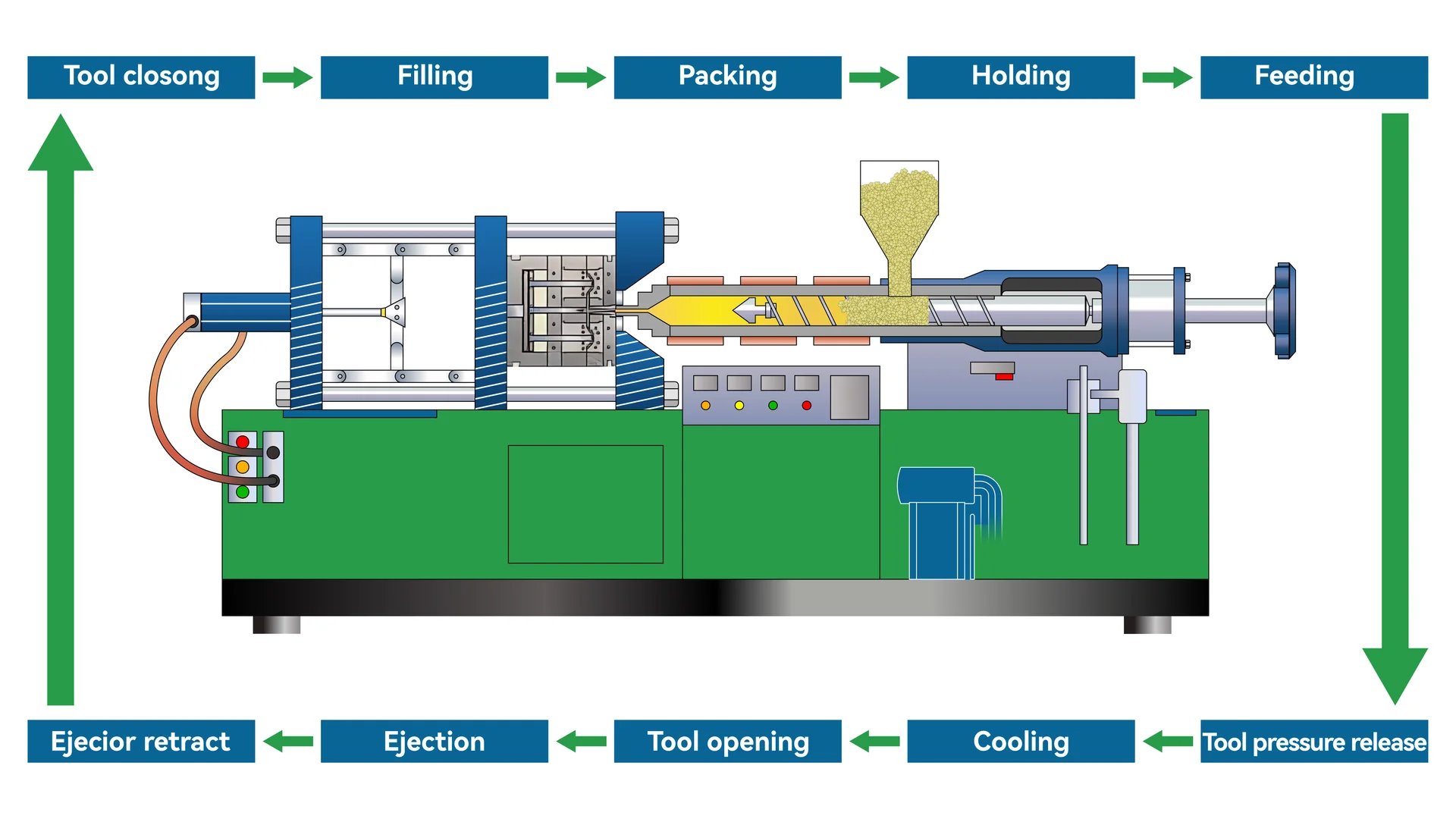
Production Efficiency Comparison
Injection molding amazed me when I started in manufacturing. This method produces high-quality products fast. Speed is not the only advantage.
-
Short Molding Cycle: Injection molding finishes products in seconds or minutes. CNC machining takes much longer. The speed of this process still excites me. It’s thrilling to see a product form so quickly.
-
Automation Compatibility: Observing a factory using automation is fascinating. Injection molding machines work with robots and manipulators effortlessly. They handle automatic feeding and picking. This looks like a perfectly choreographed dance. Automation keeps production efficient and costs low for large numbers of products.
In contrast, processes such as CNC machining1 may require more manual setup and adjustments, which can slow down production rates.
Quality of Products
Quality is very important in my work. Injection molding delivers on this promise.
-
Dimensional Accuracy: Precision is critical in product design. Injection molding uses controlled parameters to keep parts very accurate in size. I’ve seen these precise parts fit together perfectly. This method meets strict assembly requirements that can challenge other processes.
-
Surface Finish: Holding a flawless product feels satisfying. Injection molding often creates products with an impeccable surface finish. Issues like flash or shrinkage marks decrease significantly. Each product seems crafted with care.
Process Type | Dimensional Accuracy | Surface Quality | Cost Per Unit | Production Speed |
---|---|---|---|---|
Injection Molding | High | Excellent | Low | Very Fast |
CNC Machining | Moderate | Good | Moderate | Moderate |
Compression Molding | Low | Variable | Low | Slow |
Design Flexibility
Creating designs is one of the most thrilling parts of my job.
- High Design Freedom: Injection molding provides vast opportunities for complex designs. Internal structures and detailed features are possible. Bringing creative ideas to life with such flexibility is exhilarating. This suits consumer electronics, where creativity and functionality meet.
In contrast, methods like 3D printing2 offer design freedom but move slower and cost more.
Material Adaptability
Let’s talk about materials. Injection molding excels here.
-
Diverse Material Options: Injection molding works with many thermoplastics and thermosetting plastics, such as PE, PP or ABS are just a few examples. I love this versatility! Choosing the right material for each project ensures performance meets expectations.
-
Incorporating Additives: Adding fillers or colorants is one of my favorite tricks! These enhancements elevate product performance and aesthetics, helping products stand out in the marketplace.
Cost Efficiency in Production
Cost is always a consideration for experienced designers.
-
High Raw Material Utilization: Injection molding uses materials efficiently, causing less waste; nearly all raw materials become products! This lowers the cost per unit in mass production—very rewarding for designers who want innovative yet economically smart designs!
-
Economies of Scale: Initial mold design costs may be high; however, over large production runs, the cost spreads out nicely! Mass production becomes very beneficial for businesses without high expenses!
In comparison, methods such as manual machining3 can lead to higher costs per unit due to inefficiencies.
Injection molding has a faster production cycle than CNC machining.True
Injection molding can produce items in seconds to minutes, while CNC machining takes longer due to manual setup, making injection molding more efficient.
Compression molding produces parts with better surface finishes than injection molding.False
Injection molding typically yields excellent surface finishes, while compression molding may result in defects requiring additional finishing work.
What types of products are best suited for injection molding?
Ever thought about why injection molding is such a popular process for producing items like toys and medical devices? This method produces a wide array of products. Many items benefit from this very efficient manufacturing technique.
Injection molding is perfect for producing many items such as consumer electronics, car parts, medical devices, toys, packages and home appliances. The process really shines at forming complex shapes with high accuracy. It is the top choice for these very different industries.
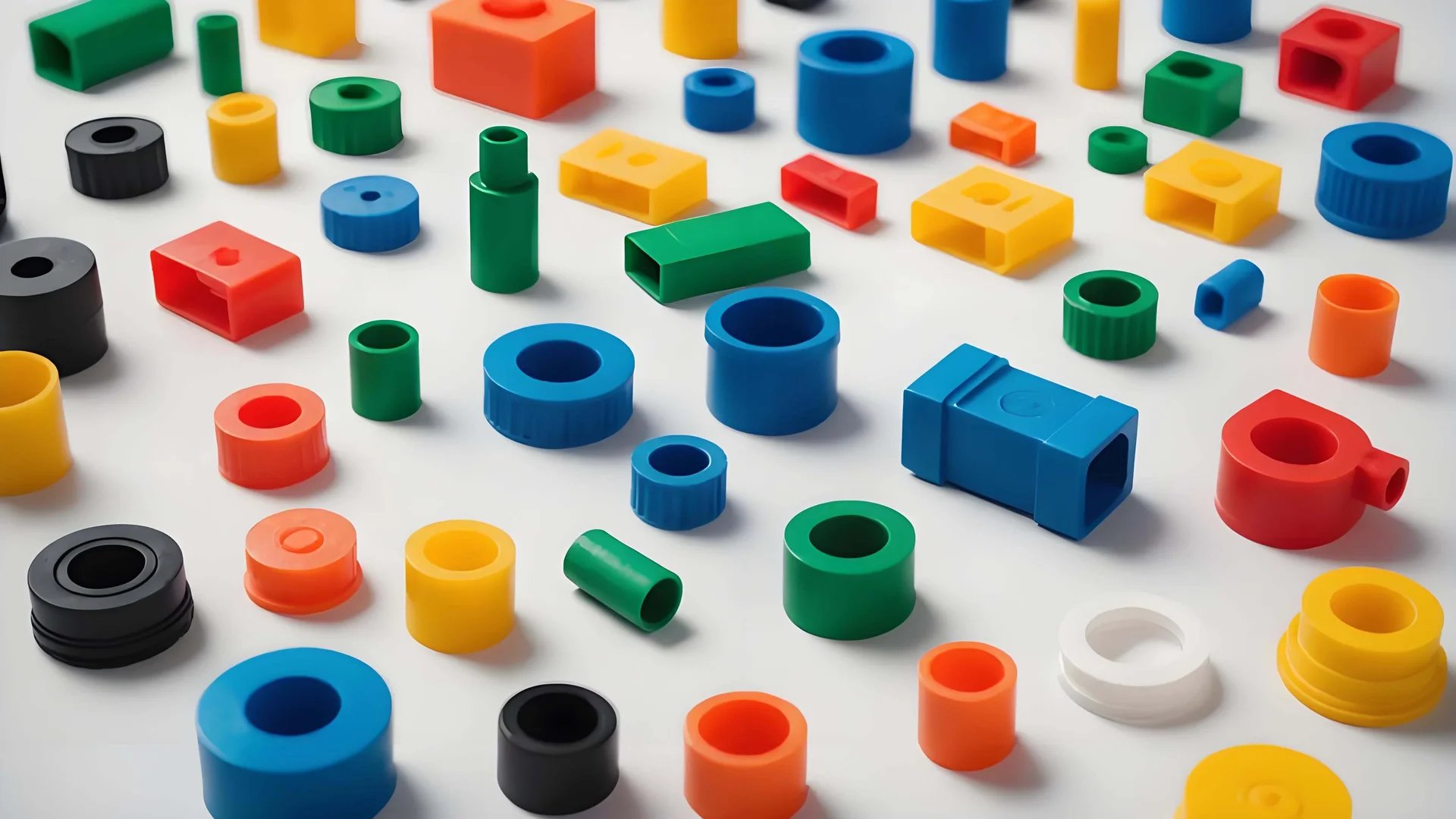
Consumer Electronics Components
Injection molding is exciting in consumer electronics. I once worked on new gadget casings. Creating intricate designs for high production was challenging. But injection molding helped us produce components like buttons and connectors that fit perfectly. The ability to use various plastics, like polycarbonate4, helped achieve durable and lightweight designs. This is perfect for today’s tech.
Automotive Parts
The automotive industry fascinates with the role of injection molding. I’ve seen how it helps make parts like dashboards and bumpers quickly. High accuracy is very important. Every part must fit correctly to guarantee safety and performance. Various thermoplastics are used, such as ABS and polypropylene5, to achieve desired characteristics.
Medical Devices
The medical field was really eye-opening for me. Injection molding is very important because of the need for precision and following strict rules. I designed parts for syringes and diagnostic devices, focusing on quality. Materials like polypropylene and polycarbonate6 helped meet biocompatibility standards while providing necessary strength.
Toys
Who doesn’t enjoy toys? The toy industry is a fun space for injection molding! I worked on intricate designs with bright colors, like classic LEGO bricks. Safe and strong plastics are used to create joyful and secure toys, protecting children’s well-being.
Packaging
Packaging benefits greatly from injection molding too. I made containers, caps, and closures for large-scale production projects without losing quality. Using PET and HDPE materials makes packaging efficient and friendly to the environment.
Home Appliances
Finally, think about home appliances. Injection molding makes everything from housings to knobs in products like blenders and microwaves. The ability to create complex shapes really expands design possibilities!
Summary Table of Applications
Industry | Common Products | Typical Plastics Used |
---|---|---|
Consumer Electronics | Casings, buttons, connectors | Polycarbonate |
Automotive | Dashboards, bumpers | ABS, polypropylene |
Medical Devices | Syringes, diagnostic devices | Polypropylene, polycarbonate |
Toys | LEGO bricks | ABS |
Packaging | Containers, caps | PET, HDPE |
Home Appliances | Housings, knobs | ABS |
Injection molding is ideal for consumer electronics components.True
Injection molding efficiently produces intricate and durable components for consumer electronics, ensuring high production volumes and lightweight designs.
Medical devices are not suitable for injection molding.False
Injection molding is highly suitable for medical devices, providing precision and compliance with strict regulations for safety and quality.
What are the potential limitations of injection molding?
Injection molding is often praised for its efficiency. However, I have learned during my journey in product design that it has limitations. Recognizing these challenges really matters. These challenges allow us to choose wisely in our projects. Smart choices are essential.
Injection molding has some possible drawbacks. Initial costs for mold production are high. Creating molds takes a long time. Not all materials work. Design limits affect shape freedom. Environmental impact is important for sustainability.
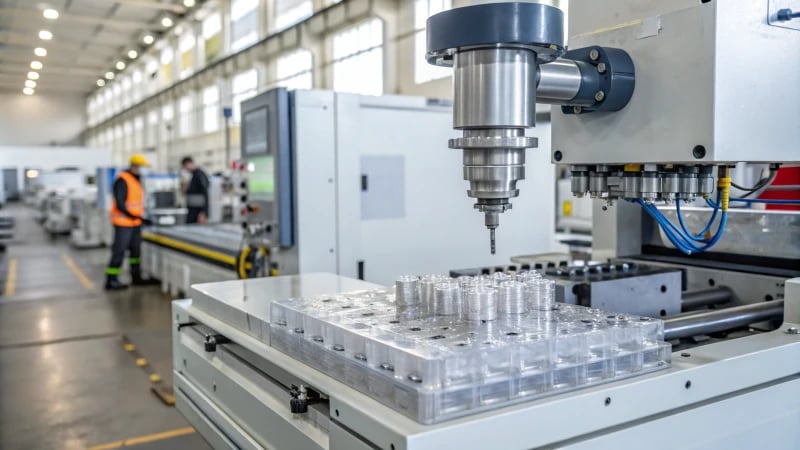
High Initial Costs
Among the first challenges was the high initial cost of custom molds. I recall needing a mold for a new gadget and the quote was thousands of dollars. That steep price made me reconsider our plans. For small batches or startups with tight funds, injection molding can seem like a luxury, not an option.
Additionally, the complexity of the mold design can escalate costs even further, especially if intricate features are needed. It’s essential to assess your project’s scale and budget when considering this production method.
Long Lead Times
Another problem was the long lead time for making molds. I had a project needing quick prototypes and waiting weeks felt endless. This timeline may not align with projects requiring quick turnaround times, such as prototype development or urgent production needs.
When deadlines loom, remember this delay; it could spell the difference between success and failure.
Material Limitations
Injection molding offers many material choices but also has material limitations. Not every plastic suits the process, especially tough ones that don’t flow well under pressure. At times, I’ve wanted to use a particular material, only to discover our mold design couldn’t handle it. This forced us to pick new materials which often meant creating new molds, increasing both time and costs.
Moreover, once a mold is designed for a specific material, changing materials can sometimes necessitate a complete redesign of the mold.
Design Constraints
There are also design constraints that bring frustration. Though great for complex shapes, parts need designs that allow easy mold removal. This rule limits design freedom and can stifle creativity. One design had an ideal undercut but made the mold complex; designers must also consider wall thickness uniformity to avoid issues like warping or incomplete filling during the injection process.
Environmental Considerations
The environmental impact of injection molding can’t be overlooked. Energy use during production is significant, especially in heating and cooling phases. As someone invested in sustainability, I’ve had to explore alternatives or adapt projects to reduce our environmental impact.
Sustainability is becoming increasingly important in manufacturing practices; it’s vital for designers and companies to explore environmentally friendly alternatives or practices within injection molding processes.
Limitation | Description |
---|---|
High Initial Costs | Significant upfront investment in mold design and production. |
Long Lead Times | Extended timeframes required for custom mold creation can hinder project timelines. |
Material Limitations | Not all plastics are suitable; changing materials can require a complete mold redesign. |
Design Constraints | Parts must allow easy ejection from molds; undercuts can complicate designs. |
Environmental Impact | High energy consumption; concerns over plastic recyclability and sustainability issues. |
Injection molding has high initial costs for mold production.True
The production of custom molds in injection molding requires significant upfront investment, making it less feasible for small projects.
All plastics are suitable for injection molding processes.False
Not all plastics can be used in injection molding; some require special considerations due to viscosity and flow characteristics.
How can you optimize your designs for injection molding?
Are you ready to improve your injection molding designs? Let’s explore strategies that change your design process. These methods raise the quality of your products!
Optimize designs for injection molding by choosing suitable materials. Apply design principles for manufacturability. Focus on improving mold designs. Implement automation where needed. Test and iterate regularly. Regular tests improve the design.
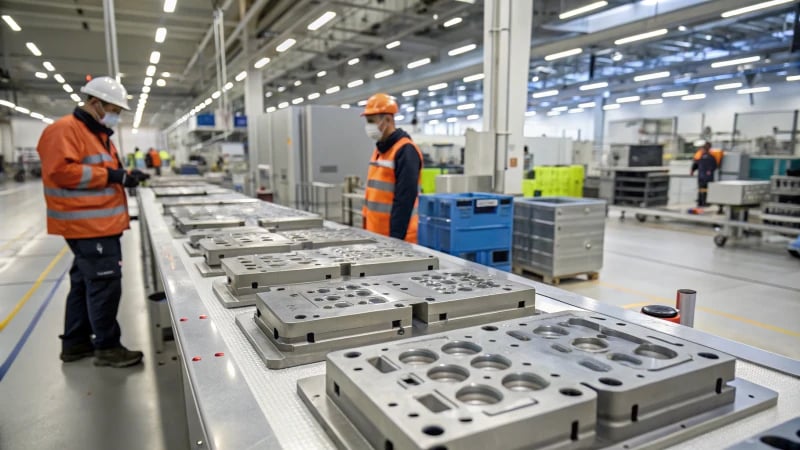
Understand Material Properties
To optimize your designs for injection molding, start by selecting the right material based on the product requirements. Different plastics have unique properties that can impact the molding process and final product quality. For instance, thermoplastics like polypropylene (PP)7 are excellent for their flexibility, while polycarbonate (PC)8 offers high impact resistance.
Material Type | Key Properties | Ideal Use Case |
---|---|---|
Polypropylene | Flexibility, chemical resistance | Packaging, automotive parts |
Polycarbonate | High impact resistance | Safety glasses, electronic housings |
Design for Manufacturability (DFM)
Utilizing DFM principles ensures that your designs are easy to manufacture without unnecessary complexity. Here are some guidelines:
- Avoid sharp corners: Use radii instead of sharp edges to prevent stress concentration.
- Consider draft angles: Design parts with appropriate draft angles (usually 1-3 degrees) to facilitate mold release.
- Uniform wall thickness: Maintain consistent wall thickness to avoid warping and uneven cooling.
Optimize Mold Design
The design of the mold itself can significantly influence the quality and efficiency of the injection molding process. Consider these aspects:
- Gate design: Choose a suitable gate type (e.g., edge gate, pin gate) to improve flow and minimize defects like flash9.
- Cooling channels: Integrate efficient cooling channels to shorten cycle times by maintaining optimal temperature control during the process.
Implement Automation
Automation can streamline the injection molding process, reducing labor costs and increasing production rates. Consider implementing:
- Robotic arms: For automatic loading and unloading of parts to minimize manual handling.
- Automated quality control: Use sensors and cameras to ensure products meet quality standards consistently.
Test and Iterate
Regular testing and iteration of your designs are crucial for optimizing them for injection molding. Conduct:
- Prototyping: Use 3D printing or rapid prototyping to validate designs before committing to mold production.
- Simulation software: Utilize simulation tools to predict how your designs will behave during the injection molding process, allowing you to make adjustments before manufacturing.
By integrating these strategies into your design workflow, you can effectively optimize your designs for injection molding, enhancing both efficiency and product quality.
Thermoplastics like polypropylene are flexible materials.True
Polypropylene is known for its flexibility and chemical resistance, making it suitable for various applications like packaging and automotive parts.
Implementing automation reduces labor costs in injection molding.True
Automation, such as robotic arms and automated quality control, streamlines processes and minimizes manual handling, leading to reduced labor expenses.
Conclusion
Injection molding provides high efficiency, superior quality, design flexibility, and cost-effectiveness, making it an optimal choice for producing complex plastic parts across various industries.
-
Explore this link to discover detailed insights into how injection molding stands against other methods like CNC machining and compression molding. ↩
-
This link provides an overview of different manufacturing processes, helping you understand the broader context of injection molding’s role in the industry. ↩
-
Learn about the cost implications of various manufacturing techniques, including how injection molding can save money in large-scale production. ↩
-
Explore various product types suited for injection molding to enhance your design process and material selection. ↩
-
Learn about industries that benefit from injection molding to identify potential applications for your designs. ↩
-
Discover the advantages of using injection molding for manufacturing specific items and optimizing production methods. ↩
-
This link provides a comprehensive guide on material selection which is vital for optimizing injection molded designs. ↩
-
Find out how automation can benefit your injection molding processes and improve overall efficiency. ↩
-
Learn about design principles that enhance manufacturability in injection molding, ensuring cost-effective production. ↩