Ever find yourself knee-deep in the intricacies of plastic manufacturing, wondering which mold design is your best bet?
Hot runner mold design improves efficiency by reducing cycle times, enhancing product quality, and minimizing waste, offering advantages over traditional cold runner systems.
I remember the first time I faced the decision between hot and cold runner systems. It felt like standing at a crossroads with a map in a foreign language. But as I dug deeper, I realized that hot runner molds offer not just practical benefits but also long-term gains in production efficiency and quality. The way they streamline processes and reduce material waste is akin to finding that perfect shortcut on your daily commute—a game changer. Let’s delve into how these advantages play out in real-world scenarios.
Hot runner molds reduce cycle time in manufacturing.True
Hot runner systems maintain plastic at optimal temperatures, speeding up cycles.
Hot runner molds increase production waste compared to cold runners.False
Hot runners minimize waste by eliminating the need for sprue and runners.
- 1. How Does Hot Runner Mold Design Improve Product Quality?
- 2. How Do Hot Runner Molds Boost Production Efficiency?
- 3. Can Hot Runner Molds Help Save Raw Materials?
- 4. What Are the Key Points in Designing Hot Runner Molds?
- 5. How Does Temperature Control Impact Hot Runner Mold Performance?
- 6. What Are the Potential Challenges of Using Hot Runner Molds?
- 7. Conclusion
How Does Hot Runner Mold Design Improve Product Quality?
Have you ever wondered why some plastic products just seem flawless?
Hot runner mold design enhances product quality by ensuring consistent melt flow and temperature control, reducing shrinkage and warping defects, and maintaining uniformity in multi-cavity molds.
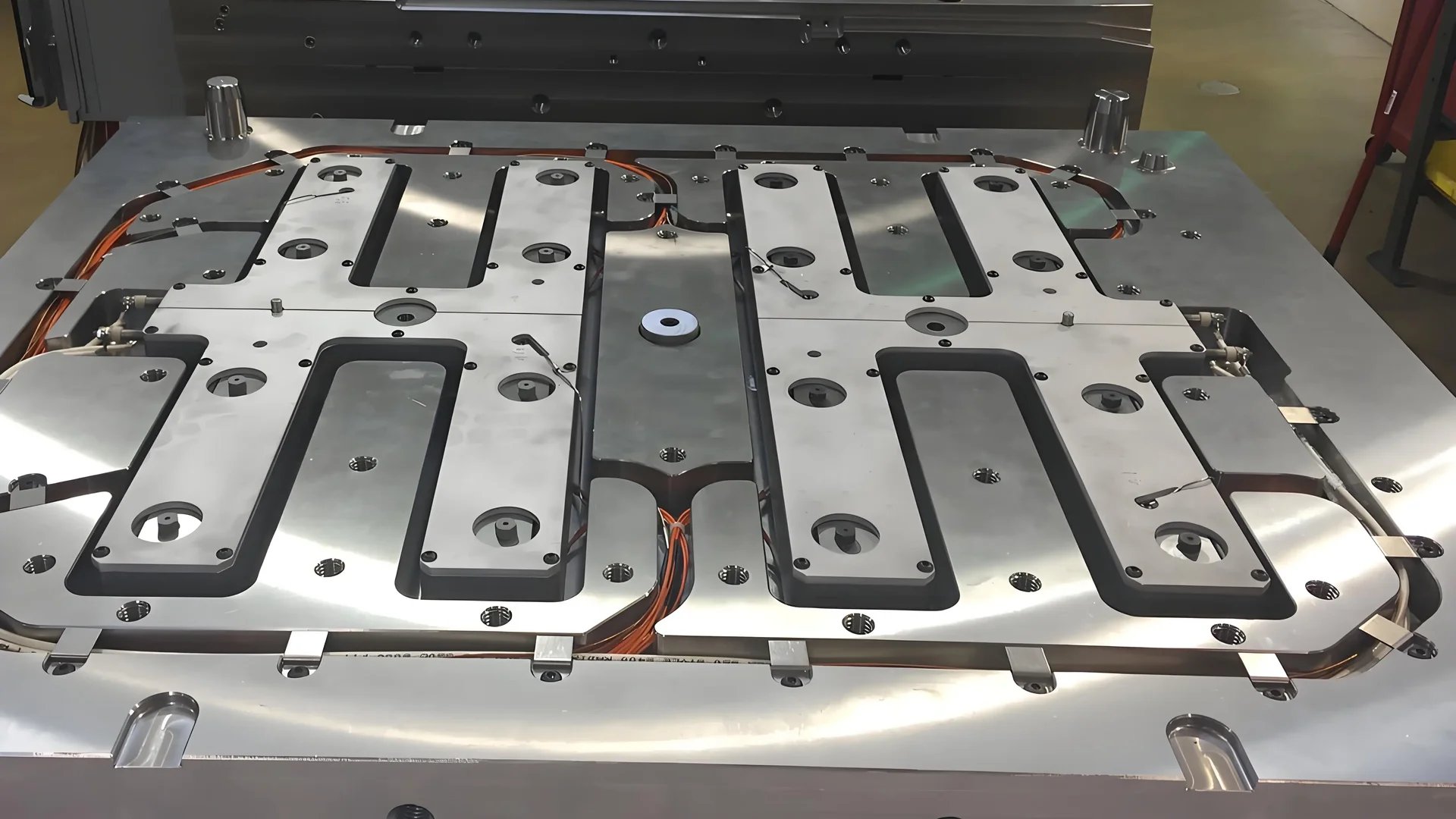
I remember the first time I saw the difference hot runner molds made in product quality. I was working on a project with complex plastic parts, and the defects we were getting were just endless—shrinkage, warping, you name it. Switching to hot runner molds was like flipping a switch; suddenly, the consistency was there.
Key Components of Hot Runner Mold Design
Let’s dive into the essentials of hot runner mold design1, which focuses on selecting the right hot runner system tailored to plastic material characteristics and product size. For instance:
- Heat-sensitive plastics: Demand precise temperature control to avoid any breakdown.
- High-viscosity plastics: Require larger flow channels to ensure smooth cavity filling.
This strategic selection process ensures optimal flow conditions for varying product requirements.
Layout and Temperature Control
Balanced Layout: Achieving equal melt distribution across multiple cavities is crucial for product consistency. I once worked on a multi-cavity mold where balancing the layout meant the difference between success and redoing the entire batch. It often involves meticulous parameter calculations using CAD software.
Aspect | Description |
---|---|
Balanced Layout | Equal melt distribution in multi-cavity molds. |
Unbalanced Layout | Adjustments for specific shapes or restrictions. |
Temperature Control: Heating elements like rods and coils are strategically placed to keep the temperature uniform across the mold. It’s like baking a cake; if one side is hotter than the other, you end up with a mess. Here, temperature sensors are critical in keeping things stable.
Coordination and Sealing Design
The interaction between the hot runner and mold2 is key to maintaining integrity. Effective sealing prevents leakages that could compromise product quality, while a well-coordinated cooling system helps manage heat distribution effectively.
- Sealing Methods: High-temperature-resistant rubber or metal seals prevent melt leakage.
- Cooling System: Coordinates with the hot runner to manage heat effectively without affecting the melt flow.
Understanding these aspects of hot runner design can significantly impact the quality of injection-molded products. The implications for industries like consumer electronics and automotive manufacturing are profound, offering tangible benefits in both cost savings and product quality improvement.
Embracing a comprehensive approach to mold design3 not only enhances product quality but also aligns with sustainable manufacturing practices by reducing material waste and energy consumption. Through continued innovation in hot runner technologies, there’s always potential to elevate manufacturing standards further.
Hot runner molds reduce material wastage.True
By ensuring precise melt flow and temperature control, material wastage is minimized.
Unbalanced layouts ensure equal melt distribution.False
Balanced layouts, not unbalanced, ensure equal melt distribution across cavities.
How Do Hot Runner Molds Boost Production Efficiency?
Imagine cutting your production time in half while saving on material costs—that’s the magic of hot runner molds in injection molding.
Hot runner molds enhance production efficiency by reducing cycle times, minimizing waste, and ensuring consistent product quality, bypassing the solidification step for faster, efficient molding compared to cold runners.
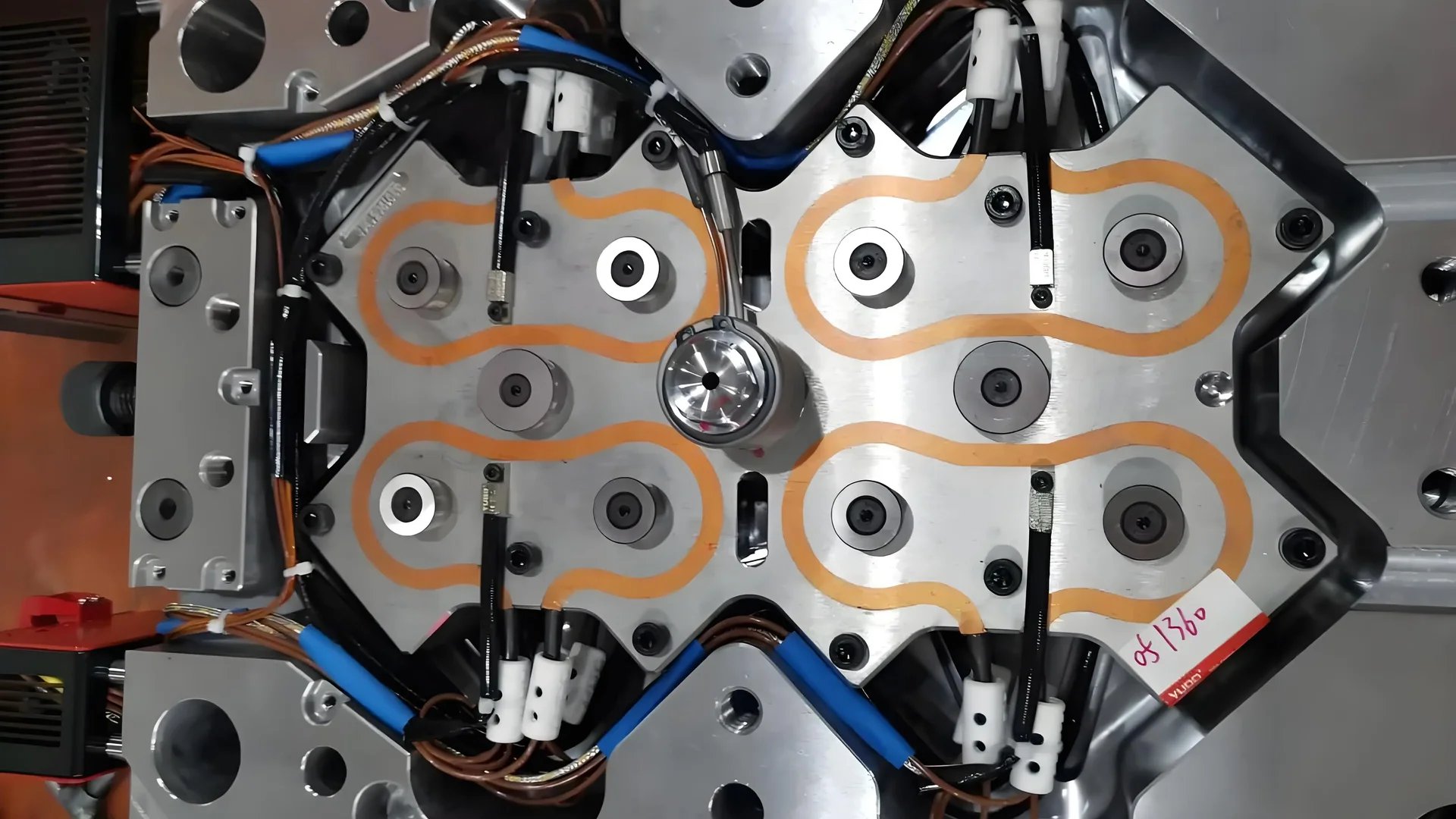
Shortened Molding Cycle
Picture this: I’ve just finished a project where switching to hot runner molds felt like upgrading from dial-up to high-speed internet. The immediate benefit? Drastically reduced cycle times. In my case, I saw the cycle time for small plastic items drop from 20-30 seconds to a swift 10-15 seconds. This immediate demolding, compared to waiting for solidification with cold runners, truly transformed our production line’s efficiency.
Waste Reduction and Material Savings
I remember the days of cleaning up after cold runner processes and feeling guilty about the mountains of plastic waste. Hot runner molds were a game-changer, keeping the plastic molten and eliminating excess waste. This shift saved us 20-30% in raw materials, especially vital when working with costly engineering plastics. The material cost savings4 were not just a bonus—they were crucial to staying competitive.
Improved Product Quality and Consistency
The first time I used hot runner molds, I was blown away by the uniformity in product quality. Each batch came out with consistent wall thickness and no defects like short shots or shrinkage marks. For mass production, this level of consistency is priceless, especially when manufacturing precision parts like those found in consumer electronics.
Facilitation of Automated Production
Automation was always a goal I aimed for in our production processes. With hot runner molds, integrating automation became seamless. The molds worked harmoniously with robotic systems for part picking and insert placement, reducing manual labor and boosting overall production efficiency. This integration made it easier to meet tight deadlines without compromising on quality.
Advantages | Cold Runner Molds | Hot Runner Molds |
---|---|---|
Cycle Time | Longer | Shorter |
Waste Generation | High | Low |
Product Consistency | Variable | High |
Automation Compatibility | Moderate | High |
Incorporating hot runner molds has been a pivotal move in my manufacturing journey, enhancing efficiency across industries such as automotive and electronics. These systems are not just improving processes—they’re revolutionizing them. Explore more5 about how hot runner systems are setting new standards in manufacturing efficiencies worldwide.
Hot runner molds reduce cycle time by half.True
Hot runner molds decrease cycle times from 20-30 seconds to 10-15 seconds.
Hot runner molds increase waste generation.False
They minimize waste by keeping plastic molten, unlike cold runners.
Can Hot Runner Molds Help Save Raw Materials?
Imagine saving heaps of raw materials in your production line—sounds like a dream, right? Hot runner molds might just make it a reality by cutting down waste and boosting efficiency.
Hot runner molds reduce raw material waste in injection molding by eliminating runner waste, decreasing costs, and improving sustainability.

I remember standing on the factory floor, watching as a mountain of plastic waste piled up from our cold runner molds. It was disheartening, not just because of the cost, but also because of the environmental impact. That’s when I stumbled upon hot runner systems, and they transformed everything.
Understanding Hot Runner Systems
Hot runner molds work like magic for optimizing material use. They keep the plastic melt fluid within the runners, so we don’t have to throw away solidified plastic with each cycle. Unlike cold runners, which left us with heaps of unusable waste, hot runners maintain the material’s usability throughout the process.
The Design Impact
The design of a hot runner system6 is crucial. I learned the hard way that selecting the right system involves understanding plastic properties. For example, with heat-sensitive plastics like PVC, temperature control is vital to avoid degradation. High-viscosity plastics need wider channels to ensure smooth filling without increasing material waste.
Plastic Type | Considerations |
---|---|
Heat-sensitive (e.g., PVC) | Precise temperature control to avoid decomposition |
High-viscosity (e.g., PC) | Larger channels for reduced flow resistance |
Layout and Efficiency
The layout of a hot runner system can make or break efficiency. A balanced layout helps evenly fill multiple cavities, reducing inconsistencies and waste. I’ve used simulation tools to optimize layouts, ensuring each cavity gets just the right amount of plastic melt.
For more complex shapes, sometimes an unbalanced layout7 is necessary, but tweaking channel sizes or timing can keep efficiency high.
Temperature Control
Temperature control is another area where precision matters. By installing heating elements properly and placing temperature sensors strategically, I’ve avoided defects from overheating or cooling that lead to waste.
Advantages Over Cold Runners
Hot runner molds have been game-changers for me compared to cold runners. They keep all material usable, drastically cutting material costs over time—especially important when using pricey engineering plastics.
Moreover, they enhance product quality by ensuring even filling and reducing defects like short shots and shrinkage marks that often result in wasted material.
Learn more about hot runner mold advantages8 and how they can enhance production efficiency and sustainability.
Hot runner molds eliminate runner waste.True
Hot runner systems keep plastic melt liquid, reducing solid waste.
Cold runners are more efficient than hot runners.False
Cold runners produce solid waste, unlike hot runners, which are more efficient.
What Are the Key Points in Designing Hot Runner Molds?
Ever wondered how designing hot runner molds can feel like a puzzle, piecing together efficiency and precision?
Key points in designing hot runner molds include selecting the appropriate system for the plastic type, ensuring even layout, precise temperature control, and seamless coordination with the mold to improve product quality and production efficiency.
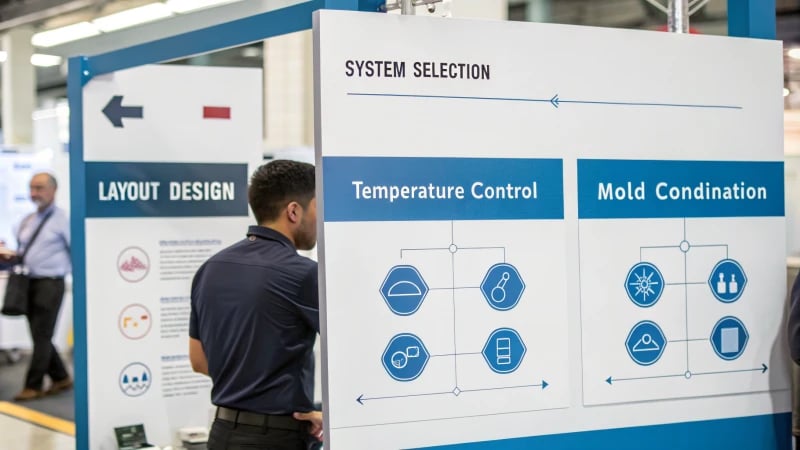
When I first got into designing hot runner molds, it felt like assembling a complex puzzle. Each piece—system selection, layout, temperature control, and mold coordination—had to fit perfectly to ensure a smooth operation. Let me take you through what I’ve learned over the years.
Selection of Hot Runner System
Deciding on the right hot runner system starts with knowing your plastic inside out. I once worked on a project with PVC, a heat-sensitive material that needed a system with flawless temperature control. It was all about balancing the right amount of heat to prevent decomposition and avoid that nasty hydrogen chloride gas. Trust me, getting this right made all the difference in product quality.
Material Type | System Requirement |
---|---|
Heat-sensitive | Uniform heating, precise control |
High-viscosity | Larger flow channel diameter |
For more details on characteristics of plastic materials9, understanding these properties is crucial for selecting the appropriate system.
Hot Runner Layout
A balanced layout is crucial for uniform filling across cavities. Imagine designing a mold for bottle caps; each cavity needs to get its fair share of the plastic melt simultaneously. I remember using CAD software to tweak layouts, ensuring every twist and turn was just right.
- Unbalanced layouts may be necessary for complex structures10 or shape restrictions. Adjustments in flow size or timing can really help manage pressure differences.
Temperature Control
Temperature control is where the magic happens. Selecting and placing heating elements like rods or coils should be done with an eye for power and efficiency. In one project, using thermocouples kept everything on track—monitoring and adjusting temperatures in real time was a game-changer.
Element Type | Use Case |
---|---|
Heating Rods | Overall system heating |
Heating Coils | Localized heating (e.g., nozzles) |
Thermocouples | Fast response temperature changes |
Coordination Between Hot Runner and Mold
Getting the hot runner system to play nice with the mold is key. I remember a time when poor sealing led to leaks—talk about a learning experience! Using high-temperature seals like copper helped prevent that kind of mishap in future projects.
The cooling system should complement the hot runner11 by providing localized cooling where needed without disrupting the temperature field. This helps maintain consistent product quality and prevents defects such as shrinkage marks or short shots.
By paying attention to these details, designing hot runner molds becomes more than just a technical task—it’s an art of balancing precision and practicality.
PVC requires uniform heating in hot runner systems.True
Heat-sensitive plastics like PVC need uniform heating to prevent degradation.
All hot runner molds use unbalanced layouts.False
Balanced layouts are preferred for even filling, except in complex designs.
How Does Temperature Control Impact Hot Runner Mold Performance?
Ever wondered how the temperature in a hot runner mold can make or break your molding process?
Temperature control in hot runner molds ensures consistent melt flow, efficient mold filling, and minimizes defects, leading to high-quality products and reduced energy waste.
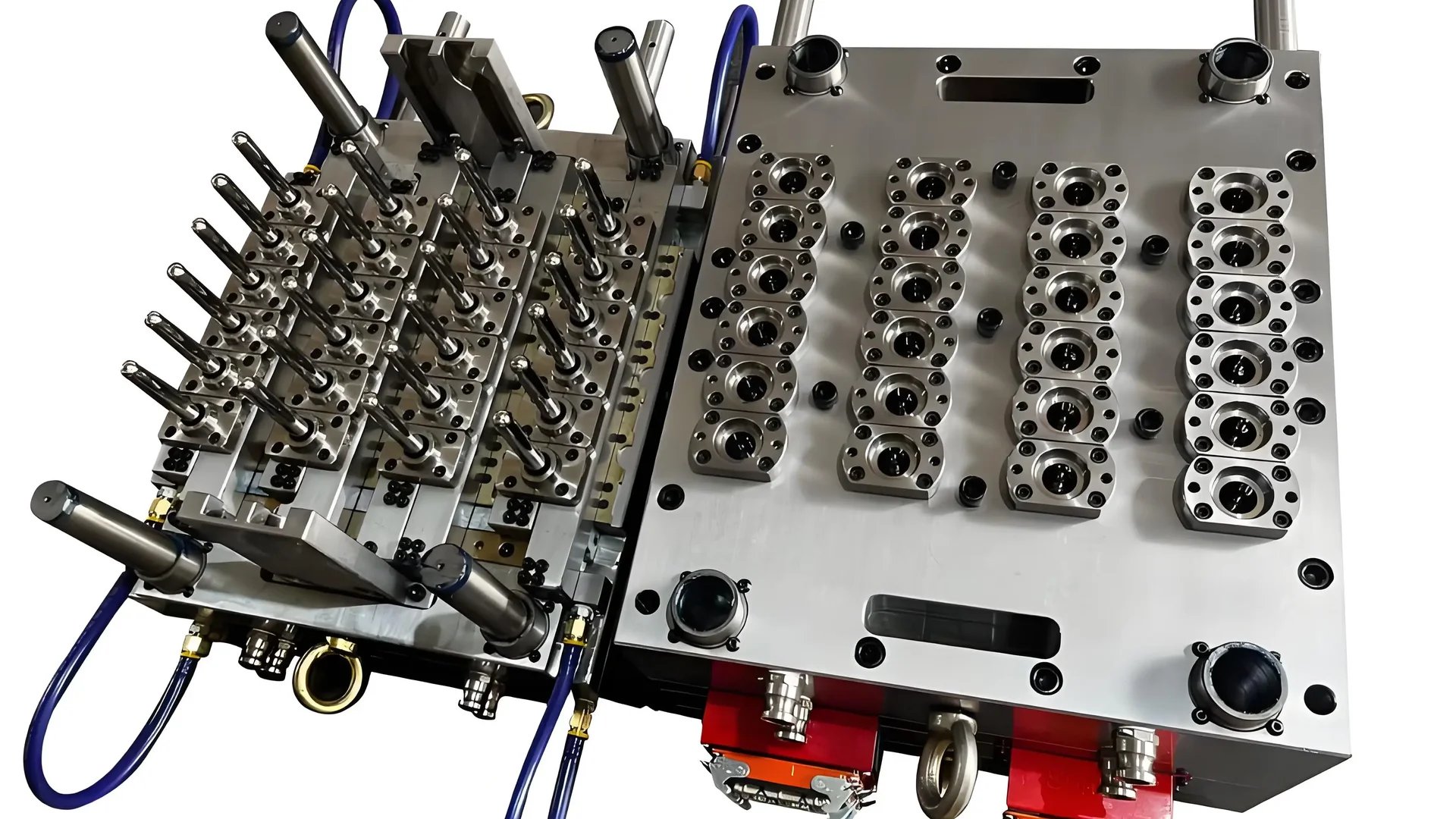
The Emotional Rollercoaster of Temperature Control
I remember the first time I realized just how critical temperature control was in mold design. It was like discovering that the missing puzzle piece I had been searching for was right under my nose all along. I was working on a project with heat-sensitive plastics, and the slightest deviation in temperature would result in disastrous defects. That’s when it hit me – maintaining a consistent temperature wasn’t just a technical necessity; it was the heartbeat of the entire molding process.
Importance of Temperature Control in Hot Runner Molds
Getting the temperature just right in a hot runner system is like cooking the perfect steak—too hot, and you’ll burn it; too cold, and it won’t cook through properly. Inconsistencies can lead to issues like short shots or flash. For example, working with PVC requires pinpoint accuracy in temperature management to prevent decomposition and ensure quality. Choosing a hot runner system12 with even heating is key.
Key Considerations for Temperature Management
Selection of Heating Elements
The choice of heating elements can feel like choosing the right pair of shoes for a marathon—you need something that’s reliable and fits perfectly. In our hot runner system, heating rods inside manifolds provide uniform heat, while coils focus on specific areas like nozzles.
Heating Element | Installation | Purpose |
---|---|---|
Heating Rods | Inside Manifold | Uniform Heat |
Heating Coils | At Nozzles | Local Heat |
Temperature Sensors and Their Placement
Temperature sensors are akin to having a trusty GPS when you’re exploring new terrain. They offer real-time guidance by monitoring crucial areas such as manifolds and nozzles, allowing for precise adjustments.
- Thermocouples: Perfect for fast response needs.
- Thermal Resistors: Great for high precision situations.
Effects on Product Quality and Consistency
It’s incredible how something as simple as temperature control can transform product consistency. It’s like having a magic wand that reduces defects such as shrinkage marks and enhances dimensional accuracy. When crafting products with intricate designs or thin walls, a balanced hot runner layout13 is your best friend.
Mastering temperature management not only optimizes production but also cuts down on waste, leading to impressive cost savings over time. It’s these little victories that make the world of mold design so rewarding.
Temperature fluctuations cause mold defects.True
Inconsistent temperatures can lead to defects like short shots or flash.
Heating coils are placed inside manifolds.False
Heating rods, not coils, are typically placed inside manifolds for uniform heat.
What Are the Potential Challenges of Using Hot Runner Molds?
When I first ventured into using hot runner molds, I was both excited and slightly apprehensive. These molds promise incredible efficiency but come with their own set of hurdles.
Hot runner molds face challenges like complex designs, high initial costs, maintenance needs, and temperature control issues. Effective management requires meticulous planning and regular maintenance.
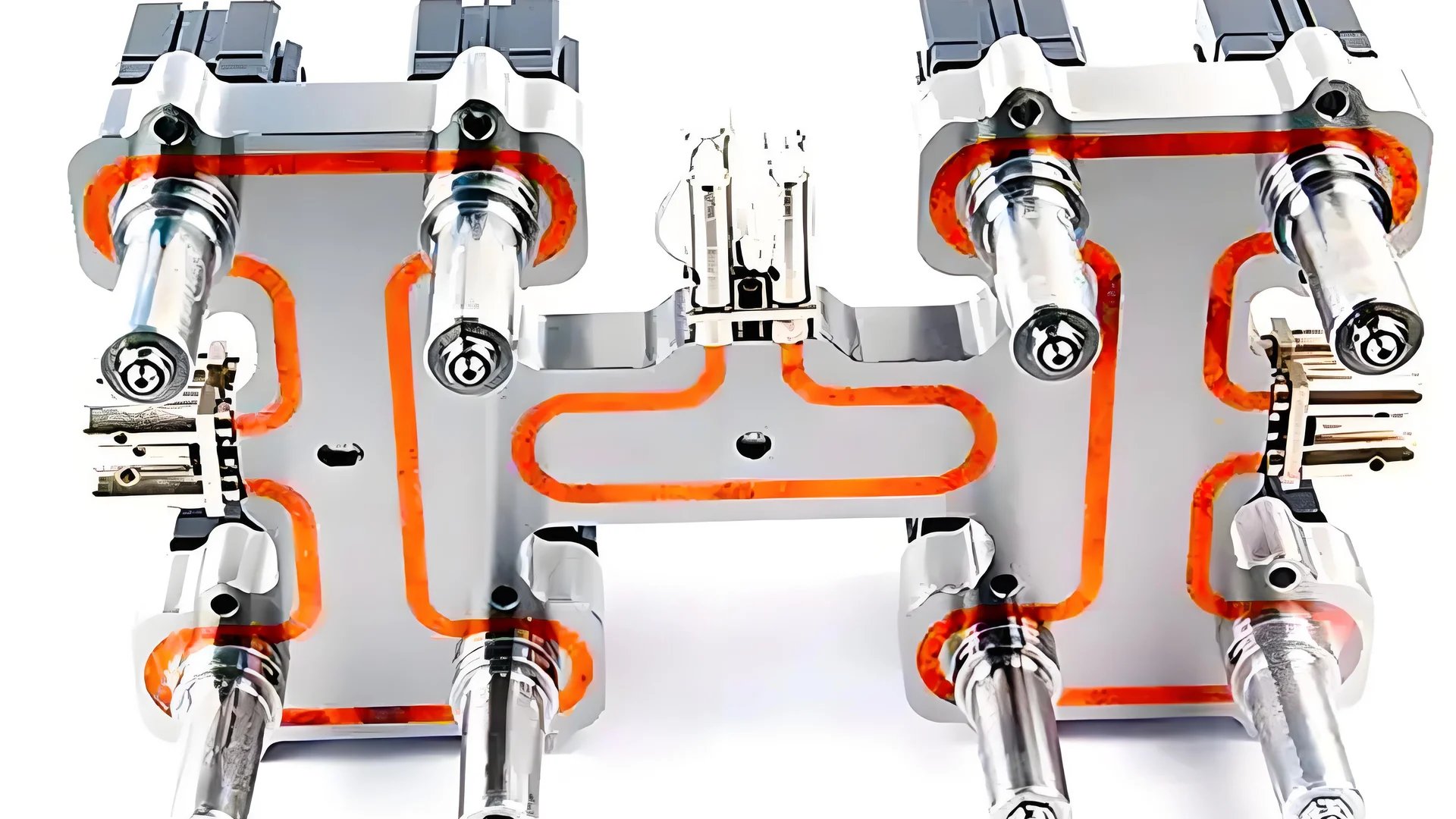
Complex System Design
I remember my first encounter with a hot runner mold system. It was like stepping into a new world of intricate designs, with nozzles and manifolds that demanded precise alignment. I quickly realized that any misalignment could lead to leaks or uneven fills—problems I definitely wanted to avoid. That’s when I turned to CAD software14 to simulate flow and temperature distribution, which became an invaluable tool in achieving a balanced layout for multi-cavity molds.
High Initial Investment
I won’t sugarcoat it—investing in hot runner systems is a significant financial commitment. The initial costs for components like heating elements and sensors can be daunting. However, I’ve found that the long-term benefits, like reducing material waste and improving efficiency, often outweigh the initial investment. Evaluating the cost-effectiveness15 through detailed financial analysis was key for me in making informed decisions.
Component | Description | Cost Implications |
---|---|---|
Nozzles | Distribute melt | High precision needed |
Manifold | Channels melt | Custom design costs |
Sensors | Monitor temp | Essential for control |
Maintenance Requirements
Maintenance is one area where I’ve learned to be proactive rather than reactive. Regularly checking components like heaters and sensors has become part of my routine to prevent wear and tear. Cleaning is crucial to prevent buildup, ensuring everything runs smoothly. I’ve even trained my team on proper maintenance procedures, scheduling inspections regularly to minimize downtime. Using predictive maintenance tools16 has further enhanced reliability by catching issues early on.
Temperature Control Challenges
Temperature control in hot runner systems is something I handle with utmost care because it directly affects product quality. Variations in temperature can cause warping or incomplete fills—defects that are frustrating to manage. By strategically placing temperature sensors17 throughout the mold, I’ve been able to maintain consistent temperatures, although it requires skilled operators who understand these sophisticated systems. A comprehensive training program18 for my team has been invaluable in ensuring effective operation.
Hot runner molds require complex system designs.True
Hot runner molds involve intricate designs with components like nozzles and manifolds.
Temperature control is not crucial in hot runner molds.False
Temperature control is vital to avoid defects such as warping or incomplete fills.
Conclusion
Hot runner mold design enhances efficiency by reducing cycle times, minimizing waste, and improving product quality through precise temperature control and optimized layouts for various plastic materials.
-
Understanding how to select hot runner systems for various plastics ensures optimal processing and reduces defects. ↩
-
Proper sealing prevents leaks, ensuring high product quality and protecting molds from damage. ↩
-
Explores how strategic mold design decisions directly enhance the quality of molded products. ↩
-
Discover how hot runner molds reduce raw material waste and lower overall production costs in injection molding. ↩
-
Explore the global impact of hot runner systems on improving manufacturing processes across industries. ↩
-
Discover detailed comparisons between hot and cold runner systems to understand efficiency gains. ↩
-
Explore scenarios where unbalanced layouts are beneficial and how they are implemented. ↩
-
Find out how hot runner molds increase consistency and reduce waste in manufacturing. ↩
-
Understanding material properties is crucial for selecting the appropriate hot runner system. ↩
-
Explore design strategies for complex mold structures using unbalanced layouts. ↩
-
Learn about efficient cooling system designs that complement hot runner functionality. ↩
-
Learn about selecting hot runner systems that maintain uniform temperature to enhance mold performance. ↩
-
Discover how balanced layouts in hot runner systems improve product consistency and reduce defects. ↩
-
Explore how CAD software enhances mold design with precision simulations. ↩
-
Discover methods to assess the financial benefits of investing in hot runner systems. ↩
-
Understand how predictive maintenance tools can improve mold reliability and reduce downtime. ↩
-
Investigate how temperature sensors ensure quality in injection molding processes. ↩
-
Find out about training programs that help operators manage sophisticated molding equipment. ↩