Ever wondered how to turn ordinary plastic into a masterpiece? Advanced in-mold decoration is the secret sauce.
To apply advanced in-mold decoration in injection molding, follow these steps: prepare the design, print the film, position the film, conduct molding, and perform post-processing. This technique enhances aesthetics and provides wear protection.
It’s fascinating how these steps, though seemingly straightforward, are like pieces of a puzzle that fit perfectly together to create something truly spectacular. I remember when I first tried my hand at in-mold decoration—I was a bundle of nerves, unsure if my designs would survive the molding process. But with each stage, from carefully positioning the film to the satisfying click of the final product, I learned that attention to detail and a bit of patience can transform a design from good to jaw-dropping.
As you dive into this process, you’ll find that preparation is everything. Each phase offers its own set of challenges and opportunities. Whether it’s selecting the right materials or ensuring precise alignment during film positioning, these details can make or break your project. So let’s explore the nuances together and discover how to troubleshoot common issues that may arise along the way.
IMD enhances the aesthetic appeal of plastic components.True
IMD integrates graphics into plastics, improving visual appeal.
Film positioning is not required in the IMD process.False
Film positioning is a crucial step in the IMD process.
How Does In-Mold Decoration Enhance Product Aesthetics?
Remember the time you wished your favorite gadget looked as good as it performed? With in-mold decoration, that’s no longer just a dream. Let’s dive into how this technique transforms products into visual masterpieces.
In-mold decoration enhances aesthetics by integrating vibrant graphics and textures into plastics, ensuring durability and design flexibility, and offering a superior finish over traditional techniques.

The Basics of In-Mold Decoration
Imagine you’re piecing together a puzzle, but instead of cardboard pieces, you’re using vibrant films and molten plastic. That’s essentially what in-mold decoration (IMD) does. It involves placing a pre-printed film into a mold before injecting plastic. As the plastic fills the mold, it bonds with the film, creating a unified part with a decorative surface. I remember my first encounter with IMD at a trade show; it was like watching art come to life through engineering.
Benefits | Description |
---|---|
Seamless Integration | Eliminates the need for post-production decoration, ensuring a smoother finish. |
Durability | Graphics are embedded within the product, making them resistant to wear. |
Design Flexibility | Allows for complex patterns and colors that traditional methods can’t achieve. |
Enhanced Visual Appeal
One of the most thrilling aspects of IMD is how it offers vivid graphics1 and high-quality finishes that elevate the appearance of products. I often find myself comparing IMD to the joy of seeing your favorite painting embedded in something you use every day. Unlike stickers or paint, IMD designs are impervious to scratches and fading.
- Vibrant Colors: The method supports a wide range of hues, enhancing brand identity.
- Complex Patterns: Intricate designs are achievable, meeting diverse aesthetic needs.
Comparison with Traditional Techniques
When I first started in this field, traditional decoration methods like pad printing or hot stamping seemed like the norm. However, they often lack the precision and longevity of IMD. Here’s how they compare:
Feature | In-Mold Decoration | Traditional Methods |
---|---|---|
Durability | Highly durable, scratch-resistant | Susceptible to wear and tear |
Design Complexity | Supports intricate designs | Limited complexity |
Cost Efficiency | Cost-effective for large volumes | More cost-effective for smaller runs |
Application Across Industries
IMD is popular in various sectors such as automotive interiors2 and consumer electronics due to its aesthetic versatility. For instance, car dashboards utilize IMD for elegant finishes without compromising functionality.
Automotive interiors3 benefit from IMD by achieving consistent design elements that align with branding goals. In consumer electronics, IMD allows for sleek surfaces that enhance user interaction, such as in smartphones or remote controls.
By exploring how IMD compares4 with other techniques, designers like Jacky can make informed decisions about adopting this technology in their projects. Understanding the aesthetic advantages of IMD can lead to innovative designs that capture consumer interest.
Overall, IMD is revolutionizing the way products are designed and appreciated in the marketplace. Its ability to integrate visuals directly into the manufacturing process not only enhances aesthetics but also contributes to the overall quality and longevity of the product.
In-mold decoration eliminates post-production decoration.True
IMD integrates graphics during manufacturing, removing the need for extra steps.
Traditional methods offer more design complexity than IMD.False
IMD supports intricate designs, surpassing traditional methods in complexity.
What Materials Are Best for In-Mold Decoration?
Ever wondered how those sleek, shiny surfaces on your favorite gadgets come to life?
For optimal in-mold decoration, use durable, heat-resistant materials like polycarbonate (PC), polybutylene terephthalate (PBT), and acrylonitrile butadiene styrene (ABS) due to their compatibility and resilience.
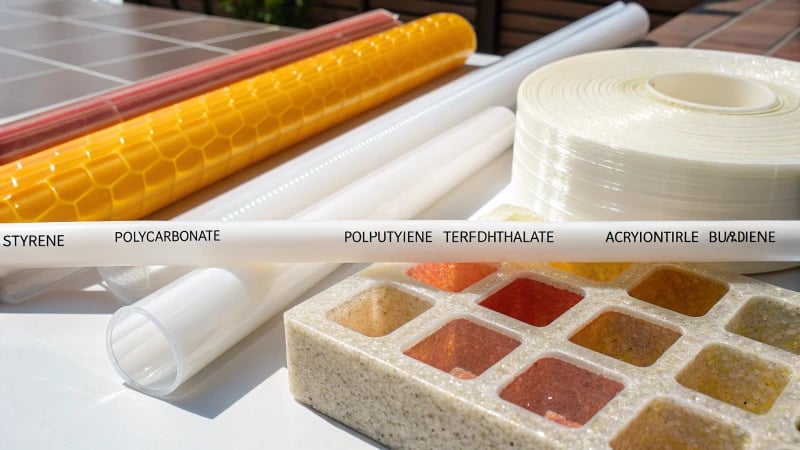
Understanding In-Mold Decoration
In-mold decoration (IMD) isn’t just a process; it’s an art form that bridges the gap between functionality and aesthetics. I remember the first time I saw a perfectly finished plastic part; it was like seeing magic unfold. Designers, like Jacky, know that getting this right means considering both material compatibility and how amazing the final product will look.
Popular Materials for IMD
Polycarbonate (PC)
I’ve always been amazed by polycarbonate’s resilience. It’s like the superman of plastics—tough yet clear as glass, perfect for electronic displays where every detail matters. Its ability to work with various inks5 ensures your graphics look top-notch.
Property | Polycarbonate |
---|---|
Impact Resistance | High |
Heat Resistance | Moderate |
Optical Clarity | Excellent |
Polybutylene Terephthalate (PBT)
PBT brings to mind images of robust automotive components cruising down a highway, all thanks to its chemical resistance and dimensional stability. It’s the go-to for parts that need to last.
Property | PBT |
---|---|
Chemical Resistance | High |
Dimensional Stability | Excellent |
Aesthetic Appeal | Moderate |
Acrylonitrile Butadiene Styrene (ABS)
When I think of ABS, I remember those glossy consumer gadgets that feel good in hand and look stunning on display. It’s ideal when you need something that balances toughness with an eye-catching finish.
Key Considerations
Choosing the right material is like finding the perfect ingredient for your favorite dish—it makes all the difference. You need something that can take the heat (literally) without losing its cool.
- Heat Resistance: The material should withstand molding temperatures like a pro.
- Ink Compatibility: Ensure it pairs well with decorative inks6.
- Cost Efficiency: It’s all about getting the best bang for your buck without compromising on looks or longevity.
For designers like Jacky, diving into these nuances can truly transform a product’s appeal and durability. By weaving these insights into your design tapestry, you can craft masterpieces that shine in automotive interiors or on consumer electronics. Let’s make those surfaces pop!
Polycarbonate has excellent optical clarity for IMD.True
Polycarbonate is known for its high impact resistance and optical clarity, making it ideal for electronic displays.
ABS is not suitable for consumer goods due to low gloss.False
ABS is widely used in consumer goods because of its good balance of toughness and gloss.
How Do You Prepare Designs for In-Mold Decoration?
I remember the first time I heard about in-mold decoration (IMD) – it sounded like magic, blending graphics right into a product! But how do you actually prepare designs for such a complex process?
To prepare designs for in-mold decoration, ensure material compatibility, use precise CAD modeling, achieve accurate graphic alignment, and understand the mold design and IMD process for successful outcomes.
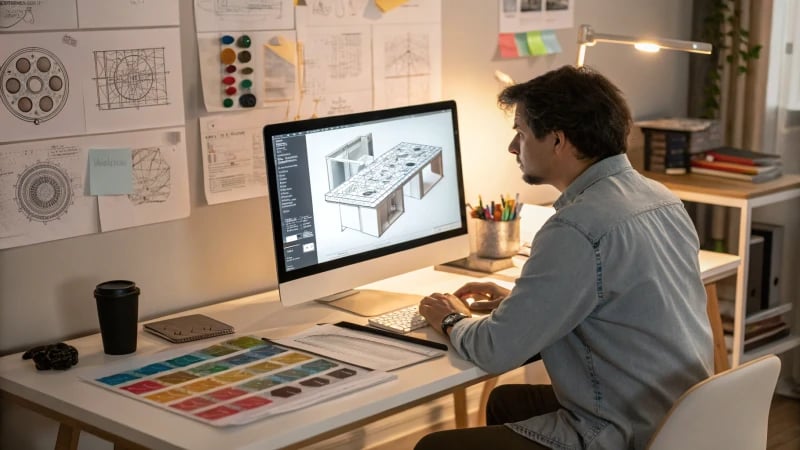
Understanding the In-Mold Decoration Process
Imagine this: you have a beautifully designed graphic, and you want it to be an integral part of your product. That’s where in-mold decoration7 comes in. It starts by placing a pre-printed label or film into a mold before the molding cycle. This way, your graphics aren’t just an afterthought—they’re embedded within the product, offering both durability and stunning looks. For me, getting familiar with materials like polycarbonate films is key to making this happen seamlessly.
Key Design Considerations
- Material Compatibility: One time, I selected a material without considering its bonding properties, and let’s just say it was a costly lesson. Picking the right materials like polycarbonate or polypropylene is crucial because they bond well with substrates.
- CAD Modeling: Precision is everything. I remember tweaking CAD models late into the night to ensure graphics aligned perfectly. A tiny misalignment can lead to big headaches later.
- Graphic Placement: Placing graphics in the mold correctly is like fitting the last piece of a puzzle. It needs to be perfect to avoid distortion.
Consideration | Details |
---|---|
Material Selection | Choose materials that withstand molding conditions |
Graphic Design | Ensure clarity and color accuracy |
Mold Design | Accommodate label thickness and alignment |
Collaborative Efforts with Mold Designers
I can’t stress enough how important it is to collaborate closely with mold designers. I once spent hours discussing alignment features8 with them, which paid off when everything fit perfectly during the first trial. Mock-ups or simulations are incredibly helpful to foresee how designs will look post-molding.
Testing and Prototyping
Testing feels like an insurance policy to me—essential and reassuring. I’ve conducted numerous tests under various conditions like heat and humidity to ensure the durability of decorative elements. Prototyping helps spot potential issues early on, saving lots of time and resources.
Integration with Manufacturing Processes
Lastly, integrating the IMD process within existing workflows is essential. It was fascinating to learn about the thermal dynamics of the injection molding process9 and its interaction with decorative films. By designing with these constraints in mind, smoother operations and better outcomes are achievable.
By focusing on these aspects, I’ve learned to prepare designs that not only look great but also function seamlessly within in-mold decoration processes. This ensures that my projects are both aesthetically pleasing and robust, ready to impress and endure.
Polycarbonate films are used in in-mold decoration.True
Polycarbonate films are commonly used for their compatibility and durability.
Misalignment during molding is not a concern in IMD.False
Misalignment can cause graphics distortion, affecting the final product quality.
What Are Common Challenges in In-Mold Decoration?
Diving into the world of in-mold decoration (IMD) is like navigating a labyrinth of challenges and triumphs.
Common challenges in in-mold decoration involve alignment issues, material compatibility, color consistency, and surface defects, requiring careful planning and teamwork between design and manufacturing.
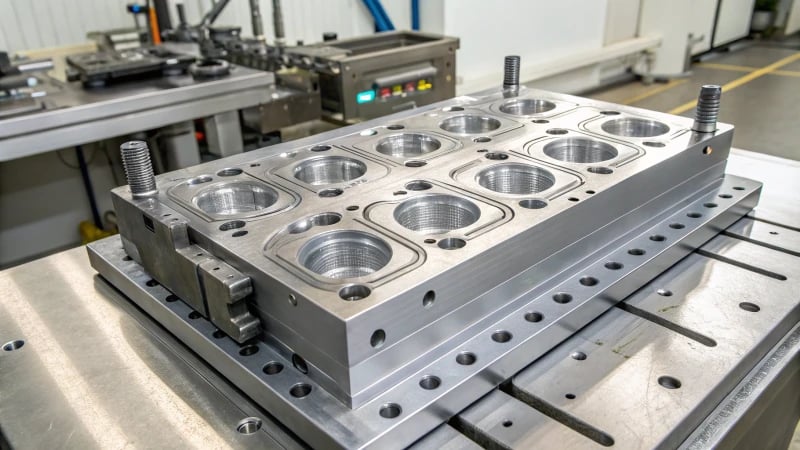
Alignment Issues
I remember the first time I encountered alignment problems. It was a project for a sleek new gadget, and the decorative film just wouldn’t sit right. Misalignment can spell disaster, especially when precision is key. I’ve learned that using high-quality fixtures and setting tight tolerances are lifesavers. It’s all about getting that perfect fit to avoid defects.
Ensuring precise alignment between the mold and the decorative film is crucial. Misalignment can lead to defective products, which is especially problematic in industries demanding high precision, like consumer electronics.
Material Compatibility
Ah, the trials of material compatibility! Picture this: after weeks of work, seeing the decorative film peel off was heartbreaking. I realized how crucial it is to select the right materials to avoid adhesion woes. Luckily, advancements in material science10 are offering more options than ever. The trick is finding that perfect pair to ensure durability.
Material incompatibility between the decorative film and the substrate can lead to adhesion problems. Selecting the right combination of materials is essential to prevent peeling or delamination.
Material | Pros | Cons |
---|---|---|
Polycarbonate | High durability | Can be expensive |
ABS | Cost-effective | Limited temperature resistance |
Color Consistency
Ensuring consistent color can feel like chasing a rainbow. I’ve had my fair share of products that came out with colors off by just enough to notice. It’s usually due to temperature fluctuations or ink mishaps. Adopting standardized color matching systems has been a game-changer for maintaining uniformity.
Achieving consistent color across batches is a recurring challenge. Factors like temperature variations and improper ink formulations can affect color uniformity.
Surface Defects
Surface defects like warping or bubbling are like ghosts haunting your product’s integrity. Once, during a crunch period, improper temperature control led to these issues, costing us time and money. But with advanced temperature management techniques11, we can now keep these defects at bay.
By understanding these challenges, designers like myself can better prepare for successful in-mold decoration projects, ensuring both aesthetic appeal and functional quality are achieved. Plus, with ongoing advancements in IMD technology, there are always new solutions emerging to tackle these age-old problems.
Misalignment can lead to defective IMD products.True
Misalignment between mold and decorative film results in defects.
Polycarbonate is cost-effective for IMD projects.False
Polycarbonate is durable but can be expensive, not cost-effective.
How can you master quality control in In-Mold Decoration?
Ever tried molding a masterpiece only to watch it lose its charm mid-process? That’s where quality control in In-Mold Decoration (IMD) steps in, ensuring every detail shines through.
For effective In-Mold Decoration quality control, prioritize comprehensive inspections, process refinement, and robust testing methods to consistently meet design and aesthetic standards.
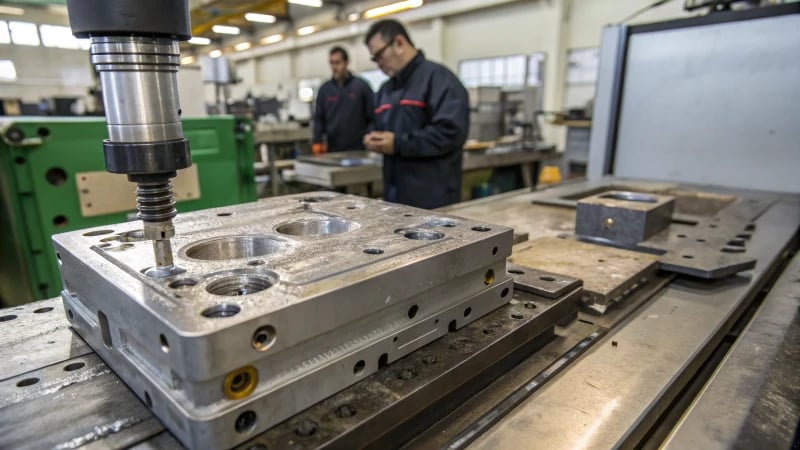
My Journey Through Quality Control in IMD
When I first stepped into the world of In-Mold Decoration, I remember being both excited and overwhelmed. The process seemed magical yet daunting, like trying to bake a cake where every layer must not only taste good but look flawless too. I quickly learned that ensuring quality in IMD is akin to being a meticulous chef—every ingredient and step must be just right.
-
Material Selection: Choosing materials felt like picking the right spices for my dish. The inks and films must endure the heat and pressure of molding, so I always check IMD Material Properties12 to ensure they’re up to the task.
-
Process Optimization: I’ve found that tweaking temperatures and pressures is crucial. It’s like adjusting the oven settings to get that perfect cake rise without any cracks.
-
Inspection and Testing: I remember the first time I caught a defect during an inspection—it was like finding a tiny shell in scrambled eggs. Regular checks are essential. I use visual inspections, adhesion tests, and color consistency checks to keep everything on track.
Inspection Method | Purpose |
---|---|
Visual Inspection | Detect surface defects |
Adhesion Tests | Ensure film bonding |
Color Consistency Check | Verify color accuracy |
Advanced Techniques for Quality Assurance
-
Automated Systems: Investing in automated inspection13 systems was a game-changer for me. These systems act like an extra pair of eyes, catching imperfections with precision that human inspection might miss.
-
Data Analysis Tools: Analyzing data collected during the process helped me see patterns, much like spotting trends in family recipes that indicate when something might go awry.
-
Training and Standardization: Training my team and standardizing procedures across shifts has been vital. It’s like teaching everyone to follow the same recipe so each cake comes out just right every time.
Implementing these strategies involves continuous monitoring14 and adjustments based on feedback. It’s a learning curve, but seeing a project come together beautifully makes every bit of effort worthwhile. By integrating these techniques, you can elevate the quality of your IMD projects and ensure each piece is a work of art.
Material selection is crucial for IMD quality.True
Choosing appropriate materials ensures durability and compatibility in IMD.
Automated systems reduce human error in IMD.True
Automated systems use cameras and sensors to enhance precision in IMD.
Conclusion
Advanced in-mold decoration (IMD) enhances plastic aesthetics by embedding graphics during injection molding. Key steps include design preparation, film positioning, and quality control for optimal results.
-
Discover how IMD achieves vibrant graphics to enhance product aesthetics. ↩
-
Explore how IMD is applied in automotive interiors for elegant finishes. ↩
-
Explore how IMD is applied in automotive interiors for elegant finishes. ↩
-
Understand how IMD stands against traditional methods in terms of aesthetics and durability. ↩
-
Explore various inks suitable for IMD to ensure high-quality graphics on finished products. ↩
-
Learn about top inks that ensure vibrant and durable finishes for in-mold decoration projects. ↩
-
Discover the comprehensive steps involved in IMD, enhancing understanding of design integration. ↩
-
Learn about mold design features that improve graphic alignment precision. ↩
-
Explore how injection molding impacts decorative elements and ensure optimal design outcomes. ↩
-
Exploring this link provides insights into the latest materials available for IMD, helping you choose the best options for your designs. ↩
-
Understanding advanced temperature management techniques can help reduce surface defects, enhancing product quality. ↩
-
This guide provides an in-depth look at the essential material properties needed for successful In-Mold Decoration. ↩
-
Explore how automated systems enhance inspection processes, offering greater precision and efficiency in detecting defects. ↩
-
Learn about effective methods for continuous monitoring, crucial for maintaining and improving quality in manufacturing. ↩