Tuning injection pressure resembles solving a puzzle. Every piece has a vital role. Each part shapes the final product. The result holds importance.
Think about the product’s design, material properties and mold characteristics to change injection pressure well. These elements affect how the melt enters the mold. This impact influences the quality of the final product. Quality matters greatly.
I remember my first big project at the company. The design of a sleek new gadget caught my attention. This was not only about how it looked. Balance was key. Wall thickness, shape complexity and size were important. Thin walls needed higher pressure to prevent short shots. Larger structures required more force to move the melt. Material choice was really challenging. High-viscosity plastics needed more power in the channels. The mold itself played a crucial role, too. Every curve in the runner system or gate size could change everything. It could mean the difference between success and failure. Every detail required careful tuning for high product quality.
Material properties affect injection pressure adjustments.True
Different materials require specific pressures for optimal flow and fill.
Injection pressure is irrelevant to mold characteristics.False
Mold design affects how pressure influences the melt's flow and fill.
How Does Wall Thickness Impact Injection Pressure?
Journey into the captivating world of plastic molding. Wall thickness and injection pressure perform a delicate dance together.
Wall thickness in injection molding acts like an unsung hero. It decides how much pressure is necessary. Thick walls allow the plastic to cool slowly using less pressure. But thin walls require more pressure to avoid unwanted short shots. Balance is key.
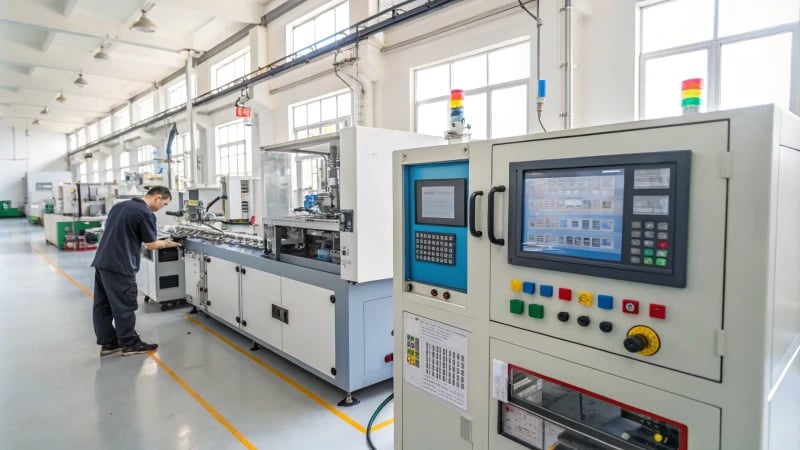
Influence of Wall Thickness on Injection Pressure
I remember the first time I learned about how wall thickness affects injection pressure during a project. It seemed very simple at first. We worked on a smooth plastic shell and I thought, "How hard could this be?" But wall thickness turned out to be the key factor or maybe the surprising problem.
Thicker walls are easy for the plastic melt. They keep heat and let everything flow nicely. Less pressure works because the melt doesn’t freeze quickly. Thin walls, though, are a race against time. They cool fast, so higher pressure fills the mold completely before it cools too much.
Structural Factors and Their Impact
Wall Thickness
- Thick Walls: Thick walls feel like a break. Lower pressure is enough because cooling happens slowly, which lets the melt flow well.
- Thin Walls: This is where the challenge is; fast cooling needs quick filling with higher pressure to stop defects.
Shape Complexity
Once, we created a part with deep holes and tricky areas. On paper, it seemed simple. Little did I know, these features added more challenges! They increased resistance to the melt, demanding extra pressure. You learn these lessons only during a project.
Feature | Impact on Pressure |
---|---|
Deep holes | Increases pressure |
Tricky areas | Increases pressure |
Complex shapes | Alters flow paths |
Material Characteristics
I often think about how material thickness plays a part. Some thick materials like polycarbonate feel like pushing honey through a straw – they need much more pressure. In contrast, thin materials slide easily with less pressure.
Understanding these parts is very important, not just in theory. It’s vital for choosing the right materials and changing settings. It saves costs and brings my designs to life smoothly.
Explore more about plastic material properties1 and how they influence molding processes.
Thicker walls require higher injection pressure.False
Thicker walls require lower injection pressure due to slower cooling.
Thin walls cool faster, needing more injection pressure.True
Thin walls cool quickly, needing higher pressure to fill molds.
How Does Material Viscosity Affect Pressure Adjustment?
Sometimes people wonder why certain materials don’t flow easily. Viscosity holds the answer. It controls how materials move and impacts the pressure shifts in manufacturing.
Material thickness matters a lot when deciding the pressure needed to change flow rates. Thick materials, like polycarbonate, need extra pressure because they resist flow. Thin materials, like polyethylene, need less pressure.
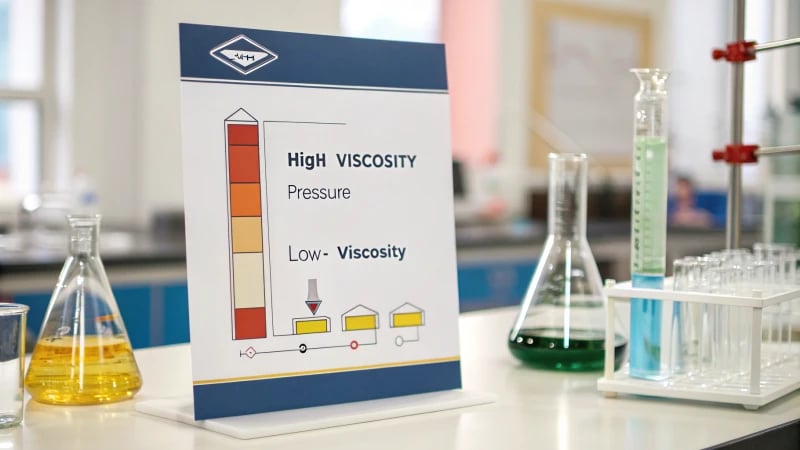
Viscosity and Its Effect on Pressure
Have you ever tried to pour honey from a jar on a cool morning? That’s viscosity. It shows how strongly a material fights against moving. In my early days working with molds, I learned that understanding viscosity felt like dancing with each type of material; every step depended on how it flows.
Take polycarbonate (PC), for instance. It has high viscosity. It feels like trying to pour thick syrup on a cold day. More injection pressure is needed to shape it. Polyethylene (PE), on the other hand, is like making a smoothie on a warm day. It is easy-going and needs less pressure.
Material Type vs. Pressure Needs
Material Type | Viscosity Level | Typical Pressure Required |
---|---|---|
Polycarbonate (PC) | High | 100-150 MPa |
Polyethylene (PE) | Low | 50-100 MPa |
Structure and Viscosity Connection
When designing detailed or oddly shaped products, I saw how structure made things tricky. Filling a thin plastic cup needs more pressure than a thick jug because it cools faster. I’ve experienced it.
- Wall Thickness: Thick walls let high-viscosity materials fill up slowly, reducing pressure needs. Thin walls are quick.
- Shape Complexity: Adding deep holes or complex features increases pressure needs.
- Size: Bigger pieces often need more pressure due to higher resistance.
Consider how these structural factors2 interact with material viscosity to optimize injection pressures.
Viscosity’s Effect on Other Properties
I remember being careful with materials sensitive to heat. Wrong pressure could heat them too much and ruin them. I learned this lesson with polyvinyl chloride (PVC).
- Heat Sensitivity: High-viscosity materials might overheat. Balancing pressure and temperature is very important.
- Crystallinity: Changing pressure alters how materials like nylon form crystals, impacting toughness or transparency.
For more details on plastic material characteristics3, expert resources can be helpful.
Practical Uses and Thoughts
In my journey, balancing mold design is like fine-tuning an instrument. Efficient runner systems, gate types, and good venting all play roles in successful manufacturing.
- Runner Systems: Well-designed runners lower pressure needs by easing resistance.
- Gate Types: Smaller openings, like pin gates, increase resistance, needing more pressure.
- Venting: Good venting is very important. It ensures easy flow and reduces backpressure.
Every part should work well with the mold factors4 to get the best results in production.
High-viscosity materials need higher injection pressures.True
High-viscosity materials have poor fluidity, requiring more force to flow.
Low-viscosity materials generate more shear heat under pressure.False
High-viscosity materials generate more shear heat due to resistance.
Why is mold design critical in determining injection pressure?
Have you ever thought about how a tiny detail in mold design transforms the whole injection molding process?
Mold design is very important for setting injection pressure. It affects how easily the material flows. The sizes of runners matter a lot. Gate types really influence pressure needed. Venting works to help pressure go down. All these factors decide how much pressure the material needs to really fill the mold cavity.
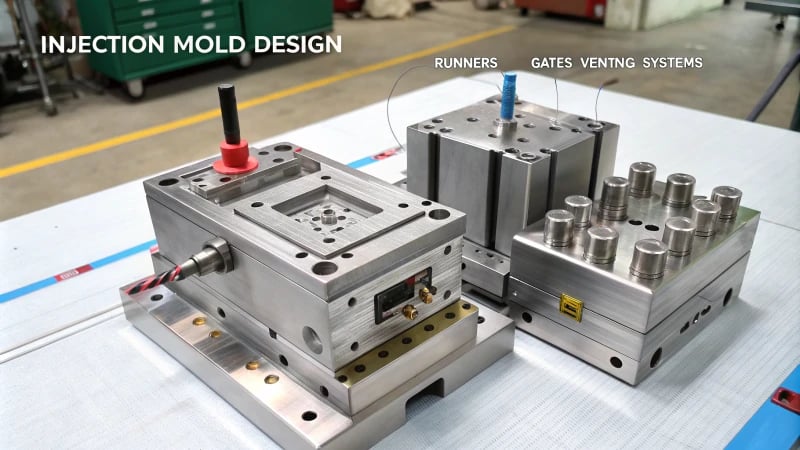
Structure of Plastic Products
The wall thickness of plastic parts is important. Thin walls need higher pressure because they cool fast. Quick filling helps avoid issues. Thick walls let the material flow easily, needing less pressure. Even tiny details matter.
Similarly, complex shapes are also important. Projects with difficult designs, like deep holes and many gates, need more pressure because they resist the flow. These designs are hard but also give chances to be creative and solve problems.
Characteristics of Plastic Materials
Knowing a material’s viscosity is really crucial. Thick plastics like polycarbonate are challenging, needing more pressure to flow through molds. I tried different materials and found that each one behaves differently.
Heat sensitivity keeps me alert. Some plastics need careful handling to stop them from breaking down. This is like balancing pressure and heat settings carefully.
Mold Factors
Runner system design is very important. A good runner lowers the required pressure a lot. I remember a project where changing the runner size improved flow a lot.
Gate type and size matter too; bigger gates need less pressure. These changes bring "aha!" moments in mold design.
Gate Type Impact Table
Gate Type | Required Pressure |
---|---|
Pin Gate | High |
Side Gate | Medium |
Latent Gate | Low |
Venting systems are crucial too, letting air escape, lowering back pressure and making the injection process easier.
Role of Material Selection
Choosing the right material is like finding a perfect match for your design. Material features, like crystallinity5, work best with precise pressure during molding. This impacts how hard and clear a product is. Getting material characteristics and mold design to work together helps produce high-quality results.
By understanding these things and using insights from plastic materials6, I’ve balanced mold configurations to improve product quality while keeping costs in check. It’s about finding the perfect balance where design and production work well together.
Thin walls require higher injection pressure.True
Thin walls cool rapidly, increasing resistance and needing more pressure.
Larger gates increase injection pressure.False
Larger gates reduce flow resistance, decreasing the necessary pressure.
How do gate types affect injection pressure requirements?
Do you ever think about how small aspects of injection molding might change things a lot? Gate types affect how much pressure is used during injection.
Gate types change injection pressure by altering flow resistance. Pin gates often need higher pressures. Their openings are small. Side gates might use less pressure. The design and size of the gate really impact the overall injection pressure. Very much so.
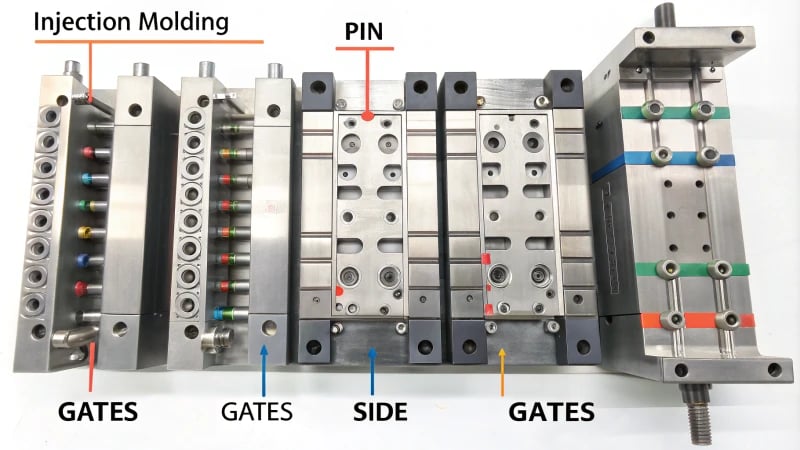
Understanding Gate Types and Their Influence
I remember when I started learning about mold design. The world of gate types seemed very complex. Realizing how minor elements could change things significantly was surprising. Pin gates, for instance, have very small openings. These really increase flow resistance, requiring more pressure to fill the mold properly.
On the other hand, side gates often have bigger openings. Less resistance occurs, which means lower injection pressures. This knowledge really changed the way I improved production efficiency.
The Role of Gate Size and Shape
The gate’s size really affects pressure needs. Larger gates let the melt flow more easily, so less pressure is needed. I compared pin and side gates in a project and created a simple table to understand them better:
Gate Type | Typical Size | Injection Pressure Impact |
---|---|---|
Pin Gate | Small (0.5-1mm) | Higher due to resistance |
Side Gate | Larger (>1mm) | Lower, less resistance |
Structural and Material Considerations
- Wall Thickness: Products with thick walls let the melt flow easily. Thin walls cool quickly, needing higher pressures. I’ve noticed thin-walled products sometimes need 30-50MPa more pressure than thick ones.
- Material Viscosity: Some materials, like polycarbonate, have very high viscosity. They need a lot of pressure to overcome flow resistance.
- Mold Design: The details in mold design control pressure needs. Complex structures with many gates require well-balanced pressures for smooth flow.
For deeper insights, view different injection molding techniques7.
Practical Insights
Understanding gate types and their effect on pressure greatly improves manufacturing processes. Adjusting gate sizes or types has helped projects increase efficiency and save a lot of money. Carefully analyzing these variables results in high-quality and very cost-effective outcomes.
For more on this subject, consider exploring advanced mold design strategies8.
Pin gates require higher injection pressure.True
Pin gates have small openings, increasing flow resistance and pressure.
Side gates increase injection pressure requirements.False
Side gates have larger openings, reducing resistance and pressure.
Conclusion
Adjusting injection pressure in molding requires careful consideration of product design, material properties, wall thickness, and mold characteristics to ensure high-quality outcomes.
-
Gain insights into how different plastic materials influence the injection molding process and required pressures. ↩
-
Explore how different structural features affect injection molding pressures and efficiency. ↩
-
Learn about how material traits influence molding processes and outcomes. ↩
-
Understand how mold design choices can adjust necessary injection pressures. ↩
-
Examining material properties helps in understanding their impact on molding processes, especially regarding pressure settings. ↩
-
Understanding venting systems will highlight their role in reducing injection pressures by improving airflow. ↩
-
Explore diverse techniques to optimize mold designs based on gate types, enhancing efficiency. ↩
-
Gain insights into cutting-edge strategies for adjusting mold designs according to gate type impacts. ↩