Tweaking injection pressure resembles refining a recipe. Achieving the ideal level is crucial. Accuracy really matters.
Adjusting injection pressure requires a focus on the product’s needs, its complexity and material properties. Balancing these elements is vital. Product strength, precision and appearance depend on it. Defects must be avoided.
When I began adjusting injection pressures, it felt like solving a puzzle. Different pieces needed to fit together perfectly. They included performance demands, product structure and materials. In one case, I worked with strong car parts. I had to carefully increase pressure to fill the mold correctly. It was very important not to overdo it. Finding the right balance is key. Knowledge of each factor improves both quality and efficiency in production.
Higher injection pressure improves product strength.True
Increasing pressure can enhance material flow, filling molds better and improving strength.
Low injection pressure reduces production defects.False
Lower pressure may lead to incomplete filling, increasing defects like voids or weak spots.
What Are the Mechanical Performance Requirements for Plastic Products?
Have you ever thought about why plastic products are dependable and adaptable? Their strength and flexibility are key.
Plastic products require specific mechanical qualities such as strength, toughness, precise size and good looks. Product use and how complex it is change these needs. Injection pressure and processing techniques depend on these factors.
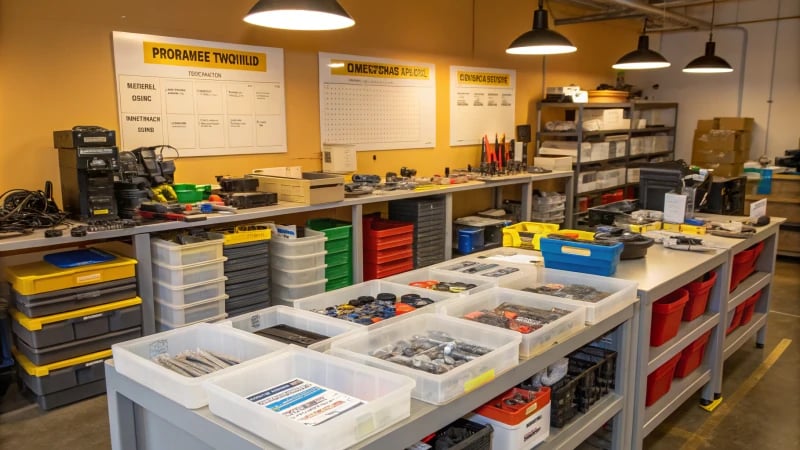
Mechanical Strength and Toughness
Early in my product design journey, I found learning about mechanical strength and toughness1 hard. Picture creating car parts where high injection pressure plays a big role. For instance, forming polyamide (PA) often needs pressure from 100 to 150 MPa to develop a strong internal structure without too much stress. It brought to mind my first project – designing a tough phone case, trying to keep strength without breaking.
Dimensional Accuracy
Accuracy is crucial, especially in places like precision instrument accessory work. I remember struggling with keeping dimensional accuracy; it felt like tightrope walking, managing injection pressure between 60 and 100 MPa to prevent changes after molding. This careful balance meant using the right holding pressure and time – a lesson that taught me patience. Patience was key.
Appearance Quality
In products where looks are vital, like clear PMMA items, pressure management2 prevents defects. An injection pressure of 70 to 100 MPa often works well, yet requires the perfect speed. In my early design days, I crafted a shiny jewelry box where any small imperfection was unacceptable. It was a delicate dance of precision. Precision mattered a lot.
Product Type | Injection Pressure (MPa) |
---|---|
High Strength | 100-150 |
High Precision | 60-100 |
High Gloss | 70-100 |
Structural Complexity
Simple Structures
Simple designs, like flat plates, bring relief – they need less pressure, around 50 to 70 MPa for polyethylene (PE). This straightforward approach helps reduce defect risks. I helped design a simple food container where this method made production easy.
Complex Structures
Intricate structures, like thin-walled parts, tell a different story. They demand more pressure (100 to 180 MPa) to fill molds completely without short shots. It reminds me of when I created a complex toy full of detailed features; achieving precision in each detail was a victory of patience.
Material Properties
High Viscosity Materials
High viscosity materials such as polycarbonate (PC), need higher pressures (100 to 150 MPa). I learned this the hard way during a project involving high-temperature-resistant parts – it was a lesson in balancing temperature and speed to avoid shear heat effects. Balancing was essential.
Low Viscosity Materials
For low viscosity materials like polypropylene (PP), pressures between 70 and 100 MPa are normal. Yet, complex designs sometimes need pressures up to 130 MPa. This flexibility helped when I designed stackable storage bins where durability was important.
Understanding these aspects really allows plastic products to perform as intended in various situations. Designers and manufacturers should adjust parameters for each product’s specific needs by exploring resources on injection pressure guidelines3.
High strength plastics need 100-150 MPa pressure.True
Automotive parts require high injection pressure for dense structure.
Low viscosity materials require over 150 MPa pressure.False
Low viscosity materials typically use 70-100 MPa, not over 150 MPa.
How does structural complexity influence injection pressure?
Curious about how intricate plastic product designs alter molding methods? Explore the intriguing realm of injection pressures. These pressures bring our creations to life in an excellent way.
Complex plastic products need higher injection pressure to fill the mold completely. Higher pressure stops defects and keeps quality high. This change is important to beat resistance. It keeps the flow smooth. Smooth flow affects efficiency and keeps products strong.
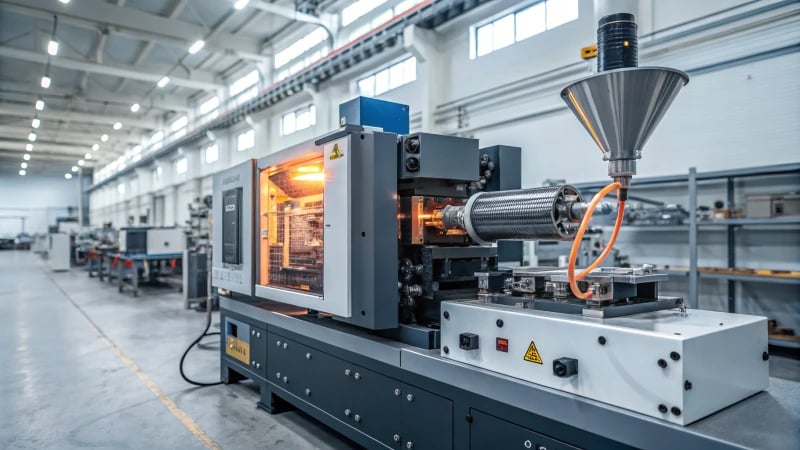
Understanding the Influence of Structural Complexity
I remember when I first created a plastic item with detailed shapes. Thin walls and deep spaces felt like solving a big puzzle. More complex shapes needed higher injection pressures to fill the mold correctly. For example, thin-walled parts4 bring cooling issues. They really need just the right pressure to avoid problems.
Comparing Simple vs. Complex Structures
Structure Type | Injection Pressure (MPa) |
---|---|
Simple | 50-70 |
Complex | 100-180 |
In my early days, I worked on easy items like flat plates where lower pressures were usually enough. Later, I explored more complex designs with several gates, which really changed everything. These designs needed precise changes to stop defects. I recall my first important project where I had to carefully adjust pressure to deal with flow resistance in complex designs.
Material Properties and Complexity
Different materials present unique challenges. I worked with high-viscosity materials like polycarbonate5. They needed higher pressure to move through complex designs. Low-viscosity materials offered some ease but still demanded attention, especially with complex structures.
Balancing Performance Requirements
Balancing performance needs and tricky structures became an art. High-strength items needed increased pressure; however, I had to avoid adding too much stress. Precision items taught me a big lesson: dimensional stability relies on exact pressure control—one mistake could ruin the whole batch.
Understanding how structural complexity and injection pressure connect feels like mastering a craft. It mixes efficiency and integrity to produce perfect plastic parts. Accuracy and appearance matter in this delicate dance of design and engineering, where each step really counts.
Thin-walled parts require higher injection pressure.True
Thin walls cool quickly, needing high pressure to prevent short shots.
Simple structures need 100-180 MPa injection pressure.False
Simple structures require 50-70 MPa, not the higher range for complex designs.
Why Is It Important to Adjust Pressure According to Material Properties?
Ever thought about why achieving a perfect finish on plastic parts often seems out of reach?
Changing pressure based on what materials can do is very important. It greatly affects how well something works, its exact shape and how it looks at the end. Correct pressure stops mistakes. It keeps the product good. This is very important in things like injection molding. Quality must be maintained.
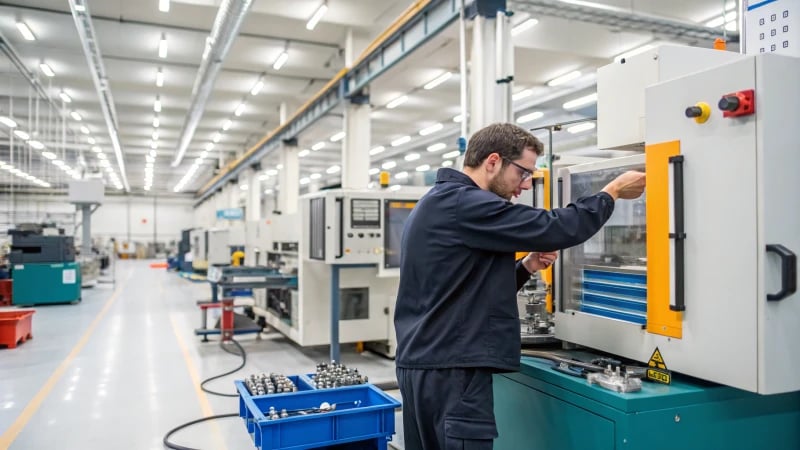
Performance Needs for Plastic Products
Starting my work on plastic product design changed everything. Learning about how plastic behaves under pressure was like opening a new door. Some car parts look sleek and need to be strong without flaws. Correct injection pressure6 is key. High pressure is really necessary for strength in car parts. It fills every tiny space, giving that solid feel people expect. However, I remember a time when too much pressure led to cracks later. It’s truly a fine line.
Requirement Type | Example Products | Recommended Pressure |
---|---|---|
High Strength & Toughness | Automotive Parts | 100-150 MPa |
Size Accuracy and Looks
Designing a precise tool accessory taught me a lot. Every little detail counts. I realized the importance of right pressure for keeping shapes stable after removing them from molds. It feels like cooking; just the right mix (or pressure) is crucial.
Think about ugly marks on plastic products. Pressure adjustments help fix those. No one likes defects like flash or trapped air, especially on shiny products.
Product Structure Challenges
Simple shapes are easy with lower pressures, but complex shapes? They need careful attention to fill every part well, especially with thin walls or deep holes; this makes a difference. Structural complexity directly impacts pressure adjustments7.
Structure Type | Complexity Level | Pressure Range |
---|---|---|
Simple | Low | 50-70 MPa |
Complex | High | 100-180 MPa |
How Material Thickness Matters
Working with different materials taught me that thickness is a big deal. High-thickness materials like polycarbonate (PC) require more pressure to flow smoothly. Less thick materials like polyethylene (PE) often need less pressure unless the design changes that.
Balancing pressure with material traits is really where the magic starts. This doesn’t just create any product but one that lasts without breaking down or having flaws. That quality is something I always look for in my work.
High pressure increases internal stress in plastic parts.True
Excessive pressure can lead to increased internal stress in plastics.
Low viscosity materials always require high pressure.False
Low viscosity materials generally require lower pressures unless design demands.
How Does Injection Pressure Influence Product Appearance?
When I began working with injection molding, I was surprised by the impact of injection pressure on a product’s look. This pressure really changes the surface. It transforms everything.
Injection pressure changes how the product looks by controlling plastic flow into the mold. Correct pressure creates a smooth surface and stops problems like flash or trapped air. It really improves the quality.
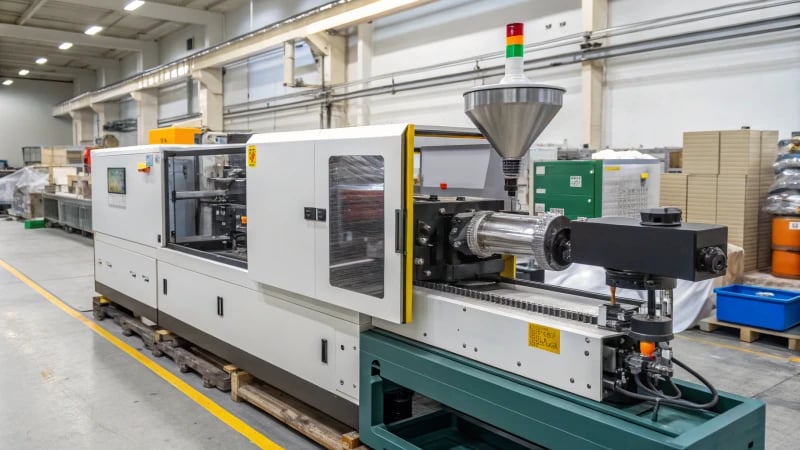
Understanding Injection Pressure’s Impact on Appearance
Injection pressure influences how the plastic melt behaves as it enters and fills the mold cavity. It’s like pouring syrup into a pancake mold – the right pressure fills every corner without spilling over. High injection pressure can ensure that complex and high-strength products achieve the required structural integrity. For instance, products made from polyamide (PA)8 may require pressures between 100-150MPa to ensure sufficient density and strength. However, excessive pressure can lead to undesirable effects such as internal stresses or flash, affecting appearance negatively.
Balancing Pressure for Different Product Needs
- Gloss and Surface Finish: Products requiring high gloss, like transparent plastics (e.g., PMMA), need precise pressure control. An optimal range of 70-100MPa ensures smooth filling without air entrapment or flash.
- High gloss needs careful pressure control.
- Dimensional Stability: High-precision parts demand careful pressure regulation. Lower pressures, around 60-100MPa, with controlled holding time, maintain dimensional accuracy while minimizing rebound.
- Accurate parts require lower pressures to stay true to design.
Considering Structural Complexity
I remember a difficult thin-walled design needing higher pressures to prevent short shots. Complex designs, such as thin-walled or multi-gate products, require higher pressures to avoid short shots due to rapid cooling. For polycarbonate (PC)9, we applied roughly 100-150MPa to maintain perfect form.
Product Type | Injection Pressure Range (MPa) |
---|---|
Simple structures (PE) | 50-70 |
Complex structures | 100-180 |
Adjusting for Material Properties
The viscosity of materials plays a significant role in determining injection pressure. Once, I worked with thick PPO materials and had to increase pressure to about 120-160MPa. High-viscosity materials like PPO need higher pressures (120-160MPa) to facilitate proper flow. Conversely, lower viscosity materials like PE require less pressure unless the design complexity or quality demands increase.
These elements – pressure, material properties and design complexity – are crucial for creating products that look good and hold strong. Ensuring the right balance of pressure tailored to the specific requirements of the product and material can greatly influence not only the structural integrity but also the appearance quality of injection-molded products.
High injection pressure ensures structural integrity.True
High pressure fills complex molds fully, ensuring product strength.
Lower viscosity materials always require higher pressure.False
Lower viscosity materials generally need less pressure unless design complexity increases.
Conclusion
Adjusting injection pressure is crucial for optimizing plastic product performance, balancing strength, accuracy, and appearance based on material properties and structural complexity to avoid defects.
-
Explore specific injection pressures for automotive parts to ensure strength and toughness. ↩
-
Learn about various injection pressures for different materials to optimize performance. ↩
-
Learn about various injection pressures for different materials to optimize performance. ↩
-
Explore why thin-walled parts need sufficient injection pressure to avoid defects and ensure complete mold filling. ↩
-
Learn how polycarbonate’s viscosity demands higher injection pressures for effective molding. ↩
-
Understand how proper injection pressure affects product quality and performance. ↩
-
Learn about the importance of pressure in complex structure manufacturing. ↩
-
Explore specific pressure settings for polyamide products to ensure strength and avoid defects. ↩
-
Learn about appropriate injection pressures for polycarbonate products to maintain quality. ↩