Injection molding isn’t just a process; it’s an art form that demands precision. Even the tiniest adjustments can lead to breathtaking improvements in product quality.
To adjust back pressure in injection molding for better quality, it’s essential to understand its role in compacting the melt, promoting plasticization uniformity, and ensuring full mixing of additives. Set back pressure based on material properties and product requirements, using trial production to refine settings.
While this provides a foundational understanding, diving deeper into specific methods and considerations can optimize production outcomes. Let’s explore how careful adjustments and attention to related parameters can transform your injection molding process.
Back pressure affects product consistency in injection molding.True
Adjusting back pressure ensures uniform melt compaction, reducing defects.
What Is the Impact of Back Pressure on Product Consistency?
Back pressure plays a crucial role in injection molding, directly influencing product consistency and quality.
Back pressure in injection molding affects product consistency by compacting the melt, enhancing plasticization uniformity, and ensuring even distribution of additives. Proper adjustment leads to stable physical properties and uniform product color, minimizing defects like bubbles and flow marks.
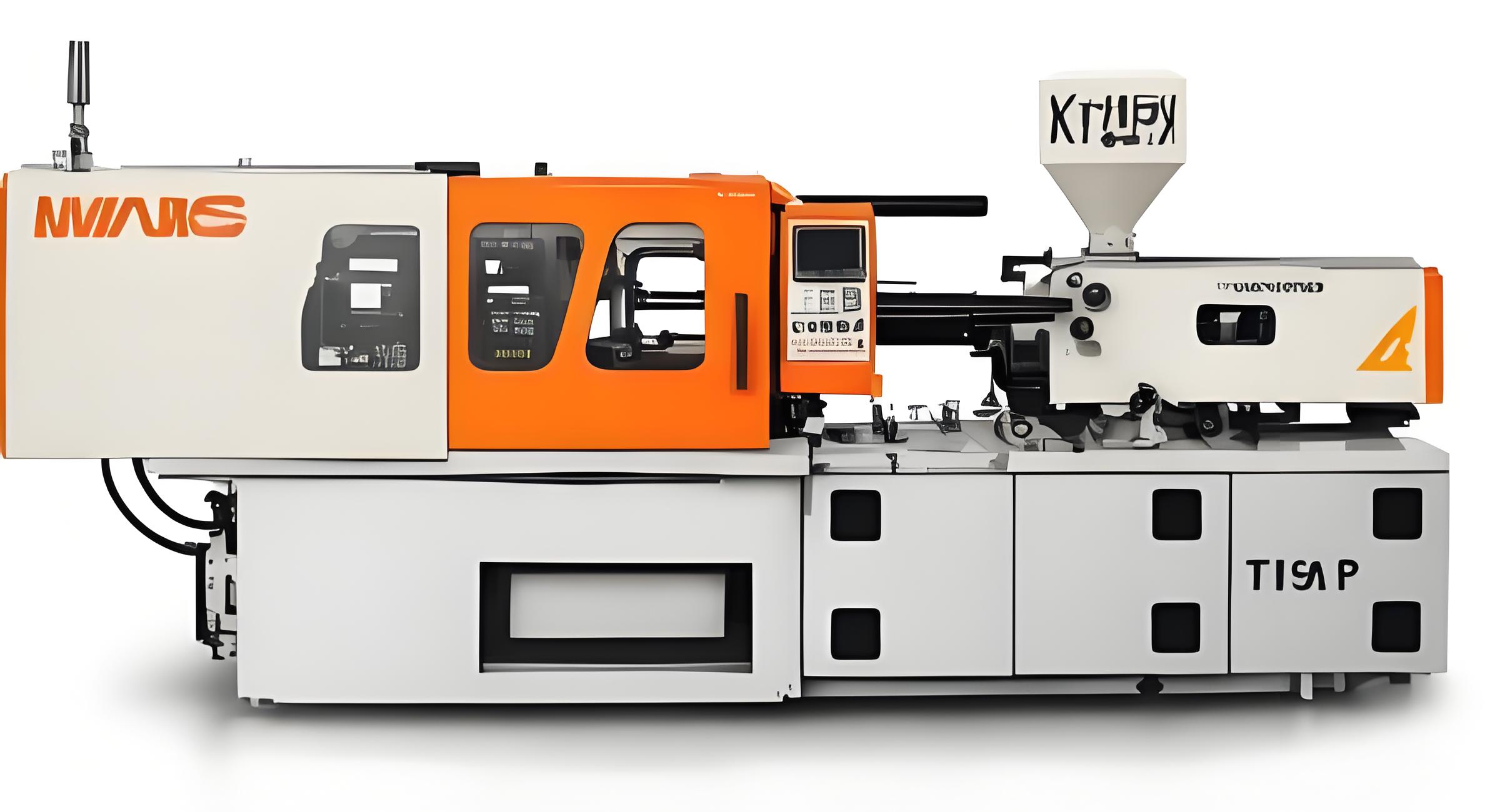
Understanding Back Pressure’s Role
In injection molding, back pressure is essential for ensuring the melt inside the barrel is adequately compacted. This compaction aids in eliminating gases, which helps reduce bubbles and voids in the final product. By promoting plasticization uniformity1, back pressure ensures that the melted plastic achieves consistent viscosity, leading to stable physical properties.
Moreover, back pressure increases the residence time of the melt, facilitating better mixing of pigments and additives. This results in a more uniform product color, essential for maintaining product consistency across batches.
Appropriate Back Pressure Ranges
Different materials require specific back pressure settings to optimize product consistency. For instance, plastics like polyethylene (PE) and polypropylene (PP), known for their good fluidity, generally require a lower back pressure range of 0.5MPa to 2MPa. Conversely, materials like polycarbonate (PC) and polyamide (PA), which have poor fluidity and are heat-sensitive, benefit from higher back pressures ranging from 2MPa to 5MPa.
Material Type | Typical Back Pressure Range |
---|---|
Polyethylene (PE) | 0.5MPa – 2MPa |
Polypropylene (PP) | 0.5MPa – 2MPa |
Polycarbonate (PC) | 2MPa – 5MPa |
Polyamide (PA) | 2MPa – 5MPa |
Observing Changes in Product Consistency
When adjusting back pressure, trial production helps observe changes in product appearance and physical attributes. If issues such as bubbles or shrinkage occur, increasing the back pressure may resolve them. On the other hand, if problems like flow marks or difficulties in demolding arise, reducing the back pressure could be beneficial.
It’s crucial to consider associated parameters like screw speed and injection pressure when fine-tuning back pressure. This holistic approach ensures that all elements of the injection process work harmoniously to maintain product consistency.
Key Considerations
When adjusting back pressure, ensure it remains within an optimal range to avoid increased wear on machinery and energy consumption. Additionally, attention must be paid to the plasticizing temperature and time to prevent adversely affecting the plastic’s quality.
For specialized materials or products with unique requirements, combining back pressure adjustments with other process parameters, such as mold temperature and holding pressure, might be necessary to achieve desired results. Understanding these key considerations2 can significantly enhance product consistency.
High back pressure reduces bubbles in products.True
Increased back pressure compacts the melt, eliminating gases and reducing bubbles.
Polypropylene requires high back pressure for consistency.False
Polypropylene generally requires a lower back pressure range of 0.5MPa to 2MPa.
How to Identify the Right Back Pressure Range for Different Plastics?
Choosing the correct back pressure is crucial for quality in injection molding.
To identify the right back pressure range for different plastics, assess the material’s flow characteristics and heat sensitivity. Generally, use lower back pressure for high-fluidity plastics like PE and PP, and higher for less fluid, heat-sensitive materials like PC and PA.

Understanding Material Characteristics
The first step in identifying the right back pressure range is understanding the specific characteristics of the plastic being used. Each type of plastic has unique properties that influence how it responds during the injection molding process.
- High Fluidity Plastics: Materials such as polyethylene (PE) and polypropylene (PP) are known for their excellent flow characteristics. These plastics typically require a lower back pressure, generally between 0.5MPa to 2MPa. The low range helps prevent excessive shear stress and potential degradation of the material.
- Low Fluidity Plastics: On the other hand, plastics like polycarbonate (PC) and polyamide (PA) have poorer flow characteristics and higher heat sensitivity. For these materials, a higher back pressure range of approximately 2MPa to 5MPa is recommended to ensure proper plasticization and uniformity.
Practical Steps for Determination
1. Preliminary Setting and Observation
Start with a preliminary back pressure setting based on the material’s general requirements. Gradually increase or decrease the pressure while observing the product’s quality during trial production.
- Signs to Increase Pressure: If you notice bubbles, shrinkage, or dimensional instability, this might be an indicator to increase back pressure.
- Signs to Decrease Pressure: Conversely, flow marks, flash, or demolding difficulties suggest a reduction might be necessary.
2. Consider Additional Parameters
Adjusting back pressure in isolation is rarely effective. It’s crucial to concurrently monitor and adjust related parameters such as screw speed, injection pressure, and injection speed. Ensuring these factors harmonize with your back pressure adjustments can significantly enhance product quality.
3. Document and Refine
After determining an effective range through trial production, document the optimal settings. This documentation will serve as a reference for future production runs, ensuring consistency and quality across batches.
Material-Specific Considerations
Some plastics may have additional requirements due to their composition or intended product application. For instance, certain pigments or additives may necessitate alterations in the standard approach.
To better visualize this, consider using a table that outlines recommended back pressure ranges based on common plastic types:
Plastic Type | Recommended Back Pressure Range |
---|---|
Polyethylene (PE) | 0.5MPa – 2MPa |
Polypropylene (PP) | 0.5MPa – 2MPa |
Polycarbonate (PC) | 2MPa – 5MPa |
Polyamide (PA) | 2MPa – 5MPa |
While this provides a foundation for setting back pressures, always consider the unique aspects of your production needs and consult equipment manuals or industry guides3 for precise adjustments.
High fluidity plastics need lower back pressure.True
High fluidity plastics like PE and PP require 0.5MPa to 2MPa.
Polycarbonate requires the lowest back pressure range.False
Polycarbonate needs higher back pressure, around 2MPa to 5MPa.
What Are the Steps to Adjust Back Pressure Effectively?
Adjusting back pressure is crucial for optimizing injection molding, impacting the quality and consistency of products.
To adjust back pressure effectively, locate the adjustment interface, set initial values based on material properties, conduct trial production, and observe changes. Fine-tune settings by monitoring product quality and machine parameters until optimal conditions are met.

Understanding Back Pressure Adjustment
The process of adjusting back pressure begins with recognizing its critical role in injection molding. Back pressure affects the compactness of the melt within the barrel, facilitating the removal of gases and reducing defects like bubbles and voids. Additionally, it ensures uniform plasticization, thereby stabilizing the physical properties of products.
Determining Initial Back Pressure Settings
Start by identifying the adjustment interface on your injection molding machine. This could be a physical button or a parameter setting screen.
Initial Settings by Material:
Material Type | Suggested Back Pressure Range |
---|---|
Polyethylene (PE) | 0.5 MPa – 2 MPa |
Polypropylene (PP) | 0.5 MPa – 2 MPa |
Polycarbonate (PC) | 2 MPa – 5 MPa |
Polyamide (PA) | 2 MPa – 5 MPa |
Conducting Trial Production
Upon setting an initial back pressure value, proceed with trial mold production. Observe changes in the product’s appearance, size, and physical properties:
- Increase Back Pressure: If issues like bubbles or shrinkage occur, suggesting inadequate compactness or mixing.
- Decrease Back Pressure: If defects such as flow marks or difficulties in demolding appear, which might indicate excessive pressure.
Monitoring Machine Parameters
During adjustments, it’s crucial to monitor parameters like screw speed, injection pressure, and injection speed. Ensuring these align with back pressure adjustments is key to maintaining a balanced process.
Finalizing and Recording Optimal Settings
After multiple trials and refinements, identify the optimal back pressure settings. Document these for consistent future production. Remember that while adjusting back pressure, be mindful of potential effects on screw wear and energy consumption.
For further insights into optimizing your injection molding process4, consider exploring how these adjustments interplay with other parameters such as mold temperature and holding pressure.
Back pressure affects product quality in injection molding.True
Back pressure impacts melt compactness, reducing defects and stabilizing properties.
Polyethylene requires higher back pressure than polycarbonate.False
Polyethylene needs 0.5-2 MPa, while polycarbonate requires 2-5 MPa.
Why Is It Important to Consider Other Parameters When Adjusting Back Pressure?
Adjusting back pressure alone isn’t enough; other parameters significantly influence injection molding outcomes.
Considering other parameters alongside back pressure adjustment is crucial as it ensures optimal melt quality, product consistency, and operational efficiency. Coordinating with factors like screw speed, injection pressure, and mold temperature maximizes the benefits of back pressure adjustments and enhances overall production quality.

Coordinating Screw Speed and Back Pressure
One crucial aspect of injection molding is balancing screw speed5 with back pressure. High screw speeds can lead to inadequate mixing and increased shear, affecting product consistency. Conversely, low speeds might result in longer cycle times. Adjusting the screw speed in harmony with back pressure helps achieve a uniform melt.
Synchronizing Injection Pressure with Back Pressure
Injection pressure directly influences the packing of the melt into the mold cavity. When adjusting back pressure, it’s vital to consider how it interacts with injection pressure6. Proper synchronization prevents defects like flashing or incomplete filling, ensuring the final product meets specifications.
The Role of Mold Temperature
Mold temperature significantly affects the cooling rate of the molded part, impacting shrinkage and dimensional stability. As back pressure adjustments alter the melt’s characteristics, maintaining an appropriate mold temperature7 ensures that the cooling rate complements these changes, thereby enhancing product quality.
Impact of Material-Specific Parameters
Different plastics exhibit varying behaviors under similar processing conditions. For example, high-viscosity materials might require higher back pressures, but also demand careful control of other parameters to prevent issues like degradation or poor surface finish. Adapting processing parameters specific to the material type, such as adjusting holding pressure or cooling time, is essential for optimal results.
Utilizing Process Monitoring Tools
Modern injection molding machines often come equipped with advanced monitoring tools that provide real-time feedback on various process parameters. Utilizing these tools allows operators to fine-tune process settings8 efficiently, ensuring that any changes in back pressure are complemented by appropriate adjustments elsewhere in the process.
Screw speed affects melt quality in injection molding.True
High screw speeds can lead to inadequate mixing and increased shear.
Mold temperature does not impact product quality.False
Mold temperature affects cooling rate, impacting shrinkage and stability.
Conclusion
Adjusting back pressure is crucial for enhancing product quality in injection molding. By applying these insights, you can make informed decisions that lead to consistent results.
-
Gain insights into achieving uniform plasticization during injection molding.: Walls in any plastic-molded part should be no less than 40 to 60 percent that of adjacent walls, and all should fit within recommended thickness ranges for the … ↩
-
Explore vital factors when fine-tuning back pressure for optimal results.: The back pressure settings typically start at fifty PSI and increase in ten PSI increments. The maximum hydraulic pressure for the equipment is … ↩
-
Provides detailed guidelines and industry standards for optimal back pressure settings.: Suggested BP Settings. Material suppliers and RJG recommend BP to be set to approximately 500-1,000 specific psi. This refers to the pressure in … ↩
-
Learn how various parameter adjustments enhance molding process efficiency.: 1. Temperature Control: · 2. Injection Speed: · 3. Cooling Time: · 4. Plastic Material Selection: · 5. Screw Speed and Back Pressure: · 6. Injection … ↩
-
Understand how screw speed affects melt mixing and shear rates.: Most people readily accept that screw rotation provides most (about 70–90%) of the energy needed to melt the plastic for the shot, so it is important. ↩
-
Learn how injection and back pressures interplay during molding.: BP is resistance applied to the back of the screw during plasticizing (screw recovery). It tries to resist the screw achieving the shot size position. ↩
-
Explore how mold temperature impacts cooling and product quality.: In semi-crystalline materials the mold temperature is an important factor in determining the degree of crystallinity in the polymer. The degree … ↩
-
Discover tools for optimizing process parameters in real-time.: Kistler offers sensors to monitor cavity pressure and temperature in the injection molding process – the fundamental basis for efficient monitoring and control. ↩