Have you ever been in the hardware store, looking at various plastic materials, thinking about which is best for your task?
ABS plastic is known for its superior mechanical strength and aesthetic appeal, making it ideal for durable applications. In contrast, PP is lighter and offers excellent chemical resistance, making it suitable for products where weight and chemical exposure are concerns.
Examining the unique features of ABS and PP Materials helps you choose the best material for your next project. Consider their properties, benefits and real-world uses.
ABS plastic has higher mechanical strength than PP.True
ABS is popular for its very strong build, which suits it for long-lasting uses.
What are the key differences in mechanical properties between ABS and PP?
When picking between ABS and PP plastics, knowing their mechanical features is crucial to select wisely for your task.
ABS boasts higher mechanical strength and abrasion resistance, ideal for durable products. PP is lighter with less impact resistance but excels in lightweight applications.
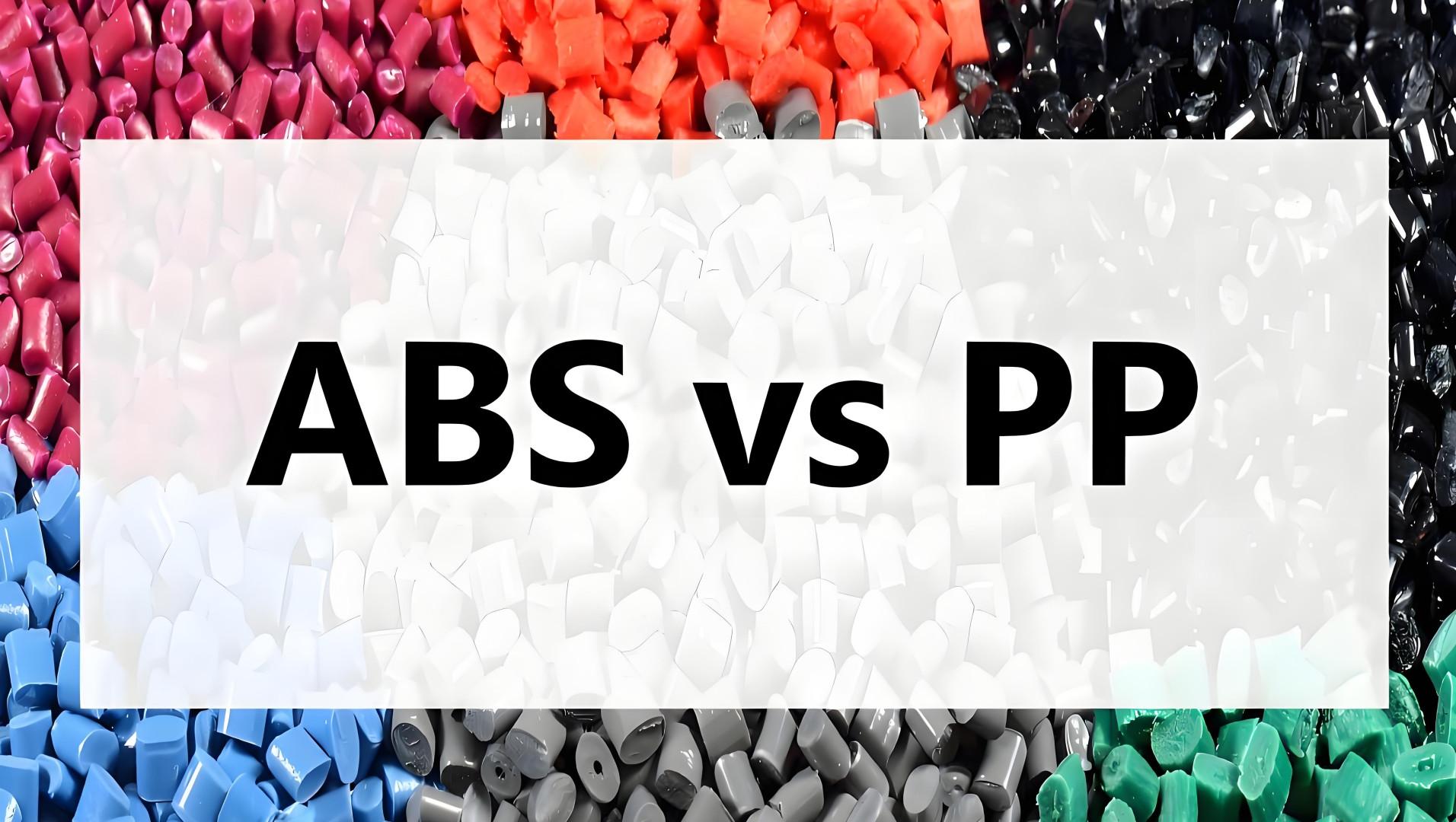
Strength Comparison
ABS plastic is known for its strong toughness. This trait suits it for things like computer keyboards and car parts that need to last long. For example, products from ABS can handle outside pressures without breaking.
On the other side, PP (polypropylene) plastic is often not as strong, especially against impacts. Things made only from PP might break when hit. But, its strength may rise when blended with other elements. Studies on PP wood-plastic mixtures1 show they bend better than some plastics, but still lack the toughness of ABS.
Abrasion Resistance
ABS resists wear because of its structure, making it handle friction in many places. This resilience makes ABS popular where vehicles and machines are built.
PP has weaker wear resistance. Yet, its performance possibly improves with additives or certain techniques. Adding wear-resistance additives to PP2 may help it last longer for some uses.
Density and Weight
ABS has a higher density, leading to heavier items. This trait is useful where weight is good for steady use.
PP has less density, making it perfect for light uses like car parts where being light helps in saving fuel.
Property | ABS | PP |
---|---|---|
Strength | High | Moderate |
Abrasion Resistance | Excellent | Moderate (can rise) |
Density | High | Low |
Applications in Industry
ABS, with its high strength and wear resistance, is chosen for long-lasting and good-looking products like gadget covers and car parts.
PP, with its light weight and chemical sturdiness, fits packaging and throwaway goods where cheap production and simple making are key.
So, picking ABS or PP depends on what the use needs. For items needing high strength and durability, ABS is normally better. For uses where light weight and chemical resistance are main needs, PP might work better.
ABS has higher mechanical strength than PP.True
ABS's terpolymer structure offers excellent strength, suitable for lasting uses.
PP is heavier than ABS due to higher density.False
PP has a lower density than ABS. It is perfect for lightweight uses.
How does the cost of ABS compare to PP in manufacturing?
Knowing the price differences between ABS and PP plastics is important for choosing affordable production options.
Generally, PP plastic is more cost-effective than ABS due to its simpler production process and lower raw material costs. However, the choice should consider specific performance requirements, as ABS offers superior strength and aesthetic quality.
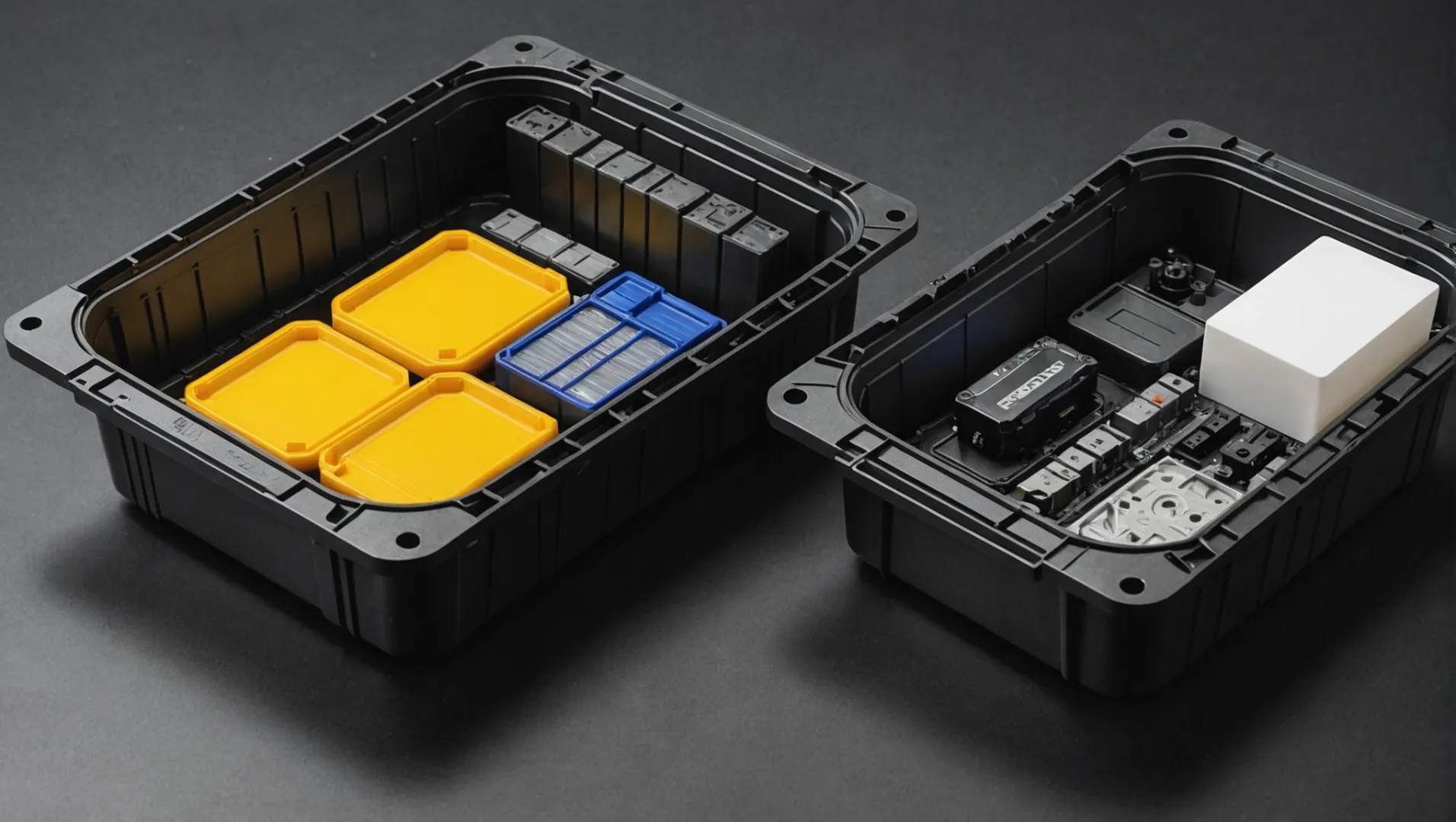
Using Cost Study: ABS vs. PP Plastics
When checking materials for products, price is very important. ABS (Acrylonitrile Butadiene Styrene) plastic is usually more expensive than Polypropylene (PP). This is because its production is complicated and the base materials cost more to get the needed qualities. For example, ABS‘s strong build3 and nice look often justify its price in things that need strength and good appearance.
On the other hand, PP plastic is known for being cheap. Its easier production and plenty of raw materials make it a low-cost option. PP‘s lightweight nature further lowers costs in shipping and handling, making it perfect for producing large quantities of single-use items like packaging materials.
Feature | ABS Plastic | PP Plastic |
---|---|---|
Strength | High | Moderate |
Density | High | Low |
Resistance to Chemicals | Moderate | High |
When Price and Performance Meet
While thinking about prices is necessary, the final choice depends on what the product needs. Items that need to last long, like car interiors or electronic cases, often merit spending on ABS due to its toughness and ability to stay firm under pressure.
For uses where lighter weight and chemical resistance matter—like food containers or light car parts—PP is preferred. Though not as strong as ABS, PP might be mixed with other materials to give a middle ground between function and cost.
Industry Methods and Price Effects
In fields like electronics, where exact shaping and looks are key, the extra price of ABS is balanced by its better shaping abilities and final product quality. Meanwhile, PP‘s steadiness with chemicals4 makes it common in packaging and chemical storage use, where holding up against acids and bases is important.
In the end, producers must think over these points carefully, matching material choice with both budget limits and function needs to achieve better production results.
PP plastic is more cost-effective than ABS.True
PP has an easier creation method and reduced material expenses.
ABS offers higher chemical resistance than PP.False
PP is famous for its strong resistance to chemicals compared to ABS.
Which industries commonly use ABS versus PP plastics?
ABS and PP plastics possess special qualities that render them fitting for different sectors, ranging from car manufacturing to packaging.
ABS plastic is extensively used in the automotive and electronics industries due to its strength and aesthetic quality, whereas PP is favored in the packaging industry for its lightweight and chemical resistance properties.
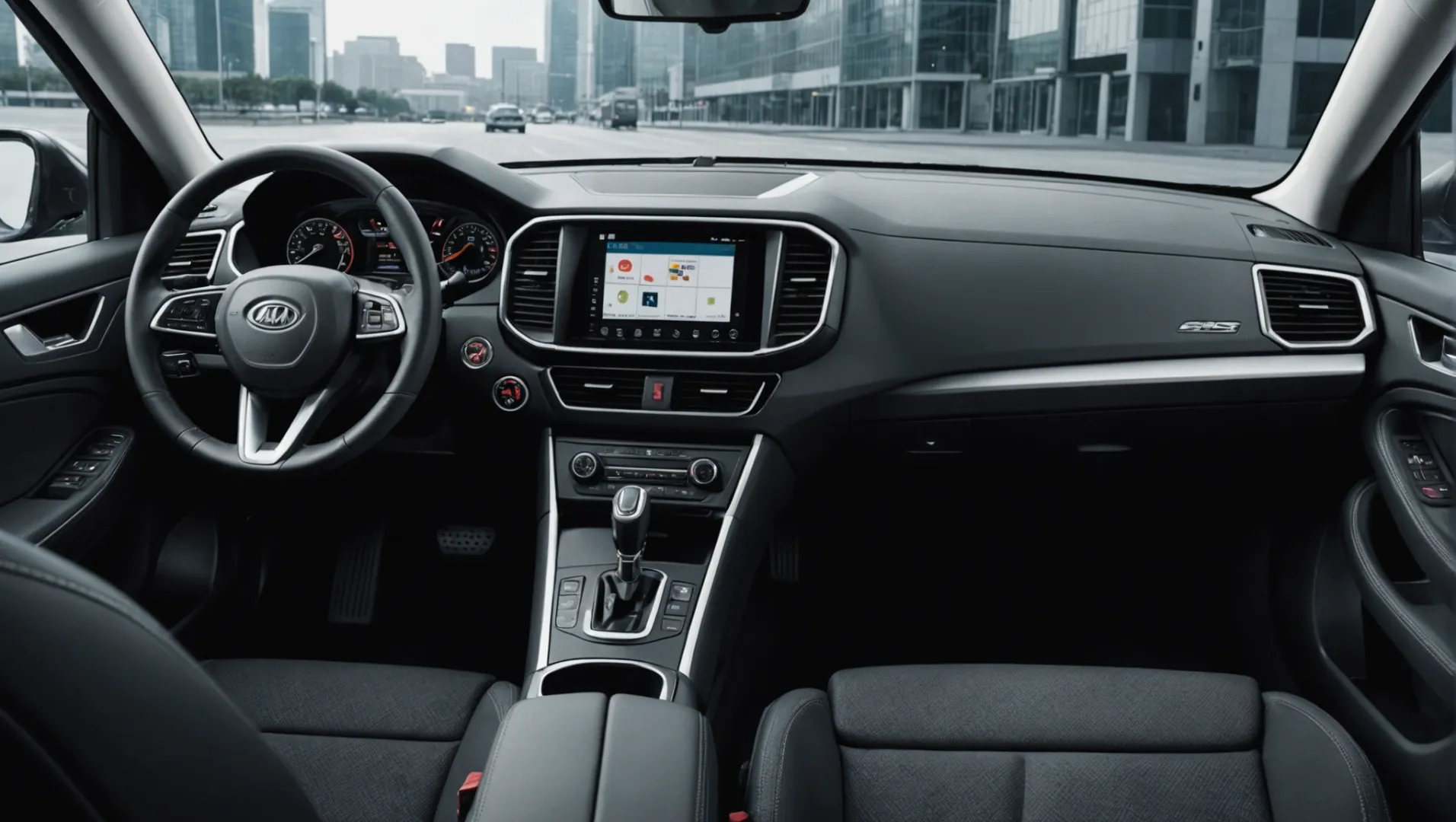
Automotive Industry: Using ABS and PP Plastics
Cars use a lot of ABS and PP plastics, but in different ways. ABS plastic5 often finds use in car interiors like dashboards and central panels because it is strong and looks nice. It handles impacts well, so it suits parts needing toughness.
In contrast, PP plastics6 help reduce weight in vehicles. Parts like bumpers and inside features benefit from PP‘s lightness, which probably helps save fuel by lessening the car’s weight.
Component | ABS Plastic | PP Plastic |
---|---|---|
Dashboards | ✓ | |
Bumpers | ✓ | |
Interior Panels | ✓ | ✓ (when lightweight needed) |
Electronics Industry: ABS Rules
In electronics, ABS plastic stands out because it insulates well and is sturdy. It is seen in the covers of things like TVs, screens, and keyboards. ABS molds easily into complex shapes needed for modern gadgets.
PP finds less use in electronics because it is not as strong, but it resists chemicals, so some parts exposed to chemicals or heat use it.
Packaging Industry: PP Reigns
The packaging business mostly opts for PP plastics7 because they are light and resist chemicals well. This makes PP great for food packages, medicine containers, and daily items like plastic bags and bottles. Its easy processing into films broadens its use in packaging.
ABS sees little use in packaging due to cost and weight but sometimes helps with durable and fancy-looking packages.
Toy Industry: Both Materials
Both ABS and PP are common in making toys, but for separate reasons. ABS works well for toys needing strength, impact resistance, and bright colors as it takes dye very well. Many premium toys use ABS for these reasons.
PP is often used in toys where saving money and weight matters more than strength.
In summary, choosing between ABS or PP plastics depends largely on what the industry requires—balancing strength, weight, chemical resistance, and cost.
ABS is used for car bumpers due to strength.False
PP, not ABS, goes into bumpers because it is light.
PP plastic is commonly used in packaging industry.True
PP's lightness and resistance to chemicals suit it very well for packaging.
How do ABS and PP perform under different thermal conditions?
ABS and PP plastics show different behaviors when hot, affecting their use for certain purposes.
ABS plastic, with a glass transition temperature of 105°C, offers high thermal stability, making it ideal for heat-resistant applications. Conversely, PP plastic’s moderate thermal resistance is beneficial in environments requiring lightweight materials with sufficient heat tolerance.
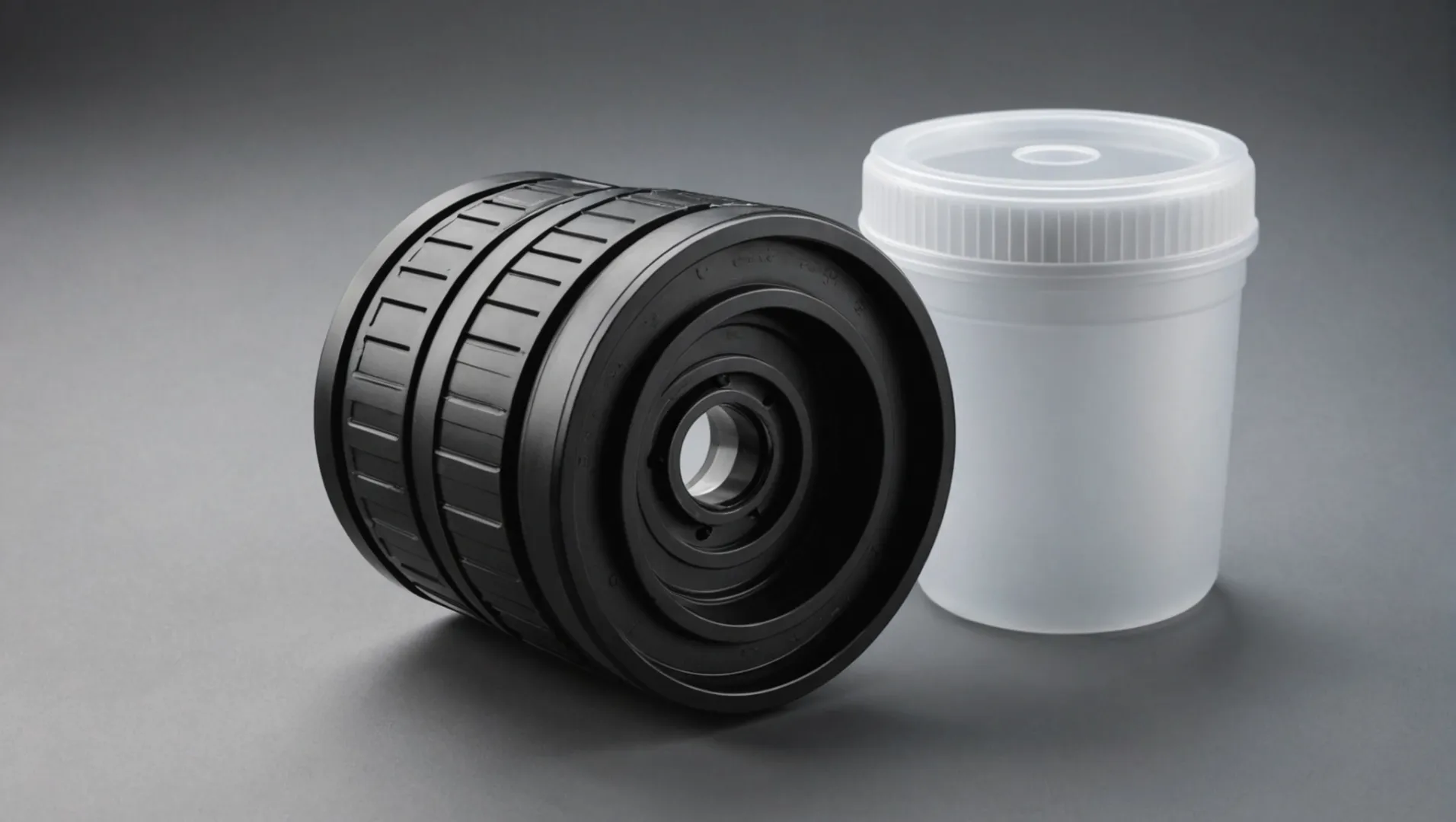
Understanding Thermal Traits of ABS and PP Plastics
Choosing between ABS (acrylonitrile butadiene styrene) and PP (polypropylene) plastics requires knowing their thermal traits. Each plastic behaves differently when heated, affecting its use and lifespan in various situations.
ABS Plastic: Strong Stability with Heat
ABS stands out for its strong mechanical performance8 and easy processing. It begins to soften around 105°C. This trait keeps ABS steady in environments with higher temperatures, fitting applications like electronic casings and car parts.
-
Processing Temperature: ABS functions well from 204 to 238°C, supporting hot manufacturing methods like injection molding.
-
Uses: Because of its good thermal stability, you find ABS in items like computer keyboards and car dashboards, where heat stability is needed.
PP Plastic: Medium Heat Resistance
PP holds medium heat resistance compared to ABS. It may not face extreme heat like ABS, yet its lightness and resistance to chemicals make it suitable in different cases.
-
Heat Resistance: PP plastics resist heat above 100°C, fitting them for microwave-safe containers and hot water pipes.
-
Thermal Stability in Mixes: In wood-plastic mixes, PP shows a middle level of thermal stability. This allows PP mixes to keep their form in moderately warm settings.
Trait | ABS | PP |
---|---|---|
Glass Transition Temp | ~105°C | Changes, usually >100°C |
Processing Temp Range | 204 – 238°C | Less than ABS |
Key Uses | Electronic casings, car parts | Microwave-safe items, hot water pipes |
Think About Use Context
When choosing ABS or PP, one should think about the specific heat requirements of the use case. In places with big temperature changes or high heat, ABS plastic’s stability9 offers benefits. Yet, if weight reduction and chemical resistance are key, along with medium heat exposure, PP stands as the better option.
To sum up, knowing these plastics’ thermal traits assists creators in picking the best material for their purposes.
ABS plastic has a glass transition temperature of 105°C.True
ABS stays firm up to 105°C before becoming soft, suitable for warm uses.
PP plastic can withstand temperatures over 200°C.False
PP's heat resistance typically exceeds 100°C, though it rarely reaches 200°C.
Conclusion
Pick ABS or PP depending on what your task requires, like sturdiness or lightness. Think about these elements to enrich your choice.
-
Explore how PP composites compare in strength with other plastics.: Wood plastic composite lumber is made of a mixture of wood fibers and plastic materials. Composite decking is usually heavier than PVC decking, but lighter … ↩
-
Discover additives that enhance PP’s abrasion resistance.: Select a product number from the table below to view a product data sheet for these materials using polypropylene as the base resin. ↩
-
Explore why ABS is valued for its mechanical strength.: Impact resistance: ABS plastic is known for its excellent impact resistance, making it suitable for applications that require durability and toughness. ↩
-
Discover how PP’s chemical stability benefits packaging.: Household and consumer goods: Many household products are made from polypropylene due to its durability, chemical resistance, and versatility. Examples include … ↩
-
Explore why ABS is ideal for automotive interior components.: ABS is commonly used for parts that include dashboard components, seat backs, seat belt components, handles, door loners, pillar trim, and … ↩
-
Discover how PP contributes to lightweight car parts.: In the automotive industry, PP’s commonly used for bumpers, chemical tanks, cable insulation, and gas cans. Polypropylene is also often utilized … ↩
-
Learn why PP is preferred for packaging solutions.: Polypropylene is also low density when compared to other plastics, so for manufacturers, they have the benefit of saving money from low weight. ↩
-
Explore how ABS’s strength supports high-temperature applications.: Tensile Strength, Ultimate, 22.1 – 74.0 MPa, 3210 – 10700 psi, Average value: 38.6 MPa Grade Count:60. Tensile Strength, Yield, 13.0 – 65.0 MPa, 1890 – 9430 psi … ↩
-
Learn about ABS’s heat resilience in various industries.: This work investigates the accelerated thermal degradation of acrylonitrile–butadiene–styrene (ABS) due to aging at elevated temperatures (>80 °C). ↩