Diving into the world of injection molding can feel overwhelming, especially when faced with choices like ABS, PP, and PVC. But understanding these materials is key to ensuring your project shines!
ABS, PP, and PVC differ in injection molding based on their chemical properties, physical characteristics, processing performance, and application suitability. ABS is known for its strength and toughness, PP for its flexibility and low density, while PVC offers good corrosion resistance and flame retardancy.
Understanding these differences is crucial for selecting the right material for your injection molding projects. Whether you’re working in automotive, construction, or consumer goods, each material has distinct advantages that could align with your specific needs. Dive deeper into their unique characteristics to make an informed decision.
ABS is ideal for automotive parts due to its toughness.True
ABS's high impact resistance and durability make it suitable for automotive applications.
What Are the Chemical Properties of ABS, PP, and PVC?
Discover how the chemical makeup of ABS, PP, and PVC determines their applications and performance in injection molding.
ABS, PP, and PVC exhibit unique chemical properties that influence their use in injection molding. ABS is resistant to acids and alkalis, PP remains stable against most chemicals except strong acids, while PVC is chemically resistant but decomposes under heat or light.

Understanding ABS‘s Chemical Properties
Acrylonitrile-Butadiene-Styrene, commonly referred to as ABS, is a thermoplastic polymer known for its robustness and versatility. Chemically, ABS showcases excellent resistance to corrosive chemicals such as acids, alkalis, and salts. This property makes it a preferred choice for applications requiring durability and longevity. For instance, in the automotive industry, ABS is frequently used due to its ability to withstand harsh chemical environments without degrading. Moreover, its ease of processing and molding further enhances its appeal for complex manufacturing projects.
Exploring PP‘s Stability
Polypropylene (PP) is distinguished by its non-toxic and odorless nature. It is a highly crystalline polymer, which contributes to its impressive chemical stability. Except for its susceptibility to concentrated sulfuric and nitric acids, PP maintains stability against a wide range of chemical reagents. This stability makes it suitable for food packaging and medical equipment, where material integrity against various substances is critical. Additionally, PP‘s lightweight characteristic supports its widespread use in applications where weight reduction is beneficial.
The Dual Nature of PVC
Polyvinyl Chloride (PVC) is celebrated for its chemical corrosion resistance. However, it exhibits a dual nature as it decomposes when exposed to high temperatures or light, releasing hydrogen chloride, which is harmful. This decomposition potential necessitates careful handling and processing conditions. Despite this limitation, PVC‘s low cost and excellent flame retardancy make it a popular choice in construction materials like pipes and fittings, where corrosion resistance is crucial.
Property | ABS | PP | PVC |
---|---|---|---|
Corrosion Resistance | Resistant to acids and alkalis | Stable except strong acids | Resistant but decomposes under heat/light |
Processing | Easy to mold | Lightweight and stable | Requires careful handling |
Understanding these chemical properties helps manufacturers select the appropriate material for specific applications, ensuring product performance and safety across industries1.
ABS is resistant to acids and alkalis.True
ABS's chemical structure provides excellent resistance to corrosive chemicals.
PP decomposes under light exposure.False
PP remains stable under light, unlike PVC which decomposes under heat/light.
How Do Physical Properties Influence Material Selection in Injection Molding?
In injection molding, choosing the right material hinges on understanding physical properties like hardness, density, and heat resistance. These characteristics directly influence the performance and application of the final product.
Physical properties such as hardness, density, heat resistance, and transparency significantly influence material selection in injection molding. For example, ABS is chosen for its high hardness and impact resistance, PP for its low density and good heat resistance, while PVC is selected for its adjustable hardness and corrosion resistance.
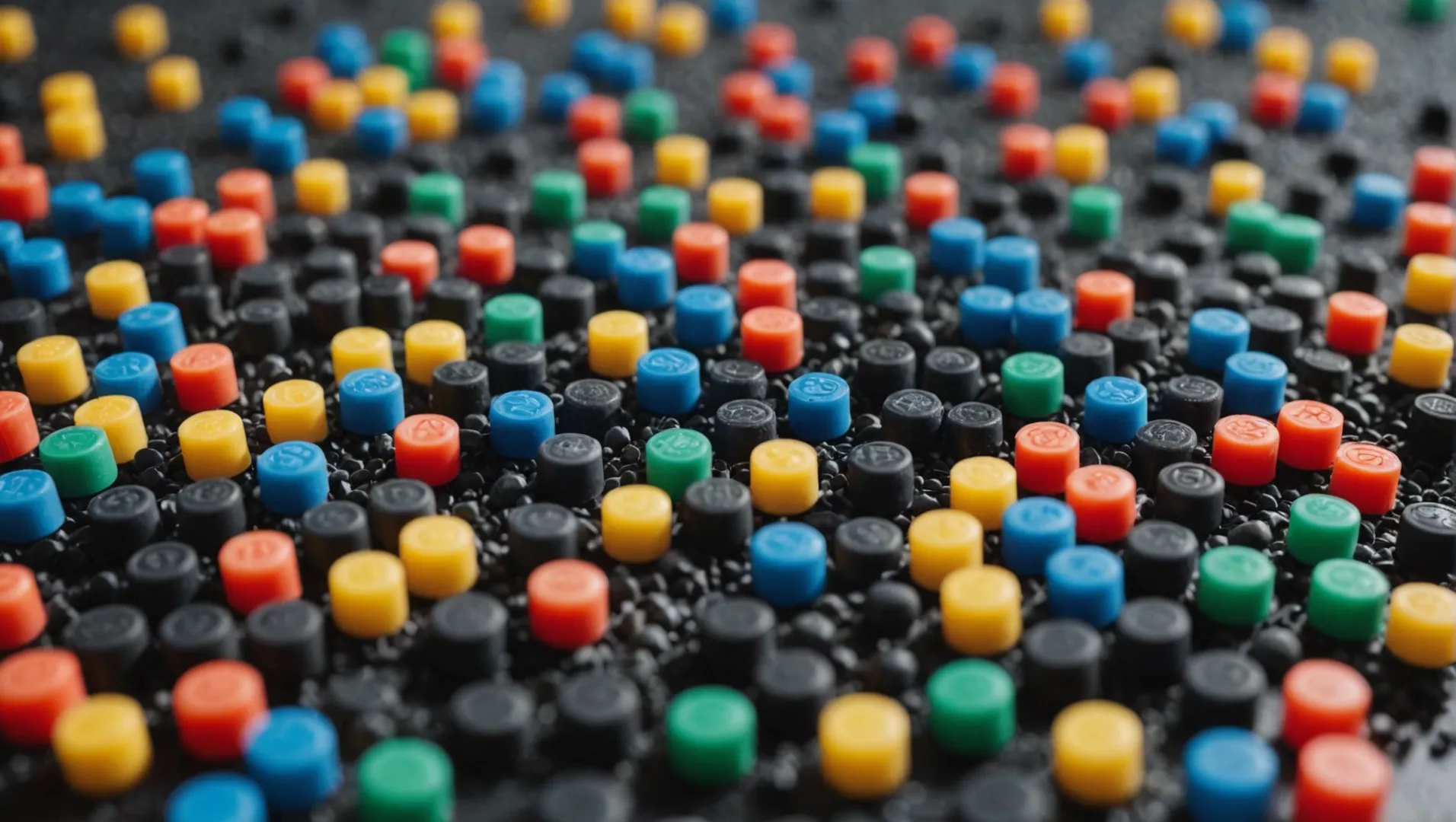
Understanding the Role of Hardness in Material Selection
Hardness plays a pivotal role in determining the durability and wear resistance of the molded product. ABS2 is renowned for its high hardness and excellent impact resistance, making it ideal for applications where strength is paramount, such as automotive parts and electronics housings. Conversely, PP3 offers lower hardness but greater flexibility, suitable for applications that demand pliability without compromising integrity.
Density: A Crucial Factor
Density affects both the weight and cost-effectiveness of the final product. With PP4 boasting the lowest density at approximately 0.90-0.91g/cm³, it is preferred in industries requiring lightweight materials, such as packaging and medical devices. Meanwhile, PVC5 has a higher density range of 1.3-1.4g/cm³, aligning well with construction applications where robustness is critical.
The Impact of Heat Resistance
Heat resistance determines a material’s ability to retain properties under temperature variations. PP6, with its superior heat resistance, is ideal for applications exposed to elevated temperatures, such as automotive interiors. ABS7 holds moderate heat resistance, making it suitable for everyday consumer goods. In contrast, PVC‘s8 poor heat tolerance restricts its use to environments with lower temperature demands.
Transparency and Its Influence on Aesthetic Decisions
The transparency of a material can dictate its application based on aesthetic needs. Both ABS and PP9 can be manufactured into clear or translucent products, offering versatility in design and use in items like toys and food containers. On the other hand, PVC‘s10 inherent opacity can be modified through additives to meet specific visual requirements in products like signage and piping.
These properties collectively guide engineers and designers in selecting the appropriate material for injection molding projects, ensuring optimal performance and cost-efficiency.
ABS is preferred for automotive parts due to high hardness.True
ABS's hardness and impact resistance make it ideal for durable automotive applications.
PP is unsuitable for high-temperature environments.False
PP's superior heat resistance makes it suitable for high-temperature applications.
What Is the Role of Processing Performance in Choosing Injection Molding Materials?
Selecting the right injection molding material is pivotal for production efficiency and product quality. Processing performance plays a crucial role in this decision, impacting ease of manufacturing, cost, and final product attributes.
Processing performance influences material choice in injection molding by affecting fluidity, shrinkage, and drying requirements. PP exhibits the best fluidity, while ABS has minimal shrinkage. PVC requires careful handling due to its poor fluidity and higher drying needs.
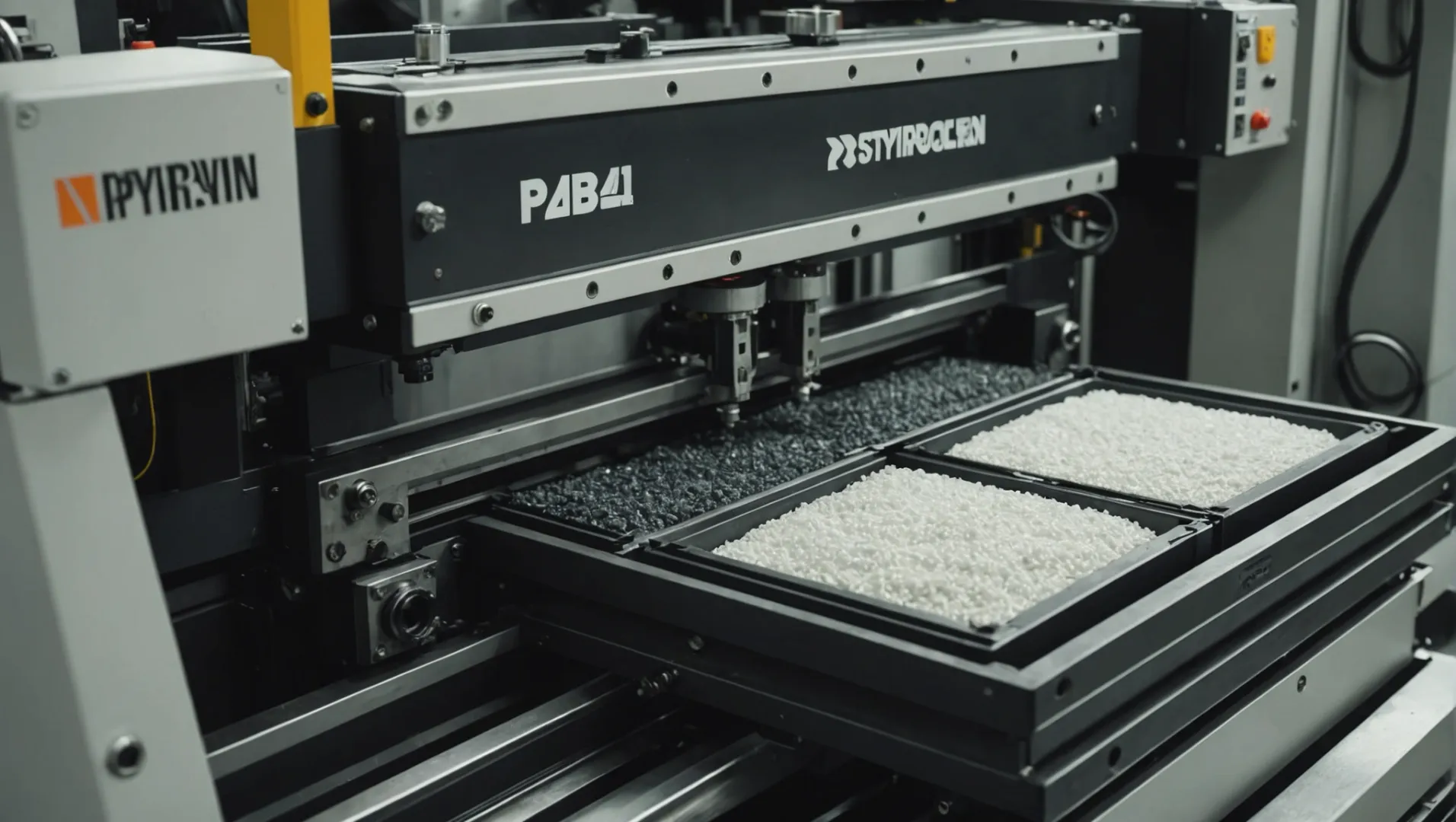
Fluidity and Mold Filling
Fluidity is vital in determining how well a material can fill the mold during injection molding. Polypropylene (PP)11 stands out with exceptional fluidity, making it easier to fill complex molds efficiently. This characteristic often translates into faster cycle times and reduced production costs.
In contrast, PVC (Polyvinyl Chloride)12 has poor fluidity, necessitating higher injection pressures and temperatures to achieve complete mold filling. This requirement can lead to increased energy consumption and potential wear on machinery, impacting overall cost-effectiveness.
Shrinkage Rates
Shrinkage is a critical factor influencing dimensional accuracy and part consistency. ABS (Acrylonitrile-Butadiene-Styrene Copolymer)13 boasts a low shrinkage rate of about 0.4%-0.7%, making it an excellent choice for precision parts where tight tolerances are necessary.
PP, however, has a larger shrinkage range of 1.5%-2.5%, which might require design adjustments or additional processing steps to compensate for dimensional changes post-molding. PVC also offers minimal shrinkage, ranging from 0.1%-0.5%, beneficial for applications demanding high dimensional stability.
Drying Requirements
The drying requirements of materials before processing can influence both the ease and cost of manufacturing. Generally, PP and ABS do not require extensive pre-drying unless stored under humid conditions, which adds to their appeal in terms of processing convenience.
Conversely, PVC typically requires thorough drying to prevent moisture from affecting the molding process and compromising product quality. This additional step can increase lead times and costs, factors that must be weighed against its benefits such as flame retardancy.
Understanding these aspects of processing performance is essential for making informed material choices in injection molding applications. The decision should align with the specific needs of your project, considering factors such as product design complexity, desired properties, and production efficiency.
PP has the best fluidity for injection molding.True
Polypropylene's exceptional fluidity aids in efficient mold filling.
PVC requires less drying than ABS before processing.False
PVC needs thorough drying; ABS generally requires minimal pre-drying.
Which Applications Best Suit ABS, PP, and PVC?
Choosing the right plastic for your application can make all the difference in durability, performance, and cost. ABS, PP, and PVC each offer distinct benefits for various industries and uses.
ABS is ideal for automotive and electronics due to its toughness; PP suits food packaging and medical equipment thanks to its non-toxicity; PVC is perfect for construction materials and insulation given its flame retardancy.
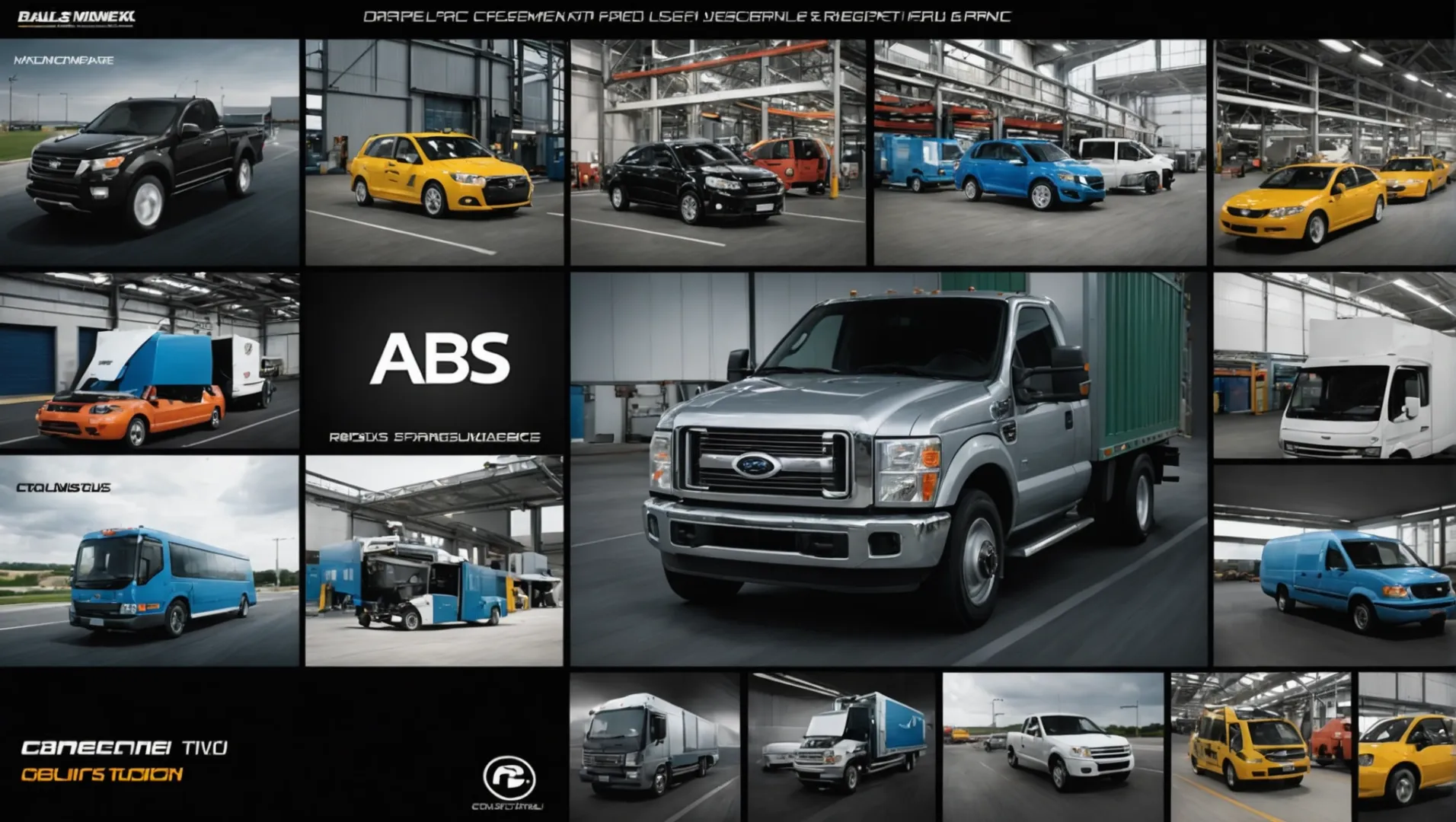
ABS: The Durable Choice for Automotive and Electronics
ABS (Acrylonitrile-Butadiene-Styrene) is renowned for its robustness and adaptability. Its high strength and toughness14 make it perfect for automotive applications such as dashboards, wheel covers, and interior trim. Additionally, the electrical housings and consumer electronics industries prefer ABS for its appealing finish and impact resistance.
Application Area | Benefits of Using ABS |
---|---|
Automotive | High impact resistance, aesthetic finish |
Electronics | Good electrical insulation properties, robust structure |
Consumer Goods | Durable, easy to mold into complex shapes |
PP: Safe and Reliable for Food and Medical Uses
Polypropylene (PP) stands out for its excellent chemical stability and resistance to high temperatures. This makes it a preferred choice for food packaging15 containers that need to withstand microwaving. In the medical field, PP‘s non-toxic nature ensures safety in items like syringes and medical containers.
Application Area | Benefits of Using PP |
---|---|
Food Packaging | Heat resistant, non-toxic |
Medical Equipment | Sterilizable, chemical resistant |
Automotive Interiors | Lightweight, durable |
PVC: Economical and Flame-Resistant for Construction
PVC (Polyvinyl Chloride) is widely used in the construction industry due to its affordability and flame retardancy. It serves well in building materials like pipes, window frames16, and flooring. Furthermore, its excellent insulation properties make it suitable for wire and cable coverings.
Application Area | Benefits of Using PVC |
---|---|
Construction Materials | Cost-effective, flame retardant |
Wire Insulation | Good electrical insulation, corrosion resistant |
Artificial Leather | Durable, versatile |
Choosing between these materials depends heavily on the specific requirements of the application. Considerations such as cost, durability, environmental impact, and specific industry standards should guide your material selection process.
ABS is ideal for automotive applications.True
ABS offers high impact resistance and an aesthetic finish, perfect for cars.
PVC is used in food packaging for its non-toxicity.False
PVC is not typically used in food packaging due to potential toxicity concerns.
Conclusion
Ultimately, choosing the right material—ABS, PP, or PVC—can elevate your product’s performance. Reflect on your project’s needs to make the best choice.
-
Explore diverse uses of ABS, PP, and PVC across various sectors.: Benefits and Applications of ABS · Housings · Lawn and garden equipment · Lenses · Lighting · Medical/Health Care (surgical instruments, IV-system … ↩
-
Explore how ABS hardness benefits automotive applications.: Higher notched izod impact strength than other types of ABS. However has lower tensile strength and creep resistance. ↩
-
Discover where PP’s flexibility is most advantageous.: Polypropylene is waterproof and extremely resistant to moisture absorption, which adds to its packaging benefits and flexibility as a packaging material. ↩
-
Learn why low density makes PP ideal for lightweight products.: Polypropylene is also low density when compared to other plastics, so for manufacturers, they have the benefit of saving money from low weight. ↩
-
Find out why high-density PVC suits construction needs.: These versatile PVC sheets are perfect for a variety of applications, including signage, displays, and fabrication. Made from high-quality, durable material. ↩
-
Uncover how PP’s heat resistance benefits automotive interiors.: In the packaging sector, polypropylene’s good heat resistance is a boon. It can be used for containers that hold hot foods or liquids without … ↩
-
See which products benefit from ABS’s moderate heat tolerance.: Talc and mica, on the other hand, are plate-like fillers that can improve the heat resistance of ABS by forming a barrier to heat transfer … ↩
-
Understand PVC’s usage limitations due to heat sensitivity.: Even so, the most recommended upper limit is 80 ℃. Any more beyond this temperature means that the PVC pipe might be at risk of damage and losing its structure. ↩
-
Identify products leveraging ABS and PP’s transparency.: Transparent ABS, also called MABS plastic material, which has excellent transparency, impact toughness and good processing properties. ↩
-
Explore how additives alter PVC’s opacity for various uses.: The smaller the haze value, the higher the transparency, and higher gloss values indicate enhanced gloss. ↩
-
Learn why PP’s fluidity aids in efficient mold filling.: Polypropylene (PP) is a thermoplastic addition polymer, which is used predominantly in injection molding applications. PP is inexpensive and easy to access. ↩
-
Understand PVC’s processing demands and how it impacts production.: PVC can be volatile and difficult to work with. The material degrades easier than most. Also CPVC, a common type of PVC will outgas hydrochloric … ↩
-
Discover how ABS’s low shrinkage supports precise manufacturing.: ABS Shrinkage and Compensation The shrinkage rate for ABS is slightly higher than PLA, averaging 0.4-0.9% overall. Besides, ABS warps easily as … ↩
-
Learn why ABS is favored for car parts due to impact resistance.: ABS plastic’s strength, impact resistance, and surface finish make it suitable for automotive applications. Toys and games: ABS plastic is a popular material … ↩
-
Discover why PP is ideal for safe food storage.: PP products can safely undergo high heat without having to worry about chemical leaching or taste and odor issues, making them compatible for … ↩
-
Explore how PVC benefits construction through cost-efficiency and durability.: It is resistance fire, water, flame and corrosion. It has light weight and great insulating property. As a building material, PVC is cheap and … ↩